What Is Metal Made Of

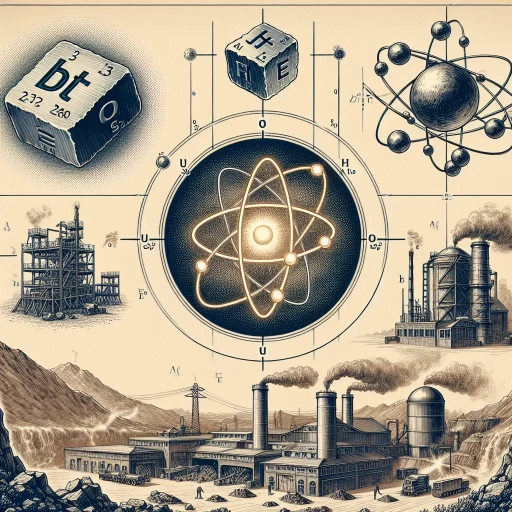
Metals are fundamental materials in modern society, underpinning various industries from construction and manufacturing to electronics and transportation. But what exactly are metals made of? To understand this, it's crucial to delve into three key aspects: the chemical composition of metals, the diverse types of metals and their sources, and the manufacturing and refining processes that transform raw materials into usable products. Starting with the chemical composition, metals are typically alloys or pure elements with specific atomic structures that confer unique properties such as strength, conductivity, and malleability. This foundational knowledge sets the stage for exploring the wide range of metal types, each with its own set of characteristics and natural sources. Finally, understanding how metals are manufactured and refined reveals the intricate processes that ensure their quality and usability. By examining these facets, we gain a comprehensive insight into what makes metals so versatile and essential. Let's begin by examining the chemical composition of metals, which forms the basis of their inherent properties and applications.
Chemical Composition of Metals
Understanding the chemical composition of metals is crucial for grasping their properties, applications, and behaviors. This complex topic can be broken down into several key areas. First, it is essential to delve into the **Atomic Structure and Elements**, as this foundational knowledge explains how metals are formed at the atomic level and how their elemental composition influences their characteristics. Additionally, **Alloys and Their Components** play a significant role, as combining different metals can enhance strength, durability, and other desirable traits. Lastly, **Impurities and Trace Elements** must be considered, as even small amounts of these can significantly impact a metal's performance and usability. By exploring these aspects, we can gain a comprehensive understanding of metal chemistry. Let's begin by examining the atomic structure and elements that form the basis of all metals.
Atomic Structure and Elements
Atomic structure and elements are fundamental concepts in understanding the chemical composition of metals. At the heart of every element lies its atomic structure, which consists of protons, neutrons, and electrons. Protons and neutrons reside in the nucleus, while electrons orbit around it in electron shells. The number of protons in an atom's nucleus determines the element's identity, known as the atomic number. For instance, iron (Fe) has an atomic number of 26, meaning it has 26 protons in its nucleus. Neutrons contribute to the atom's mass but not its charge; the sum of protons and neutrons gives the atomic mass. Elements are substances composed of atoms with the same number of protons, making them chemically identical. Metals, a class of elements, are characterized by their ability to conduct electricity and heat, malleability, and typically shiny appearance. The periodic table organizes elements based on their atomic number and recurring chemical properties. Metals are predominantly found on the left side and in the middle of the periodic table. The arrangement of electrons in an atom is crucial for understanding chemical behavior. Electron shells are filled according to specific rules, such as the Aufbau principle and Hund's rule. Metals often have fewer electrons in their outermost shell compared to nonmetals, which makes them more likely to lose electrons and form positive ions (cations). This tendency to lose electrons is a key factor in metal reactivity and their ability to form alloys and compounds. In metals, the outermost electrons are delocalized, meaning they are not bound to a single atom but are free to move within the metal lattice. This "sea of electrons" model explains many metallic properties, including high electrical conductivity and malleability. When metals react with other elements, such as oxygen or sulfur, they can form compounds like oxides or sulfides. These reactions involve the transfer of electrons from the metal atoms to the nonmetal atoms, resulting in ionic bonds. Understanding atomic structure and elements is essential for comprehending the chemical composition of metals. It explains why metals exhibit certain properties and how they interact with other substances. For example, iron's ability to form rust (iron oxide) when exposed to oxygen is a direct result of its atomic structure and electron configuration. Similarly, aluminum's resistance to corrosion can be attributed to its thin layer of oxide that forms on its surface, protecting it from further reaction. In summary, the atomic structure and elemental nature of metals dictate their chemical behavior and composition. By grasping these fundamental principles, one can better understand why metals are made up of specific elements and how these elements contribute to the overall properties of metals. This knowledge is crucial for various applications in materials science, engineering, and chemistry.
