What Is A Flange

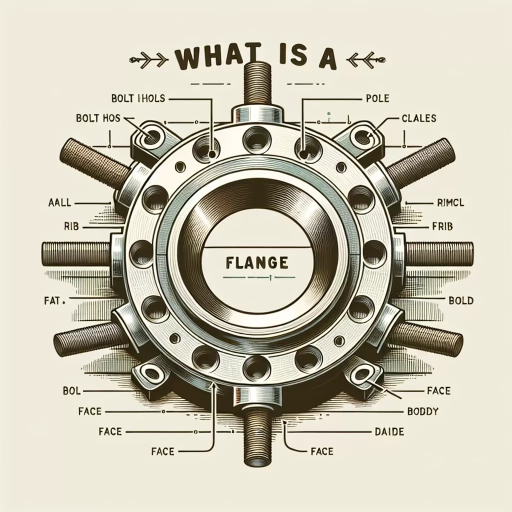
In the realm of engineering and industrial applications, few components are as crucial yet often overlooked as the flange. A flange is a fundamental part of many mechanical systems, serving as a vital connector that ensures the integrity and functionality of pipelines, valves, and other equipment. This article delves into the multifaceted world of flanges, providing a comprehensive overview that spans their definition and purpose, design and construction, and installation, maintenance, and safety considerations. By understanding these aspects, readers will gain a deeper appreciation for how flanges contribute to the efficiency and reliability of various industrial processes. We begin by exploring the definition and purpose of a flange, which sets the stage for a detailed examination of their design, construction, and the critical steps involved in their installation and maintenance. This foundational knowledge is essential for appreciating the broader role that flanges play in ensuring operational safety and performance. Let us start with the core question: what is a flange and why is it so important?
Definition and Purpose of a Flange
In the realm of engineering and industrial manufacturing, flanges play a crucial role in connecting and sealing pipes, valves, and other equipment. These versatile components are essential for ensuring the integrity and safety of various systems, from plumbing and HVAC to chemical processing and oil refining. To fully understand the significance of flanges, it is important to delve into their basic definition and function, which will be explored in detail. Additionally, recognizing the diverse types of flanges available is vital for selecting the appropriate one for specific applications. Finally, examining the common applications of flanges will highlight their widespread utility across different industries. By exploring these aspects, we can gain a comprehensive understanding of the definition and purpose of a flange, which is fundamental to their effective use in modern engineering practices. This article will provide an in-depth look at the basic definition and function of flanges, the various types available, and their common applications, ultimately shedding light on the definition and purpose of a flange.
Basic Definition and Function
A flange is a fundamental component in various mechanical systems, particularly in piping and plumbing, serving as a critical interface for connecting, supporting, and sealing pipes, valves, and other equipment. At its core, a flange is a flat, circular piece of metal with bolt holes around its perimeter. This basic definition underscores its primary function: to provide a secure and leak-tight connection between two or more components. The function of a flange is multifaceted. Firstly, it acts as a mechanical joint, allowing for the easy assembly and disassembly of piping systems. This is particularly important in industrial settings where maintenance and repairs are frequent. By using bolts or studs to secure the flanges together, technicians can quickly disconnect sections of piping without having to cut or weld them. Secondly, flanges play a crucial role in ensuring the integrity of the system by providing a reliable seal. The gasket or seal ring placed between the mating surfaces of two flanges prevents fluid leakage, which is essential for maintaining system pressure and preventing environmental contamination. This sealing capability is vital in applications involving hazardous materials or high-pressure fluids. Additionally, flanges serve as structural supports within piping systems. They can distribute stress evenly across the connection points, thereby enhancing the overall stability and durability of the system. This is particularly important in dynamic environments where vibrations or thermal expansions could otherwise compromise the integrity of the connections. In terms of design, flanges come in various types to suit different applications. For instance, weld neck flanges are used for high-pressure applications due to their robust design, while slip-on flanges offer greater flexibility and ease of installation. Blind flanges, on the other hand, are used to seal off the end of a pipe or valve, preventing fluid flow. In summary, the basic definition and function of a flange highlight its importance as a versatile and indispensable component in mechanical engineering. Whether it's facilitating easy assembly, ensuring leak-tight seals, or providing structural support, the flange plays a pivotal role in maintaining the efficiency and safety of various industrial processes. Its adaptability to different environments and applications makes it an essential element in modern engineering practices.
