What Is A Drive Shaft

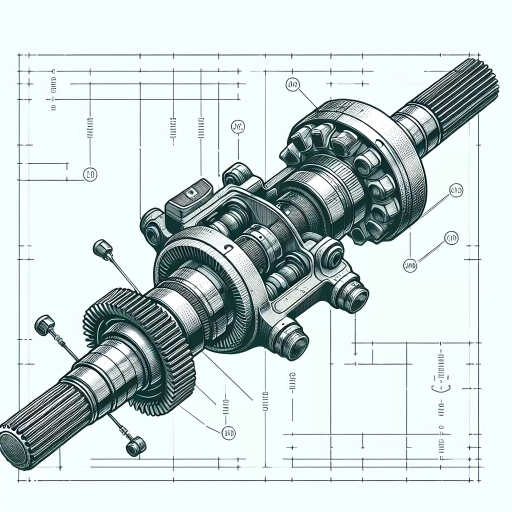
A drive shaft is a critical component in the mechanical transmission of power, playing a pivotal role in various machinery and vehicles. This essential part connects the engine to the transmission and ultimately to the wheels or other driven components, ensuring smooth and efficient power transfer. In this article, we will delve into the intricacies of drive shafts, starting with an **Introduction to Drive Shafts**, where we explore their history, types, and applications. We will then examine the **Components and Construction of Drive Shafts**, detailing the materials, design considerations, and manufacturing processes that go into creating these robust yet precise mechanisms. Finally, we will discuss the **Functionality and Maintenance of Drive Shafts**, highlighting how they operate under different conditions and the importance of regular maintenance to prevent wear and tear. By understanding these aspects, readers will gain a comprehensive insight into the vital role drive shafts play in modern machinery. Let us begin by exploring what drive shafts are and their significance in mechanical systems.
Introduction to Drive Shafts
Drive shafts are a crucial component in the mechanical transmission of power, playing a pivotal role in various industries and applications. Understanding the intricacies of drive shafts begins with grasping their fundamental definition and purpose. These components are designed to transmit rotational motion and torque from one part of a machine to another, ensuring efficient and reliable operation. However, the significance of drive shafts extends beyond their immediate function. Historically, the development of drive shafts has been a cornerstone in the evolution of mechanical engineering, with advancements in materials and design contributing to improved performance and durability. Today, drive shafts are ubiquitous in common applications such as automotive systems, industrial machinery, and aerospace technology. By exploring these aspects—definition and purpose, historical development, and common applications—we can gain a comprehensive understanding of how drive shafts have become an indispensable element in modern engineering. Let us start by delving into the definition and purpose of drive shafts, which form the foundation of their importance and functionality.
Definition and Purpose
In the realm of mechanical engineering and automotive technology, the drive shaft plays a pivotal role in the transmission of power from the engine to the wheels, ensuring efficient and smooth operation of vehicles. **Definition and Purpose** are fundamental aspects that underscore the significance of this critical component. A drive shaft, by definition, is a long rod or tube that connects the transmission to the differential in a vehicle, serving as a conduit for rotational energy. It is typically made from high-strength materials such as steel or aluminum to withstand the stresses and torques involved in power transmission. The drive shaft's primary purpose is to transfer torque generated by the engine through the transmission system to the wheels, thereby propelling the vehicle forward. This process involves converting the rotational energy produced by the engine into linear motion at the wheels. The purpose of a drive shaft extends beyond mere power transmission; it also ensures that this energy is delivered efficiently and reliably. By maintaining a consistent speed and torque output, the drive shaft helps in optimizing fuel efficiency, reducing wear on other components, and enhancing overall vehicle performance. Additionally, modern drive shafts are often designed with universal joints or constant velocity (CV) joints at each end, which allow for flexibility and smooth operation even when the vehicle is navigating uneven terrain or making sharp turns. Moreover, the design and construction of drive shafts have evolved significantly over time to meet the demands of contemporary automotive engineering. Advanced materials and manufacturing techniques have led to lighter yet stronger drive shafts, contributing to improved fuel economy and reduced emissions. Furthermore, innovations such as balanced drive shafts and precision-engineered joints have minimized vibrations and noise, enhancing driver comfort and reducing maintenance needs. In summary, understanding the definition and purpose of a drive shaft is essential for appreciating its integral role in vehicle mechanics. As a critical link between the engine and wheels, it not only facilitates power transmission but also contributes to the overall efficiency, reliability, and performance of the vehicle. This foundational knowledge sets the stage for delving deeper into the intricacies of drive shafts and their importance in modern automotive design.
