What Does Cim Mean

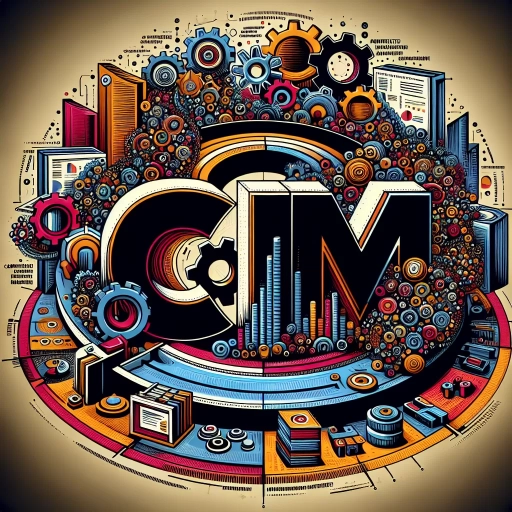
In the rapidly evolving landscape of technology and manufacturing, the term "CIM" (Computer-Integrated Manufacturing) has become a cornerstone of modern industrial practices. CIM represents a holistic approach to production, integrating various aspects of manufacturing processes under a unified, computer-controlled system. This innovative methodology not only enhances efficiency and productivity but also opens up new avenues for applications and uses across diverse industries. Understanding the basics of CIM is crucial for grasping its full potential, which includes the seamless integration of design, production, and quality control. As we delve into the world of CIM, we will explore its applications and uses, highlighting how it transforms traditional manufacturing paradigms. Additionally, we will examine the benefits and future prospects of CIM, shedding light on its role in shaping the future of industry. To begin this journey, it is essential to **Understand the Basics of CIM**, laying the groundwork for a comprehensive exploration of this transformative technology.
Understanding the Basics of CIM
Understanding the basics of Computer-Integrated Manufacturing (CIM) is crucial for anyone interested in modern industrial processes. CIM represents a holistic approach to manufacturing, integrating various aspects of production to enhance efficiency, quality, and productivity. To grasp the essence of CIM, it is essential to delve into three key areas: the definition and acronym expansion, historical context and development, and core principles and objectives. Firstly, understanding the definition and acronym expansion of CIM sets the foundation for comprehending its scope and components. This involves breaking down what each letter stands for and how these elements interconnect within the manufacturing process. Secondly, exploring the historical context and development of CIM provides insight into how this concept evolved over time. This includes understanding the technological advancements and industrial needs that drove its creation. Lastly, examining the core principles and objectives of CIM reveals its operational framework and goals. This involves looking at how CIM aims to streamline production, improve quality control, and optimize resource allocation. By starting with a clear definition and understanding of what CIM entails, we can then navigate through its historical development and finally, delve into its core principles and objectives. Let's begin by expanding on the definition and acronym of CIM to establish a solid foundation for our exploration.
Definition and Acronym Expansion
**Understanding the Basics of CIM: Definition and Acronym Expansion** To delve into the intricacies of CIM, it is essential to start with its fundamental definition and acronym expansion. CIM stands for Computer-Integrated Manufacturing, a term that encapsulates the integration of various manufacturing processes and systems using computer technology. This integration aims to enhance efficiency, productivity, and quality by automating and optimizing all aspects of the manufacturing process. At its core, CIM involves the use of computers to control and coordinate different manufacturing functions such as design, production planning, material handling, and quality control. The acronym itself breaks down into three key components: **Computer**, **Integrated**, and **Manufacturing**. The **Computer** aspect refers to the use of advanced computer systems and software to manage and control manufacturing operations. **Integrated** signifies the seamless connection and coordination between different departments and processes within the manufacturing environment. Finally, **Manufacturing** encompasses all activities related to the production of goods. In practice, CIM integrates various technologies including Computer-Aided Design (CAD), Computer-Aided Manufacturing (CAM), and Enterprise Resource Planning (ERP) systems. CAD allows for the digital design of products, while CAM translates these designs into instructions for automated machinery. ERP systems manage business resources such as materials, labor, and finances in real-time, ensuring that all components of the manufacturing process are aligned and optimized. The implementation of CIM has numerous benefits for manufacturers. It reduces production time and costs by minimizing manual errors and maximizing automation. It also enhances product quality through precise control over production processes and real-time monitoring. Additionally, CIM facilitates better decision-making by providing comprehensive data analytics and insights into every stage of the manufacturing cycle. In summary, understanding CIM begins with grasping its definition as an integrated system that leverages computer technology to streamline and optimize manufacturing processes. By breaking down the acronym into its constituent parts—computer, integrated, and manufacturing—we gain a clearer insight into how CIM operates to improve efficiency, quality, and overall performance in modern manufacturing environments. This foundational knowledge is crucial for appreciating the broader implications and applications of CIM in contemporary industrial settings.
