What Size Wire For 30 Amps

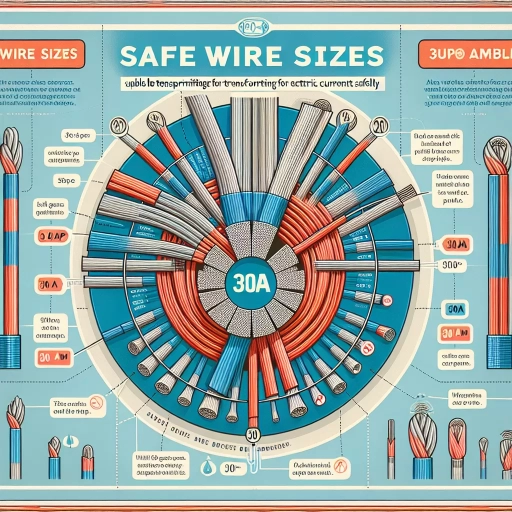
When it comes to electrical wiring, selecting the right wire size for your needs is crucial for safety, efficiency, and compliance with electrical codes. For applications requiring 30 amps, understanding the correct wire size is paramount to avoid overheating, electrical fires, and system failures. This article delves into the essential aspects of wire sizing for 30 amps, starting with **Understanding the Basics of Wire Sizing for 30 Amps**, where we explore the fundamental principles and factors that influence wire size selection. We will then move on to **Calculating the Right Wire Size for 30 Amps**, providing a step-by-step guide on how to determine the appropriate wire size based on specific conditions such as voltage drop and conductor material. Finally, we will discuss **Practical Applications and Safety Considerations**, highlighting real-world scenarios and safety protocols to ensure your electrical setup is both functional and safe. By grasping these key concepts, you will be well-equipped to make informed decisions about your electrical wiring needs. Let's begin by understanding the basics of wire sizing for 30 amps.
Understanding the Basics of Wire Sizing for 30 Amps
Understanding the basics of wire sizing for 30 amps is a crucial aspect of electrical engineering and safety. When dealing with electrical systems, it is imperative to select the correct wire gauge to ensure efficient and safe operation. This article delves into three key areas that highlight the significance of proper wire sizing: the importance of correct wire gauge, factors influencing wire size selection, and the consequences of incorrect wire sizing. Correct wire gauge is fundamental because it directly affects the performance and longevity of electrical circuits. Using a wire that is too small can lead to overheating and potential fires, while a wire that is too large may be wasteful and inefficient. The importance of correct wire gauge cannot be overstated, as it ensures that the electrical current flows smoothly without causing damage to the system or posing a risk to users. Factors influencing wire size selection include the type of material used, the length of the wire, and the ambient temperature. These variables must be carefully considered to determine the optimal wire size for a given application. For instance, longer wires may require a larger gauge to compensate for increased resistance, while higher ambient temperatures may necessitate even larger gauges to prevent overheating. Consequences of incorrect wire sizing can be severe and include reduced system efficiency, increased risk of electrical fires, and potential damage to equipment. Incorrectly sized wires can also lead to premature wear and tear on electrical components, resulting in costly repairs and downtime. In the following sections, we will explore each of these critical aspects in detail, starting with the importance of correct wire gauge. By understanding why the right wire gauge is essential, you will be better equipped to make informed decisions when designing or maintaining electrical systems.
