What Is Ink Made Of

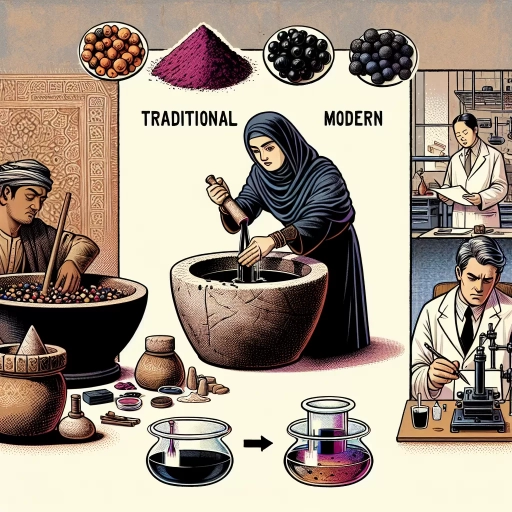
Ink, a fundamental tool in human communication and artistic expression, has been a cornerstone of civilization for thousands of years. From ancient hieroglyphs to modern-day printing, the composition and production of ink have evolved significantly, reflecting advancements in technology and materials science. This article delves into the intricate world of ink, exploring its chemical composition, the diverse types of ink and their unique ingredients, and the meticulous manufacturing process that ensures quality and consistency. Understanding the chemical makeup of ink is crucial, as it determines its performance, durability, and environmental impact. We will begin by examining the chemical composition of ink, which sets the foundation for understanding its various types and the rigorous manufacturing processes involved. By uncovering these aspects, we gain a deeper appreciation for the complexity and importance of ink in our daily lives. Let us start with the fundamental question: what is ink made of?
Chemical Composition of Ink
The chemical composition of ink is a complex blend of various components, each playing a crucial role in its performance, durability, and aesthetic appeal. At the heart of any ink formulation are **dyes and pigments**, which provide the color and vibrancy that make ink visible on different surfaces. However, these colorants are just one part of the equation. **Solvents and carriers** are essential for dissolving and transporting the dyes or pigments, ensuring that the ink flows smoothly and consistently through writing instruments or printing systems. Additionally, **additives and stabilizers** enhance the ink's shelf life, prevent degradation, and improve its overall stability and performance under various conditions. Understanding these three key components is vital for appreciating the science behind ink and its diverse applications. Let's start by delving into the world of **dyes and pigments**, the foundational elements that give ink its color and character.
1. Dyes and Pigments
Dyes and pigments are the cornerstone components of ink, each playing a distinct role in the chemical composition that defines its color, durability, and performance. **Dyes** are dissolved in the ink's liquid carrier, typically water or a solvent, and are characterized by their ability to penetrate the substrate they are applied to. This solubility allows dyes to create vibrant, transparent colors that can blend seamlessly with other dyes. However, their solubility also means they can be prone to fading over time due to exposure to light, water, or other environmental factors. Dyes are often used in applications where high color intensity is required but long-term durability is not the primary concern, such as in food coloring, cosmetics, and certain types of printing inks. On the other hand, **pigments** are insoluble particles that remain suspended within the ink's carrier. Unlike dyes, pigments do not dissolve; instead, they adhere to the surface of the substrate, providing a more opaque and lightfast color. This property makes pigments highly resistant to fading and degradation, making them ideal for applications where longevity is crucial, such as in automotive paints, architectural coatings, and high-quality printing inks. Pigments can be derived from natural sources like minerals or synthesized chemically. For instance, carbon black is a common pigment used in black inks due to its excellent lightfastness and high tinting strength. The choice between dyes and pigments in ink formulation depends on the intended use and desired properties of the final product. Inks used for artistic purposes might favor dyes for their vibrant colors and blending capabilities, while industrial inks might rely more heavily on pigments for their durability and resistance to environmental stressors. Additionally, some inks may combine both dyes and pigments to achieve a balance between color intensity and longevity. In terms of chemical composition, dyes typically consist of complex organic molecules with chromophores—groups of atoms responsible for absorbing light and producing color. These molecules are designed to interact with light in specific ways to produce the desired hue. Pigments, however, can be composed of a wide range of materials including metals (like titanium dioxide for white pigments), metal oxides (such as iron oxide for reds and yellows), and carbon-based compounds (like carbon black). The physical properties of these pigment particles, such as particle size and distribution, also play a critical role in determining the final appearance and performance of the ink. Understanding the differences between dyes and pigments is essential for formulating inks that meet specific requirements. For example, in digital printing, pigment-based inks are often preferred because they offer better lightfastness and water resistance compared to dye-based inks. Conversely, in certain textile applications, dye-based inks may be chosen for their ability to penetrate fabric fibers and create deep, rich colors. In conclusion, the interplay between dyes and pigments in ink formulation is a delicate balance that influences the aesthetic appeal, durability, and overall performance of the ink. By selecting the appropriate type and combination of these colorants, manufacturers can tailor their inks to meet a wide range of applications, from artistic expression to industrial use, ensuring that the final product meets both functional and aesthetic standards.
