What Is Cfm

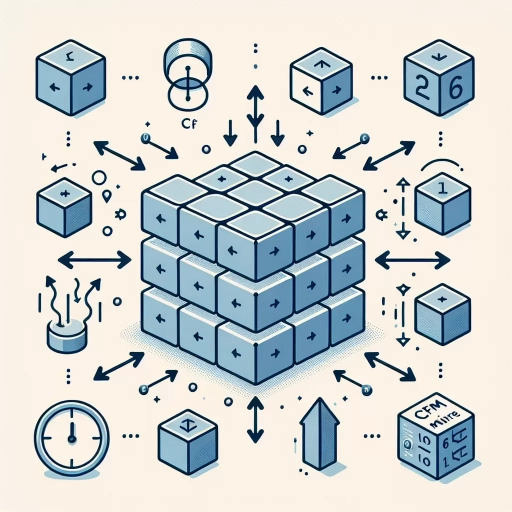
In the realm of engineering and industrial applications, the term "CFM" (Cubic Feet per Minute) is a crucial metric that measures the volume of air or gas flowing through a given space in a minute. Understanding CFM is essential for optimizing performance, efficiency, and safety in various systems. This article delves into the multifaceted world of CFM, starting with **Understanding the Basics of CFM**, where we explore its fundamental principles and how it is defined. We then examine **Applications and Uses of CFM**, highlighting its importance in HVAC systems, industrial processes, and other critical areas. Finally, we discuss **Calculations, Measurements, and Standards for CFM**, providing insights into how CFM is calculated, measured, and standardized to ensure accuracy and compliance. By grasping these concepts, readers will gain a comprehensive understanding of CFM and its pivotal role in modern engineering. Let's begin by diving into the foundational aspects of CFM to establish a solid groundwork for our exploration.
Understanding the Basics of CFM
Understanding the basics of CFM (Cubic Feet per Minute) is crucial for anyone involved in fields such as engineering, HVAC, and industrial processes. CFM is a fundamental metric that measures the volume of air or gas moving through a space or system over a specified period. To grasp the significance of CFM, it is essential to delve into its definition and abbreviation, which provide a clear understanding of what it represents. Additionally, exploring the historical context and development of CFM reveals how this measurement has evolved over time to become a standard in various industries. Finally, familiarizing oneself with the key components and terminology associated with CFM ensures a comprehensive understanding of its application and importance. By examining these aspects, readers can gain a solid foundation in understanding the basics of CFM, enabling them to make informed decisions and optimize systems effectively. This article will guide you through these critical elements, ensuring you have a thorough understanding of CFM.
Definition and Abbreviation
Understanding the basics of CFM (Cubic Feet per Minute) begins with a clear grasp of definitions and abbreviations. CFM is a unit of measurement used to describe the volume of air that flows through a given space in one minute. It is crucial in various fields such as HVAC (Heating, Ventilation, and Air Conditioning), industrial processes, and automotive systems. The term "CFM" itself stands for Cubic Feet per Minute, indicating the rate at which air moves. In the context of HVAC systems, CFM is essential for determining the efficiency and capacity of air handlers, fans, and blowers. For instance, a higher CFM rating means that the system can move more air, which is vital for maintaining optimal indoor air quality and temperature control. In industrial settings, CFM helps in calculating the airflow required for processes like ventilation in factories or dust collection systems. Abbreviations related to CFM include terms like SCFM (Standard Cubic Feet per Minute), which measures airflow at standard conditions of temperature and pressure, typically 60°F (15°C) and 1 atm. Another important abbreviation is ACFM (Actual Cubic Feet per Minute), which measures airflow under actual operating conditions, taking into account factors such as temperature and humidity. Understanding these definitions and abbreviations is fundamental because they help in selecting the right equipment for specific applications. For example, knowing the required CFM for a room or process allows engineers and technicians to choose fans or blowers that can meet those needs efficiently. Misunderstanding these terms can lead to underperformance or overcapacity issues, resulting in wasted energy and resources. Moreover, being familiar with CFM and its related abbreviations enables professionals to communicate effectively with clients and colleagues. It facilitates accurate specifications in project planning, ensuring that all stakeholders are on the same page regarding system requirements and performance expectations. In summary, grasping the definition of CFM and its associated abbreviations is pivotal for anyone working with air flow systems. It ensures that systems are designed and operated optimally, enhancing performance, efficiency, and overall effectiveness. By understanding these basics, individuals can make informed decisions that contribute to better air quality, energy efficiency, and system reliability.
