What Happens To A Metal Pipe When Heated With A 100°c Liquid

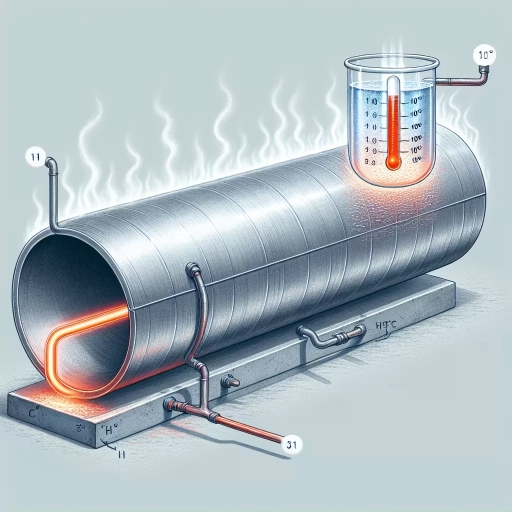
When a metal pipe is subjected to heating with a 100°C liquid, several critical phenomena occur that are essential to understand for both theoretical and practical purposes. This process involves more than just a simple temperature increase; it encompasses significant changes in the physical properties of the metal. The article delves into three key aspects: **Thermal Expansion and Deformation**, which explores how the metal pipe changes in size and shape due to the heat; **Material Properties and Changes**, which examines the alterations in the material's structure and behavior; and **Practical Implications and Safety Considerations**, which discusses the real-world consequences and safety measures necessary when dealing with heated metal pipes. Understanding these aspects is crucial for engineers, technicians, and anyone working with metal components in various industries. As we begin to explore these topics, it becomes clear that the initial and most immediate effect of heating a metal pipe is its thermal expansion and deformation, setting the stage for a deeper analysis of the subsequent changes and implications. Therefore, our first focus will be on **Thermal Expansion and Deformation**.
Thermal Expansion and Deformation
Thermal expansion and deformation are fundamental concepts in physics and engineering, governing how materials respond to changes in temperature. This phenomenon is crucial in various fields, including construction, manufacturing, and mechanical engineering. When materials are heated or cooled, they undergo linear expansion, which can significantly impact the dimensions of structures such as pipes. For instance, the linear expansion of a pipe can lead to changes in its length, affecting its overall performance and integrity. Additionally, radial expansion occurs when materials expand outward from their center, which can have profound effects on the structural integrity of components like cylinders and tubes. This radial expansion can cause stress and strain on the material, potentially leading to structural deformation. Understanding these aspects is vital to prevent failures and ensure the longevity of structures. In this article, we will delve into the specifics of linear expansion of pipes, the effects of radial expansion, and the potential for structural deformation, ultimately shedding light on the broader implications of thermal expansion and deformation.
Linear Expansion of the Pipe
When a metal pipe is subjected to a 100°C liquid, it undergoes a phenomenon known as linear expansion, which is a fundamental aspect of thermal expansion and deformation. This process occurs because the atoms within the metal gain kinetic energy as they absorb heat, causing them to vibrate more vigorously and move further apart. As a result, the material expands in all directions, including along its length. The extent of this expansion can be quantified using the coefficient of linear thermal expansion (α), which is specific to each material. For metals, this coefficient typically ranges from 10^-5 to 10^-6 per degree Celsius. For instance, if a pipe made of steel (with an α of approximately 12 × 10^-6 per °C) is heated from room temperature (20°C) to 100°C, its length will increase by a factor proportional to the temperature change and the coefficient of expansion. To calculate this increase, one can use the formula: ΔL = α × L × ΔT, where ΔL is the change in length, L is the original length, and ΔT is the change in temperature. For example, if the original length of the steel pipe is 10 meters and it is heated from 20°C to 100°C, the change in length would be approximately 0.012 meters or 12 millimeters. This linear expansion is crucial in engineering and construction because it must be accounted for to prevent structural damage or malfunction. In pipelines, for instance, expansion joints are often installed to accommodate these changes in length, ensuring that the system remains functional and safe under varying thermal conditions. Similarly, in building construction, allowances must be made for the thermal expansion of materials to avoid cracking or buckling. Understanding linear expansion is also essential for maintaining the integrity of mechanical systems. For example, in engines and machinery, components are designed with thermal expansion in mind to ensure proper fit and function over a range of operating temperatures. Failure to account for this expansion can lead to overheating, wear, and eventual failure of critical components. In summary, the linear expansion of a metal pipe when heated with a 100°C liquid is a predictable and quantifiable phenomenon governed by the material's coefficient of thermal expansion. This understanding is vital for designing and maintaining systems that operate under varying thermal conditions, ensuring safety, efficiency, and longevity. By incorporating considerations of thermal expansion into engineering practices, we can build more resilient and reliable structures and machinery.
