What Is Pressure Measured In

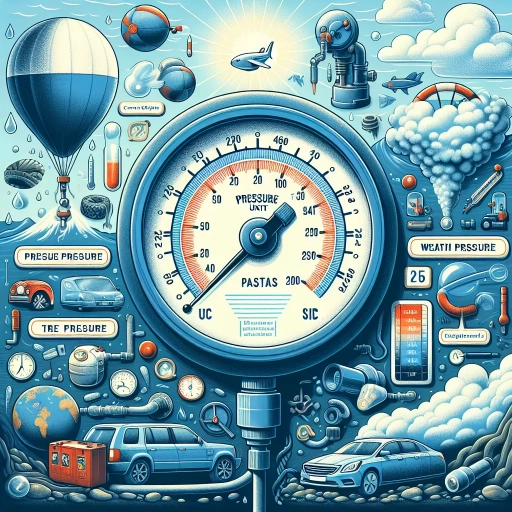
Pressure, a fundamental physical quantity, is a measure of the force exerted per unit area on an object or surface. It is a critical parameter in various fields, including science, engineering, and everyday life. Understanding pressure and its measurement is essential for numerous applications, from monitoring weather patterns to ensuring the safety and efficiency of industrial processes. This article delves into the multifaceted world of pressure measurement, starting with an exploration of the different units used to quantify pressure. We will examine the various scientific and industrial applications where accurate pressure measurement is crucial, highlighting its role in fields such as meteorology, aerospace, and manufacturing. Additionally, we will discuss the tools and techniques employed to measure pressure, ranging from simple barometers to sophisticated electronic sensors. By grasping these concepts, readers will gain a comprehensive understanding of how pressure is measured and its significance across diverse disciplines. Let us begin by exploring the foundational aspect of pressure measurement: **Understanding Pressure Units**.
Understanding Pressure Units
Understanding pressure units is crucial for a wide range of applications, from engineering and physics to everyday life. Pressure, a fundamental physical quantity, is measured in various units that can sometimes be confusing without a clear understanding. This article aims to demystify the concept of pressure units by delving into three key areas: the definition of pressure units, common pressure units in everyday use, and the process of converting between different units. First, we will explore the **definition of pressure units**, which lays the groundwork for understanding how pressure is quantified. This foundational knowledge is essential for grasping the nuances of different measurement systems. Next, we will examine **common pressure units in everyday use**, highlighting how these units are applied in various contexts such as weather forecasting, automotive maintenance, and medical diagnostics. Finally, we will discuss **conversion between different units**, providing practical insights and tools for seamlessly transitioning between different measurement systems. By understanding these aspects, readers will gain a comprehensive appreciation of pressure units and their practical applications. Let's begin by defining what pressure units are and how they are established.
1. Definition of Pressure Units
Pressure, a fundamental physical quantity, is measured in various units that help quantify the force exerted per unit area on an object. Understanding these units is crucial for accurate calculations and applications across different fields such as engineering, physics, and meteorology. The most commonly used pressure units include **Pascals (Pa)**, **Atmospheres (atm)**, **Bars**, **Pounds per Square Inch (PSI)**, and **Millimeters of Mercury (mmHg)**. **Pascals (Pa)** are the standard unit of pressure in the International System of Units (SI). One Pascal is defined as one Newton per square meter, making it a versatile and precise unit for scientific and technical applications. For instance, atmospheric pressure at sea level is approximately 101,325 Pascals. **Atmospheres (atm)** are another widely recognized unit, with one atmosphere being the standard atmospheric pressure at sea level. This unit is often used in chemistry and physics to describe the pressure of gases. It is equivalent to 101,325 Pascals or 760 mmHg. The **Bar** is a metric unit that is close to atmospheric pressure; one Bar equals 100,000 Pascals or 0.987 atm. This unit is commonly used in meteorology to measure atmospheric pressure and in engineering for fluid dynamics. In the United States, **Pounds per Square Inch (PSI)** is a prevalent unit for measuring pressure. One PSI is equal to 6,894.76 Pascals. This unit is frequently used in automotive and industrial contexts, such as tire pressure and hydraulic systems. **Millimeters of Mercury (mmHg)**, also known as torr, is a unit derived from the height of a mercury column that exerts a given pressure. One mmHg is equivalent to 1 torr and equals 133.322 Pascals. This unit is traditionally used in medicine to measure blood pressure and in scientific research involving gases. Each of these units has its specific applications and advantages. For example, Pascals offer precision and consistency across scientific disciplines, while PSI is more intuitive for everyday applications in the United States. Understanding these different units allows for seamless conversion between them, ensuring accuracy and clarity in various fields where pressure measurements are critical. In summary, the diversity of pressure units reflects the broad range of contexts in which pressure is measured and applied. From the precise scientific measurements in Pascals to the practical uses of PSI and mmHg, each unit plays a vital role in ensuring that pressure is accurately quantified and communicated. This understanding is essential for both theoretical calculations and real-world applications, making it a cornerstone of scientific and engineering practices.