2. Solvents and Carriers
In the intricate composition of ink, solvents and carriers play pivotal roles that are both complementary and essential. Solvents, which can include water, glycols, or organic compounds like ethanol and acetone, serve as the medium in which the other ink components are dissolved or suspended. These liquids facilitate the flow of ink through the printing process by reducing its viscosity and ensuring smooth application onto various surfaces. For instance, in aqueous inks used in digital printing, water acts as the primary solvent, allowing for easy dispersion of pigments and dyes while maintaining a consistent flow rate through the printer's nozzles. In contrast, solvent-based inks used in industrial applications may employ more volatile solvents to achieve rapid drying times and robust adhesion on non-porous substrates. Carriers, on the other hand, are typically oils or resins that encapsulate and transport the pigment particles within the ink formulation. They enhance the stability and shelf life of the ink by preventing pigment settling and aggregation. In flexographic printing, for example, carriers such as mineral oils or vegetable oils help maintain a uniform dispersion of pigments, ensuring consistent color quality across large print runs. Additionally, carriers can influence the final appearance of the printed material by affecting factors like gloss and durability. For instance, inks formulated with resin-based carriers often exhibit improved scratch resistance and lightfastness compared to those using simpler oil-based carriers. The interplay between solvents and carriers is critical for achieving optimal ink performance. The choice of solvent can affect how well pigments are dispersed within the carrier, while the carrier's properties influence how effectively the solvent evaporates during the drying process. This balance is particularly important in modern printing technologies where high-speed production demands both rapid drying times and excellent print quality. By carefully selecting and combining solvents and carriers, ink manufacturers can tailor their products to meet specific application requirements, whether it be for vibrant digital prints, durable industrial coatings, or precise flexographic labels. Moreover, advancements in solvent and carrier technology have led to the development of more environmentally friendly ink formulations. Water-based inks with bio-derived carriers are becoming increasingly popular due to their lower VOC (volatile organic compound) emissions and reduced environmental impact. Similarly, UV-curable inks that use photoinitiators as carriers offer energy-efficient drying processes without the need for heat, further minimizing their ecological footprint. In summary, solvents and carriers are indispensable components of ink composition, each contributing uniquely to its overall performance. Their synergy ensures that inks flow smoothly, dry efficiently, and adhere well to various substrates while maintaining vibrant color and durability. As printing technologies continue to evolve, the strategic selection and innovation of solvents and carriers will remain crucial for meeting the demands of diverse applications while adhering to stringent environmental standards.
