What Is A Gantry

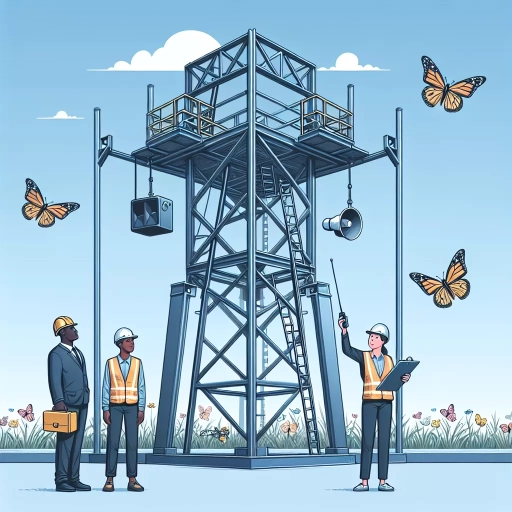
A gantry is a versatile and essential piece of equipment found in various industrial and technological settings. At its core, a gantry system consists of a bridge-like structure that supports a moving component, allowing for precise and efficient movement along multiple axes. This article delves into the multifaceted world of gantries, starting with their definition and purpose, which underpin their functionality and widespread adoption. We will explore how gantries are applied across different sectors, from manufacturing and construction to healthcare and logistics, highlighting their adaptability and impact. Additionally, we will examine the technological advancements that have enhanced gantry systems over time and discuss future trends that promise to further elevate their capabilities. By understanding the fundamental aspects of gantries, their diverse applications, and the innovations driving their evolution, readers will gain a comprehensive insight into these critical systems. Let us begin by defining and exploring the purpose of a gantry.
Definition and Purpose of a Gantry
A gantry, a structural framework used to support and move heavy loads, is a crucial piece of equipment in various industries. Understanding its definition and purpose is essential for appreciating its significance. Historically, gantries have evolved from simple wooden or metal frames to sophisticated, high-tech systems. This evolution is rooted in the need for efficient and safe material handling, which will be explored in the **Historical Context and Evolution** section. The primary functions of gantries span multiple sectors, including construction, manufacturing, and logistics, where they play a pivotal role in enhancing productivity and safety, as detailed in **Primary Functions in Various Industries**. The design and components of gantries are equally important, as they determine the efficiency and reliability of these systems, a topic that will be delved into in **Key Components and Design Elements**. By examining these aspects, we can gain a comprehensive understanding of the gantry's role and importance. Let's begin by tracing the historical context and evolution of gantries to see how they have developed over time.
Historical Context and Evolution
The historical context and evolution of gantries are deeply intertwined with the development of engineering, construction, and manufacturing technologies. The term "gantry" itself originates from the Old French word "gantrie," meaning a bridge or a beam, reflecting its earliest use in medieval times as a simple beam or frame to support loads. In the 18th and 19th centuries, gantries became integral to shipbuilding and maritime industries. They were used as overhead cranes to lift and move heavy ship components, significantly enhancing efficiency and safety in shipyards. The Industrial Revolution further accelerated the evolution of gantries, as they were adapted for use in factories and manufacturing plants to handle heavy machinery and materials. The early 20th century saw the introduction of electric and hydraulic systems, which transformed gantries into more sophisticated and powerful tools. This period also marked the beginning of their widespread use in civil engineering projects, such as bridge construction and tunnel boring. The advent of computer-controlled systems in the latter half of the 20th century allowed for even greater precision and automation, making gantries indispensable in modern construction and manufacturing processes. Today, gantries are used across various industries, including aerospace, automotive, and healthcare, where they facilitate precise movements and heavy lifting tasks. Advances in materials science have led to the development of lighter yet stronger gantries, while advancements in robotics and artificial intelligence continue to enhance their capabilities. The evolution of gantries has been a gradual process driven by technological innovation, reflecting human ingenuity in solving complex engineering challenges. Understanding this historical context is crucial for appreciating the definition and purpose of a gantry. A gantry is essentially a structural frame that supports a hoist or other lifting device, enabling the movement of heavy loads with precision and control. Its purpose is multifaceted: it enhances safety by minimizing manual handling risks, improves efficiency by streamlining operations, and provides versatility in adapting to various industrial needs. The continuous evolution of gantries underscores their importance as a fundamental tool in modern engineering and manufacturing practices.