Radial Expansion and Its Effects
When a metal pipe is subjected to heating with a 100°C liquid, it undergoes significant changes due to radial expansion, a fundamental aspect of thermal expansion and deformation. Radial expansion refers to the outward movement of the pipe's diameter as it absorbs heat energy. This phenomenon occurs because the atoms within the metal gain kinetic energy and start vibrating more vigorously, causing them to move further apart. As a result, the material expands in all directions, including radially. The effects of radial expansion on a metal pipe are multifaceted. Firstly, the increase in diameter can lead to a reduction in the pipe's wall thickness, potentially compromising its structural integrity and pressure resistance. This is particularly critical in applications where the pipe is under stress or subjected to high pressures, such as in plumbing or industrial processes. Secondly, radial expansion can cause the pipe to elongate longitudinally, which may result in buckling or bending if the pipe is constrained at both ends. This deformation can lead to misalignment and stress concentrations at joints and connections, increasing the risk of leaks or failures. Moreover, radial expansion affects the pipe's material properties. The increased temperature can alter the metal's mechanical properties, such as its tensile strength and ductility. For instance, some metals may become softer and more prone to deformation at elevated temperatures, while others might experience a decrease in their yield strength. These changes can impact the pipe's ability to withstand external loads and internal pressures, necessitating careful consideration in design and operation. In practical terms, understanding radial expansion is crucial for ensuring the safe and efficient operation of systems involving heated metal pipes. Engineers must account for these expansions during the design phase by incorporating appropriate clearances and supports to accommodate the increased dimensions. Additionally, regular maintenance and inspections are essential to monitor any signs of excessive deformation or stress that could indicate impending failure. In conclusion, radial expansion is a critical factor when dealing with metal pipes heated by a 100°C liquid. It influences both the physical dimensions and material properties of the pipe, necessitating careful engineering and maintenance practices to prevent adverse effects such as structural weakening, deformation, and potential failures. By comprehending these dynamics, professionals can ensure the reliability and longevity of systems that rely on heated metal pipes.
