What Is A Check Valve

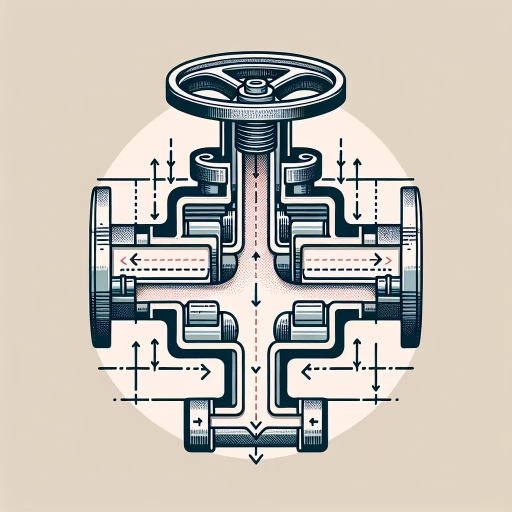
In the realm of fluid dynamics and mechanical engineering, check valves play a crucial role in ensuring the unidirectional flow of fluids, gases, or other substances. These valves are essential components in various industrial, commercial, and residential applications, where they prevent backflow and maintain system integrity. To fully appreciate the significance of check valves, it is important to delve into their fundamental principles, explore their diverse applications, and understand their benefits and maintenance requirements. Understanding the basics of check valves is foundational to grasping how they operate and why they are indispensable in many systems. This includes examining their design, functionality, and the different types available. Beyond their basic operation, check valves find extensive use in industries such as water treatment, chemical processing, and power generation. Their applications are as varied as they are critical, highlighting their versatility and importance. The benefits of using check valves are numerous, including enhanced system safety, reduced risk of contamination, and improved overall efficiency. However, like any mechanical component, they require regular maintenance to ensure optimal performance. By exploring these aspects—understanding the basics, applications, and benefits along with maintenance—readers can gain a comprehensive insight into the world of check valves. To begin this journey into the world of check valves, let's start by **Understanding the Basics of Check Valves**.
Understanding the Basics of Check Valves
Check valves are a crucial component in various industrial and mechanical systems, ensuring the unidirectional flow of fluids and preventing backflow, which can lead to system damage or inefficiency. Understanding the basics of check valves is essential for engineers, technicians, and anyone involved in the design, operation, and maintenance of fluid handling systems. This article delves into the fundamental aspects of check valves, starting with their **Definition and Purpose**, where we explore how these valves function and why they are indispensable in different applications. We then examine the **Types of Check Valves**, highlighting the diverse designs and materials used to cater to various operational needs. Finally, we discuss the **Key Components and Design** of check valves, providing insights into their construction and how these elements contribute to their overall performance. By grasping these core concepts, readers will gain a comprehensive understanding of check valves and their role in maintaining system integrity. This knowledge is vital for optimizing system performance and ensuring safety across a wide range of industries. Understanding the basics of check valves is a foundational step in mastering fluid control and system reliability.
Definition and Purpose
**Definition and Purpose** A check valve, also known as a non-return valve or one-way valve, is a crucial component in various fluid systems, including pipelines, pumps, and hydraulic circuits. Its primary function is to allow fluid to flow in one direction while preventing it from flowing in the opposite direction. This unidirectional flow control is essential for maintaining system integrity, preventing backflow, and ensuring operational safety. The purpose of a check valve can be multifaceted. In piping systems, it prevents backflow that could lead to contamination, damage to equipment, or even catastrophic failures. For instance, in water supply lines, check valves prevent wastewater from entering the potable water supply, thereby safeguarding public health. In industrial settings, such as chemical processing plants, check valves protect against the backflow of hazardous materials that could cause accidents or environmental disasters. In mechanical systems involving pumps and compressors, check valves play a vital role in maintaining efficiency and reliability. They prevent the backflow of fluids when the pump or compressor stops operating, which helps in reducing wear and tear on the equipment and minimizing the risk of damage due to reverse flow. Additionally, check valves are used in safety applications to prevent the release of pressurized fluids or gases that could pose a risk to personnel or equipment. The design of check valves varies depending on the application and the type of fluid being handled. Common types include swing check valves, lift check valves, ball check valves, and diaphragm check valves. Each type has its own advantages and is suited for specific conditions such as high-pressure applications, corrosive environments, or low-flow scenarios. Understanding the basics of check valves is fundamental for engineers, technicians, and operators who design, install, and maintain fluid systems. Proper selection and installation of check valves can significantly enhance system performance, reduce maintenance costs, and ensure compliance with safety regulations. In summary, the definition and purpose of a check valve underscore its importance as a critical component that ensures directional flow control, prevents backflow-related hazards, and maintains the overall efficiency and safety of fluid systems.