2. Common Pressure Units in Everyday Use
In everyday life, understanding common pressure units is crucial for a variety of applications, from monitoring weather conditions to ensuring the safety of industrial processes. Two of the most frequently encountered pressure units are **Pounds per Square Inch (PSI)** and **Pascals (Pa)**. **Pounds per Square Inch (PSI)** is a widely used unit in the United States and other countries that follow the Imperial system. It measures pressure as the force exerted by one pound on an area of one square inch. PSI is commonly seen in automotive and industrial contexts, such as tire pressure gauges, hydraulic systems, and pneumatic tools. For instance, car tires are typically inflated to pressures ranging from 30 to 40 PSI, while industrial hydraulic systems can operate at much higher pressures, often exceeding 1,000 PSI. The familiarity and practicality of PSI make it a staple in many daily applications. On the other hand, **Pascals (Pa)** is the standard unit of pressure in the International System of Units (SI). It is defined as one newton per square meter. Pascals are more commonly used in scientific and technical fields where precision is paramount. For example, atmospheric pressure at sea level is approximately 101,325 Pascals, which is often rounded to 100,000 Pa for simplicity. In engineering and physics, Pascals are preferred due to their direct relationship with other SI units, facilitating calculations and conversions. Additionally, Pascals are used in meteorology to measure atmospheric pressure changes that influence weather patterns. The distinction between these units highlights their respective domains of use. While PSI is more intuitive for everyday tasks due to its widespread adoption in consumer products, Pascals offer a more precise and consistent framework for scientific and technical applications. Understanding both units allows individuals to navigate different contexts effectively, whether it's checking tire pressure or analyzing complex engineering data. Moreover, knowing how to convert between these units can be highly beneficial. For instance, converting PSI to Pascals involves multiplying the PSI value by 6894.76 (since 1 PSI is approximately equal to 6894.76 Pascals). This conversion capability enhances flexibility and ensures that measurements can be communicated accurately across different systems. In summary, PSI and Pascals are two fundamental pressure units that serve distinct purposes in our daily lives. PSI's practicality makes it a favorite in consumer and industrial settings, while Pascals' precision makes them indispensable in scientific and technical fields. By grasping these units and their applications, individuals can better understand and interact with the world around them, from the simplest household tasks to complex scientific endeavors. This dual understanding not only enriches our appreciation of pressure but also equips us with the knowledge needed to navigate various real-world scenarios effectively.
3. Conversion Between Different Units
When delving into the realm of pressure measurement, understanding the conversion between different units is crucial for accurate and meaningful comparisons. Pressure, a fundamental physical quantity, can be expressed in various units depending on the context and geographical location. The most common units include Pascals (Pa), millimeters of mercury (mmHg), pounds per square inch (psi), and atmospheres (atm). To convert between these units, one must grasp the underlying relationships. For instance, 1 atmosphere is equivalent to 101,325 Pascals, which in turn is equal to 760 millimeters of mercury or approximately 14.7 pounds per square inch. These conversions are essential in various fields such as engineering, medicine, and meteorology. In engineering, converting psi to Pa can help in designing systems that operate under specific pressure conditions. In medicine, understanding the conversion from mmHg to Pa is vital for interpreting blood pressure readings accurately. The process of conversion involves simple arithmetic operations. For example, to convert psi to Pa, one multiplies the psi value by 6894.76 since 1 psi equals 6894.76 Pascals. Conversely, to convert Pa to psi, you divide the Pa value by 6894.76. Similarly, converting between mmHg and Pa involves knowing that 1 mmHg is approximately 133.322 Pascals. Understanding these conversions not only enhances technical communication but also ensures safety and precision in applications where pressure plays a critical role. For instance, in aviation and aerospace engineering, accurate pressure readings are vital for maintaining aircraft performance and safety. Misinterpretation or incorrect conversion could lead to catastrophic consequences. Moreover, familiarity with multiple units allows for a broader understanding of historical and cultural contexts. Different regions have traditionally used different units for pressure measurement; knowing these equivalencies facilitates cross-cultural and interdisciplinary collaboration. For example, while the metric system (Pascals) is widely used in scientific research globally, psi remains common in many industrial applications in the United States. In conclusion, mastering the conversion between different pressure units is a fundamental skill that bridges theoretical knowledge with practical application. It ensures that measurements are accurately interpreted and communicated across diverse fields and geographical boundaries. Whether you are an engineer designing high-pressure systems or a healthcare professional monitoring patient vital signs, understanding these conversions is indispensable for precision and reliability in your work. By grasping these relationships, you can navigate the complex landscape of pressure measurement with confidence and accuracy.
