What Is Directional Cutting

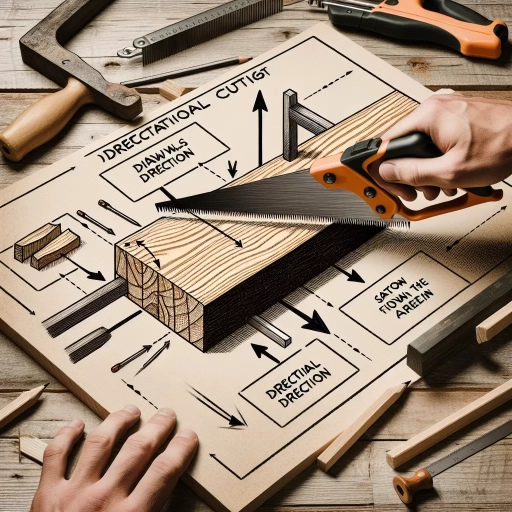
Understanding the Basics of Directional Cutting
Understanding the basics of directional cutting is a fundamental aspect of various industries, including hairstyling, woodworking, and even navigation. This technique involves cutting materials in a specific direction to achieve desired outcomes, such as enhancing texture, ensuring safety, or optimizing performance. To fully grasp the concept of directional cutting, it is essential to explore three key areas: its definition and purpose, its historical context and evolution, and the key principles and techniques involved. **Definition and Purpose** will delve into the core meaning of directional cutting and why it is crucial in different fields. This section will explain how directional cutting impacts the final product's quality and functionality. **Historical Context and Evolution** will trace the origins and development of directional cutting techniques over time. This will highlight how advancements in technology and understanding have shaped current practices. **Key Principles and Techniques** will provide a detailed look at the methods and guidelines that professionals follow to execute directional cutting effectively. By understanding these principles, individuals can apply them in their respective fields with precision and accuracy. By examining these three aspects, readers will gain a comprehensive understanding of directional cutting, starting with its **Definition and Purpose**.
Definition and Purpose
**Definition and Purpose** Directional cutting, a fundamental technique in hairstyling, is defined as the strategic cutting of hair to create movement, texture, and flow in a specific direction. This method involves cutting the hair at an angle or with a particular bias to enhance the natural growth pattern, thereby achieving a more dynamic and visually appealing hairstyle. The purpose of directional cutting is multifaceted: it not only adds volume and texture but also helps in framing the face, accentuating facial features, and creating a balanced silhouette. By cutting hair in a way that follows or contrasts with its natural growth direction, stylists can control how the hair falls, ensuring that it moves gracefully and maintains its shape throughout the day. This technique is particularly useful for clients with specific hair types or textures, as it can help manage unruly locks, reduce bulkiness, or add layers for a more polished look. Moreover, directional cutting allows stylists to create personalized styles that cater to individual preferences and lifestyles, making it an essential skill for any hairstylist aiming to deliver high-quality, tailored services. Understanding the basics of directional cutting is crucial for mastering various hairstyling techniques and ensuring that each cut is both aesthetically pleasing and functional. By grasping this foundational concept, stylists can unlock a wide range of creative possibilities, enabling them to transform ordinary haircuts into extraordinary works of art that enhance their clients' confidence and overall appearance.
