What Is Woven Fabric

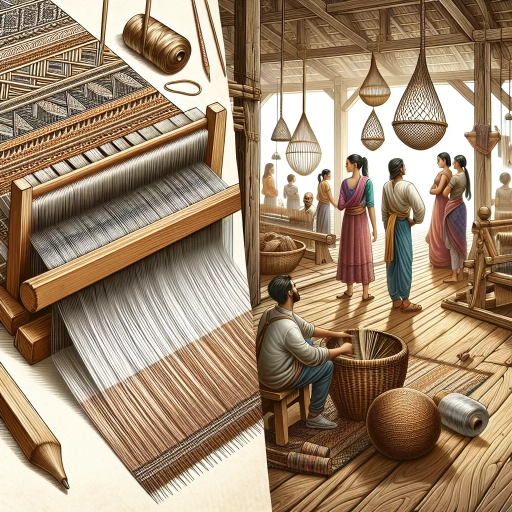
Woven fabric, a cornerstone of textile manufacturing, has been a vital component of human civilization for millennia. Its versatility, durability, and aesthetic appeal make it a staple in various industries, from fashion and interior design to industrial applications. To fully appreciate the significance of woven fabric, it is essential to delve into its fundamental aspects. This article will explore the basics of woven fabric, including the types of weaves, fibers used, and the structural integrity that defines it. We will also examine the intricate process of creating woven fabric, highlighting the machinery, techniques, and craftsmanship involved. Additionally, we will discuss the diverse applications and benefits of woven fabric, showcasing its impact on daily life and specialized fields. By understanding these facets, readers will gain a comprehensive insight into what makes woven fabric such a valuable material. Let us begin by **Understanding the Basics of Woven Fabric**.
Understanding the Basics of Woven Fabric
Understanding the basics of woven fabric is a multifaceted journey that encompasses various aspects, each contributing to the rich tapestry of textile knowledge. At its core, woven fabric is a material created through the interlacing of two sets of yarns, typically a warp and a weft, using a loom or other weaving device. To delve into this subject comprehensively, it is essential to explore three key areas: the definition and history of woven fabric, the types of fibers used in its creation, and the basic weaving techniques employed. The **definition and history of woven fabric** provide a foundational understanding of how this material has evolved over time, from ancient civilizations to modern manufacturing processes. This historical context not only highlights the technological advancements but also underscores the cultural significance of woven fabrics across different societies. Additionally, **types of fibers used in woven fabrics** play a crucial role in determining the fabric's properties, such as durability, comfort, and aesthetic appeal. Fibers can range from natural materials like cotton and wool to synthetic options like polyester and nylon, each offering unique characteristics that cater to various applications. Lastly, **basic weaving techniques** are the backbone of fabric production, involving methods such as plain weave, twill, and satin. These techniques influence the fabric's texture, strength, and visual appeal, making them vital for both traditional craftsmanship and industrial manufacturing. By examining these elements, one can gain a profound appreciation for the complexity and beauty of woven fabric. Let us begin this exploration by delving into the **definition and history of woven fabric**, tracing its origins and evolution over centuries.
Definition and History of Woven Fabric
Woven fabric, a cornerstone of textile production, has a rich and diverse history that spans thousands of years. The definition of woven fabric is straightforward: it is a type of fabric created by interlacing two or more sets of yarns, threads, or fibers at right angles to each other. This interlacing process, known as weaving, can be achieved using various techniques and tools, from simple handlooms to complex industrial machinery. The history of woven fabric dates back to ancient civilizations, where the earliest evidence of weaving can be traced to around 7000 BCE in the Neolithic period. During this time, people began to transition from nomadic hunter-gatherer lifestyles to more settled agricultural communities, leading to the development of more sophisticated textile production methods. The invention of the loom, which facilitated the systematic interlacing of threads, marked a significant milestone in the evolution of woven fabrics. Early looms were simple frame looms or ground looms, but as civilizations advanced, so did the technology, with the introduction of more complex devices like the warp-weighted loom and later the mechanized loom during the Industrial Revolution. Throughout history, different cultures have developed unique weaving techniques and patterns that reflect their artistic, social, and economic contexts. For instance, ancient Egyptians were renowned for their fine linens, while the Incas in South America created intricate textiles using wool from llamas and alpacas. In Asia, the art of silk weaving originated in China over 5,000 years ago and spread throughout the region, becoming a symbol of luxury and status. European medieval societies also had their own distinct weaving traditions, with guilds of skilled weavers producing high-quality fabrics for both practical use and ceremonial purposes. The Industrial Revolution in the 18th and 19th centuries revolutionized the production of woven fabrics by introducing mechanized looms that could weave much faster and more efficiently than human hands. This led to a mass production of textiles, making woven fabrics more accessible and affordable for the general population. However, it also brought about significant changes in the textile industry, including the displacement of traditional craftsmen and the rise of factory-based manufacturing. Today, woven fabrics continue to play a vital role in various aspects of life, from clothing and home furnishings to industrial applications such as filtration and medical textiles. Modern weaving techniques combine traditional methods with advanced technology, allowing for a wide range of fabric types and qualities. Understanding the basics of woven fabric involves appreciating both its historical significance and its contemporary relevance, recognizing how this ancient craft has evolved over time to meet the diverse needs of different societies and cultures. By delving into the definition and history of woven fabric, one can gain a deeper appreciation for the intricate processes and rich cultural heritage behind this fundamental material.
