What Is Glue Made Of

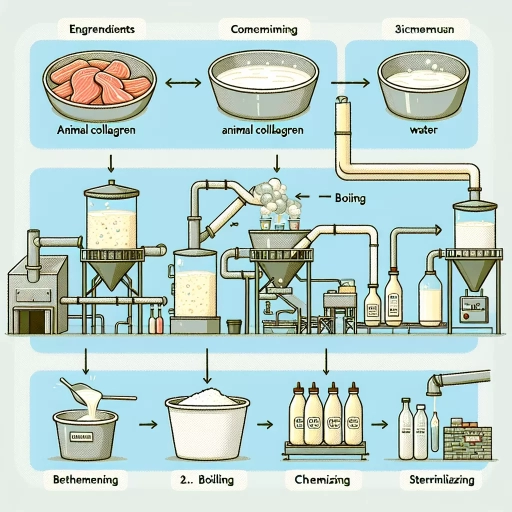
Glue, a ubiquitous adhesive found in various forms and applications, is a staple in both everyday life and industrial processes. From crafting and DIY projects to construction and manufacturing, glue plays a crucial role in bonding materials together. But what exactly is glue made of? To understand the intricacies of this versatile substance, it is essential to delve into its chemical composition, explore the diverse types of glue and their unique ingredients, and examine the manufacturing process along with the safety considerations involved. This article will provide a comprehensive overview of glue, starting with its fundamental chemical makeup. By understanding the chemical composition of glue, we can appreciate how different elements combine to create a strong and durable bond. This foundational knowledge will then be expanded upon by discussing the various types of glue and their specific ingredients, followed by an examination of the manufacturing process and the critical safety considerations that must be observed. Let us begin by uncovering the chemical composition of glue, the backbone of its adhesive properties.
Chemical Composition of Glue
Glue, a ubiquitous substance in both everyday life and industrial applications, owes its versatility and effectiveness to its complex chemical composition. At its core, glue is a mixture of various components that work together to provide strong bonding properties. This intricate blend includes **polymers and resins**, which form the backbone of the adhesive, providing structural integrity and durability. Additionally, **adhesives and binders** play a crucial role in ensuring that the glue adheres well to different surfaces, enhancing its sticking power. Furthermore, **solvents and additives** are incorporated to improve the glue's flow, drying time, and overall performance. Understanding these components is essential for appreciating the science behind how glue works. In this article, we will delve into the chemical composition of glue, exploring each of these key elements in detail to uncover the secrets behind this indispensable adhesive. By examining polymers and resins, adhesives and binders, and solvents and additives, we will gain a comprehensive understanding of the chemical composition of glue.
Polymers and Resins
Polymers and resins are fundamental components in the chemical composition of glue, playing a crucial role in its adhesive properties and durability. **Polymers**, which are large molecules composed of repeating units called monomers, form the backbone of many adhesives. These macromolecules can be natural, such as cellulose and proteins, or synthetic, like polyvinyl acetate (PVA) and polyethylene. The specific type of polymer used determines the glue's strength, flexibility, and resistance to environmental factors like temperature and moisture. For instance, acrylic polymers are known for their excellent bonding strength and resistance to chemicals, making them ideal for industrial applications. **Resins**, on the other hand, are typically viscous liquids or solids that harden when exposed to heat or a chemical catalyst. They can be derived from plants or synthesized chemically. In adhesive formulations, resins often serve as binders that hold the polymer chains together, enhancing the glue's cohesive strength. Epoxy resins, for example, are highly prized for their exceptional mechanical properties and chemical resistance, making them a staple in high-performance adhesives used in aerospace and automotive industries. The combination of polymers and resins in glue formulations allows for a wide range of applications. For instance, cyanoacrylate adhesives (commonly known as super glue) rely on a polymer resin that rapidly polymerizes upon contact with moisture in the air, forming an incredibly strong bond. Similarly, hot melt adhesives use thermoplastic resins that melt when heated and solidify upon cooling, providing a quick and efficient bonding process suitable for packaging and crafting. The versatility of polymers and resins also enables the development of specialized glues tailored to specific needs. For example, silicone-based adhesives combine polymers with silicone resins to create flexible bonds that are resistant to extreme temperatures and chemicals, making them ideal for sealing applications in construction and electronics. Additionally, biodegradable adhesives are being developed using natural polymers like starch and cellulose, which are combined with plant-based resins to produce environmentally friendly alternatives. In summary, the interplay between polymers and resins is essential for creating glues with diverse properties and applications. By understanding the chemical composition of these components, manufacturers can design adhesives that meet precise requirements across various industries, from consumer goods to advanced engineering. This synergy underscores the importance of polymer and resin chemistry in the development of effective and reliable adhesives.
