What Is Tyvek

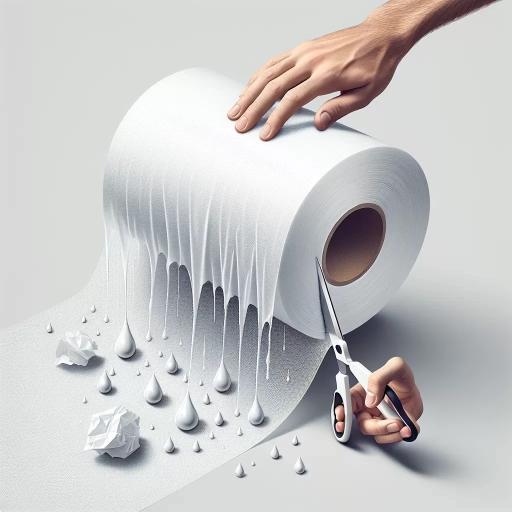
Tyvek, a synthetic material developed by DuPont, has revolutionized various industries with its unique properties and versatile applications. Known for its durability, water resistance, and breathability, Tyvek has become a staple in construction, packaging, and even fashion. This article delves into the multifaceted world of Tyvek, exploring its origins, technical aspects, and practical uses. We will begin by introducing Tyvek, tracing its history and the science behind its creation. Next, we will delve into the technical aspects of Tyvek, examining its composition and the manufacturing process that makes it so resilient. Finally, we will discuss the practical uses and benefits of Tyvek, highlighting its impact on different sectors and why it remains a preferred choice for many professionals. By understanding these facets, readers will gain a comprehensive insight into what makes Tyvek such an invaluable material. Let us start our journey into the world of Tyvek with an **Introduction to Tyvek**.
Introduction to Tyvek
Tyvek, a synthetic material known for its durability and versatility, has become a staple in various industries since its inception. This high-quality, informative, and engaging article delves into the multifaceted world of Tyvek, exploring its history, properties, and applications. We begin by tracing the **History and Development of Tyvek**, uncovering the origins of this innovative material and the milestones that have shaped its evolution. Next, we examine the **Basic Properties and Characteristics** that make Tyvek so unique, including its water resistance, breathability, and strength. Finally, we explore the **Common Applications and Uses** of Tyvek, from construction and medical packaging to fashion and art. By understanding these aspects, readers will gain a comprehensive insight into why Tyvek remains a preferred choice across diverse sectors. Let us start our journey through the fascinating history of Tyvek, which sets the stage for its widespread adoption and enduring relevance.
History and Development of Tyvek
The history and development of Tyvek, a synthetic material renowned for its unique properties, trace back to the 1950s when chemist Ray McIntire at DuPont discovered a new type of polyethylene fiber. Initially, McIntire was experimenting with a polymer solution that he accidentally discovered could be spun into fibers. This serendipitous discovery led to the creation of Tyvek, a name derived from the words "ty" (a prefix indicating a new type of material) and "vek" (a suffix suggesting strength and durability). In the early 1960s, DuPont began to develop Tyvek further, recognizing its potential due to its lightweight, yet incredibly strong and durable nature. The material was first introduced commercially in 1967 as a wrapping material for buildings to provide weatherproofing and insulation. Its use quickly expanded beyond construction to various industries such as packaging, medical devices, and even clothing. One of the key factors that contributed to Tyvek's widespread adoption was its unique combination of properties: it is waterproof, breathable, and resistant to chemicals and abrasion. These characteristics made it an ideal material for applications where both protection and flexibility were crucial. For instance, in the medical field, Tyvek is used in surgical gowns and drapes because it provides a barrier against bacteria while allowing moisture vapor to escape. Throughout the 1970s and 1980s, DuPont continued to innovate with Tyvek, introducing new forms such as Tyvek envelopes and mailing bags that capitalized on its lightweight yet robust nature. These products revolutionized the postal industry by offering a durable alternative to traditional paper envelopes. In recent years, Tyvek has seen further advancements with the development of specialized grades tailored for specific applications. For example, Tyvek 40L is designed for use in medical packaging where sterility is paramount, while Tyvek 1073B is optimized for construction wraps due to its enhanced tear resistance. The versatility of Tyvek has also led to its adoption in fashion and art. Designers have incorporated Tyvek into clothing lines due to its unique texture and durability. Additionally, artists have used Tyvek as a medium for creating sculptures and other forms of art that benefit from its malleable yet resilient properties. Today, Tyvek remains a cornerstone product for DuPont, with its applications spanning across multiple sectors including construction, healthcare, packaging, and even consumer goods. Its enduring popularity is a testament to the innovative spirit of Ray McIntire and the continuous research and development efforts by DuPont over the decades. As technology continues to evolve, it is likely that Tyvek will remain at the forefront of material science innovation, offering solutions that combine strength, durability, and versatility in ways that few other materials can match.