Historical Context and Development
**Historical Context and Development** The concept of Computer-Integrated Manufacturing (CIM) has its roots in the late 20th century, emerging as a response to the need for greater efficiency and productivity in manufacturing processes. In the 1960s and 1970s, advancements in computer technology and automation began to transform industrial practices. The introduction of Numerical Control (NC) machines, which could be programmed to perform specific tasks, marked an early step towards integrating computers into manufacturing. By the 1980s, this integration had evolved into Computer-Aided Design (CAD), Computer-Aided Manufacturing (CAM), and Computer-Aided Engineering (CAE). These technologies allowed for the digital design of products, simulation of manufacturing processes, and automated production planning. The term "CIM" was coined during this period to describe the holistic approach of integrating these various computer-aided systems to create a seamless flow from design to production. The development of CIM was further accelerated by advancements in networking technologies and the advent of Enterprise Resource Planning (ERP) systems. ERP allowed companies to manage all aspects of their operations, including supply chain management, inventory control, and human resources, through a single integrated platform. This integration enabled real-time data sharing across different departments, enhancing decision-making and operational efficiency. In the 1990s and early 2000s, CIM continued to evolve with the introduction of new technologies such as Product Lifecycle Management (PLM) and Manufacturing Execution Systems (MES). PLM focused on managing the entire lifecycle of a product from conception through disposal, while MES provided real-time monitoring and control over production processes. These advancements allowed for more precise control over manufacturing operations and better coordination between different stages of production. Today, CIM is at the forefront of Industry 4.0, which emphasizes the use of smart technologies such as artificial intelligence, machine learning, and the Internet of Things (IoT). These technologies enable real-time data analytics, predictive maintenance, and autonomous decision-making within manufacturing environments. The integration of these smart technologies into CIM systems has significantly enhanced productivity, reduced costs, and improved product quality. Understanding the historical context and development of CIM is crucial for appreciating its current role in modern manufacturing. From its early beginnings with NC machines to its current state with Industry 4.0 technologies, CIM has continuously evolved to meet the changing needs of industry. This evolution underscores the importance of integrating various technological advancements to achieve optimal efficiency and innovation in manufacturing processes. As industries continue to adopt more sophisticated technologies, the principles of CIM remain foundational in driving forward the future of manufacturing.