Historical Development
The historical development of drive shafts is a fascinating narrative that spans centuries, reflecting the evolution of engineering, technology, and industrial needs. The earliest precursors to modern drive shafts date back to ancient civilizations, where simple wooden or stone rods were used to transmit rotational motion in primitive machinery such as windmills and waterwheels. As societies advanced, so did the materials and designs used in these early drive systems. In ancient Greece and Rome, for instance, engineers employed more sophisticated mechanisms involving wooden axles and leather straps to power various machines. The Industrial Revolution marked a significant turning point in the development of drive shafts. With the advent of steam power and the introduction of iron and steel, drive shafts became more robust and efficient. During this period, engineers like James Watt and Richard Trevithick developed more complex machinery that required reliable transmission systems. The use of universal joints, first patented by Robert Hooke in 1663 but later refined by Carl W. Borgeson in the late 19th century, allowed for smoother power transmission over longer distances and through varying angles. The 20th century saw further innovations with the introduction of new materials and technologies. The widespread adoption of automobiles led to significant advancements in drive shaft design, particularly with the development of constant velocity (CV) joints by Alfred H. Rzeppa in the 1920s. These CV joints enabled vehicles to maintain consistent power transmission even at high speeds and through tight turns, revolutionizing automotive engineering. In addition to automotive applications, drive shafts continued to play a crucial role in industrial machinery. Advances in materials science led to the use of high-strength alloys and composites, enhancing durability and reducing weight. Modern manufacturing techniques such as precision machining and computer-aided design (CAD) have further optimized drive shaft performance, allowing for tighter tolerances and improved efficiency. Today, drive shafts are integral components in a wide range of industries including aerospace, marine engineering, and renewable energy. The integration of advanced technologies such as carbon fiber and smart materials has opened new possibilities for lighter yet stronger drive shafts. Moreover, advancements in digital technologies have enabled real-time monitoring and predictive maintenance of drive shafts, extending their lifespan and reducing downtime. In conclusion, the historical development of drive shafts is a testament to human ingenuity and the relentless pursuit of innovation. From humble beginnings with wooden rods to sophisticated modern designs incorporating cutting-edge materials and technologies, drive shafts have evolved to meet the demands of an increasingly complex world. Understanding this rich history provides valuable context for appreciating the critical role that drive shafts play in contemporary engineering and technology.
Common Applications
Drive shafts are versatile components that play a crucial role in various mechanical systems, ensuring the efficient transmission of power and torque. Their common applications span across multiple industries, highlighting their adaptability and importance. In the automotive sector, drive shafts are integral to the drivetrain, connecting the transmission to the differential, thereby enabling the vehicle to move. They are also found in heavy-duty machinery such as tractors and construction equipment, where they facilitate robust power transfer necessary for demanding tasks. In industrial settings, drive shafts are used in conveyor systems, pumps, and generators to ensure smooth operation and reliability. Additionally, they are essential in marine applications, linking the engine to the propeller in boats and ships. The aerospace industry also relies on drive shafts for critical systems like engine starters and fuel pumps. Furthermore, in renewable energy systems such as wind turbines, drive shafts connect the rotor blades to the generator, converting kinetic energy into electrical power. Their presence in agricultural machinery like combine harvesters and plows underscores their role in enhancing productivity. Even in consumer products like lawn mowers and power tools, drive shafts are vital for efficient performance. The widespread use of drive shafts across these diverse applications underscores their significance as a fundamental component in mechanical engineering, ensuring that power is transmitted effectively and reliably. This ubiquity makes understanding drive shafts essential for anyone interested in the mechanics behind modern machinery and vehicles.