Historical Context and Development
**Historical Context and Development** The concept of Cubic Feet per Minute (CFM) has its roots in the early days of industrialization, particularly in the 19th century when mechanical engineering and fluid dynamics began to take shape. As industries grew, the need to measure airflow and gas flow rates became increasingly important for optimizing processes in manufacturing, heating, ventilation, and air conditioning (HVAC) systems. The term "CFM" itself is a unit of measurement that quantifies the volume of air moving through a given space in one minute, expressed in cubic feet. Historically, the development of CFM as a standard unit was influenced by the Industrial Revolution. During this period, engineers like Sir Isaac Newton and later, Bernoulli, laid the foundational principles of fluid dynamics. These principles were crucial for understanding how fluids (including gases) behave under various conditions. As factories expanded and machinery became more complex, accurate measurements of airflow were necessary to ensure efficient operation and safety. In the late 19th and early 20th centuries, advancements in HVAC technology further solidified the importance of CFM. The invention of the first modern air conditioning system by Willis Carrier in 1902 marked a significant milestone. Carrier's system required precise control over airflow to maintain consistent temperatures and humidity levels, making CFM a critical metric. This innovation paved the way for widespread adoption of air conditioning in commercial and residential settings. The mid-20th century saw significant improvements in measurement tools and standards. The American Society of Heating, Refrigerating and Air-Conditioning Engineers (ASHRAE) played a pivotal role in standardizing CFM measurements through rigorous testing protocols and guidelines. These standards ensured that CFM readings were consistent across different applications, enhancing reliability and efficiency. Today, CFM remains a fundamental metric in various fields including HVAC, automotive engineering, and industrial processes. Modern technologies such as anemometers and flow meters have made it easier to accurately measure CFM with high precision. Understanding CFM is essential for designing efficient ventilation systems, optimizing engine performance in vehicles, and ensuring safe working conditions in industrial environments. In summary, the historical context and development of CFM are deeply intertwined with the evolution of industrial engineering and fluid dynamics. From its early roots in the Industrial Revolution to its current widespread use across multiple industries, CFM has become an indispensable tool for measuring airflow and ensuring optimal performance in a variety of applications. This understanding is crucial for anyone looking to grasp the basics of CFM and its practical applications.
Key Components and Terminology
To fully grasp the concept of CFM (Cubic Feet per Minute), it is crucial to understand its key components and associated terminology. **CFM** itself measures the volume of air that flows through a given space in one minute, typically used to describe the performance of fans, blowers, and other air-moving devices. A fundamental component in this context is **airflow**, which refers to the movement of air from one point to another. This airflow is influenced by several factors including **pressure**, **velocity**, and **resistance**. **Pressure**, often measured in inches of water gauge (in.w.g.) or pounds per square inch (PSI), is the force exerted by the air as it moves through a system. **Velocity**, measured in feet per minute (FPM), indicates the speed at which air travels. Understanding these metrics helps in calculating CFM using the formula: CFM = Area (in square feet) x Velocity (in feet per minute). Another critical term is **static pressure**, which is the resistance to airflow when the fan or blower is not operating. This is contrasted with **total pressure**, which includes both static and dynamic components when the system is in operation. **Dynamic pressure** accounts for the energy associated with moving air. **Ductwork** and **ventilation systems** also play significant roles in CFM calculations. Ducts are channels through which air flows, and their dimensions, shape, and material can affect airflow resistance. Ventilation systems, including components like grilles, diffusers, and dampers, further influence airflow patterns and overall system efficiency. Additionally, terms like **AMCA (Air Movement and Control Association) ratings** and **certifications** are important for ensuring that air-moving devices meet specific standards for performance and safety. These ratings provide a benchmark for comparing different products based on their CFM output under standardized conditions. In summary, understanding CFM requires a grasp of airflow dynamics, pressure measurements, velocity calculations, and the impact of ductwork and ventilation systems. By familiarizing yourself with these key components and terminology, you can better evaluate and optimize air-moving systems to achieve efficient and effective air circulation. This foundational knowledge is essential for making informed decisions in various applications ranging from residential heating and cooling to industrial ventilation systems.
