What Boeing Planes To Avoid

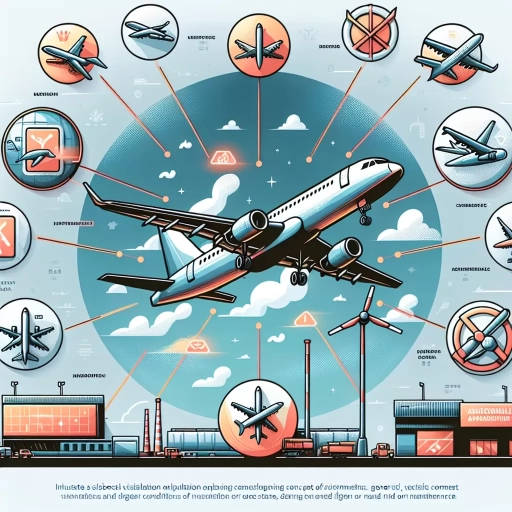
When considering air travel, safety is paramount, and the choice of aircraft can significantly impact one's confidence in the journey. Boeing, a leading manufacturer of commercial airplanes, has a mixed history with some models raising more concerns than others. This article delves into the Boeing planes that travelers might want to avoid, focusing on three critical areas: Historical Safety Concerns and Incidents, Design and Engineering Flaws, and Maintenance and Operational Challenges. By examining these aspects, we can better understand which Boeing models have faced significant issues in the past. Starting with Historical Safety Concerns and Incidents, we will explore the notable events and accidents that have marred the safety record of certain Boeing planes, setting the stage for a deeper analysis of their design and operational challenges.
Historical Safety Concerns and Incidents
Historical safety concerns and incidents in aviation have been pivotal in shaping the industry's safety standards and regulatory frameworks. The aviation sector has faced numerous challenges over the years, each contributing to a more robust and safer environment for passengers and crew. Three significant examples that highlight these concerns are the 737 MAX crashes and subsequent grounding, the safety issues surrounding the DC-10 series, and the early model problems of the Boeing 747. The 737 MAX crashes, which resulted in the loss of hundreds of lives, led to a global grounding of the aircraft and a thorough reevaluation of its design and certification process. Similarly, the DC-10 series faced multiple high-profile incidents that exposed systemic flaws in its design and maintenance practices. Early models of the Boeing 747 also encountered several safety issues, including structural weaknesses and operational challenges. These incidents have not only led to immediate corrective actions but have also driven long-term improvements in aircraft design, testing, and regulatory oversight. Transitioning to one of the most recent and impactful incidents, the 737 MAX crashes and grounding serve as a stark reminder of the ongoing need for vigilance and continuous improvement in aviation safety.
737 MAX Crashes and Grounding
The 737 MAX crashes and subsequent grounding represent one of the most significant aviation safety crises in recent history. On October 29, 2018, Lion Air Flight 610, a Boeing 737 MAX 8, crashed into the Java Sea shortly after takeoff from Jakarta, Indonesia, resulting in the deaths of all 189 people on board. Just over four months later, on March 10, 2019, Ethiopian Airlines Flight 302, another 737 MAX 8, crashed near Addis Ababa, Ethiopia, killing all 157 passengers and crew members. These tragedies led to a global grounding of the 737 MAX fleet by regulatory authorities worldwide. Investigations into both crashes revealed a common cause: the malfunctioning of the Maneuvering Characteristics Augmentation System (MCAS), a software system designed to prevent the aircraft from stalling. MCAS relied on data from a single angle of attack sensor, which in both incidents provided incorrect readings, causing the system to repeatedly push the nose of the plane downward. This led to a loss of control by the pilots, who were not adequately informed about the MCAS system or its potential failure modes. The grounding of the 737 MAX was swift and widespread. By March 2019, aviation authorities in numerous countries had banned the aircraft from flying, followed by the U.S. Federal Aviation Administration (FAA) on March 13, 2019. The FAA's decision marked a significant shift from its initial stance of supporting the continued operation of the 737 MAX with enhanced pilot training. Boeing faced intense scrutiny and criticism for its handling of the MCAS system's development and certification process. It was revealed that Boeing had not fully disclosed the existence and functionality of MCAS to pilots or regulatory bodies, and that the company had lobbied against more stringent training requirements for pilots transitioning to the 737 MAX from earlier models. The aftermath of the crashes included multiple investigations, lawsuits, and congressional hearings. Boeing agreed to pay billions of dollars in compensation to families of the victims and faced significant financial penalties. The company also implemented software updates to the MCAS system, enhanced pilot training programs, and made other safety improvements before the 737 MAX was cleared to return to service by regulatory bodies around the world. The 737 MAX grounding highlighted broader historical safety concerns within Boeing and the aviation industry. It underscored issues related to regulatory oversight, corporate transparency, and the balance between technological innovation and safety protocols. The incident served as a stark reminder of the importance of robust safety standards and open communication between manufacturers, regulators, and operators to ensure public trust in air travel. As a result, future aircraft designs and certification processes are likely to be subject to even more rigorous scrutiny to prevent similar tragedies.