Components and Construction of Drive Shafts
Drive shafts are a critical component in the transmission of power within vehicles and machinery, ensuring efficient and reliable operation. The construction of drive shafts involves several key elements that contribute to their performance and durability. This article delves into the essential aspects of drive shafts, starting with the **Materials Used**. The choice of materials is paramount as it directly influences the strength, weight, and corrosion resistance of the drive shaft. Common materials include steel, aluminum, and carbon fiber, each offering unique benefits depending on the application. Next, we explore the **Key Components** that make up a drive shaft. These include universal joints and yokes, which facilitate smooth power transmission and flexibility. Understanding these components is crucial for maintaining and repairing drive shafts effectively. Finally, the **Manufacturing Process** is examined, highlighting the steps involved in producing high-quality drive shafts. From initial design to final assembly, this process ensures that drive shafts meet stringent standards for performance and safety. By understanding these three critical aspects—materials, components, and manufacturing process—we can appreciate the complexity and importance of drive shafts in modern machinery. Let's begin by examining the **Materials Used** in drive shaft construction, which sets the foundation for their overall functionality.
Materials Used
When it comes to the components and construction of drive shafts, the choice of materials is paramount for ensuring durability, performance, and safety. Drive shafts are subjected to various stresses including torsional loads, bending forces, and vibrations, making the selection of appropriate materials crucial. **Steel** remains a primary material due to its high strength-to-weight ratio, excellent torsional rigidity, and cost-effectiveness. High-strength steel alloys such as 4130 and 4140 are commonly used because they offer superior mechanical properties necessary for withstanding the harsh conditions encountered in automotive and industrial applications. These alloys can be heat-treated to enhance their hardness and fatigue resistance. **Aluminum** is another popular choice, particularly in lighter vehicle applications where weight reduction is critical. Aluminum drive shafts are often used in high-performance vehicles due to their lower density compared to steel, which helps in reducing overall vehicle weight and improving fuel efficiency. However, aluminum has lower strength and stiffness compared to steel, necessitating careful design considerations to ensure adequate performance. **Carbon Fiber** has emerged as a cutting-edge material for drive shafts in high-performance and specialized applications. Carbon fiber reinforced polymers (CFRP) offer exceptional strength-to-weight ratios, significantly outperforming traditional metals. This makes them ideal for racing cars and other high-performance vehicles where every gram of weight saved can translate into improved speed and handling. However, the higher cost and complexity of manufacturing CFRP drive shafts limit their widespread adoption. **Fiber-reinforced polymers (FRP)**, including glass fiber and aramid fiber composites, are also gaining traction due to their balanced properties of strength, stiffness, and weight. These materials are particularly useful in applications requiring resistance to corrosion and fatigue. FRP drive shafts are often used in marine and aerospace industries where exposure to harsh environments is common. In addition to these primary materials, **surface treatments** play a vital role in enhancing the performance and longevity of drive shafts. Processes such as chrome plating or nitriding can improve surface hardness and wear resistance, reducing the risk of damage from friction and abrasion. These treatments also help in minimizing the effects of corrosion, thereby extending the service life of the drive shaft. The **design and manufacturing process** of drive shafts also influence the choice of materials. For instance, hollow drive shafts made from high-strength steel can achieve significant weight savings without compromising on strength. Similarly, advanced manufacturing techniques like forging and machining allow for precise control over material properties and geometries, ensuring optimal performance under various operating conditions. In conclusion, the selection of materials for drive shafts is a critical aspect that directly impacts their functionality, reliability, and overall performance. By understanding the unique properties and advantages of different materials such as steel, aluminum, carbon fiber, and fiber-reinforced polymers, engineers can design and construct drive shafts that meet specific application requirements while ensuring safety and efficiency. The integration of surface treatments and advanced manufacturing techniques further enhances the capabilities of these components, making them indispensable in modern machinery and vehicles.
