What Is Alloy Steel

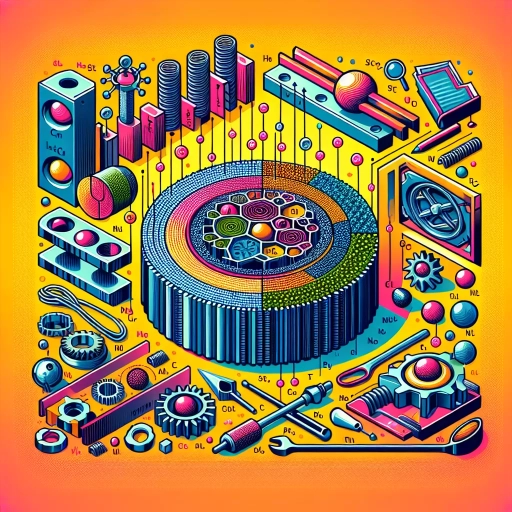
Alloy steel is a versatile and highly sought-after material in various industries due to its enhanced properties compared to plain carbon steel. By incorporating elements such as chromium, nickel, molybdenum, and vanadium into the steel alloy, manufacturers can tailor the material's strength, durability, and resistance to corrosion and heat. This article delves into the world of alloy steel, starting with an **Introduction to Alloy Steel**, where we explore its fundamental composition and how it differs from other types of steel. We will then examine the **Types and Classification of Alloy Steels**, highlighting the diverse range of alloys and their unique characteristics. Finally, we will discuss the **Properties and Applications of Alloy Steels**, detailing how these materials are utilized in critical sectors such as aerospace, automotive, and construction. Understanding these aspects is crucial for appreciating the significance and versatility of alloy steel. Let's begin by exploring what alloy steel is and how it is defined in the **Introduction to Alloy Steel**.
Introduction to Alloy Steel
Alloy steel, a versatile and robust material, has been a cornerstone of modern industry for centuries. This high-performance steel is distinguished by its unique composition and historical development, which have significantly influenced its widespread use. To understand the significance of alloy steel, it is essential to delve into its definition and basic composition, which sets the foundation for its exceptional properties. Historically, the evolution of alloy steel has been marked by continuous innovation, transforming it from a rudimentary material to a sophisticated alloy with diverse applications. Today, alloy steel plays a critical role in various industries, from construction and automotive to aerospace and energy, due to its enhanced strength, durability, and resistance to corrosion. By exploring these aspects—definition and basic composition, historical development and evolution, and importance in modern industry—we can appreciate the full scope of alloy steel's impact and utility. Let us begin by examining the fundamental characteristics that define alloy steel.
Definition and Basic Composition
Alloy steel is a type of steel alloy that contains elements other than carbon to enhance its mechanical properties. The definition of alloy steel hinges on the presence of these additional elements, which can include manganese, chromium, vanadium, tungsten, and nickel, among others. These elements are added in varying proportions to achieve specific characteristics such as increased strength, toughness, hardness, and resistance to corrosion and wear. The basic composition of alloy steel typically includes a base of iron and carbon, similar to regular steel, but with the addition of one or more alloying elements. Iron, the primary component, makes up the bulk of the alloy, while carbon is present in smaller amounts to form carbides that contribute to the steel's hardness. The alloying elements are then added to this iron-carbon matrix to impart the desired properties. For instance, chromium enhances corrosion resistance and is commonly found in stainless steels; manganese improves strength and hardenability; vanadium increases toughness and resistance to wear; and nickel enhances ductility and resistance to corrosion. The specific composition of alloy steel can vary widely depending on the intended application. For example, high-strength low-alloy (HSLA) steels contain small amounts of alloying elements like manganese, silicon, and vanadium to achieve high strength without significant increases in cost. On the other hand, tool steels may contain higher percentages of tungsten, molybdenum, and vanadium to achieve exceptional hardness and wear resistance. The precise combination and concentration of these elements are carefully controlled during the manufacturing process to ensure that the final product meets the required specifications. Understanding the definition and basic composition of alloy steel is crucial for selecting the appropriate material for various industrial applications. From construction and automotive to aerospace and manufacturing, alloy steels play a vital role due to their tailored properties. By knowing how different elements influence the behavior of steel, engineers and manufacturers can design and produce components that meet stringent performance criteria, ensuring safety, efficiency, and durability. This foundational knowledge also facilitates ongoing research and development in the field of metallurgy, driving innovation in materials science and engineering.
