What Are Bowling Balls Made Of

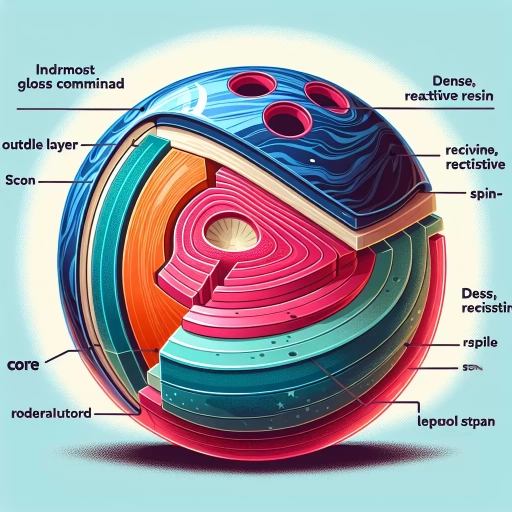
Materials Used in Bowling Ball Construction
Bowling, pastime turned professional sport, employs intricate engineering, especially during the construction of its core equipment - the bowling ball. Today's bowling balls are a far cry from the wooden balls of old. Engineered to influence the game dynamically, they leverage various high-grade materials in their construction. These include urethane and reactive resins, particle composite materials, and plastic or polyester. The choice of material not only affects the appearance but also significantly impacts the ball’s performance, including its trajectory and impact on the pins. The first, urethane and reactive resin, are quintessential elements in high-performance bowling balls. These materials enhance the hook potential of the ball, thereby aiding in accurate strikes. Incorporating such substances leads to a more durable and resilient ball, enabling bowlers to exert additional force without causing damage. We will now delve deeper into these materials, starting with the role and influence of urethane and reactive resin in bowling ball construction.
1. Urethane and Reactive Resin
Urethane and reactive resin make up two critical categories of materials used in bowling ball construction, vastly contributing to the ball's performance on the lane. First introduced in the early 1980s, urethane was a significant breakthrough from the previously used plastic or rubber materials, revolutionizing the whole bowling sport. Urethane bowling balls provide a perfect balance between durability and controllability. They exhibit enhanced hook potential due to their ability to grip the bowling lane, a critical requirement for bowlers looking to make controlled, accurate shots. These balls have a higher friction level, enabling a strong curve as they descend the lane, requiring a skilled technique to ensure their successful use. On the other end of the spectrum, reactive resin—a further development of urethane—serves as the material of choice for professional and experienced bowlers due to its high reactivity on the lanes. The particles in the reactive resin react to the friction from the bowling lane, initiating a sharp hook that can assist in a higher strike probability. The motion that reactive resin balls can achieve is unmatched. Moreover, these balls can absorb oil on the bowling lanes, reducing the friction and thus, allowing the aggressive hook. However, such bowling balls require proper care and maintenance as their porosity may cause them to absorb dirt or become saturated with lane oil, which can potentially affect their performance. As such, reactive resin and urethane materials in bowling balls not only highlight the evolution of the sport but also play a crucial role in deciding the outcome of a given match. Formats like urethane and reactive resin illustrate how material science can transform an activity, providing players with greater control and influence in their game. In the intricate world of bowling, the right selection of materials in ball construction makes all the difference.