3. Additives and Stabilizers
In the intricate composition of ink, additives and stabilizers play a crucial role in enhancing its performance, durability, and overall quality. These components are meticulously selected to address specific challenges that ink may face during its application and lifespan. **Additives**, for instance, are substances added to the ink formulation to improve its flow characteristics, wetting properties, and drying times. One common additive is **surfactants**, which reduce the surface tension of the ink, allowing it to spread evenly and penetrate the substrate more effectively. This is particularly important in printing processes where uniform coverage is essential. Another type of additive is **anti-foaming agents**, which prevent the formation of bubbles within the ink, ensuring smooth and consistent application without interruptions. **Stabilizers**, on the other hand, are designed to maintain the chemical and physical integrity of the ink over time. **UV stabilizers** are a key example; these compounds absorb ultraviolet light that could otherwise cause the ink to degrade or discolor. This is vital for inks used in outdoor applications or those exposed to sunlight, as it ensures that the printed material retains its vibrancy and clarity. **Antioxidants** are another type of stabilizer that protect the ink from oxidative reactions, which can lead to spoilage or changes in color. By preventing these reactions, antioxidants help extend the shelf life of the ink and maintain its consistency during storage and use. Additionally, **pH adjusters** and **buffering agents** are used to stabilize the pH level of the ink, which is crucial for maintaining its chemical stability and preventing unwanted reactions that could affect its performance. These agents help in maintaining a stable pH environment, ensuring that the ink remains compatible with various substrates and printing systems. **Corrosion inhibitors** are also important stabilizers, especially in metal-based inks, as they prevent corrosion of metal components in printing equipment, thereby extending the lifespan of machinery and reducing maintenance costs. The careful selection and integration of these additives and stabilizers into ink formulations require a deep understanding of their interactions with other components such as pigments, dyes, solvents, and binders. This balance is critical because excessive use of additives can sometimes have adverse effects on the ink's performance or environmental impact. Therefore, manufacturers must conduct thorough testing to ensure that the final product meets both functional requirements and regulatory standards. In summary, additives and stabilizers are indispensable elements in the chemical composition of ink. They enhance the ink's functionality by improving its flow characteristics, preventing degradation, and ensuring long-term stability. By understanding the roles these components play, manufacturers can create high-quality inks that meet diverse application needs while maintaining durability and consistency. This attention to detail in ink formulation underscores the complexity and sophistication involved in producing a seemingly simple yet highly versatile substance like ink.
Types of Ink and Their Ingredients
In the world of printing and writing, the type of ink used can significantly impact the quality, durability, and aesthetic appeal of the final product. Understanding the different types of ink and their ingredients is crucial for both professionals and enthusiasts. This article delves into three primary categories of ink: dye-based ink, pigment-based ink, and specialty inks such as UV and metallic. Each type has its unique characteristics, advantages, and applications. Dye-based ink, for instance, is known for its vibrant colors and fluid consistency, making it ideal for certain printing processes. Pigment-based ink, on the other hand, offers superior lightfastness and durability, making it a favorite among artists and printers seeking long-lasting results. Specialty inks, including UV and metallic varieties, cater to specific needs such as security printing and decorative designs. By exploring these categories in depth, readers will gain a comprehensive understanding of how different inks are formulated and how they can be best utilized. Let's begin by examining the properties and uses of dye-based ink, a versatile and widely used type of ink in various applications.
1. Dye-Based Ink
**Dye-Based Ink** Dye-based ink is one of the most commonly used types of ink, particularly in consumer-grade printers and writing instruments. Unlike pigment-based ink, which relies on finely ground particles suspended in a liquid carrier, dye-based ink dissolves the colorants directly into the liquid. This dissolution process results in a more fluid and consistent ink flow, making it ideal for high-speed printing applications. The primary components of dye-based ink include water, dyes, surfactants, and other additives. The dyes themselves are typically organic compounds that are highly soluble in water. These dyes can be derived from various sources, including synthetic chemicals and natural substances like plants and minerals. The solubility of these dyes allows them to penetrate deeply into the paper or other printing surfaces, producing vibrant and uniform colors. Surfactants play a crucial role in dye-based ink by reducing the surface tension of the liquid, enabling it to spread evenly across the printing surface. This ensures that the ink adheres well to the paper and dries quickly without forming blobs or streaks. Additionally, surfactants help in maintaining the stability of the ink by preventing the dyes from precipitating out of solution over time. Other additives in dye-based ink may include humectants to prevent drying out, anti-foaming agents to reduce foam formation during printing, and UV stabilizers to protect the ink from fading due to exposure to sunlight. These additives collectively enhance the performance and longevity of the ink. One of the key advantages of dye-based ink is its ability to produce a wide range of colors with high chromatic intensity. However, it also has some limitations. For instance, dye-based ink tends to be less lightfast compared to pigment-based ink, meaning it can fade more quickly when exposed to sunlight. Additionally, because it penetrates deeply into paper, it may not be as suitable for archival purposes or applications where long-term color stability is critical. Despite these limitations, dye-based ink remains a popular choice for everyday printing needs due to its cost-effectiveness and ease of use. Its fluid consistency makes it well-suited for inkjet printers, which rely on precise droplet placement to create detailed images. In summary, dye-based ink offers a balance of color vibrancy, ease of application, and affordability that makes it an indispensable tool in both personal and commercial printing contexts.
