What Is Dtf Transfer

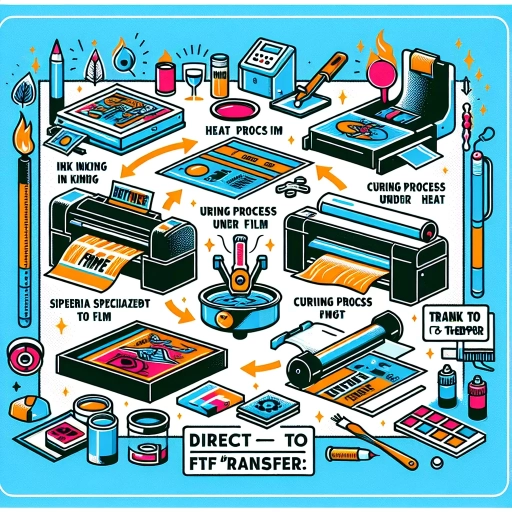
Direct-to-film (DTF) transfer is a revolutionary printing technology that has transformed the way we produce custom apparel and other fabric items. Unlike traditional methods, DTF transfer offers a versatile and efficient solution for creating high-quality, detailed designs on various fabrics. This article delves into the intricacies of DTF transfer, starting with an in-depth look at **Understanding DTF Transfer Technology**, where we explore the fundamental principles behind this innovative process. We will then examine **How DTF Transfer Works**, detailing the step-by-step process from design creation to application. Finally, we will discuss **Applications and Benefits of DTF Transfer**, highlighting its versatility, cost-effectiveness, and environmental advantages. By understanding these aspects, you will gain a comprehensive insight into why DTF transfer is becoming a preferred choice in the textile industry. Let's begin by diving into the core of this technology in **Understanding DTF Transfer Technology**.
Understanding DTF Transfer Technology
Understanding DTF (Direct-to-Film) transfer technology is crucial for anyone involved in the printing industry, particularly those interested in high-quality, durable, and versatile textile printing. This innovative method has revolutionized the way we produce custom apparel and other fabric items. To fully grasp the intricacies of DTF transfer, it is essential to delve into its core components. First, we need to understand the **Definition and Basics of DTF Transfer**, which explains the fundamental principles and processes involved in this technology. Next, exploring the **History and Evolution of DTF Printing** provides valuable insights into how this technology has developed over time, highlighting key milestones and advancements. Finally, examining the **Key Components of the DTF Transfer Process** reveals the critical elements that make this technology effective, from the film itself to the necessary equipment and materials. By starting with a clear understanding of the basics, we can appreciate the full scope of DTF transfer technology and its significant impact on modern printing practices. Therefore, let us begin by defining and exploring the basics of DTF transfer.
Definition and Basics of DTF Transfer
**Definition and Basics of DTF Transfer** Direct-to-Film (DTF) transfer is a versatile and innovative printing technology that has revolutionized the textile industry by offering a flexible, high-quality, and cost-effective method for customizing fabrics. Unlike traditional screen printing or direct-to-garment (DTG) printing, DTF transfer involves printing designs onto a special heat transfer film rather than directly onto the fabric. This process allows for greater versatility in terms of fabric types and design complexity. At its core, DTF transfer involves several key components: a printer, special DTF ink, a heat press, and the DTF transfer film itself. The process begins with the design being printed onto the transfer film using a printer loaded with DTF ink. This ink is specifically formulated to adhere well to various fabric types without compromising the softness or texture of the material. Once printed, the film is then coated with a hot melt powder that acts as an adhesive when heated. The next step involves placing the printed film on top of the desired fabric and applying heat and pressure using a heat press. The heat melts the adhesive powder, causing it to bond securely with the fabric. After cooling, the excess film is peeled away, leaving behind a vibrant and durable design that is resistant to fading and wear. One of the significant advantages of DTF transfer is its compatibility with a wide range of fabrics, including cotton, polyester, blends, and even stretchy materials like spandex. This makes it particularly appealing for custom apparel such as t-shirts, hoodies, athletic wear, and more. Additionally, DTF transfer does not require pre-treatment of fabrics or post-treatment processes like curing ovens, making it more straightforward and less labor-intensive compared to other methods. The technology also supports full-color prints with intricate details and gradients without the need for multiple screens or plates. This makes it ideal for complex designs and small to medium-sized production runs where flexibility and speed are crucial. Furthermore, DTF transfer maintains fabric softness and breathability, ensuring that the finished product feels comfortable against the skin. In summary, DTF transfer technology offers a robust solution for textile customization by combining ease of use, versatility in fabric compatibility, and high-quality print results. Its ability to handle intricate designs on various fabric types without compromising comfort makes it an essential tool in modern textile printing. Whether you are a small business owner looking to offer custom apparel or an individual seeking unique personalized items, understanding the basics of DTF transfer can open up new possibilities in textile customization.