Historical Context and Evolution
**Historical Context and Evolution** Directional cutting, a technique fundamental to various industries including hairstyling, woodworking, and even surgical procedures, has a rich and evolving history that spans centuries. The concept of directional cutting first emerged in ancient civilizations where artisans and craftsmen understood the importance of aligning cuts with the natural grain or texture of materials to achieve optimal results. In hairstyling, for instance, ancient Egyptians and Greeks used simple tools like razors and shears to cut hair in ways that respected the natural growth patterns of the hair follicles, enhancing both aesthetics and manageability. As civilizations advanced, so did the tools and techniques. During the Renaissance period, European barbers developed more sophisticated methods of cutting hair that took into account the direction of hair growth. This was crucial for creating styles that were not only fashionable but also durable and easy to maintain. The Industrial Revolution brought significant advancements with the invention of mechanized cutting tools, allowing for more precise and efficient cuts across various materials. In the 20th century, directional cutting became a cornerstone of modern hairstyling. Pioneers like Vidal Sassoon revolutionized the industry by introducing geometric cutting techniques that emphasized cutting hair in the direction of its growth. This approach not only simplified the styling process but also enabled hairstylists to create versatile, low-maintenance styles that became iconic of the era. Sassoon's methods were based on understanding the anatomy of the head and the natural flow of hair, principles that remain foundational in contemporary hairstyling. Beyond hairstyling, directional cutting has played a critical role in woodworking and carpentry. Woodworkers have long recognized that cutting wood against its grain can lead to splitting and weakening of the material, while cutting with the grain ensures strength and durability. This principle has been applied in various woodworking techniques from ancient shipbuilding to modern furniture making. In medical fields, particularly in surgical procedures, directional cutting is equally vital. Surgeons must carefully plan incisions to align with the natural fibers of tissues to minimize damage and promote healing. This precision is crucial for reducing scarring and ensuring optimal recovery times. Throughout its evolution, directional cutting has been shaped by technological advancements, cultural influences, and practical necessities. Today, it remains an essential skill across multiple disciplines, underpinning best practices in hairstyling, woodworking, and surgery. Understanding the historical context and evolution of directional cutting provides a deeper appreciation for its importance and underscores the need for continued innovation and refinement in these fields. By respecting the natural directions of materials and tissues, practitioners can achieve superior outcomes that are both aesthetically pleasing and functionally sound. This foundational knowledge is key to mastering the basics of directional cutting and applying it effectively in various professional contexts.
Key Principles and Techniques
Understanding the basics of directional cutting hinges on mastering several key principles and techniques that guide the process. At its core, directional cutting is a method used in various industries such as hairdressing, woodworking, and even surgery to ensure precise and controlled cuts that align with the natural grain or direction of the material being worked on. **Key Principles:** 1. **Grain Alignment:** The most fundamental principle is understanding and aligning cuts with the natural grain of the material. In hairdressing, this means cutting hair in the direction it grows to avoid split ends and breakage. Similarly, in woodworking, cutting with the grain prevents splintering and ensures a smoother finish. 2. **Tension Control:** Maintaining the right tension is crucial. For instance, in hair cutting, too much tension can lead to uneven cuts, while too little may result in a lack of precision. 3. **Angle Precision:** The angle at which cuts are made significantly impacts the outcome. In surgical procedures, precise angles are critical for minimizing tissue damage and ensuring optimal healing. **Techniques:** 1. **Sectioning:** Dividing the material into manageable sections allows for more precise control over each cut. This technique is particularly useful in hairdressing where sectioning helps maintain evenness and symmetry. 2. **Blade or Tool Orientation:** Proper orientation of cutting tools is essential. For example, in woodworking, keeping the blade at a consistent angle relative to the wood grain ensures clean cuts without splintering. 3. **Follow-Through:** Completing each cut with a smooth follow-through ensures that the cut is clean and even. This technique helps prevent jagged edges or uneven finishes. 4. **Visual Alignment:** Using visual aids or guides can enhance accuracy. In surgical contexts, surgeons often use markers or guides to ensure cuts are made along precise lines. **Application Across Industries:** - **Hairdressing:** Directional cutting in hairdressing involves cutting hair in the direction it grows to enhance natural texture and prevent damage. Techniques like point cutting and slice-and-dice methods rely heavily on understanding grain direction. - **Woodworking:** Woodworkers must cut wood along its grain to avoid splintering and achieve a smooth finish. This principle is especially important when working with hardwoods which are more prone to splitting. - **Surgery:** In surgical contexts, directional cutting is critical for minimizing tissue damage and promoting optimal healing. Surgeons must align their cuts with the natural fibers of tissues to reduce trauma. By adhering to these principles and techniques, practitioners across various fields can achieve more precise, controlled, and effective cuts that enhance the quality of their work. Whether it's a hairstylist aiming for a flawless cut, a woodworker seeking a smooth finish, or a surgeon striving for minimal tissue damage, understanding directional cutting is paramount for achieving desired outcomes. This foundational knowledge not only improves skill levels but also ensures safety and efficiency in each respective field.
