What Are 3 Things Required On A Workplace Label

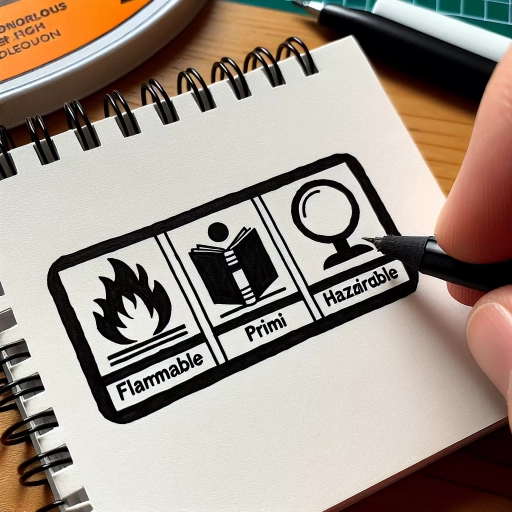
In today's fast-paced and safety-conscious work environments, accurate labeling is crucial for ensuring the well-being of employees and the efficiency of operations. Workplace labels serve as vital communication tools, providing essential information that helps prevent accidents, streamline processes, and maintain compliance with regulations. There are three key components that must be included on these labels to make them effective: essential information, safety and health warnings, and handling and storage instructions. Essential information includes details about the product or substance being labeled, such as its name, composition, and intended use. Safety and health warnings alert workers to potential hazards associated with the product, helping them take necessary precautions. Finally, handling and storage instructions guide employees on how to safely manage and store the product to avoid accidents. By understanding these critical elements, workplaces can significantly reduce risks and enhance overall safety. Let's start by delving into the first of these components: essential information.
1. Essential Information
When delving into the essential information about a product, it is crucial to consider several key aspects that ensure safety, compliance, and informed decision-making. This article will provide a comprehensive overview of three critical components: the product name and manufacturer, hazard statements and pictograms, and precautionary statements. Understanding the product name and manufacturer is fundamental as it establishes accountability and traceability. Knowing who produced the product can help in identifying potential risks and benefits associated with its use. Additionally, hazard statements and pictograms serve as vital warnings about the dangers a product may pose, enabling users to take necessary precautions. Finally, precautionary statements offer guidance on how to safely handle and use the product, minimizing risks to health and environment. By examining these elements, users can make well-informed decisions and ensure safe usage. Let's begin by exploring the first of these essential components: the product name and manufacturer.
1.1 Product Name and Manufacturer
When it comes to ensuring compliance and safety in the workplace, one of the critical components is the accurate labeling of products. This is where the **Product Name and Manufacturer** information becomes paramount. Under the umbrella of essential information required on a workplace label, the product name and manufacturer details serve as foundational elements that help in identifying the substance, understanding its potential hazards, and facilitating proper handling and use. The **Product Name** is a clear and concise identifier that distinguishes one product from another. It must be specific enough to avoid confusion with other substances, ensuring that workers can quickly identify what they are dealing with. This name should align with the chemical name or common name as listed in the Safety Data Sheet (SDS) or other regulatory documents. For instance, if a label reads "Bleach," it should correspond to the SDS for that particular bleach product, providing a direct link to detailed safety information. The **Manufacturer** section is equally important as it provides contact information for the entity responsible for producing the substance. This includes the name, address, and phone number of the manufacturer or distributor. Having this information readily available allows workers to reach out for additional safety data, report any adverse reactions, or seek guidance on proper use and disposal. It also holds the manufacturer accountable for ensuring that their product meets safety standards and regulations. In compliance with regulations such as OSHA's Hazard Communication Standard (HCS) in the United States or similar standards in other countries, these details must be prominently displayed on the label. This ensures that workers have immediate access to crucial information that can prevent accidents and protect their health. For example, if a worker is exposed to a chemical and needs immediate medical attention, knowing the product name and manufacturer can expedite the process of obtaining necessary safety data sheets and emergency contact information. Moreover, accurate labeling helps in maintaining a safe work environment by facilitating proper storage, handling, and disposal practices. It also aids in training programs where workers need to understand the specific risks associated with each product they handle. By including both the product name and manufacturer on labels, employers can demonstrate their commitment to workplace safety and compliance with regulatory standards. In summary, the inclusion of **Product Name and Manufacturer** on workplace labels is not just a regulatory requirement but a critical step in ensuring workplace safety. These details provide essential information that helps workers identify substances accurately, understand their hazards, and seek necessary support when needed. As part of the broader framework of essential information required on workplace labels, these elements play a pivotal role in safeguarding health and preventing accidents in various industrial settings.