Importance of Correct Wire Gauge
The importance of correct wire gauge cannot be overstated, particularly when it comes to ensuring the safe and efficient transmission of electrical power. In the context of understanding the basics of wire sizing for a 30-amp circuit, selecting the appropriate wire gauge is crucial for several reasons. Firstly, using a wire with an incorrect gauge can lead to overheating, which is a significant safety hazard. When a wire is too small for the current it needs to carry, it can heat up excessively, potentially causing fires or damaging electrical components. Conversely, using a wire that is too large may not pose immediate risks but can be wasteful and unnecessarily expensive. From a performance perspective, correct wire gauge ensures that the electrical system operates efficiently. A wire that is too small will have higher resistance, leading to voltage drops and reduced system performance. This can result in dim lights, slow motor speeds, and other operational issues. On the other hand, a wire that is too large will have lower resistance but may be overkill for the application, adding unnecessary cost and complexity. In addition to safety and performance considerations, correct wire gauge also plays a role in compliance with electrical codes and standards. Most jurisdictions have specific regulations regarding wire sizing based on the National Electric Code (NEC) or similar standards. Using the wrong gauge can result in non-compliance, which may lead to failed inspections and costly rework. For a 30-amp circuit specifically, the American Wire Gauge (AWG) system typically recommends using a 10-gauge wire for most residential applications. This gauge strikes a balance between safety, efficiency, and cost-effectiveness. However, the exact gauge required can vary depending on factors such as the length of the run, ambient temperature, and the type of insulation used. In summary, selecting the correct wire gauge is essential for ensuring the safety, efficiency, and compliance of an electrical system. For a 30-amp circuit, using a 10-gauge wire is generally recommended but should be verified based on specific conditions to avoid potential hazards and performance issues. By understanding and adhering to these guidelines, individuals can ensure their electrical systems operate reliably and safely.
Factors Influencing Wire Size Selection
When selecting the appropriate wire size for a 30-amp electrical circuit, several critical factors must be considered to ensure safety, efficiency, and compliance with electrical codes. **Voltage Drop** is one of the primary considerations; it refers to the loss of voltage as electricity travels through the wire. A smaller wire size can result in a higher voltage drop, which may lead to overheating and reduced system performance. Therefore, it is essential to choose a wire size that minimizes voltage drop while maintaining the required current flow. **Current Carrying Capacity** is another crucial factor. The wire must be able to handle the maximum current load without overheating or failing. For a 30-amp circuit, the wire size should be sufficient to carry this current safely over the expected distance. **Insulation Type** also plays a significant role; different insulation materials have varying temperature ratings and resistance to environmental factors such as moisture and chemicals. For instance, wires with PVC insulation are common but may not be suitable for high-temperature applications or outdoor use without additional protection. **Ambient Temperature** affects the wire's ability to dissipate heat generated by electrical resistance. In hotter environments, wires may need to be upsized to prevent overheating. Conversely, in cooler environments, smaller wires might suffice. **Conductor Material** is another important consideration; copper and aluminum are common materials used in electrical wiring. Copper is generally preferred due to its higher conductivity and durability, but it is more expensive than aluminum. **Distance** between the power source and the load is also a key factor. Longer distances require larger wire sizes to compensate for increased resistance and potential voltage drop. Additionally, **Bundle Size** and **Number of Conductors** in a cable can impact the overall size needed; more conductors in a bundle can increase the required wire size due to mutual heating effects. **Local Electrical Codes** and **Standards** must be adhered to when selecting wire sizes. These codes often specify minimum requirements based on the factors mentioned above and ensure compliance with safety standards. For example, the National Electric Code (NEC) provides guidelines for wire sizing based on ampacity tables that account for various conditions. In summary, selecting the right wire size for a 30-amp circuit involves a careful analysis of voltage drop, current carrying capacity, insulation type, ambient temperature, conductor material, distance, bundle size, and adherence to local electrical codes. By considering these factors comprehensively, you can ensure that your electrical system operates safely and efficiently. This understanding is fundamental to designing reliable and compliant electrical circuits.