Core Principles and Objectives
Understanding the basics of Customer Interaction Management (CIM) begins with grasping its core principles and objectives. At its heart, CIM is designed to enhance and streamline interactions between a business and its customers, fostering a more personalized, efficient, and satisfying experience. The core principles of CIM revolve around several key tenets: **customer-centricity**, **integration**, **real-time responsiveness**, and **data-driven decision-making**. **Customer-centricity** is the foundation of CIM, emphasizing the importance of understanding and meeting individual customer needs. This involves leveraging various channels—such as social media, email, phone, and in-person interactions—to engage with customers in their preferred manner. By doing so, businesses can build stronger relationships and improve customer satisfaction. **Integration** is another critical principle, as it ensures that all customer touchpoints are interconnected. This means that data from different channels is consolidated into a single, unified view, allowing businesses to have a comprehensive understanding of each customer's history and preferences. Integrated systems enable seamless transitions between different communication channels, reducing friction and enhancing the overall customer experience. **Real-time responsiveness** is essential for modern customer interaction management. With the advent of digital technologies, customers expect immediate responses to their queries and concerns. CIM systems are designed to provide real-time feedback and support, whether through automated chatbots or live agents, ensuring that customer issues are addressed promptly and effectively. Finally, **data-driven decision-making** underpins the effectiveness of CIM. By analyzing customer data from various sources, businesses can gain valuable insights into customer behavior, preferences, and pain points. This data can be used to tailor marketing campaigns, improve product offerings, and optimize customer service processes, ultimately driving better outcomes for both the business and its customers. The objectives of CIM are multifaceted but ultimately focused on improving customer satisfaction and driving business success. Key objectives include **enhancing customer engagement**, **improving operational efficiency**, **increasing customer retention**, and **boosting revenue**. By engaging customers more effectively across multiple touchpoints, businesses can increase loyalty and advocacy. Operational efficiency is improved through streamlined processes and better resource allocation, while increased customer retention reduces churn rates and associated costs. Ultimately, these efforts contribute to higher revenue through increased sales and improved customer lifetime value. In summary, the core principles and objectives of CIM are interwoven to create a cohesive strategy that prioritizes customer satisfaction while driving business growth. By adopting a customer-centric approach, integrating all touchpoints, responding in real-time, and making data-driven decisions, businesses can leverage CIM to achieve significant improvements in their customer interaction management capabilities. This not only enhances the customer experience but also positions the business for long-term success in a competitive market.
Applications and Uses of CIM
The integration of Computer-Integrated Manufacturing (CIM) has revolutionized various sectors by enhancing efficiency, precision, and productivity. This article delves into the multifaceted applications and uses of CIM, highlighting its transformative impact across different domains. We will explore how CIM optimizes **Industrial and Manufacturing Processes** by automating production lines, improving quality control, and reducing operational costs. Additionally, we will discuss the crucial role of **Information Technology Integration** in enabling seamless data exchange and real-time monitoring, thereby fostering a more connected and responsive manufacturing environment. Finally, we will examine **Real-World Case Studies and Examples** that illustrate the practical benefits and successful implementations of CIM in diverse industries. By understanding these aspects, readers will gain a comprehensive insight into the potential of CIM to drive innovation and excellence in modern manufacturing. Let us begin by examining how CIM is transforming **Industrial and Manufacturing Processes**.
Industrial and Manufacturing Processes
In the realm of industrial and manufacturing processes, Computer-Integrated Manufacturing (CIM) plays a pivotal role in enhancing efficiency, productivity, and quality. CIM integrates various aspects of manufacturing, including design, production, and quality control, into a cohesive system that leverages advanced technologies such as computer-aided design (CAD), computer-aided manufacturing (CAM), and enterprise resource planning (ERP). This integration allows for real-time monitoring and control of the entire production process, enabling manufacturers to respond swiftly to changes in demand or production issues. At the heart of CIM is the automation of manufacturing processes. Automated systems, such as robotic assembly lines and CNC machines, are programmed to perform tasks with precision and speed, significantly reducing human error and increasing throughput. Additionally, CIM facilitates the use of simulation tools to test and optimize production workflows before actual implementation, thereby minimizing downtime and improving overall process efficiency. The application of CIM also extends to supply chain management. By integrating ERP systems with CIM, manufacturers can streamline inventory management, scheduling, and logistics. This holistic approach ensures that raw materials are available when needed, reducing lead times and improving delivery schedules. Furthermore, CIM enables real-time data analytics, providing insights into production metrics such as yield rates, defect rates, and machine performance. These insights are crucial for continuous improvement initiatives aimed at optimizing manufacturing processes. Quality control is another critical area where CIM excels. Advanced sensors and machine vision systems integrated into CIM systems can inspect products in real-time, detecting defects or anomalies that might otherwise go unnoticed until later stages of production. This proactive approach to quality control not only enhances product reliability but also reduces waste and rework costs. Moreover, CIM supports flexible manufacturing systems (FMS) which allow for the rapid reconfiguration of production lines to accommodate different products or production volumes. This flexibility is particularly valuable in today's fast-paced market where consumer preferences can change rapidly. By leveraging CIM technologies, manufacturers can adapt quickly to these changes without significant disruptions to their operations. In summary, CIM transforms industrial and manufacturing processes by fostering a highly integrated, automated, and data-driven environment. Its applications span across design, production, quality control, supply chain management, and continuous improvement initiatives. As a result, CIM not only boosts operational efficiency but also enhances product quality and customer satisfaction, making it an indispensable tool for modern manufacturing enterprises.