2. Pigment-Based Ink
Pigment-based ink is a type of ink that relies on finely ground pigments suspended in a liquid carrier to produce its color and writing properties. Unlike dye-based inks, which dissolve in the carrier fluid, pigment-based inks maintain their solid form, ensuring greater lightfastness and durability. This characteristic makes pigment-based inks ideal for applications where longevity and resistance to fading are crucial, such as in archival documents, fine art printing, and high-quality commercial printing. The composition of pigment-based ink includes several key components. The pigments themselves are typically derived from minerals or synthetic materials and are chosen for their vibrant colors and stability. Common pigments include carbon black for black ink, iron oxide for reds and yellows, and titanium dioxide for whites. These pigments are ground into extremely fine particles to ensure even dispersion and optimal color consistency. The liquid carrier in pigment-based ink serves multiple purposes: it facilitates the flow of the ink through the printing or writing instrument, helps to suspend the pigments evenly, and often includes additives to enhance performance. Glycerin, for example, is commonly added to improve flow characteristics and prevent clogging in pens and printers. Surfactants may also be included to reduce surface tension and improve wetting properties on various substrates. One of the significant advantages of pigment-based ink is its resistance to water and light. Because the pigments do not dissolve in water, they are less likely to bleed or run when exposed to moisture, making them suitable for use in fountain pens and other writing instruments where water resistance is important. Additionally, the solid nature of the pigments provides better UV stability, meaning that the colors will remain vibrant over time without significant fading. However, pigment-based inks also have some limitations. Due to the particulate nature of the pigments, these inks can be more prone to clogging in fine-tip pens or high-resolution printers if not properly formulated. Moreover, because pigments do not dissolve completely in the carrier fluid, they may require more aggressive agitation or stirring before use to ensure uniform dispersion. In summary, pigment-based ink offers superior durability and color retention compared to dye-based alternatives, making it a preferred choice for applications requiring long-lasting results. Its unique composition of finely ground pigments suspended in a carefully formulated carrier fluid ensures optimal performance across various printing and writing technologies. While it presents some challenges related to clogging and dispersion, these can be mitigated through proper formulation and handling practices. As such, pigment-based ink remains an essential tool in industries where high-quality, enduring prints are paramount.
3. Specialty Inks (e.g., UV, Metallic)
Specialty inks, such as UV and metallic inks, are designed to offer unique properties that set them apart from conventional printing inks. **UV Inks**, for instance, are formulated to cure under ultraviolet light rather than through evaporation or heat. This curing process allows UV inks to maintain their vibrancy and durability on a wide range of surfaces, including plastics, metals, and non-porous materials. The ingredients in UV inks typically include photoinitiators that react to UV light, monomers which form the polymer matrix, and pigments or dyes for color. These components work together to create a fast-drying, scratch-resistant finish that is ideal for applications such as packaging, labels, and industrial printing. **Metallic Inks**, on the other hand, are engineered to produce a reflective, metallic appearance. These inks contain metallic powders or flakes—commonly aluminum or bronze—that give the printed surface a shiny, mirror-like finish. The metallic particles are usually suspended in a carrier fluid along with binders and other additives to ensure even dispersion and adhesion. Metallic inks are often used in luxury packaging, automotive coatings, and decorative printing where a high-end aesthetic is desired. Their ability to add depth and visual appeal makes them a popular choice for branding and marketing materials. Both UV and metallic inks require specialized printing equipment and techniques due to their unique properties. For example, UV inks need UV curing lamps to initiate the polymerization process, while metallic inks may require specific gravure or flexographic presses to handle the heavy metal content effectively. Despite these additional requirements, these specialty inks offer unparalleled benefits in terms of durability, appearance, and versatility, making them indispensable tools in various industries where high-quality finishes are paramount. By understanding the ingredients and applications of these specialty inks, printers and designers can leverage their unique advantages to create innovative and visually striking products that stand out in the market.