Historical Development and Evolution
The historical development and evolution of alloy steel are deeply intertwined with advancements in metallurgy and industrial needs. The journey began with ancient civilizations, where early forms of alloying were discovered through trial and error. For instance, the Wootz steel produced in India around 300 BCE was an early form of high-carbon steel alloyed with small amounts of other elements, showcasing an early understanding of material properties enhancement. In the Middle Ages, Damascus steel emerged, renowned for its strength and durability due to the presence of carbon and other trace elements. However, it wasn't until the Industrial Revolution that significant strides were made in alloy steel production. The discovery of the Bessemer process in 1855 by Sir Henry Bessemer allowed for mass production of steel, paving the way for further experimentation with alloys. The late 19th and early 20th centuries saw a surge in the development of various alloy steels. The introduction of chromium in the late 19th century led to the creation of stainless steel, which revolutionized industries requiring corrosion-resistant materials. Other key elements like nickel, molybdenum, and vanadium were also incorporated into steel alloys to enhance properties such as strength, toughness, and resistance to wear and tear. The 20th century witnessed the development of specialized alloy steels tailored for specific applications. For example, high-speed tool steels containing tungsten and molybdenum were developed for cutting tools that could withstand high temperatures and maintain their hardness. Similarly, low-alloy steels with additions like manganese and silicon were created for structural applications requiring improved strength-to-weight ratios. Modern advancements in metallurgy have led to the creation of sophisticated alloy steels with unique properties. The use of advanced techniques such as powder metallurgy and vacuum induction melting has enabled the production of high-performance alloys with precise control over chemical composition. Today, alloy steels are integral to various industries including aerospace, automotive, construction, and energy, where their enhanced mechanical properties and durability are crucial. In summary, the evolution of alloy steel has been a continuous process driven by technological innovations and industrial demands. From ancient Wootz steel to modern high-performance alloys, each step has built upon previous discoveries, leading to the diverse range of alloy steels available today. Understanding this historical context is essential for appreciating the complexity and versatility of alloy steel in contemporary applications.
Importance in Modern Industry
In modern industry, alloy steel plays a pivotal role due to its enhanced mechanical properties, which significantly outperform those of plain carbon steel. The addition of various alloying elements such as chromium, molybdenum, vanadium, and nickel to the steel matrix allows for tailored strength, toughness, and resistance to corrosion and wear. This versatility makes alloy steel indispensable in critical applications across multiple sectors. For instance, in the aerospace industry, high-strength alloy steels are used in aircraft components where weight reduction and high performance are crucial. In the automotive sector, alloy steels are employed in engine parts and structural components to improve fuel efficiency and durability. The construction industry also relies heavily on alloy steels for building high-rise structures and bridges, where strength and resistance to environmental degradation are paramount. Additionally, alloy steels are vital in the energy sector for manufacturing pipelines and equipment that must withstand extreme temperatures and pressures. The ability of alloy steel to be heat-treated further enhances its properties, making it suitable for a wide range of industrial processes. Overall, the importance of alloy steel in modern industry lies in its ability to meet specific performance requirements, ensuring reliability, efficiency, and safety across diverse applications.
Types and Classification of Alloy Steels
Alloy steels are a diverse group of materials that offer enhanced properties compared to carbon steels, making them indispensable in various industrial applications. This article delves into the types and classification of alloy steels, focusing on three key categories: High-Strength Low-Alloy (HSLA) Steels, Stainless Steels, and Tool Steels and Special Purpose Alloys. Each of these categories brings unique benefits and is tailored for specific uses. HSLA Steels, for instance, are known for their high strength-to-weight ratio and resistance to corrosion, making them ideal for structural components in construction and automotive industries. Stainless Steels, on the other hand, are renowned for their excellent corrosion resistance and aesthetic appeal, commonly used in kitchenware, medical equipment, and architectural features. Tool Steels and Special Purpose Alloys are engineered for extreme hardness and wear resistance, often employed in manufacturing tools and machinery. By understanding these classifications, engineers and manufacturers can select the most appropriate alloy steel for their needs. This article will explore each of these categories in detail, starting with the versatile and widely used High-Strength Low-Alloy (HSLA) Steels.