Information Technology Integration
**Information Technology Integration in CIM: Enhancing Efficiency and Productivity** The integration of Information Technology (IT) is a cornerstone of Computer-Integrated Manufacturing (CIM), transforming traditional manufacturing processes into highly efficient and automated systems. This synergy between IT and manufacturing enables real-time data exchange, seamless communication, and optimized production workflows. At the heart of CIM, IT integration involves the convergence of various technologies such as computer-aided design (CAD), computer-aided manufacturing (CAM), computer-aided engineering (CAE), and enterprise resource planning (ERP) systems. By leveraging these technologies, manufacturers can design products more accurately, simulate production scenarios to predict outcomes, and manage resources more effectively. One of the key applications of IT in CIM is the implementation of Manufacturing Execution Systems (MES). MES integrates data from different stages of production, providing a holistic view of the manufacturing process. This allows for real-time monitoring, quality control, and immediate corrective actions, significantly reducing errors and downtime. Additionally, IT enables the use of advanced analytics and artificial intelligence (AI) to analyze production data, predict maintenance needs, and optimize production schedules. Another critical aspect of IT integration in CIM is the adoption of Industry 4.0 technologies such as the Internet of Things (IoT) and cloud computing. IoT devices embedded in machinery and equipment provide continuous feedback on performance metrics, enabling predictive maintenance and reducing the likelihood of equipment failures. Cloud computing facilitates the storage and processing of vast amounts of data generated during the manufacturing process, making it accessible across different departments and locations. The integration of IT also enhances collaboration and communication within the supply chain. Electronic Data Interchange (EDI) and other digital communication tools ensure that all stakeholders, from suppliers to customers, are informed about production status, inventory levels, and delivery schedules. This transparency and real-time communication help in managing expectations and ensuring that the entire supply chain operates in harmony. Moreover, IT integration in CIM supports the development of smart factories where automation and robotics play a pivotal role. By integrating robotic systems with AI and machine learning algorithms, manufacturers can achieve higher levels of precision and flexibility in their production processes. These smart factories are capable of adapting to changing market demands quickly, producing customized products efficiently, and maintaining high-quality standards consistently. In summary, the integration of Information Technology into CIM is a game-changer for modern manufacturing. It not only enhances operational efficiency but also drives innovation, improves product quality, and reduces costs. As technology continues to evolve, the role of IT in CIM will become even more critical, enabling manufacturers to stay competitive in a rapidly changing global market. By embracing these advancements, industries can move towards a future where production is more intelligent, agile, and responsive to customer needs.
Real-World Case Studies and Examples
In the realm of Computer-Integrated Manufacturing (CIM), real-world case studies and examples serve as powerful testimonials to its efficacy and versatility. One compelling example is the implementation of CIM at the Ford Motor Company. Ford integrated various manufacturing processes, including design, production planning, and quality control, into a unified system. This integration enabled real-time data sharing across different departments, significantly reducing production time and improving product quality. For instance, Ford's use of computer-aided design (CAD) and computer-aided manufacturing (CAM) allowed for rapid prototyping and precise machining, leading to a 30% reduction in development time for new vehicle models. Another notable case is the adoption of CIM by Boeing in its aircraft manufacturing. Boeing leveraged CIM to streamline its complex assembly processes, incorporating advanced robotics and automated inspection systems. This not only enhanced precision but also reduced labor costs and improved safety by minimizing human error. The integration of enterprise resource planning (ERP) systems with CIM further optimized supply chain management, ensuring timely delivery of components and reducing inventory costs. In the pharmaceutical industry, companies like Pfizer have utilized CIM to enhance compliance with stringent regulatory requirements. By integrating manufacturing execution systems (MES) with quality control modules, Pfizer ensured that every batch of medication met rigorous standards. This automated tracking and documentation process not only improved compliance but also reduced the risk of contamination and errors, thereby safeguarding public health. The automotive parts supplier, Bosch, is another exemplary case. Bosch implemented a CIM system that integrated its global supply chain, enabling seamless communication between suppliers, manufacturers, and distributors. This resulted in improved inventory management, reduced lead times, and enhanced customer satisfaction. Additionally, Bosch's use of predictive maintenance tools within its CIM framework allowed for proactive equipment maintenance, minimizing downtime and increasing overall plant efficiency. These real-world examples underscore the multifaceted benefits of CIM. By integrating various aspects of manufacturing into a cohesive system, companies can achieve significant improvements in productivity, quality, and cost efficiency. Moreover, CIM's ability to adapt to diverse industries highlights its universal applicability, making it an indispensable tool for modern manufacturing operations seeking to stay competitive in a rapidly evolving global market. Whether it's optimizing production workflows, enhancing product quality, or ensuring regulatory compliance, CIM stands as a testament to the transformative power of technology in manufacturing.
