What Is Cwb

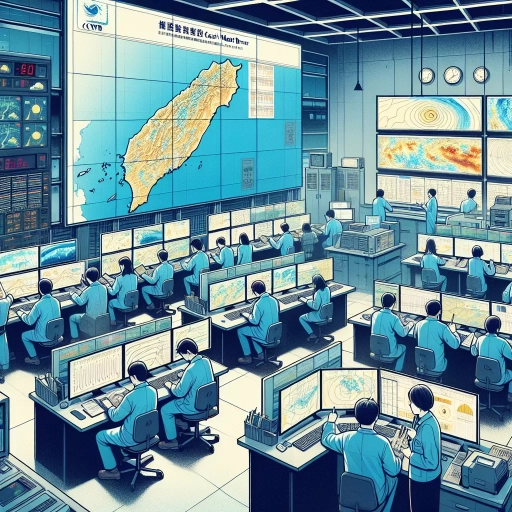
In the realm of construction and engineering, the term "CWB" stands for "Cold-Formed Welded" or "Cold-Worked" steel, but it is most commonly associated with the Canadian Welding Bureau (CWB). The CWB plays a pivotal role in ensuring the quality and safety of welding practices across various industries. This article delves into the multifaceted aspects of CWB, starting with **Understanding the Basics of CWB**, where we explore its foundational principles and certification processes. We will then examine **Applications and Uses of CWB**, highlighting how its standards and certifications are applied in diverse sectors such as oil and gas, transportation, and building construction. Finally, we will discuss **Benefits and Challenges of Implementing CWB**, analyzing the advantages of adhering to CWB standards while also addressing the potential hurdles faced during implementation. By understanding these core elements, readers will gain a comprehensive insight into the significance and impact of CWB in modern engineering. Let us begin by **Understanding the Basics of CWB** to lay the groundwork for a deeper exploration of this critical topic.
Understanding the Basics of CWB
Understanding the Basics of CWB (Canadian Welding Bureau) is a foundational step for anyone involved in welding and fabrication, particularly within the Canadian industry. This article delves into the essential aspects of CWB, providing a comprehensive overview that is both informative and engaging. To begin, we will explore the **Definition and Acronym Expansion**, clarifying what CWB stands for and its significance in the welding sector. Next, we will delve into the **Historical Context and Development**, tracing the evolution of CWB from its inception to its current status as a leading authority in welding standards. Finally, we will examine the **Key Components and Structure**, detailing the organizational framework and critical elements that make CWB a trusted benchmark for quality and safety. By understanding these core aspects, readers will gain a solid grasp of what CWB entails, setting the stage for a deeper exploration into the intricacies of this vital organization. Transitioning seamlessly into the heart of our discussion, let us embark on Understanding the Basics of CWB.
Definition and Acronym Expansion
Understanding the basics of CWB (Certified Welding Bureau) begins with a clear grasp of definitions and acronym expansions, which are fundamental to navigating the complex landscape of welding standards and certifications. CWB itself stands for Certified Welding Bureau, an organization that plays a crucial role in ensuring the quality and safety of welding practices in Canada. The acronym CWB is often associated with several key terms that are essential for anyone involved in the welding industry. Firstly, **CWB** is synonymous with **Certified Welding Bureau**, which is a division of the CWB Group. This organization is responsible for administering welding certification programs, conducting audits, and providing training to ensure compliance with national and international welding standards. The CWB Group also encompasses other critical components such as **CSA** (Canadian Standards Association), which develops and publishes standards for various industries including welding. Another important acronym is **W47.1**, which refers to the Canadian standard for fusion welding of steel. This standard, developed by CSA and administered by CWB, outlines the requirements for the qualification of welding personnel, procedures, and materials. Understanding W47.1 is crucial for any welding operation aiming to meet Canadian regulatory requirements. Additionally, **W59** stands for the Canadian standard for welded steel construction, focusing on the fabrication and inspection of welded steel structures. This standard ensures that structures are built to withstand various environmental and operational stresses, thereby enhancing public safety. The term **CWB Certification** itself is a badge of excellence, indicating that a welder, welding engineer, or fabricator has met rigorous standards set by the CWB. This certification process involves rigorous testing and evaluation to ensure that individuals possess the necessary skills and knowledge to perform high-quality welding work. In summary, understanding the definitions and acronym expansions related to CWB is pivotal for anyone seeking to grasp the fundamentals of welding standards and certifications. By recognizing what CWB, CSA, W47.1, and W59 represent, professionals in the welding industry can better navigate regulatory requirements, enhance their skills, and contribute to safer and more reliable construction practices. This foundational knowledge not only aids in compliance but also fosters a culture of excellence within the industry, ultimately benefiting both practitioners and the public at large.