High-Strength Low-Alloy (HSLA) Steels
High-Strength Low-Alloy (HSLA) steels are a category of alloy steels that offer a unique combination of high strength, toughness, and resistance to corrosion, making them highly versatile and widely used in various industrial applications. Unlike conventional carbon steels, HSLA steels contain small amounts of alloying elements such as vanadium, niobium, titanium, and molybdenum. These elements enhance the mechanical properties of the steel by forming fine precipitates within the microstructure, which improve grain refinement and reduce the carbon content, thereby minimizing the risk of brittleness. HSLA steels are classified based on their yield strength, which ranges from 250 to 550 MPa (36,000 to 80,000 psi). This classification allows for the selection of specific grades tailored to different engineering requirements. For instance, HSLA-80 and HSLA-100 are commonly used in shipbuilding due to their high strength-to-weight ratio and resistance to fatigue. In contrast, HSLA-50 and HSLA-60 are often employed in the automotive industry for components like chassis and suspension parts where a balance between strength and formability is crucial. The production process of HSLA steels involves controlled rolling and cooling techniques to achieve the desired microstructural properties. Microalloying with elements like niobium or vanadium helps in achieving fine grain size, which significantly enhances the toughness and weldability of the steel. Additionally, HSLA steels exhibit better resistance to atmospheric corrosion compared to plain carbon steels due to the presence of small amounts of elements like copper and phosphorus. In terms of applications, HSLA steels are extensively used in construction for building frames, bridges, and high-rise structures where high strength and durability are essential. They are also preferred in the oil and gas industry for pipelines and offshore platforms due to their excellent resistance to sour service environments. Furthermore, HSLA steels find significant use in the manufacturing of heavy machinery, railcars, and military vehicles where a combination of strength, toughness, and weldability is paramount. Overall, High-Strength Low-Alloy steels represent a critical advancement in steel technology, offering a balanced set of mechanical properties that make them indispensable across various sectors. Their ability to provide high performance at relatively low alloy content makes them an economical choice for many engineering applications, contributing significantly to the efficiency and reliability of modern infrastructure and machinery.
Stainless Steels
Stainless steels are a subset of alloy steels that are renowned for their exceptional corrosion resistance, durability, and aesthetic appeal. These steels contain a minimum of 10.5% chromium content, which forms a thin layer of oxide on the surface, known as a passivation layer, that protects the metal from further chemical reactions and corrosion. This unique property makes stainless steels ideal for applications in harsh environments such as marine, chemical processing, and medical equipment. There are several types of stainless steels, each classified based on their microstructure and chemical composition. **Austenitic stainless steels**, which include the popular 304 and 316 grades, are the most widely used due to their high corrosion resistance and formability. They contain significant amounts of chromium, nickel, and sometimes molybdenum. **Ferritic stainless steels** have a lower chromium content compared to austenitic grades but are less expensive and still offer good corrosion resistance. **Martensitic stainless steels** are known for their high strength and hardness, making them suitable for applications requiring wear resistance, such as cutlery and surgical instruments. **Duplex stainless steels** combine the benefits of both austenitic and ferritic structures, offering enhanced strength and corrosion resistance. The classification of stainless steels also extends to their specific applications. For instance, **Precipitation Hardening (PH) stainless steels** can be strengthened through heat treatment, making them suitable for high-strength applications like aerospace components. **Super Austenitic stainless steels** have higher molybdenum content than standard austenitic grades, providing superior resistance to pitting and crevice corrosion in severe environments. In addition to their technical properties, stainless steels are also valued for their hygiene and sustainability. They are non-toxic and easy to clean, which is why they are commonly used in food processing equipment and medical devices. Furthermore, stainless steels are 100% recyclable, contributing to a more sustainable future by reducing waste and conserving natural resources. Overall, the versatility of stainless steels makes them an indispensable material in various industries. Their ability to withstand corrosive conditions while maintaining strength and durability ensures that they remain a preferred choice for engineers and designers seeking reliable and long-lasting solutions.