Types of Fibers Used in Woven Fabrics
Woven fabrics, a cornerstone of textile manufacturing, owe their versatility and durability to the diverse array of fibers used in their construction. These fibers can be broadly categorized into natural, synthetic, and blended types, each offering unique properties that cater to various needs and applications. **Natural Fibers** are derived from plants, animals, and minerals. **Cotton**, one of the most widely used natural fibers, is renowned for its breathability, softness, and absorbency. It is a staple in casual wear and home textiles. **Linen**, extracted from flax plants, is prized for its cooling properties and strength, making it ideal for summer clothing. **Silk**, obtained from silkworm cocoons, is celebrated for its luxurious feel and lustrous appearance, often used in high-end fashion. **Wool**, sourced from sheep and other animals, provides excellent insulation and is commonly used in winter garments. **Hemp** and **Bamboo** fibers are gaining popularity due to their sustainability and eco-friendly nature. **Synthetic Fibers**, on the other hand, are man-made and offer a range of benefits including durability, ease of care, and affordability. **Polyester** is one of the most common synthetic fibers, known for its resistance to wrinkles and shrinkage. It is often blended with other fibers to enhance performance. **Nylon** is strong and lightweight, making it perfect for outdoor gear and activewear. **Acrylic** mimics the warmth of wool without the high cost, making it a popular choice for knitwear. **Spandex**, or elastane, adds stretch to fabrics, which is crucial for garments that require flexibility like sportswear and swimwear. **Blended Fibers** combine the best attributes of natural and synthetic fibers. For instance, a cotton-polyester blend offers the softness of cotton with the durability of polyester. These blends are versatile and can be tailored to meet specific requirements such as wrinkle resistance, moisture-wicking properties, or enhanced strength. The ability to blend fibers allows manufacturers to create fabrics that are both functional and aesthetically pleasing. The choice of fiber significantly influences the final product's texture, comfort, and performance. Understanding these different types of fibers is essential for selecting the right fabric for various applications, whether it be clothing, upholstery, or industrial textiles. By leveraging the unique characteristics of each fiber type, manufacturers can produce woven fabrics that meet a wide range of needs, from everyday wear to specialized uses. This knowledge empowers consumers to make informed decisions about their fabric choices, ensuring they get the best possible product for their intended use. In summary, the diversity of fibers available for woven fabrics underscores the complexity and richness of textile science, allowing for endless possibilities in fabric creation.