1.2 Hazard Statements and Pictograms
When it comes to ensuring safety in the workplace, one of the critical components is the proper use of hazard statements and pictograms on labels. These elements are essential for communicating potential dangers associated with chemicals and other hazardous substances, thereby protecting workers from harm. Hazard statements are concise phrases that describe the nature of the hazard posed by a substance, such as "Toxic if inhaled" or "Causes skin irritation." These statements are standardized to ensure clarity and consistency across different products and regions, making it easier for workers to understand the risks involved. Pictograms, on the other hand, are visual symbols that convey hazard information quickly and effectively. These symbols are designed to be universally understood, transcending language barriers and ensuring that critical safety information is communicated clearly to all workers. For example, the skull and crossbones pictogram indicates acute toxicity, while the exclamation mark symbol signifies irritation or other health hazards. The combination of hazard statements and pictograms provides a comprehensive warning system that alerts workers to potential dangers and guides them in handling substances safely. The use of hazard statements and pictograms is mandated by various regulatory bodies, such as the Occupational Safety and Health Administration (OSHA) in the United States and the European Chemicals Agency (ECHA) in Europe. These regulations, such as OSHA's Hazard Communication Standard (HCS) and the Globally Harmonized System of Classification and Labelling of Chemicals (GHS), specify the types of statements and pictograms that must be used on labels to ensure uniformity and effectiveness in hazard communication. In practice, workplace labels that include hazard statements and pictograms serve multiple purposes. They not only warn workers about immediate dangers but also provide guidance on safe handling practices, first aid measures, and emergency procedures. For instance, a label might include a hazard statement like "May cause respiratory irritation" along with a pictogram of a gas cylinder, indicating that the substance can release harmful vapors. This information helps workers take necessary precautions, such as wearing appropriate personal protective equipment (PPE) or ventilating the area. Moreover, these labels play a crucial role in training and education programs within the workplace. By familiarizing workers with the meanings of different hazard statements and pictograms, employers can enhance overall safety awareness and compliance with safety protocols. This proactive approach to hazard communication reduces the risk of accidents and ensures a safer working environment for everyone. In summary, hazard statements and pictograms are indispensable components of workplace labels, providing critical safety information that protects workers from chemical hazards. Their standardized use ensures clarity, consistency, and effectiveness in communicating potential dangers, thereby fostering a safer and more informed workplace culture. As part of essential information required on workplace labels, these elements are vital for maintaining compliance with regulatory standards and promoting overall workplace safety.
1.3 Precautionary Statements
### 1.3 Precautionary Statements Precautionary statements are a critical component of workplace labels, serving as a direct communication tool to ensure the safe handling, use, and storage of hazardous substances. These statements are designed to provide clear, concise instructions that mitigate risks associated with chemical exposure. According to the Globally Harmonized System of Classification and Labelling of Chemicals (GHS), precautionary statements are categorized into four types: prevention, response, storage, and disposal. **Prevention Statements** aim to prevent adverse effects by advising on safe practices. For example, "Wear protective gloves/protective clothing/eye protection/face protection" or "Avoid breathing dust/fume/gas/mist/vapours/spray." These statements are crucial for minimizing exposure risks during the handling of hazardous materials. **Response Statements** guide users on how to react in case of an emergency or exposure. Examples include "If inhaled: Remove person to fresh air and keep comfortable for breathing" or "If skin irritation occurs: Get medical advice/attention." These instructions are vital for immediate response actions that can significantly reduce the severity of adverse effects. **Storage Statements** provide guidance on how to store hazardous substances safely. For instance, "Store in a well-ventilated place. Keep cool" or "Store locked up." Proper storage practices are essential for preventing accidents and ensuring that chemicals do not degrade over time. **Disposal Statements** outline the appropriate methods for disposing of hazardous substances. Examples include "Dispose of contents/container to an approved waste disposal plant" or "Collect spillage." Correct disposal is crucial for environmental protection and preventing contamination. Incorporating these precautionary statements on workplace labels ensures that employees are well-informed about the necessary precautions to take when working with hazardous chemicals. This not only enhances workplace safety but also complies with regulatory requirements, thereby reducing the risk of accidents and ensuring a healthier work environment. By following these guidelines, employers can foster a culture of safety and responsibility within their organization. In summary, precautionary statements are an indispensable part of workplace labels, providing essential information that helps prevent accidents, respond to emergencies, store chemicals safely, and dispose of them properly. Their inclusion is a key requirement for maintaining a safe and compliant workplace environment.
