What Is Sublimation Ink

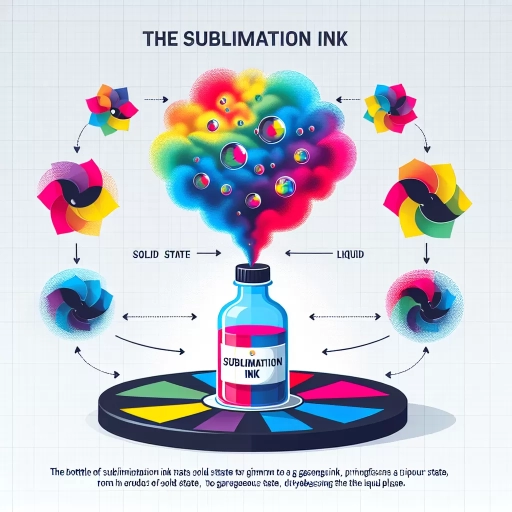
Sublimation ink is a specialized type of dye that has revolutionized the world of printing and design, particularly in the realms of textiles, ceramics, and other materials. This unique ink undergoes a process called sublimation, where it transitions directly from a solid to a gas state without going through the liquid phase, allowing it to bond deeply with the substrate. Understanding the basics of sublimation ink is crucial for anyone looking to leverage its capabilities. In this article, we will delve into the fundamental principles of sublimation ink, explore its diverse applications and uses across various industries, and provide best practices and tips for optimal usage. By grasping these key aspects, you will be well-equipped to harness the full potential of sublimation ink. Let's begin by understanding the basics of sublimation ink, which forms the foundation for its versatile applications and effective use.
Understanding Sublimation Ink Basics
Understanding the basics of sublimation ink is crucial for anyone looking to delve into the world of sublimation printing. This process, which involves transferring dye onto materials like ceramics, fabrics, and metals, relies heavily on the unique properties of sublimation ink. To grasp the full potential of this technology, it is essential to explore three key aspects: the chemical composition of sublimation ink, how it works, and the various types available. Firstly, understanding the chemical composition of sublimation ink provides a foundational knowledge of its behavior and performance. This involves knowing the specific dyes and additives that make up the ink, which are designed to transition from a solid to a gas state without going through the liquid phase—a process known as sublimation. Secondly, comprehending how sublimation ink works is vital for optimizing print quality and ensuring successful transfers. This includes understanding the heat and pressure requirements necessary for the sublimation process to occur effectively. Lastly, recognizing the different types of sublimation ink available allows users to select the most appropriate option for their specific needs. Whether it's for printing on fabrics, ceramics, or other materials, each type of ink has its own set of characteristics that can significantly impact the final result. By starting with an in-depth look at the **Chemical Composition of Sublimation Ink**, we can build a solid foundation for understanding the intricacies of this versatile printing method.
Chemical Composition of Sublimation Ink
Understanding the chemical composition of sublimation ink is crucial for appreciating its unique properties and applications. Sublimation ink, used in the sublimation printing process, is a specialized dye-based ink that undergoes a phase transition from solid to gas without going through the liquid phase. This process, known as sublimation, allows the ink to bond with polyester fabrics, ceramics, and other materials at the molecular level. The chemical composition of sublimation ink typically includes a mixture of dyes, glycols, and other additives. The dyes are the primary components responsible for the color and vibrancy of the ink. These dyes are usually disperse dyes, which are finely ground powders that dissolve in the glycol-based carrier fluid. The most common glycols used are diethylene glycol (DEG) and triethylene glycol (TEG), which serve as solvents to carry the dyes through the printing process. These glycols have low viscosity and high boiling points, making them ideal for maintaining the ink's fluidity and stability during printing. In addition to dyes and glycols, sublimation ink may contain various additives to enhance its performance. Surfactants are added to improve the ink's wetting properties on the substrate, ensuring even distribution and preventing beading or pooling. Anti-foaming agents help prevent foam formation during the printing process, which can lead to defects in the final product. UV stabilizers may also be included to protect the dyes from degradation caused by exposure to ultraviolet light, thereby maintaining color intensity over time. The precise formulation of sublimation ink can vary depending on the manufacturer and the intended application. For instance, inks designed for textile printing might have different surfactant levels compared to those intended for ceramic or metal substrates. Understanding these variations is essential for achieving optimal results in different sublimation applications. In summary, the chemical composition of sublimation ink is a carefully balanced blend of dyes, glycols, and additives that enable it to undergo sublimation efficiently while ensuring vibrant colors and durability on various substrates. This complex formulation is what makes sublimation ink so versatile and effective in producing high-quality images on a wide range of materials. By grasping the intricacies of its chemical makeup, users can better appreciate the science behind sublimation printing and optimize their techniques for superior outcomes.