Adhesives and Binders
Adhesives and binders are the cornerstone components of glue, playing a crucial role in its chemical composition and functionality. These substances are designed to form strong bonds between different materials, such as metals, plastics, wood, and textiles. Adhesives are typically polymers or resins that undergo a chemical reaction to create a durable bond. They can be categorized into various types based on their chemical nature, including acrylics, epoxies, polyurethanes, and silicones. Each type has unique properties that make them suitable for specific applications; for instance, epoxy adhesives are known for their high strength and resistance to chemicals, while silicone adhesives offer flexibility and thermal stability. Binders, on the other hand, are substances that hold particles together and adhere them to a surface. In the context of glue, binders often work in conjunction with adhesives to enhance the overall bonding performance. Common binders include natural polymers like starch and cellulose, as well as synthetic polymers such as polyvinyl acetate (PVA) and polyvinyl alcohol (PVOH). The choice of binder depends on the desired properties of the glue, such as its drying time, strength, and environmental resistance. The chemical composition of adhesives and binders can vary widely depending on their intended use. For example, white glue (PVA glue) is primarily composed of polyvinyl acetate dissolved in water along with additives like plasticizers to improve flexibility and preservatives to extend shelf life. Hot melt adhesives, which are used in applications like packaging and crafting, are typically made from thermoplastic polymers such as ethylene-vinyl acetate (EVA) or polyethylene. In addition to their primary components, adhesives and binders may also contain fillers, solvents, and other additives that enhance their performance characteristics. Fillers like silica or calcium carbonate can improve the mechanical strength of the adhesive, while solvents help in achieving the right viscosity for application. Additives such as UV stabilizers or antioxidants can protect the adhesive from degradation over time. Understanding the chemical composition of adhesives and binders is essential for selecting the right type of glue for a particular application. It allows users to predict how well the glue will perform under various conditions and ensures that it meets the required standards of strength, durability, and safety. Whether it's for industrial manufacturing or everyday household use, the science behind adhesives and binders is what makes glue an indispensable tool in modern life. By appreciating these components' roles within glue's chemical makeup, we can better harness their potential to create strong, reliable bonds across a wide range of materials.