Scientific and Industrial Applications of Pressure Measurement
Pressure measurement is a fundamental aspect of various scientific and industrial fields, playing a crucial role in understanding and controlling processes across diverse disciplines. This article delves into the multifaceted applications of pressure measurement, highlighting its significance in physics and chemistry, industrial operations, and medical practices. In physics and chemistry, precise pressure measurements are essential for studying thermodynamic properties, chemical reactions, and material behavior under different conditions. Industrial uses of pressure measurement are equally vital, as they ensure the safe and efficient operation of machinery, pipelines, and manufacturing processes. Additionally, in medical contexts, accurate blood pressure measurement is critical for diagnosing and managing cardiovascular health. By exploring these three key areas—pressure measurement in physics and chemistry, industrial uses of pressure measurement, and medical applications of blood pressure measurement—we gain a comprehensive understanding of how this fundamental principle underpins many of our technological advancements and health monitoring systems. Let us begin by examining the role of pressure measurement in physics and chemistry, where its impact is particularly pronounced.
1. Pressure Measurement in Physics and Chemistry
Pressure measurement is a fundamental concept in both physics and chemistry, playing a crucial role in understanding various phenomena and processes across these disciplines. In physics, pressure is defined as the force exerted per unit area on an object or surface, typically measured in units such as pascals (Pa) or pounds per square inch (psi). This measurement is essential for studying fluid dynamics, where it helps in understanding the behavior of gases and liquids under different conditions. For instance, in hydrostatics, pressure measurements are used to determine the depth of fluids and the forces acting on submerged objects. In aerodynamics, pressure sensors are critical for assessing air resistance and lift forces on aircraft and vehicles. In chemistry, pressure measurement is vital for understanding chemical reactions and the properties of substances. The ideal gas law, \(PV = nRT\), where \(P\) is pressure, \(V\) is volume, \(n\) is the number of moles of gas, \(R\) is the gas constant, and \(T\) is temperature, relies heavily on accurate pressure measurements to predict the behavior of gases. This law is foundational in understanding many chemical processes, including those in industrial settings such as chemical synthesis and separation techniques. Additionally, pressure measurements are crucial in high-pressure chemistry experiments where reactions occur under extreme conditions, often leading to the discovery of new materials and compounds. The scientific applications of pressure measurement extend beyond these basic principles. In materials science, high-pressure experiments are used to study the properties of materials under extreme conditions, which can reveal insights into their structural and electronic properties. For example, diamond anvil cells are used to create ultra-high pressures that allow scientists to study the behavior of materials at pressures that mimic those found deep within the Earth's mantle. In environmental science, pressure sensors are used to monitor atmospheric pressure changes, which are important for weather forecasting and understanding climate patterns. Industrial applications of pressure measurement are equally significant. In the oil and gas industry, accurate pressure measurements are critical for drilling operations and reservoir management. Pressure sensors help in monitoring wellbore pressure to ensure safe and efficient extraction of hydrocarbons. In manufacturing processes, pressure gauges are used to control and monitor the performance of machinery and equipment, such as pumps, compressors, and hydraulic systems. In aerospace engineering, precise pressure measurements are essential for ensuring the integrity of aircraft systems, including fuel tanks and hydraulic lines. Furthermore, advancements in technology have led to the development of sophisticated pressure measurement tools. Modern pressure sensors, such as piezoelectric sensors and capacitive sensors, offer high accuracy and reliability. These sensors are integrated into various industrial control systems, enabling real-time monitoring and automation. The integration of IoT (Internet of Things) technology with pressure measurement devices has further enhanced their utility by allowing remote monitoring and data analytics, which can significantly improve operational efficiency and safety. In conclusion, pressure measurement is a cornerstone of both physics and chemistry, with far-reaching implications across scientific research and industrial applications. Its importance spans from fundamental understanding of physical laws to critical industrial processes, highlighting the necessity of precise and reliable pressure measurement techniques in advancing our knowledge and technological capabilities.