Applications and Uses of CFM
Cubic Feet per Minute (CFM) is a crucial metric in various industries, measuring the volume of air that flows through a given space in one minute. This measurement is essential for ensuring efficient ventilation, air quality, and system performance across different settings. In industrial and commercial environments, CFM plays a vital role in maintaining safe working conditions and optimizing production processes. In residential settings, it is critical for the proper functioning of HVAC systems, ensuring comfortable living spaces and energy efficiency. Beyond these common applications, CFM also has specialized uses in various industries such as healthcare, aerospace, and manufacturing, where precise air flow control is paramount. Understanding the applications and uses of CFM in these diverse contexts is fundamental to appreciating its significance. By delving into industrial and commercial settings, residential and HVAC systems, and specialized applications, we can gain a comprehensive insight into the importance of CFM. This article will explore these facets in detail, ultimately leading to a deeper understanding of the basics of CFM.
Industrial and Commercial Settings
In industrial and commercial settings, the measurement of Cubic Feet per Minute (CFM) plays a crucial role in ensuring efficient operations, safety, and compliance with regulatory standards. CFM is essential for evaluating the performance of ventilation systems, which are vital for maintaining air quality and removing hazardous substances from the work environment. For instance, in manufacturing facilities, CFM measurements help in designing and optimizing ventilation systems to remove dust, fumes, and other airborne contaminants that could pose health risks to workers. This not only improves workplace safety but also enhances productivity by providing a healthier environment. In commercial buildings such as offices, malls, and hotels, CFM is critical for heating, ventilation, and air conditioning (HVAC) systems. Proper CFM ensures that the air is circulated effectively, maintaining a comfortable temperature and humidity level. This is particularly important in densely populated areas where inadequate ventilation can lead to discomfort and health issues among occupants. Additionally, accurate CFM measurements are necessary for energy efficiency; over- or under-ventilation can significantly impact energy consumption and operational costs. In healthcare facilities, precise CFM measurements are crucial for infection control and patient safety. Ventilation systems must be designed to meet specific CFM requirements to prevent the spread of airborne pathogens and maintain sterile environments. Similarly, in food processing plants, CFM is vital for ensuring that air quality meets food safety standards by controlling moisture levels and preventing contamination. Furthermore, CFM is a key factor in compliance with various industrial and commercial regulations. For example, OSHA (Occupational Safety and Health Administration) standards require specific ventilation rates to ensure worker safety in various industries. Non-compliance can result in fines and legal repercussions, making accurate CFM measurements a necessity for risk management. In summary, CFM is an indispensable metric in industrial and commercial settings due to its impact on worker safety, operational efficiency, energy consumption, and regulatory compliance. By accurately measuring and managing CFM, businesses can create healthier work environments, optimize their operations, and reduce costs while adhering to stringent safety and health standards. This underscores the importance of understanding and applying CFM principles across diverse industrial and commercial applications.
