What Does Smt Mean

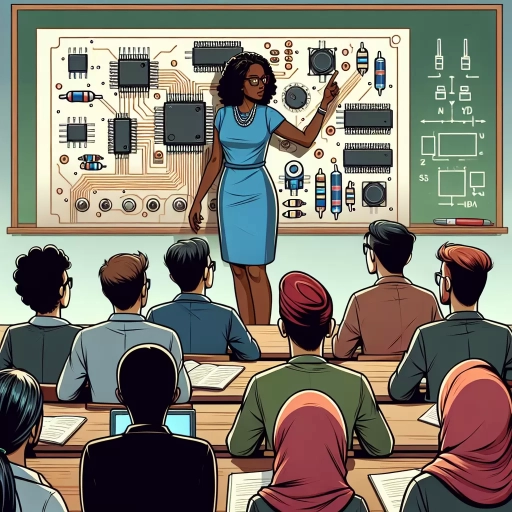
In the realm of modern electronics, the acronym SMT stands for Surface Mount Technology, a revolutionary manufacturing process that has transformed the way electronic components are assembled onto printed circuit boards (PCBs). This technology has become a cornerstone in various industries, from consumer electronics to aerospace, due to its efficiency, reliability, and miniaturization capabilities. To fully appreciate the impact of SMT, it is essential to delve into its fundamental principles, explore its diverse applications across different sectors, and examine the technological advancements that are shaping its future. Understanding the basics of SMT is crucial as it lays the groundwork for comprehending how this technology has become indispensable in today's electronic landscape. By grasping the core concepts of SMT, we can better appreciate its widespread applications and the innovative trends that are driving its evolution. In this article, we will first explore the basics of SMT, followed by its applications and industries, and finally, the technological advancements and future trends that are redefining this critical field. Let us begin by understanding the basics of SMT.
Understanding the Basics of SMT
In the realm of modern electronics, Surface Mount Technology (SMT) has revolutionized the way components are integrated into circuit boards, significantly enhancing efficiency, reliability, and miniaturization. To fully appreciate the impact of SMT, it is essential to delve into its fundamental aspects. This article will provide a comprehensive overview by first defining what SMT is and expanding on its acronym, ensuring clarity on the terminology involved. Next, it will explore the historical context and development of SMT, tracing its evolution from traditional through-hole technology to the sophisticated methods used today. Finally, it will delve into the key components and terminology associated with SMT, highlighting the critical elements that make this technology so pivotal. By understanding these core aspects—definition, historical context, and key components—readers will gain a solid foundation in the basics of SMT, enabling them to appreciate its significance and applications in contemporary electronics manufacturing. This foundational knowledge is crucial for anyone looking to grasp the intricacies of Surface Mount Technology and its role in shaping the future of electronic devices. Understanding the Basics of SMT is therefore a vital step for both professionals and enthusiasts alike.
Definition and Acronym Expansion
**Understanding the Basics of SMT: Definition and Acronym Expansion** Surface Mount Technology (SMT) is a method of mounting electronic components onto a printed circuit board (PCB) where the components are placed directly onto the surface of the PCB. This contrasts with through-hole technology, where components are inserted into holes drilled in the PCB. The acronym "SMT" encapsulates the essence of this modern manufacturing process, which has revolutionized the electronics industry by enabling the production of smaller, more complex, and highly reliable electronic devices. At its core, SMT involves several key steps: component selection, PCB design, component placement, soldering, and inspection. The components used in SMT are specifically designed to be mounted on the surface of the PCB, featuring leads or terminations that are soldered to pads on the board. This approach allows for higher component density, reduced board size, and improved performance characteristics such as lower inductance and capacitance. The use of automated placement machines and reflow soldering techniques further enhances the efficiency and precision of the SMT process. The widespread adoption of SMT has been driven by its numerous advantages. It facilitates the creation of compact devices with increased functionality, making it ideal for applications in consumer electronics, automotive systems, medical devices, and aerospace. Additionally, SMT reduces material costs and minimizes the risk of component failure due to mechanical stress. The process also supports the use of Ball Grid Array (BGA) packages and other advanced packaging technologies that are crucial for high-speed digital circuits. In summary, Surface Mount Technology is a cornerstone of modern electronics manufacturing. Its definition underscores a sophisticated yet efficient method for assembling electronic circuits that are integral to today's technological landscape. By understanding the basics of SMT, engineers and manufacturers can leverage its capabilities to innovate and produce cutting-edge electronic products that meet the demands of an increasingly interconnected world. As technology continues to evolve, the role of SMT will remain pivotal in enabling the development of smaller, smarter, and more reliable electronic devices.