Alloys and Their Components
Alloys are composite materials made from a mixture of two or more elements, at least one of which is a metal. These combinations are designed to enhance the properties of the individual components, such as strength, durability, corrosion resistance, and thermal conductivity. The chemical composition of alloys can vary widely depending on their intended application. For instance, stainless steel is an alloy primarily composed of iron, chromium, and sometimes nickel, which provides excellent resistance to corrosion and high-temperature strength. Another example is titanium alloy, often used in aerospace due to its high strength-to-weight ratio and resistance to fatigue; it typically includes titanium as the base metal combined with elements like aluminum, vanadium, and molybdenum. In the context of chemical composition, alloys can be classified into several types based on their primary metal component. Ferrous alloys, which contain iron as the main element, include steel and cast iron. Non-ferrous alloys do not contain iron and include materials like aluminum alloys (often mixed with copper, zinc, or magnesium) and copper alloys (such as brass and bronze). The specific chemical composition of an alloy determines its physical and mechanical properties. For example, adding chromium to steel creates stainless steel by forming a protective oxide layer that prevents rusting. The process of creating an alloy involves mixing the constituent elements in specific proportions and then subjecting them to various treatments such as melting, casting, forging, or heat treatment. This process allows for the manipulation of microstructure and phase composition to achieve desired properties. Understanding the chemical composition of metals and how they interact when combined is crucial for developing new alloys with tailored characteristics. In addition to enhancing mechanical properties, alloys can also be designed for specific functional requirements. For example, superalloys are high-performance alloys used in extreme environments such as jet engine components; they are typically made from nickel or cobalt base metals combined with elements like chromium, tungsten, and rhenium for superior heat resistance and strength. Overall, the versatility and performance of alloys make them indispensable in modern technology and industry. By carefully selecting and combining different elements based on their chemical properties, engineers can create materials that meet precise specifications for a wide range of applications, from consumer goods to advanced industrial and aerospace technologies.
Impurities and Trace Elements
Impurities and trace elements play a crucial role in the chemical composition of metals, significantly influencing their physical and chemical properties. These substances, often present in small quantities, can either be naturally occurring or introduced during the metal's extraction and processing stages. Impurities are typically unwanted elements that can degrade the metal's performance, while trace elements are minor constituents that may have beneficial or detrimental effects. For instance, in steel production, impurities such as carbon, sulfur, and phosphorus can affect the metal's strength, ductility, and corrosion resistance. Carbon, although essential for steel's hardness and strength, must be controlled within specific limits to avoid brittleness. Sulfur and phosphorus, on the other hand, are generally considered harmful impurities because they can form weak points in the metal structure. Trace elements like manganese, silicon, and chromium are often intentionally added to metals to enhance their properties. Manganese, for example, improves steel's hardenability and resistance to wear. Silicon is used in aluminum alloys to increase their strength and corrosion resistance. Chromium is a key component in stainless steel, providing excellent corrosion resistance due to the formation of a protective oxide layer. The presence of impurities and trace elements can also impact the metal's microstructure. For example, certain impurities can lead to the formation of inclusions or precipitates that alter the metal's grain structure, affecting its mechanical properties. Conversely, beneficial trace elements can stabilize desirable microstructures, enhancing the overall performance of the metal. In addition to their direct effects on metal properties, impurities and trace elements can influence the metal's behavior during various industrial processes. For instance, some impurities may lower the melting point of a metal, making it easier to cast or weld. However, others may cause hot shortness—a condition where the metal becomes brittle at high temperatures—leading to cracking during fabrication. The control and management of impurities and trace elements are critical in metal production. Advanced analytical techniques such as spectroscopy and chromatography are employed to detect and quantify these elements accurately. By understanding and controlling the levels of impurities and trace elements, manufacturers can produce metals with consistent and predictable properties, ensuring they meet specific industry standards and applications. In summary, impurities and trace elements are integral components of a metal's chemical composition, influencing its physical and chemical characteristics. While impurities can be detrimental, trace elements can be beneficial when controlled appropriately. The precise management of these elements is essential for producing high-quality metals that meet various industrial requirements.
