What Is Compressed Air

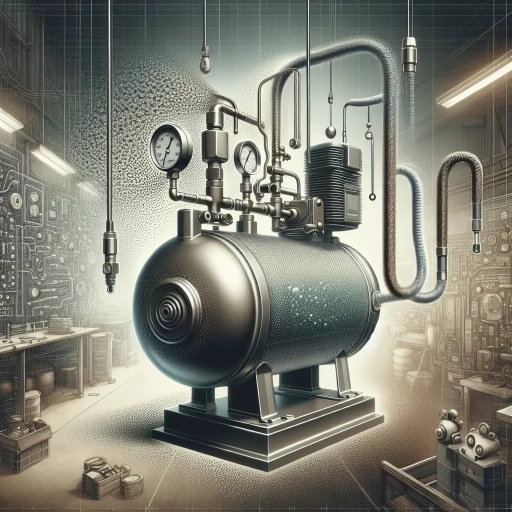
Compressed air is a versatile and essential resource in various industries, from manufacturing and construction to healthcare and automotive. Understanding its fundamental nature, production process, and diverse applications is crucial for appreciating its significance. This article delves into the core aspects of compressed air, starting with a detailed explanation of **What is Compressed Air?**, which clarifies its definition and properties. Next, it explores **How is Compressed Air Produced?**, outlining the mechanical processes involved in compressing air. Finally, it highlights **Uses and Applications of Compressed Air**, showcasing its widespread utility across different sectors. By examining these key facets, readers will gain a comprehensive understanding of compressed air's role and importance. Let's begin by defining the essence of compressed air itself: **What is Compressed Air?**
What is Compressed Air?
Compressed air is a versatile and essential component in various industrial, commercial, and even domestic settings. To fully understand its significance, it is crucial to delve into its definition and basic principles, historical development and applications, as well as the scientific fundamentals of air compression. Starting with the **Definition and Basic Principles**, compressed air is essentially atmospheric air that has been compressed to a pressure higher than normal atmospheric pressure. This process involves reducing the volume of air, which increases its pressure, making it useful for powering tools, machinery, and other equipment. Understanding these principles is fundamental to appreciating how compressed air systems operate and are maintained. The **Historical Development and Applications** of compressed air reveal its evolution from ancient civilizations to modern industries. From powering pneumatic tools in construction to driving machinery in manufacturing, compressed air has become indispensable across multiple sectors. Its applications span from medical devices to automotive systems, highlighting its widespread utility. Finally, the **Scientific Fundamentals of Air Compression** explain the thermodynamic processes involved in compressing air. This includes understanding the laws of thermodynamics, heat transfer, and the mechanics of compression. By grasping these scientific underpinnings, one can better appreciate the efficiency and safety considerations in compressed air systems. To begin our exploration, let's first define what compressed air is and examine its basic principles.
Definition and Basic Principles
Compressed air, a fundamental component in various industrial and commercial applications, is defined as air that has been compressed to a pressure greater than atmospheric pressure. The basic principles underlying compressed air involve the mechanical process of reducing the volume of air, thereby increasing its pressure. This is typically achieved using compressors, which work by drawing in ambient air, compressing it through mechanical or electrical means, and then storing it in tanks or distributing it through a network of pipes. The core principle of compressed air is based on Boyle's Law, which states that for a given mass of an ideal gas at constant temperature, the volume of the gas is inversely proportional to the pressure. By applying this principle, compressors can significantly reduce the volume of air while proportionally increasing its pressure. The efficiency and effectiveness of compressed air systems depend on several key factors, including the type of compressor used (such as reciprocating, rotary screw, or centrifugal), the quality of the air being compressed (which can be affected by moisture content and contaminants), and the design of the distribution system. In practical terms, compressed air is used in a wide range of applications. It powers pneumatic tools like drills and saws in manufacturing and construction, drives machinery in factories, and is essential for various processes in industries such as food processing, pharmaceuticals, and automotive manufacturing. Additionally, compressed air is used in medical devices, dental equipment, and even in consumer products like air guns and paint sprayers. The quality of compressed air is crucial for its intended use. For instance, in medical and food processing applications, the air must be free from contaminants and moisture to ensure safety and product integrity. This necessitates the use of air dryers and filters within the compressed air system to remove impurities and control humidity levels. In summary, compressed air is a versatile medium that leverages mechanical compression to increase air pressure, making it indispensable across diverse sectors. Understanding its definition and basic principles is essential for optimizing its use and ensuring the reliability and efficiency of systems that depend on it. By adhering to these principles and maintaining high standards of air quality, industries can harness the full potential of compressed air to drive productivity and innovation.