Historical Context and Development
The historical context and development of Surface Mount Technology (SMT) are pivotal in understanding its evolution and significance in modern electronics manufacturing. The journey of SMT began in the 1960s, when the need for miniaturization and increased component density became paramount. Initially, through-hole technology dominated the industry, but it had limitations in terms of size and complexity. The advent of SMT marked a revolutionary shift, allowing for smaller, lighter, and more reliable electronic devices. In the early stages, SMT faced numerous challenges, including the development of suitable components and manufacturing processes. The first surface mount devices (SMDs) were introduced in the late 1960s, but they were not widely adopted until the 1980s. This period saw significant advancements in materials science, leading to the creation of leadless ceramic chip carriers and other SMDs. The introduction of reflow soldering techniques further facilitated mass production, enabling the widespread adoption of SMT. The 1990s witnessed a surge in SMT's popularity due to advancements in automation and computer-aided design (CAD). Automated pick-and-place machines and inspection systems improved efficiency and accuracy, while CAD software enhanced design capabilities. This decade also saw the rise of ball grid array (BGA) packages, which offered even higher component densities and better thermal performance. Today, SMT is the cornerstone of modern electronics manufacturing, driving innovations in fields such as consumer electronics, automotive systems, and aerospace. The continuous development of new materials and technologies has enabled further miniaturization and increased functionality. For instance, the introduction of flip-chip technology and wafer-level packaging has pushed the boundaries of component integration. Understanding the historical context and development of SMT is essential for appreciating its current role in the electronics industry. From its humble beginnings to its current status as a global standard, SMT has transformed how electronic devices are designed, manufactured, and integrated into various applications. This evolution underscores the importance of ongoing research and innovation in maintaining technological advancements and meeting future demands for more sophisticated and compact electronic systems. By grasping this historical narrative, one can better comprehend the basics of SMT and its profound impact on modern technology.
Key Components and Terminology
**Understanding the Basics of SMT: Key Components and Terminology** Surface Mount Technology (SMT) is a cornerstone of modern electronics manufacturing, and grasping its key components and terminology is essential for anyone looking to delve into this field. At the heart of SMT lies the **Printed Circuit Board (PCB)**, which serves as the foundation for mounting various electronic components. The PCB is typically made from layers of conductive material, such as copper, sandwiched between insulating layers like fiberglass or ceramic. **Surface Mount Devices (SMDs)** are the primary components used in SMT. These include resistors, capacitors, inductors, and integrated circuits (ICs), all designed to be mounted directly onto the surface of the PCB. Unlike through-hole components, SMDs do not require holes drilled into the board, making them more compact and efficient. **Solder Paste**, a mixture of metal particles and flux, is applied to the PCB pads where SMDs will be placed. This paste melts during the soldering process, forming strong electrical connections between components and the board. **Pick-and-Place Machines** are critical in the SMT assembly process. These automated systems accurately place SMDs onto their designated positions on the PCB at high speeds, ensuring precision and consistency. Following placement, the board undergoes **Reflow Soldering**, where it is heated to a temperature that melts the solder paste, securing the components in place. Other key terms include **Stencil**, a metal template used to apply solder paste accurately onto the PCB pads; **Inspection Systems**, which use optical or X-ray technology to verify component placement and solder quality; and **Conformal Coating**, a protective layer applied over the assembled board to shield it from environmental factors like moisture and dust. Understanding these components and processes is vital for anyone involved in electronics manufacturing. Whether you're an engineer designing new products or a technician on the production floor, familiarity with SMT terminology ensures that you can communicate effectively and contribute to the efficient production of high-quality electronic devices. By mastering these basics, you'll be better equipped to navigate the complexities of modern electronics assembly and contribute to the ongoing innovation in this field.
Applications and Industries Using SMT
Surface Mount Technology (SMT) has revolutionized the way components are mounted onto printed circuit boards (PCBs), significantly enhancing the efficiency, reliability, and miniaturization of electronic devices. This innovative technique is pivotal across various industries, each leveraging SMT to meet specific demands and challenges. In the realm of electronics manufacturing and assembly, SMT enables the rapid production of complex PCBs with high precision and reduced labor costs. The automotive and aerospace industries rely on SMT for the development of sophisticated control systems and safety-critical components that require utmost reliability and durability. Additionally, medical devices and consumer electronics benefit from SMT's ability to integrate compact, high-performance components, ensuring both functionality and user safety. As we delve into these applications, it becomes clear that understanding the basics of SMT is essential for appreciating its transformative impact on modern technology. By exploring these diverse industries, we will gain a deeper insight into how SMT has become an indispensable tool in contemporary manufacturing. Understanding the basics of SMT will provide a foundational knowledge that underscores its critical role in these sectors.