History and Evolution of DTF Printing
The history and evolution of Direct-to-Film (DTF) printing are closely tied to advancements in digital printing technology and the demand for versatile, high-quality textile transfers. **Early Beginnings:** The concept of DTF printing emerged in the early 2000s as a response to the limitations of traditional heat transfer methods. Initially, it was seen as a niche technology, primarily used by small-scale printers and hobbyists. **Technological Advancements:** The real breakthrough came with the development of advanced inkjet printers capable of printing directly onto a special film. This film, coated with a heat-activated adhesive, allowed for the transfer of detailed images onto various fabrics without the need for additional layers or intermediaries. **Mid-2000s to 2010s:** As digital printing technology improved, so did the quality and efficiency of DTF printing. The introduction of high-resolution inkjet heads and specialized inks enhanced color vibrancy and durability. This period also saw the rise of automated cutting machines, which streamlined the process by accurately cutting out printed designs, reducing waste and labor time. **Modern Era:** By the 2010s, DTF printing had become a mainstream method in the textile industry. The advent of more affordable and user-friendly DTF printers made it accessible to a broader range of businesses, from small custom apparel shops to large-scale manufacturers. This accessibility was further amplified by online platforms offering DTF supplies and tutorials, democratizing the technology. **Key Innovations:** Several key innovations have driven the evolution of DTF printing. One significant development is the improvement in adhesive formulations, which now offer better durability and wash resistance. Another crucial advancement is the introduction of eco-friendly inks that meet stringent environmental standards without compromising on quality. **Market Expansion:** Today, DTF printing is used across various sectors, including custom apparel, promotional products, and even industrial applications. Its versatility in printing on different fabric types, including cotton, polyester, and blends, has made it a preferred choice for many businesses. The ability to produce small to large quantities efficiently has also made DTF an attractive option for both niche markets and mass production. **Future Outlook:** As technology continues to advance, we can expect further improvements in print resolution, ink durability, and environmental sustainability. The integration of AI and automation is likely to enhance production efficiency and reduce costs. Additionally, ongoing research into new materials and adhesives will expand the range of substrates that can be printed on using DTF technology. In summary, the history and evolution of DTF printing reflect a journey from niche technology to mainstream industry standard. Driven by technological advancements and market demand, DTF has become an indispensable tool for anyone looking to create high-quality textile transfers efficiently and effectively.
Key Components of DTF Transfer Process
The DTF (Direct-to-Film) transfer process is a versatile and efficient method for customizing apparel, accessories, and other materials with intricate designs. At its core, the DTF transfer process involves several key components that ensure high-quality results. 1. **DTF Film**: This is the primary material used in the process. The film is coated with a special adhesive that allows it to bond well with various fabrics. It comes in different thicknesses and types, each suited for specific applications. 2. **Ink**: The ink used in DTF printing is specially formulated to adhere well to the film and subsequently to the fabric. These inks are typically water-based or solvent-based, depending on the desired finish and durability. 3. **Printer**: A high-resolution printer, often an inkjet printer, is necessary for printing the design onto the DTF film. The printer must be capable of producing detailed images with vibrant colors. 4. **Cutter**: After printing, the design needs to be cut out from the film. This can be done manually or using an automated cutting plotter for precision and efficiency. 5. **Heat Press**: The heat press is crucial for transferring the printed design from the film onto the fabric. It applies heat and pressure to ensure a strong bond between the adhesive on the film and the fabric. 6. **Temperature and Pressure Settings**: Proper temperature and pressure settings are essential for a successful transfer. The ideal settings vary depending on the type of fabric and film used but generally range between 150°C to 200°C (302°F to 392°F) and 2-4 bar of pressure. 7. **Transfer Time**: The duration for which the heat press is applied also plays a critical role. Typically, this ranges from 10 to 20 seconds, though it may vary based on specific requirements. 8. **Peeling Method**: After the transfer process, the film is peeled off, revealing the design on the fabric. There are two common peeling methods: hot peel and cold peel, each offering different advantages in terms of finish and durability. 9. **Post-Transfer Care**: To ensure longevity of the transferred design, proper care instructions should be followed. This includes washing inside out, avoiding bleach, and drying on a low heat setting. By understanding these key components and their roles within the DTF transfer process, users can achieve professional-grade results with minimal effort, making it an attractive option for both small-scale hobbyists and large-scale commercial operations.