Types of Check Valves
Check valves are crucial components in various fluid systems, ensuring that the flow of liquids or gases remains unidirectional. There are several types of check valves, each designed to meet specific application requirements and offer unique advantages. **Ball Check Valves** are among the most common types, featuring a ball that moves freely within the valve body. When fluid flows in the correct direction, the ball is pushed out of the way, allowing flow; however, when the flow reverses, the ball returns to its seat, sealing the valve. **Swing Check Valves**, on the other hand, use a hinged flap that swings open to allow flow and closes when the flow reverses. These valves are often used in larger pipe sizes due to their simplicity and effectiveness. **Lift Check Valves** operate similarly to swing check valves but use a spring-loaded disc instead of a hinged flap. This design allows for more precise control over the opening and closing of the valve. **Diaphragm Check Valves** employ a flexible diaphragm that moves in response to fluid pressure, making them suitable for applications where low pressure drop is critical. **Butterfly Check Valves** combine the functionality of a check valve with that of a butterfly valve, offering a compact design that is ideal for space-constrained installations. **Piston Check Valves** use a spring-loaded piston that moves up to allow flow and returns to its seat when the flow reverses, providing a tight seal. These valves are particularly useful in high-pressure applications. **Silent Check Valves**, also known as non-slam check valves, are designed to close slowly and quietly, reducing the risk of water hammer and associated noise. This makes them suitable for use in systems where sudden closures could cause damage. **Duckbill Check Valves** feature a rubber or elastomeric sleeve that forms the shape of a duck's bill when fluid flows through it. When the flow reverses, the sleeve collapses back onto itself, sealing the valve. These valves are often used in wastewater treatment and other applications where contamination must be prevented. **In-Line Check Valves** are designed to be installed directly into a pipeline, offering a streamlined solution that minimizes space requirements and reduces pressure drop. Each type of check valve has its own set of characteristics, advantages, and limitations, making them suitable for different industrial, commercial, and residential applications. Understanding these variations is essential for selecting the right check valve for a particular system, ensuring optimal performance, safety, and efficiency. By choosing the appropriate type of check valve, users can prevent backflow, reduce wear and tear on equipment, and maintain the integrity of their fluid systems.
Key Components and Design
When delving into the intricacies of check valves, it is crucial to understand their key components and design elements, as these factors collectively ensure the valve's functionality and reliability. At the heart of any check valve lies the **valve body**, which houses all other components and provides structural integrity. The **valve seat** is another critical component, serving as the surface against which the **disc** or **flapper** closes to prevent backflow. The disc or flapper itself is typically made from durable materials such as metal or resilient elastomers, designed to withstand various fluid pressures and velocities. The **spring** or **weight** mechanism plays a pivotal role in check valves, particularly in spring-loaded designs. This component helps to return the disc to its closed position once the forward flow ceases, thereby preventing reverse flow. In weight-actuated designs, gravity assists in closing the valve when flow stops. **Pins** and **hinges** are also essential for certain types of check valves, such as swing check valves, allowing the disc to pivot freely between open and closed positions. The **seal** is another vital component, ensuring that the valve closes tightly to prevent any leakage. Materials used for seals must be compatible with the fluid being handled and capable of withstanding operational pressures and temperatures. **Mounting flanges** or **threads** facilitate easy installation and integration into piping systems, making it simpler to incorporate check valves into existing infrastructure. In terms of design, check valves can be categorized into several types based on their operational mechanism. **Swing check valves**, for instance, feature a hinged disc that swings open with forward flow and closes with reverse flow. **Lift check valves** use a spring-loaded disc that lifts off its seat during forward flow but returns to its closed position when flow stops. **Ball check valves** employ a floating ball that moves up and down within the valve body, sealing against a seat when backflow occurs. Each design type has its own set of advantages and is suited for specific applications. For example, swing check valves are often used in larger pipe sizes due to their simplicity and reliability, while lift check valves are preferred in applications requiring higher precision and tighter shutoff. Understanding these key components and design variations is essential for selecting the right check valve for a particular application, ensuring optimal performance, and preventing potential issues such as backflow or system damage. By grasping these fundamentals, engineers and technicians can better design and maintain fluid handling systems that are efficient, safe, and reliable.