Types of Flanges
Flanges are crucial components in various industrial applications, serving as connectors for pipes, valves, and other equipment. There are several types of flanges, each designed to meet specific needs and operating conditions. **Weld Neck Flanges** are one of the most common types, known for their high strength and resistance to stress. These flanges have a long, tapered hub that provides excellent support against external loads and are often used in high-pressure and high-temperature applications. **Slip-On Flanges**, on the other hand, are simpler and less expensive. They slide over the pipe and are welded in place, making them easier to install but less robust than weld neck flanges. **Blind Flanges** are used to seal the end of a piping system or vessel, effectively blocking the flow of fluids. They do not have a center hole and are typically used for maintenance purposes or to isolate sections of a system. **Lap Joint Flanges** are another type, characterized by a two-part design: the flange itself and a stub end. This configuration allows for easy disassembly and is often used in low-pressure applications where frequent maintenance is required. **Socket Weld Flanges** are similar to slip-on flanges but have a socket into which the pipe is inserted before being welded. This type offers better resistance to internal pressure compared to slip-on flanges but is generally used for smaller pipe sizes. **Threaded Flanges** are threaded internally and externally, allowing them to be screwed onto threaded pipes without welding. They are commonly used in low-pressure applications where welding is not feasible or desirable. **Orifice Flanges** are specialized flanges used in conjunction with orifice plates to measure the flow rate of fluids. These flanges have additional features such as pressure taps and are designed to ensure accurate flow measurement. **Ring Type Joint (RTJ) Flanges** feature a metal ring gasket that provides a tight seal under high pressure and temperature conditions, making them ideal for critical applications in industries like oil and gas. Each type of flange is engineered to address specific challenges and requirements, ensuring that the piping system operates safely and efficiently. Understanding the different types of flanges is essential for selecting the right component for a particular application, thereby ensuring optimal performance and reliability. By choosing the appropriate flange type, engineers can mitigate risks associated with leakage, corrosion, and mechanical failure, ultimately enhancing the overall integrity of the system.
Common Applications
Flanges are versatile components that find widespread application across various industries due to their robust design and functional versatility. In the context of piping systems, flanges serve as critical connectors that enable the joining and disconnection of pipes, valves, pumps, and other equipment. One of the most common applications of flanges is in the oil and gas industry, where they are used to connect pipelines, wellheads, and other equipment under high pressure and temperature conditions. Here, flanges must be engineered to withstand extreme environments, making them a crucial element in ensuring the integrity and safety of the entire system. In chemical processing plants, flanges are essential for connecting reactors, heat exchangers, and other process equipment. These flanges often need to be resistant to corrosive substances and high temperatures, necessitating the use of specialized materials such as stainless steel or titanium. Similarly, in power generation facilities, flanges are used in steam turbines and boiler systems where they must endure high pressures and temperatures without compromising the system's performance or safety. Flanges also play a vital role in water treatment and distribution systems. Here, they are used to connect pipes that transport water from treatment plants to residential areas. These flanges must be durable enough to withstand the constant flow of water and potential contaminants while ensuring a leak-free connection. Additionally, in HVAC (heating, ventilation, and air conditioning) systems, flanges are employed to connect ducts and other components that distribute air throughout buildings. In marine engineering, flanges are integral to shipbuilding and offshore platforms. They are used to connect pipes that carry fuel, water, and other fluids essential for the operation of these vessels. The marine environment poses unique challenges such as saltwater corrosion and extreme weather conditions, making the selection of flange materials and designs particularly critical. Furthermore, flanges are used in automotive manufacturing for connecting engine components like exhaust systems and turbochargers. Here, they need to be lightweight yet strong enough to handle high temperatures and pressures generated by engine operations. Across these diverse applications, the common thread is the need for reliability, durability, and precision in flange design and manufacturing. Whether it's ensuring the safe transport of hazardous materials or maintaining efficient operation in harsh environments, flanges are indispensable components that contribute significantly to the overall performance and safety of various industrial systems. Their ability to facilitate easy assembly and disassembly makes them an essential part of modern engineering practices.