Consequences of Incorrect Wire Sizing
Incorrect wire sizing can have severe and far-reaching consequences, making it crucial to understand the basics of wire sizing, especially when dealing with a 30-amp circuit. One of the most immediate risks is overheating, which occurs when a wire is too small to handle the current load. Overheated wires can lead to insulation melting, exposing the conductive core and increasing the risk of electrical fires. These fires can be devastating, causing significant property damage and potentially endangering lives. Furthermore, overheating can also reduce the lifespan of electrical components and appliances connected to the circuit, leading to premature failures and costly repairs. In addition to fire hazards, incorrect wire sizing can result in voltage drops, which affect the performance of electrical devices. When a wire is undersized, it offers higher resistance to the flow of current, causing a drop in voltage at the point of use. This can lead to inefficient operation of appliances, reduced power output, and even complete system failures. For instance, in a 30-amp circuit powering a heating system or an electric motor, an undersized wire could cause the device to run at lower efficiency or not at all, leading to discomfort or operational downtime. Another critical consequence is the potential for electrical shock. If a wire is not sized correctly and becomes overheated or damaged, it can compromise the integrity of the insulation, creating a path for electricity to flow through unintended routes. This increases the risk of electrical shock to individuals who come into contact with the wiring or connected devices. Electrical shock can range from minor injuries to life-threatening conditions, making proper wire sizing essential for safety. From an economic perspective, incorrect wire sizing can lead to significant financial losses. Overheated wires and subsequent electrical fires may result in costly repairs or replacements of damaged equipment and property. Additionally, frequent replacements of prematurely failed components due to voltage drops or overheating add up over time, increasing maintenance costs. In some cases, incorrect wiring may also lead to fines or penalties if it violates local electrical codes and standards. Moreover, incorrect wire sizing can impact the reliability and longevity of an electrical system. Properly sized wires ensure that the system operates within safe and efficient parameters, extending the lifespan of both the wiring and connected devices. Conversely, undersized wires can lead to chronic issues such as flickering lights, intermittent power losses, and frequent circuit breaker trips, all of which indicate underlying problems that need immediate attention. In conclusion, the consequences of incorrect wire sizing are multifaceted and severe. They include increased risks of electrical fires and shocks, reduced efficiency and performance of electrical devices, higher maintenance costs, and potential economic losses. Therefore, it is imperative to understand and apply the correct principles of wire sizing for any given current load, such as a 30-amp circuit, to ensure safety, efficiency, and reliability in electrical systems. By doing so, individuals can avoid these detrimental outcomes and ensure their electrical installations operate optimally and securely.
Calculating the Right Wire Size for 30 Amps
When it comes to ensuring the safe and efficient transmission of electrical power, calculating the right wire size is paramount. For a 30-amp circuit, several key factors must be considered to avoid overheating, voltage drops, and potential safety hazards. The process begins with understanding the American Wire Gauge (AWG) system, which provides a standardized method for selecting wires based on their diameter and current-carrying capacity. However, this is just the starting point. It is equally important to consider voltage drop and distance, as these factors can significantly impact the performance and reliability of the electrical circuit. Additionally, accounting for environmental factors such as temperature, humidity, and exposure to elements is crucial for long-term durability and safety. By meticulously evaluating these aspects, you can ensure that your wiring system is both high-quality and reliable. Let's start by delving into the foundational aspect of wire sizing: Using the American Wire Gauge (AWG) System.
Using the American Wire Gauge (AWG) System
When calculating the right wire size for a 30-amp circuit, understanding the American Wire Gauge (AWG) system is crucial. The AWG system is a standardized method for measuring the diameter of electrical wires, with smaller gauge numbers indicating larger wire diameters and higher current-carrying capacities. This system is essential because it directly influences the safety and efficiency of electrical installations. For a 30-amp circuit, you need to select a wire that can handle the current without overheating or causing a fire hazard. The AWG system helps in this selection by providing a clear correlation between wire size and current capacity. For instance, according to the National Electric Code (NEC), a 10-gauge wire is typically recommended for circuits up to 30 amps at 120/240 volts. This is because a 10-gauge wire has a sufficient cross-sectional area to carry the current without excessive resistance, which could lead to overheating. Using the AWG system involves considering several factors, including the type of insulation, ambient temperature, and the length of the wire run. For example, if you are running wires through hot attics or areas with high ambient temperatures, you may need to use a larger gauge wire to compensate for the increased resistance due to heat. Additionally, longer wire runs require larger gauges to minimize voltage drop and ensure reliable operation. The AWG system also accounts for different types of wire materials such as copper and aluminum. Copper wires generally have better conductivity and are more commonly used in residential and commercial applications. However, aluminum wires can be cost-effective alternatives but require larger gauges due to their lower conductivity compared to copper. In practice, using the AWG system involves consulting tables or charts that list the maximum current-carrying capacity for each gauge size under various conditions. These resources are often provided in electrical codes and standards documents like the NEC. By referencing these tables and considering specific installation conditions, electricians and DIY enthusiasts can accurately determine the appropriate wire size for their needs. In summary, the AWG system is a vital tool for ensuring that electrical installations are safe and efficient. By understanding how to apply this system when calculating wire sizes for specific current requirements like 30 amps, individuals can avoid potential hazards such as overheating and electrical fires. It underscores the importance of precision in electrical work and highlights why adhering to standardized gauging systems is paramount in maintaining electrical safety standards.