2. Particle Composite Materials
Particle composite materials are a prominent component in the fabrication of bowling balls, holding immense relevance in the sport. At the molecular level, bowling balls are a composite material of two primary parts: the core, made of high-density minerals, and the coverstock, built of plastic or urethane, sometimes even reactive resin. This intricate balance of different materials is all to ensure that the bowling balls are robust, durable, and maintain an effective reaction on the diverse range of bowling lane surfaces. Particle composites in bowling balls, specifically regarding the coverstock, are the unsung heroes that dramatically alter the ball's performance. The particle composite coverstock plays a role not frequently recognized: influencing the friction between the ball and the lane. This could greatly impact a bowler's performance. The properties of the composite particles offer the sought-after blend of robustness and friction control. Furthermore, they increase the ball's versatility, allowing it to be effective on numerous lane conditions. The coverstock's composition varies dramatically from ball to ball; for instance, plastic balls have a smoother finish and less friction, ideal for beginners. In contrast, particle composite balls have a textured finish and more hook potential, perfect for advanced players seeking an aggressive bowl. Originally, bowling balls were made of hard rubber. Subsequently, advancements in materials science led to the introduction of balls made from urethane, the reactive resin, and eventually, to particle composite materials. Particle composite bowling balls are unique in that they include small glass or ceramic particles embedded within the coverstock. These additional particles significantly increase the ball's traction on the lane, offering superior hook potential. They are very gritty and can grasp the lane surface better than regular urethane or reactive resin coverstocks. This ability places them in high demand among professional bowlers, for whom precision and control are paramount. In terms of creating the core, the particle composite materials used are loaded with high-density materials such as barium or iron. The properties of these particles determine the ball's spin radius and hook potential. A dense core material results in a high overall ball weight, which directly influences the ball's momentum and hitting power, leading to a higher pin knockdown potential. The wise use of particle composite materials in manufacturing has radically evolved the sport—the bowling ball's components now significantly dictate how the game is played and strategized. Therefore, understanding particle composite materials' role in bowling ball construction is crucial. They have revolutionized the bowling industry by enabling the creation of balls with varying performances to suit different players' skill levels and styles. These materials have not just enhanced the look and feel of the bowling balls but also made a significant impact on how the game is played worldwide. With the continuous development in materials technology, it is exciting to anticipate what could be in store for the future of bowling balls and the sport as a whole. Single-handedly, the particle composite revolution has amplified skill expression in bowling's nuanced world.
3. Plastic and Polyester
Bowling balls constructed from plastic and polyester are prevalent, particularly among novice bowlers due to their affordability and durability. Plastic is one of the most basic materials used in the construction of bowling balls. It provides a comfortable grip and is ideal for straight shots. The polyester variant, on the other hand, is akin to an upgraded version of plastic balls, providing better velocity and accuracy on the bowling lane. Interestingly, polyester was among the first materials utilized in developing the exterior shell of bowling balls. Its widespread acceptance was primarily due to its improved resilience and ability to maintain a straight path while bowling, compared to its wooden and rubber counterparts. Additionally, polyester bowling balls exhibited a smoother and polished exterior, ensuring less friction with the lane and hence, escalated speed. It is the perfect choice for hitting spares due to its tendency to resist hooking or curving. Importantly, both plastic and polyester balls are lighter, which reduces the risk of potential strain on the bowler's arms while throwing. With improved lane coverage and a boosted strike probability, polyester balls, in particular, are suitable for bowlers spanning different skill levels. However, seasoned players may prefer balls crafted from resin or urethane for their superior control and spin capacity. Overall, plastic and polyester bowling balls, with their inherent qualities of durability, affordability, and control, continue to earn a well-deserved spot in the world of bowling.
Manufacturing Process of Bowling Balls
Manufacturing a bowling ball is not just about casting a resourceful sphere that can strike pins on a bowling alley; it's about fusing science, technology, and engineering. The article precisely dissects this sophisticated process of bowling ball production into three cardinal phases: Core Creation and Design, Coverstock Application and Finishing, and Quality Control and Testing. First off, 'Core Creation and Design' details how the heart of the bowling ball, the core, is meticulously designed to influence the ball’s movement and spin. The manufacturing process begins here, where engineers, with the assistance of computer software, develop various core shapes for different bowling ball styles. As we transit from core configuration to the actual sphere formation, 'Coverstock Application and Finishing' elucidates how the ball's outer shell, known as the coverstock, is applied over the core, granting the ball its desired hardness, friction, and aesthetics. Finally, 'Quality Control and Testing' stresses on the rigorous quality assurance testing each ball undergoes to ensure its performance, durability, and conformity to regulatory standards. Now, let's delve into the first phase of the manufacturing process, 'Core Creation and Design.'