Applications and Uses of Check Valves
Check valves are a crucial component in various fluid control systems, ensuring that fluids flow in one direction while preventing backflow. These valves are indispensable across multiple sectors due to their reliability and efficiency. In industrial settings, check valves play a vital role in maintaining process integrity and preventing potential hazards. They are also essential in residential and commercial environments, where they protect plumbing systems from damage caused by backpressure. Additionally, specialized applications in various industries, such as aerospace, marine, and chemical processing, rely on check valves to meet specific operational demands. Understanding the diverse applications and uses of check valves is paramount for optimizing system performance and safety. This article will delve into the industrial applications, residential and commercial uses, and specialized applications of check valves, providing a comprehensive overview that transitions seamlessly into understanding the basics of these critical devices. By exploring these facets, readers will gain a deeper appreciation for the importance and versatility of check valves in modern engineering and everyday life.
Industrial Applications
Industrial applications of check valves are diverse and critical, ensuring the smooth operation and safety of various systems across different sectors. In the **petroleum and gas industry**, check valves prevent backflow in pipelines, protecting against contamination and maintaining pressure integrity. This is particularly important during drilling operations where backflow could lead to catastrophic failures. Similarly, in **chemical processing**, check valves safeguard against the mixing of incompatible substances by preventing reverse flow, thereby enhancing plant safety and efficiency. In **power generation**, check valves are essential in steam systems to prevent water hammer and ensure that steam flows in one direction, thus maintaining turbine efficiency and preventing damage. Within **water treatment plants**, these valves help in preventing contaminated water from flowing back into clean water lines, ensuring the quality of treated water. In **HVAC systems**, check valves are used to control the flow of refrigerants and prevent backflow, which can cause system inefficiencies and potential damage to compressors. The **pharmaceutical industry** also relies heavily on check valves to maintain sterile conditions by preventing the backflow of contaminants into clean process lines. Additionally, in **marine engineering**, these valves are crucial for preventing seawater from flowing back into bilge systems or other critical machinery, thereby protecting against corrosion and mechanical failure. In **food processing**, check valves ensure that ingredients and products move in a controlled manner without cross-contamination, adhering to stringent hygiene standards. Furthermore, in **nuclear power plants**, the use of check valves is vital for maintaining the integrity of cooling systems and preventing radioactive material from entering non-radioactive areas. Overall, the versatility and reliability of check valves make them indispensable components across a wide range of industrial applications. By preventing backflow and ensuring unidirectional flow, these valves contribute significantly to operational safety, efficiency, and compliance with regulatory standards. Their role in maintaining system integrity underscores their importance as a fundamental element in modern industrial processes.
Residential and Commercial Uses
Check valves play a crucial role in both residential and commercial settings, ensuring the smooth operation of various systems by preventing backflow and maintaining pressure. In residential contexts, check valves are often integrated into plumbing systems to safeguard against potential hazards such as sewage backflow and water contamination. For instance, they are commonly used in sump pumps to prevent water from flowing back into the sump pit after it has been pumped out, thereby protecting basements from flooding. Additionally, check valves are essential in home heating systems, particularly in radiant floor heating and boiler systems, where they prevent hot water from circulating back into the boiler when it is not in use, thus enhancing efficiency and reducing energy consumption. In commercial environments, the importance of check valves is even more pronounced due to the larger scale and complexity of the systems involved. In industrial settings, check valves are critical components of process piping systems where they ensure that fluids flow in one direction only, preventing damage to equipment and maintaining process integrity. For example, in chemical processing plants, check valves protect against the backflow of hazardous chemicals into other parts of the system, which could lead to dangerous reactions or contamination. Similarly, in commercial HVAC systems, check valves help maintain optimal system performance by preventing refrigerant from flowing back into the compressor when it is off, thereby extending the lifespan of the equipment and reducing maintenance costs. Furthermore, in high-rise buildings and large commercial facilities, check valves are vital in fire suppression systems. They ensure that water or other fire-suppressing agents flow only towards the area of need during an emergency, preventing backflow that could compromise the effectiveness of the system. In healthcare facilities, check valves are used in medical gas systems to prevent cross-contamination between different gas lines, ensuring patient safety. Overall, the versatility and reliability of check valves make them indispensable in a wide range of residential and commercial applications, contributing significantly to safety, efficiency, and operational reliability across various sectors. By understanding their role and importance, users can better appreciate the critical function these valves serve in maintaining the integrity of complex systems.
