What Is A Fender

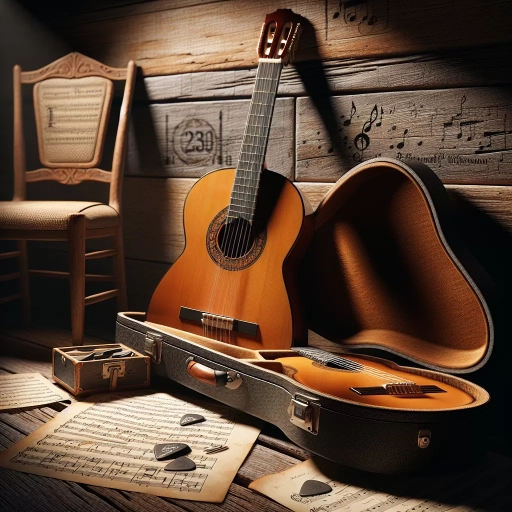
A fender, often overlooked but crucial in various contexts, plays a significant role in protecting and enhancing the functionality of different structures and vehicles. This article delves into the multifaceted world of fenders, providing a comprehensive overview that spans their fundamental principles, design and construction, and their diverse applications. To begin, it is essential to **Understand the Basics of a Fender**, which involves grasping its primary function and the materials used in its creation. This foundational knowledge sets the stage for exploring the intricate **Design and Construction of Fenders**, where we examine the engineering and craftsmanship that go into making these protective components. Finally, we will discuss the **Applications and Importance of Fenders**, highlighting their critical role in industries such as automotive, maritime, and construction. By understanding these aspects, readers will gain a deeper appreciation for the importance and versatility of fenders. Let us start by **Understanding the Basics of a Fender**.
Understanding the Basics of a Fender
Understanding the basics of a fender is crucial for anyone interested in maritime safety, boat maintenance, or simply appreciating the intricacies of nautical engineering. A fender serves as a protective barrier between a vessel and other objects, such as docks, piers, or other boats, preventing damage and ensuring smooth docking operations. To delve into the world of fenders, it is essential to explore three key aspects: their definition and purpose, historical development, and the various types available. Firstly, understanding the definition and purpose of a fender provides a foundational knowledge of its role in maritime safety. This includes how fenders are designed to absorb impact and distribute pressure, thereby safeguarding both the vessel and the docking structure. Secondly, examining the historical development of fenders reveals how these devices have evolved over time to meet changing maritime needs. From early wooden and rope fenders to modern materials like rubber and foam, this evolution highlights significant advancements in durability and effectiveness. Lastly, exploring the different types of fenders—such as cylindrical, bow, and corner fenders—demonstrates the versatility and specialized functions of these protective devices. Each type is tailored to specific docking scenarios, ensuring that there is a suitable fender for every maritime requirement. By starting with a clear understanding of what a fender is and its primary purpose, we can better appreciate its importance and functionality in various maritime contexts. Let us begin by defining and exploring the purpose of a fender in more detail.
Definition and Purpose
**Understanding the Basics of a Fender: Definition and Purpose** A fender, in its most fundamental form, is a protective barrier designed to absorb and distribute the impact of collisions, thereby safeguarding the integrity of a vehicle or structure. The term "fender" is often used interchangeably with "bumper," although they serve slightly different purposes. While a bumper is typically a rigid structure at the front or rear of a vehicle intended to absorb minor impacts, a fender is more specifically the metal panel that covers the wheel wells and supports the bumper. The primary purpose of a fender is to shield the vehicle's body from damage caused by road debris, minor accidents, and weather conditions. In automotive contexts, fenders are crucial for maintaining the aesthetic appeal and structural integrity of a vehicle. They are usually made from durable materials such as steel or fiberglass and are designed to be replaceable in case of damage. This replaceability ensures that minor accidents do not result in extensive repairs to the entire vehicle body. Additionally, fenders play a significant role in aerodynamics by helping to direct airflow around the vehicle, which can improve fuel efficiency and overall performance. Beyond their functional benefits, fenders also contribute to the overall design and style of a vehicle. They can be customized with various finishes and designs to enhance the vehicle's appearance, making them an essential component for car enthusiasts who value both form and function. In maritime contexts, fenders serve a similar protective role but are typically larger and more robust to handle the forces involved in docking and undocking operations. Here, they protect both the vessel and the dock from damage during these maneuvers. In summary, the definition and purpose of a fender revolve around its role as a protective and supportive component that enhances safety, durability, and aesthetics. Whether on land or sea, fenders are indispensable elements that ensure the longevity and operational efficiency of vehicles and structures by mitigating potential damage from everyday use and minor impacts. Understanding the basics of fenders is essential for appreciating their multifaceted contributions to both functionality and design in various applications.