Basic Properties and Characteristics
Tyvek, a synthetic material developed by DuPont, boasts a unique set of basic properties and characteristics that make it highly versatile and widely used across various industries. At its core, Tyvek is a nonwoven fabric made from high-density polyethylene fibers. This composition gives Tyvek its remarkable strength-to-weight ratio, allowing it to be both lightweight and incredibly durable. One of the most distinctive features of Tyvek is its impermeability to water and air, yet it remains breathable due to its microporous structure. This balance of impermeability and breathability makes Tyvek an ideal material for applications requiring protection against moisture and wind while allowing for moisture vapor transmission. Another key characteristic of Tyvek is its resistance to chemicals, UV light, and extreme temperatures. It can withstand exposure to a wide range of chemicals without degrading, making it suitable for use in hazardous environments. Additionally, Tyvek's UV resistance ensures that it does not break down when exposed to sunlight, maintaining its integrity over time. Its thermal stability allows it to perform well in both high and low temperatures, further expanding its utility. The physical properties of Tyvek also include high tensile strength and tear resistance, which contribute to its durability and longevity. These attributes make Tyvek an excellent choice for packaging materials, construction wraps, and protective clothing. Furthermore, Tyvek is easy to clean and maintain; it can be washed or sterilized without losing its structural integrity. From an environmental perspective, Tyvek is recyclable and can be reused in various forms. This eco-friendly aspect aligns with modern sustainability goals and reduces waste. The material's non-toxic nature ensures that it does not pose health risks during use or disposal. In terms of aesthetics and functionality, Tyvek can be printed upon using standard inkjet or screen printing techniques, making it a popular choice for banners, signs, and other promotional materials. Its smooth surface finish also makes it suitable for various graphic applications. Overall, the combination of strength, durability, impermeability, breathability, chemical resistance, UV stability, and recyclability makes Tyvek a highly versatile material with a wide range of applications. Whether used in construction, packaging, medical devices, or graphic arts, Tyvek's unique properties ensure that it performs reliably under diverse conditions. This multifaceted nature has cemented Tyvek's place as a go-to material in numerous industries, highlighting its value as a reliable and innovative solution for various needs.
Common Applications and Uses
Tyvek, a versatile and innovative material developed by DuPont, has found its way into a myriad of applications across various industries due to its unique properties. One of the most significant uses of Tyvek is in the construction industry, where it serves as a durable and breathable house wrap. This application helps to prevent air leaks and moisture intrusion, thereby enhancing the energy efficiency and structural integrity of buildings. Additionally, Tyvek is widely used in the medical field for its sterility and resistance to chemicals, making it an ideal material for packaging medical instruments and supplies. Its impermeability to water yet breathability to vapor makes it a preferred choice for surgical gowns and drapes, ensuring both protection and comfort for healthcare professionals. In the realm of packaging, Tyvek's strength, tear resistance, and light weight make it an excellent material for shipping envelopes and bags. These properties ensure that contents are well-protected during transit while minimizing shipping costs due to reduced weight. The material's chemical resistance also makes it suitable for packaging hazardous materials safely. Furthermore, Tyvek's durability and resistance to UV degradation have led to its adoption in outdoor applications such as banners, signs, and even protective covers for outdoor furniture. The textile industry also leverages Tyvek's unique characteristics by incorporating it into clothing and gear designed for extreme conditions. For instance, Tyvek jackets and pants are popular among workers in hazardous environments due to their protective qualities against chemicals and abrasion. Similarly, outdoor enthusiasts appreciate Tyvek's use in camping gear like ground cloths and emergency blankets because of its lightweight yet robust nature. In addition to these practical applications, Tyvek has also found a niche in the art world. Its smooth surface and durability make it an attractive medium for artists who create murals or other large-scale installations that need to withstand various environmental conditions. Moreover, Tyvek's recyclability aligns with the growing demand for sustainable materials across all sectors. Overall, Tyvek's versatility stems from its combination of strength, breathability, chemical resistance, and light weight. These attributes have enabled it to become a go-to material in diverse fields ranging from construction and healthcare to packaging and art. As technology continues to evolve, it is likely that new and innovative applications of Tyvek will emerge, further solidifying its place as a cornerstone material in modern industry.