Historical Development and Applications
The historical development of compressed air dates back to ancient civilizations, where primitive forms of air compression were used for various purposes. In the 17th century, the first mechanical air compressors were developed, primarily for scientific experiments and industrial applications. By the 19th century, compressed air became a crucial component in mining and construction, facilitating the use of pneumatic tools and improving efficiency significantly. The early 20th century saw the widespread adoption of compressed air in manufacturing, particularly in the automotive and aerospace industries. The invention of the rotary screw compressor in the 1930s revolutionized the field by providing a more efficient and reliable means of air compression. This innovation enabled broader applications across different sectors, including healthcare, where compressed air is used for medical equipment and anesthesia systems. In modern times, compressed air has become an indispensable resource in numerous industries. It powers pneumatic tools such as drills, saws, and sanders in construction and manufacturing. In the food and beverage industry, compressed air is used for packaging, bottling, and cleaning processes. The oil and gas sector relies on compressed air for drilling operations and maintaining equipment. Additionally, compressed air plays a critical role in transportation systems, powering air brakes in trains and buses. In the healthcare sector, it supports life-saving equipment like ventilators and anesthesia machines. The use of compressed air also extends to environmental applications such as wastewater treatment plants and air pollution control systems. Moreover, advancements in technology have led to the development of more efficient compressors with lower energy consumption and reduced noise levels. Modern compressors are designed with sustainability in mind, incorporating features such as variable speed drives and heat recovery systems to minimize environmental impact. Overall, the historical development of compressed air has been marked by continuous innovation and expansion into diverse fields. From its early beginnings in scientific experiments to its current widespread use across various industries, compressed air remains a vital component in modern industrial processes and daily life. Its applications continue to evolve with technological advancements, ensuring its relevance and importance for years to come.
Scientific Fundamentals of Air Compression
The scientific fundamentals of air compression are rooted in the principles of thermodynamics and fluid mechanics. Compressed air is created by reducing the volume of air, which increases its pressure according to Boyle's Law, which states that at constant temperature, the volume of a gas is inversely proportional to the pressure. This process involves forcing air molecules into a smaller space, thereby increasing their kinetic energy and density. The compression process typically occurs in a compressor, where mechanical energy is converted into potential energy stored in the compressed air. There are several types of compressors, including reciprocating, rotary screw, and centrifugal compressors, each operating on different mechanical principles but achieving the same goal of compressing air. During compression, the temperature of the air increases due to the conversion of mechanical work into heat energy, as described by the first law of thermodynamics. This heat generation can be managed through cooling systems to maintain efficiency and prevent overheating. The ideal gas law (PV = nRT) also plays a crucial role in understanding how pressure, volume, and temperature are interrelated during the compression process. In practical applications, compressed air is often stored in tanks to allow for a steady supply of high-pressure air. The storage capacity and pressure rating of these tanks are critical factors in ensuring safe and efficient use of compressed air. Safety considerations include adhering to standards for tank design, regular maintenance, and proper usage to avoid accidents such as tank rupture or air leaks. Understanding the scientific fundamentals of air compression is essential for optimizing its use across various industries, including manufacturing, healthcare, and construction. By grasping these principles, engineers and technicians can design more efficient systems, troubleshoot issues effectively, and ensure the reliable operation of compressed air systems. Additionally, knowledge of these fundamentals aids in selecting the appropriate compressor type and configuration for specific applications, thereby enhancing overall system performance and reducing energy consumption. In summary, the scientific fundamentals of air compression revolve around thermodynamic principles, mechanical energy conversion, and fluid dynamics. These principles guide the design, operation, and maintenance of compressed air systems, ensuring their safe and efficient use across diverse industrial settings.
How is Compressed Air Produced?