Basic Weaving Techniques
Understanding the basics of woven fabric begins with mastering the fundamental techniques of weaving. Weaving is a centuries-old craft that involves interlacing two sets of yarns or threads at right angles to create a fabric. The primary components in weaving are the warp and weft. The warp threads are stretched on a loom and run lengthwise, while the weft threads are inserted across the warp, creating the fabric's width. Here are some basic weaving techniques that form the foundation of this art: 1. **Plain Weave**: This is the simplest and most common type of weave. In a plain weave, each weft thread passes over one warp thread and then under the next, creating a straightforward and durable fabric. This technique is used in everyday fabrics like cotton sheets and towels. 2. **Twill Weave**: Twill weaving involves passing the weft thread over two or more warp threads before going under one. This creates a diagonal pattern on the fabric, making it stronger and more flexible than plain weave. Denim jeans are a classic example of twill weave. 3. **Satin Weave**: In satin weaving, the weft thread floats over several warp threads before going under one, resulting in a smooth, glossy surface. This technique is often used in luxurious fabrics like silk and satin. 4. **Basket Weave**: This technique mimics the look of woven baskets by alternating two weft threads over and under two warp threads. It creates a textured fabric with a grid-like pattern, commonly seen in home decor items like placemats and wall hangings. 5. **Tabby Weave**: Similar to plain weave but with a more intricate pattern, tabby weave involves alternating the weft thread over and under multiple warp threads in a specific sequence. This method allows for various designs and is often used in traditional textiles. 6. **Pick-Up Weave**: This technique involves manually picking up specific warp threads to create patterns or designs on the fabric. It is commonly used in traditional and artisanal weaving to add unique elements to the fabric. 7. **Dobby Weave**: Dobby weaving uses a special attachment on the loom that allows for more complex patterns by lifting specific warp threads. This method is used to create intricate designs and is often seen in high-quality fabrics. 8. **Jacquard Weave**: Named after its inventor, Joseph Marie Jacquard, this technique uses a mechanical system to control the warp threads, enabling the creation of highly detailed and intricate patterns. It is widely used in luxury fabrics and custom textiles. Each of these techniques requires a different level of skill and equipment but collectively they form the backbone of woven fabric production. Understanding these basic weaving techniques not only appreciates the craftsmanship behind woven fabrics but also opens up possibilities for creative expression and innovation in textile design. Whether you are an artisan weaver or an enthusiast, mastering these techniques can lead to the creation of beautiful, functional, and unique fabrics that reflect both tradition and modernity.
The Process of Creating Woven Fabric
The process of creating woven fabric is a multifaceted and intricate journey that involves several critical stages. From the initial preparation of yarns and threads to the actual weaving process, and finally, the application of finishing treatments, each step plays a vital role in determining the quality and characteristics of the final product. The journey begins with the meticulous preparation of yarns and threads, where raw materials such as cotton, wool, or synthetic fibers are spun into usable strands. This foundational step sets the stage for the subsequent weaving process, which utilizes various looms and mechanisms to interlace these yarns into a cohesive fabric. Once the fabric is woven, it undergoes finishing treatments that enhance its texture, durability, and aesthetic appeal. Understanding these three key stages—preparation of yarns and threads, the weaving process, and finishing treatments—is essential for appreciating the craftsmanship and technology that go into creating high-quality woven fabrics. Let us delve deeper into the first of these stages: the preparation of yarns and threads.
Preparation of Yarns and Threads
The preparation of yarns and threads is a crucial step in the process of creating woven fabric, as it directly influences the quality, texture, and durability of the final product. This phase involves several key stages that transform raw materials into usable yarns. It begins with **fiber selection**, where natural fibers such as cotton, wool, and silk, or synthetic fibers like polyester and nylon, are chosen based on their properties and intended use. Once selected, these fibers undergo **cleaning and sorting** to remove impurities and ensure uniformity. Next, the fibers are subjected to **carding or combing**, processes that align them in the same direction. Carding produces a rope-like strand called a sliver, which is then spun into yarn. Combing, on the other hand, produces a more refined and aligned fiber bundle, resulting in smoother and stronger yarns. The **spinning** process converts these aligned fibers into continuous strands of yarn by twisting them together. The twist rate can vary depending on the desired yarn strength and texture. After spinning, the yarns may undergo additional treatments such as **dyeing** or **finishing**. Dyeing involves immersing the yarns in colorants to achieve the desired hue, while finishing treatments can include processes like bleaching, napping, or applying chemicals to enhance softness, wrinkle resistance, or other properties. **Winding** is another critical step where the yarns are wound onto spools or cones in a manner that prevents tangling and ensures even tension. This is particularly important for weaving as it affects the smooth operation of looms. Some yarns may also be **plied** together to create thicker, stronger threads suitable for specific weaving requirements. Finally, **quality control** checks are conducted to ensure that the prepared yarns meet the necessary standards for weaving. This includes testing for tensile strength, color consistency, and other parameters that impact fabric performance. In summary, the meticulous preparation of yarns and threads is foundational to producing high-quality woven fabric. Each stage from fiber selection to quality control contributes to the final product's aesthetic appeal, durability, and functionality. Understanding these processes highlights the complexity and craftsmanship involved in transforming raw materials into the versatile and essential textiles we use daily.