2. Safety and Health Warnings
When it comes to ensuring safety and health, it is crucial to be aware of the various hazards that can pose risks to individuals and the environment. This article delves into three critical areas: physical hazards, health hazards, and environmental hazards. Each of these categories presents unique challenges that must be addressed to maintain a safe and healthy environment. Physical hazards, such as slips, trips, and falls, or machinery malfunctions, can lead to immediate injuries and accidents. Health hazards, including exposure to toxic substances or infectious diseases, can have long-term effects on well-being. Environmental hazards, such as pollution and climate change, impact not only human health but also the planet's ecosystem. Understanding these different types of hazards is essential for implementing effective safety measures and mitigating risks. In the following sections, we will explore each of these areas in detail, starting with physical hazards, which are often the most immediate and visible threats to safety.
2.1 Physical Hazards
### 2.1 Physical Hazards Physical hazards in the workplace are a significant concern for safety and health, as they can lead to immediate and severe injuries or even fatalities. These hazards encompass a wide range of potential dangers, including but not limited to, tripping hazards, falling objects, electrical hazards, and machinery-related risks. For instance, tripping hazards such as uneven flooring, loose wires, or cluttered walkways can cause slips, trips, and falls—some of the most common workplace accidents. Falling objects, whether from shelves or construction sites, pose a constant threat to employees below, emphasizing the importance of proper storage and securing of materials. Electrical hazards are another critical physical hazard that must be addressed. Poorly maintained electrical equipment, exposed wiring, and overloaded circuits can result in electrical shocks or fires. Ensuring that all electrical systems are regularly inspected and maintained by qualified personnel is crucial. Machinery-related risks also fall under this category; moving parts of machinery can cause severe injuries if proper guards are not in place or if operators are not adequately trained. To mitigate these risks, workplaces must implement robust safety measures. This includes conducting regular risk assessments to identify potential hazards, providing comprehensive training to employees on how to handle equipment safely, and ensuring that all necessary personal protective equipment (PPE) is available and used correctly. Clear labeling of hazardous areas and equipment is also essential; labels should clearly indicate the nature of the hazard and any necessary precautions or safety protocols. In addition to these measures, maintaining a clean and organized workspace is vital. Regular housekeeping practices such as cleaning up spills immediately, securing loose items, and keeping walkways clear can significantly reduce the risk of accidents. Employers must also ensure compliance with relevant safety standards and regulations, such as those set by OSHA (Occupational Safety and Health Administration), to create a safe working environment. By understanding and addressing these physical hazards proactively, workplaces can significantly reduce the risk of injuries and fatalities, thereby fostering a safer and healthier environment for all employees. This proactive approach not only protects workers but also enhances productivity and overall workplace well-being. Therefore, it is imperative for employers to prioritize physical hazard mitigation as part of their broader safety and health strategy.