Specialized Applications in Various Industries
Check valves, with their unique ability to allow fluid flow in one direction while preventing it in the other, find specialized applications across a wide range of industries. In the **petroleum and gas industry**, check valves are crucial for maintaining pipeline integrity and preventing backflow, which can lead to contamination or damage to equipment. For instance, in oil refineries, these valves ensure that crude oil flows only in the intended direction, safeguarding against potential hazards such as explosions or spills. In **power generation**, particularly in nuclear and thermal plants, check valves play a vital role in ensuring the safe operation of cooling systems. They prevent backflow into the reactor or boiler, thereby maintaining system pressure and preventing overheating or other catastrophic failures. Similarly, in **chemical processing**, check valves are essential for controlling the flow of corrosive or hazardous materials, protecting both the equipment and the environment from potential leaks or spills. The **water treatment and supply sector** also relies heavily on check valves to prevent contamination of potable water supplies. These valves are used in water distribution systems to ensure that treated water flows only towards consumers and not back into the treatment plant, thereby maintaining water quality and public health standards. In **aviation and aerospace**, check valves are used in fuel systems to prevent fuel backflow during engine shutdown or when switching between fuel tanks. This is critical for maintaining aircraft safety and performance. Additionally, in **marine engineering**, check valves are employed in ballast systems to control the flow of seawater, ensuring stable vessel operations and preventing flooding. In **medical devices**, such as dialysis machines and ventilators, check valves are used to regulate fluid flow and prevent backflow, which is essential for patient safety. For example, in dialysis machines, these valves ensure that blood flows through the dialyzer without any backflow that could contaminate the blood or compromise the treatment process. Lastly, in **HVAC (Heating, Ventilation, and Air Conditioning) systems**, check valves are utilized to control the flow of refrigerants and prevent backflow into compressors or other components, which can cause system failure or inefficiency. This ensures optimal performance and energy efficiency of HVAC systems. In summary, the specialized applications of check valves span multiple industries where fluid flow control is critical for safety, efficiency, and operational integrity. Their ability to prevent backflow makes them indispensable components in various industrial settings.
Benefits and Maintenance of Check Valves
Check valves are a crucial component in various industrial and residential plumbing systems, ensuring the unidirectional flow of fluids and preventing backflow. These valves offer numerous benefits, including enhanced system efficiency, reduced risk of contamination, and protection against potential damage from reverse flow. In this article, we will delve into the advantages of check valves over other valve types, highlighting their unique features and performance capabilities. Additionally, we will discuss key considerations for the installation and operation of check valves to ensure optimal functionality. Finally, we will provide essential maintenance and troubleshooting tips to help users extend the lifespan of these vital components. By understanding these aspects, readers will gain a comprehensive insight into the benefits and maintenance of check valves, setting the stage for a deeper exploration of their fundamental principles in the section titled "Understanding the Basics of Check Valves."
Advantages Over Other Valve Types
Check valves offer several distinct advantages over other valve types, making them a preferred choice in various industrial and residential applications. One of the primary benefits is their ability to prevent backflow, which is crucial in systems where fluid flow direction must be strictly controlled. Unlike gate or ball valves, which require manual operation to change flow direction, check valves automatically allow fluid to flow in one direction while blocking it in the opposite direction. This inherent functionality reduces the risk of contamination and damage from reverse flow, enhancing system reliability and safety. Another significant advantage of check valves is their simplicity and low maintenance requirements. Unlike more complex valves such as globe or needle valves, check valves typically have fewer moving parts and no external controls. This simplicity not only reduces the likelihood of mechanical failure but also minimizes the need for frequent maintenance checks and repairs. Additionally, check valves are often less expensive to purchase and install compared to other types of valves, providing a cost-effective solution for flow control needs. In terms of performance, check valves are highly efficient due to their minimal resistance to forward flow. This characteristic is particularly beneficial in applications where high flow rates are necessary, such as in water supply systems or chemical processing plants. The low pressure drop across check valves ensures that the system operates at optimal efficiency, reducing energy consumption and enhancing overall performance. Moreover, check valves are versatile and can be used in a wide range of environments and applications. They are available in various materials and configurations to suit different fluid types and operating conditions. For instance, swing check valves are suitable for larger pipe sizes and higher flow rates, while lift check valves are more appropriate for smaller pipes and lower flow rates. This adaptability makes them an ideal choice for diverse industries including oil and gas, power generation, and wastewater treatment. In summary, the advantages of check valves over other types include their automatic operation to prevent backflow, simplicity and low maintenance needs, cost-effectiveness, high efficiency in flow control, and versatility in various applications. These benefits collectively make check valves an indispensable component in many fluid handling systems, ensuring reliable operation and minimizing potential risks associated with reverse flow.