Types of Metals and Their Sources
Metals are a cornerstone of modern society, playing crucial roles in various industries from construction to electronics. Understanding the different types of metals and their sources is essential for appreciating their significance. This article delves into three primary categories: Ferrous Metals, Non-Ferrous Metals, and Precious Metals. Ferrous Metals, such as iron and steel, are foundational in the construction and automotive sectors due to their strength and durability. Non-Ferrous Metals like aluminum, copper, and zinc are vital for their lightweight and conductive properties, making them indispensable in aerospace, electrical wiring, and galvanizing processes. Precious Metals, including gold, silver, and platinum, are highly valued for their rarity and versatility in jewelry, electronics, and catalytic converters. Each category has unique characteristics and applications that make them integral to our daily lives. By exploring these metal types and their sources, we gain insight into the complex supply chains and technological advancements that shape our world. Let's begin by examining Ferrous Metals: Iron and Steel, the backbone of modern infrastructure.
Ferrous Metals: Iron and Steel
Ferrous metals, primarily composed of iron and steel, are among the most widely used and versatile materials in modern industry. **Iron**, the base metal, is extracted from iron ore through a process known as smelting, where the ore is heated in a blast furnace with coke and limestone to remove impurities. The resulting product is pig iron, which can be further refined to produce pure iron or alloyed with other elements to create various types of steel. **Steel**, an alloy of iron and carbon, is produced by reducing the carbon content of pig iron through a process called steelmaking. This can be achieved through different methods such as the Basic Oxygen Process (BOP) or the Electric Arc Furnace (EAF) process. Steel's properties can be tailored by adjusting the carbon content and adding other alloying elements like manganese, chromium, and nickel. This flexibility makes steel indispensable in construction, automotive manufacturing, and consumer goods. The sources of ferrous metals are primarily iron ore deposits found in various parts of the world. Major producers include Australia, Brazil, China, and India. Iron ore is mined from open-pit or underground mines and then processed to extract the iron content. The global demand for ferrous metals is driven by their strength, durability, and affordability, making them essential for infrastructure development and industrial applications. In addition to their widespread use in structural materials, ferrous metals also play critical roles in other industries. For instance, steel is used in the production of machinery, appliances, and tools due to its high tensile strength and resistance to wear. Iron, in its pure form or as part of alloys like stainless steel, is also crucial in medical equipment and cookware due to its non-toxic nature and heat conductivity. The recycling of ferrous metals is another significant aspect of their lifecycle. Steel is one of the most recycled materials globally, with many steel products being made from recycled steel scrap. This not only conserves natural resources but also reduces energy consumption and environmental impact associated with primary production. In summary, ferrous metals—iron and steel—are fundamental to modern society due to their strength, versatility, and widespread availability. Their extraction from iron ore, processing into various forms of steel, and extensive use across multiple industries underscore their importance. Additionally, the recyclability of these metals ensures a sustainable supply chain, making them a cornerstone of industrial development.
Non-Ferrous Metals: Aluminum, Copper, and Zinc
Non-ferrous metals, such as aluminum, copper, and zinc, are crucial components in various industrial and everyday applications due to their unique properties and versatility. **Aluminum**, the most abundant metal in the Earth's crust, is lightweight, corrosion-resistant, and an excellent conductor of electricity. It is primarily extracted from bauxite ore through the Bayer process and electrolysis. Aluminum's applications range from aircraft and automotive parts to packaging materials and electrical wiring. Its recyclability makes it an environmentally friendly choice, contributing significantly to sustainable practices. **Copper**, known for its exceptional electrical conductivity and thermal properties, is a vital element in modern technology. It is often mined from copper sulfide ores using flotation and smelting processes. Copper's widespread use includes electrical wiring, electronics, plumbing, and architectural features due to its durability and resistance to corrosion. Additionally, copper alloys like brass (copper-zinc) and bronze (copper-tin) enhance its strength and versatility. **Zinc**, another significant non-ferrous metal, is primarily extracted from sphalerite (zinc sulfide) ore through flotation and roasting processes. Zinc is highly valued for its protective qualities against corrosion when applied as a coating to other metals, a process known as galvanization. It is also essential in the production of batteries, alloys like brass, and various consumer goods such as coins and hardware. Zinc's role in human health as an essential mineral further underscores its importance across different sectors. These non-ferrous metals are sourced from diverse geological formations around the world. For instance, Australia and China are major producers of aluminum-rich bauxite, while Chile and Peru lead in copper production. Zinc deposits are found in significant quantities in countries like Australia, China, and Peru. The extraction and processing of these metals involve complex technologies that ensure efficient recovery while minimizing environmental impact. In summary, aluminum, copper, and zinc are indispensable non-ferrous metals that contribute significantly to various industries due to their unique properties. Their extraction processes involve advanced technologies that balance economic needs with environmental considerations. Understanding these metals' sources and applications provides insight into their critical role in modern society and underscores the importance of sustainable metal production practices.