Primary Functions in Various Industries
In various industries, primary functions are the core activities that drive the operational efficiency and productivity of an organization. Here’s a breakdown of these functions across different sectors: **Manufacturing:** The primary functions in manufacturing include production planning, material procurement, inventory management, quality control, and distribution. These activities ensure that products are made efficiently and meet quality standards before being shipped to customers. **Healthcare:** In healthcare, primary functions focus on patient care, diagnosis, treatment, and preventive medicine. These include clinical services, medical research, patient education, and administrative support to ensure high-quality care and patient satisfaction. **Finance:** The primary functions in finance involve financial planning, budgeting, accounting, risk management, and investment analysis. These activities help organizations manage their financial resources effectively and make informed investment decisions. **Technology:** In the tech industry, primary functions include software development, data analytics, cybersecurity, network management, and customer support. These activities drive innovation, protect data integrity, and ensure smooth operations. **Construction:** For construction companies, primary functions include project planning, site management, material procurement, labor coordination, and quality assurance. These activities ensure that projects are completed on time, within budget, and to the required standards. **Retail:** In retail, primary functions encompass inventory management, supply chain logistics, customer service, marketing, and sales. These activities aim to maximize sales while maintaining customer satisfaction and operational efficiency. **Agriculture:** The primary functions in agriculture involve crop planning, soil management, irrigation systems, pest control, harvesting, and livestock care. These activities are crucial for optimizing crop yields and ensuring sustainable farming practices. **Transportation:** For transportation companies, primary functions include route planning, vehicle maintenance, cargo handling, safety compliance, and customer service. These activities ensure safe and efficient movement of goods and people. Understanding these primary functions is essential for any organization looking to optimize its operations and achieve its goals. In the context of a gantry system, which is often used in manufacturing and construction for lifting heavy loads or providing structural support, these primary functions highlight the importance of precision and reliability in equipment design and operation. A gantry system must be capable of performing its intended function efficiently and safely to support the broader operational objectives of an industry.
Key Components and Design Elements
When discussing the definition and purpose of a gantry, it is crucial to delve into its key components and design elements, as these factors collectively define its functionality and efficiency. A gantry typically consists of several primary components: the frame or structure, which provides the overall framework and support; the beams or girders, which span across the frame to create the working platform; and the trolleys or carriages, which move along these beams to facilitate material handling. The design elements of a gantry are equally important. **Stability** is a critical design consideration, ensuring that the gantry can withstand various loads without compromising safety. This is achieved through robust materials and a sturdy construction. **Mobility** is another key aspect, with many gantries featuring wheels or tracks that allow them to be easily relocated or repositioned as needed. **Adjustability** is also a significant design element, enabling users to customize the height and span of the gantry to suit different tasks and environments. Additionally, **ergonomics** play a vital role in gantry design. Features such as ergonomic handles, intuitive controls, and comfortable working heights enhance user experience and reduce fatigue. **Safety features** are paramount, including load limits, safety stops, and protective barriers to prevent accidents. The **material selection** for the gantry's components is also critical, with choices often made based on durability, weight capacity, and resistance to environmental factors like corrosion or extreme temperatures. Incorporating **technology** into gantry design can further enhance its capabilities. For instance, automated systems can streamline operations by allowing for remote control or programmed movements. **Customization options** are another design element, enabling users to tailor their gantry to specific applications through modular components or bespoke designs. Overall, the combination of these key components and thoughtful design elements ensures that a gantry serves its purpose effectively—whether it's in construction, manufacturing, logistics, or any other industry requiring efficient material handling and precise movement. By understanding these elements, users can better appreciate the versatility and utility of a gantry system.
Applications of Gantry Systems Across Different Sectors
Gantry systems, known for their versatility and precision, have become indispensable across various sectors due to their ability to enhance efficiency, safety, and productivity. In industrial manufacturing and assembly lines, gantry systems play a crucial role in automating processes, ensuring consistent quality, and reducing labor costs. They are also pivotal in construction and heavy lifting operations, where their robust design and high load capacity make them ideal for handling large and heavy materials. Additionally, in medical and healthcare settings, gantry systems are used in advanced imaging technologies such as MRI and CT scanners, providing precise and stable platforms for diagnostic procedures. These applications highlight the multifaceted nature of gantry systems, each tailored to meet the specific demands of different industries. Transitioning to the industrial sector, we delve into how gantry systems revolutionize manufacturing and assembly lines by streamlining production processes and improving overall operational efficiency.