Potential for Structural Deformation
When a metal pipe is subjected to heating with a 100°C liquid, the potential for structural deformation becomes a significant concern. Thermal expansion, the tendency of materials to expand when heated, is a fundamental physical phenomenon that can lead to various forms of deformation. As the metal pipe absorbs heat from the liquid, its atoms gain kinetic energy and start vibrating more vigorously, causing them to move further apart. This increase in atomic spacing results in the expansion of the material. The extent of thermal expansion depends on the specific metal's coefficient of thermal expansion (CTE), which varies among different materials. For instance, metals like copper and aluminum have higher CTEs compared to steel, meaning they expand more significantly under the same temperature increase. When a metal pipe expands, it can experience several types of deformation. One common form is linear expansion, where the length of the pipe increases. However, if the pipe is constrained at both ends, this expansion can lead to compressive stresses within the material, potentially causing buckling or bending. Another critical aspect is the differential expansion that occurs when different parts of the pipe are heated unevenly. This can happen if the liquid does not distribute heat uniformly along the pipe's length or if there are variations in the pipe's thickness or material composition. Such non-uniform heating can induce bending or warping, as different sections of the pipe expand at different rates. Moreover, thermal expansion can also lead to changes in the pipe's cross-sectional shape. If the pipe is not perfectly round or if there are pre-existing imperfections, heating can exacerbate these irregularities, leading to ovalization or other forms of geometric distortion. These deformations not only affect the structural integrity of the pipe but also its functional performance, particularly in applications where precise dimensions are crucial. In addition to these immediate effects, repeated cycles of heating and cooling can cause fatigue in the material over time. Each cycle of thermal expansion and contraction can introduce micro-cracks and other defects that gradually weaken the pipe's structure, increasing its susceptibility to failure under stress. Understanding and managing thermal expansion and deformation are essential for maintaining the integrity and performance of metal pipes in various industrial and engineering contexts. By selecting materials with appropriate CTEs, ensuring uniform heating, and designing systems that accommodate thermal expansion, engineers can mitigate the risks associated with structural deformation and ensure reliable operation of critical infrastructure.
Material Properties and Changes
Material properties are fundamental to understanding the behavior and performance of various substances under different conditions. These properties can undergo significant changes due to external factors, making it crucial to study their alterations. This article delves into three key aspects of material changes: alterations in mechanical strength, changes in electrical conductivity, and possible phase transitions. Mechanical strength, for instance, can be affected by stress, temperature, and material composition, impacting the durability and reliability of materials. Electrical conductivity, on the other hand, can vary with temperature and the presence of impurities, influencing the material's ability to conduct electricity. Phase transitions, such as melting or crystallization, occur when materials change from one state to another, often driven by temperature or pressure changes. Understanding these changes is essential for predicting how materials will behave in various applications. As we explore these topics, we will also transition into discussing thermal expansion and deformation, highlighting how temperature affects the physical dimensions and structural integrity of materials. By examining these aspects, we can better appreciate the complex interactions that govern material behavior and optimize their use in engineering and technology.
Alterations in Mechanical Strength
When a metal pipe is subjected to heating with a 100°C liquid, several alterations in its mechanical strength can occur, significantly impacting its performance and durability. The primary concern is the thermal expansion of the metal, which can lead to changes in its dimensions and potentially cause stress within the material. Metals generally expand when heated, and this expansion can be uniform or non-uniform depending on the temperature distribution and the material's thermal conductivity. For instance, if one part of the pipe heats up faster than another, it may expand more rapidly, creating uneven stresses that could compromise the structural integrity of the pipe. Moreover, prolonged exposure to elevated temperatures can induce microstructural changes within the metal. At 100°C, many metals are below their recrystallization temperatures, but repeated thermal cycling or prolonged heating can still cause grain growth or precipitation hardening, which affect mechanical properties. For example, in some alloys, heating can lead to the formation of precipitates that harden the material but may also reduce ductility. Conversely, other metals might undergo softening due to annealing effects where internal stresses are relieved, leading to a decrease in yield strength. Another critical aspect is the potential for oxidation or corrosion when metals are heated in the presence of certain liquids. At 100°C, especially if the liquid is aqueous or contains corrosive substances, the metal surface may react chemically, forming oxides or other compounds that weaken the material over time. This corrosion can be particularly detrimental as it not only reduces mechanical strength but also creates localized weaknesses that can propagate cracks under stress. Additionally, the heating process itself may introduce residual stresses into the metal pipe. These stresses arise from differential cooling rates after heating and can significantly alter the material's mechanical behavior. Residual tensile stresses on the surface can increase susceptibility to cracking and fatigue failure, while compressive stresses might offer some protection against crack propagation but could still affect overall strength. In summary, heating a metal pipe with a 100°C liquid induces various alterations in its mechanical strength due to thermal expansion, microstructural changes, potential corrosion, and residual stresses. Understanding these effects is crucial for predicting and ensuring the safe operation of metal components under thermal loads, thereby preventing premature failure and maintaining structural integrity. This knowledge is essential for engineers and materials scientists who design and manage systems involving heated metal components to ensure optimal performance and longevity.