Residential and HVAC Systems
In the realm of residential and HVAC (Heating, Ventilation, and Air Conditioning) systems, understanding CFM (Cubic Feet per Minute) is crucial for ensuring optimal performance, efficiency, and comfort. CFM measures the volume of air that an HVAC system can move or exchange within a given time frame, typically one minute. This metric is essential for several reasons. Firstly, it helps in sizing the HVAC system appropriately for a residential space. An undersized system may struggle to maintain desired temperatures, while an oversized system can lead to inefficiency and higher energy bills. By calculating the CFM requirements based on factors such as room size, insulation quality, and desired airflow rates, homeowners can ensure their HVAC system operates effectively. Moreover, CFM plays a significant role in maintaining indoor air quality. Proper ventilation is vital for removing stale air and introducing fresh air into the home. This is particularly important in modern homes that are often well-sealed to conserve energy but can suffer from poor air circulation. By ensuring that the HVAC system has adequate CFM, homeowners can prevent issues like moisture buildup, mold growth, and the accumulation of indoor pollutants. Additionally, CFM affects the distribution of heated or cooled air throughout the home. Balanced airflow ensures that each room receives an appropriate amount of conditioned air, preventing hot spots in summer or cold spots in winter. From a practical standpoint, understanding CFM also aids in selecting the right components for an HVAC system. For instance, choosing fans with the correct CFM rating ensures they can handle the airflow demands without overworking or underperforming. Similarly, when installing ductwork, knowing the CFM requirements helps in designing ducts that minimize resistance and maximize airflow efficiency. This not only enhances system performance but also reduces noise levels and prolongs the lifespan of the equipment. In terms of energy efficiency, CFM is a key factor. An HVAC system operating at optimal CFM levels consumes less energy compared to one that is either over- or under-sized. This translates into lower utility bills and a reduced carbon footprint. Furthermore, many modern HVAC systems come with features like variable speed fans that adjust CFM based on real-time conditions to optimize energy use. In conclusion, CFM is a fundamental aspect of residential HVAC systems. It influences system sizing, indoor air quality, airflow distribution, component selection, and overall energy efficiency. By grasping the importance of CFM and ensuring it aligns with the specific needs of a home, homeowners can enjoy a more comfortable living environment while minimizing operational costs and environmental impact. This understanding is pivotal for making informed decisions when installing or upgrading an HVAC system, ultimately leading to better performance and satisfaction.
Specialized Applications in Various Industries
Specialized applications of CFM (Cubic Feet per Minute) are ubiquitous across various industries, each leveraging this measurement to optimize performance, efficiency, and safety. In the **HVAC (Heating, Ventilation, and Air Conditioning) industry**, CFM is crucial for designing ventilation systems that ensure proper air circulation and indoor air quality. For instance, HVAC engineers use CFM to calculate the airflow required to maintain comfortable temperatures and humidity levels in buildings, thereby enhancing occupant health and productivity. In **industrial manufacturing**, CFM plays a vital role in dust collection and fume extraction systems. By accurately measuring airflow, manufacturers can ensure that hazardous particles are effectively removed from the workspace, reducing the risk of respiratory diseases among workers. This also helps in maintaining a clean environment, which is essential for precision manufacturing processes. The **automotive industry** relies heavily on CFM for engine performance tuning. Airflow meters measure the CFM of air entering the engine, allowing technicians to adjust fuel injection rates precisely, which improves engine efficiency, power output, and fuel economy. Additionally, CFM is used in vehicle ventilation systems to provide a comfortable driving environment. In **medical facilities**, precise airflow measurement is critical for maintaining sterile environments. Operating rooms and laboratories require controlled air circulation to prevent contamination and ensure patient safety. CFM measurements help in designing these systems to meet stringent standards. The **aerospace industry** also utilizes CFM for various applications, including cabin pressurization and air supply systems in aircraft. Accurate airflow measurements are essential for maintaining a safe internal environment during flight, ensuring passenger comfort and safety. Furthermore, in **agriculture**, CFM is used in grain drying and ventilation systems. Proper airflow helps in drying grains efficiently, reducing moisture content to prevent spoilage and maintain crop quality. This is particularly important for large-scale farming operations where timely and effective drying can significantly impact yield and profitability. Lastly, **environmental monitoring** relies on CFM to measure air quality and detect pollutants. Air samplers use CFM to collect representative samples of air, which are then analyzed for various pollutants, helping in the enforcement of environmental regulations and public health policies. In summary, the measurement of CFM is a fundamental aspect across diverse industries, enabling the design and operation of efficient, safe, and high-performance systems. Whether it's ensuring indoor air quality, optimizing engine performance, or maintaining sterile environments, CFM remains an indispensable metric that drives innovation and excellence in various fields.