Design and Construction of Flanges
In the realm of engineering and industrial manufacturing, flanges play a crucial role in connecting pipes, valves, and other equipment, ensuring the integrity and functionality of various systems. The design and construction of flanges are intricate processes that involve careful consideration of several key factors. This article delves into the essential aspects of flange design and construction, starting with the **Materials Used in Flange Manufacturing**, which highlights the importance of selecting appropriate materials to meet specific application requirements. It then explores **Dimensions and Standards**, outlining the critical role that adherence to industry standards plays in ensuring compatibility and safety. Finally, it examines **Manufacturing Processes**, detailing the various techniques and technologies employed to produce high-quality flanges. Understanding these elements is fundamental to appreciating the **Definition and Purpose of a Flange**, which will be discussed in detail, providing a comprehensive overview of how flanges serve as vital components in diverse industrial applications. By grasping these foundational concepts, engineers and industry professionals can better design, construct, and utilize flanges to optimize system performance and reliability.
Materials Used in Flange Manufacturing
In the design and construction of flanges, the choice of materials is crucial for ensuring durability, performance, and safety. The selection of materials depends on various factors including the application, operating conditions, and compatibility with other components in the system. For instance, in high-temperature and high-pressure applications such as those found in power plants or chemical processing, flanges are often made from robust materials like carbon steel, stainless steel, or alloy steel. These metals offer excellent strength, resistance to corrosion, and the ability to withstand extreme temperatures without compromising structural integrity. For applications where corrosion resistance is paramount, such as in marine or chemical environments, materials like titanium, Hastelloy, or Inconel are preferred. These alloys exhibit superior resistance to corrosive substances and can maintain their properties even in harsh conditions. In contrast, for less demanding applications such as plumbing or low-pressure piping systems, materials like cast iron or ductile iron may be sufficient due to their cost-effectiveness and adequate mechanical properties. In addition to metals, other materials like plastic or composite materials are also used in flange manufacturing for specific applications. For example, PVC or PTFE flanges are commonly used in water treatment plants or chemical processing where non-reactive surfaces are necessary. These materials offer advantages such as lightweight construction, ease of installation, and resistance to certain types of corrosion. The manufacturing process also influences the choice of material; for example, forged flanges are typically made from steel alloys due to their ability to withstand high stresses during the forging process. On the other hand, cast flanges can be produced from a wider range of materials including cast iron and stainless steel because casting allows for more complex geometries and larger sizes. Furthermore, the surface finish and treatment of the material play a significant role in flange performance. Surface treatments such as machining, grinding, or coating can enhance the material's properties by improving smoothness, reducing friction, and increasing resistance to wear and tear. Coatings like zinc plating or epoxy painting can provide additional protection against corrosion in aggressive environments. In summary, the materials used in flange manufacturing are diverse and carefully selected based on the specific requirements of the application. By choosing the right material and employing appropriate manufacturing techniques and surface treatments, engineers can ensure that flanges perform reliably under various operating conditions, thereby contributing to the overall efficiency and safety of the system. This meticulous approach underscores the importance of material selection in the design and construction of flanges.