How Sublimation Ink Works
**How Sublimation Ink Works** Sublimation ink is a specialized type of dye that undergoes a unique transformation process, allowing it to transition directly from a solid to a gas state without going through the liquid phase. This phenomenon, known as sublimation, is the cornerstone of how sublimation ink works. Here’s a detailed look at the process: 1. **Printing**: The journey begins with printing the design onto a transfer paper using sublimation ink. This ink is typically made up of sublimation dyes, which are designed to vaporize at high temperatures. 2. **Heat Press**: Once the design is printed, the transfer paper is placed on top of the substrate (such as ceramic, polyester fabric, or metal) and then inserted into a heat press. The heat press applies high pressure and temperature, usually around 400°F (200°C), to the transfer paper. 3. **Sublimation Process**: When exposed to this heat, the sublimation dyes in the ink vaporize and turn into gas. This gas then penetrates the substrate material. For materials like polyester fabric, the gas molecules diffuse into the polymer chains, while for ceramics and metals, they bond with the surface coating. 4. **Cooling and Solidification**: As the substrate cools down, the gas molecules return to their solid state, embedding themselves within the material. This results in a permanent, full-color image that is resistant to fading and wear. 5. **Bonding**: The final step involves the bonding of these solidified dye molecules with the substrate material. This bonding ensures that the image remains vibrant and durable over time, making it ideal for various applications such as custom apparel, home decor items, and promotional products. The efficiency of sublimation ink relies heavily on the compatibility between the ink and the substrate material. For instance, polyester fabrics work best because their polymer chains can open up to allow dye molecules to penetrate during the heating process. Similarly, ceramics and metals must have a special coating that can bond with the sublimation dyes. In summary, sublimation ink works by leveraging the unique properties of sublimation dyes to create durable, high-quality images on various materials through a process involving printing, heating, vaporization, diffusion, cooling, and bonding. This technology has revolutionized the field of custom printing by offering a versatile and reliable method for producing vibrant designs that last. Understanding these basics is crucial for anyone looking to explore the world of sublimation printing effectively.
Types of Sublimation Ink
**Types of Sublimation Ink** Understanding the various types of sublimation ink is crucial for achieving optimal results in sublimation printing. Sublimation ink, used in the process of transferring dye onto materials like ceramics, fabrics, and metals, comes in several formulations tailored to specific applications. **Dye-Sublimation Ink** is the most common type and is designed for use with sublimation printers. It contains sublimation dyes that change from a solid to a gas state when heated, allowing them to penetrate the substrate and create vibrant, long-lasting images. **Eco-Solvent Sublimation Ink** is another variant, known for its environmental friendliness and durability. These inks are formulated with eco-friendly solvents that reduce the impact on the environment while maintaining high-quality print performance. They are often used for printing on outdoor materials due to their resistance to fading and weathering. **UV-Resistant Sublimation Ink** is specifically designed to withstand exposure to ultraviolet light, making it ideal for products that will be exposed to sunlight or UV radiation. This type of ink ensures that the colors remain vibrant and do not degrade over time, even under harsh conditions. **Metallic Sublimation Ink** adds a luxurious touch to prints by incorporating metallic pigments. These inks create reflective, shimmering effects that are particularly popular for decorative items and promotional products. **Ceramic Sublimation Ink** is optimized for printing on ceramic surfaces such as mugs, plates, and tiles. This ink is formulated to withstand the high temperatures required for curing on these substrates without losing color intensity or clarity. **Textile Sublimation Ink** is designed for use on fabric materials like polyester and polyester blends. It ensures soft, breathable prints that do not crack or peel off over time, making it perfect for apparel and home textiles. Each type of sublimation ink has its unique characteristics and benefits, making it essential to choose the right one based on the specific application and desired outcome. By understanding these differences, users can maximize the quality and longevity of their sublimation prints, ensuring professional-grade results every time. Whether you're printing on ceramics, fabrics, or metals, selecting the appropriate sublimation ink is key to achieving vibrant colors and durable finishes that meet your needs.