Historical Context and Development
Understanding the basics of CWB (Certified Welding Bureau) requires a deep dive into its historical context and development. The origins of CWB trace back to the early 20th century, a period marked by rapid industrialization and the increasing demand for standardized welding practices. As industries such as construction, automotive, and aerospace expanded, the need for reliable and safe welding techniques became paramount. In response, various organizations began to develop standards and certifications to ensure the quality and integrity of welded structures. In Canada, this need was particularly pressing due to the country's vast infrastructure projects and heavy industries. The Canadian Standards Association (CSA) played a pivotal role in establishing guidelines for welding practices. However, it was the formation of the CWB in 1947 that truly revolutionized the field. Initially known as the Dominion Bureau of Standards, it later evolved into the CWB, focusing exclusively on welding standards and certifications. The CWB's development was driven by collaboration between industry stakeholders, government agencies, and technical experts. This collective effort led to the creation of comprehensive standards such as CSA W47.1 (Certification of Companies for Fusion Welding of Steel) and CSA W47.2 (Certification of Companies for Fusion Welding of Aluminum). These standards not only ensured that companies adhered to rigorous quality control measures but also provided a framework for continuous improvement in welding techniques. Over the years, the CWB has continued to evolve, incorporating advancements in technology and materials science. The introduction of new welding processes like MIG (GMAW) and TIG (GTAW) necessitated updates to existing standards, ensuring that they remained relevant and effective. Additionally, the CWB has expanded its scope to include training programs for welders and inspectors, further enhancing the skillset of industry professionals. Today, the CWB is recognized as a leading authority in welding certification, not just within Canada but globally. Its rigorous standards and certification processes have become benchmarks for industries worldwide. The historical context and development of CWB underscore the importance of collaboration, innovation, and adherence to quality standards in ensuring the safety and reliability of welded structures. This legacy continues to shape the future of welding, making it an essential component of modern engineering and construction practices. By understanding this historical context, one can better appreciate the significance of CWB certifications and their role in maintaining high standards within the welding industry.
Key Components and Structure
Understanding the basics of CWB (Certified Welding Bureau) involves grasping its key components and structure, which are pivotal for ensuring the quality and safety of welding practices. At the heart of CWB lies a robust framework that encompasses several critical elements. **Certification Programs** are a cornerstone, offering various levels of certification for welders, welding supervisors, and welding engineers. These programs are designed to validate the skills and knowledge of welding professionals, ensuring they meet stringent industry standards. **Training and Education** play a vital role in the CWB structure. The organization provides comprehensive training resources and educational materials that cater to different skill levels, from beginners to advanced professionals. This includes workshops, seminars, and online courses that cover topics such as welding techniques, safety protocols, and quality control measures. By investing in continuous learning, CWB fosters a culture of excellence within the welding community. The **Standards and Codes** component is another essential part of CWB's structure. The organization adheres to and promotes adherence to national and international standards, such as those set by CSA (Canadian Standards Association) and AWS (American Welding Society). These standards ensure that welding practices are consistent, reliable, and safe across different industries. CWB also participates in the development and revision of these standards, contributing to the evolution of best practices in welding. **Inspection and Testing** are integral to CWB's quality assurance process. The organization conducts rigorous inspections and testing to verify that welding work meets the required standards. This includes non-destructive testing (NDT) methods like radiography, ultrasonic testing, and magnetic particle testing, as well as destructive testing techniques such as tensile and bend tests. These processes help identify any defects or weaknesses in welds, ensuring that only high-quality work is certified. **Auditing and Compliance** are also key components of CWB's structure. Regular audits are conducted to ensure that certified welding facilities and personnel comply with the established standards and codes. This involves reviewing documentation, observing welding processes, and evaluating the overall quality management system. Non-compliance can result in corrective actions or even revocation of certification, emphasizing CWB's commitment to maintaining high standards. Lastly, **Industry Collaboration** is a vital aspect of CWB's structure. The organization works closely with industry stakeholders, including manufacturers, contractors, and regulatory bodies, to address common challenges and advance the field of welding. This collaborative approach helps in sharing best practices, adopting new technologies, and aligning with emerging industry trends. In summary, the key components and structure of CWB are designed to promote excellence in welding through certification, training, adherence to standards, rigorous inspection and testing, auditing for compliance, and industry collaboration. These elements collectively ensure that welding practices are safe, reliable, and of the highest quality, making CWB a trusted authority in the welding industry.