Benefits and Future of CIM
The integration of Computer-Integrated Manufacturing (CIM) into modern industrial processes has revolutionized the manufacturing landscape, offering a myriad of benefits that are poised to shape the future of production. At its core, CIM combines various technologies such as computer-aided design (CAD), computer-aided manufacturing (CAM), and enterprise resource planning (ERP) to create a seamless and highly efficient production environment. This article delves into the multifaceted advantages of CIM, focusing on three key areas: Efficiency and Productivity Gains, Technological Advancements and Trends, and Challenges and Future Directions. By examining these aspects, we can understand how CIM not only enhances current manufacturing practices but also sets the stage for innovative breakthroughs. Starting with Efficiency and Productivity Gains, we explore how CIM streamlines operations, reduces errors, and significantly boosts output, making it an indispensable tool for contemporary manufacturers. This foundational benefit underscores the transformative power of CIM and serves as a compelling reason for its widespread adoption.
Efficiency and Productivity Gains
Efficiency and productivity gains are pivotal benefits of Computer-Integrated Manufacturing (CIM), transforming the manufacturing landscape by seamlessly integrating various production processes. CIM's holistic approach ensures that all aspects of manufacturing, from design and production planning to execution and quality control, are optimized for maximum efficiency. By leveraging advanced technologies such as CAD/CAM, CNC machining, and robotics, CIM minimizes manual intervention, reducing errors and increasing precision. This integration also enables real-time monitoring and data analytics, allowing for swift identification of bottlenecks and immediate corrective actions. As a result, production cycles are significantly shortened, and overall throughput is enhanced. Additionally, CIM facilitates better resource allocation and inventory management, reducing waste and optimizing material usage. The automation inherent in CIM systems further boosts productivity by enabling 24/7 operation without the need for human intervention during non-working hours. This continuous operation capability not only increases output but also improves product consistency and quality. Moreover, CIM's data-driven insights support continuous improvement initiatives, enabling manufacturers to refine their processes iteratively based on performance metrics. This iterative improvement cycle ensures that efficiency and productivity gains are not one-time achievements but ongoing enhancements. In the future, as CIM continues to evolve with advancements in AI, IoT, and Industry 4.0 technologies, we can expect even more sophisticated automation and optimization strategies. For instance, predictive maintenance will become more prevalent, reducing downtime and increasing overall equipment effectiveness. The integration of AI will also enable more intelligent decision-making processes, further optimizing production workflows. Ultimately, the future of CIM promises unparalleled levels of efficiency and productivity, positioning manufacturers for sustained competitiveness in a rapidly evolving global market.