The Weaving Process: Looms and Mechanisms
The weaving process, a cornerstone of textile production, relies heavily on the intricate mechanisms of looms to transform raw materials into woven fabric. At its core, weaving involves the interlacing of two sets of yarns: the warp and the weft. The warp yarns are stretched taut on the loom, while the weft yarns are inserted across them in a perpendicular direction. This interlacing creates the fabric's texture and pattern. Looms, the primary tools in this process, have evolved significantly over time. From ancient handlooms to modern automated machines, each type of loom has its unique characteristics and advantages. Handlooms, for instance, allow for greater flexibility and control over the weaving process, making them ideal for artisanal and custom fabric production. These looms consist of a simple frame with heddles that separate the warp threads, enabling the weaver to manually insert the weft yarns. In contrast, mechanized looms have revolutionized the textile industry by increasing efficiency and productivity. The power loom, invented by Edmund Cartwright in the late 18th century, was a pivotal innovation that enabled mass production of woven fabrics. These looms use a series of cams or computer-controlled systems to automate the shedding (opening) and picking (insertion of weft) processes, significantly speeding up fabric creation. Modern industrial looms further refine this technology with advanced mechanisms such as air-jet and water-jet looms. Air-jet looms use compressed air to propel the weft yarn through the shed, while water-jet looms utilize a stream of water for this purpose. Both types offer high-speed weaving capabilities and are particularly suited for producing lightweight fabrics like cotton and polyester blends. The mechanisms within these looms are equally fascinating. The shedding mechanism, which separates the warp threads into two layers (the shed), is crucial for allowing the weft yarn to pass through. This is typically achieved using heddles or healds attached to harnesses that move up and down in a coordinated manner. The picking mechanism then inserts the weft yarn into this shed before the beat-up mechanism presses it firmly into place against the previously woven fabric. Additionally, modern looms often feature sophisticated control systems that allow for precise control over fabric density, pattern design, and yarn tension. These systems can be programmed to create complex patterns and textures, making it possible to produce a wide range of fabrics from simple plains to intricate jacquards. In summary, the weaving process is a harmonious blend of traditional craftsmanship and modern technology, with looms serving as the linchpin between raw materials and finished fabric. Understanding the various types of looms and their mechanisms provides insight into how different fabrics are created and highlights the ingenuity behind one of humanity's oldest yet most dynamic industries. Whether it's a handloom or an automated industrial loom, each plays a vital role in transforming yarns into woven fabric—a testament to human innovation and creativity.
Finishing Treatments for Woven Fabrics
Finishing treatments for woven fabrics are crucial steps in the textile manufacturing process, enhancing the fabric's performance, appearance, and durability. These treatments can significantly impact the final product's quality and usability. After weaving, fabrics often undergo various finishing processes to achieve desired properties such as softness, wrinkle resistance, water repellency, or flame retardancy. One common finishing treatment is **bleaching**, which involves using chemicals to remove natural pigments and impurities from the fabric, resulting in a brighter and more uniform color. **Dyeing** follows bleaching, where the fabric is immersed in dye baths to achieve the desired color. **Printing** is another method used to add patterns and designs onto the fabric using techniques like screen printing or digital printing. **Mechanical finishing** includes processes such as **napping**, which raises the fibers to create a soft, fuzzy surface, and **sanforizing**, which shrinks the fabric before it is cut and sewn to prevent further shrinkage. **Calendaring** involves passing the fabric through heated rollers to smooth and polish its surface, giving it a glossy finish. **Chemical finishing** treatments are also widely used. For example, **wrinkle resistance treatments** like permanent press or easy care involve applying chemicals that reduce fabric wrinkling. **Waterproofing** and **water repellency treatments** use coatings or membranes to prevent water penetration while allowing moisture vapor to escape, making the fabric breathable. **Flame retardant treatments** are applied to fabrics intended for use in environments where fire safety is critical. Additionally, **soil release treatments** make cleaning easier by allowing dirt and stains to be removed more efficiently. **Antimicrobial treatments** inhibit the growth of bacteria and fungi on the fabric, which is particularly important for fabrics used in medical applications or active wear. The choice of finishing treatment depends on the intended use of the fabric. For instance, fabrics destined for outdoor gear might undergo waterproofing and UV protection treatments, while those for bedding might be treated for softness and wrinkle resistance. Each treatment can significantly enhance the functionality and aesthetic appeal of woven fabrics, making them suitable for a wide range of applications from clothing and home textiles to industrial uses. In summary, finishing treatments are essential in transforming raw woven fabrics into high-quality products that meet specific performance criteria. By understanding these various treatments, manufacturers can tailor their fabrics to meet diverse consumer needs, ensuring that the final product is both functional and appealing. This attention to detail in the finishing process underscores the complexity and sophistication involved in creating woven fabrics that are both durable and visually appealing.