Applications and Uses of Sublimation Ink
Sublimation ink has revolutionized the world of printing, offering a versatile and high-quality method for creating vibrant, durable images on a wide range of materials. This innovative technology is not only limited to specific products but also extends its applications across various industries. In this article, we will delve into the diverse applications and uses of sublimation ink, starting with its ability to print on various materials. Whether it's ceramics, fabrics, metals, or plastics, sublimation ink ensures a seamless transfer of designs that are both long-lasting and visually appealing. We will also explore the common products made with sublimation ink, from personalized mugs and t-shirts to custom phone cases and decorative items. Additionally, we will examine the differences between industrial and home use of sublimation ink, highlighting the unique benefits and challenges associated with each context. By understanding these aspects, readers will gain a comprehensive insight into how sublimation ink can be effectively utilized in different settings. Let's begin by exploring how sublimation ink can be used for printing on various materials.
Printing on Various Materials
Printing on various materials is a versatile and dynamic field that has seen significant advancements, particularly with the use of sublimation ink. Sublimation ink, known for its ability to transition directly from a solid to a gas state without going through the liquid phase, offers unparalleled flexibility in terms of the range of materials it can be applied to. This unique property allows for vibrant, full-color prints that are both durable and long-lasting. One of the most common applications of sublimation printing is on ceramics and glassware. Mugs, plates, and other household items can be transformed into personalized gifts or promotional products with intricate designs and colors that are resistant to fading or chipping. The process involves coating the ceramic surface with a sublimation-friendly layer, printing the design using sublimation ink, and then heat-pressing it to ensure the ink penetrates deeply into the material. Fabric is another popular medium for sublimation printing. Polyester fabrics, in particular, are ideal because they contain the necessary polymer chains that allow the sublimation ink to bond effectively. This makes it possible to create custom apparel such as t-shirts, hoodies, and scarves with detailed graphics and patterns that do not peel off over time. The fabric retains its softness and breathability while showcasing vibrant colors that are resistant to washing and wear. Metallic surfaces also benefit from sublimation printing. Aluminum and stainless steel products like water bottles, phone cases, and keychains can be printed with high-resolution images that appear almost three-dimensional due to the reflective nature of these metals. The process typically involves applying a special coating to the metal surface before printing and heat-pressing it to ensure a durable finish. Wooden items such as coasters, cutting boards, and picture frames can also be enhanced with sublimation prints. However, these materials often require a specific coating or laminate layer to facilitate the sublimation process effectively. Once prepared, wooden surfaces can display rich colors and detailed designs that complement their natural texture. In addition to these materials, sublimation printing can be applied to various other substrates including stone, marble, and even some types of plastic. Each material requires its own set of preparations and coatings but offers unique opportunities for creative expression and customization. The versatility of sublimation printing extends beyond personal use; it has significant commercial applications as well. Businesses can leverage this technology to produce branded merchandise such as promotional items for events or corporate gifts. Artists and designers can also use sublimation printing to create unique pieces that stand out in terms of both quality and aesthetic appeal. In conclusion, printing on various materials using sublimation ink opens up a wide array of possibilities for both personal and professional applications. Its ability to produce high-quality prints on diverse substrates makes it an invaluable tool in industries ranging from advertising to artistry. Whether you're looking to create personalized gifts or mass-produce branded merchandise, sublimation ink offers a reliable solution that ensures vibrant colors and lasting durability across multiple materials.