Industrial Manufacturing and Assembly Lines
Industrial manufacturing and assembly lines are the backbone of modern production, leveraging advanced technologies to optimize efficiency, precision, and productivity. At the heart of these operations are gantry systems, which play a crucial role in streamlining processes across various sectors. In industrial manufacturing, gantry systems are utilized for material handling, welding, cutting, and inspection tasks. These systems consist of overhead beams or frames that support moving trolleys or cranes, allowing for the precise movement of heavy loads and tools over large work areas. In assembly lines, gantry systems enhance the automation of repetitive tasks, reducing labor costs and improving product quality. For instance, in automotive manufacturing, gantries are used to transport vehicle bodies through different stages of assembly, ensuring consistent and accurate placement of components. Similarly, in aerospace manufacturing, gantries facilitate the assembly of complex aircraft structures by providing precise positioning and movement of heavy components. The versatility of gantry systems extends beyond traditional manufacturing. In the food processing industry, gantries are used for packaging and palletizing products, ensuring high-speed and accurate handling of perishable goods. In construction, gantries support the assembly of large prefabricated components, such as building modules and bridge sections, enabling faster and more efficient construction processes. Moreover, gantry systems are integral to the implementation of Industry 4.0 technologies. They can be integrated with robotics, artificial intelligence, and IoT sensors to create smart manufacturing environments. This integration enables real-time monitoring, predictive maintenance, and adaptive control, further enhancing operational efficiency and reducing downtime. The benefits of using gantry systems in industrial manufacturing and assembly lines are multifaceted. They offer increased flexibility, allowing for easy reconfiguration to accommodate different product lines or production requirements. Additionally, gantries improve workplace safety by minimizing manual handling of heavy loads and reducing the risk of accidents. From a financial perspective, the investment in gantry systems can lead to significant cost savings through reduced labor costs, improved product quality, and extended equipment lifespan. In summary, gantry systems are indispensable in modern industrial manufacturing and assembly lines, offering unparalleled precision, efficiency, and adaptability. Their widespread adoption across various sectors underscores their critical role in driving innovation and productivity in today's industrial landscape.
Construction and Heavy Lifting Operations
Construction and heavy lifting operations are critical components of various industrial sectors, including construction, manufacturing, and logistics. These operations involve the movement and placement of heavy loads, which require precision, safety, and efficiency. Gantry systems play a pivotal role in these processes due to their versatility and capability to handle substantial weights. In construction, gantry systems are often used for tasks such as lifting and placing large building components, like prefabricated walls or heavy machinery. These systems provide a stable and controlled environment for lifting operations, reducing the risk of accidents and improving project timelines. For instance, in bridge construction, gantries can be used to lift and position massive concrete sections or steel beams with high accuracy. In heavy lifting operations within manufacturing facilities, gantries are essential for moving heavy equipment or raw materials around the plant. They enable the precise positioning of components during assembly processes, enhancing productivity and reducing manual labor. For example, in shipbuilding yards, gantry cranes are used to lift and place large ship sections into position, facilitating the efficient assembly of vessels. Logistics and warehousing also benefit significantly from gantry systems. In these settings, gantries are used for loading and unloading heavy cargo from trucks or ships. They streamline the material handling process, ensuring that goods are moved quickly and safely. This is particularly important in ports where gantry cranes are indispensable for container handling, allowing for rapid turnaround times and increased throughput. The use of gantry systems in these sectors is not only about lifting capacity but also about precision and control. Modern gantries are equipped with advanced technologies such as automated control systems and sensors that ensure accurate placement of loads. This level of precision minimizes the risk of damage to both the load and the surrounding infrastructure. Moreover, gantry systems are designed to be adaptable to different environments and tasks. They can be customized to meet specific needs, whether it's for indoor manufacturing facilities or outdoor construction sites. Their modular design allows for easy assembly and disassembly, making them a cost-effective solution for temporary or long-term projects. In summary, gantry systems are indispensable tools in construction and heavy lifting operations across various sectors. Their ability to handle heavy loads with precision and safety makes them a crucial component of modern industrial practices. Whether it's in construction, manufacturing, or logistics, gantries enhance efficiency, reduce risks, and contribute significantly to the overall success of projects.