2. Industrial Uses of Pressure Measurement
Pressure measurement plays a pivotal role in various industrial sectors, where precise monitoring and control are crucial for safety, efficiency, and product quality. In the **petroleum and gas industry**, pressure measurement is essential for drilling, extraction, and transportation processes. Drilling operations rely on accurate pressure readings to ensure the stability of the wellbore and prevent blowouts, which can be catastrophic. During extraction, pressure sensors monitor the flow rates and pressures within pipelines to optimize production and detect any anomalies that could indicate leaks or blockages. Additionally, in refining processes, pressure measurements help control the conditions under which crude oil is processed into various petroleum products, ensuring that the chemical reactions occur within safe and optimal parameters. In **chemical processing**, pressure measurement is vital for maintaining the integrity of reactors and other equipment. Chemical reactions often involve high pressures and temperatures, and any deviation from the set parameters can lead to unsafe conditions or reduced product quality. Pressure sensors help operators adjust the reaction conditions in real-time, ensuring that the process remains stable and efficient. Furthermore, in the **pharmaceutical industry**, precise pressure control is necessary during the manufacturing of drugs to maintain sterile environments and ensure the consistency of the final product. The **power generation sector** also heavily relies on pressure measurement. In nuclear power plants, pressure sensors are used to monitor the coolant systems that prevent overheating of the reactor core. In thermal power plants, pressure measurements are critical for managing steam pressures in boilers and turbines, which directly affects the plant's efficiency and safety. Moreover, in **aerospace engineering**, accurate pressure measurements are indispensable for the design and operation of aircraft and spacecraft. Pressure sensors monitor cabin pressure, fuel tank pressures, and engine performance, ensuring safe flight operations and optimal engine performance. In **food processing**, pressure measurement is used to ensure the safety and quality of food products. High-pressure processing (HPP) is a method used to sterilize food without heat, preserving nutrients and flavor. Pressure sensors are essential for maintaining the high pressures required during HPP, ensuring that the food is safely processed without compromising its quality. Additionally, in **water treatment**, pressure measurements help manage water distribution systems by monitoring pipeline pressures to detect leaks and optimize water flow rates. Overall, the industrial applications of pressure measurement underscore its importance in maintaining operational safety, efficiency, and product quality across diverse sectors. By providing real-time data on pressure conditions, these measurements enable industries to make informed decisions, prevent accidents, and optimize processes, ultimately contributing to economic growth and public safety.
3. Medical Applications of Blood Pressure Measurement
**Medical Applications of Blood Pressure Measurement** Blood pressure measurement is a cornerstone in medical diagnostics, playing a crucial role in assessing cardiovascular health and guiding clinical decision-making. The significance of blood pressure monitoring extends across various medical disciplines, from primary care to specialized cardiology and nephrology. In clinical practice, blood pressure is measured to diagnose and manage hypertension, a condition that affects millions worldwide and is a major risk factor for heart disease, stroke, and kidney disease. Regular monitoring helps healthcare providers track changes in blood pressure over time, enabling early detection of hypertension and timely intervention. For instance, the American Heart Association recommends regular blood pressure checks for adults aged 40 and older, or younger individuals with risk factors such as obesity or family history of hypertension. Beyond diagnosis, blood pressure measurement is essential for monitoring the effectiveness of antihypertensive treatments. Healthcare providers use blood pressure readings to adjust medication dosages or switch between different classes of antihypertensive drugs to achieve optimal control. This personalized approach ensures that patients receive the most effective treatment while minimizing potential side effects. In critical care settings, continuous blood pressure monitoring is vital for managing patients with acute cardiovascular conditions such as heart failure or acute coronary syndrome. Invasive blood pressure monitoring via arterial catheters provides real-time data, allowing for immediate adjustments in treatment strategies to stabilize the patient's condition. This is particularly important in intensive care units where rapid changes in blood pressure can indicate life-threatening complications. Blood pressure measurement also plays a critical role in prenatal care. Hypertension during pregnancy can lead to preeclampsia, a potentially severe condition that poses risks to both mother and fetus. Regular blood pressure checks during prenatal visits help identify women at risk, enabling early intervention with bed rest, medication, or delivery if necessary. Furthermore, blood pressure monitoring is integral to research in cardiovascular medicine. Large-scale epidemiological studies rely on accurate blood pressure measurements to understand the prevalence and impact of hypertension in different populations. These studies inform public health policies aimed at reducing the burden of cardiovascular diseases through lifestyle modifications and community-based interventions. In addition to these clinical applications, advancements in technology have expanded the scope of blood pressure measurement. Wearable devices and mobile health applications now allow patients to monitor their blood pressure at home, enhancing patient engagement and facilitating more frequent measurements outside the clinical setting. These tools can provide valuable insights into blood pressure variability and patterns that may not be evident through sporadic clinic visits. In conclusion, the medical applications of blood pressure measurement are multifaceted and indispensable. From diagnosing and managing hypertension to guiding critical care decisions and informing public health strategies, accurate blood pressure measurement remains a fundamental tool in modern medicine. As technology continues to evolve, it is likely that the role of blood pressure monitoring will expand further, offering new avenues for improving patient outcomes and advancing our understanding of cardiovascular health.