Common Products Made with Sublimation Ink
Sublimation ink is a versatile and innovative printing medium that has revolutionized various industries by enabling the creation of high-quality, durable, and visually appealing products. One of the most significant applications of sublimation ink lies in its ability to transform ordinary items into personalized and customized goods. For instance, **ceramic mugs** are a popular product made with sublimation ink. By using a heat press, the ink is transferred onto the mug, resulting in vibrant and long-lasting designs that make for unique gifts or personal keepsakes. Similarly, **t-shirts and apparel** benefit from sublimation printing, allowing for intricate designs and patterns that do not fade quickly, making them ideal for promotional materials, event merchandise, and fashion statements. **Metallic items** such as aluminum water bottles, phone cases, and keychains are also frequently produced using sublimation ink. The process involves coating these items with a special polymer layer that reacts with the sublimation ink when heated, creating a seamless and durable finish. This method ensures that the designs remain intact even after repeated use or exposure to environmental factors. Additionally, **home decor items** like coasters, wall art, and tableware can be enhanced with sublimation printing. These products not only add a personal touch to living spaces but also serve as functional pieces that withstand daily wear and tear. In the realm of **stationery and office supplies**, sublimation ink is used to create customized notebooks, journals, and mousepads. These items are perfect for branding purposes or as personalized gifts for clients and employees. The ink's ability to produce detailed and vibrant images makes it an excellent choice for creating visually appealing stationery that stands out. Furthermore, **sports equipment** such as water bottles, athletic wear, and accessories can be customized using sublimation ink. This allows teams and athletes to personalize their gear with logos, names, and numbers in a durable and long-lasting manner. The use of sublimation ink extends into **promotional products** as well. Items like tote bags, umbrellas, and even car accessories can be printed with this ink to create eye-catching promotional materials that leave a lasting impression. The durability of sublimation prints ensures that these promotional items remain effective over time, providing continuous brand visibility. In summary, sublimation ink has opened up a wide array of possibilities for creating customized products across various sectors, from everyday household items to specialized sports gear and promotional materials. Its unique properties make it an indispensable tool for anyone looking to add a personal touch or professional branding to their products.
Industrial vs. Home Use
When it comes to the applications and uses of sublimation ink, a significant distinction lies between industrial and home use. Sublimation ink, known for its ability to transform directly from a solid to a gas state without going through the liquid phase, is versatile and can be utilized in various settings. In **industrial settings**, sublimation ink is often used on a large scale for mass production of customized products such as textiles, ceramics, and metal items. Industrial-grade sublimation printers are designed to handle high volumes and offer precise control over temperature and pressure, ensuring consistent quality. These printers are typically more robust and feature advanced technologies like automatic ink management systems and high-resolution print heads. Companies leverage sublimation ink to produce branded merchandise, promotional items, and personalized gifts efficiently. For instance, sports apparel manufacturers use sublimation to create custom jerseys with intricate designs and vibrant colors that do not fade easily. Similarly, ceramic manufacturers employ sublimation to decorate plates, mugs, and other tableware with detailed images and patterns. On the other hand, **home use** of sublimation ink has become increasingly popular with the advent of affordable and user-friendly sublimation printers. Hobbyists and small business owners can now create personalized items such as t-shirts, phone cases, and home decor items with ease. Home-based sublimation involves using smaller-scale printers that are designed for convenience and ease of use. These printers are often compact, energy-efficient, and come with user-friendly software that allows individuals to design and print their own projects. For example, craft enthusiasts use sublimation ink to create unique gifts like customized mugs, keychains, and photo blankets. Additionally, small businesses can utilize home-based sublimation setups to offer bespoke products to their customers without the need for large-scale industrial equipment. Despite these differences in scale and application, both industrial and home use of sublimation ink share common benefits such as durability and vibrant color retention. However, the choice between industrial and home use depends largely on the volume of production required and the level of precision needed. While industrial settings demand high-quality equipment capable of handling large volumes efficiently, home users can achieve professional-grade results with more accessible and affordable tools. This dual applicability underscores the versatility of sublimation ink as a medium that can cater to diverse needs across various sectors. In summary, whether it is for mass production in industrial settings or for creative projects at home, sublimation ink offers unparalleled flexibility and quality. Its ability to transform into a gas state allows for deep penetration into materials without compromising on color intensity or durability. As technology continues to evolve, we can expect even more innovative applications of sublimation ink across both industrial and home use scenarios.