DC-10 Series Safety Issues
The DC-10 series, developed by McDonnell Douglas, has been marred by a history of significant safety issues and incidents that have led to numerous fatalities and raised concerns about its reliability. One of the most notable incidents was the crash of Turkish Airlines Flight 981 in 1974, which resulted in the deaths of all 346 people on board. This tragedy was attributed to a faulty cargo door that burst open during flight, causing decompression and loss of control. The investigation revealed inadequate safety measures and design flaws in the cargo door mechanism. Another critical incident occurred in 1979 with American Airlines Flight 191, where an engine fell off during takeoff due to improper maintenance procedures. This led to a crash that killed all 271 people on board and two people on the ground. The National Transportation Safety Board (NTSB) identified the cause as a faulty engine pylon attachment that had been improperly maintained. The DC-10 also faced issues related to its fuel tank design. In 1989, United Airlines Flight 232 suffered a catastrophic failure of its tail-mounted engine, which led to a loss of hydraulic systems and subsequent crash landing in Sioux City, Iowa. Although there were survivors, 111 lives were lost. The incident highlighted vulnerabilities in the aircraft's design and maintenance practices. Additionally, the DC-10 was subject to several Federal Aviation Administration (FAA) airworthiness directives due to recurring problems with its electrical systems, landing gear, and other critical components. These directives often mandated immediate corrective actions to ensure continued safe operation. The cumulative effect of these incidents and ongoing safety concerns led many airlines and regulatory bodies to scrutinize the DC-10 more closely than other aircraft. While some improvements were made over time, the reputation of the DC-10 as a less safe option persisted, contributing to its eventual decline from commercial service. In summary, the DC-10 series has faced multiple severe safety issues and incidents throughout its operational history, including fatal crashes due to design flaws, maintenance errors, and systemic vulnerabilities. These historical safety concerns underscore why the DC-10 is often cited as one of the Boeing planes—or rather, non-Boeing planes—to avoid when considering air travel safety.
Early 747 Model Problems
The early 747 models, introduced in the late 1960s and early 1970s, faced several significant problems that raised historical safety concerns. One of the primary issues was the aircraft's complex and innovative design, which included a high-bypass turbofan engine and a unique upper deck. This complexity led to teething problems, including engine reliability issues and structural concerns. The Pratt & Whitney JT9D engines, which powered the initial 747s, experienced frequent failures and overheating, necessitating numerous modifications and updates. Additionally, the aircraft's high altitude and speed capabilities put additional stress on its airframe, leading to instances of fatigue and cracking in certain structural components. Another critical issue was the lack of adequate training for pilots transitioning from smaller aircraft to the massive 747. The sheer size and weight of the plane, combined with its advanced systems, made it challenging for pilots to adapt quickly. This led to several incidents where pilot error contributed to safety issues. For example, the 1972 crash of Japan Airlines Flight 446 during takeoff from Tokyo's Haneda Airport highlighted the need for more comprehensive training programs. Furthermore, early 747 models were plagued by electrical system malfunctions and hydraulic system failures. These issues often resulted in loss of critical flight controls or navigation systems, posing significant risks to safe flight operations. The 1974 crash of Turkish Airlines Flight 981, which was attributed to a faulty cargo door that led to decompression and subsequent loss of control, underscored the importance of robust safety protocols and rigorous maintenance practices. The early years of the 747 also saw concerns regarding its fuel efficiency and range performance. While the aircraft was designed to be more efficient than its predecessors, initial models did not meet expected fuel economy standards, which affected operational costs and route planning. This issue was particularly pertinent given the rising fuel prices of the 1970s. In response to these challenges, Boeing and regulatory bodies implemented numerous safety improvements and design modifications. Enhanced engine designs, improved pilot training programs, and stricter maintenance standards were among the measures taken to address these early problems. Despite these initial hurdles, the Boeing 747 went on to become one of the most iconic and reliable commercial airliners in history, with many of its early issues serving as valuable lessons in aviation safety and design evolution.