Electronics Manufacturing and Assembly
Electronics manufacturing and assembly are pivotal processes in the production of modern electronic devices, with Surface Mount Technology (SMT) playing a crucial role. SMT has revolutionized the electronics industry by enabling the rapid and precise assembly of components onto printed circuit boards (PCBs). This technology involves mounting tiny components such as resistors, capacitors, and integrated circuits directly onto the surface of a PCB, significantly reducing the size and weight of electronic devices while enhancing their performance and reliability. In the realm of electronics manufacturing, SMT offers several key advantages. It allows for higher component density, which is essential for producing compact devices like smartphones, laptops, and wearable technology. The automated nature of SMT processes ensures consistency and accuracy, minimizing human error and improving overall product quality. Additionally, SMT facilitates faster production times compared to traditional through-hole technology, making it ideal for high-volume manufacturing. The applications of SMT are diverse and widespread across various industries. In consumer electronics, SMT is used in the production of televisions, audio equipment, and gaming consoles. The automotive industry relies heavily on SMT for manufacturing advanced driver-assistance systems (ADAS), infotainment systems, and safety features like airbag controllers. Medical devices such as defibrillators, pacemakers, and diagnostic equipment also benefit from SMT due to its ability to create highly reliable and miniaturized circuits. Aerospace and defense industries utilize SMT for building complex electronic systems that require high precision and durability. These systems include navigation, communication, and control modules that are critical for military and space applications. Furthermore, the industrial sector employs SMT in control systems for machinery, robotics, and automation equipment, ensuring efficient and reliable operation. The integration of SMT into these industries has not only improved product performance but also driven innovation. For instance, the Internet of Things (IoT) devices, which are becoming increasingly prevalent in smart homes and cities, rely on SMT for their compact design and low power consumption. As technology continues to advance, the role of SMT in electronics manufacturing will remain vital, enabling the creation of smaller, smarter, and more efficient electronic devices that underpin modern life. By leveraging the capabilities of SMT, manufacturers can meet the growing demand for sophisticated electronics while maintaining high standards of quality and reliability.
Automotive and Aerospace Industries
The automotive and aerospace industries are pivotal sectors that heavily rely on Surface Mount Technology (SMT) for the production of sophisticated electronic components. In the automotive sector, SMT plays a crucial role in manufacturing advanced driver-assistance systems (ADAS), infotainment systems, and engine control units. These components require high reliability and precision, which SMT delivers through its ability to mount tiny components with high accuracy and speed. For instance, modern vehicles equipped with features like lane departure warning systems, adaptive cruise control, and automatic emergency braking rely on complex electronic circuits that are efficiently produced using SMT. This technology ensures that these critical systems operate flawlessly under various environmental conditions, enhancing vehicle safety and performance. In the aerospace industry, the stakes are even higher due to the stringent requirements for reliability and durability. Aerospace electronics must withstand extreme temperatures, vibrations, and other harsh conditions. SMT is instrumental in meeting these demands by enabling the production of compact, lightweight, and highly reliable electronic assemblies. Components such as navigation systems, communication equipment, and flight control systems are all manufactured using SMT techniques. The precision and consistency offered by SMT are essential for ensuring that these critical systems function correctly in the challenging environment of space or high-altitude flight. Additionally, the miniaturization capabilities of SMT allow for the integration of multiple functionalities into smaller form factors, which is particularly advantageous in aerospace applications where space and weight are critical factors. Both industries also benefit from the cost-effectiveness and efficiency of SMT. The technology allows for high-volume production with minimal human intervention, reducing labor costs and increasing throughput. This is particularly important in the automotive industry where economies of scale are crucial for maintaining competitiveness. In aerospace, while the volumes may be lower, the complexity and customization of electronic assemblies make SMT an indispensable tool for achieving the required levels of quality and reliability. Moreover, as both industries continue to evolve with advancements in technology such as autonomous vehicles and reusable spacecraft, the role of SMT will only become more pronounced. The integration of artificial intelligence, IoT sensors, and other advanced technologies will necessitate even more sophisticated electronic components that can be reliably produced using SMT. Therefore, it is clear that Surface Mount Technology remains a cornerstone in the development and manufacturing processes of both the automotive and aerospace industries, enabling them to innovate while maintaining the highest standards of performance and reliability.