Compressed air is a vital component in various industrial, commercial, and even residential applications, serving as a reliable source of power for tools, machinery, and processes. Understanding how compressed air is produced involves delving into several key aspects. First, it is essential to explore the different **Types of Compressors and Their Mechanisms**, as these devices are the heart of any compressed air system. Each type of compressor, whether it be a reciprocating, rotary screw, or centrifugal compressor, operates on distinct principles that affect efficiency and output. Next, the **Steps Involved in the Compression Process** must be examined to grasp the sequential actions that transform ambient air into compressed air. This includes intake, compression, cooling, and storage. Finally, **Energy Consumption and Efficiency Considerations** are crucial for optimizing the production process, as they directly impact operational costs and environmental sustainability. By understanding these elements, one can appreciate the complexity and importance of compressed air production. Let's begin by examining the various types of compressors and their mechanisms.
Types of Compressors and Their Mechanisms
Compressed air is produced through various types of compressors, each with its unique mechanism and application. **Reciprocating Compressors** are the most common type, utilizing pistons and cylinders to compress air. These compressors work on the principle of positive displacement, where the piston moves up and down in the cylinder, drawing in air during the downstroke and compressing it during the upstroke. They are widely used in small-scale industrial applications due to their simplicity and efficiency. **Rotary Screw Compressors** employ two interlocking helical screws that rotate in opposite directions to compress air. As the screws turn, they draw in air through an inlet port and push it out through an outlet port after compression. This type is known for its high efficiency, reliability, and continuous operation, making them ideal for large-scale industrial use. **Centrifugal Compressors** use a spinning impeller to accelerate air, which then passes through a diffuser where the kinetic energy is converted into potential energy, resulting in compressed air. These compressors are typically used in high-flow applications such as power plants and large industrial processes due to their ability to handle high volumes of air. **Axial Compressors** also utilize spinning blades but in a linear fashion along an axis. Air is drawn in at one end and compressed as it passes through multiple stages of blades and stators, which gradually increase the pressure. These compressors are often used in jet engines and gas turbines because of their high flow rates and efficiency. **Scroll Compressors** involve two spiral-shaped members, one fixed and one moving, that orbit each other to compress air. As the moving scroll orbits the fixed scroll, pockets of air are trapped and compressed, then discharged at the center. These compressors are known for their quiet operation and are commonly used in air conditioning systems and refrigeration units. **Diaphragm Compressors** use a flexible diaphragm that moves back and forth to compress air. The diaphragm is typically driven by an electric motor or hydraulic system. These compressors are often used in applications requiring high purity and low contamination levels, such as in laboratories and medical equipment. Each type of compressor has its own set of advantages and disadvantages, making them suitable for different applications based on factors such as flow rate, pressure requirements, noise levels, and maintenance needs. Understanding the mechanisms behind these compressors is crucial for selecting the right type for specific industrial or commercial needs, ensuring efficient and reliable compressed air production.
Steps Involved in the Compression Process
The compression process is a critical component in the production of compressed air, involving several key steps that ensure efficient and safe operation. Here’s a detailed overview: 1. **Intake of Air**: The process begins with the intake of ambient air, which is drawn into the compressor through an inlet valve. This air is typically filtered to remove dust, debris, and other contaminants that could damage the compressor or affect the quality of the compressed air. 2. **Compression**: Once inside the compressor, the air is compressed by reducing its volume. This can be achieved through various methods, including reciprocating (piston) compressors, rotary screw compressors, or centrifugal compressors. Each type of compressor has its own mechanism for compressing air but all increase the pressure by forcing the air into a smaller space. 3. **Cooling**: During compression, the air temperature increases due to the conversion of kinetic energy into heat energy. To manage this heat and prevent overheating, compressors often include cooling systems such as air-cooled or water-cooled heat exchangers. Cooling helps maintain optimal operating temperatures and prevents damage to the compressor. 4. **Storage**: After compression and cooling, the compressed air is stored in a tank or reservoir. This storage allows for a buffer against demand fluctuations and ensures a steady supply of compressed air when needed. The tank also helps to smooth out any pulsations in the airflow from the compressor. 5. **Drying**: Compressed air often contains moisture from the ambient air it was drawn from. To prevent condensation and corrosion in downstream equipment, the compressed air may be dried using desiccant dryers or refrigerated dryers. This step is crucial for maintaining air quality and preventing damage to tools and machinery. 6. **Filtration**: Additional filtration may be applied after drying to remove any remaining impurities such as oil droplets, particulates, or other contaminants that could affect the performance of pneumatic tools or equipment. 7. **Regulation**: The final step involves regulating the pressure of the compressed air to match the requirements of the application. Pressure regulators adjust the output pressure to ensure it remains within a specified range, ensuring consistent performance and safety. 8. **Distribution**: The regulated compressed air is then distributed through a network of pipes to various points of use within a facility. Proper distribution involves ensuring that the piping system is well-maintained, leak-free, and sized appropriately to minimize pressure drops. By following these steps meticulously, compressed air systems can provide reliable, high-quality air for a wide range of industrial, medical, and other applications. Each step plays a vital role in ensuring that the compressed air produced meets the necessary standards for safety, efficiency, and effectiveness.