Dimensions and Standards
When it comes to the design and construction of flanges, understanding dimensions and standards is paramount. Flanges are critical components in piping systems, serving as connectors that allow for the easy assembly and disassembly of pipes, valves, and other equipment. The precision in their dimensions ensures safe, efficient, and reliable operation. Standards such as those set by the American Society of Mechanical Engineers (ASME) and the American National Standards Institute (ANSI) provide a framework for flange design. These standards dictate specific dimensions, materials, and tolerances to ensure compatibility and performance across different applications. For instance, ASME B16.5 covers steel pipe flanges and flanged fittings up to 24 inches in diameter, while ASME B16.47 addresses larger sizes. These standards specify details like bolt circle diameter, bolt hole size, and flange thickness to guarantee uniformity. The dimensions of a flange include its outer diameter, inner diameter (bore), bolt circle diameter, number of bolts, and thickness. Each dimension must be meticulously adhered to in order to prevent leaks or structural failures. For example, the gasket seating surface area must be precisely machined to ensure a tight seal when the flange is bolted together with another flange or component. Material standards are also crucial; flanges can be made from various materials such as carbon steel, stainless steel, or alloy steel, each with its own set of properties and applications. The choice of material depends on factors like operating temperature, pressure, and corrosive environment. For instance, stainless steel flanges are often used in chemical processing due to their resistance to corrosion. In addition to dimensional accuracy and material selection, manufacturing standards play a significant role. Flanges must be fabricated using processes that meet stringent quality controls. This includes machining operations such as drilling bolt holes and facing the gasket seating surface. Non-destructive testing methods like radiography or ultrasonic testing may also be employed to detect any defects in the material. Adhering to these standards not only ensures compliance with regulatory requirements but also enhances safety and reliability in industrial operations. Properly designed and constructed flanges minimize the risk of leaks or failures that could lead to downtime or even catastrophic accidents. Therefore, understanding and adhering to established dimensions and standards is essential for anyone involved in the design and construction of flanges. By following these guidelines meticulously, engineers and manufacturers can produce high-quality flanges that meet the demands of various industries ranging from oil and gas to chemical processing and power generation. This attention to detail translates into improved performance, reduced maintenance costs, and an overall safer working environment. In summary, dimensions and standards form the backbone of flange design and construction, ensuring that these critical components function optimally under diverse operating conditions.
Manufacturing Processes
In the realm of engineering and construction, the design and construction of flanges are intricately linked with various manufacturing processes. These processes are crucial for ensuring the integrity, durability, and performance of flanges, which serve as critical connectors in pipelines, valves, and other equipment. The manufacturing of flanges typically begins with material selection, where high-strength metals such as carbon steel, stainless steel, or alloy steel are chosen based on the application requirements. Once the material is selected, it undergoes several key processes. **Forging** is a common method used for producing flanges, especially those that require high strength and resistance to stress. In this process, the metal is heated and shaped using dies to achieve the desired form. Forging allows for the creation of complex geometries and enhances the grain structure of the material, leading to improved mechanical properties. **Casting** is another viable option for manufacturing flanges, particularly when intricate designs or large sizes are involved. This process involves pouring molten metal into a mold, allowing it to solidify, and then removing it from the mold. Casting offers flexibility in terms of design complexity but may require additional machining steps to achieve precise dimensions. **Machining** plays a pivotal role in the final stages of flange production. This involves cutting, drilling, and grinding operations to ensure that the flange meets precise specifications. CNC machining is often employed for its accuracy and efficiency in producing complex features such as bolt holes and sealing surfaces. **Welding** can also be integral in flange manufacturing, especially for larger or custom designs where multiple components need to be joined together. Techniques like shielded metal arc welding (SMAW), gas metal arc welding (GMAW), or submerged arc welding (SAW) are commonly used depending on the material and application. **Heat Treatment** is a critical post-manufacturing process that can significantly enhance the mechanical properties of flanges. Processes such as annealing, normalizing, or hardening are applied to relieve stresses, improve toughness, or increase hardness according to the specific requirements of the application. Finally, **Quality Control** measures are essential throughout the manufacturing process to ensure that flanges meet industry standards and specifications. This includes dimensional checks, material testing, and non-destructive testing (NDT) techniques like radiography or ultrasonic testing to detect any defects or irregularities. By combining these manufacturing processes—forging, casting, machining, welding, heat treatment, and rigorous quality control—engineers can produce high-quality flanges that are reliable, durable, and capable of withstanding the demands of various industrial applications. The meticulous attention to detail in each step of the manufacturing process ensures that flanges perform optimally in their role as connectors in complex systems.