Medical Devices and Consumer Electronics
The integration of Surface Mount Technology (SMT) in medical devices and consumer electronics has revolutionized these industries by enhancing performance, reliability, and miniaturization. In the medical sector, SMT enables the development of sophisticated diagnostic and therapeutic devices that are both compact and highly functional. For instance, portable defibrillators, insulin pumps, and implantable devices such as pacemakers and neurostimulators rely on SMT to pack complex electronic circuits into small, lightweight packages. This miniaturization allows for greater patient mobility and comfort while maintaining or even improving the accuracy and reliability of medical treatments. Additionally, SMT facilitates the production of disposable medical devices like biosensors and diagnostic strips, which are crucial for point-of-care testing and real-time health monitoring. In consumer electronics, SMT is a cornerstone technology that drives innovation and efficiency. Smartphones, tablets, smartwatches, and other wearable devices owe their sleek designs and advanced functionalities to SMT. By allowing for the precise placement of tiny components such as capacitors, resistors, and integrated circuits onto printed circuit boards (PCBs), SMT ensures high-density packaging without compromising on performance. This has led to the development of thinner, lighter devices with extended battery life and enhanced computational capabilities. Furthermore, SMT supports the integration of advanced features like high-resolution displays, advanced sensors for gesture recognition or biometric authentication, and robust connectivity options including Wi-Fi and Bluetooth. The reliability and consistency offered by SMT also reduce production costs and improve product lifespan, making consumer electronics more accessible and affordable for a broader audience. The synergy between SMT and these industries extends beyond just device manufacturing; it also influences design flexibility and future-proofing. With SMT, manufacturers can easily update or modify designs without significant retooling costs, allowing them to keep pace with rapid technological advancements. This adaptability is particularly important in both medical devices and consumer electronics where innovation cycles are short and market demands are high. Overall, the application of SMT in these sectors not only enhances product functionality but also contributes to improved user experiences, making it an indispensable technology in modern electronics manufacturing.
Technological Advancements and Future Trends in SMT
The realm of Surface Mount Technology (SMT) has witnessed unprecedented growth and innovation, transforming the landscape of electronic manufacturing. At the forefront of these advancements are three key trends that are reshaping the industry: component miniaturization, integration with artificial intelligence and robotics, and a heightened focus on sustainability and environmental considerations. Component miniaturization has enabled the creation of smaller, more efficient devices, driving the development of compact and powerful electronics. The integration of AI and robotics is revolutionizing production processes, enhancing precision, speed, and overall efficiency. Meanwhile, sustainability and environmental considerations are becoming increasingly important, as manufacturers seek to reduce their ecological footprint while maintaining high-quality standards. Understanding these future trends is crucial for anyone looking to grasp the evolving dynamics of SMT. To fully appreciate these advancements, it is essential to first understand the basics of SMT, which will provide a solid foundation for exploring these cutting-edge developments. By delving into these topics, we can better navigate the exciting and rapidly changing world of SMT.
Advancements in Component Miniaturization
**SMT** stands for Surface Mount Technology, a method of mounting electronic components onto a printed circuit board (PCB) using surface mount devices (SMDs). This technology has revolutionized the electronics industry by enabling the production of smaller, more efficient, and cost-effective electronic devices. **Advancements in Component Miniaturization** The relentless drive for innovation in Surface Mount Technology (SMT) has led to significant advancements in component miniaturization. This trend is pivotal in the evolution of modern electronics, enabling the creation of compact, high-performance devices that are integral to our daily lives. Component miniaturization involves reducing the size of electronic components while maintaining or enhancing their functionality. Recent breakthroughs in materials science and manufacturing processes have facilitated the development of smaller, yet more powerful components. For instance, the introduction of 0201 (0.02 inches by 0.01 inches) and even smaller 01005 (0.01 inches by 0.005 inches) SMDs has allowed for denser PCB designs, enabling the production of smaller form factor devices such as smartphones, wearables, and IoT devices. These miniaturized components also contribute to reduced power consumption and increased reliability due to shorter signal paths and lower thermal resistance. Furthermore, advancements in 3D packaging technologies like System-in-Package (SiP) and Wafer-Level Packaging (WLP) have enabled the integration of multiple components into a single package, further reducing overall device size while enhancing performance. The integration of these technologies with emerging trends like artificial intelligence, 5G connectivity, and the Internet of Things (IoT) is set to propel future innovations in SMT, driving the development of even more sophisticated and compact electronic systems. As component miniaturization continues to advance, it will play a crucial role in shaping the future of electronics, enabling the creation of devices that are not only smaller but also more powerful and efficient.