How DTF Transfer Works
Direct-to-Film (DTF) transfer printing is a versatile and efficient method for producing high-quality, custom designs on various fabrics. This innovative technique has gained popularity due to its ease of use, durability, and wide range of applications. To fully understand the process, it is essential to delve into the key components and steps involved. Firstly, the **Step-by-Step Guide to the DTF Printing Process** will walk you through each stage, from preparing the design to applying the transfer onto the fabric. This detailed guide ensures that you grasp the technical aspects and can replicate the process effectively. Additionally, the **Role of Adhesive and Transfer Film in DTF** highlights the critical role these components play in ensuring a successful transfer. Understanding how these elements interact is crucial for achieving optimal results. Lastly, a **Comparison with Other Printing Technologies** will provide insight into how DTF stands out from other methods, such as screen printing and sublimation. This comparison will help you make informed decisions about which printing method best suits your needs. By exploring these aspects, you will gain a comprehensive understanding of how DTF transfer works. Let's begin with the **Step-by-Step Guide to the DTF Printing Process** to see how this technology comes to life.
Step-by-Step Guide to the DTF Printing Process
The DTF (Direct-to-Film) printing process is a versatile and efficient method for creating custom transfers that can be applied to various fabrics, including cotton, polyester, and blends. Here’s a step-by-step guide to understanding how DTF printing works: 1. **Preparation**: Begin by preparing your design using graphic design software. Ensure the design is mirrored since it will be printed in reverse on the film. 2. **Printing**: Use a specialized DTF printer to print your design onto a heat transfer film. This film is coated with a special adhesive that allows it to bond well with fabrics. 3. **Curing**: After printing, the film needs to be cured in a drying tunnel or with a heat gun to fix the ink and prevent smudging. 4. **Weeding**: Remove the excess film around the design, leaving only the printed area. This step is crucial for ensuring clean and precise transfers. 5. **Application of Adhesive Powder**: Apply a layer of adhesive powder over the printed design. This powder helps in bonding the film to the fabric during the heat press process. 6. **Heat Pressing**: Place the powder-coated film onto your fabric, ensuring it is centered and smooth. Use a heat press machine to apply high pressure and temperature (usually around 300°F for 10-15 seconds) to bond the film to the fabric. 7. **Peeling**: After the heat press cycle is complete, allow the transfer to cool slightly before peeling off the carrier film. The design should now be securely bonded to the fabric. 8. **Finishing**: Inspect the transfer for any imperfections and wash the garment according to the manufacturer’s instructions to ensure durability. This step-by-step guide highlights the key stages involved in creating and applying DTF transfers, making it an invaluable resource for anyone looking to understand how DTF transfer works and how to implement it effectively. By following these steps meticulously, you can achieve high-quality, long-lasting prints on various fabrics, making DTF printing a preferred choice for custom apparel and promotional products.
Role of Adhesive and Transfer Film in DTF
In the process of Direct-to-Film (DTF) transfer, adhesives and transfer films play crucial roles that are integral to the overall success of the printing technique. The adhesive, typically a specialized hot melt or pressure-sensitive adhesive, is applied to the film after the ink has been printed. This adhesive layer is designed to bond well with various fabrics, ensuring that the printed design adheres securely once transferred. The quality of the adhesive directly impacts the durability and longevity of the transferred image; a good adhesive ensures that the design remains vibrant and intact even after multiple washes and wear. The transfer film itself serves as a carrier for both the ink and the adhesive. It is usually a thin, flexible material that can be easily handled during the printing and transfer process. The film must have properties that allow it to release the ink and adhesive smoothly onto the fabric without leaving any residue or affecting the image quality. In DTF printing, this film is typically coated with a release agent to facilitate this smooth release. During the transfer process, heat and pressure are applied to the film, causing the adhesive to melt and bond with the fabric. Once cooled, the film is peeled away, leaving behind a crisp, detailed image on the fabric. The combination of a high-quality adhesive and an appropriate transfer film ensures that this process is efficient and results in a professional-grade finish. Moreover, advancements in adhesive technology have expanded the versatility of DTF transfers, allowing them to be used on a wide range of fabrics including cotton, polyester, and blends. This versatility makes DTF an attractive option for various applications such as custom apparel, promotional products, and textile decorations. In summary, adhesives and transfer films are essential components in DTF transfer technology. They work in tandem to ensure that printed designs are transferred accurately and durably onto fabrics. The quality of these materials directly influences the final product's appearance and longevity, making them critical factors in achieving successful DTF transfers.