Manufacturing Process and Quality Control
In the realm of manufacturing, the pursuit of excellence is a multifaceted endeavor that involves meticulous attention to detail at every stage. The manufacturing process, when executed with precision and care, ensures that the final product meets the highest standards of quality. This article delves into the critical components of this process, highlighting three pivotal aspects: raw material selection, mixing and blending, and testing and quality assurance. Each of these stages plays a crucial role in the overall quality of the product. The selection of raw materials sets the foundation for the entire process, as it directly impacts the final product's characteristics. The mixing and blending phase ensures uniformity and consistency, which are essential for maintaining quality. Finally, rigorous testing and quality assurance protocols guarantee that the product adheres to stringent standards before it reaches the market. By understanding these interconnected stages, manufacturers can optimize their processes to produce high-quality products consistently. Let us begin by examining the first and most fundamental step: raw material selection.
1. Raw Material Selection
**Raw Material Selection** The foundation of high-quality ink lies in the meticulous selection of raw materials, a critical step that significantly influences the final product's performance, durability, and aesthetic appeal. This process involves a thorough evaluation of various components, each contributing unique properties essential for the ink's intended use. For instance, pigments or dyes are chosen based on their color strength, lightfastness, and chemical stability. Pigments, which are finely ground powders, offer superior lightfastness and durability compared to dyes, making them ideal for applications requiring long-term color retention such as printing on fabrics or plastics. Dyes, on the other hand, are dissolved in the ink vehicle and are often used in writing instruments where fluidity and quick-drying properties are paramount. The ink vehicle, typically a mixture of solvents and binders, plays a crucial role in maintaining the ink's viscosity and ensuring it adheres well to the substrate. Solvents like water, glycerin, or volatile organic compounds (VOCs) help in achieving the desired consistency and flow characteristics. Binders such as polymers or resins enhance the ink's adhesion and resistance to wear and tear. Additives like surfactants, defoamers, and UV stabilizers are also incorporated to improve wetting properties, prevent foam formation during application, and protect the ink from ultraviolet degradation. The quality of these raw materials is rigorously tested to ensure they meet stringent standards. Suppliers are often vetted through rigorous audits to guarantee consistency in material quality. Laboratory tests are conducted to verify the purity, concentration, and compatibility of each component. For example, pigment dispersion tests assess how well pigments are dispersed within the ink vehicle, while viscosity measurements ensure that the ink flows smoothly through printing heads or writing tips. Moreover, environmental and health considerations are increasingly important in raw material selection. Manufacturers are shifting towards eco-friendly alternatives such as bio-based solvents and pigments derived from natural sources. This not only reduces the environmental footprint but also aligns with consumer preferences for sustainable products. Regulatory compliance is another key factor; materials must adhere to local and international standards regarding toxicity, flammability, and other safety parameters. In summary, the careful selection of raw materials is a cornerstone of ink manufacturing. It requires a deep understanding of the chemical and physical properties of each component and their interactions within the ink formulation. By choosing high-quality raw materials and ensuring their compatibility and performance, manufacturers can produce inks that meet or exceed industry standards for quality, reliability, and sustainability. This meticulous approach to raw material selection is integral to maintaining the integrity of the manufacturing process and ensuring consistent quality control throughout production.