2.2 Health Hazards
### 2.2 Health Hazards In the context of workplace safety, understanding and mitigating health hazards is crucial for protecting employees from potential harm. Health hazards encompass a broad range of risks that can lead to illness, injury, or even death. These hazards can be categorized into several key areas: chemical, biological, physical, and ergonomic. **Chemical Hazards** are among the most prevalent and include substances such as solvents, pesticides, and heavy metals. Exposure to these chemicals can occur through inhalation, skin contact, or ingestion, leading to acute or chronic health issues. For instance, prolonged exposure to volatile organic compounds (VOCs) can cause respiratory problems and neurological damage. Proper labeling and handling procedures are essential to minimize these risks. **Biological Hazards** involve living organisms or their by-products that can cause disease. These include bacteria, viruses, fungi, and parasites. Workers in healthcare, agriculture, and laboratory settings are particularly at risk. For example, healthcare workers may be exposed to bloodborne pathogens like HIV and hepatitis B, while agricultural workers might encounter zoonotic diseases from animals. **Physical Hazards** refer to environmental factors that can cause harm through physical means. This includes noise pollution, which can lead to hearing loss; extreme temperatures that can cause heat stress or hypothermia; and radiation exposure from sources like X-rays or UV light. In manufacturing environments, workers may be exposed to loud machinery or hazardous materials that emit ionizing radiation. **Ergonomic Hazards** arise from the interaction between workers and their work environment. Poor ergonomics can lead to musculoskeletal disorders (MSDs) such as back strain, carpal tunnel syndrome, and repetitive strain injuries. These issues often result from inadequate workspace design, improper lifting techniques, or prolonged periods of sitting or standing. To effectively manage these health hazards in the workplace, it is imperative to implement robust safety protocols. This includes conducting regular risk assessments to identify potential hazards, providing appropriate personal protective equipment (PPE), and ensuring that all employees receive comprehensive training on safe working practices. Clear labeling of hazardous materials and areas is also critical; labels should include information on the nature of the hazard, necessary precautions, and emergency procedures. In summary, recognizing and addressing health hazards in the workplace is vital for maintaining a safe and healthy environment. By understanding the different types of hazards—chemical, biological, physical, and ergonomic—employers can take proactive steps to protect their employees from harm. Effective labeling and safety protocols are key components of this strategy, ensuring that workers are aware of potential dangers and know how to mitigate them. This not only enhances workplace safety but also contributes to overall employee well-being and productivity.
2.3 Environmental Hazards
### 2.3 Environmental Hazards Environmental hazards pose significant risks not only to human health but also to the ecosystem and overall environmental sustainability. In the context of workplace safety, understanding and mitigating these hazards is crucial for maintaining a safe and healthy environment. One of the primary environmental hazards in the workplace is chemical contamination. Chemicals used in various industrial processes can release harmful fumes, contaminate water sources, and pollute soil. For instance, volatile organic compounds (VOCs) emitted from solvents and cleaning agents can lead to indoor air pollution, causing respiratory issues and other health problems among workers. Another critical environmental hazard is waste management. Improper disposal of hazardous materials can result in soil and groundwater contamination, affecting both local ecosystems and human health. For example, improper disposal of batteries and electronics can lead to the leaching of toxic metals like lead and mercury into the environment. Climate change also plays a role in workplace environmental hazards. Extreme weather events such as heatwaves, floods, and storms can disrupt operations and pose direct risks to workers. For example, heat stress is becoming increasingly common in outdoor work environments due to rising temperatures, leading to dehydration, heat exhaustion, and even death. Additionally, natural disasters can damage infrastructure and disrupt supply chains, further exacerbating environmental hazards. To address these environmental hazards effectively, workplaces must implement robust safety measures. This includes conducting regular risk assessments to identify potential hazards, providing appropriate personal protective equipment (PPE), and ensuring that all employees are trained in safe handling practices for chemicals and waste. Proper ventilation systems should be installed to reduce indoor air pollution, and emergency response plans should be in place for natural disasters. Furthermore, adopting sustainable practices such as recycling programs and energy-efficient technologies can help minimize the overall environmental footprint of the workplace. Incorporating environmental hazard awareness into workplace safety protocols is essential for protecting both human health and the environment. By understanding the risks associated with chemical contamination, waste management, and climate change impacts, employers can take proactive steps to create a safer and more sustainable work environment. This not only ensures compliance with regulatory standards but also fosters a culture of responsibility and sustainability within the organization. Ultimately, addressing environmental hazards is a critical component of maintaining a safe and healthy workplace that benefits both employees and the broader community.