Key Components (e.g., Universal Joints, Yokes)
When delving into the components and construction of drive shafts, it is crucial to understand the key elements that ensure their functionality and durability. Among these, universal joints and yokes stand out as critical components that facilitate the efficient transmission of power from the engine to the wheels or other driven components. **Universal Joints:** Universal joints, also known as U-joints, are pivotal in allowing drive shafts to operate smoothly even when they are not perfectly aligned. These joints consist of a central cross-shaped member with four arms, each connected to a yoke. The universal joint enables the drive shaft to rotate while accommodating misalignment between the driving and driven shafts, which is inevitable due to the suspension movement of vehicles or machinery. This flexibility is essential for maintaining constant velocity and preventing vibrations that could lead to premature wear and tear on the drive shaft and other connected components. High-quality universal joints are typically made from robust materials such as steel or aluminum and are designed to withstand significant torque and stress. **Yokes:** Yokes are another vital component in the drive shaft assembly, serving as the interface between the universal joints and the drive shaft itself. These yokes are essentially the ends of the drive shaft that connect to the universal joints, allowing for smooth rotation and torque transmission. Yokes come in various designs, including single-cardan, double-cardan, and constant velocity (CV) types, each suited to different applications based on their ability to handle misalignment and maintain constant velocity. For instance, CV joints are commonly used in front-wheel drive vehicles where significant misalignment occurs due to steering and suspension movements. The material selection for yokes is critical; they are often made from high-strength steel alloys to ensure durability and resistance to fatigue. **Construction and Integration:** The integration of universal joints and yokes into the drive shaft assembly involves precise engineering to ensure optimal performance. The drive shaft itself is typically a tubular or solid rod made from high-strength materials like steel or aluminum, designed to withstand torsional stresses. The universal joints are attached to the yokes at each end of the drive shaft, allowing for flexibility and smooth power transmission. In some applications, additional components such as center bearings or support bearings may be included to reduce stress on the drive shaft and improve overall stability. In summary, universal joints and yokes are indispensable components in the construction of drive shafts, enabling them to operate efficiently under various conditions. Their ability to accommodate misalignment and maintain constant velocity ensures that power is transmitted smoothly from the engine to the wheels or other driven components, thereby enhancing the overall performance and longevity of the vehicle or machinery. Understanding these key components is essential for appreciating the intricate mechanics involved in drive shaft design and construction.
Manufacturing Process
The manufacturing process of drive shafts is a meticulous and highly specialized operation that involves several critical steps to ensure the production of high-quality, durable components. It begins with the selection of raw materials, typically high-strength steel alloys or advanced composites, which are chosen for their tensile strength, torsional rigidity, and resistance to fatigue. Once the materials are sourced, they undergo a series of rigorous tests to verify their mechanical properties. The next step involves cutting and machining the raw material into the desired shape and size. This is often achieved through CNC machining or other precision cutting techniques to maintain tight tolerances. Following this, the drive shaft undergoes various heat treatment processes such as quenching and tempering to enhance its mechanical properties further. These treatments help in achieving the optimal balance between hardness and ductility. After heat treatment, the drive shaft is subjected to surface finishing processes like grinding and polishing to achieve a smooth surface finish. This step is crucial as it reduces friction and wear during operation, thereby extending the lifespan of the drive shaft. Additionally, some drive shafts may undergo coating or plating processes to provide corrosion resistance and improve overall durability. Assembly is another key phase in the manufacturing process. Here, components such as universal joints, flanges, and yokes are attached to the drive shaft using precise welding or machining techniques. These components are critical for facilitating smooth power transmission and allowing for flexibility in the drive system. Quality control is an integral part of the manufacturing process. Each drive shaft undergoes a series of inspections and tests including dimensional checks, material analysis, and dynamic testing to ensure it meets stringent industry standards. These tests simulate real-world operating conditions to verify that the drive shaft can withstand various loads and stresses without failing. Finally, the finished drive shafts are packaged and shipped to automotive manufacturers or other industries where they are integrated into vehicles or machinery. Throughout this entire process, manufacturers adhere to strict quality control protocols and industry standards such as those set by the Society of Automotive Engineers (SAE) or the International Organization for Standardization (ISO). In summary, the manufacturing process of drive shafts is a complex interplay of material selection, precision machining, heat treatment, surface finishing, assembly, and rigorous quality control. Each step is designed to produce a component that is not only functional but also reliable and long-lasting under demanding operational conditions. This meticulous approach ensures that drive shafts can efficiently transmit power while maintaining safety and performance standards across various applications.