Energy Consumption and Efficiency Considerations
Energy consumption and efficiency are critical considerations in the production of compressed air, as they directly impact operational costs, environmental footprint, and overall system performance. Compressed air production involves several stages, each with its own energy demands. The primary energy consumer in this process is the compressor itself, which converts electrical or mechanical energy into compressed air. The efficiency of the compressor is a key factor; more efficient compressors can significantly reduce energy consumption. For instance, rotary screw compressors and centrifugal compressors are often preferred for their high efficiency compared to older piston-type compressors. Another crucial aspect is the system's design and maintenance. Properly sized piping and fittings minimize pressure drops, reducing the compressor's workload and subsequent energy consumption. Regular maintenance, such as filter cleaning and oil changes, ensures optimal compressor performance. Additionally, using variable speed drives (VSDs) allows compressors to adjust their output according to demand, further optimizing energy use. Heat recovery systems can also enhance efficiency by capturing waste heat generated during compression and using it for other purposes like heating water or buildings. This not only reduces energy waste but also provides an additional benefit by offsetting heating costs. Furthermore, air leaks in the distribution system can lead to significant energy losses. Identifying and sealing these leaks is essential for maintaining system efficiency. Implementing smart sensors and monitoring systems can help detect leaks early, ensuring that the compressed air system operates at peak efficiency. In terms of broader strategies, companies can adopt best practices such as load management and demand control. This involves matching compressor output with actual demand rather than running at full capacity continuously. Energy audits can also help identify areas where improvements can be made to reduce overall energy consumption. Lastly, selecting the right type of compressor for specific applications is vital. For example, oil-free compressors may be more energy-efficient in certain environments where oil contamination is a concern. Similarly, choosing compressors with advanced technologies like inverter drives can provide better control over airflow rates and pressures, leading to improved efficiency. By focusing on these energy consumption and efficiency considerations, organizations can significantly reduce their operational costs while contributing to a more sustainable future. This holistic approach ensures that compressed air systems are not only effective but also environmentally responsible and cost-efficient.
Uses and Applications of Compressed Air
Compressed air is a versatile and essential component in various sectors, offering a wide range of applications that enhance efficiency, safety, and productivity. This article delves into the diverse uses of compressed air, highlighting its significance in industrial, commercial, and specialized fields. In the industrial realm, compressed air plays a crucial role in manufacturing and automation, powering tools and machinery that drive production processes. Beyond industry, compressed air also finds extensive use in commercial and residential settings, supporting HVAC systems, pneumatic tools, and other essential services. Additionally, its specialized applications extend to medical, aerospace, and other critical sectors where precision and reliability are paramount. By exploring these different facets, we can appreciate the multifaceted nature of compressed air and its indispensable role in modern society. Let us begin by examining its industrial uses, particularly in manufacturing and automation, where compressed air is the backbone of many operational processes.
Industrial Uses: Manufacturing and Automation
In the realm of industrial manufacturing, compressed air plays a pivotal role in enhancing efficiency, productivity, and safety. It is a versatile tool that powers a wide array of machinery and systems, making it an indispensable component in various sectors. For instance, in the automotive industry, compressed air is used to operate pneumatic tools such as drills, wrenches, and sanders, which are essential for assembly lines. Similarly, in textile manufacturing, compressed air drives looms and spinning machines, ensuring smooth fabric production. In food processing, compressed air is utilized for cleaning and conveying food products, maintaining hygiene standards while minimizing manual labor. The pharmaceutical industry also relies heavily on compressed air for sterilization processes and the operation of packaging machinery. Furthermore, in chemical plants, compressed air is used to power pneumatic valves and actuators that control fluid flow, ensuring precise and safe operations. Automation is another critical area where compressed air excels. Pneumatic systems, which are driven by compressed air, are integral to robotic assembly lines and material handling systems. These systems provide the necessary force and precision for tasks such as gripping, lifting, and moving components with high accuracy. Additionally, compressed air is used in control systems to activate solenoid valves and cylinders that manage fluid flow and pressure in automated processes. The use of compressed air also extends to safety mechanisms within industrial settings. For example, it powers safety valves that prevent over-pressurization in boilers and other pressure vessels. In hazardous environments, compressed air can be used to power tools that are intrinsically safe, reducing the risk of ignition from electrical sparks. Moreover, the reliability and simplicity of pneumatic systems make them a preferred choice over hydraulic or electric systems in many applications. Compressed air systems are generally easier to maintain and repair compared to their counterparts, which can significantly reduce downtime and operational costs. This reliability is crucial in high-volume production environments where any interruption can lead to substantial losses. In summary, compressed air is a fundamental resource in industrial manufacturing and automation. Its versatility, reliability, and safety features make it an essential tool across various industries, from automotive and textile manufacturing to food processing and pharmaceutical production. By powering pneumatic tools and systems, compressed air enhances efficiency, productivity, and safety, making it a cornerstone of modern industrial operations.