Tools and Techniques for Measuring Pressure
Measuring pressure accurately is a critical task in various industries, including engineering, manufacturing, and healthcare. To ensure precise and reliable readings, it is essential to understand the diverse tools and techniques available. This article delves into the key aspects of pressure measurement, starting with an exploration of the different types of pressure gauges and meters. These devices vary significantly in design, functionality, and application, making it crucial to select the right tool for specific needs. Additionally, we will compare digital vs. analog pressure measurement devices, highlighting their respective advantages and limitations. Finally, we will discuss the importance of calibration and accuracy in pressure measurement, as these factors directly impact the reliability of the data obtained. By understanding these elements, professionals can make informed decisions and ensure that their pressure measurement practices are both effective and accurate. Let us begin by examining the various types of pressure gauges and meters that form the foundation of precise pressure measurement.
1. Types of Pressure Gauges and Meters
When it comes to measuring pressure, the choice of tool is crucial for accuracy and reliability. Among the various tools and techniques available, pressure gauges and meters stand out as essential instruments in a wide range of industries, from industrial manufacturing to medical devices. There are several types of pressure gauges and meters, each designed to meet specific needs and applications. **Mechanical Pressure Gauges** are perhaps the most common type. These gauges use a mechanical linkage to translate pressure changes into a readable dial or pointer. They are robust, easy to use, and often inexpensive, making them suitable for everyday industrial use. Within this category, **Bourdon Tube Gauges** are particularly popular due to their simplicity and reliability. The Bourdon tube is a curved tube that straightens as pressure increases, moving a pointer on a dial to indicate the pressure. **Digital Pressure Gauges** offer a more modern alternative with higher precision and ease of use. These gauges convert pressure into an electrical signal that is then displayed on an LCD screen. They often include additional features such as data logging, alarm settings, and calibration options. Digital gauges are ideal for applications requiring precise measurements and quick data retrieval. **Piezoresistive Pressure Sensors** are another type that relies on the piezoresistive effect, where the electrical resistance of a material changes in response to applied pressure. These sensors are highly sensitive and can measure very small changes in pressure, making them suitable for applications in aerospace, automotive, and medical devices. **Capacitive Pressure Sensors** use a capacitor to measure pressure. The capacitance changes as the distance between two plates varies with applied pressure. These sensors are known for their high accuracy and stability over time, making them popular in environments where precise and consistent measurements are critical. **Strain Gauge Pressure Sensors** utilize strain gauges attached to a diaphragm or other flexible element. As pressure is applied, the diaphragm deforms, causing the strain gauge to change its electrical resistance. These sensors are versatile and can be used in various configurations to measure different types of pressure. **Differential Pressure Gauges** measure the difference in pressure between two points rather than absolute pressure. These gauges are essential in applications such as HVAC systems, where the pressure difference across filters or valves needs to be monitored. **Absolute Pressure Gauges** measure pressure relative to a perfect vacuum, providing an absolute value of pressure. These gauges are necessary in environments where atmospheric pressure variations could affect readings, such as in scientific research or high-altitude applications. **Gauge Pressure Gauges** measure pressure relative to atmospheric pressure, which is the most common type used in everyday industrial settings. They provide a reading that indicates how much above or below atmospheric pressure the system is operating. In summary, the selection of the right type of pressure gauge or meter depends on the specific requirements of the application, including accuracy, range, and environmental conditions. By understanding the different types available, users can ensure that their measurements are accurate, reliable, and tailored to their needs. Whether it's a simple mechanical gauge or a sophisticated digital sensor, each tool plays a vital role in ensuring the safe and efficient operation of various systems across diverse industries.