Functionality and Maintenance of Drive Shafts
Drive shafts are a crucial component in the mechanical system of vehicles, machinery, and other equipment, playing a pivotal role in the efficient transfer of power. Understanding their functionality and maintenance is essential for ensuring optimal performance and longevity. This article delves into the intricate details of drive shafts, beginning with **How Drive Shafts Transfer Power**, where we explore the mechanics behind their operation and the importance of precise alignment and balance. We then examine **Signs of Wear and Tear**, highlighting the indicators that signal the need for intervention to prevent catastrophic failures. Finally, we discuss **Maintenance and Repair Techniques**, providing practical insights into the methods and tools required to keep drive shafts in top condition. By grasping these key aspects, individuals can better appreciate the significance of drive shafts and take proactive steps to maintain their integrity, thereby enhancing overall system reliability and efficiency. Let's start by understanding how drive shafts transfer power, a fundamental concept that underpins their entire functionality.
How Drive Shafts Transfer Power
**How Drive Shafts Transfer Power** Drive shafts play a crucial role in the mechanical transmission of power within vehicles and machinery, ensuring efficient and reliable operation. At its core, a drive shaft is a long rod or tube that connects the transmission to the differential or final drive, facilitating the transfer of rotational energy. Here’s how this process works: when the engine produces torque, it is transmitted through the transmission system, which adjusts the speed and torque according to the vehicle's requirements. The drive shaft then receives this rotational energy and transmits it to the differential, where it is split into two separate paths for the wheels. The drive shaft itself is typically composed of a tubular structure with universal joints at each end. These universal joints allow for flexibility, enabling the drive shaft to accommodate changes in angle as the vehicle moves over uneven terrain or during suspension travel. This flexibility is essential because it ensures smooth power delivery even when the drive shaft is not perfectly aligned with the transmission and differential. In addition to universal joints, drive shafts often include center bearings or support bearings to stabilize and balance the shaft during rotation. These bearings help distribute the weight and stress evenly, reducing vibration and noise while enhancing overall durability. The material used for drive shafts is also critical; high-strength steel or aluminum alloys are common choices due to their strength-to-weight ratio, which helps in minimizing weight while maintaining structural integrity. This balance is vital for optimizing fuel efficiency and performance. Moreover, drive shafts are designed with safety features such as slip yokes and flanges that secure the shaft in place while allowing for slight movements necessary during operation. The slip yoke, for instance, allows for slight length changes in the drive shaft as it rotates, preventing damage from excessive stress. In terms of maintenance, regular inspection of drive shaft components is essential. Signs of wear on universal joints or bearings can lead to significant issues if left unaddressed. Lubrication of these components is also crucial; greasing universal joints periodically can extend their lifespan and ensure smooth operation. Overall, the drive shaft's ability to transfer power efficiently relies on its robust design, precise engineering, and proper maintenance. By understanding how drive shafts function and taking steps to maintain them, one can ensure optimal performance and longevity of the vehicle or machinery. This underscores the importance of drive shafts in modern mechanical systems and highlights their role as a critical link between power generation and application.