Solvents and Additives
Solvents and additives play a crucial role in the chemical composition of glue, enhancing its performance, shelf life, and usability. Solvents are substances that dissolve the adhesive polymers, facilitating their application and ensuring a uniform spread. Common solvents include water, organic compounds like acetone or toluene, and glycols. Water-based adhesives are popular due to their ease of use, low toxicity, and environmental friendliness. Organic solvents, on the other hand, are often used in industrial settings where faster drying times are necessary. However, they can be hazardous and require proper ventilation. Additives are incorporated into glue formulations to improve specific properties. Plasticizers, for instance, increase flexibility and reduce brittleness in the dried adhesive film. Fillers such as silica or calcium carbonate enhance the adhesive's strength and durability while also reducing costs. Thickeners like polymers or resins adjust the viscosity of the glue to make it easier to apply in various conditions. Antioxidants and UV stabilizers protect the adhesive from degradation caused by exposure to light or oxygen, extending its shelf life and maintaining its bonding strength over time. Preservatives are another critical additive, preventing microbial growth in water-based adhesives. This is particularly important for products that may be stored for extended periods or used in environments prone to moisture. Additionally, some adhesives contain wetting agents that improve the spreadability of the glue on surfaces, ensuring better contact and stronger bonds. The choice of solvents and additives depends on the intended application of the glue. For example, adhesives used in construction might include additives that enhance thermal stability and resistance to moisture, while those used in medical applications must be biocompatible and free from harmful substances. Understanding the role of solvents and additives is essential for selecting the right type of glue for a specific task, ensuring optimal performance and safety. In summary, solvents dissolve adhesive polymers for easy application, while additives enhance various properties such as flexibility, strength, shelf life, and usability. The careful selection of these components is vital for creating effective and reliable adhesives tailored to diverse applications. By understanding how solvents and additives contribute to the chemical composition of glue, users can make informed decisions about which products best meet their needs.
Types of Glue and Their Ingredients
In the world of adhesives, the variety of glues available can be overwhelming, each with its unique properties and applications. From crafting and DIY projects to industrial manufacturing, the right type of glue is crucial for achieving strong and durable bonds. This article delves into three prominent types of glue: White Glue (PVA Glue), Epoxy Glue, and Hot Melt Glue. White Glue, known for its versatility and ease of use, is a staple in many households and classrooms. Epoxy Glue, on the other hand, offers exceptional strength and resistance, making it a favorite among professionals. Hot Melt Glue, with its quick-drying properties, is ideal for applications requiring rapid bonding. Understanding these different types of glue not only enhances your ability to choose the right adhesive for your needs but also provides insight into their chemical composition. By exploring the ingredients and chemical makeup of these glues, you can better appreciate their performance characteristics and ensure optimal use in various projects. Transitioning into the chemical composition of glue, we will examine how these ingredients contribute to the distinct properties of each adhesive type.
White Glue (PVA Glue)
White glue, commonly known as PVA (Polyvinyl Acetate) glue, is a versatile and widely used adhesive that has become a staple in various industries and households. Composed primarily of polyvinyl acetate, a synthetic polymer, this glue is renowned for its ease of use, flexibility, and non-toxic nature. The ingredients in white glue typically include water, polyvinyl acetate resin, and additives such as preservatives to prevent bacterial growth and thickeners to enhance viscosity. The polyvinyl acetate resin is the core component that provides the adhesive properties, while the water acts as a solvent to facilitate application. One of the key advantages of white glue is its ability to bond a wide range of materials, including paper, fabric, wood, and even some plastics. This makes it an essential tool in crafting, school projects, and DIY home repairs. Additionally, PVA glue is known for its quick-drying properties; it usually sets within a few minutes, allowing for rapid project completion. The glue also retains some degree of flexibility after drying, which helps in absorbing minor vibrations or movements without cracking. In terms of safety, white glue is generally considered non-toxic and hypoallergenic, making it suitable for use by children and individuals with sensitive skin. However, it is still important to follow proper handling and application guidelines to avoid any potential health risks. For instance, while the glue itself is non-toxic, ingesting large amounts can cause gastrointestinal issues due to its adhesive properties. The versatility of white glue extends beyond its common applications; it is also used in various industrial processes. For example, in the construction industry, PVA glue is often used as a bonding agent in drywall and plastering due to its strong adhesive properties and ability to form a flexible bond that can withstand minor structural movements. In the textile industry, it serves as a fabric adhesive for bonding fabrics together or attaching them to other materials. In conclusion, white glue or PVA glue stands out as a multifaceted adhesive that combines ease of use with robust bonding capabilities. Its composition of polyvinyl acetate resin dissolved in water along with minor additives makes it an indispensable tool across multiple sectors. Whether you are a crafter looking for a reliable adhesive for your projects or an industrial worker needing a strong yet flexible bond, white glue is an excellent choice that offers both performance and safety.