Historical Development
The historical development of fenders is a fascinating narrative that intertwines technological innovation, maritime evolution, and practical necessity. The concept of fenders dates back to ancient times when ships were first constructed. In the earliest days of seafaring, sailors used natural materials such as logs, stones, or even animal hides to protect their vessels from damage during docking or collisions. As maritime trade and naval warfare expanded, so did the need for more robust and effective protective measures. During the Age of Sail, wooden fenders became common. These were often simple wooden blocks or planks attached to the hulls of ships to absorb impacts. The introduction of iron and steel in shipbuilding during the Industrial Revolution led to the development of more durable fendering systems. Metal fenders were initially cumbersome but provided superior protection against the rigors of docking and undocking. The late 19th and early 20th centuries saw significant advancements in fender technology. The invention of rubber and its subsequent use in fender design revolutionized the industry. Rubber fenders offered greater elasticity and shock absorption compared to their metal counterparts, reducing damage to both ships and dock structures. This period also witnessed the introduction of pneumatic fenders, which could be inflated to varying pressures to accommodate different types of vessels and docking conditions. In the mid-20th century, synthetic materials like polyurethane and polyethylene began to be used in fender manufacturing. These materials offered enhanced durability, resistance to weathering, and lower maintenance costs. Modern fenders now come in a variety of shapes, sizes, and materials tailored for specific applications—from small recreational boats to massive container ships. The development of fenders has also been influenced by advancements in dock design and construction. Modern docking systems often incorporate sophisticated fendering systems that include energy-absorbing materials, flexible panels, and even intelligent fender systems that can monitor and adjust to different docking scenarios. These innovations have significantly reduced the risk of damage during berthing operations, enhancing safety and efficiency in maritime operations. Understanding the historical development of fenders provides a deeper appreciation for their importance in modern maritime practices. From humble beginnings with natural materials to the sophisticated, high-tech solutions of today, fenders have evolved to meet the changing needs of an increasingly complex and demanding maritime environment. This evolution underscores the critical role that fenders play in protecting vessels, docks, and the people involved in maritime activities, making them an indispensable component of safe and efficient seafaring operations.
Types of Fenders
When delving into the world of fenders, it becomes evident that these protective barriers come in a variety of types, each designed to serve specific purposes and cater to different needs. **Bumper Fenders**, for instance, are the most common type and are integrated into the front and rear bumpers of vehicles. These fenders are typically made of durable materials such as plastic or metal and are engineered to absorb minor impacts without sustaining significant damage. **Cycle Fenders**, on the other hand, are designed for bicycles and motorcycles, providing protection from mud, water, and debris thrown up by the wheels. These fenders are usually lightweight and aerodynamically shaped to enhance performance. **Marine Fenders** are another crucial type, used in the maritime industry to protect boats and ships from damage during docking or mooring. These fenders can be made from materials like rubber, foam, or even inflatable designs, offering varying levels of cushioning and durability. **Dock Fenders**, a subset of marine fenders, are specifically designed for use on docks and piers, ensuring that vessels can safely come alongside without causing damage to either the boat or the docking structure. In industrial settings, **Machine Fenders** play a vital role in safeguarding equipment and machinery from accidental impacts. These fenders are often made from robust materials like steel or heavy-duty plastics and are mounted around machinery to prevent damage from moving parts or external collisions. **Railway Fenders** are specialized for use in rail transportation, protecting trains and railway infrastructure from potential collisions at stations or during maintenance operations. For construction and heavy-duty applications, **Rubber Fenders** are widely used due to their high resilience and ability to absorb significant impacts without permanent deformation. These fenders can be found in various forms, including cylindrical, square, or even custom shapes tailored to specific requirements. **Plastic Fenders**, while less common than their rubber counterparts, offer a lighter alternative with good resistance to corrosion and weathering. In addition to these types, there are also **Inflatable Fenders** which are particularly useful in situations where space is limited or where the fender needs to be easily deployable. These inflatable designs are often used in marine environments but can also be adapted for other applications requiring temporary or adjustable protection. Understanding the different types of fenders is essential for selecting the right one for your specific needs. Whether it's for vehicle protection, maritime safety, industrial safeguarding, or any other application, choosing the appropriate fender type ensures optimal performance and longevity. Each type of fender has its unique characteristics, advantages, and uses, making it crucial to consider factors such as material durability, impact resistance, and environmental conditions when making a selection. By recognizing these distinctions, you can better appreciate the role that fenders play in various contexts and make informed decisions to enhance safety and efficiency.