Technical Aspects of Tyvek
Tyvek, a synthetic material renowned for its versatility and durability, is a staple in various industries ranging from construction to medical packaging. To fully appreciate the capabilities of Tyvek, it is essential to delve into its technical aspects. This article will explore three critical dimensions: the material composition and manufacturing process, its physical and chemical properties, and its performance in various environmental conditions. Understanding the material composition and manufacturing process of Tyvek provides a foundational insight into its inherent strengths and limitations. This knowledge is crucial for determining its suitability for different applications. Additionally, examining the physical and chemical properties of Tyvek reveals how it withstands different environmental stresses, such as temperature fluctuations, moisture exposure, and chemical resistance. Finally, evaluating its performance in various environmental conditions helps in predicting its longevity and reliability across diverse settings. By examining these technical aspects, we can better harness the potential of Tyvek in our daily applications. Let us begin by exploring the material composition and manufacturing process that underpins the unique characteristics of Tyvek.
Material Composition and Manufacturing Process
**Material Composition and Manufacturing Process** Tyvek, a synthetic material developed by DuPont, is renowned for its unique properties and versatile applications. At its core, Tyvek is composed of high-density polyethylene (HDPE) fibers that are extruded and then randomly laid down to create a non-woven fabric. This distinct composition gives Tyvek its exceptional strength, durability, and resistance to water, chemicals, and UV light. The manufacturing process of Tyvek involves several critical steps. Initially, HDPE resin is melted and extruded through a spinneret to form long, thin fibers. These fibers are then stretched and aligned in a specific manner to enhance their tensile strength. The next step involves the use of a flash-spinning process, where the fibers are rapidly cooled and solidified, resulting in a web-like structure. This web is subsequently compressed and bonded using heat and pressure to create the final non-woven fabric. One of the key factors contributing to Tyvek's performance is its unique fiber structure. The flash-spinning process creates fibers with a high degree of crystallinity, which enhances their mechanical properties. Additionally, the random orientation of these fibers within the fabric ensures that Tyvek exhibits isotropic strength, meaning it has equal strength in all directions. This isotropy is crucial for applications where consistent performance is essential. The manufacturing process also allows for various treatments and finishes to be applied to the Tyvek fabric, further expanding its utility. For instance, Tyvek can be treated with additives to improve its resistance to specific chemicals or to enhance its UV stability. These treatments make Tyvek suitable for a wide range of applications, from medical packaging and construction materials to protective clothing and envelopes. In summary, the material composition and manufacturing process of Tyvek are integral to its technical aspects. The combination of HDPE fibers, flash-spinning technology, and careful processing steps results in a material that is both robust and versatile. Understanding these elements is essential for appreciating the full potential of Tyvek and its diverse applications across various industries.