Epoxy Glue
Epoxy glue stands out as a versatile and robust adhesive within the diverse array of glues available. Known for its exceptional strength, durability, and resistance to various environmental factors, epoxy glue is widely used in industrial, commercial, and even household applications. Unlike other types of glue that may rely on moisture or heat to set, epoxy glue is a two-part system consisting of a resin and a hardener. When these components are mixed together in the correct ratio, they undergo a chemical reaction known as polymerization, resulting in a strong, rigid bond. The ingredients in epoxy glue are crucial to its performance. The resin typically contains epoxide groups, which are highly reactive molecules that form cross-links with the hardener. The hardener, often an amine or polyamine compound, catalyzes this reaction. This cross-linking process creates a three-dimensional network that provides epoxy glue with its remarkable mechanical properties, including high tensile strength, impact resistance, and chemical resistance. Additionally, epoxy glues can be formulated with various additives such as fillers, pigments, and plasticizers to enhance their performance for specific tasks. One of the key advantages of epoxy glue is its ability to bond a wide range of materials, including metals, plastics, glass, and wood. This versatility makes it an essential tool in industries such as aerospace, automotive, and construction. For instance, in the aerospace industry, epoxy glues are used to bond composite materials like carbon fiber and fiberglass due to their high strength-to-weight ratio and resistance to extreme temperatures. In addition to its industrial applications, epoxy glue is also popular among hobbyists and DIY enthusiasts. It can be used for repairing broken items, creating art pieces, and even in woodworking projects. The clear versions of epoxy glue are particularly favored for their ability to produce a transparent bond that does not obscure the appearance of the materials being joined. Despite its many benefits, epoxy glue does have some limitations. It requires careful mixing to ensure the correct ratio of resin to hardener, and it can take several hours or even days to fully cure depending on the specific formulation and environmental conditions. However, these drawbacks are often outweighed by its superior bonding capabilities and long-lasting durability. In summary, epoxy glue is a powerful adhesive that offers unparalleled strength and versatility. Its unique two-part system and ability to form strong cross-links make it an indispensable tool across various industries and applications. Whether you are a professional engineer or a hobbyist looking for a reliable bonding solution, epoxy glue is certainly worth considering due to its exceptional performance characteristics and wide range of uses.
Hot Melt Glue
Hot melt glue, a versatile and widely used adhesive, is a key component in various industrial and consumer applications. Unlike traditional glues that rely on solvents or water to activate their adhesive properties, hot melt glue is thermoplastic, meaning it becomes fluid when heated and solidifies upon cooling. This unique characteristic allows for rapid bonding times, making it an essential tool in manufacturing processes such as bookbinding, packaging, and crafting. The primary ingredients of hot melt glue include thermoplastic polymers like ethylene-vinyl acetate (EVA), polyethylene, and polypropylene. These polymers provide the glue with its strength and durability. Additional components such as tackifying resins enhance the adhesive properties by improving the glue's ability to wet surfaces, while waxes like paraffin or microcrystalline wax help in controlling viscosity and flow characteristics. Fillers such as silica or calcium carbonate may also be added to improve thermal stability and reduce costs. One of the significant advantages of hot melt glue is its fast setting time, which can range from a few seconds to several minutes depending on the specific formulation. This rapid curing process makes it ideal for high-volume production lines where speed is crucial. Additionally, hot melt adhesives are generally free from solvents, which reduces the risk of toxic fumes and environmental hazards associated with solvent-based adhesives. In terms of application, hot melt glue is used across various industries. In packaging, it is used to seal boxes and cartons efficiently. In bookbinding, it helps in attaching covers and binding pages together. Crafters and DIY enthusiasts also rely on hot melt glue for its ease of use and quick results in projects ranging from scrapbooking to furniture repair. Despite its many benefits, hot melt glue has some limitations. It can be less flexible than other types of adhesives, which may lead to cracking over time if the bonded materials expand or contract significantly. However, advancements in formulations have led to the development of more flexible hot melts that mitigate this issue. In summary, hot melt glue stands out due to its rapid bonding capabilities, solvent-free composition, and versatility across different applications. Its thermoplastic nature and customizable formulations make it a valuable tool in both industrial and consumer settings, contributing significantly to the diverse world of adhesives.