Changes in Electrical Conductivity
When a metal pipe is heated with a 100°C liquid, several significant changes occur in its electrical conductivity, which are intricately linked to the material's thermal and structural properties. Electrical conductivity in metals is primarily governed by the free movement of electrons within the material's crystal lattice. At room temperature, metals exhibit high electrical conductivity due to the efficient transfer of electrons. However, as the temperature increases, the atoms in the metal lattice begin to vibrate more vigorously, a phenomenon known as thermal agitation. This increased atomic motion introduces more resistance to the flow of electrons, thereby reducing the metal's electrical conductivity. The specific change in electrical conductivity can be attributed to the scattering of electrons by phonons, which are quantized modes of vibration in the crystal lattice. As the temperature rises to 100°C, the phonon population increases, leading to more frequent collisions between electrons and phonons. These collisions impede the smooth flow of electrons, resulting in higher resistivity. For instance, in metals like copper and aluminum, which are commonly used in piping due to their excellent electrical and thermal properties, this effect is particularly pronounced. The resistivity of copper at 100°C is approximately 1.7 times its value at 20°C, illustrating a substantial decrease in electrical conductivity. Additionally, heating can induce structural changes in the metal, such as grain growth or the formation of defects, which can further affect its electrical properties. For example, if the heating process causes the metal to undergo recrystallization or grain coarsening, this could alter the material's microstructure and potentially introduce more scattering sites for electrons, thus reducing conductivity. Understanding these changes is crucial for various engineering applications, including electrical wiring and heat exchangers. In the context of a metal pipe heated with a 100°C liquid, these changes must be considered to ensure optimal performance and safety. For instance, in electrical circuits, the increased resistance could lead to higher energy losses and reduced efficiency, while in heat exchangers, it might affect the overall thermal conductivity and heat transfer rates. In summary, when a metal pipe is heated with a 100°C liquid, the resulting thermal agitation and structural changes significantly impact its electrical conductivity. This decrease in conductivity is a critical factor in designing and operating systems that rely on the electrical and thermal properties of metals, highlighting the importance of considering these material changes in practical applications.
Possible Phase Transitions
When a metal pipe is subjected to heating with a 100°C liquid, several potential phase transitions can occur, each influencing the material's properties and behavior. At the molecular level, metals are composed of atoms arranged in a crystalline structure. As the temperature increases, the kinetic energy of these atoms rises, causing them to vibrate more vigorously. This increased motion can lead to various phase transitions depending on the metal's specific characteristics and the temperature range. One possible phase transition is the change from a solid to a liquid state, known as melting. However, for most metals, 100°C is below their melting point; thus, this transition is unlikely unless the metal has a very low melting point, such as certain alloys or tin. More commonly, heating a metal pipe to 100°C will cause it to undergo thermal expansion. As the atoms gain energy and move further apart, the metal expands in all directions. This expansion can be significant and must be considered in engineering applications to avoid structural damage or misalignment. Another important consideration is the potential for changes in the metal's microstructure. Some metals undergo phase transitions within their solid state, known as allotropic transformations. For example, certain steels can undergo martensitic transformations when heated or cooled rapidly, which can significantly alter their mechanical properties such as hardness and ductility. However, these transformations typically occur at higher temperatures than 100°C. Additionally, heating can induce stress relief in metals that have been previously cold-worked or subjected to mechanical stress. The increased thermal energy allows dislocations within the crystal structure to move more freely, reducing internal stresses and potentially altering the metal's strength and ductility. In terms of material properties, heating a metal pipe to 100°C can also affect its electrical and thermal conductivity. Generally, metals exhibit decreased electrical conductivity with increasing temperature due to increased atomic vibrations that scatter electrons. Conversely, thermal conductivity may remain relatively stable or decrease slightly depending on the specific metal and its purity. Understanding these phase transitions and changes in material properties is crucial for predicting how a metal pipe will behave under various thermal conditions. This knowledge is essential for designing safe and efficient systems in industries such as plumbing, aerospace, and automotive engineering where metals are subjected to diverse temperature regimes. By recognizing the potential phase transitions and associated property changes, engineers can ensure that metal components perform reliably and maintain their structural integrity over their service life.