Comparison with Other Printing Technologies
When comparing DTF (Direct-to-Film) transfer technology with other printing technologies, several key differences and advantages emerge. Unlike traditional screen printing, which requires a significant setup process and is often cost-effective only for large quantities, DTF transfer allows for small to medium-sized print runs without the need for extensive preparation. This flexibility makes DTF ideal for custom orders and niche markets. In contrast to sublimation printing, which is limited to polyester fabrics and requires a heat press to transfer the design, DTF transfers can be applied to a wide range of fabrics including cotton, polyester, and blends. This versatility is a significant advantage as it opens up more possibilities for apparel and textile customization. DTF transfer also stands out from direct-to-garment (DTG) printing in terms of durability and ease of application. DTG printing involves directly printing ink onto the fabric using inkjet technology, which can be time-consuming and may not be as durable as DTF transfers. DTF transfers, on the other hand, are applied using a heat press, ensuring a long-lasting finish that withstands washing and wear. Another technology often compared to DTF is heat transfer vinyl (HTV). While HTV is popular for its ease of use and quick application time, it typically has a more rigid feel compared to DTF transfers. DTF transfers offer a softer, more flexible finish that integrates seamlessly with the fabric, making them more comfortable to wear. Additionally, DTF transfers do not require the use of specialized inks or printers like some other technologies do. The process involves printing onto a special film that is then applied to the fabric, making it accessible to a broader range of users without the need for expensive equipment. Overall, DTF transfer technology offers a unique combination of flexibility, durability, and versatility that sets it apart from other printing methods. Its ability to handle small print runs, work with various fabrics, and provide a comfortable finish makes it an attractive option for those looking to customize apparel and textiles efficiently and effectively.
Applications and Benefits of DTF Transfer
Direct-to-film (DTF) transfer technology has revolutionized the way various industries approach custom apparel and product decoration. This innovative method offers a multitude of applications and benefits, making it a preferred choice over traditional methods. In this article, we will delve into the common uses of DTF transfer in various industries, highlighting its versatility and widespread adoption. We will also explore the advantages DTF transfer holds over traditional screen printing methods, including its ease of use, flexibility, and high-quality results. Additionally, we will discuss the cost-effectiveness and durability of DTF transfers, which contribute significantly to their popularity. By understanding these aspects, it becomes clear why DTF transfer is becoming the go-to solution for many businesses. Let's start by examining the common uses of DTF transfer in various industries, where its impact is most evident.
Common Uses of DTF Transfer in Various Industries
Direct-to-Film (DTF) transfer technology has revolutionized various industries with its versatility and efficiency. In the **apparel industry**, DTF transfers are widely used for custom t-shirt printing, allowing for intricate designs and vibrant colors on a variety of fabrics, including cotton, polyester, and blends. This method is particularly favored for its ease of use and cost-effectiveness, making it ideal for small to medium-sized businesses and start-ups. In **promotional products**, DTF transfers enable the creation of customized items such as hats, bags, and accessories with high-resolution graphics. This is especially beneficial for marketing campaigns where unique and eye-catching designs are crucial. The durability of DTF transfers ensures that the printed images remain intact even after multiple washes and uses. The **sports industry** also leverages DTF transfers to produce custom jerseys, uniforms, and other athletic wear. The ability to print detailed logos, numbers, and names makes it a go-to solution for both professional and amateur teams. Additionally, DTF transfers are used in **event merchandise**, such as festival tees and concert apparel, where quick turnaround times are essential. In **crafting and hobby projects**, DTF transfers offer a user-friendly way to add personalized designs to various materials like fabric, wood, and even ceramics. Crafters can create unique gifts or decorative items with minimal equipment and expertise. This versatility extends into **educational settings** where students can engage in creative projects that combine art and technology. Moreover, **healthcare and medical industries** utilize DTF transfers for creating custom scrubs, lab coats, and other medical attire with specific logos or identifiers. The hygiene and durability requirements of these garments are met by the high-quality finish of DTF prints. Lastly, in **automotive and industrial sectors**, DTF transfers are applied to produce custom labels, decals, and signage that withstand harsh environments. These transfers are resistant to chemicals, UV light, and abrasion, making them suitable for use on vehicles, machinery, and other industrial equipment. Overall, the common uses of DTF transfer across various industries highlight its adaptability, cost-effectiveness, and high-quality output, making it an indispensable tool for both commercial and personal applications.