Medical and Healthcare Settings
In medical and healthcare settings, gantry systems play a crucial role in enhancing patient care and treatment outcomes. These systems, characterized by their overhead structure and movable components, are particularly valuable in diagnostic imaging and surgical procedures. For instance, in radiology departments, gantry-based MRI (Magnetic Resonance Imaging) machines allow for precise and detailed imaging of the body's internal structures. The gantry's ability to rotate and adjust its position ensures comprehensive coverage and high-resolution images, which are essential for accurate diagnoses. In surgical settings, gantry systems support advanced robotic surgery platforms. These platforms enable surgeons to perform complex procedures with greater precision and minimal invasiveness. The gantry's flexibility allows for optimal positioning of surgical instruments, enhancing the surgeon's dexterity and reducing recovery times for patients. Additionally, gantry systems are integral to radiation therapy, where they facilitate precise targeting of tumors during treatments like linear accelerator (linac) therapy. This precision minimizes damage to surrounding healthy tissue, improving treatment efficacy and patient safety. Furthermore, gantry systems contribute to patient safety by providing stable and secure environments for medical procedures. In operating rooms, they can support lighting and monitoring equipment, ensuring that medical teams have clear visibility and real-time data during surgeries. In rehabilitation settings, gantry-based systems can assist in physical therapy by providing adjustable support structures that help patients regain mobility and strength. The integration of gantry systems with advanced technologies such as AI and IoT further enhances their utility in healthcare. For example, AI-driven gantries can optimize imaging protocols based on patient data, while IoT connectivity enables real-time monitoring and remote maintenance of medical equipment. This synergy between gantry systems and cutting-edge technology not only improves the efficiency of healthcare operations but also contributes to better patient outcomes. Overall, the versatility and precision of gantry systems make them indispensable in various medical and healthcare applications, from diagnostic imaging to surgical interventions and patient care. Their ability to adapt to different clinical needs underscores their importance in modern healthcare infrastructure.
Technological Advancements and Future Trends in Gantry Systems
The evolution of gantry systems has been marked by significant technological advancements, setting the stage for a future that promises even greater efficiency, sustainability, and innovation. At the heart of these developments are three key areas: integration with automation and robotics, advances in materials and structural integrity, and sustainability and energy efficiency improvements. As gantry systems become increasingly integrated with automation and robotics, they are transforming industrial processes by enhancing precision, speed, and reliability. This integration is not only streamlining operations but also enabling the handling of complex tasks with unprecedented accuracy. Additionally, breakthroughs in materials science are leading to the development of stronger, lighter, and more durable gantry structures, which in turn are expanding their applications across various industries. Furthermore, a growing focus on sustainability is driving innovations that make gantry systems more energy-efficient, reducing their environmental footprint while maintaining performance. As we delve into these advancements, it becomes clear that the integration of automation and robotics is a pivotal trend that will continue to shape the future of gantry systems. This integration is poised to revolutionize how gantries operate, making them indispensable tools in modern manufacturing and beyond.
Integration with Automation and Robotics
Integration with automation and robotics is a pivotal aspect of technological advancements in gantry systems, significantly enhancing their efficiency, precision, and versatility. By leveraging advanced automation technologies, gantry systems can be seamlessly integrated with robotic arms, vision systems, and other intelligent devices to perform complex tasks with minimal human intervention. This integration allows for real-time data exchange and synchronization between different components, enabling precise control over the movement and operation of the gantry. For instance, robotic arms can be mounted on gantries to handle delicate or heavy payloads with high accuracy, while vision systems can provide real-time feedback to adjust the gantry's movement based on environmental changes or specific task requirements. The use of automation in gantry systems also facilitates the implementation of Industry 4.0 principles, such as predictive maintenance and smart manufacturing. Advanced sensors and IoT devices embedded within the gantry system can monitor performance metrics and predict potential failures, allowing for proactive maintenance and reducing downtime. Additionally, machine learning algorithms can analyze operational data to optimize gantry movements and improve overall system efficiency. This level of automation not only enhances productivity but also ensures a safer working environment by minimizing the risk of human error. In terms of future trends, the integration of gantry systems with emerging technologies like artificial intelligence (AI) and the Internet of Things (IoT) is expected to drive further innovation. AI can enable gantries to adapt to changing conditions autonomously, such as adjusting speed or trajectory based on real-time data from sensors. The IoT will continue to play a crucial role in connecting gantry systems with other machinery and devices within a factory setting, fostering a more interconnected and efficient manufacturing ecosystem. Furthermore, advancements in robotics will lead to more sophisticated and flexible gantry designs capable of performing a wider range of tasks with greater precision. Overall, the integration of automation and robotics into gantry systems represents a significant leap forward in technological capabilities, offering enhanced performance, increased safety, and improved operational efficiency. As these technologies continue to evolve, we can expect even more sophisticated and intelligent gantry systems that will redefine the landscape of modern manufacturing and industrial processes.