Design and Construction of Fenders
The design and construction of fenders are critical components in maritime and coastal engineering, ensuring the safety and integrity of both vessels and docking infrastructure. A comprehensive understanding of fender systems involves several key aspects: the materials used, the structural components that make up these systems, and the customization options available to meet specific needs. **Materials Used** is a foundational element, as the choice of material directly impacts the durability, performance, and cost-effectiveness of fenders. From traditional rubber and foam to advanced polyurethane and hybrid materials, each type offers unique benefits and drawbacks that must be carefully considered. **Structural Components** delve into the intricate details of how these materials are assembled and integrated into functional units. This includes understanding the various types of fenders such as pneumatic, foam-filled, and cell fenders, each with its own set of advantages and applications. **Customization Options** highlight the flexibility and adaptability of modern fender systems. Whether it's tailoring dimensions to fit specific dock configurations or incorporating specialized features for enhanced performance, customization ensures that fenders can be optimized for a wide range of operational environments. By examining these three critical areas—materials used, structural components, and customization options—we can gain a deeper appreciation for the complexity and importance of fender design and construction. Let's begin by exploring the **Materials Used** in greater detail.
Materials Used
When it comes to the design and construction of fenders, the choice of materials is paramount for ensuring durability, functionality, and aesthetic appeal. Fenders, which serve as protective barriers between vehicles and other objects, must withstand various environmental conditions and impacts. Here, several key materials are commonly utilized due to their unique properties. **Rubber** is one of the most traditional and widely used materials for fenders. Its flexibility allows it to absorb impacts without sustaining significant damage, making it an ideal choice for automotive applications. Rubber fenders can be found in various forms, from simple bumper strips to more complex designs that integrate with vehicle bodywork. Additionally, rubber's resistance to weathering and UV degradation ensures that it remains effective over time. **Plastic**, particularly high-impact plastics like polypropylene and polyethylene, is another popular material for fenders. These plastics offer excellent strength-to-weight ratios, making them lightweight yet robust. They can be molded into complex shapes and are often used in modern vehicle designs where aerodynamics and aesthetics are crucial. Plastic fenders can also be reinforced with fibers or other additives to enhance their impact resistance. **Steel** and **aluminum** are metals frequently used in fender construction, especially in heavy-duty applications such as trucks and industrial vehicles. Steel provides exceptional strength and rigidity, while aluminum offers a lighter alternative with comparable durability. These metals can be formed into various shapes and are often used in conjunction with other materials to create hybrid fender systems that balance weight and strength. **Composite materials**, such as fiberglass and carbon fiber, are gaining popularity in high-performance vehicle designs. These materials offer superior strength-to-weight ratios compared to traditional metals, allowing for the creation of lightweight yet incredibly strong fenders. Composite fenders are particularly beneficial in racing and sports cars where every gram of weight saved can translate into improved performance. **Recycled materials** are also being increasingly incorporated into fender design to promote sustainability. Recycled plastics and rubber can be repurposed into durable fender components, reducing waste and the environmental footprint of vehicle manufacturing. This trend aligns with the automotive industry's growing focus on eco-friendly practices. In addition to these primary materials, various **coatings** and **treatments** are applied to enhance fender performance. For instance, UV-resistant coatings protect against sun damage, while anti-corrosive treatments ensure that metal fenders remain rust-free in harsh environments. These finishes not only extend the lifespan of the fender but also maintain its appearance over time. The selection of materials for fender construction is a critical aspect of vehicle design, influenced by factors such as intended use, environmental conditions, and regulatory requirements. By leveraging the unique properties of different materials—whether it's the flexibility of rubber, the strength of metals, or the lightweight nature of composites—manufacturers can create fenders that are both functional and aesthetically pleasing. This thoughtful material selection ensures that fenders not only protect vehicles from damage but also contribute to their overall performance and longevity.