Applications and Uses of CWB
The Continuous Welding Beam (CWB) is a versatile and highly efficient technology that has revolutionized various industries with its robust applications and uses. This innovative method of welding has found significant traction in industrial and manufacturing settings, where it enhances productivity and quality. In the construction and building industry, CWB is instrumental in creating strong, durable structures that meet stringent safety standards. Additionally, environmental and safety considerations are paramount when implementing CWB, as it offers solutions that minimize waste and ensure a safer working environment. Understanding the multifaceted applications of CWB is crucial for optimizing its benefits across different sectors. This article delves into the industrial and manufacturing applications, construction and building industry uses, and environmental and safety considerations of CWB, providing a comprehensive overview that transitions seamlessly to understanding the basics of this technology. By exploring these key areas, readers will gain a deeper insight into how CWB can be effectively utilized to drive efficiency, safety, and sustainability in their respective fields.
Industrial and Manufacturing Applications
Industrial and manufacturing applications are a cornerstone of the diverse uses of Continuous Wave (CWB) technology. In these sectors, CWB plays a crucial role in enhancing efficiency, precision, and safety. One of the primary applications is in material processing, where CWB lasers are used for cutting, welding, and surface treatment of metals and other materials. The high power density and precise control offered by CWB lasers enable clean cuts with minimal thermal distortion, making them ideal for industries such as automotive, aerospace, and electronics manufacturing. Additionally, CWB lasers are employed in additive manufacturing processes like 3D printing, where they help create complex geometries with high accuracy. In the realm of quality control and inspection, CWB technology is utilized for non-destructive testing (NDT) and spectroscopy. For instance, CWB lasers can be used in Laser-Induced Breakdown Spectroscopy (LIBS) to analyze the chemical composition of materials without causing damage. This technique is invaluable in industries where material integrity is paramount, such as in the production of medical devices and pharmaceuticals. Moreover, CWB technology finds significant application in the field of robotics and automation. Here, it is used for tasks like seam tracking and adaptive welding, allowing robots to dynamically adjust their welding paths based on real-time feedback. This enhances the flexibility and reliability of automated manufacturing systems, particularly in high-volume production environments. The use of CWB also extends to surface treatment processes such as laser cleaning and surface hardening. Laser cleaning with CWB technology can remove contaminants from surfaces without damaging the underlying material, which is crucial in industries like food processing and semiconductor manufacturing. Surface hardening, on the other hand, involves using CWB lasers to heat-treat metal surfaces, improving their wear resistance and durability. Furthermore, CWB technology is integral to the development of advanced sensors and monitoring systems. These sensors can be used to monitor environmental conditions, detect anomalies in production lines, and ensure compliance with safety standards. For example, optical sensors based on CWB lasers can measure temperature, pressure, and vibration levels in real-time, enabling predictive maintenance and reducing downtime. In summary, the applications of CWB technology in industrial and manufacturing settings are multifaceted and transformative. From material processing and quality control to robotics and surface treatment, CWB lasers offer unparalleled precision, efficiency, and reliability. As industries continue to evolve towards more automated and sophisticated processes, the role of CWB technology is likely to expand further, driving innovation and excellence in manufacturing.