Best Practices and Tips for Using Sublimation Ink
When it comes to achieving professional-grade results with sublimation ink, several key best practices and tips can make all the difference. To ensure your prints are vibrant, durable, and of the highest quality, it's essential to focus on three critical areas: choosing the right printer and paper, optimizing printing settings, and troubleshooting common issues. Each of these elements plays a crucial role in the overall success of your sublimation projects. By selecting the appropriate printer and paper, you lay the foundation for excellent print quality. Optimizing your printing settings allows you to fine-tune the process for optimal results. Finally, knowing how to troubleshoot common issues can save you time and frustration, ensuring that your projects are completed efficiently. Starting with the basics, choosing the right printer and paper is the first step towards achieving outstanding sublimation prints. This initial decision sets the stage for all subsequent steps, making it a vital component of your workflow. Therefore, it is crucial to understand the characteristics of different printers and papers to make an informed choice that aligns with your specific needs and goals.
Choosing the Right Printer and Paper
When it comes to sublimation printing, selecting the right printer and paper is crucial for achieving high-quality results. Sublimation ink requires specific conditions to transfer effectively onto materials like ceramics, fabrics, and metals, making the choice of printer and paper paramount. First, consider the type of printer you need. Sublimation printing typically involves using an inkjet printer designed for this purpose. Look for printers that are compatible with sublimation ink cartridges or those that can be converted to use sublimation inks. Epson printers are often popular choices due to their compatibility and reliability in this context. Ensure the printer has a high resolution (at least 1440 dpi) to produce detailed and vibrant prints. Next, focus on the paper quality. Sublimation paper, also known as heat transfer paper, is specially coated to handle the sublimation process. This paper must be able to withstand high temperatures without degrading or discoloring. Opt for papers with a smooth finish and a weight of around 100-120 gsm for optimal results. The coating on the paper should be even and consistent to ensure uniform ink absorption and transfer. Another critical factor is the size of the paper. Choose papers that match your printer's capabilities and the size of your projects. Standard sizes like A4 and A3 are common, but larger formats may be necessary for bigger projects such as banners or large fabric prints. In addition to these technical considerations, it's important to consider the environmental impact of your choices. Look for eco-friendly options in both printers and papers where possible. Some manufacturers offer recycled or biodegradable sublimation papers that can help reduce your carbon footprint without compromising on quality. Finally, always follow the manufacturer's guidelines for both the printer and the paper to ensure optimal performance. This includes using the correct settings on your printer, such as the right temperature and pressure settings during the heat transfer process, and handling the paper carefully to avoid creases or damage. By carefully selecting a compatible printer and high-quality sublimation paper, you can significantly enhance the outcome of your sublimation projects. This attention to detail will help you achieve vibrant colors, sharp images, and durable transfers that meet your expectations and satisfy your clients if you're working professionally. Remember that investing in the right tools from the outset can save time and resources in the long run by reducing errors and improving overall quality.