2. Mixing and Blending
In the intricate process of ink manufacturing, mixing and blending are crucial steps that ensure the final product meets stringent quality standards. This phase involves combining various raw materials, such as pigments, dyes, resins, solvents, and additives, in precise proportions to achieve the desired color, consistency, and performance characteristics. The mixing process typically begins with the dispersion of pigments or dyes in a solvent or resin medium. High-speed mixers or grinding mills are often employed to break down pigment particles into a uniform dispersion, ensuring that the color is evenly distributed throughout the ink. Blending follows the dispersion stage, where different components are combined according to a carefully formulated recipe. This step requires meticulous attention to detail, as even slight variations in the ratio of ingredients can significantly impact the ink's viscosity, flow characteristics, and overall performance. Advanced mixing technologies, such as ultrasonic mixers or high-shear blenders, may be used to ensure thorough homogenization of the mixture. Additionally, quality control measures are integrated at this stage to monitor parameters like pH levels, viscosity, and particle size distribution. To maintain consistency and quality, manufacturers often implement automated systems that can accurately measure and dispense ingredients. These systems minimize human error and ensure that each batch of ink adheres to the specified formulation. Furthermore, inline monitoring and testing during the mixing and blending process allow for real-time adjustments to be made, ensuring that the final product meets or exceeds industry standards. The importance of mixing and blending cannot be overstated; these processes directly influence the ink's performance in various applications, from printing on paper to digital displays. For instance, inks used in high-speed printing presses require optimal viscosity to maintain consistent flow rates, while inks for digital displays must have precise color stability to ensure vibrant and accurate color reproduction. In summary, the mixing and blending stages in ink manufacturing are pivotal for producing high-quality inks that meet specific performance criteria. By leveraging advanced technologies and rigorous quality control measures, manufacturers can ensure that their inks deliver consistent results across a wide range of applications, thereby enhancing the overall quality and reliability of the final product. This meticulous approach underscores the commitment to excellence that defines the ink manufacturing process.
3. Testing and Quality Assurance
Testing and Quality Assurance are pivotal components of the manufacturing process, ensuring that the final product meets stringent standards and consumer expectations. In the context of ink production, these phases are crucial for guaranteeing the consistency, performance, and safety of the ink. The testing phase involves a series of rigorous evaluations to assess various properties of the ink, such as viscosity, color strength, lightfastness, and chemical stability. Viscosity testing, for instance, determines the flow characteristics of the ink, which is essential for its application in different printing technologies like offset, screen, or digital printing. Color strength tests measure the intensity and vibrancy of the ink's hue, while lightfastness tests evaluate how well the ink resists fading when exposed to light. Chemical stability tests ensure that the ink does not degrade over time or react adversely with other materials it may come into contact with. Quality Assurance (QA) processes are integrated throughout the manufacturing cycle to prevent defects and ensure compliance with industry standards. This includes raw material inspection, where suppliers are vetted and materials are tested for purity and quality before being used in production. During the manufacturing process, QA involves regular sampling and testing of batches to detect any deviations from specifications. This proactive approach helps in identifying and addressing potential issues early on, thereby minimizing waste and reducing the risk of defective products reaching the market. Additionally, QA protocols include documentation and record-keeping, which facilitate traceability and accountability. This not only enhances transparency but also aids in continuous improvement by providing valuable data for process optimization. Furthermore, many ink manufacturers adhere to international standards such as ISO 9001 for quality management systems and ISO 14001 for environmental management. These certifications underscore a commitment to quality and sustainability, reassuring customers that the ink is produced under controlled conditions that prioritize both product excellence and environmental responsibility. The culmination of these efforts results in high-quality ink that performs reliably across various applications, from artistic creations to industrial printing processes. By emphasizing testing and quality assurance, manufacturers can build trust with their customers, maintain a competitive edge in the market, and contribute to the overall integrity of the products they produce. Ultimately, this meticulous attention to detail ensures that every batch of ink meets or exceeds customer expectations, reflecting a dedication to excellence that is integral to the manufacturing process.