Applications and Benefits of Woven Fabric
Woven fabrics have been a cornerstone of human civilization, offering a myriad of applications that span across various industries. From the everyday clothing we wear to the upholstery that adorns our homes, woven fabrics play a pivotal role in our daily lives. Beyond these familiar uses, woven fabrics also find significant applications in technical textiles, where they are employed in industrial and medical settings due to their unique properties. Additionally, the sustainability and durability of woven fabrics make them an attractive choice for consumers and manufacturers alike, contributing to a more environmentally conscious future. This article will delve into these diverse applications, starting with the textile industry's use of woven fabrics in clothing, upholstery, and more, highlighting how these versatile materials continue to shape our world in multifaceted ways. --- **Textile Industry Uses: Clothing, Upholstery, and More**
Textile Industry Uses: Clothing, Upholstery, and More
The textile industry is a multifaceted sector that leverages woven fabric in a myriad of applications, each offering unique benefits and functionalities. At its core, woven fabric is a fundamental material in the production of clothing, which accounts for a significant portion of the industry's output. From casual wear to high-fashion garments, woven fabrics such as cotton, wool, and synthetic blends provide durability, comfort, and aesthetic appeal. The versatility of woven fabrics allows designers to create a wide range of clothing items, from lightweight summer dresses to heavy winter coats, catering to diverse consumer needs and preferences. Beyond clothing, woven fabrics play a crucial role in upholstery, enhancing both the functionality and aesthetics of furniture. Upholstery fabrics must withstand heavy use while maintaining their appearance and comfort. Woven fabrics like velvet, linen, and tweed are popular choices due to their strength, texture, and visual appeal. These materials not only provide durability but also contribute to the overall design and ambiance of a room, making them essential components in interior design. In addition to these primary uses, woven fabrics have numerous other applications that highlight their versatility and utility. In the automotive industry, woven fabrics are used for car seats and interior linings, ensuring both comfort and safety. Medical textiles, another significant area, utilize woven fabrics for surgical gowns, hospital bedding, and implantable devices due to their sterility, strength, and biocompatibility. Furthermore, woven fabrics are integral in industrial settings for producing filters, geotextiles, and technical textiles that serve various engineering purposes. The benefits of using woven fabrics across these applications are manifold. They offer superior strength and durability compared to non-woven or knitted fabrics, making them ideal for high-wear items. The weave pattern allows for excellent breathability, which is crucial in clothing and upholstery to prevent moisture buildup and ensure user comfort. Moreover, woven fabrics can be easily treated with finishes that enhance their performance characteristics, such as water resistance, flame retardancy, or antimicrobial properties. In terms of sustainability, many woven fabrics are made from natural fibers like cotton and wool, which are biodegradable and renewable resources. This aspect is increasingly important as consumers and manufacturers alike focus on reducing environmental impact. Additionally, the recyclability of some woven fabrics further contributes to a more circular economy within the textile industry. In conclusion, the textile industry's reliance on woven fabric is a testament to its versatility, durability, and wide-ranging applications. From everyday clothing and home furnishings to specialized industrial and medical uses, woven fabrics provide a combination of functionality, comfort, and aesthetic appeal that is hard to match with other materials. As technology continues to evolve and consumer demands shift towards sustainability and performance, the role of woven fabric in the textile industry remains pivotal and dynamic.