Construction and Building Industry Uses
The construction and building industry is a cornerstone of modern society, and it heavily relies on various materials and technologies to ensure the durability, safety, and aesthetic appeal of structures. One crucial aspect of this industry is the use of Certified Welding Bureau (CWB) standards and certifications. CWB plays a pivotal role in ensuring that welding practices meet stringent quality and safety standards, which is essential for the integrity of buildings, bridges, and other infrastructure. In the construction sector, CWB certifications are mandatory for many projects to guarantee that welds are performed by skilled and qualified personnel. This is particularly important for high-rise buildings, where structural integrity is paramount. Builders and architects must adhere to CWB guidelines to ensure that all welded joints can withstand various environmental conditions and loads. For instance, in seismic zones, buildings must be designed and constructed to resist earthquakes, and CWB-certified welds provide the necessary assurance that the structure can endure such stresses. Moreover, CWB standards are integral in the fabrication of steel components used in construction. From beams and columns to piping and ductwork, these components must be welded according to precise specifications to maintain their structural integrity. In industrial settings, such as power plants and chemical facilities, CWB-certified welds are critical for ensuring the safety and reliability of equipment and pipelines. The meticulous adherence to CWB protocols helps prevent catastrophic failures that could lead to accidents or environmental disasters. In addition to structural elements, CWB certifications also extend to specialized applications like bridge construction. Bridges require robust and durable welds that can withstand constant traffic flow and harsh weather conditions. Here, CWB standards ensure that welders follow best practices, using appropriate materials and techniques that guarantee the longevity of the bridge. Furthermore, CWB's influence extends beyond traditional construction materials like steel. The bureau also provides guidelines for welding other metals and alloys used in various building components, such as aluminum in architectural features or stainless steel in sanitary installations. This comprehensive approach ensures that all aspects of a building project meet high standards of quality and safety. In summary, the construction and building industry's reliance on CWB certifications underscores the importance of rigorous quality control in welding practices. By adhering to CWB standards, builders can ensure that their structures are safe, durable, and compliant with regulatory requirements. This not only enhances public safety but also contributes to the overall efficiency and sustainability of construction projects. As the industry continues to evolve with new technologies and materials, the role of CWB in maintaining excellence in welding practices remains indispensable.
Environmental and Safety Considerations
When considering the applications and uses of Controlled Wetting Behavior (CWB) materials, it is crucial to delve into the environmental and safety considerations that accompany their deployment. CWB materials, which are designed to manipulate the spreading and wetting properties of liquids on surfaces, have a wide range of applications from biomedical devices to industrial coatings. However, their use must be balanced with careful attention to environmental impact and safety protocols. From an environmental perspective, the production and disposal of CWB materials can have significant implications. The manufacturing process often involves the use of chemicals and solvents that could potentially harm ecosystems if not managed properly. Therefore, it is essential to adopt sustainable manufacturing practices that minimize waste and ensure the safe disposal of by-products. Additionally, the materials themselves should be designed with recyclability and biodegradability in mind to reduce their long-term environmental footprint. Safety considerations are equally paramount. CWB materials can be used in various settings, including medical devices and consumer products, where they come into direct contact with humans. Ensuring that these materials are non-toxic and hypoallergenic is critical to prevent adverse health reactions. For instance, in biomedical applications such as wound dressings or implantable devices, the biocompatibility of CWB materials must be rigorously tested to avoid any harmful interactions with biological tissues. In industrial settings, CWB coatings may be exposed to harsh conditions such as high temperatures or corrosive substances. Here, the durability and stability of these materials under various environmental conditions must be thoroughly evaluated to prevent degradation or failure that could lead to accidents or environmental hazards. Furthermore, workers handling these materials should follow strict safety guidelines to avoid exposure to potentially hazardous substances during application or maintenance processes. Regulatory compliance is another key aspect of environmental and safety considerations for CWB materials. Manufacturers must adhere to stringent regulations set by governing bodies such as the Environmental Protection Agency (EPA) in the United States or the European Chemicals Agency (ECHA) in Europe. These regulations dictate standards for chemical safety, waste management, and product labeling to ensure that CWB materials do not pose undue risks to human health or the environment. In conclusion, while CWB materials offer numerous benefits across various applications, their use necessitates a comprehensive approach to environmental stewardship and safety. By integrating sustainable practices into their production cycle, ensuring biocompatibility and durability, adhering to regulatory standards, and implementing robust safety protocols, we can harness the full potential of CWB technology while minimizing its adverse impacts on both human health and the environment. This balanced approach not only enhances the reliability and efficacy of CWB materials but also contributes to a more sustainable future for all stakeholders involved.