Installation and Operation Considerations
When considering the installation and operation of check valves, several key factors must be taken into account to ensure optimal performance and longevity. **Installation Considerations:** Proper installation is crucial for the effective functioning of a check valve. The valve should be installed in the correct orientation, as specified by the manufacturer, to prevent backflow and ensure smooth operation. It is also important to select the right type of check valve for the specific application, taking into account factors such as flow rate, pressure drop, and fluid characteristics. For instance, swing check valves are suitable for low-pressure applications with high flow rates, while ball check valves are better suited for applications requiring quick closure. Additionally, ensuring that the valve is properly sized for the system can prevent issues like turbulence and noise. **Operation Considerations:** During operation, regular monitoring is essential to maintain the valve's efficiency. Check valves should be inspected periodically for signs of wear or damage, such as corrosion or erosion, which can compromise their sealing ability. Proper maintenance involves cleaning or replacing worn-out parts and ensuring that the valve operates freely without any obstructions. It is also critical to adhere to the manufacturer's guidelines for operating conditions such as temperature and pressure limits to avoid premature failure. Furthermore, integrating check valves into a comprehensive maintenance schedule can help in identifying potential issues before they become major problems, thereby reducing downtime and enhancing overall system reliability. By carefully considering these installation and operation factors, users can maximize the benefits of check valves, including preventing backflow, reducing pressure surges, and protecting downstream equipment from potential damage. This meticulous approach not only extends the lifespan of the valve but also contributes significantly to the overall efficiency and safety of the system.
Maintenance and Troubleshooting Tips
**Maintenance and Troubleshooting Tips** To ensure the optimal performance and longevity of check valves, regular maintenance and prompt troubleshooting are essential. Here are some key tips to keep in mind: 1. **Regular Inspection**: Periodically inspect the check valve for signs of wear, corrosion, or damage. Check for any leaks around the valve seat or stem seals. Use visual inspection tools like borescopes if necessary. 2. **Cleaning**: Clean the valve regularly to prevent debris buildup. Disassemble the valve if possible, and use a soft brush or cloth to remove any sediment or particulate matter. Avoid using harsh chemicals that could damage the valve materials. 3. **Lubrication**: Ensure that moving parts are properly lubricated. Use a lubricant compatible with the valve materials to prevent corrosion and wear. 4. **Flow Direction**: Always ensure that the check valve is installed in the correct direction of flow. Incorrect installation can lead to premature failure or malfunction. 5. **Pressure Testing**: Conduct periodic pressure tests to verify that the valve is functioning correctly. This involves checking for backflow and ensuring that the valve closes properly under various pressure conditions. 6. **Replacement of Parts**: Replace worn-out or damaged parts promptly. Use genuine replacement parts to maintain the valve's performance and reliability. 7. **Troubleshooting Common Issues**: - **Leakage**: If leakage is observed, inspect the valve seat and seals for damage or wear. Replace these components if necessary. - **Failure to Close**: Check for debris or sediment that may be preventing the valve from closing properly. Clean or replace the valve as needed. - **Sticking**: Apply lubricant to moving parts if the valve is sticking. If the issue persists, consider replacing the valve. 8. **Documentation**: Keep detailed records of maintenance activities, including dates, procedures performed, and any parts replaced. This helps in tracking the valve's history and planning future maintenance. By following these maintenance and troubleshooting tips, you can significantly extend the lifespan of your check valves, ensure their reliable operation, and minimize downtime due to failures. Regular upkeep not only saves time and money but also enhances overall system efficiency and safety. Incorporating these practices into your routine maintenance schedule will help you derive the maximum benefits from your check valves while minimizing potential issues.