Technical Textiles: Industrial and Medical Applications
Technical textiles, often referred to as "technical fabrics," are specialized materials engineered for specific performance characteristics rather than aesthetic appeal. These advanced textiles have revolutionized various industries, particularly in industrial and medical applications, where their unique properties offer significant benefits. In industrial settings, technical textiles are crucial for enhancing efficiency, safety, and durability. For instance, geotextiles used in civil engineering projects such as road construction and landfill management provide stability and prevent soil erosion. Similarly, filtration textiles are employed in water treatment plants to remove impurities and contaminants from water, ensuring clean drinking water for communities. Protective clothing made from technical textiles like Kevlar and Nomex safeguard workers from hazardous conditions such as high temperatures and chemical exposure. Additionally, composites like carbon fiber and glass fiber reinforced polymers (FRP) are used in aerospace and automotive industries for their lightweight yet incredibly strong properties, contributing to fuel efficiency and structural integrity. In the medical field, technical textiles play a vital role in patient care and treatment. Medical implants such as vascular grafts and hernia meshes are made from biocompatible materials that integrate with the body's tissues without causing adverse reactions. Wound dressings and bandages infused with antimicrobial agents help prevent infection and promote faster healing. Surgical meshes used in procedures like hernia repair provide long-term support to weakened tissues. Furthermore, diagnostic textiles like biosensors can monitor vital signs continuously, offering real-time health data that aids in early diagnosis and treatment of diseases. The benefits of these technical textiles are multifaceted. They offer enhanced performance under extreme conditions, which is critical in both industrial and medical environments. Their durability extends the lifespan of products, reducing maintenance costs and the need for frequent replacements. Moreover, many technical textiles are designed with sustainability in mind; they can be recycled or biodegradable, contributing to a more environmentally friendly approach to manufacturing. In summary, technical textiles have transformed the way industries operate by providing solutions that are both functional and innovative. Their applications span from infrastructure development to healthcare advancements, underscoring their importance in modern technology. As research continues to push the boundaries of what these materials can achieve, it is clear that technical textiles will remain a cornerstone of industrial and medical progress for years to come.
Sustainability and Durability of Woven Fabrics
Sustainability and durability are paramount considerations in the realm of woven fabrics, as these attributes not only enhance the lifespan of the material but also contribute to a more environmentally conscious textile industry. Woven fabrics, by their very nature, offer a robust and long-lasting alternative to other types of fabrics. The interlacing of warp and weft threads creates a strong and stable fabric that can withstand wear and tear better than non-woven or knitted fabrics. This inherent durability means that woven fabrics require less frequent replacement, reducing the overall demand for new materials and thereby minimizing waste. From a sustainability perspective, woven fabrics can be made from a variety of eco-friendly materials such as organic cotton, hemp, and recycled polyester. Organic cotton, for instance, is grown without the use of synthetic pesticides or fertilizers, which reduces the environmental impact associated with conventional cotton farming. Hemp, another sustainable option, requires less water and pesticides compared to traditional crops and has natural UV resistance properties that enhance its durability. Recycled polyester, derived from post-consumer plastic waste like bottles, reduces the need for virgin raw materials and helps in closing the loop on textile waste. Moreover, the production process of woven fabrics can be optimized for sustainability. Techniques such as zero-waste design and upcycling can significantly reduce fabric scraps during manufacturing. Additionally, many textile manufacturers are adopting sustainable dyeing practices that use natural dyes or low-impact dyeing methods to minimize water pollution and chemical usage. The benefits of sustainable and durable woven fabrics extend beyond environmental considerations; they also offer economic advantages. Long-lasting fabrics reduce the need for frequent purchases, saving consumers money in the long run. Furthermore, high-quality woven fabrics can be repurposed or upcycled into new products at the end of their life cycle, extending their utility and reducing waste. In applications ranging from clothing to home textiles and industrial uses, the combination of sustainability and durability in woven fabrics is particularly valuable. For example, in the fashion industry, sustainable woven fabrics can help brands achieve their sustainability goals while maintaining product quality. In home textiles like upholstery and bedding, durable woven fabrics ensure longevity and comfort without compromising on style or functionality. In conclusion, the sustainability and durability of woven fabrics make them an attractive choice across various industries. By leveraging eco-friendly materials, optimizing production processes, and promoting long-lasting products, manufacturers can contribute to a more sustainable future while providing consumers with high-quality textiles that stand the test of time. This synergy between sustainability and durability underscores the significant role that woven fabrics play in fostering a more responsible and resilient textile ecosystem.