Technological Advancements and Trends
**Technological Advancements and Trends** In the realm of Computer-Integrated Manufacturing (CIM), technological advancements have been pivotal in transforming the manufacturing landscape. CIM, which stands for Computer-Integrated Manufacturing, integrates various manufacturing processes and systems through the use of computer technology to enhance efficiency, productivity, and quality. Recent trends and advancements in CIM are driven by the convergence of several key technologies. Firstly, the advent of Industry 4.0 has brought about a significant shift towards smart manufacturing. This includes the integration of Internet of Things (IoT) devices, artificial intelligence (AI), and machine learning (ML) algorithms to create intelligent and interconnected systems. These technologies enable real-time data collection, predictive maintenance, and adaptive control systems, thereby optimizing production processes and reducing downtime. Another critical trend is the adoption of cloud computing and edge computing. Cloud-based solutions allow for scalable data storage and processing, facilitating seamless collaboration across global supply chains. Edge computing, on the other hand, enables faster data processing at the point of generation, reducing latency and improving the responsiveness of manufacturing systems. The rise of additive manufacturing, commonly known as 3D printing, has also revolutionized CIM. This technology allows for the rapid prototyping and production of complex parts with unprecedented precision and flexibility. Coupled with advanced materials science, additive manufacturing is opening new avenues for innovation in product design and development. Furthermore, advancements in robotics and automation have led to the development of more sophisticated and versatile manufacturing robots. These robots, equipped with AI and ML capabilities, can perform a wide range of tasks from assembly to quality control with high accuracy and speed. Additionally, the integration of augmented reality (AR) and virtual reality (VR) into CIM is enhancing training programs, design processes, and even real-time production monitoring. These technologies provide immersive experiences that improve operator training, reduce errors, and enhance overall operational efficiency. Lastly, cybersecurity has become a paramount concern as CIM systems become increasingly interconnected. Advanced security protocols and intrusion detection systems are being implemented to protect sensitive data and prevent potential disruptions to manufacturing operations. These technological advancements not only enhance the current capabilities of CIM but also pave the way for future innovations. As these trends continue to evolve, they will drive further improvements in productivity, quality, and sustainability within the manufacturing sector. The future of CIM promises even more integrated, intelligent, and efficient manufacturing processes that will redefine the boundaries of industrial production.
Challenges and Future Directions
**Challenges and Future Directions** Despite the numerous benefits of Computer-Integrated Manufacturing (CIM), several challenges must be addressed to fully realize its potential. One of the primary hurdles is the high initial investment required for implementing CIM systems. The cost of purchasing and integrating advanced machinery, software, and training personnel can be prohibitive for many organizations, especially small and medium-sized enterprises. Additionally, the complexity of CIM systems often necessitates significant changes in organizational culture and processes, which can be difficult to manage and may lead to resistance from employees. Another challenge is ensuring data security and integrity within CIM environments. With the increasing reliance on interconnected systems and data exchange, there is a heightened risk of cyber-attacks and data breaches. This necessitates robust cybersecurity measures to protect sensitive information and maintain operational continuity. Moreover, the rapid evolution of technology means that CIM systems must be continuously updated to remain relevant. This requires ongoing investment in research and development as well as regular training for employees to keep their skills aligned with technological advancements. Looking ahead, future directions for CIM are promising and multifaceted. The integration of emerging technologies such as Artificial Intelligence (AI), Internet of Things (IoT), and blockchain will further enhance the efficiency, flexibility, and transparency of manufacturing processes. AI can optimize production workflows, predict maintenance needs, and improve product quality through real-time monitoring and analysis. IoT enables real-time data collection from various sources across the supply chain, facilitating better decision-making and more agile responses to market demands. Blockchain technology offers a secure and transparent way to track materials, components, and finished products throughout their lifecycle, enhancing traceability and reducing counterfeiting risks. Furthermore, advancements in robotics and automation will continue to drive productivity gains by automating repetitive tasks and freeing human workers for more complex and creative roles. In terms of sustainability, future CIM systems will increasingly focus on reducing environmental impact through energy-efficient operations, waste minimization, and the use of renewable resources. This aligns with broader industry trends towards circular economy practices and corporate social responsibility. Finally, the adoption of Industry 4.0 principles will continue to shape the future of CIM by fostering greater collaboration between humans, machines, and data systems. This holistic approach will lead to more resilient supply chains, improved product customization capabilities, and enhanced customer satisfaction. In summary, while there are significant challenges associated with implementing and maintaining CIM systems, the future holds immense promise for innovation and growth. By addressing these challenges head-on and embracing emerging technologies, manufacturers can unlock new levels of efficiency, sustainability, and competitiveness in an increasingly complex global market.