Structural Components
In the design and construction of fenders, understanding the role and functionality of structural components is crucial for ensuring durability, safety, and performance. Structural components are the backbone of any fender system, providing the necessary strength and stability to withstand various environmental and operational stresses. These components typically include the fender panel, which is the primary contact surface between the fender and the vessel or dock; the backing panel, which adds additional support and helps distribute impact forces; and the mounting system, comprising brackets, bolts, and other hardware that secure the fender to its base structure. The fender panel itself can be made from a variety of materials such as rubber, polyurethane, or foam, each chosen for its specific properties like resilience, energy absorption, and resistance to wear. For instance, rubber fenders are popular due to their high elasticity and ability to absorb significant impact without permanent deformation. Polyurethane fenders offer a balance between hardness and flexibility, making them suitable for applications requiring both durability and energy absorption. Foam fenders, on the other hand, are lighter and often used in smaller-scale applications where weight is a concern. The backing panel plays a critical role in enhancing the structural integrity of the fender by providing additional support against compressive forces. This component helps in distributing the impact load more evenly across the fender panel, thereby reducing the risk of damage or failure. The material selection for backing panels often includes steel or reinforced concrete, chosen for their high strength-to-weight ratio and ability to resist deformation under load. The mounting system is another vital structural component that ensures the fender remains securely attached to its base structure. This includes brackets that are designed to absorb and distribute forces efficiently, bolts that provide secure fastening, and sometimes additional reinforcement like shear plates or anchor rods. The design of these mounting components must consider factors such as corrosion resistance, particularly in marine environments where exposure to seawater is common. In addition to these primary structural components, other elements such as end caps and protective coatings also contribute significantly to the overall performance of fenders. End caps prevent damage to the edges of fender panels during impacts, while protective coatings help protect against environmental degradation and extend the lifespan of the fender. When designing and constructing fenders, engineers must carefully consider the interplay between these structural components to achieve optimal performance. This involves conducting thorough analyses of expected loads, environmental conditions, and operational requirements. Advanced computational tools like finite element analysis (FEA) are often employed to simulate various scenarios and validate the design before actual construction begins. In summary, the structural components of fenders are essential for their functionality and longevity. By selecting appropriate materials and designing these components with careful consideration of operational demands and environmental factors, engineers can create fender systems that are both effective and durable. This attention to detail in structural design ensures that fenders can reliably protect vessels, docks, and other infrastructure from damage during berthing operations.
Customization Options
When it comes to the design and construction of fenders, customization options play a crucial role in ensuring that these protective barriers meet the specific needs of various applications. Fenders are not one-size-fits-all solutions; they must be tailored to accommodate different types of vessels, docking systems, and environmental conditions. For instance, in high-traffic ports, fenders may need to be more robust and durable to withstand frequent impacts. Here, customization allows for the use of reinforced materials such as polyurethane or rubber compounds that offer superior resistance to abrasion and compression. In addition to material selection, the shape and size of fenders can also be customized. For example, cone fenders are often preferred in berthing areas where space is limited due to their compact design and high energy absorption capacity. On the other hand, arch fenders might be chosen for larger vessels because they provide a wider contact area and better protection against severe impacts. The ability to customize these dimensions ensures that fenders can effectively mitigate damage without compromising operational efficiency. Another significant aspect of customization is the integration of advanced technologies. Modern fenders can be equipped with sensors and monitoring systems that detect impact forces and alert operators to potential damage or wear. This real-time data can help in predictive maintenance, reducing downtime and extending the lifespan of both the fenders and the docking infrastructure. Furthermore, some fenders can be designed with built-in mooring systems or quick-release hooks for easier berthing and unberthing processes, enhancing safety and reducing labor costs. Customization also extends to aesthetic considerations, particularly in marinas or recreational docking areas where visual appeal is important. Fenders can be color-coded or branded to match the aesthetic of the surrounding environment, making them blend seamlessly into their surroundings while still providing essential protection. This attention to detail not only enhances the overall appearance but also contributes to a more cohesive and professional-looking docking facility. Moreover, environmental factors must be considered during the customization process. In areas prone to extreme weather conditions such as high winds or icy waters, fenders may need specialized coatings or treatments to maintain their integrity. For instance, some fenders can be treated with UV-resistant materials to prevent degradation from sunlight exposure, while others might be designed with anti-freeze properties to remain flexible in cold temperatures. In conclusion, the customization options available in the design and construction of fenders are vast and multifaceted. By tailoring these protective barriers to specific requirements—whether it be material composition, shape and size, technological integration, aesthetic appeal, or environmental resilience—operators can ensure optimal performance and longevity. This level of customization not only enhances safety but also contributes to operational efficiency and cost-effectiveness in various maritime settings.