Precious Metals: Gold, Silver, and Platinum
Precious metals, including gold, silver, and platinum, are highly valued for their rarity, aesthetic appeal, and industrial applications. **Gold**, often associated with wealth and luxury, is a ductile and malleable metal with excellent conductivity. It is primarily extracted from veins of quartz and other rocks through processes like placer mining and hardrock mining. Gold's resistance to corrosion makes it ideal for jewelry, coins, and electronics. **Silver**, known for its high thermal and electrical conductivity, is another versatile precious metal. It is commonly found in ores such as argentite and galena. Silver mining often occurs alongside copper and lead mining due to their frequent co-occurrence in ore deposits. Its uses range from cutlery and coins to solar panels and medical applications. **Platinum**, the rarest of the three, is a dense and malleable metal with high melting points. It is primarily mined in South Africa from the Bushveld Complex, a large layered igneous intrusion. Platinum's catalytic properties make it crucial in automotive exhaust systems and the production of nitric acid. Additionally, it is used in jewelry and dental implants due to its strength and resistance to corrosion. These precious metals are not only significant in economic terms but also play critical roles in various technological and industrial sectors, underscoring their importance in modern society.
Manufacturing and Refining Processes
Manufacturing and refining processes are the backbone of modern industry, transforming raw materials into the products that shape our daily lives. These processes involve several critical stages, each contributing to the final quality and functionality of the end product. First, **Extraction from Ores and Minerals** is the initial step where raw materials are obtained from natural sources. This stage sets the foundation for all subsequent processes. Next, **Smelting and Refining Techniques** come into play, where extracted materials are purified and transformed into usable forms. Finally, **Alloying and Shaping Methods** allow for the creation of specific alloys and the molding of these materials into their desired forms. Understanding these stages is essential for appreciating the complexity and precision involved in manufacturing. By delving into these processes, we can better comprehend how raw materials are transformed into the sophisticated products we rely on. Let's begin by exploring the first crucial step: **Extraction from Ores and Minerals**.
Extraction from Ores and Minerals
Extraction from ores and minerals is a critical step in the manufacturing and refining processes of metals. This process involves the separation of valuable metals from their naturally occurring ore, which is a mixture of minerals and other substances. The extraction method depends on the type of metal and its chemical properties. For instance, iron is often extracted through smelting, where iron ore is heated with carbon to produce pig iron. This process reduces the iron oxides in the ore to pure iron. Copper, on the other hand, can be extracted using various methods including flotation, where copper minerals are separated from other minerals based on their hydrophobic properties. Once separated, these minerals undergo further refining processes such as electrolysis to produce high-purity copper. Aluminum extraction involves the Bayer process, where bauxite ore is treated with sodium hydroxide to separate alumina (aluminum oxide), which is then smelted in an electrolytic cell to produce pure aluminum. Gold extraction often employs cyanidation, where gold ore is mixed with a cyanide solution that dissolves the gold, allowing it to be separated from other minerals. The gold is then precipitated out of the solution using zinc or activated carbon. These extraction methods are not only crucial for obtaining raw metals but also play a significant role in determining the environmental impact and economic viability of metal production. In addition to these specific methods, general steps such as crushing, grinding, and flotation are common across many types of ore extraction. These mechanical processes break down the ore into smaller particles, making it easier to separate the desired minerals from waste rock. Advanced technologies like bioleaching and hydrometallurgy are also being developed to improve efficiency and reduce environmental footprint. Overall, the extraction from ores and minerals is a complex yet essential phase in metal production, requiring careful consideration of both technical feasibility and sustainability. As technology continues to evolve, new methods are being developed to make this process more efficient and environmentally friendly, ensuring a steady supply of metals for various industrial applications while minimizing adverse impacts on ecosystems.