Manufacturing Process and Safety Considerations
In the realm of modern manufacturing, the process of producing goods is multifaceted and intricate, requiring careful consideration of several critical factors. This article delves into the comprehensive aspects of manufacturing, focusing on three pivotal elements: Raw Material Sourcing, Production Steps and Quality Control, and Safety Precautions and Environmental Impact. The sourcing of raw materials sets the foundation for the entire production process, influencing both the quality and sustainability of the final product. The production steps, including various stages of processing and assembly, must be meticulously managed to ensure efficiency and adherence to quality standards. Additionally, safety precautions are paramount to protect workers and the environment from potential hazards, while also minimizing the ecological footprint of the manufacturing process. Understanding these components is essential for optimizing manufacturing operations. As we explore these aspects in detail, we will ultimately transition to a specific application: the Chemical Composition of Glue, highlighting how these principles are applied in the production of this ubiquitous adhesive material. By examining these interconnected elements, we can gain a deeper appreciation for the complexity and importance of manufacturing processes.
Raw Material Sourcing
Raw material sourcing is a critical component of the glue manufacturing process, directly influencing the quality, safety, and environmental impact of the final product. This phase involves the procurement of various raw materials such as polymers, resins, solvents, fillers, and additives. For instance, in the production of adhesives like epoxy or polyurethane, key raw materials include epichlorohydrin and bisphenol A for epoxy, and isocyanates and polyols for polyurethane. The sourcing process must adhere to stringent quality control measures to ensure that these materials meet specific standards for purity, consistency, and performance. Manufacturers often engage in rigorous supplier selection and auditing to guarantee that raw materials are free from contaminants and impurities. This includes conducting regular tests for chemical composition, viscosity, and other physical properties. Additionally, ethical sourcing practices are increasingly important, with many companies opting for sustainable and responsibly sourced materials to align with environmental and social responsibility goals. For example, some adhesives may incorporate bio-based materials derived from renewable resources such as plant oils or starches, reducing reliance on fossil fuels and minimizing carbon footprint. Safety considerations are paramount during raw material sourcing. Manufacturers must comply with regulatory standards and guidelines set by organizations like the Occupational Safety and Health Administration (OSHA) and the Environmental Protection Agency (EPA). This involves ensuring that all raw materials are handled, stored, and transported safely to prevent accidents and exposure to hazardous substances. Proper labeling, packaging, and documentation are essential to maintain transparency and accountability throughout the supply chain. Moreover, the sourcing of raw materials can significantly impact the overall safety profile of the adhesive. For instance, certain solvents used in adhesive formulations can be volatile or toxic if not handled correctly. Therefore, manufacturers must select solvents that are safer for workers and the environment while still meeting performance requirements. Advanced technologies such as green chemistry principles are being integrated into sourcing strategies to develop safer alternatives without compromising adhesive strength or durability. In conclusion, raw material sourcing is a multifaceted process that underpins the quality, safety, and sustainability of glue production. By prioritizing stringent quality control, ethical sourcing practices, and adherence to safety regulations, manufacturers can ensure that their adhesives not only perform optimally but also contribute positively to environmental stewardship and worker safety. This holistic approach to raw material sourcing is crucial for maintaining high standards in the manufacturing process and ultimately delivering reliable products that meet consumer needs while minimizing risks.