Calculations, Measurements, and Standards for CFM
Calculations, measurements, and standards are crucial components in understanding and managing airflow, particularly when it comes to Cubic Feet per Minute (CFM). CFM is a vital metric in various industries, including HVAC, manufacturing, and construction, as it determines the efficiency and effectiveness of ventilation systems. To grasp the concept of CFM fully, it is essential to delve into three key areas: **Formulas and Calculation Methods**, which provide the mathematical foundation for determining airflow rates; **Measurement Tools and Techniques**, which outline the practical approaches to measuring CFM accurately; and **Industry Standards and Regulations**, which ensure compliance with safety and performance guidelines. By exploring these aspects, individuals can gain a comprehensive understanding of how to calculate, measure, and adhere to standards for CFM. This article aims to guide readers through these critical elements, ultimately leading to a deeper **Understanding the Basics of CFM**.
Formulas and Calculation Methods
When delving into the realm of CFM (Cubic Feet per Minute), understanding the underlying formulas and calculation methods is crucial for accurate measurements and standards. CFM is a measure of airflow, often used in HVAC systems, industrial processes, and various engineering applications. The calculation of CFM involves several key formulas that help in determining the volume of air moving through a given space or system. One fundamental formula for calculating CFM is derived from the relationship between volume, area, and velocity: \( \text{CFM} = \text{Area} \times \text{Velocity} \). Here, the area is typically measured in square feet and velocity in feet per minute. For instance, if you know the cross-sectional area of a duct and the air velocity within it, you can easily compute the CFM using this formula. Another critical method involves using the fan curve or performance data provided by manufacturers. These curves plot airflow against static pressure, allowing engineers to select fans that meet specific CFM requirements under various operating conditions. Additionally, the use of psychrometric charts can be essential for calculating CFM in systems where humidity and temperature variations are significant. In practical applications, measurements are often taken using anemometers or pitot tubes to determine air velocities at multiple points within a duct or system. These readings are then averaged to obtain a representative velocity value, which is subsequently used in CFM calculations. It's also important to consider factors such as duct shape, size, and any obstructions that could affect airflow patterns. Standards for CFM calculations are typically governed by industry bodies like ASHRAE (American Society of Heating, Refrigerating and Air-Conditioning Engineers) and AMCA (Air Movement and Control Association). These organizations provide guidelines on measurement techniques, instrumentation accuracy, and data interpretation to ensure consistency and reliability across different applications. In summary, mastering the formulas and calculation methods for CFM is essential for ensuring accurate airflow measurements and compliance with industry standards. By understanding these principles and applying them correctly, engineers can design more efficient systems, optimize performance, and maintain high levels of air quality and safety. Whether in HVAC design, industrial ventilation, or other fields requiring precise airflow control, a solid grasp of CFM calculations is indispensable.