Applications and Importance of Fenders
Fenders are versatile protective devices that play a crucial role in various industries, ensuring safety, reducing damage, and enhancing operational efficiency. Their applications span across marine, automotive, and industrial sectors, each with unique benefits and importance. In the marine sector, fenders are essential for protecting vessels and dock structures from impact during berthing and mooring operations. They help prevent costly repairs and maintain the integrity of both ships and harbor facilities. In the automotive industry, fenders serve as critical components of vehicle design, safeguarding against minor collisions and maintaining the aesthetic appeal of vehicles. Additionally, in industrial settings, fenders are used to protect machinery and equipment from accidental impacts, thereby ensuring continuous operation and minimizing downtime. Understanding the diverse applications of fenders is key to appreciating their significance across these different fields. This article will delve into these uses, starting with the critical role of fenders in marine environments.
Marine Use
In the realm of marine use, fenders play a crucial role in safeguarding vessels, docks, and other marine infrastructure from damage caused by collisions and impacts. These protective devices are essential for ensuring the safety and longevity of both the ships and the docking facilities. When a vessel approaches a dock or another ship, the potential for collision is high, and this is where fenders come into play. By absorbing the impact and distributing the force evenly, fenders prevent significant damage to the hull of the ship and the dock's structure. This not only reduces maintenance costs but also minimizes downtime, allowing for smoother and more efficient maritime operations. The importance of fenders extends beyond mere protection; they are also critical for facilitating safe berthing and mooring processes. In busy ports where multiple vessels are constantly arriving and departing, the risk of accidental contact is heightened. Fenders provide a buffer zone that allows ships to dock securely without causing harm to either the vessel or the dock. This is particularly important for large cargo ships and tankers, which carry valuable and often hazardous materials. The use of high-quality fenders ensures that these operations are conducted with minimal risk, thereby safeguarding both human life and the environment. Moreover, fenders are designed to withstand various environmental conditions such as harsh weather, saltwater corrosion, and extreme temperatures. This durability makes them an indispensable asset in marine environments where equipment must be resilient to endure the rigors of sea and weather. For instance, pneumatic fenders are widely used in offshore applications due to their ability to absorb high impact forces while maintaining their shape and functionality over time. Similarly, foam-filled fenders offer excellent resistance to compression and are ideal for smaller vessels and recreational boats. In addition to their practical applications, fenders also contribute significantly to the economic viability of maritime industries. By reducing the frequency and severity of damage incidents, fenders help lower repair costs and minimize the need for frequent replacements. This translates into substantial savings for shipowners and port operators, who can then allocate resources more effectively towards other critical aspects of their operations. Furthermore, the reliability provided by fenders enhances operational efficiency, enabling ships to stay on schedule and maintain their cargo delivery commitments. From a regulatory perspective, the use of fenders is often mandated by maritime authorities to ensure compliance with safety standards. Ports and shipping companies must adhere to these regulations to avoid penalties and maintain their operational licenses. Therefore, investing in high-quality fenders is not just a best practice but a legal necessity that underscores the importance of safety in marine operations. In conclusion, the role of fenders in marine use cannot be overstated. They are vital components that safeguard vessels, docks, and other marine infrastructure from potential damage. By ensuring safe berthing, reducing maintenance costs, withstanding harsh environmental conditions, contributing to economic efficiency, and complying with regulatory standards, fenders are an indispensable part of modern maritime operations. Their importance underscores the critical need for robust protective measures in an industry where safety and reliability are paramount.