Tool Steels and Special Purpose Alloys
Tool steels and special purpose alloys are critical components within the broader category of alloy steels, distinguished by their unique properties and applications. Tool steels, specifically designed for making tools, are characterized by their high hardness, wear resistance, and ability to withstand high temperatures. These steels are alloyed with elements such as tungsten, molybdenum, vanadium, and chromium to enhance their mechanical properties. For instance, high-speed tool steels (HSS) contain tungsten and molybdenum, enabling them to maintain their hardness even at elevated temperatures, making them ideal for cutting tools and machinery parts. Hot work tool steels, on the other hand, are used in die-casting and forging due to their resistance to thermal shock and high-temperature strength. Special purpose alloys, another subset of alloy steels, are tailored for specific industrial needs that require unique combinations of properties. These alloys can include maraging steels, which are known for their ultra-high strength and toughness achieved through the addition of nickel, cobalt, and titanium. Maraging steels find applications in aerospace and defense industries where high strength-to-weight ratios are crucial. Another example is stainless steels, which are alloyed with chromium to provide corrosion resistance, making them essential in chemical processing, food handling, and medical equipment. Additionally, there are precipitation-hardening (PH) steels that gain strength through heat treatment processes involving the precipitation of intermetallic compounds, often used in aerospace and automotive applications. The classification of these alloys is based on their chemical composition and the specific properties they are designed to exhibit. For tool steels, the AISI (American Iron and Steel Institute) classification system is commonly used, categorizing them into groups such as high-speed steels, hot work steels, cold work steels, and shock-resisting steels. Special purpose alloys may be classified based on their primary alloying elements or their intended use. Understanding these classifications is vital for selecting the appropriate material for a given application, ensuring optimal performance and longevity. In summary, tool steels and special purpose alloys represent a sophisticated segment of alloy steels, engineered to meet demanding industrial requirements. Their diverse compositions and heat treatment processes allow them to serve in a wide range of critical applications, from high-speed cutting tools to corrosion-resistant components in harsh environments. The precise classification and understanding of these materials are essential for engineers and manufacturers seeking to leverage their unique properties effectively.
Properties and Applications of Alloy Steels
Alloy steels are a class of steels that owe their unique properties to the addition of various alloying elements. These materials are renowned for their enhanced mechanical properties, superior corrosion resistance, and diverse industrial applications. The mechanical properties of alloy steels, including strength, hardness, and toughness, are significantly improved due to the presence of elements such as chromium, molybdenum, and vanadium. This enhancement makes them ideal for demanding environments where high performance is critical. Additionally, alloy steels exhibit excellent corrosion resistance and durability, which are crucial in extending the lifespan of structures and machinery. Their versatility is further underscored by their widespread use in construction, automotive, and aerospace industries. Understanding these aspects is essential for appreciating the full potential of alloy steels. To delve deeper into these benefits, let's first explore the mechanical properties of alloy steels, focusing on their strength, hardness, and toughness.
Mechanical Properties: Strength, Hardness, and Toughness
Mechanical properties such as strength, hardness, and toughness are crucial in determining the suitability of alloy steels for various applications. **Strength**, often measured through tensile tests, indicates a material's ability to withstand stress without failing. Alloy steels can be engineered to have high strength by adding elements like carbon, chromium, and molybdenum, which enhance the steel's microstructure and grain size. For instance, high-strength low-alloy (HSLA) steels are designed for structural applications where load-bearing capacity is paramount. **Hardness**, typically assessed using the Rockwell or Brinell hardness tests, reflects a material's resistance to indentation and abrasion. Alloying elements such as tungsten and vanadium can significantly increase the hardness of steel, making it ideal for wear-resistant components like cutting tools and gears. However, increased hardness often comes at the expense of ductility and toughness. **Toughness**, which is the ability of a material to absorb energy and plastically deform without fracturing, is critical for applications where impact resistance is necessary. Toughness is often evaluated through Charpy impact tests. Alloy steels can be alloyed with elements like manganese and nickel to improve their toughness while maintaining other desirable properties. For example, in shipbuilding and construction, alloy steels with balanced strength and toughness are essential to ensure structural integrity under various loading conditions. The interplay between these mechanical properties is complex; optimizing one property can compromise others. For instance, increasing the carbon content in steel enhances strength and hardness but may reduce toughness. Therefore, the selection of alloy steels must be based on a thorough understanding of the specific application requirements. By carefully choosing the right alloying elements and processing conditions, engineers can tailor the mechanical properties of alloy steels to meet the demands of diverse industries, from aerospace to automotive manufacturing. This versatility underscores the importance of understanding and manipulating the mechanical properties of alloy steels to achieve optimal performance in various applications.