Considering Voltage Drop and Distance
When calculating the right wire size for a 30-amp circuit, it is crucial to consider the impact of voltage drop and distance. Voltage drop occurs when electrical current flows through a conductor, causing a reduction in voltage due to the resistance of the wire. This phenomenon can lead to inefficiencies, overheating, and even safety hazards if not properly managed. The distance between the power source and the load significantly affects voltage drop; longer distances result in greater voltage drops due to increased resistance. To mitigate these issues, electrical engineers and technicians use various tools and guidelines. The National Electric Code (NEC) provides tables and formulas that help determine the appropriate wire size based on current, voltage, and distance. For instance, using the NEC's voltage drop tables, one can calculate the maximum allowable voltage drop for a given circuit. Typically, this is set at 3% for branch circuits and 5% for feeder circuits to ensure that the voltage at the load remains within acceptable limits. In practical terms, when designing a 30-amp circuit, you would first determine the total length of the wire run from the panel to the load. Then, using NEC tables or online calculators, you would select a wire size that ensures the voltage drop does not exceed the specified percentage. For example, if you are running a 30-amp circuit over 100 feet, you might need to use a larger gauge wire (such as 10 AWG) compared to a shorter run (where 12 AWG might suffice). Additionally, factors such as wire material (copper vs. aluminum), insulation type, and ambient temperature also influence voltage drop calculations. Copper wires generally have lower resistance than aluminum wires, making them preferable for longer runs or higher current applications. Insulation type affects how efficiently heat is dissipated from the wire, which in turn impacts its overall performance under load conditions. In summary, considering voltage drop and distance is essential when determining the right wire size for a 30-amp circuit. By adhering to NEC guidelines and accounting for various factors that influence electrical resistance and heat dissipation, you can ensure safe and efficient operation of your electrical system. Properly sizing your wires not only prevents potential hazards but also maintains optimal performance over time. This meticulous approach underscores the importance of thorough planning in electrical design to guarantee reliable and efficient power delivery.
Accounting for Environmental Factors
When calculating the right wire size for a 30-amp electrical circuit, it is crucial to consider various environmental factors that can significantly impact the performance and safety of the wiring. Environmental conditions such as temperature, humidity, and exposure to sunlight or moisture can affect the wire's insulation and conductor properties. For instance, high temperatures can reduce the wire's ampacity, necessitating larger wire sizes to maintain safe and efficient operation. Similarly, humid or wet conditions may require wires with specialized insulation that can withstand moisture without compromising electrical integrity. Additionally, wires exposed to direct sunlight may degrade faster due to UV radiation, which could necessitate more frequent inspections and replacements. Moreover, the physical environment where the wiring will be installed also plays a critical role. Wires running through attics or crawl spaces may be subjected to extreme temperatures and humidity levels compared to those in climate-controlled areas. In such cases, using wires with higher temperature ratings or specialized insulation can mitigate potential risks. The presence of corrosive substances in industrial settings or coastal areas further complicates the selection process, as wires must be resistant to corrosion to ensure longevity. Another important consideration is the ambient air temperature around the wiring. The National Electric Code (NEC) provides guidelines for derating wires based on ambient temperatures; for example, if the ambient temperature exceeds 86°F (30°C), the wire's ampacity must be reduced accordingly. This ensures that the wiring does not overheat and cause a fire hazard. In summary, accounting for environmental factors is essential when determining the appropriate wire size for a 30-amp circuit. By considering temperature, humidity, exposure conditions, and other environmental elements, you can select wiring that not only meets but exceeds safety standards, ensuring reliable and efficient electrical performance over time. This holistic approach to wire sizing helps prevent overheating, electrical fires, and other hazards associated with inadequate wiring choices. Therefore, it is imperative to consult relevant codes and standards such as those provided by the NEC and to consult with electrical professionals if there are any doubts about the specific environmental conditions of your installation site.