Installation, Maintenance, and Safety Considerations
In the realm of industrial and mechanical engineering, the proper installation, maintenance, and safety considerations of critical components are paramount to ensuring operational efficiency, reliability, and safety. Among these components, flanges play a crucial role in connecting pipes, valves, and other equipment, making their correct handling essential. This article delves into the three key aspects that underpin the effective use of flanges: **Proper Installation Techniques**, which highlight the best practices for securing these connections; **Maintenance and Inspection Guidelines**, outlining regular checks and upkeep to prevent failures; and **Safety Precautions During Use**, emphasizing measures to mitigate risks associated with flange operations. By understanding these critical considerations, engineers and technicians can ensure that flanges function optimally, reducing downtime and enhancing overall system performance. This comprehensive approach sets the stage for a deeper exploration into the **Definition and Purpose of a Flange**, providing a foundational understanding of why these components are indispensable in various industrial settings.
Proper Installation Techniques
Proper installation techniques are crucial for ensuring the longevity, efficiency, and safety of any system that incorporates flanges. When installing flanges, it is essential to follow a meticulous process to avoid potential leaks, damage, or even catastrophic failures. First, the surface preparation is key; both the flange and the mating surface must be clean and free from any debris or contaminants. This step ensures a tight seal and prevents any foreign particles from compromising the integrity of the connection. Next, aligning the flanges correctly is vital. Misalignment can lead to uneven stress distribution, which may result in gasket failure or flange warping. Use alignment tools if necessary to ensure that the bolt holes are perfectly aligned. Once aligned, apply a thin layer of lubricant to the threads of the bolts to facilitate smooth tightening and prevent galling. The choice of gasket is also critical. Select a gasket material that is compatible with the fluid being handled and the operating conditions such as temperature and pressure. Ensure that the gasket is properly seated in its groove or on its surface before assembling the flanges. Tightening the bolts in a star pattern (cross-pattern) is recommended to distribute the force evenly across the flange. This method helps in achieving uniform compression on the gasket, thereby preventing leaks and ensuring a secure seal. It is also important to follow the recommended torque values specified by the manufacturer to avoid over-tightening or under-tightening. Post-installation checks are equally important. Inspect the flange connection for any signs of leakage by applying a leak detection method such as a soap solution or an ultrasonic leak detector. Additionally, ensure that all bolts are tightened securely but not excessively, as this could damage the flange or gasket. Finally, maintaining accurate records of installation procedures and inspections can help in future maintenance and troubleshooting. Regular inspections should be conducted to check for signs of wear, corrosion, or other forms of degradation that could compromise the integrity of the flange connection. By adhering strictly to these proper installation techniques, you can significantly reduce the risk of failures, enhance system reliability, and ensure compliance with safety standards. Properly installed flanges not only contribute to operational efficiency but also play a critical role in preventing accidents and environmental hazards associated with leaks or ruptures. Therefore, it is imperative that all personnel involved in flange installation are well-trained and adhere to best practices outlined in industry standards and guidelines.