Design and Engineering Flaws
Design and engineering flaws in aircraft can have catastrophic consequences, highlighting the critical importance of rigorous testing and quality control in the aviation industry. This article delves into three significant examples that underscore these risks: Rudder Hardover Issues in 737s, Fuel Tank Ignition Risks in 737s, and Electrical System Failures in older models. Each of these flaws has led to serious incidents and underscores the need for continuous improvement in design and engineering practices. The Rudder Hardover Issues, for instance, have been linked to several accidents where the rudder suddenly and unexpectedly moved to its full deflection, causing loss of control. Similarly, Fuel Tank Ignition Risks have been a concern due to the potential for fuel tanks to ignite under certain conditions, posing a significant threat to passenger safety. Electrical System Failures in older models have also been a recurring problem, leading to various malfunctions that can compromise aircraft safety. Understanding these flaws is crucial for preventing future accidents and ensuring the highest standards of safety in aviation. This article will first explore the Rudder Hardover Issues in 737s, examining the causes, consequences, and measures taken to mitigate this critical design flaw.
Rudder Hardover Issues in 737s
The Boeing 737, one of the most widely used commercial aircraft, has faced several critical issues over the years, with rudder hardover being a particularly concerning problem. This issue involves the sudden and uncommanded movement of the rudder, which can lead to loss of control and potentially catastrophic outcomes. The rudder hardover phenomenon was first identified in the 1990s and has been linked to a combination of design and engineering flaws. At the heart of the problem is the rudder control system, specifically the rudder power control unit (PCU) and its interaction with the hydraulic system. The PCU is responsible for controlling the movement of the rudder, but in certain conditions, it can malfunction, causing the rudder to move unexpectedly. This can happen due to a variety of factors including hydraulic fluid contamination, faulty valve operation, or electrical issues within the PCU. One of the most notable incidents involving rudder hardover occurred on October 31, 1994, when USAir Flight 427 crashed near Pittsburgh, Pennsylvania, resulting in the loss of all 132 lives on board. The National Transportation Safety Board (NTSB) investigation concluded that a probable cause of the crash was a malfunction of the rudder PCU. Similar incidents have been reported in other 737 flights, highlighting a systemic issue rather than isolated events. Boeing and regulatory bodies have implemented several modifications and safety directives to mitigate these risks. These include redesigning the rudder PCU, enhancing maintenance procedures to ensure hydraulic fluid purity, and providing additional training for pilots to handle such emergencies. However, despite these efforts, concerns about the reliability and safety of the 737's rudder control system persist. The rudder hardover issue underscores broader design and engineering flaws in some Boeing aircraft. It highlights the importance of rigorous testing, robust design standards, and continuous monitoring of aircraft systems to prevent such malfunctions. For passengers and airlines considering which Boeing planes to avoid, understanding these historical issues can inform decision-making and emphasize the need for stringent safety protocols. In summary, while Boeing has taken steps to address rudder hardover issues in the 737, the history of this problem serves as a cautionary tale about the critical importance of meticulous design, thorough testing, and ongoing maintenance in ensuring aviation safety. As such, it remains a significant factor for those evaluating the safety profile of different Boeing aircraft models.
Fuel Tank Ignition Risks in 737s
Fuel tank ignition risks in Boeing 737s are a critical concern that highlights significant design and engineering flaws. The primary issue revolves around the potential for fuel tank explosions, which can be catastrophic. One of the most notable incidents was the 1996 crash of TWA Flight 800, a Boeing 747, but similar risks exist in 737 models due to shared design elements. The central problem is the presence of flammable air-fuel mixtures within the fuel tanks, particularly when they are not fully filled. In these conditions, the ullage (the empty space above the fuel) can contain a mixture of air and fuel vapors that is highly susceptible to ignition. Boeing 737s, especially older models, lack adequate protection against such ignitions. The Federal Aviation Administration (FAA) has mandated various safety measures over the years, including the installation of nitrogen generation systems (NGS) to reduce the oxygen levels in the ullage, thereby minimizing the risk of explosion. However, these modifications have been implemented gradually, and many older 737s may still be vulnerable. Another significant flaw is the electrical wiring and components located near the fuel tanks. Aging wiring and components can deteriorate over time, leading to arcing or short circuits that could ignite the flammable mixture. This risk is exacerbated by the lack of robust protective measures such as arc fault circuit interrupters (AFCIs) in older aircraft designs. Additionally, maintenance practices play a crucial role in mitigating these risks. Poor maintenance can lead to undetected issues with wiring and other components, further increasing the likelihood of an ignition event. Boeing has faced criticism for not adequately addressing these issues in its design and maintenance recommendations for the 737 fleet. In summary, fuel tank ignition risks in Boeing 737s underscore serious design and engineering flaws that have been partially addressed but remain a concern, especially for older models. These risks include flammable air-fuel mixtures, inadequate protection against ignition, and potential electrical hazards. While regulatory bodies and Boeing have taken steps to mitigate these risks, ongoing vigilance and continuous improvement are necessary to ensure passenger safety.