Applications and Benefits of Directional Cutting
Directional cutting, a sophisticated machining technique, has revolutionized various industries by offering unparalleled precision and efficiency. This method involves cutting materials in a specific direction to achieve optimal results, and its applications are multifaceted. In the realm of manufacturing, directional cutting plays a crucial role in producing high-quality components with intricate designs. Beyond its industrial uses, this technique also excels in precision engineering, where minute details are paramount. Additionally, directional cutting significantly impacts material efficiency and cost by minimizing waste and optimizing resource utilization. By exploring these facets, we can fully appreciate the transformative power of directional cutting. Let us begin by examining its industrial uses in manufacturing, where the technique has become an indispensable tool for modern production processes.
Industrial Uses in Manufacturing
In the realm of manufacturing, directional cutting emerges as a pivotal technique that significantly enhances the efficiency and precision of various industrial processes. This method, which involves cutting materials in a specific direction to optimize the mechanical properties of the final product, has far-reaching applications across multiple sectors. For instance, in the aerospace industry, directional cutting is crucial for producing lightweight yet robust components such as aircraft wings and fuselage sections. By aligning the cut with the material's grain or fiber orientation, manufacturers can ensure that these components possess superior strength-to-weight ratios, thereby improving fuel efficiency and overall aircraft performance. In automotive manufacturing, directional cutting plays a key role in the production of high-strength steel parts. By cutting steel sheets in directions that align with their rolling direction, manufacturers can exploit the material's inherent anisotropy to create parts with enhanced tensile strength and reduced weight. This is particularly important for safety-critical components like crash structures and chassis members, where optimal material properties are essential for passenger safety. The construction industry also benefits from directional cutting, especially in the fabrication of composite materials used in building structures. Directional cutting allows for the precise alignment of fibers within these composites, resulting in improved structural integrity and resistance to environmental stresses. This technique is particularly valuable in the creation of advanced building materials such as carbon fiber reinforced polymers (CFRP), which are increasingly used in high-rise buildings and other large-scale construction projects. Furthermore, directional cutting is integral to the production of advanced medical devices. In orthopedic implants, for example, precise cutting techniques are used to create implants with tailored mechanical properties that mimic natural bone tissue. By cutting titanium alloys or other biomaterials in specific directions, manufacturers can achieve optimal implant stability and biocompatibility, leading to better patient outcomes. In addition to these specific applications, directional cutting offers several overarching benefits that contribute to its widespread adoption in manufacturing. One of the primary advantages is the ability to maximize material efficiency by minimizing waste and optimizing material usage. This not only reduces production costs but also aligns with sustainability goals by conserving resources. Moreover, directional cutting enables the creation of complex geometries and shapes that would be difficult or impossible to achieve through traditional cutting methods. This flexibility opens up new design possibilities, allowing engineers to innovate and create products with enhanced functionality and performance. Overall, directional cutting is a versatile and powerful tool in modern manufacturing, offering a range of industrial uses that span multiple sectors. Its ability to tailor material properties at the microstructural level makes it an indispensable technique for producing high-performance components that meet stringent quality standards. As technology continues to evolve, the applications and benefits of directional cutting are likely to expand further, driving innovation and excellence in various fields of manufacturing.