3. Handling and Storage Instructions
When it comes to handling and storing materials, whether they are hazardous chemicals, fragile equipment, or sensitive data, it is crucial to follow strict guidelines to ensure safety, integrity, and compliance. Effective handling and storage practices are multifaceted and involve several key components. First, **safe handling practices** are essential to prevent accidents and injuries. This includes proper training for personnel, use of appropriate protective gear, and adherence to established protocols. Second, **storage conditions** must be carefully managed to maintain the quality and stability of the materials. This involves controlling environmental factors such as temperature, humidity, and exposure to light. Finally, **disposal guidelines** are critical to ensure that materials are disposed of in a manner that is both safe and environmentally responsible. By focusing on these three areas—safe handling practices, storage conditions, and disposal guidelines—we can ensure that our operations are not only efficient but also safe and compliant with regulatory standards. Let's begin by examining the importance of **safe handling practices** in detail.
3.1 Safe Handling Practices
### 3.1 Safe Handling Practices Safe handling practices are crucial for maintaining a secure and healthy work environment, particularly when dealing with hazardous materials or equipment. These practices not only protect the individuals handling the materials but also ensure compliance with regulatory standards and prevent potential accidents. Here are some key elements of safe handling practices that should be integrated into any workplace: **Personal Protective Equipment (PPE):** The use of PPE is fundamental in safeguarding against physical, chemical, and biological hazards. This includes gloves, safety glasses, face masks, and protective clothing tailored to the specific risks associated with the task at hand. Ensuring that all employees are properly trained in the selection, use, and maintenance of PPE is essential. **Proper Lifting Techniques:** Manual handling of heavy objects is a common source of workplace injuries. Employers should educate employees on proper lifting techniques to avoid straining muscles and causing long-term damage. This includes bending at the knees rather than the waist, keeping the load close to the body, and avoiding twisting motions. **Labeling and Signage:** Clear labeling and signage are critical for identifying potential hazards and providing immediate instructions on how to handle materials safely. Workplace labels should include information such as the name of the substance, hazard warnings, first aid instructions, and any necessary precautions or personal protective equipment required. This ensures that all employees are aware of the risks involved and can take appropriate measures to mitigate them. **Training and Supervision:** Comprehensive training programs are vital for ensuring that employees understand and adhere to safe handling practices. Regular training sessions should cover topics such as emergency procedures, spill response protocols, and the correct use of safety equipment. Supervisors play a key role in enforcing these practices by monitoring compliance and addressing any deviations promptly. **Housekeeping:** Maintaining a clean and organized workspace is essential for preventing accidents. This includes ensuring that walkways are clear of obstructions, storing materials in designated areas, and regularly cleaning up spills or leaks. Good housekeeping practices reduce the risk of slips, trips, and falls while also making it easier to identify potential hazards. **Emergency Preparedness:** Having a well-defined emergency response plan in place is crucial for handling unexpected incidents safely. This plan should include procedures for evacuating the area, contacting emergency services, and providing first aid. Regular drills and training exercises help ensure that employees are prepared to respond effectively in emergency situations. By implementing these safe handling practices, workplaces can significantly reduce the risk of injuries and illnesses while fostering a culture of safety and responsibility among employees. This not only enhances workplace safety but also contributes to overall productivity and employee well-being.