Maintenance and Inspection Guidelines
**Maintenance and Inspection Guidelines** Proper maintenance and regular inspection are crucial for ensuring the longevity and safety of flanges in various industrial applications. These guidelines are integral to the overall lifecycle management of flanges, complementing their installation and contributing to a safe operational environment. To begin with, **visual inspections** should be conducted regularly to identify any signs of wear, corrosion, or damage. This includes checking for cracks, pitting, or erosion on the flange surface and gasket areas. Any visible damage necessitates immediate attention to prevent further deterioration. **Leakage checks** are also essential; even minor leaks can indicate a larger issue such as improper gasket seating or flange misalignment. **Cleaning and lubrication** play significant roles in maintaining flange integrity. Regular cleaning helps remove debris and contaminants that could compromise the seal or cause corrosion. Lubricating the bolts and threads can ease the process of tightening and loosening, reducing the risk of galling or seizing. However, it is important to use lubricants compatible with the materials involved to avoid any adverse chemical reactions. **Bolt tightening** procedures must be followed meticulously. Over-tightening can lead to flange warping or gasket failure, while under-tightening may result in leaks. The recommended torque values should be adhered to, and bolts should be tightened in a star pattern to ensure even distribution of force. **Gasket replacement** is another critical aspect; gaskets should be inspected for signs of wear and replaced as needed to maintain a tight seal. **Documentation and record-keeping** are vital components of a comprehensive maintenance program. Detailed records of inspections, maintenance activities, and any repairs or replacements help in tracking the history of each flange. This information can be invaluable for predictive maintenance strategies and compliance with regulatory standards. In addition to these routine practices, **periodic testing** may be required depending on the application. For instance, pressure testing can verify the integrity of the flange connection under operational conditions. It is also important to adhere to industry-specific standards and guidelines such as those provided by ASME (American Society of Mechanical Engineers) or API (American Petroleum Institute). By following these maintenance and inspection guidelines, operators can significantly reduce the risk of flange-related failures, ensure compliance with safety regulations, and optimize the performance of their equipment. Regular maintenance not only extends the lifespan of flanges but also contributes to a safer working environment by minimizing potential hazards associated with faulty connections. Thus, integrating these practices into routine operations is essential for maintaining reliable and efficient industrial systems.
Safety Precautions During Use
When it comes to the use of flanges, safety precautions are paramount to ensure the well-being of personnel and the integrity of the system. During installation, maintenance, and operation, several key considerations must be adhered to. First and foremost, proper training is essential; individuals handling flanges should be well-versed in their correct usage and any specific safety protocols associated with the particular type of flange being used. Personal protective equipment (PPE) such as gloves, safety glasses, and hard hats should always be worn to protect against potential hazards like flying debris or chemical spills. The environment in which the flange is being used also plays a critical role. Ensure that the workspace is clear of obstructions and that there are no flammable materials nearby, especially when working with flanges in high-pressure or high-temperature applications. Regular inspections are crucial; flanges should be checked for signs of wear, corrosion, or damage before each use. Any compromised flanges should be replaced immediately to prevent leaks or catastrophic failures. Proper tightening and loosening techniques are vital to avoid over-tightening or under-tightening, which can lead to gasket failure or other structural issues. Always follow the manufacturer's guidelines for torque specifications and use appropriate tools to avoid damaging the flange or surrounding components. Additionally, ensure that all connections are secure before pressurizing the system to prevent accidents caused by loose fittings. In situations where flanges are exposed to hazardous materials, extra precautions must be taken. Use compatible materials for gaskets and seals to prevent chemical reactions that could compromise the integrity of the flange. Emergency shutdown procedures should be clearly outlined and understood by all personnel involved in the operation of the system. Finally, adherence to industry standards and regulations is indispensable. Compliance with standards such as those set by the American Society of Mechanical Engineers (ASME) or the International Organization for Standardization (ISO) ensures that safety protocols are aligned with best practices. By meticulously following these safety precautions during the use of flanges, operators can significantly reduce the risk of accidents, maintain system reliability, and ensure a safe working environment. This comprehensive approach to safety underscores the importance of careful planning and execution in all phases of flange usage.