Practical Applications and Safety Considerations
When discussing the practical applications and safety considerations of electrical systems, it is crucial to delve into several key areas. First, understanding the common uses for 30-amp circuits is essential as these circuits are often used in residential settings for powering appliances such as electric dryers, air conditioners, and electric ranges. Second, adhering to safety standards and regulations is paramount to prevent electrical hazards and ensure compliance with local and national codes. Lastly, following best practices for installation is vital to guarantee that the electrical system operates efficiently and safely. By examining these aspects, individuals can make informed decisions about their electrical needs while minimizing risks. This article will explore each of these critical components in detail, starting with the common uses for 30-amp circuits, which are a cornerstone of modern residential electrical infrastructure.
Common Uses for 30-Amp Circuits
**Common Uses for 30-Amp Circuits** 30-amp circuits are a staple in many residential and commercial electrical systems, offering a balance between power delivery and safety. These circuits are commonly used for various applications where moderate to high electrical loads are anticipated. One of the most prevalent uses is for electric dryers, which require a dedicated 30-amp circuit to ensure safe and efficient operation. Similarly, electric water heaters often necessitate a 30-amp circuit due to their significant power requirements. In addition, many electric ranges and cooktops, especially those with multiple burners or high-wattage elements, are wired on 30-amp circuits to handle their substantial electrical demands. In larger homes or commercial settings, 30-amp circuits may also be used for HVAC systems, particularly for smaller air conditioning units or heat pumps. These circuits provide the necessary power for the compressor and fan motors without overloading the electrical system. Furthermore, electric vehicle charging stations often require a 30-amp circuit to support Level 2 charging, which significantly reduces charging times compared to standard Level 1 charging. Beyond these specific appliances, 30-amp circuits can be utilized in various other scenarios where concentrated power is needed. For instance, they might be used in workshops or garages to support high-power tools such as table saws, drill presses, or welding equipment. In outdoor settings, 30-amp circuits can power large outdoor lighting systems or pool pumps, ensuring reliable operation without straining the electrical infrastructure. It is crucial to note that the installation and use of 30-amp circuits must adhere to strict safety guidelines to prevent electrical hazards. This includes ensuring that the correct gauge wire is used (typically 10-gauge for 30-amp circuits) and that all connections are secure and meet local electrical codes. Additionally, circuit breakers or fuses rated for 30 amps should be installed to protect against overloads and short circuits. By understanding the common uses and safety considerations associated with 30-amp circuits, homeowners and electricians can ensure efficient and safe electrical system design and operation.