Practical Implications and Safety Considerations
In the realm of industrial operations, understanding the practical implications and safety considerations associated with thermal expansion and deformation is crucial for maintaining operational integrity and ensuring worker safety. This article delves into three key areas that highlight the importance of these considerations: the impact on pipe integrity and durability, the risk of leaks or failures, and the essential safety protocols for handling heated pipes. Each of these aspects is interwoven to provide a comprehensive view of how thermal expansion can affect critical infrastructure. By examining how thermal changes influence pipe integrity, we can better anticipate potential vulnerabilities. Additionally, understanding the risks of leaks or failures helps in implementing preventive measures to avoid catastrophic incidents. Finally, adhering to stringent safety protocols when handling heated pipes is vital to prevent accidents and ensure a safe working environment. These considerations are foundational in managing the challenges posed by thermal expansion and deformation, making them indispensable for any industrial setting. Transitioning seamlessly into the specifics of thermal expansion and deformation, this article aims to equip readers with the knowledge necessary to navigate these complex issues effectively.
Impact on Pipe Integrity and Durability
When a metal pipe is subjected to heating with a 100°C liquid, several critical factors impact its integrity and durability, necessitating careful consideration for practical implications and safety. The primary concern is thermal expansion, where the metal pipe material expands as it heats up. This expansion can lead to increased stress on the pipe, particularly if it is constrained or if there are significant temperature gradients along its length. Over time, repeated cycles of heating and cooling can cause fatigue, potentially leading to cracks or fractures. Additionally, the thermal conductivity of the pipe material plays a crucial role. Metals with high thermal conductivity, such as copper or aluminum, will distribute heat more evenly compared to those with lower conductivity like steel. However, even in materials with good thermal conductivity, localized hot spots can occur due to uneven heating or poor insulation, further exacerbating stress concentrations. Corrosion is another significant factor that affects pipe integrity when exposed to heated liquids. Many metals are more susceptible to corrosion at elevated temperatures, especially if the liquid contains corrosive substances. For instance, if the liquid is acidic or contains dissolved oxygen, it can accelerate corrosion processes such as pitting or general corrosion, weakening the pipe over time. Furthermore, the mechanical properties of the metal pipe are altered at higher temperatures. Yield strength and tensile strength typically decrease with increasing temperature, making the pipe more prone to deformation or failure under load. This is particularly relevant in high-pressure applications where even a slight reduction in mechanical strength could have catastrophic consequences. From a practical standpoint, these factors underscore the importance of proper design and material selection for pipes intended for use with heated liquids. Engineers must consider thermal expansion coefficients, corrosion resistance, and mechanical properties at elevated temperatures to ensure long-term durability and safety. Regular inspections and maintenance are also essential to detect any signs of degradation early on. In terms of safety considerations, it is crucial to implement measures that prevent overheating and ensure uniform temperature distribution. This may include using appropriate insulation materials, monitoring temperature levels closely, and employing safety valves or pressure relief mechanisms to mitigate potential failures. By understanding these impacts on pipe integrity and taking proactive steps to address them, operators can significantly reduce the risk of accidents and extend the lifespan of their piping systems.