1. Core Creation and Design
A crucial phase in the manufacturing process of bowling balls is the core creation and design stage. This element determines the ball’s performance dynamics as it greatly influences the ball's motion on the lane. Initially, cores were made of dense and weighty material to achieve a high spinning insensitivity. However, over time, the evolution of bowling ball technology has introduced cores of different shapes; from symmetrical, like spheres or cylinders, to asymmetrical designs like lightbulbs or elliptical shapes, carefully designed using computer-aided design (CAD) software. The materials used to make the core are usually high-density materials like a blend of polyester and barium (for the outer layer) and a blend of calcium carbonate and phenolic resin for the inner layer. The blending results in a higher density core. With these variety cores structure, they introduce variable dynamics which allowing bowler to select ideal performance characteristics suitable for their style and bowling conditions. The process of developing the core begins with the crafting of mold pattern pieces. Next, a polyester resin is prepared before being poured into the mold. After a curing process, the core is released from the mold, inspected for quality, and then sent for further processing. The materials used, combined with the design of the core, determine the overall balance of the ball, its spin rate, hook potential, and the trajectory. Therefore, core creation and design is an intricate and important process in the manufacturing of bowling balls. It must be carried out with precision to ensure the ball performs to its maximum potential on the bowling lane.
2. Coverstock Application and Finishing
In the manufacturing process of bowling balls, the application of the coverstock, and its subsequent finishing process, both play pivotal roles in determining the overall performance of the ball on the bowling lane. Starting with the coverstock application, this is the external layer of the bowling ball, typically made of plastic, urethane, reactive resin, or particle (proactive). Notably, the coverstock composes most of the ball's total weight and profoundly influences its reaction on the lane. The precise composition of this outer shell depends on the kind of performance required from the ball—for example, while plastic coverstocks provide excellent control, they offer limited hook potential, making them ideal for beginners. In contrast, reactive resin or proactive coverstocks generate a high hook potential and rapid backend reaction, making them suitable for experienced bowlers aiming for strikes. Once the coverstock is applied, the bowling ball enters the finishing phase, significantly impacting the bowling ball's movement on the lane. The finish of the ball can range from 'dull' to 'shiny,' each delivering unique trajectories and reactions when in contact with the bowling lane. For instance, a glossy finish will allow the ball to 'skid' more on the lane surface, delaying the ball's hook and providing a vigorous backend reaction. On the other hand, a dull finish increases the ball's traction, resulting in an earlier hook and smoother path to the pins. While the coverstock and finish may seem minimal aspects in the grand scheme of bowling ball manufacturing, their application requires precision and expertise. Differing from ball to ball, the specific type of coverstock and its exact finish can result in an array of ball movements on the lane, making this phase of production incredibly significant. After the coverstock application and finishing, the ball is thoroughly checked for any surface irregularities before it’s moved to the subsequent phases of the manufacturing process. Moreover, it's essential to note the varying regulations in professional bowling concerning ball specifications, especially the coverstock's hardness and surface roughness. Consequently, manufacturers must adhere to these regulations during the application and finishing phases, ensuring that all produced bowling balls meet the acceptable standards. Thus, the application of the coverstock and the finishing process are not only instrumental in a bowling ball's final performance but also relevant in ensuring credibility, integrity, and fairness within the sport of bowling.
3. Quality Control and Testing
Quality control and testing are crucial aspects in the manufacturing process of bowling balls, ensuring customers receive a durable and reliable product. The third stage in the process, it involves a series of multifaceted tests to guarantee the overall quality, integrity, weight, and balance of the bowling balls. The integrity of a bowling ball's internal components is vital - any flaw or variation can drastically affect the ball's motion and player's performance. Thus, manufacturers employ X-ray technology to capture images of the ball's interior. The method offers a non-destructive means of inspecting the core, the filler material, and the overall ball structure for any inconsistencies or deformities. If any discrepancies are found, the ball is rejected to maintain the high standard of quality. Next, the bowling balls undergo weight and balance measurements. These factors play a pivotal role in how the ball will perform. They determine the ball’s hook potential and the player’s control over it. The ball's overall weight is checked and measured initially, but the focus quickly switches to the ball's balance. A carefully calibrated scale tests for static imbalance. If imbalance is determined beyond acceptable standards, the product doesn’t proceed to the next stage and is deemed defective. The final quality control tests involve the ball's outer shell or coverstock. A ball's interaction with the lane's surface greatly influences its performance. Therefore, rigorous testing of the ball's hardness, friction, and durability is employed. Hardness testing ensures the ball meets the industry standards for hardness, which contributes to the ball's durability and impacts its throwing characteristics. Meanwhile, friction testing ensures the ball will react appropriately when rolling down a bowling lane, influencing the manner it hooks or skids. The manufacturers also conduct durability tests designed to simulate the wear and tear of repeated bowling impacts. These include drop tests and survival in varying temperature conditions to guarantee their resilience. In conclusion, the quality control and testing stage is an indispensable part of the bowling ball manufacturing process. It guarantees not only the optimal performance of a bowling ball but also its compliance with industry-set standards and ordinances. This stringent quality control not only helps in maintaining the high grade of bowling balls but also preserves the credibility and reputation of manufacturers in the highly competitive market of bowling equipment.