3.2 Storage Conditions
### 3.2 Storage Conditions Proper storage conditions are crucial for maintaining the integrity and safety of materials in the workplace. When it comes to handling and storing substances, whether they are chemicals, hazardous materials, or everyday supplies, adhering to specific storage conditions can prevent accidents, ensure compliance with regulations, and protect both the environment and human health. Here are some key considerations: **Temperature Control**: Many substances have optimal temperature ranges for storage. For instance, certain chemicals may degrade or become unstable if exposed to extreme temperatures. Similarly, some pharmaceuticals require refrigeration to maintain their potency. Ensuring that storage areas are climate-controlled can help in preserving the quality of the stored items. **Humidity Levels**: Humidity can significantly impact the stability of materials. For example, moisture-sensitive compounds may react with water vapor, leading to spoilage or hazardous reactions. On the other hand, some materials may require a controlled humidity environment to prevent drying out or becoming brittle. Monitoring and controlling humidity levels in storage areas is essential. **Light Protection**: Light exposure can be detrimental to certain substances. Photodegradable materials, such as some plastics and chemicals, can break down when exposed to UV light. This can lead to a loss of functionality or even the formation of hazardous byproducts. Storing these materials in light-protected areas or using UV-resistant packaging can mitigate these risks. **Ventilation and Air Quality**: Adequate ventilation is vital for preventing the accumulation of fumes or gases that could be hazardous. This is particularly important for storing volatile organic compounds (VOCs) or other substances that release harmful vapors. Ensuring good air quality through proper ventilation systems helps in maintaining a safe working environment. **Segregation and Compatibility**: Different substances should be stored in a way that prevents cross-contamination or incompatible reactions. For example, acids and bases should be stored separately to avoid dangerous chemical reactions. Similarly, flammable materials should be kept away from ignition sources. Segregating substances based on their compatibility ensures that potential hazards are minimized. **Labeling and Signage**: Clear labeling and signage are critical for identifying what is being stored and under what conditions it should be kept. This includes warning labels for hazardous materials, instructions for handling, and indicators of specific storage requirements such as temperature or humidity levels. Proper labeling ensures that employees can handle and store materials safely and correctly. By adhering to these storage conditions, workplaces can significantly reduce the risk of accidents, ensure compliance with safety regulations, and maintain the quality of stored materials. This not only protects employees but also contributes to a more efficient and safe working environment. Implementing these guidelines as part of broader handling and storage instructions is essential for any workplace aiming to prioritize safety and operational excellence.
3.3 Disposal Guidelines
When it comes to ensuring a safe and compliant workplace, proper disposal guidelines are crucial. These guidelines serve as a critical component of the broader handling and storage instructions that are essential for maintaining a secure environment. Here are some key points to consider: **Proper Disposal Methods**: The first step in effective disposal is identifying the appropriate methods for different types of waste. Hazardous materials, such as chemicals and biological agents, require specialized disposal procedures to prevent environmental contamination and health risks. For instance, chemical waste should be segregated based on compatibility and disposed of through licensed facilities that adhere to regulatory standards. Similarly, biological waste must be treated with disinfectants or incinerated according to local regulations. **Labeling and Documentation**: Clear labeling and documentation are vital for ensuring that waste is handled correctly. Workplace labels should include information about the type of waste, its hazards, and the recommended disposal method. This information helps employees understand how to handle each type of waste safely and efficiently. Additionally, maintaining detailed records of waste disposal activities can help in auditing compliance with regulatory requirements. **Training and Awareness**: Employee training is another critical aspect of effective waste disposal. Workers need to be educated on the proper procedures for handling and disposing of various types of waste. Regular training sessions should cover topics such as recognizing hazardous materials, using personal protective equipment (PPE), and following established protocols for waste segregation and disposal. This not only ensures compliance but also fosters a culture of safety within the workplace. **Regulatory Compliance**: Adherence to local, national, and international regulations is paramount when it comes to waste disposal. Employers must familiarize themselves with relevant laws and guidelines that govern waste management in their jurisdiction. For example, the Resource Conservation and Recovery Act (RCRA) in the United States sets standards for hazardous waste management, while the European Union's Waste Framework Directive provides a comprehensive framework for waste management across member states. **Environmental Considerations**: Finally, environmental considerations play a significant role in disposal guidelines. Employers should strive to adopt sustainable practices that minimize environmental impact. This includes recycling where possible, reducing waste generation through efficient processes, and choosing disposal methods that are environmentally friendly. By integrating these practices into their overall waste management strategy, businesses can contribute to a cleaner environment while also enhancing their reputation as responsible corporate citizens. In summary, effective disposal guidelines are an integral part of handling and storage instructions in any workplace. By implementing proper disposal methods, ensuring clear labeling and documentation, providing thorough employee training, adhering to regulatory standards, and considering environmental impact, organizations can ensure a safe and compliant work environment that protects both employees and the environment. These measures not only help in preventing accidents but also contribute to a more sustainable future by promoting responsible waste management practices.