Physical and Chemical Properties
When delving into the technical aspects of Tyvek, it is crucial to understand its physical and chemical properties, which underpin its unique performance characteristics. Tyvek, a synthetic material produced by DuPont, is known for its exceptional durability, versatility, and resistance to various environmental factors. Physically, Tyvek is a non-woven fabric made from high-density polyethylene fibers that are randomly arranged to create a strong yet lightweight material. This non-woven structure contributes to its high tensile strength, tear resistance, and puncture resistance, making it an ideal choice for applications such as construction wraps, medical packaging, and protective clothing. Chemically, Tyvek's polyethylene composition provides inherent resistance to chemicals, moisture, and UV light. The material is hydrophobic, meaning it repels water and does not absorb moisture, which is particularly beneficial in applications where dryness is critical. Additionally, Tyvek's chemical inertness ensures that it does not react with most substances, maintaining its integrity even when exposed to harsh chemicals or extreme temperatures. This property is especially valuable in medical settings where sterility and contamination control are paramount. The physical properties of Tyvek also include its breathability and vapor permeability. Unlike many other synthetic materials, Tyvek allows moisture vapor to pass through while keeping liquid water out, a characteristic known as "breathable waterproofing." This feature makes it suitable for use in building envelopes where moisture management is essential to prevent mold and structural damage. Furthermore, Tyvek's low thermal conductivity helps in reducing heat transfer, contributing to energy efficiency in buildings. From a chemical standpoint, the stability of Tyvek under various conditions is noteworthy. It retains its physical properties over a wide temperature range and does not degrade when exposed to sunlight or ozone. This stability ensures that Tyvek maintains its performance over time, even in harsh outdoor environments. The material's resistance to microbial growth adds another layer of durability, as it does not support the growth of mold or mildew. In summary, the physical and chemical properties of Tyvek—its strength, water resistance, breathability, chemical inertness, and stability—make it a highly versatile material with a wide range of applications. These properties are fundamental to understanding why Tyvek is chosen for demanding tasks across industries such as construction, healthcare, and packaging. By leveraging these attributes, Tyvek continues to be a reliable solution for applications requiring durability, performance, and reliability under diverse conditions.
Performance in Various Environmental Conditions
Performance in various environmental conditions is a critical aspect of Tyvek's technical profile, showcasing its versatility and reliability across diverse settings. Tyvek, a synthetic material made from high-density polyethylene fibers, exhibits exceptional durability and resistance to environmental factors. In extreme temperatures, Tyvek maintains its structural integrity, performing well in both hot and cold conditions. It retains its strength and flexibility even when exposed to temperatures ranging from -40°C to 120°C, making it an ideal choice for applications in harsh climates. Humidity and moisture also pose no significant threat to Tyvek's performance. Unlike natural fibers that can degrade or become brittle when exposed to water, Tyvek is inherently hydrophobic and does not absorb moisture. This property ensures that it remains lightweight and retains its insulating properties even in wet conditions, making it suitable for use in construction, packaging, and protective clothing. Chemical resistance is another key attribute of Tyvek. It is non-reactive with most chemicals and can withstand exposure to acids, bases, and solvents without compromising its integrity. This makes Tyvek an excellent material for use in chemical processing, pharmaceuticals, and other industries where chemical exposure is a concern. In addition to its chemical and moisture resistance, Tyvek also offers superior UV stability. Unlike many synthetic materials that degrade under prolonged exposure to ultraviolet light, Tyvek retains its color and physical properties over time. This stability ensures that products made from Tyvek remain functional and aesthetically pleasing even after extended outdoor use. Wind and weather conditions also do not affect Tyvek's performance significantly. Its tight weave and dense fiber structure provide excellent wind resistance, making it a popular choice for outdoor applications such as banners, signs, and protective coverings. Moreover, Tyvek's smooth surface prevents the buildup of snow and ice, reducing the risk of structural damage during winter months. The material's performance is further enhanced by its ability to resist biological degradation. Unlike natural fibers that can be susceptible to mold, mildew, or insect damage, Tyvek is resistant to biological attack. This ensures that products made from Tyvek remain durable and long-lasting without the need for additional treatments or preservatives. In summary, Tyvek's performance in various environmental conditions underscores its robustness and adaptability. Whether exposed to extreme temperatures, moisture, chemicals, UV light, wind, or biological agents, Tyvek consistently demonstrates superior durability and reliability. These attributes make it an invaluable material across a wide range of industries and applications where performance under diverse conditions is paramount.