Advantages Over Traditional Screen Printing Methods
DTF (Direct-to-Film) transfer offers several significant advantages over traditional screen printing methods, making it a preferred choice for many applications. One of the primary benefits is **versatility**; DTF transfers can be applied to a wide range of fabrics, including cotton, polyester, and blends, without the need for specific fabric preparation. This flexibility is particularly valuable in the apparel industry where diverse materials are commonly used. Another key advantage is **cost-effectiveness**. Unlike traditional screen printing, which requires a minimum order quantity and involves high setup costs due to the need for screens, DTF transfers can be produced in small quantities with minimal upfront costs. This makes it an ideal solution for small businesses, custom orders, and promotional products. **Speed and efficiency** are also notable advantages. With DTF transfers, the production process is significantly faster compared to screen printing. The transfers can be printed quickly using digital printers, and the application process is straightforward, involving just heat and pressure. This rapid turnaround time allows businesses to meet tight deadlines and respond quickly to market demands. Additionally, **detail and precision** are enhanced with DTF transfers. Digital printing technology allows for intricate designs and fine details that may be challenging or impossible to achieve with traditional screen printing methods. This makes DTF transfers particularly suitable for complex designs and small text. The **environmental impact** is another area where DTF transfers excel. Unlike screen printing, which often involves chemical-based inks and solvents, DTF transfers use eco-friendly inks that are safer for both the environment and the wearer. This aligns well with the growing consumer demand for sustainable products. Furthermore, **durability** is a significant advantage of DTF transfers. These transfers are designed to withstand multiple washes without fading or peeling, ensuring that the printed design remains vibrant and intact over time. This durability makes them suitable for a variety of applications, from casual wear to athletic apparel. In terms of **ease of use**, DTF transfers are user-friendly and do not require specialized skills or equipment beyond a heat press. This accessibility makes it possible for businesses and individuals to produce high-quality prints without extensive training or investment in complex machinery. Overall, the advantages of DTF transfers over traditional screen printing methods include versatility, cost-effectiveness, speed, precision, environmental sustainability, durability, and ease of use. These benefits make DTF transfers an attractive option for various applications in the apparel and promotional products industries.
Cost-Effectiveness and Durability of DTF Transfers
The cost-effectiveness and durability of Direct-to-Film (DTF) transfers are pivotal factors that contribute to their widespread adoption in various industries. From a financial perspective, DTF transfers offer a more economical solution compared to traditional screen printing methods, especially for small to medium-sized orders. The initial setup costs for DTF printing are lower, as it does not require the creation of screens or plates, which can be expensive and time-consuming. Additionally, the ink and film used in DTF printing are relatively affordable, making it an attractive option for businesses looking to minimize overhead costs without compromising on quality. In terms of durability, DTF transfers excel due to their robust construction and adherence properties. Once applied, these transfers exhibit excellent resistance to wear and tear, ensuring that the printed designs remain vibrant and intact even after multiple washes and uses. The polyurethane-based adhesive used in DTF transfers provides a strong bond between the film and the fabric, preventing peeling or cracking over time. This makes them ideal for applications such as custom apparel, promotional items, and industrial textiles where longevity is crucial. Furthermore, the flexibility of DTF transfers allows them to stretch without losing their integrity, making them suitable for a wide range of fabrics including cotton, polyester, and blends. Overall, the combination of cost-effectiveness and durability makes DTF transfers a highly sought-after solution for businesses seeking reliable and efficient printing methods.