Safety Standards and Regulations
When it comes to electrical installations, adhering to safety standards and regulations is paramount to prevent accidents, injuries, and fatalities. These guidelines are meticulously crafted by regulatory bodies such as the National Electric Code (NEC) in the United States, the International Electrotechnical Commission (IEC), and other local authorities. For instance, in determining the appropriate wire size for a 30-amp circuit, one must refer to the NEC's Table 310.15(B)(16), which outlines the minimum wire sizes required based on the ampacity of the circuit. This table ensures that wires are not overloaded, reducing the risk of overheating and potential fires. Safety standards also mandate proper insulation, grounding, and protection against short circuits and overloads. Grounding systems, for example, are crucial as they provide a safe path for electrical current to flow to the ground if there is a fault, thereby preventing electrical shock. Additionally, circuit breakers or fuses must be installed to interrupt the flow of electricity in case of an overload or short circuit, further enhancing safety. Moreover, safety regulations emphasize the importance of proper labeling and signage. This includes clear identification of electrical panels, outlets, and switches to ensure that only authorized personnel perform maintenance or repairs. Regular inspections are also mandated to ensure that all electrical components are in good working condition and comply with current standards. In practical applications, adherence to these safety standards is not just a legal requirement but a moral obligation. For instance, in residential settings, ensuring that all wiring meets or exceeds safety standards can significantly reduce the risk of electrical fires and electrocution. Similarly, in industrial environments where high-voltage equipment is used, strict adherence to safety protocols can prevent catastrophic accidents. Furthermore, safety considerations extend beyond the installation phase to include ongoing maintenance and training. Electricians and technicians must be trained in the latest safety protocols and best practices to handle electrical systems safely. This includes understanding personal protective equipment (PPE) requirements, lockout/tagout procedures, and emergency response plans. In summary, safety standards and regulations form the backbone of safe electrical practices. By following these guidelines meticulously, individuals can ensure that electrical installations are safe, reliable, and compliant with legal requirements. This not only protects lives but also prevents costly damages and downtime. As such, it is imperative to integrate these safety considerations into every aspect of electrical work to create a safer environment for everyone involved.
Best Practices for Installation
When it comes to the installation of electrical wiring, particularly for a 30-amp circuit, adhering to best practices is crucial for ensuring safety, efficiency, and compliance with electrical codes. The first step involves selecting the appropriate wire size, which is determined by the ampacity of the circuit and the distance from the power source. For a 30-amp circuit, a wire gauge of 10 AWG (American Wire Gauge) is typically recommended for residential applications, as it can handle the current without overheating or causing voltage drops. ### Planning and Preparation Before starting the installation, it is essential to plan the layout meticulously. This includes mapping out the route of the wiring to minimize exposure to heat sources, moisture, and physical damage. Ensure that all materials and tools are of high quality and meet local electrical codes. Conducting a thorough risk assessment helps identify potential hazards such as nearby flammable materials or areas prone to flooding. ### Safety Considerations Safety should always be the top priority during electrical installations. Wear personal protective equipment (PPE) including gloves, safety glasses, and a hard hat to protect against electrical shock and physical injury. De-energize the circuit before beginning work by switching off the main breaker or fuse. Use lockout/tagout procedures to prevent accidental power restoration. Always follow the manufacturer's instructions for any tools or equipment used in the installation process. ### Installation Techniques Proper installation techniques are vital for maintaining the integrity of the electrical system. Use wire strippers to remove insulation without damaging the conductors. Ensure all connections are secure and made using approved connectors or terminals. Avoid over-tightening or under-tightening connections, as this can lead to overheating or arcing. When running wires through walls or ceilings, use appropriate conduit or raceways to protect against physical damage and environmental factors. ### Testing and Inspection After completing the installation, thorough testing and inspection are necessary to ensure that the circuit operates safely and efficiently. Use a multimeter to verify voltage levels and check for any shorts or grounds. Inspect all connections for signs of wear or damage. Perform a load test to ensure that the circuit can handle its rated capacity without overheating. ### Documentation and Maintenance Maintaining detailed records of the installation process is important for future reference and compliance with regulatory requirements. Document all materials used, wiring routes, and test results. Regular maintenance checks should be scheduled to inspect for signs of wear, corrosion, or other issues that could compromise safety or performance. By following these best practices for installation, you can ensure that your 30-amp circuit is installed safely, efficiently, and in compliance with local electrical codes. This not only protects against immediate hazards but also ensures long-term reliability and performance of your electrical system.