Advantages in Precision Engineering
Precision engineering, a discipline that emphasizes exactness and meticulous attention to detail, offers a myriad of advantages across various industries. At the heart of precision engineering lies the ability to produce components and systems with minimal tolerances, ensuring high accuracy and reliability. One of the key benefits is **enhanced performance**; precision-engineered parts operate more efficiently, leading to improved overall system functionality. For instance, in aerospace engineering, precision-crafted components are crucial for the reliability and safety of aircraft, where even slight deviations can have critical consequences. Another significant advantage is **extended lifespan**. Precision-engineered products tend to have longer lifespans due to their precise fit and finish, which reduces wear and tear. This is particularly evident in the automotive industry, where precision-engineered engine components can significantly extend the vehicle's lifespan and reduce maintenance costs. Additionally, **cost savings** are a direct result of precision engineering; while initial investment may be higher, the long-term benefits of reduced maintenance and replacement needs outweigh these costs. **Consistency and reproducibility** are also hallmark advantages of precision engineering. By adhering to strict standards and using advanced technologies like CNC machining and 3D printing, manufacturers can produce identical parts repeatedly, which is vital in mass production scenarios. This consistency ensures that every product meets the same high standards, thereby enhancing quality control. Moreover, precision engineering fosters **innovation** by pushing the boundaries of what is possible. The ability to create complex geometries and micro-scale features opens up new possibilities for product design and functionality. For example, in medical devices, precision engineering allows for the development of intricate instruments and implants that can be tailored to individual patient needs, leading to better outcomes and improved patient care. In the context of directional cutting—a technique that involves cutting materials in specific directions to optimize material properties—precision engineering plays a pivotal role. Directional cutting leverages the anisotropic properties of materials (where properties vary depending on direction) to enhance strength, durability, and performance. By precisely controlling the cutting direction, engineers can maximize material efficiency and minimize waste, which is particularly beneficial in industries such as aerospace and automotive where lightweight yet strong materials are essential. Furthermore, precision engineering in directional cutting enables **customization**. By tailoring the cutting process to specific material properties and application requirements, engineers can create bespoke solutions that meet exacting standards. This customization capability is invaluable in fields like sports equipment manufacturing, where precision-crafted components can provide athletes with a competitive edge by optimizing performance characteristics such as weight distribution and aerodynamics. In conclusion, the advantages of precision engineering are multifaceted and far-reaching. From enhancing performance and extending lifespan to fostering innovation and enabling customization, precision engineering is a cornerstone of modern manufacturing. When combined with techniques like directional cutting, these advantages are amplified, leading to superior products that excel in their respective applications. As technology continues to evolve, the role of precision engineering will only become more critical in driving innovation and excellence across diverse industries.
Impact on Material Efficiency and Cost
**Impact on Material Efficiency and Cost** Directional cutting significantly enhances material efficiency and reduces costs in various industries, particularly in manufacturing and construction. By optimizing the cutting process to align with the inherent properties of materials, such as grain direction in wood or fiber orientation in composites, directional cutting minimizes waste and maximizes yield. This approach ensures that each cut is made with precision, reducing the likelihood of defects and the need for rework. For instance, in woodworking, cutting with the grain prevents splitting and cracking, allowing for more accurate and efficient use of timber. Similarly, in aerospace engineering, directional cutting of composite materials aligns with fiber orientation to maintain structural integrity, thereby reducing material consumption and enhancing the overall performance of the final product. The economic benefits are substantial. By reducing waste, companies can lower their raw material costs and minimize the environmental impact associated with excessive resource consumption. Additionally, the precision of directional cutting reduces the need for secondary processing steps, such as sanding or machining, which can be time-consuming and costly. This streamlined process not only saves on labor costs but also accelerates production timelines, enabling businesses to meet demand more effectively. Furthermore, the improved quality of cut materials leads to longer product lifetimes and reduced maintenance needs, which can result in significant long-term cost savings for both manufacturers and consumers. In industries where material costs are high, such as in the production of advanced composites or exotic hardwoods, the efficiency gains from directional cutting are particularly pronounced. For example, in the automotive sector, where lightweight yet strong materials are crucial for performance and safety, directional cutting helps optimize the use of expensive composite materials without compromising on structural integrity. This not only reduces material costs but also contributes to the development of more fuel-efficient vehicles. Moreover, the adoption of directional cutting techniques often necessitates the use of advanced technologies and software tools that can analyze material properties and optimize cutting paths. While these tools may represent an initial investment, they provide long-term benefits through enhanced precision and efficiency. They also enable real-time monitoring and adjustments, further optimizing the cutting process and ensuring that materials are used as efficiently as possible. In summary, directional cutting has a profound impact on material efficiency and cost by minimizing waste, optimizing material use, and reducing the need for secondary processing steps. These advantages translate into lower raw material costs, faster production times, and improved product quality, making directional cutting an indispensable technique across various industries. As technology continues to evolve, the potential for even greater efficiencies and cost savings through directional cutting will only continue to grow.