Commercial and Residential Applications
Compressed air is a versatile and essential component in both commercial and residential settings, offering a wide range of applications that enhance efficiency, safety, and convenience. In commercial environments, compressed air is crucial for various industrial processes. It powers pneumatic tools such as drills, saws, and wrenches, which are indispensable in manufacturing, construction, and automotive industries. Compressed air systems also drive machinery like air compressors, blowers, and vacuum pumps, facilitating tasks such as cleaning, drying, and conveying materials. Additionally, compressed air is used in food processing for packaging, bottling, and canning operations, ensuring hygiene and precision. In healthcare facilities, compressed air supplies power medical equipment like ventilators and anesthesia machines, while in laboratories, it supports critical instruments such as microscopes and spectrometers. In residential settings, compressed air has numerous practical uses that make everyday tasks easier. Homeowners often use portable air compressors for inflating tires, powering air tools like nail guns and impact wrenches for DIY projects, and cleaning hard-to-reach areas with air blow guns. Compressed air can also be used for painting and spraying, providing a smooth finish without the mess of traditional methods. Furthermore, compressed air is essential for maintaining home appliances such as air conditioners and refrigerators by cleaning condenser coils and ensuring optimal performance. For hobbyists and enthusiasts, compressed air powers airbrushes for art projects and pneumatic guns for recreational activities like airsoft and paintball. Overall, the versatility of compressed air makes it an invaluable resource across various sectors, from heavy industry to home maintenance and leisure activities. Its ability to provide consistent power and reliability underscores its importance in modern life.
Specialized Uses: Medical, Aerospace, and More
Compressed air has a multitude of specialized uses across various industries, each leveraging its unique properties to achieve specific goals. In the medical field, compressed air is crucial for powering surgical tools and equipment, such as drills and saws, which require high precision and reliability. It also supports life-saving devices like ventilators and anesthesia machines, ensuring patient safety and comfort. Additionally, compressed air is used in dental procedures for drills and other instruments, enhancing the efficiency and accuracy of treatments. In the aerospace industry, compressed air plays a vital role in the manufacturing and maintenance of aircraft. It powers tools for riveting, drilling, and other tasks that require high torque and speed. Compressed air systems are also integral to the operation of pneumatic systems within aircraft themselves, such as landing gear deployment and brake systems. This ensures the safety and reliability of flight operations. Beyond these sectors, compressed air has numerous other specialized applications. In the automotive industry, it is used for tire inflation, air tools in repair shops, and even in some vehicle systems like air suspension. In industrial settings, compressed air powers pneumatic actuators, valves, and cylinders that drive machinery and automate processes. It is also essential for cleaning and drying surfaces in various manufacturing processes. In the food and beverage industry, compressed air is used for packaging, conveying ingredients, and powering machinery that requires precise control over movement and pressure. For instance, it helps in the bottling process by ensuring consistent pressure to fill containers accurately. Furthermore, compressed air is utilized in environmental monitoring and control systems. For example, it powers samplers that collect air quality data and drives equipment used in wastewater treatment plants to maintain optimal operating conditions. In construction, compressed air supports the operation of pneumatic tools like jackhammers, impact wrenches, and concrete mixers, significantly enhancing productivity and efficiency on job sites. Overall, the versatility of compressed air makes it an indispensable resource across a wide range of industries, each benefiting from its ability to provide consistent power and reliability in diverse applications.