Advances in Materials and Structural Integrity
Advances in materials and structural integrity have significantly impacted the development and performance of gantry systems, driving technological advancements and future trends. The integration of high-strength, lightweight materials such as advanced alloys, carbon fiber reinforced polymers (CFRP), and smart materials has enhanced the structural efficiency of gantries. These materials offer superior strength-to-weight ratios, allowing for the construction of larger, more precise gantries without compromising on stability or increasing the overall weight. For instance, CFRP is widely used due to its exceptional tensile strength, corrosion resistance, and reduced maintenance requirements, making it ideal for applications in harsh environments. Furthermore, advancements in material science have led to the development of self-healing materials and shape memory alloys (SMAs), which can adapt to changing conditions and recover from deformation. These innovative materials enable gantries to maintain their structural integrity under various loads and environmental stresses, ensuring consistent performance over extended periods. Additionally, the use of advanced composites has facilitated the creation of complex geometries that optimize structural performance while minimizing material usage. In terms of structural integrity, advancements in computational modeling and simulation tools have revolutionized the design process. Finite element analysis (FEA) and computational fluid dynamics (CFD) allow engineers to simulate various loading conditions, predict potential failures, and optimize gantry designs for maximum efficiency and safety. These tools also enable real-time monitoring and predictive maintenance, reducing downtime and extending the lifespan of gantry systems. The integration of sensors and IoT technologies into gantry structures has further enhanced their reliability and longevity. Real-time data from sensors can be used to monitor stress levels, detect anomalies, and predict maintenance needs, ensuring proactive measures are taken to prevent failures. This convergence of materials science, computational engineering, and IoT technologies is setting the stage for future trends in gantry systems, including the development of autonomous gantries capable of self-diagnosis and adaptive operation. In conclusion, the synergy between advanced materials and enhanced structural integrity is pivotal in driving the evolution of gantry systems. As these technologies continue to advance, we can expect gantries to become even more robust, efficient, and intelligent, catering to a wide range of applications from manufacturing and logistics to medical and aerospace industries. The future of gantry systems promises increased precision, reliability, and adaptability, underscoring the critical role that advances in materials and structural integrity play in shaping technological trends.
Sustainability and Energy Efficiency Improvements
Sustainability and energy efficiency improvements are pivotal in the context of technological advancements and future trends in gantry systems. As industries strive to reduce their environmental footprint, gantry systems are being designed with enhanced energy-saving features. One key area of focus is the integration of advanced motor technologies, such as high-efficiency servo motors and variable frequency drives, which significantly reduce energy consumption by optimizing power usage according to the specific demands of the system. Additionally, the adoption of regenerative braking systems allows gantry systems to capture and reuse kinetic energy, further minimizing energy waste. The incorporation of smart sensors and IoT technologies enables real-time monitoring and optimization of system performance, ensuring that gantries operate at peak efficiency while minimizing downtime. Moreover, the use of lightweight materials and aerodynamic designs reduces the overall weight and drag of the gantry, thereby lowering the energy required for movement. Solar panels and other renewable energy sources are also being integrated into gantry systems to provide a sustainable power supply, especially in applications where traditional power sources are limited or unreliable. Innovative control algorithms and machine learning techniques are being implemented to predict and adapt to changing operational conditions, ensuring that the gantry operates at optimal efficiency levels. Furthermore, modular designs allow for easier maintenance and upgradeability, extending the lifespan of the system and reducing electronic waste. These advancements not only contribute to a more sustainable future but also enhance the overall performance, reliability, and cost-effectiveness of gantry systems, making them a cornerstone of modern industrial automation. By leveraging these technologies, industries can achieve significant reductions in their carbon footprint while maintaining or even improving productivity levels.