Technological Advancements in Bowling Ball Materials
The surge of innovation has transformed sports, and bowling is firmly in this advanced realm. The usage of the latest technology has redefined the sphere, particularly the constitution of bowling balls. Not so long ago, bowling balls were merely made from rubber and then polyester. However, the quest for better performance and pinpoint precision led to a revolution in the bowling ball industry, leveraging new technology and materials. Firstly, scientists have crossed into the realm of nanotechnology to enhance the coverstocks of bowling balls, resulting in an incredible leap in performance. Secondly, advancements in core designs have been a game-changer, providing enhanced ball motion, and therefore improved accuracy. Finally, in our rapidly changing world, the eco-conscious have not been left behind, sparking innovation around eco-friendly and sustainable materials for bowling balls. As we delve into these technological advancements, we must first explore the ever-innovative realm of nanotechnology in coverstocks, an intricate science that's changing the face of bowling forever.
1. Nanotechnology in Coverstocks
The introduction of nanotechnology into the sport of bowling, particularly in the design of coverstocks, signals a revolutionary step forward in bowling ball materials. The technology involves manipulating molecular and atomic structures to gain precise control over the traits of substances. Ultra-durable nanomaterials, designed with complex nano-scale structures, have allowed for the creation of superior coverstocks that have brought a dynamic new level of performance to the bowling arena. As one of the key considerations for bowling ball performance, the coverstock plays a critical role in the interaction between the ball and the bowling lane. The novel use of nanotechnology in coverstock design has transformed the sport, boosting performance levels by expanding the possibilities for friction control. Introducing nanocomposite materials to the coverstock promotes superior hook potential, effectively refining the ball’s traction in the oil on the lanes. This increased traction greatly enhances performance by heightening the angle and predictability of the ball's reaction to the changing conditions of the lane. Moreover, the durability of nanotechnology-made coverstocks ensures greater longevity in competitive play. Traditionally, coverstocks, especially the reactive resin ones, tended to wear relatively quickly, with their performance degrading over time. Conversely, the integration of nanotechnology has resulted in coverstocks that retain their peak performance characteristics longer, providing players with a reliable ball that stands up to extensive use without loss of effectiveness. The innovative integration of nanotechnology is not only limited to boosting performance but also extends to enhancing the aesthetic appeal of bowling balls. It provides manufacturers the ability to create vibrant, striking colors and patterns, by controlling the structural composition of the coverstock at a nanoscopic level. This makes the bowling ball not only a tool in the sport but also a persona of the player, adding an extra dimension of personalization to the game. In conclusion, as a revolutionary force shaping the advancement in bowling ball materials, nanotechnology has transformed coverstocks. It's an invaluable asset that significantly enhances performance while also offering wear resistance and decorative benefits. Its integration assures a brighter, more intricately-tuned future for the sport of bowling. Whether you're a professional athlete or a beginner, the impact of nanotechnology in terms of performance and aesthetics is undeniable in the world of bowling. The evolution of coverstock materials through nanotechnology is just the beginning, and we can expect to see more groundbreaking improvements to the game as technology continues to advance. With bowling ball manufacturers investing more and more in this technology, the future definitely promises an interesting and exciting dive into the nano-world.