Practical Uses and Benefits of Tyvek
Tyvek, a synthetic material known for its durability and versatility, has a wide range of practical uses that benefit various industries. This article delves into the multifaceted applications of Tyvek, highlighting its significance in construction and building insulation, medical and healthcare settings, and other industrial and consumer uses. In the realm of construction, Tyvek serves as an essential component in building envelopes, providing superior weather resistance and thermal insulation. Its ability to prevent air leaks while allowing moisture vapor to escape makes it a crucial element in maintaining energy efficiency and structural integrity. Moving beyond construction, Tyvek also plays a vital role in medical and healthcare applications, where its sterility and resistance to chemicals are paramount. Additionally, its use extends to other industrial and consumer sectors, where its unique properties make it an ideal material for various products. By exploring these diverse applications, we can fully appreciate the value and benefits that Tyvek brings to different fields. Let us begin by examining its critical role in construction and building insulation.
Construction and Building Insulation
Construction and building insulation are crucial components in modern architecture, significantly impacting the energy efficiency, comfort, and durability of structures. Insulation serves multiple purposes: it reduces heat transfer between the interior and exterior of a building, thereby minimizing energy consumption for heating and cooling; it enhances soundproofing by dampening external noise; and it protects against moisture, which can lead to structural damage and mold growth. In the context of practical uses and benefits of Tyvek, this synthetic material stands out as a versatile and effective insulation solution. Tyvek, a brand of flashspun high-density polyethylene fibers, is renowned for its unique properties that make it an ideal choice for various insulation applications. Its primary function is as a weather barrier, preventing water and air infiltration while allowing moisture vapor to escape. This dual capability ensures that buildings remain dry and well-ventilated, reducing the risk of mold and rot. When used in conjunction with other insulation materials like fiberglass or foam, Tyvek enhances their performance by providing an additional layer of protection against environmental elements. One of the key benefits of Tyvek in construction is its ease of installation. It can be easily wrapped around the exterior of a building before the installation of siding, making it a straightforward process for contractors. Additionally, Tyvek is highly durable and resistant to tears and punctures, ensuring long-term performance without significant maintenance. This durability also extends to its resistance against UV rays, chemicals, and pests, further enhancing its lifespan. From an energy efficiency perspective, Tyvek plays a critical role in reducing thermal bridging—areas where heat can escape through gaps in the building envelope. By creating a continuous barrier around the structure, Tyvek helps maintain consistent indoor temperatures, reducing the need for excessive heating or cooling. This not only lowers energy bills but also contributes to a more sustainable building practice. Moreover, Tyvek's breathability is a significant advantage in preventing moisture buildup within walls. Unlike traditional plastic wraps that trap moisture, Tyvek allows water vapor to escape while keeping liquid water out. This feature is particularly important in regions with high humidity or rainfall, where moisture-related issues are more prevalent. In summary, Tyvek's role in construction and building insulation is multifaceted and highly beneficial. Its ability to act as a weather barrier, enhance energy efficiency, and prevent moisture-related issues makes it an indispensable component in modern building practices. As part of a comprehensive insulation strategy, Tyvek ensures that buildings are not only more energy-efficient but also safer and more durable over time. Its practical uses and benefits underscore why it remains a preferred choice among architects, builders, and homeowners seeking to create sustainable and comfortable living spaces.