Benefits and Challenges of Implementing CWB
Implementing Continuous Welding (CWB) in industrial processes can significantly impact various aspects of operations, from economic efficiency to technical feasibility and regulatory adherence. This article delves into the multifaceted benefits and challenges associated with CWB, providing a comprehensive overview for those seeking to understand its implications. On one hand, CWB offers substantial economic advantages and cost savings by enhancing productivity, reducing material waste, and minimizing labor costs. However, it also presents technical challenges and limitations, such as the need for specialized equipment and skilled personnel, as well as potential issues with weld quality and consistency. Additionally, regulatory compliance and standards play a crucial role in ensuring that CWB processes meet industry requirements and safety protocols. By examining these key areas, this article aims to provide a balanced perspective on the implementation of CWB, ultimately guiding readers towards a deeper understanding of its benefits and challenges. To fully appreciate these insights, it is essential to first grasp the basics of CWB, which will be explored in detail in the following sections.
Economic Advantages and Cost Savings
Implementing a Continuous Welding Beam (CWB) system offers several economic advantages and significant cost savings, making it a compelling choice for various industries. One of the primary economic benefits is the reduction in material costs. CWB systems allow for the efficient use of materials by minimizing waste and optimizing the structural integrity of the beam. This is achieved through precise engineering and design, ensuring that the beam's strength is maximized while using the least amount of material necessary. Additionally, CWB systems often require fewer components compared to traditional welding methods, further reducing material expenditures. Another significant cost-saving aspect is the decrease in labor costs. The continuous welding process is typically more automated and streamlined, reducing the need for manual labor and the associated costs. This automation also leads to higher productivity rates, as the continuous process can operate for extended periods without the need for frequent stops or manual interventions. Furthermore, the reduced labor requirement translates into lower overhead costs, including training, safety equipment, and worker compensation. Maintenance and repair costs are also significantly lower with CWB systems. The continuous nature of the welds reduces the number of potential failure points, such as those found in traditional butt-welded joints. This results in fewer instances of structural failure and subsequent repairs, thereby extending the lifespan of the beam and reducing long-term maintenance expenses. Moreover, the uniformity of the continuous weld ensures consistent performance over time, minimizing the likelihood of unexpected failures that can disrupt operations and incur additional costs. Energy efficiency is another economic advantage of CWB systems. The continuous welding process often requires less energy compared to intermittent welding methods, which can lead to substantial savings on energy costs over time. This efficiency also contributes to a more environmentally friendly operation, aligning with sustainability goals and potentially qualifying for green incentives or tax credits. In summary, the economic advantages and cost savings associated with implementing a CWB system are multifaceted. From reduced material and labor costs to lower maintenance and energy expenses, CWB offers a financially attractive solution for industries seeking to optimize their operations while maintaining high standards of quality and performance. These benefits make CWB an increasingly popular choice for applications where efficiency, durability, and cost-effectiveness are paramount.