Risk of Leaks or Failures
When a metal pipe is subjected to heating with a 100°C liquid, several critical factors come into play that highlight the risk of leaks or failures. One of the primary concerns is thermal expansion, where the metal pipe material expands as it heats up. This expansion can lead to increased stress on the pipe's joints and connections, potentially causing them to weaken or fail if not properly designed or maintained. Additionally, the thermal gradient across the pipe wall can induce differential expansion rates, which may result in localized stresses that could compromise the integrity of the pipe. Another significant risk is related to the material properties of the pipe itself. Different metals have varying coefficients of thermal expansion and thermal conductivity, which can affect how they respond to heat. For instance, if a pipe is made from a material with high thermal conductivity but low ductility, it may be more prone to cracking under thermal stress. Furthermore, pre-existing flaws or defects in the pipe material can become exacerbated by the heating process, increasing the likelihood of catastrophic failures. Corrosion is another critical factor that must be considered when heating metal pipes. The presence of a liquid at 100°C can accelerate corrosion processes, especially if the liquid contains corrosive substances or if the pipe material is not resistant to the specific conditions. Corrosion can weaken the pipe over time, reducing its ability to withstand internal pressures and external stresses, thereby increasing the risk of leaks or ruptures. From a practical standpoint, these risks underscore the importance of rigorous safety protocols and regular maintenance. Engineers and operators must ensure that pipes are designed with thermal expansion in mind and that appropriate safety margins are built into the system. Regular inspections for signs of corrosion or material degradation are essential, as are proper training programs for personnel handling heated systems. Implementing robust monitoring systems to detect early signs of failure can also mitigate risks by allowing for timely interventions before a major incident occurs. In summary, heating a metal pipe with a 100°C liquid introduces several potential risks that must be carefully managed to prevent leaks or failures. Understanding and addressing these risks through proper design, maintenance, and operational practices is crucial for ensuring the safety and reliability of industrial processes involving heated metal pipes. By prioritizing these considerations, operators can significantly reduce the likelihood of adverse events and maintain a safe working environment.
Safety Protocols for Handling Heated Pipes
When handling heated pipes, especially those exposed to a 100°C liquid, it is crucial to adhere to stringent safety protocols to prevent injuries and ensure operational integrity. The primary concern is thermal burns, as direct contact with heated pipes can cause severe skin damage. To mitigate this risk, personnel should wear appropriate personal protective equipment (PPE) such as heat-resistant gloves, long-sleeved shirts, and safety glasses. Additionally, insulated sleeves or heat shields can be installed around the pipes to reduce surface temperatures and prevent accidental contact. Proper training is also essential; employees must understand the hazards associated with heated pipes and know how to handle them safely. This includes recognizing signs of overheating, such as discoloration or deformation of the pipe material, and knowing when to isolate the system for maintenance. Regular inspections are vital to identify any potential issues before they become critical; this includes checking for signs of wear, corrosion, or damage that could compromise the structural integrity of the pipe. Another critical aspect is ensuring proper ventilation in areas where heated pipes are present. High temperatures can lead to the release of harmful fumes or vapors from materials like insulation or coatings on the pipes. Adequate ventilation helps maintain a safe working environment by removing these potential hazards. Furthermore, emergency response plans should be in place in case of an accident; this includes having fire extinguishers and first aid kits readily available. From an engineering perspective, designing systems with safety in mind is paramount. This involves selecting materials that can withstand high temperatures without compromising their strength or integrity. For instance, using pipes made from materials like stainless steel or high-temperature-resistant alloys can reduce the risk of failure under thermal stress. Moreover, incorporating safety features such as thermal monitoring systems and automatic shut-off valves can help prevent overheating incidents. Finally, adherence to industry standards and regulations is mandatory. Compliance with guidelines set by organizations like OSHA (Occupational Safety and Health Administration) ensures that all safety protocols are met and that best practices are followed consistently. By combining these measures—proper PPE, training, regular inspections, adequate ventilation, robust engineering design, and compliance with regulations—organizations can significantly reduce the risks associated with handling heated pipes and create a safer working environment for all personnel involved.