2. Digital vs. Analog Pressure Measurement Devices
When it comes to measuring pressure, the choice between digital and analog pressure measurement devices is crucial, as each type offers distinct advantages and disadvantages. **Digital Pressure Measurement Devices** are highly favored for their precision, reliability, and ease of use. These devices convert the mechanical pressure into an electrical signal, which is then processed and displayed on a digital screen. This conversion process allows for high accuracy and minimal human error, making them ideal for applications requiring precise measurements. Digital pressure gauges often feature additional functionalities such as data logging, alarm settings, and compatibility with various communication protocols (e.g., RS-232, USB), enabling seamless integration into automated systems. Furthermore, digital devices are generally more resistant to environmental factors like temperature and vibration, ensuring consistent performance across different conditions. However, they may require calibration and periodic battery replacements, which can add to their overall cost. On the other hand, **Analog Pressure Measurement Devices**, such as traditional dial gauges, have been in use for decades and are still valued for their simplicity and cost-effectiveness. These devices rely on mechanical components to indicate pressure levels through a needle on a calibrated dial. Analog gauges are straightforward to read and do not require any power source, making them suitable for basic applications where high precision is not critical. They also offer a visual indication of pressure trends over time, which can be beneficial in certain monitoring scenarios. However, analog devices are more susceptible to mechanical wear and tear, leading to potential inaccuracies over time. Additionally, they may be less robust against environmental factors compared to their digital counterparts. Despite these limitations, analog gauges remain popular in industries where simplicity and low maintenance are prioritized. In summary, the selection between digital and analog pressure measurement devices should be based on the specific requirements of the application. For high-precision measurements and integration into advanced systems, digital devices are the preferred choice due to their accuracy and versatility. Conversely, for straightforward monitoring needs where simplicity and low cost are key considerations, analog devices continue to serve as reliable options. Understanding the strengths and weaknesses of each type ensures that the most appropriate tool is chosen for accurate and efficient pressure measurement.
3. Calibration and Accuracy in Pressure Measurement
Calibration and accuracy are paramount in pressure measurement, ensuring that the readings obtained are reliable and trustworthy. Calibration involves comparing the output of a pressure-measuring device against a known standard to verify its accuracy. This process is crucial because even slight deviations can lead to significant errors in various applications, from industrial processes to medical devices. For instance, in the oil and gas industry, inaccurate pressure readings can result in inefficient operations, safety hazards, or even catastrophic failures. To achieve high accuracy, several techniques are employed. One common method is using a deadweight tester, which applies a known force to a piston, generating a precise pressure that can be used as a reference point. Another approach involves comparing the device against a primary standard such as a mercury column or a precision pressure gauge. These standards are traceable to national or international standards, ensuring that the calibration is accurate and consistent. Regular calibration schedules are also essential to maintain the integrity of pressure measurements. Over time, devices can drift due to wear and tear, environmental changes, or other factors. By periodically recalibrating these devices, users can ensure that their readings remain within acceptable limits. Additionally, modern pressure-measuring instruments often incorporate advanced technologies such as digital signal processing and compensation algorithms to enhance accuracy and stability. The choice of calibration method depends on the specific application and the required level of precision. For example, in high-precision applications like aerospace engineering or scientific research, more sophisticated calibration techniques may be necessary. In contrast, simpler methods might suffice for less demanding environments such as routine maintenance tasks. Moreover, environmental factors such as temperature and humidity can significantly impact the accuracy of pressure measurements. Therefore, it is important to consider these variables during calibration and ensure that the device is compensated accordingly. Some advanced pressure sensors come with built-in temperature compensation mechanisms to mitigate these effects. In summary, calibration and accuracy are fundamental aspects of pressure measurement that cannot be overlooked. By employing rigorous calibration techniques, adhering to regular maintenance schedules, and considering environmental influences, users can ensure that their pressure measurements are reliable and accurate. This not only enhances operational efficiency but also contributes to safety and compliance with regulatory standards across various industries.