Automotive Use
In the realm of automotive design and functionality, fenders play a pivotal role that extends beyond mere aesthetics. These structural components are integral to the overall safety, performance, and durability of a vehicle. When it comes to automotive use, fenders serve multiple critical functions that underscore their importance. First and foremost, fenders act as protective barriers against road debris and weather elements. They shield the vehicle's body from stones, gravel, and other projectiles that could cause damage to the paintwork or underlying metal. This protective layer also helps in deflecting water and snow away from the vehicle's wheels, reducing the risk of hydroplaning and improving traction on wet or icy roads. Additionally, fenders help in maintaining the vehicle's aerodynamics by smoothing airflow around the wheels, which can enhance fuel efficiency and reduce wind noise. From a safety perspective, fenders are designed to absorb and distribute impact forces in the event of a collision. Modern fenders are often made from lightweight yet robust materials such as fiberglass or high-strength plastics that can crumple upon impact, thereby reducing the force transmitted to the vehicle's occupants. This crumple zone effect helps in mitigating injury severity by dissipating kinetic energy away from the passenger compartment. Moreover, fenders contribute significantly to the vehicle's structural integrity. They provide additional support to the body frame by acting as mounting points for various components like headlights, turn signals, and even suspension parts in some designs. This added reinforcement enhances the vehicle's overall rigidity and stability, particularly during cornering or braking maneuvers. The importance of fenders is also evident in their role in maintaining regulatory compliance. Automotive manufacturers must adhere to stringent safety standards set by governing bodies such as the National Highway Traffic Safety Administration (NHTSA) or the European New Car Assessment Programme (Euro NCAP). Fenders must be designed to meet these standards, ensuring that vehicles are safe for both occupants and other road users. In terms of maintenance and repair, fenders are relatively accessible components compared to other parts of the vehicle. This ease of access makes them simpler to inspect for damage and replace if necessary, which can be cost-effective for vehicle owners. Furthermore, modern fender designs often incorporate features like removable liners or clips that facilitate quicker repairs without compromising on safety or performance. Lastly, from an aesthetic standpoint, fenders significantly influence a vehicle's visual appeal. They can be styled to enhance the car's aerodynamic profile while also reflecting the brand's design language. Customizable fender flares or trim pieces allow owners to personalize their vehicles according to their preferences, adding a touch of individuality to what would otherwise be a standard model. In conclusion, the applications and importance of fenders in automotive use are multifaceted and far-reaching. They combine protective functionality with structural support and safety features while also contributing to the vehicle's overall performance and aesthetic appeal. As such, fenders remain an indispensable component in modern automotive design and engineering.
Industrial Applications
Industrial applications of fenders are diverse and critical, underscoring their importance in various sectors. In the maritime industry, fenders are essential for protecting docks, piers, and ships from damage during berthing operations. These fenders, often made from durable materials like rubber or polyurethane, absorb the impact of vessels docking, preventing costly repairs and ensuring safe navigation. For instance, pneumatic fenders are commonly used in ports due to their high energy absorption capacity and low reaction force, making them ideal for large vessels. In the construction sector, fenders play a crucial role in safeguarding structures from potential collisions. For example, bridge fenders protect bridge piers and abutments from boat impacts, while fender systems installed along riverbanks prevent erosion and damage from floating debris. Similarly, in the oil and gas industry, fenders are used to safeguard offshore platforms and pipelines from accidental collisions by ships or other marine vessels. The automotive industry also relies on fenders for both functional and aesthetic purposes. Vehicle fenders not only protect the body of the car from minor impacts but also contribute to the vehicle's aerodynamics and overall design. In manufacturing facilities, machine guards and safety barriers often incorporate fender-like components to prevent accidents and protect equipment. Furthermore, in the aerospace sector, specialized fenders are used to protect aircraft from ground handling equipment and other vehicles. These fenders are designed to be lightweight yet robust, ensuring they do not compromise the aircraft's performance while providing necessary protection. In addition to these specific applications, fenders are integral in various other industrial settings such as warehouses, where they protect racking systems from forklift impacts, and in rail transportation, where they safeguard tracks and rolling stock. The versatility of fenders extends to their material options; they can be made from a range of materials including steel, plastic, or even recycled rubber, each offering unique benefits depending on the application. The importance of fenders in industrial settings cannot be overstated. They not only prevent physical damage but also contribute to operational efficiency by reducing downtime for repairs. Moreover, they enhance safety standards by mitigating risks associated with collisions or impacts. As industries continue to evolve with technological advancements, the role of fenders will remain pivotal in ensuring the integrity and longevity of infrastructure and equipment. Therefore, understanding the applications and importance of fenders is crucial for maintaining optimal performance across various industrial sectors.