Smelting and Refining Techniques
Smelting and refining are crucial processes in the production of metals, transforming raw materials into usable forms. **Smelting** involves heating ores to high temperatures, typically in the presence of a reducing agent, to extract the metal. This process can be divided into several stages: roasting, where the ore is heated to remove impurities; reduction, where the metal is separated from its oxide form; and refining, where the extracted metal is purified. For instance, in iron smelting, iron ore is mixed with coke (a form of carbon) and limestone in a blast furnace. The coke reduces the iron oxides to pure iron, while the limestone removes impurities such as silica. **Refining** techniques further purify the extracted metal to achieve the desired properties. There are several refining methods depending on the metal being processed. For example, **electrolytic refining** is commonly used for copper and nickel. In this process, an impure anode is dissolved in an electrolyte solution, and pure metal is deposited at the cathode. Another method is **distillation**, used for metals like zinc and mercury, where the metal is heated to its boiling point and then condensed back into a solid state, leaving impurities behind. **Chemical refining** involves treating the metal with chemicals to remove impurities. For instance, in the production of aluminum, the Bayer process is used to refine bauxite ore into alumina (aluminum oxide), which is then smelted using electrolysis. **Vacuum refining** is another technique that removes impurities by heating the metal in a vacuum, causing volatile impurities to evaporate. Each refining technique is tailored to the specific properties of the metal being processed. For example, **zone refining** is used for high-purity metals like silicon and germanium, where a narrow molten zone is moved along the length of the ingot, carrying impurities with it and leaving behind a highly purified metal. In summary, smelting and refining are essential steps in metal production that involve complex chemical and physical transformations to extract and purify metals from their ores. These processes are highly specialized and vary significantly depending on the type of metal being produced, ensuring that the final product meets the required standards for various industrial applications.
Alloying and Shaping Methods
Alloying and shaping are crucial steps in the manufacturing and refining processes of metals, significantly enhancing their properties and usability. **Alloying** involves combining two or more elements, at least one of which is a metal, to create an alloy with improved strength, corrosion resistance, and other desirable characteristics. For instance, stainless steel is an alloy of iron, chromium, and sometimes nickel, which provides superior resistance to corrosion compared to pure iron. The process of alloying can be achieved through various methods such as melting the constituent elements together and then solidifying the mixture, or through mechanical alloying where powders are mixed and then consolidated. This technique allows for the creation of materials with tailored properties for specific applications. **Shaping methods** are essential for transforming raw metals or alloys into usable forms. These methods include **casting**, where molten metal is poured into a mold to achieve the desired shape; **forging**, which involves shaping metal through hammering or pressing; **rolling**, where metal is passed through rollers to reduce its thickness and increase its length; and **machining**, which uses cutting tools to remove material and achieve precise dimensions. Additionally, **extrusion** involves forcing metal through a die to create long, continuous shapes like tubes or rods. Each shaping method has its own set of advantages and is chosen based on the required shape, size, and properties of the final product. For example, casting is often used for complex shapes that cannot be easily produced by other methods, while forging is preferred for parts that need high strength and toughness. In modern manufacturing, advanced techniques such as **3D printing** (additive manufacturing) are also being employed to shape metals. This process builds parts layer by layer, allowing for the creation of complex geometries that would be difficult or impossible to achieve with traditional methods. Furthermore, **powder metallurgy** involves shaping metal powders into desired forms using compaction and sintering processes, which can produce parts with uniform microstructure and minimal waste. The combination of alloying and shaping techniques enables the production of a wide range of metal products with optimized performance characteristics. For example, in aerospace engineering, titanium alloys are often used due to their high strength-to-weight ratio and resistance to corrosion, which are achieved through precise alloying and shaping processes. Similarly, in automotive manufacturing, steel alloys are commonly used for structural components due to their strength, durability, and cost-effectiveness. In summary, alloying and shaping are integral to the manufacturing and refining processes of metals. By carefully selecting and combining elements through alloying, and then using appropriate shaping methods, manufacturers can produce materials with specific properties tailored to meet the demands of various industries. These processes not only enhance the performance of metals but also contribute to the development of innovative products and technologies.