Modern Technologies and Innovations in Directional Cutting
The realm of directional cutting has undergone a transformative evolution with the advent of modern technologies and innovations. At the heart of this revolution are three key areas: the role of CNC machines and automation, advancements in cutting tools and materials, and the integration of directional cutting with other manufacturing processes. CNC machines and automation have significantly enhanced precision and efficiency, allowing for complex cuts with minimal human intervention. Meanwhile, advancements in cutting tools and materials have improved durability and performance, enabling faster and more accurate cutting operations. Additionally, the integration of directional cutting with other manufacturing processes has streamlined production workflows, fostering a more cohesive and productive manufacturing environment. As we delve into these advancements, it becomes clear that the role of CNC machines and automation is pivotal in driving these innovations forward, setting the stage for a new era in precision cutting. --- **Role of CNC Machines and Automation**
Role of CNC Machines and Automation
In the realm of directional cutting, the integration of Computer Numerical Control (CNC) machines and automation has revolutionized the precision, efficiency, and scalability of cutting processes. CNC machines, which operate under computerized control, enable precise and repetitive cutting tasks with minimal human intervention. This technology allows for the execution of complex cutting patterns and designs that would be challenging or impossible to achieve manually. The role of CNC machines in directional cutting is multifaceted: they enhance accuracy by minimizing human error, increase productivity by performing tasks at higher speeds and for longer durations without fatigue, and improve consistency by maintaining uniform quality across multiple cuts. Automation further amplifies these benefits by integrating CNC machines into larger systems that can manage entire production workflows. Automated systems can optimize cutting sequences, adjust parameters in real-time based on material properties, and even predict maintenance needs to prevent downtime. This holistic approach ensures that directional cutting operations are not only precise but also highly efficient and cost-effective. For instance, in industries such as aerospace and automotive manufacturing, where precision is paramount, automated CNC systems can cut intricate parts with high accuracy and speed, significantly reducing production time and material waste. Moreover, the integration of advanced technologies like machine learning and IoT (Internet of Things) with CNC machines and automation systems is driving innovation in directional cutting. These technologies enable real-time monitoring and data analytics, allowing for continuous improvement in cutting processes. Predictive maintenance algorithms can detect potential issues before they occur, while machine learning algorithms can optimize cutting parameters based on historical data and real-time feedback. This synergy between CNC machines, automation, and advanced technologies is transforming directional cutting into a highly sophisticated and adaptive process. The impact of these advancements extends beyond manufacturing efficiency; they also open up new possibilities for design and innovation. With the capability to cut complex shapes and materials accurately, designers can now conceptualize and produce parts that were previously unfeasible. This has led to breakthroughs in various fields, including medical devices, where precise cutting is crucial for creating implants and surgical instruments, and renewable energy, where advanced materials require precise cutting for optimal performance. In conclusion, the role of CNC machines and automation in directional cutting is pivotal. By combining precision, speed, and adaptability, these technologies have elevated the field from a labor-intensive process to a highly automated and efficient one. As modern technologies continue to evolve, the future of directional cutting promises even greater innovations, further enhancing the capabilities of industries that rely on precise cutting operations. This integration not only streamlines production but also fosters creativity and innovation, making it an indispensable component of modern manufacturing landscapes.