Integration with AI and Robotics
**SMT** stands for Surface Mount Technology, a method used in the manufacturing of printed circuit boards (PCBs) where components are mounted directly onto the surface of the PCB. In the context of technological advancements and future trends in SMT, integration with AI and robotics is a pivotal area that promises significant enhancements in efficiency, accuracy, and productivity. The integration of Artificial Intelligence (AI) and robotics into SMT processes is revolutionizing the industry by introducing intelligent automation. AI algorithms can analyze vast amounts of data from various stages of the manufacturing process, enabling real-time monitoring and predictive maintenance. For instance, AI-powered systems can detect anomalies in component placement, soldering quality, and other critical aspects, allowing for immediate corrective actions to be taken. This proactive approach minimizes downtime and reduces the likelihood of defects, thereby improving overall product quality. Robotic systems, equipped with advanced sensors and machine learning capabilities, are being increasingly deployed to handle tasks such as component picking and placement, soldering, and inspection. These robots can operate with precision and speed that surpasses human capabilities, ensuring consistent quality across large production runs. Moreover, robotic arms can be programmed to perform complex tasks that require high dexterity, such as handling tiny components or navigating intricate PCB layouts. The synergy between AI and robotics also enables adaptive manufacturing processes. For example, AI can optimize production workflows based on real-time data from robotic operations, adjusting parameters like speed, temperature, and pressure to achieve optimal results. This dynamic optimization not only accelerates production but also ensures that the manufacturing process remains flexible and responsive to changing demands. Furthermore, the integration of AI and robotics enhances worker safety by automating hazardous tasks and reducing human exposure to potentially harmful environments. Workers can focus on higher-value tasks such as design, engineering, and quality control, while AI-driven robots handle repetitive and physically demanding jobs. In conclusion, the integration of AI and robotics in SMT represents a significant leap forward in technological advancements. By leveraging these technologies, manufacturers can achieve unprecedented levels of efficiency, accuracy, and adaptability. As the demand for sophisticated electronic devices continues to grow, the future of SMT will increasingly rely on intelligent automation to meet the challenges of complexity, speed, and quality. This trend is set to redefine the landscape of electronic manufacturing, driving innovation and excellence in the years to come.
Sustainability and Environmental Considerations
**Sustainability and Environmental Considerations** As technological advancements continue to drive the evolution of Surface Mount Technology (SMT), sustainability and environmental considerations have become increasingly paramount. SMT, which involves mounting electronic components directly onto the surface of printed circuit boards (PCBs), is a cornerstone of modern electronics manufacturing. However, this process also generates significant environmental impacts, from energy consumption and resource depletion to waste generation and chemical usage. To mitigate these effects, the industry is adopting several sustainable practices. One key strategy is the implementation of green manufacturing processes that minimize waste and reduce the use of hazardous materials. This includes transitioning to lead-free soldering, which not only complies with regulatory standards like the Restriction of Hazardous Substances (RoHS) directive but also reduces the environmental footprint of SMT operations. Additionally, manufacturers are investing in energy-efficient equipment and renewable energy sources to lower their carbon footprint. Another critical aspect is the design for recyclability and reusability of PCBs. By incorporating recyclable materials and designing boards with end-of-life recovery in mind, companies can significantly reduce electronic waste (e-waste). The use of biodegradable or recyclable packaging materials further supports this goal. Moreover, advancements in SMT technology are enabling the development of smaller, more efficient components that require fewer resources and generate less waste during production. Supply chain transparency and responsible sourcing are also gaining importance. Companies are now more likely to engage with suppliers who adhere to strict environmental and social standards, ensuring that raw materials are sourced sustainably and ethically. This holistic approach not only enhances the environmental sustainability of SMT but also contributes to a more ethical and responsible electronics industry. Innovative technologies such as 3D printing and additive manufacturing are also being explored for their potential to enhance sustainability in SMT. These methods allow for the creation of complex components with minimal material waste and can be integrated into existing SMT lines to improve overall efficiency. Furthermore, research into new materials and processes, such as graphene-based components and bio-based soldering, promises even greater reductions in environmental impact. As the electronics industry continues to grow, integrating sustainability into every stage of the SMT process is crucial. By leveraging technological advancements to reduce waste, improve efficiency, and promote ethical practices, manufacturers can ensure a more sustainable future for SMT while meeting the increasing demand for electronic devices. This convergence of technology and sustainability will be a defining trend in the future of SMT, driving innovation that benefits both the environment and the industry as a whole.