Signs of Wear and Tear
When it comes to the functionality and maintenance of drive shafts, recognizing signs of wear and tear is crucial for ensuring optimal performance and preventing costly repairs. A drive shaft, which transmits power from the engine to the wheels in a vehicle, undergoes significant stress and strain over time. One of the earliest signs of wear is vibration, which can be felt through the steering wheel or floorboard. This vibration often indicates misalignment or imbalance in the drive shaft, necessitating an inspection to adjust or replace the shaft if necessary. Another key indicator is noise; unusual clunking, rattling, or whining sounds during acceleration or deceleration can signal worn-out universal joints or other components within the drive shaft. Visual inspections are also vital; look for signs of rust, corrosion, or physical damage such as dents or cracks on the shaft itself. Additionally, excessive play in the universal joints can be a clear sign that they are nearing the end of their lifespan. Grease leaks around these joints are another red flag, suggesting that seals may be compromised and requiring immediate attention to prevent further damage. Furthermore, if you notice that your vehicle is experiencing reduced power output or struggling to maintain speed, it could be a sign that the drive shaft is no longer functioning efficiently due to wear and tear on its internal components. Regular maintenance checks, including balancing and aligning the drive shaft, can help extend its lifespan and prevent these issues from arising in the first place. By being vigilant about these signs and addressing them promptly, you can ensure that your drive shaft continues to operate smoothly and efficiently, thereby maintaining your vehicle's overall performance and reliability.
Maintenance and Repair Techniques
**Maintenance and Repair Techniques** The longevity and optimal performance of a drive shaft are heavily dependent on regular maintenance and prompt repair when necessary. Effective maintenance begins with routine inspections to identify potential issues before they escalate into major problems. This includes checking for signs of wear, such as cracks, dents, or excessive play in the shaft or its components. Lubrication is another critical aspect; ensuring that universal joints and other moving parts are adequately lubricated can significantly extend the lifespan of the drive shaft. Additionally, balancing the drive shaft is essential to prevent vibrations that could lead to premature wear or failure. In terms of repair techniques, diagnosing the root cause of any issue is paramount. For instance, if a drive shaft is experiencing excessive vibration, it may indicate an imbalance or misalignment rather than a fault with the shaft itself. Once identified, repairs can range from simple tasks like replacing worn-out universal joints or seals to more complex procedures such as straightening or replacing the drive shaft entirely. Advanced diagnostic tools, such as vibration analyzers and laser alignment systems, can aid in pinpointing issues accurately. When performing repairs, it is crucial to follow best practices to ensure safety and quality. This includes using high-quality replacement parts that meet or exceed OEM specifications and adhering to manufacturer guidelines for installation and torque settings. In some cases, specialized tools may be required to avoid damaging the drive shaft or its components during the repair process. Moreover, preventive maintenance schedules should be adhered to rigorously. For example, many manufacturers recommend periodic inspections at specific mileage intervals or after certain operational hours. These inspections can help detect early signs of wear and allow for proactive measures to be taken before a failure occurs. Incorporating advanced technologies into maintenance routines can also enhance the reliability of drive shafts. For instance, condition monitoring systems that use sensors to track real-time data on vibration levels, temperature, and other parameters can provide early warnings of potential issues. This proactive approach not only extends the lifespan of the drive shaft but also minimizes downtime and reduces overall maintenance costs. Ultimately, a well-maintained drive shaft is essential for ensuring the smooth operation of any vehicle or machinery. By combining regular inspections with prompt repairs and leveraging advanced diagnostic and maintenance techniques, operators can significantly enhance functionality while minimizing the risk of costly failures. This holistic approach underscores the importance of integrating robust maintenance strategies into overall operational practices to maximize efficiency and reliability.