Corrosion Resistance and Durability
Corrosion resistance and durability are critical properties of alloy steels, significantly enhancing their performance and lifespan in various applications. Alloy steels, by virtue of their composition, which includes elements such as chromium, nickel, molybdenum, and vanadium, exhibit superior resistance to corrosion compared to plain carbon steels. The addition of these alloying elements forms a protective oxide layer on the surface of the steel, which acts as a barrier against environmental factors like moisture, acids, and salts that could otherwise lead to degradation. For instance, stainless steel alloys, which contain a minimum of 10.5% chromium, are renowned for their excellent corrosion resistance due to the formation of a stable chromium oxide layer that prevents further chemical reactions. The durability of alloy steels is another key attribute that makes them indispensable in demanding environments. These steels possess enhanced mechanical properties such as strength, toughness, and hardness, which are achieved through careful control of the alloying elements and heat treatment processes. High-strength low-alloy (HSLA) steels, for example, are designed to offer improved strength-to-weight ratios without compromising ductility, making them ideal for structural applications in construction and automotive industries. Additionally, the inclusion of elements like molybdenum and vanadium in some alloy steels enhances their resistance to wear and fatigue, thereby extending their service life under cyclic loading conditions. In practical terms, the corrosion resistance and durability of alloy steels translate into significant economic benefits. For instance, in marine environments where seawater can be highly corrosive, using alloy steels can reduce maintenance costs and extend the lifespan of equipment such as ship hulls and offshore platforms. Similarly, in industrial settings where machinery is exposed to harsh chemicals or extreme temperatures, alloy steels can withstand these conditions better than other materials, reducing downtime and increasing overall efficiency. Moreover, the versatility of alloy steels allows them to be tailored for specific applications through adjustments in their chemical composition and processing techniques. This flexibility ensures that these materials can meet the stringent requirements of diverse industries ranging from aerospace to biomedical engineering. For example, certain alloy steels are used in surgical instruments due to their high corrosion resistance and ability to withstand sterilization processes without losing their structural integrity. In summary, the corrosion resistance and durability of alloy steels are fundamental properties that underpin their widespread use across various sectors. These attributes not only ensure the longevity of equipment but also contribute to cost savings and improved operational efficiency. As technology continues to evolve, the development of new alloy steel compositions and processing techniques will further enhance these properties, making alloy steels an even more indispensable material in modern engineering.
Industrial Applications: Construction, Automotive, and Aerospace
Alloy steels play a pivotal role in various industrial applications due to their enhanced mechanical properties, such as strength, toughness, and resistance to corrosion and wear. In the **construction industry**, alloy steels are used extensively for building high-rise structures, bridges, and other infrastructure projects. High-strength low-alloy (HSLA) steels, for instance, are preferred for their ability to withstand heavy loads while minimizing material usage, thereby reducing costs and environmental impact. These steels also exhibit excellent weldability, which is crucial for large-scale construction projects. In the **automotive sector**, alloy steels are integral to vehicle manufacturing. They are used in the production of engine components, axles, gears, and chassis due to their high strength-to-weight ratio. This property allows for the design of lighter vehicles that achieve better fuel efficiency without compromising on safety or performance. Additionally, alloy steels like stainless steel and chromium-molybdenum steel are employed in exhaust systems and other components that require resistance to corrosion and high temperatures. The **aerospace industry** also relies heavily on alloy steels for their unique combination of properties. For example, chromium-nickel-molybdenum steels are used in aircraft engine components because they offer a balance of strength, toughness, and resistance to fatigue and corrosion. These alloys can withstand the extreme conditions encountered during flight, including high temperatures and stresses. Furthermore, titanium alloys are often used in aerospace applications due to their exceptional strength-to-weight ratio and resistance to corrosion, making them ideal for structural components in aircraft and spacecraft. In all these industries, the specific alloy composition can be tailored to meet the demands of the application. For instance, adding elements like chromium, molybdenum, or vanadium can enhance hardness, toughness, or resistance to wear and tear. The versatility of alloy steels in terms of their properties and applications makes them indispensable materials across diverse industrial sectors. Their ability to be engineered for specific needs ensures that they continue to play a critical role in advancing technological capabilities and meeting the stringent requirements of modern engineering projects.