2. Advanced Core Designs for Better Performance
2. Advanced Core Designs for Better Performance
Despite the common belief that the exterior material is everything for a bowling ball, the core plays an equally substantial role. Technological advancements have allowed for a more sophisticated and advanced core designs, greatly impacting the ball's performance. Initially, cores were simple in design, often spherical or pancake-style, but with the advent of technology, engineers have embraced complex and advanced computer-aided designs. This leap has paved the way for innovative core configurations such as asymmetrical, symmetrical, and dynamic cores, each one providing a distinctive reaction on the lanes. Asymmetrical cores, characterized by an uneven distribution of mass, promote an aggressive, early hook ability—the ball's change of direction towards the pocket. Whereas, symmetrical cores, with equal mass distribution, advocate for a smoother, predictable performance on the alley. As a recent invention, dynamic cores up the ante even further. They focus on enhancing the ball’s hitting power by absorbing less kinetic energy during the collision, which results in more energy directed towards pin action. Of course, it’s not any one factor that determines the effectiveness of these cores. The core material, its density, and the type of coverstock wrapped around it also play vital parts in dictating the ball's overall performance. Typically, the core is composed of dense materials like ceramic, resin, or polymer. These materials are high in density, which allows the ball to store a significant amount of potential energy that translates into powerful strikes. Moreover, modern bowling ball technology allows the core's position to be manipulated within the ball to affect its performance. These are known as ‘mass bias’ balls. The off-set core position can provide bowlers with numerous hook potential and reaction possibilities based on small changes in drilling angle, thus offering a higher degree of customization based on a player’s unique style and bowling lane conditions. The innovation doesn't just stop at the core designs; advancements in core material research can potentially provide a whole new level of ball performance. The combination of sophisticated core designs and superior materials is placing unprecedented control in the hands of bowlers, resulting in higher scores and enhanced playing experience. The pursuit for the perfect bowling ball will continue pushing the technological boundaries, as engineers strive for cores that offer greater hook potentials, angular motions, and pin actions while preserving energy and ensuring stability. In the bowling world, the amalgamation of these technological advancements directly correlates to an improved performance. Hence, the pivot towards advanced core designs parallels the attempts to push the limits of the sports, enhancing overall accuracy, precision and tenacity on the lanes to make bowling experience truly exceptional.3. Eco-Friendly and Sustainable Materials
3. Eco-Friendly and Sustainable Materials An important attribute of the present development in bowling ball materials is a shift towards eco-friendly and sustainable materials. With growing concerns surrounding environmental sustainability, the bowling industry is not immune to this global demand. Therefore, the need for environmentally friendly and sustainable bowling ball materials cannot be overstated. Advancements in technology have paved the way for the manufacturing of bowling balls using recycled and bio-degradable materials, reducing their ecological footprints significantly. These technological strides show great promise in protecting our environment while not compromising the quality and functionality of the balls. For instance, recycled plastics and rubbers are being used in the production of some bowling balls. These materials are ground to a fine powder, heated to a precise temperature, and then press-molded into the spherical shape of a bowling ball. The use of these recycled materials helps reduce waste production and lowers the demand for raw material exploitation, thus fostering sustainability. Additionally, biodegradable materials are being used to manufacture the coverstock of the bowling balls. These materials can decompose naturally and efficiently in the environment, reducing landfill problems associated with non-degradable bowling balls. Another game-changing innovation in the realm of eco-friendly and sustainable materials is the use of plant-based resins. This cutting-edge development presents an environmentally conscious alternative to traditional petroleum-based resins, thus lessening the environmental impacts associated with the production of bowling balls. Furthermore, certain bowling ball companies are exploring the use of bio-based polyurethanes, derived from renewable resources such as plant oils. Unlike traditional polyurethane, bio-based polyurethanes generate fewer greenhouse gases during production and are more energy-efficient. Such advancements mark a significant step towards reduced carbon footprint and greater sustainability. These progressive advancements resonate well with the green consumerism movement, appealing to environmentally conscious bowlers while contributing positively to global sustainability efforts. Such shifts towards greener practices not only ensure the longevity of the sport but also act as a driving force for sustainable development in other industries. The emphasis on using eco-friendly and sustainable materials signifies that the bowling industry cares about its impact on the environment and is determined to make a positive change. Thus, it can be said that technology is playing a crucial role in bridging the gap between bowling and sustainability.