Advancements in Cutting Tools and Materials
Advancements in cutting tools and materials have significantly enhanced the precision, efficiency, and versatility of directional cutting technologies. At the forefront of these advancements are innovations in tool materials, such as the development of high-speed steel (HSS), tungsten carbide, and advanced ceramics. High-speed steel tools, for instance, offer improved hardness and wear resistance, allowing for faster cutting speeds and longer tool life. Tungsten carbide, known for its exceptional hardness and thermal resistance, is often used in solid carbide tools and inserts, enabling more aggressive cutting operations with reduced tool wear. Advanced ceramic tools, including silicon nitride and alumina-based materials, provide superior hardness and chemical inertness, making them ideal for machining hard-to-cut materials like titanium alloys and composites. Another critical area of advancement is in the realm of coatings and surface treatments. Modern cutting tools often feature advanced coatings such as titanium nitride (TiN), titanium aluminum nitride (TiAlN), and diamond-like carbon (DLC). These coatings enhance tool performance by reducing friction, improving wear resistance, and preventing adhesion between the tool and workpiece. Additionally, surface treatments like physical vapor deposition (PVD) and chemical vapor deposition (CVD) allow for the application of thin, uniform coatings that optimize tool performance under various cutting conditions. The integration of smart technologies into cutting tools has also revolutionized directional cutting. Sensors and IoT devices embedded in cutting tools can monitor parameters such as temperature, vibration, and tool condition in real-time, enabling predictive maintenance and optimizing cutting processes. This data-driven approach helps in minimizing downtime, improving tool life, and ensuring consistent product quality. Furthermore, advancements in tool geometry and design have played a crucial role in enhancing directional cutting capabilities. The use of computer-aided design (CAD) and computer-aided manufacturing (CAM) software allows for the creation of complex tool geometries tailored to specific cutting tasks. This includes the development of specialized tools with unique edge preparations and flute designs that optimize chip formation and evacuation, thereby improving cutting efficiency and reducing the risk of tool breakage. Innovations in machining processes themselves have also been influenced by advancements in cutting tools and materials. Techniques such as high-speed machining (HSM) and hard turning leverage the capabilities of advanced cutting tools to achieve high precision and surface finish without the need for subsequent grinding operations. These processes are particularly beneficial in industries requiring tight tolerances and smooth finishes, such as aerospace and automotive manufacturing. Overall, the synergy between cutting tool advancements and directional cutting technologies has transformed the landscape of modern manufacturing. By combining superior tool materials, advanced coatings, smart technologies, optimized tool geometries, and innovative machining processes, industries can achieve unprecedented levels of precision, efficiency, and productivity. As research continues to push the boundaries of what is possible with cutting tools and materials, directional cutting will remain at the forefront of technological innovation in manufacturing.
Integration with Other Manufacturing Processes
Integration with other manufacturing processes is a crucial aspect of modern directional cutting, enhancing its efficiency, precision, and overall impact. Directional cutting, which involves cutting materials in specific directions to optimize their properties and performance, can be seamlessly integrated with various advanced manufacturing techniques. For instance, when combined with Computer Numerical Control (CNC) machining, directional cutting allows for highly precise and automated processes. CNC systems can be programmed to execute complex cutting paths that align with the material's grain or fiber orientation, ensuring that the final product retains its desired mechanical properties. Another significant integration is with 3D printing or additive manufacturing. By incorporating directional cutting into the post-processing phase of 3D printed parts, manufacturers can enhance the structural integrity and surface finish of these components. This hybrid approach enables the creation of complex geometries that are not possible through traditional machining alone, while also optimizing material strength and durability. Furthermore, integrating directional cutting with composite material processing is particularly beneficial. In the production of composite parts, such as those used in aerospace and automotive industries, directional cutting ensures that fibers are aligned correctly to maximize tensile strength and resistance to fatigue. This alignment can be achieved through advanced software tools that simulate and predict the behavior of composite materials under various loads, allowing for precise cutting strategies. Additionally, the integration of directional cutting with Industry 4.0 technologies like IoT (Internet of Things) and AI (Artificial Intelligence) further elevates its potential. Real-time monitoring and data analytics enable continuous process optimization, ensuring that cutting parameters are adjusted dynamically to maintain optimal performance. AI algorithms can analyze historical data to predict and prevent potential defects or inefficiencies, thereby improving yield rates and reducing waste. In terms of quality control, integrating directional cutting with non-destructive testing (NDT) techniques such as ultrasonic inspection or X-ray computed tomography (CT) scans ensures that the cut parts meet stringent quality standards. These NDT methods allow for detailed internal examination without damaging the material, providing assurance that the directional cutting process has achieved the desired outcomes. Lastly, the integration of directional cutting with sustainable manufacturing practices is becoming increasingly important. By optimizing material usage through precise cutting strategies, manufacturers can reduce waste and minimize environmental impact. This aligns with broader industry trends towards more sustainable production methods, making directional cutting an essential tool in the pursuit of eco-friendly manufacturing. In summary, the integration of directional cutting with other advanced manufacturing processes significantly enhances its capabilities, allowing for greater precision, efficiency, and sustainability. By leveraging technologies such as CNC machining, 3D printing, composite material processing, Industry 4.0 tools, NDT techniques, and sustainable practices, manufacturers can unlock the full potential of directional cutting to produce high-performance products that meet demanding industry standards.