Production Steps and Quality Control
In the manufacturing process of glue, the production steps and quality control measures are crucial to ensure the final product meets the required standards and safety considerations. The journey begins with raw material selection, where manufacturers carefully choose ingredients such as polymers, resins, solvents, and additives based on the intended use of the glue. These materials are then mixed in specific proportions according to a formulated recipe, a process that requires precise measurement to achieve the desired consistency and performance characteristics. Following the mixing stage, the blend undergoes various physical transformations. For example, in the production of hot melt adhesives, the mixture is heated to a high temperature until it reaches a molten state. This process is closely monitored to prevent overheating, which could degrade the adhesive properties. In contrast, water-based adhesives may involve emulsification or dispersion processes to create a stable mixture. Quality control is integrated at every step of the production process. Before proceeding to the next stage, samples are taken for testing to ensure they meet specifications. This includes checks for viscosity, tensile strength, bonding time, and chemical stability. Advanced analytical techniques such as spectroscopy and chromatography may be employed to verify the chemical composition and detect any impurities. Once the adhesive has been formulated and tested, it is packaged in appropriate containers such as bottles, tubes, or drums. Here again, quality control plays a vital role; packaging materials must be compatible with the adhesive to prevent contamination or degradation during storage and transportation. Safety considerations are paramount throughout these production steps. Manufacturers must adhere to strict safety protocols to protect workers from potential hazards such as chemical exposure, burns from hot equipment, and inhalation of fumes. Personal protective equipment (PPE) like gloves, goggles, and respirators are mandatory in production areas. Additionally, facilities are designed with ventilation systems to minimize airborne contaminants. Finally, before the glue is released to the market, it undergoes rigorous final testing to ensure compliance with industry standards and regulatory requirements. This may include third-party audits and certifications that validate the product's quality and safety. By meticulously following these production steps and quality control measures, manufacturers can produce high-quality glue that not only performs well but also ensures user safety and environmental sustainability. This meticulous approach underscores the importance of integrating quality control into every facet of the manufacturing process to deliver a reliable and effective adhesive product.
Safety Precautions and Environmental Impact
In the manufacturing process of glue, safety precautions and environmental impact are paramount considerations. The production of adhesive materials involves various chemicals and processes that can pose significant risks to both human health and the environment. To mitigate these risks, manufacturers must adhere to stringent safety protocols. For instance, workers are required to wear protective gear such as gloves, goggles, and respirators to prevent exposure to harmful substances. Ventilation systems are also crucial to ensure that fumes and particles are properly filtered out of the workspace, reducing the risk of respiratory issues and other health problems. From an environmental perspective, the production of glue can have substantial impacts. Many adhesives are derived from petrochemicals, which are non-renewable resources and contribute to greenhouse gas emissions during their extraction and processing. Additionally, the manufacturing process often involves solvents and other chemicals that can contaminate waterways if not disposed of properly. To address these concerns, many manufacturers are turning to more sustainable practices. This includes the development of bio-based adhesives derived from renewable resources such as plant starches, proteins, and natural latex. These alternatives not only reduce dependence on fossil fuels but also minimize the release of harmful chemicals into the environment. Moreover, companies are implementing recycling programs for adhesive waste and adopting cleaner production technologies that minimize waste generation. For example, some manufacturers use solvent-free adhesives or water-based formulations that have lower volatile organic compound (VOC) emissions compared to traditional solvent-based adhesives. These initiatives not only help in reducing environmental footprint but also comply with increasingly stringent regulatory standards aimed at protecting public health and the environment. In summary, the manufacturing of glue necessitates a dual focus on safety precautions and environmental responsibility. By enforcing rigorous safety measures and adopting sustainable practices, manufacturers can ensure a safer working environment while minimizing their ecological impact. This holistic approach is essential for maintaining ethical standards in the industry while contributing to a healthier planet for future generations. As consumers become more aware of these issues, the demand for eco-friendly and safely produced adhesives is likely to drive further innovation in this sector.