Electrical System Failures in Older Models
Electrical system failures in older Boeing models are a significant concern, often stemming from design and engineering flaws that have been identified over the years. One of the most critical issues is the aging of electrical components, which can lead to malfunctions and failures. For instance, older Boeing 737 models have experienced problems with their electrical power generation and distribution systems, including issues with generators, relays, and circuit breakers. These components, when not properly maintained or updated, can fail unexpectedly, leading to loss of critical systems such as navigation, communication, and even flight control. Another design flaw is the use of outdated wiring and connectors. Older aircraft often have wiring that is prone to degradation over time, which can result in short circuits and electrical fires. The Boeing 747-100 and 200 series, for example, have been known to have wiring issues that have led to significant safety concerns. Additionally, the lack of redundancy in some electrical systems means that a single failure can have cascading effects, potentially leading to catastrophic outcomes. The integration of modern avionics into older airframes also poses challenges. Upgrading older aircraft with newer electronic systems can introduce compatibility issues and increase the complexity of the electrical system, making it harder to diagnose and repair faults. This is particularly evident in models like the Boeing 757, where retrofitting with advanced avionics has sometimes led to electrical system instability. Furthermore, maintenance practices play a crucial role in preventing electrical system failures. However, older models may not have been designed with modern maintenance standards in mind, making it difficult for technicians to access and replace electrical components efficiently. This can lead to prolonged downtime and increased risk of human error during maintenance procedures. In summary, electrical system failures in older Boeing models are frequently linked to inherent design and engineering flaws. These include aging components, outdated wiring, lack of redundancy, integration challenges with modern avionics, and maintenance complexities. Understanding these issues is crucial for both airlines and regulatory bodies to ensure the continued safe operation of these aircraft. Addressing these flaws through regular updates, rigorous maintenance, and adherence to modern safety standards is essential for mitigating the risks associated with electrical system failures in older Boeing models.
Maintenance and Operational Challenges
Maintaining and operating aircraft is a complex and multifaceted challenge that involves several critical aspects. One of the primary concerns is the corrosion problems that arise in aging aircraft, which can significantly compromise safety and performance. Additionally, the complexity of modern avionics systems presents a significant hurdle, as these sophisticated technologies require specialized knowledge and continuous updates to ensure optimal functioning. Furthermore, pilot training and familiarization issues are equally important, as pilots must be adequately trained to handle the advanced systems and navigate the evolving operational landscape. These challenges are interconnected and must be addressed comprehensively to ensure the safe and efficient operation of aircraft. Understanding these issues is crucial for maintaining high standards in aviation, and we will begin by examining the corrosion problems in aging aircraft, a critical factor that directly impacts the longevity and reliability of these vehicles.
Corrosion Problems in Aging Aircraft
Corrosion problems in aging aircraft pose significant maintenance and operational challenges, impacting both safety and efficiency. As aircraft age, their materials are increasingly exposed to environmental factors such as moisture, salt, and pollutants, which accelerate the corrosion process. This can lead to structural weakening, particularly in critical areas like wing spars, fuselage frames, and landing gear components. Corrosion can also compromise the integrity of electrical systems and hydraulic lines, potentially causing system failures during flight. The detection and mitigation of corrosion require frequent inspections and specialized maintenance procedures, adding to the operational costs and downtime of the aircraft. Furthermore, older aircraft may lack modern corrosion-resistant materials and coatings, making them more susceptible to damage. For instance, Boeing planes from earlier generations may have aluminum alloys that are more prone to corrosion compared to newer models with advanced materials. The cumulative effect of these factors necessitates rigorous maintenance schedules and potentially costly repairs, making it crucial for operators to carefully evaluate the long-term viability of aging aircraft in their fleet. In summary, addressing corrosion issues is a critical aspect of maintaining the airworthiness of aging aircraft, and it significantly influences the overall operational reliability and safety of these planes.