Measurement Tools and Techniques
**Measurement Tools and Techniques** Accurate measurement is the cornerstone of understanding and managing airflow, particularly when dealing with Cubic Feet per Minute (CFM). To ensure precise calculations and standards, various measurement tools and techniques are employed. At the forefront are **anemometers**, which measure air velocity. These devices come in different types, such as vane anemometers, hot wire anemometers, and pitot tubes, each suited for specific applications. For instance, vane anemometers are versatile and widely used for general airflow measurements, while hot wire anemometers offer high precision in more controlled environments. Another critical tool is the **manometer**, which measures pressure differences across ducts or vents. This is essential for calculating airflow rates using the Bernoulli's principle. **Thermocouples** and **thermistors** are also crucial as they measure temperature, a factor that influences air density and thus affects CFM calculations. Additionally, **flow hoods** and **balometers** are specialized tools that measure airflow directly at vents or ducts, providing immediate readings that can be used to adjust systems for optimal performance. Advanced techniques include **tracer gas methods**, where a known quantity of a gas is released into the system and its concentration is measured downstream to calculate airflow rates. **Laser Doppler velocimetry (LDV)** and **particle image velocimetry (PIV)** are sophisticated methods used in research and development to measure detailed airflow patterns with high accuracy. In practice, these tools are often combined with **data loggers** and **software** to collect, analyze, and interpret data over time. This integration allows for real-time monitoring and adjustments, ensuring that airflow systems operate within specified standards. For example, in HVAC systems, continuous monitoring helps maintain indoor air quality and energy efficiency by adjusting CFM based on real-time data. Standards such as those set by the American Society of Heating, Refrigerating, and Air-Conditioning Engineers (ASHRAE) and the International Organization for Standardization (ISO) provide guidelines for the selection and use of these measurement tools. Adhering to these standards ensures that measurements are reliable and consistent across different applications. In summary, the array of measurement tools and techniques available for determining CFM is diverse and sophisticated. By selecting the appropriate tool for the specific task at hand and adhering to established standards, professionals can ensure accurate calculations and optimal performance of airflow systems. This precision is vital not only for maintaining efficiency but also for ensuring safety and compliance with regulatory requirements.
Industry Standards and Regulations
Industry standards and regulations play a crucial role in ensuring the accuracy, safety, and consistency of calculations, measurements, and standards for Cubic Feet per Minute (CFM), a key metric in various industrial and commercial applications. These standards are established by reputable organizations such as the American Society of Heating, Refrigerating, and Air-Conditioning Engineers (ASHRAE) and the International Organization for Standardization (ISO). For instance, ASHRAE Standard 62.1 outlines the minimum ventilation rates for commercial buildings, which directly impacts CFM calculations to ensure indoor air quality. Similarly, ISO 14644 specifies the requirements for cleanrooms, where precise CFM measurements are critical for maintaining controlled environments. Compliance with these standards is not only mandatory but also beneficial as it ensures that equipment and systems operate efficiently and safely. Regulatory bodies like the Occupational Safety and Health Administration (OSHA) in the United States enforce standards that include ventilation requirements to protect worker health and safety. In the context of CFM, these regulations dictate the minimum airflow rates necessary to remove hazardous substances from workspaces, thereby safeguarding employees from potential health risks. Moreover, industry standards provide a common language and framework for manufacturers, engineers, and users to communicate effectively about CFM specifications. This uniformity helps in comparing different products and systems accurately, facilitating informed decision-making. For example, the Air Movement and Control Association International (AMCA) certifies fans and blowers based on their performance, including CFM ratings, which helps in selecting the right equipment for specific applications. In addition to safety and efficiency, adhering to industry standards enhances the reliability of CFM measurements. Standardized testing protocols, such as those outlined by ASHRAE and ISO, ensure that measurements are taken under consistent conditions, reducing variability and improving the accuracy of calculations. This reliability is crucial in industries where precise airflow control is vital, such as in pharmaceutical manufacturing or data centers. Overall, industry standards and regulations are essential for maintaining the integrity of CFM calculations and measurements. They provide a structured approach to ensuring compliance with safety guidelines, enhancing operational efficiency, and promoting uniformity across different sectors. By adhering to these standards, professionals can ensure that their systems operate optimally, contributing to better performance, safety, and overall quality in various applications where CFM is a critical parameter.