Medical and Healthcare Applications
In the realm of medical and healthcare applications, Tyvek stands out as a versatile and indispensable material, offering a myriad of practical uses and benefits. Known for its unique blend of durability, sterility, and breathability, Tyvek is widely utilized in various medical settings to ensure patient safety and hygiene. One of its most significant applications is in the production of surgical gowns and drapes. These garments are designed to provide an impermeable barrier against bacteria and viruses while allowing moisture vapor to escape, thereby reducing the risk of surgical site infections. The material's resistance to tears and punctures further enhances its reliability during surgical procedures. Tyvek also plays a crucial role in the packaging of medical devices and pharmaceuticals. Its impermeable nature ensures that sterile products remain uncontaminated during storage and transportation, which is vital for maintaining the integrity of medical supplies. Additionally, Tyvek's ability to withstand high temperatures makes it an ideal choice for sterilization processes such as autoclaving and gamma radiation, ensuring that medical instruments are thoroughly sanitized without compromising the packaging material. In healthcare facilities, Tyvek is often used in the construction of isolation rooms and temporary medical shelters due to its ease of installation and decontamination. This is particularly beneficial during outbreaks of infectious diseases where rapid setup of isolation areas is critical. The material's lightweight yet robust structure allows for quick deployment, providing an effective barrier against airborne pathogens. Moreover, Tyvek's use extends to personal protective equipment (PPE) such as coveralls and hoods, which are essential for healthcare workers dealing with contagious patients. These garments offer comprehensive protection while being comfortable enough for extended wear, thereby reducing the risk of exposure to harmful pathogens. The environmental benefits of Tyvek in medical settings should not be overlooked. Unlike traditional materials that may require multiple layers or additional treatments to achieve similar levels of protection, Tyvek's inherent properties reduce the need for additional resources and waste generation. This aligns with the growing emphasis on sustainable practices within healthcare. In summary, Tyvek's unique combination of strength, sterility, and breathability makes it an indispensable asset in medical and healthcare applications. From surgical gowns to packaging materials and PPE, Tyvek enhances patient safety, ensures product integrity, and supports efficient healthcare operations while contributing to a more sustainable healthcare environment. Its versatility and reliability underscore its importance as a critical component in modern medical practices.
Other Industrial and Consumer Uses
Beyond its well-known applications in construction and medical fields, Tyvek has a diverse range of other industrial and consumer uses that underscore its versatility and durability. In the realm of packaging, Tyvek is often used to protect sensitive electronic components from moisture and dust due to its unique combination of breathability and impermeability. This makes it an ideal material for shipping and storing delicate items such as circuit boards and microchips. Additionally, Tyvek's resistance to chemicals and abrasion makes it a preferred choice for packaging hazardous materials, ensuring safe transportation without compromising the integrity of the contents. In consumer goods, Tyvek is frequently utilized in the production of durable and water-resistant bags, wallets, and other accessories. Its lightweight yet robust nature allows for the creation of stylish yet functional products that can withstand daily wear and tear. For instance, many outdoor enthusiasts appreciate Tyvek's use in camping gear and apparel because it offers excellent protection against the elements while maintaining breathability, which helps prevent moisture buildup. The textile industry also leverages Tyvek's properties to create innovative fabrics. For example, Tyvek is sometimes blended with other materials to enhance the performance of outdoor clothing, providing both insulation and water resistance. This blend is particularly beneficial for garments intended for extreme weather conditions, such as ski jackets or hiking gear. Moreover, Tyvek's unique characteristics make it a valuable asset in various industrial processes. In the automotive sector, Tyvek is used in the production of airbags due to its high tensile strength and ability to withstand high temperatures without degrading. This ensures that airbags deploy reliably and safely in the event of an accident. In the realm of art and design, Tyvek has found an unexpected niche. Its malleability and resistance to tearing make it an attractive medium for artists who create intricate sculptures or installations that require both flexibility and durability. Additionally, Tyvek's ability to be dyed or printed upon allows for vibrant and durable designs that can be used in a variety of creative applications. Lastly, Tyvek plays a significant role in environmental conservation efforts. Its use in geo-textiles helps stabilize soil and prevent erosion in landscaping projects, while its application in containment systems aids in the cleanup of hazardous waste sites by preventing contaminants from spreading into surrounding soil or water. In summary, the practical uses and benefits of Tyvek extend far beyond its most recognized applications. Its unique blend of properties—breathability, durability, chemical resistance, and versatility—makes it an indispensable material across a wide spectrum of industries and consumer products. Whether protecting sensitive electronics, enhancing outdoor gear, or supporting artistic endeavors, Tyvek continues to demonstrate its value as a multifaceted and reliable material.