Complexity of Modern Avionics Systems
The complexity of modern avionics systems presents a significant challenge in the maintenance and operational aspects of Boeing planes. Modern avionics, which encompass a wide range of electronic systems including navigation, communication, and flight control, have evolved to become highly sophisticated and interconnected. These systems rely on advanced software, complex algorithms, and a multitude of sensors and actuators to ensure safe and efficient flight operations. However, this increased complexity introduces several challenges. Firstly, the sheer volume of data generated by these systems can be overwhelming. Modern aircraft can produce terabytes of data per flight, which requires advanced data analytics tools to interpret and act upon. This necessitates specialized training for maintenance personnel to understand and troubleshoot issues effectively. Additionally, the integration of multiple systems means that a fault in one system can have cascading effects on others, making diagnosis and repair more difficult. Secondly, the reliance on software updates and patches adds another layer of complexity. Ensuring that all systems are updated with the latest software versions is crucial for maintaining safety and performance standards. However, this process can be time-consuming and requires meticulous planning to avoid downtime and ensure compliance with regulatory requirements. Thirdly, the increasing use of automation in modern avionics raises concerns about pilot training and proficiency. While automation enhances safety by reducing pilot workload, it also means that pilots must be trained to understand and interact with these systems effectively. This includes knowing how to handle system failures or malfunctions, which can be particularly challenging given the complexity of these systems. Furthermore, cybersecurity is a growing concern as modern avionics become more connected to external networks. Protecting these systems from cyber threats requires robust security measures and continuous monitoring, adding another dimension to the maintenance and operational challenges. In summary, the complexity of modern avionics systems in Boeing planes demands a high level of expertise in maintenance and operation. It necessitates advanced training for personnel, sophisticated data management tools, rigorous software update protocols, enhanced pilot training programs, and robust cybersecurity measures. Addressing these challenges is critical to ensuring the safe and efficient operation of these sophisticated aircraft.
Pilot Training and Familiarization Issues
Pilot training and familiarization are critical components in ensuring the safe and efficient operation of Boeing aircraft. However, several issues can arise that impact both maintenance and operational challenges. One significant concern is the complexity of modern avionics systems, which can overwhelm pilots if they are not adequately trained. Boeing's advanced aircraft, such as the 787 Dreamliner and 737 MAX, feature sophisticated automation and digital cockpits that require extensive training to master. Inadequate training can lead to pilot errors, which may result in operational mishaps or even accidents. Another issue is the variability in training standards across different regions and airlines. While Boeing provides comprehensive training programs, the implementation and adherence to these standards can vary significantly. This inconsistency can lead to a lack of uniformity in pilot skills and knowledge, complicating maintenance and operational procedures. For instance, pilots who are not familiar with specific maintenance protocols may inadvertently overlook critical checks or procedures, potentially leading to safety issues. The transition from older models to newer ones also poses challenges. Pilots must undergo significant retraining to adapt to new systems and technologies, which can be time-consuming and costly. The 737 MAX, for example, introduced several new features compared to its predecessors, including the MCAS system that has been at the center of controversy. Insufficient familiarization with these new systems has been linked to several high-profile incidents, highlighting the need for rigorous and continuous training. Additionally, the availability of simulator training and access to real-world scenarios play a crucial role in pilot preparedness. Limited access to simulators or realistic training environments can hinder pilots' ability to handle emergency situations effectively. Boeing has been working to enhance simulator capabilities and provide more realistic training scenarios, but resource constraints and budget limitations can still affect the quality of training. Furthermore, regulatory requirements and compliance add another layer of complexity. Pilots must adhere to stringent regulations set by aviation authorities such as the Federal Aviation Administration (FAA) or the European Aviation Safety Agency (EASA). Ensuring compliance with these regulations while also maintaining operational efficiency can be challenging, especially in regions with less stringent oversight. In summary, pilot training and familiarization issues are multifaceted and can significantly impact the maintenance and operational challenges associated with Boeing aircraft. Addressing these issues requires a concerted effort from Boeing, airlines, and regulatory bodies to ensure that pilots are adequately trained, familiar with new technologies, and compliant with regulatory standards. By doing so, the safety and efficiency of Boeing aircraft operations can be enhanced, reducing the likelihood of adverse events and ensuring smoother maintenance processes.