Optimizing Printing Settings
Optimizing printing settings is a crucial step in achieving high-quality results when using sublimation ink. To ensure vibrant, durable prints, it's essential to fine-tune your printer settings according to the specific requirements of sublimation printing. Start by selecting the appropriate paper type and quality; sublimation paper is designed to handle the unique properties of sublimation ink, so using it is paramount. Adjust the print resolution to a higher setting, typically 300 DPI or higher, to capture detailed images and text. Next, configure your color management settings. Sublimation ink often requires custom color profiles to accurately translate digital colors into physical prints. Utilize ICC profiles provided by your ink and paper manufacturers or create your own through calibration processes. This step ensures that the colors you see on your screen are accurately represented on the final product. Ink density and saturation levels also play a significant role. Increase the ink density to compensate for the sublimation process, which can sometimes result in lighter colors. However, be cautious not to over-saturate, as this can lead to bleeding or poor image clarity. Additionally, consider using a "mirror" or "reverse" print setting if you're printing on materials that will be viewed from the opposite side, such as mugs or t-shirts. Temperature and pressure settings during the heat press process are equally important. Ensure your heat press is set to the recommended temperature (usually between 380°F to 400°F) and pressure for the specific material you're working with. The duration of the heat press cycle should also be optimized; typically, this ranges from 2 to 4 minutes depending on the material's thickness and type. Finally, maintain consistent environmental conditions in your workspace. Humidity and temperature fluctuations can affect both the printing and heat pressing processes, leading to inconsistent results. Regularly clean and maintain your printer to prevent clogs and ensure that each print meets your quality standards. By meticulously optimizing these printing settings, you can significantly enhance the quality and longevity of your sublimation prints. This attention to detail not only improves the aesthetic appeal but also ensures that your products withstand wear and tear over time, making them more durable and customer-friendly. Following these best practices will help you unlock the full potential of sublimation ink and produce professional-grade prints that exceed expectations.
Troubleshooting Common Issues
When working with sublimation ink, encountering common issues is not uncommon, but knowing how to troubleshoot them can significantly enhance your productivity and quality of output. One of the most frequent problems is **ghosting or shadowing**, which occurs when the image appears faint or has a ghostly outline. To address this, ensure that your printer settings are optimized for sublimation ink, and that the paper is aligned correctly. Additionally, check if the ink levels are adequate and if the print head is clean; clogged nozzles can lead to uneven ink distribution. Another common issue is **color shifting**, where the colors of the final product do not match the original design. This can be due to incorrect temperature settings during the sublimation process. Ensure that your heat press is set to the recommended temperature (usually between 380°F to 400°F) and that the pressure is evenly distributed. Also, verify that you are using the correct type of sublimation paper and ink, as some materials may react differently under heat. **Fading or discoloration** after sublimation is another challenge. This often happens if the substrate material is not suitable for sublimation or if it has been treated with chemicals that interfere with the ink. Always use materials specifically designed for sublimation, such as polyester fabrics or ceramic tiles, and ensure they are free from any chemical treatments. **Ink bleeding** can also occur, especially on fabrics, resulting in blurry edges and loss of detail. To prevent this, use a high-quality sublimation paper that absorbs ink well without causing it to spread excessively. Additionally, adjust your printer settings to reduce ink flow if necessary. **Peeling or flaking** of the sublimated image can happen if the substrate material does not bond well with the ink. This could be due to insufficient heat or pressure during the sublimation process. Ensure your heat press is functioning correctly and that you are applying enough pressure for the recommended duration. Finally, **clogged print heads** can disrupt your workflow significantly. Regularly clean your print heads using a cleaning solution specifically designed for sublimation ink printers. Running a cleaning cycle on your printer periodically can also help maintain its performance. By understanding these common issues and knowing how to troubleshoot them effectively, you can significantly improve your results when working with sublimation ink. Following best practices such as using high-quality materials, optimizing printer settings, and maintaining your equipment will help you achieve vibrant and durable prints consistently. This not only saves time but also enhances the overall quality of your work, making it more professional and appealing to clients or end-users.