Technical Challenges and Limitations
Implementing Continuous Waveform (CWB) technology, while offering numerous benefits, is not without its technical challenges and limitations. One of the primary hurdles is the complexity of signal processing and analysis. CWB signals, which are continuous and unmodulated, require sophisticated algorithms to extract meaningful information. This necessitates significant computational power and advanced software capabilities, which can be resource-intensive and may strain existing infrastructure. Additionally, the continuous nature of these signals can lead to issues with data storage and management, as large volumes of data need to be processed and stored efficiently. Another challenge is the susceptibility of CWB signals to interference and noise. Since CWB operates on a single frequency, it is more vulnerable to environmental and man-made interference compared to other modulation techniques. This can result in signal degradation and reduced accuracy in applications such as radar systems or medical imaging. Furthermore, ensuring the stability and purity of the continuous waveform is crucial but challenging, as any deviation can compromise the integrity of the signal. From a hardware perspective, generating high-quality CWB signals requires specialized equipment with precise control over frequency and amplitude. The design and manufacturing of such equipment can be costly and time-consuming, limiting widespread adoption. Moreover, maintaining these systems over time involves regular calibration and maintenance to ensure they continue to operate within specified parameters. In terms of scalability, CWB technology may face limitations when applied to large-scale systems or networks. The synchronization of multiple CWB sources can be difficult, leading to potential phase drifts and coherence issues. This makes it challenging to integrate CWB into complex systems where multiple signals need to be coordinated seamlessly. Despite these technical challenges and limitations, researchers and engineers are continually working to overcome them through advancements in technology and innovative solutions. For instance, advancements in digital signal processing and machine learning algorithms are helping to improve signal analysis and noise reduction. Additionally, advancements in materials science are leading to more stable and efficient hardware components. While the implementation of CWB presents several technical hurdles, addressing these challenges can unlock significant benefits across various fields, from medical diagnostics to aerospace engineering.
Regulatory Compliance and Standards
Regulatory compliance and standards are pivotal components in the implementation of Certified Welding Bureau (CWB) certifications, as they ensure that welding practices adhere to rigorous safety and quality benchmarks. The CWB, a leading certification body in Canada, mandates that organizations comply with a suite of standards and regulations to guarantee the integrity and reliability of welded products. These standards, often derived from international bodies such as the American Society of Mechanical Engineers (ASME) and the Canadian Standards Association (CSA), provide a framework for best practices in welding, inspection, and testing. Compliance with these standards involves a multifaceted approach. Firstly, organizations must establish and maintain a quality control program that aligns with CWB requirements. This includes developing detailed procedures for welding operations, conducting regular audits, and ensuring continuous training for welders and inspectors. Secondly, adherence to material specifications and testing protocols is crucial to verify the mechanical properties of welds. This may involve destructive and non-destructive testing methods to ensure that welds meet the required strength and durability criteria. The benefits of regulatory compliance are numerous. For instance, it enhances the safety of both the workforce and the end-users of welded products by minimizing the risk of structural failures. Compliance also fosters trust among stakeholders, including clients and regulatory bodies, thereby enhancing an organization's reputation and market competitiveness. Additionally, adhering to standards can streamline operations by reducing the likelihood of costly rework and improving overall efficiency. However, implementing and maintaining regulatory compliance comes with its challenges. One significant hurdle is the initial investment required to establish a compliant quality control system. This includes costs associated with training personnel, purchasing specialized equipment, and developing comprehensive procedural documentation. Furthermore, ongoing compliance demands continuous monitoring and updates to ensure that practices remain aligned with evolving standards and regulations. This can be resource-intensive and may divert attention from core business activities. Despite these challenges, the long-term benefits of regulatory compliance far outweigh the costs. By embedding CWB standards into their operations, organizations can achieve higher levels of quality, safety, and reliability. This not only protects against legal and financial risks but also contributes to a culture of excellence within the organization. In summary, regulatory compliance and adherence to CWB standards are essential for ensuring the integrity of welding practices, enhancing safety and quality, and driving business success in a highly regulated industry.