What Is A Torque Wrench

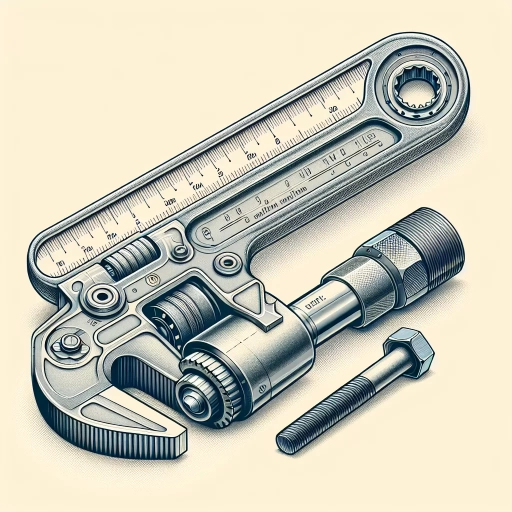
Understanding the Basics of a Torque Wrench
Understanding the basics of a torque wrench is essential for anyone involved in precision engineering, automotive repair, or any field requiring accurate bolt tightening. This tool is not just a simple gadget but a critical instrument that ensures safety and reliability in various applications. To grasp its significance, it is important to delve into three key aspects: the definition and purpose of a torque wrench, its key components and design, and the various types available. Firstly, understanding the definition and purpose of a torque wrench sets the foundation for its proper use. This involves recognizing how it measures and applies a specific amount of rotational force to bolts and fasteners, ensuring they are neither over-tightened nor under-tightened. Secondly, knowing the key components and design of a torque wrench helps in appreciating its functionality. From the handle to the drive head, each part plays a crucial role in delivering precise torque measurements. Lastly, familiarizing oneself with the different types of torque wrenches available is vital for selecting the right tool for specific tasks. Whether it's a click-type, digital, or slip-type wrench, each has its own advantages and applications. By exploring these facets, users can ensure they are using their torque wrenches effectively and safely. Let's begin by examining the definition and purpose of this indispensable tool.
Definition and Purpose
### Definition and Purpose A torque wrench is a precision tool designed to apply a specific amount of rotational force, or torque, to a bolt or nut. The primary purpose of a torque wrench is to ensure that fasteners are tightened to the exact specification required by the manufacturer, thereby preventing over-tightening or under-tightening. Over-tightening can lead to damage of the fastener or the material it is securing, while under-tightening can result in loose connections that may fail under stress. This tool is indispensable in various industries such as automotive, aerospace, construction, and engineering, where precise torque control is critical for safety and reliability. The definition of a torque wrench encompasses its mechanical or electronic mechanism that measures and limits the amount of torque applied. Traditional mechanical torque wrenches use a spring-loaded mechanism that triggers a click or slip when the set torque value is reached. Modern electronic torque wrenches, on the other hand, use digital displays and audible signals to indicate when the desired torque has been achieved. Both types ensure consistent and accurate application of torque, reducing human error and enhancing the quality of work. The purpose of using a torque wrench extends beyond mere tightening; it is about ensuring structural integrity and longevity. For instance, in automotive applications, proper torque ensures that engine components like cylinder heads and wheel lug nuts are securely fastened without causing damage to threads or gaskets. In aerospace, precise torque is crucial for assembling critical components where failure could have catastrophic consequences. In construction, it guarantees that bolts and nuts holding together heavy machinery or structural elements are securely fastened to withstand various environmental stresses. Moreover, the use of a torque wrench promotes uniformity in assembly processes. It helps in maintaining consistency across different tasks and operators, which is particularly important in high-volume manufacturing environments. This consistency not only improves product quality but also reduces the risk of human error, thereby enhancing overall safety standards. In summary, the definition and purpose of a torque wrench are intertwined with precision, safety, and reliability. By providing an accurate and controlled application of rotational force, this tool plays a vital role in ensuring that fasteners are tightened correctly, thereby safeguarding against potential failures and enhancing the overall performance of assembled components. Understanding the basics of a torque wrench is essential for anyone involved in industries where precise torque control is paramount.
Key Components and Design
When delving into the intricacies of a torque wrench, understanding its key components and design is crucial for effective usage and maintenance. At the heart of any torque wrench lies the **mechanism**, which can vary depending on the type. The most common types include **click-type**, **slip-type**, and **digital torque wrenches**. Click-type wrenches, for instance, use a mechanical mechanism that produces an audible click when the set torque is reached, signaling the user to stop applying force. Slip-type wrenches, on the other hand, slip or release when the torque limit is exceeded, preventing over-tightening. Digital torque wrenches utilize electronic sensors and displays to provide precise readings and often include additional features such as memory storage and unit conversion. Another critical component is the **handle**, which must be ergonomically designed to reduce user fatigue and ensure a secure grip. Handles can be made from various materials like steel, aluminum, or even composite materials, each offering different levels of durability and weight distribution. The **shaft** or **drive** connects the handle to the **socket** or **attachment**, and its length and material can affect the overall leverage and accuracy of the wrench. High-quality torque wrenches often feature **chrome vanadium steel** shafts for strength and resistance to wear. The **socket** or **attachment** is where the wrench interfaces with the bolt or nut. These come in various sizes and types (e.g., square drive, hex drive) to accommodate different fasteners. Ensuring that the socket fits snugly onto the fastener is essential for accurate torque application and to prevent damage to both the wrench and the fastener. **Calibration** is also a vital aspect of torque wrench design. A well-calibrated wrench ensures that it delivers consistent and accurate torque readings. Manufacturers typically calibrate their wrenches at multiple points across the torque range to guarantee precision. Users should also periodically check and recalibrate their wrenches according to manufacturer guidelines to maintain reliability. In addition to these core components, modern torque wrenches may include **additional features** such as adjustable torque settings, reversible mechanisms for both clockwise and counterclockwise operation, and storage cases to protect the tool when not in use. Some advanced models even integrate with smartphones or tablets via Bluetooth for data logging and analysis. Understanding these key components and their roles within the overall design of a torque wrench not only enhances user proficiency but also ensures that tasks are completed safely and efficiently. By recognizing how each part contributes to the tool's functionality, users can better appreciate the engineering that goes into creating such precise instruments, ultimately leading to more accurate and reliable torque applications in various industrial, automotive, and DIY contexts.
Types of Torque Wrenches
When delving into the world of torque wrenches, it is crucial to understand the various types available, each designed to cater to different needs and applications. At the core of any torque wrench is its ability to apply a precise amount of rotational force, but the mechanisms and features can vary significantly. **1. Click-Type Torque Wrenches:** These are perhaps the most common and widely used type. They operate by using a spring-loaded mechanism that triggers a audible click when the set torque value is reached. This click indicates that the desired torque has been applied, providing a clear and reliable signal to the user. Click-type wrenches are versatile and can be used in a variety of settings, from automotive to industrial applications. **2. Slip-Type Torque Wrenches:** Unlike click-type wrenches, slip-type torque wrenches do not produce an audible signal but instead slip or release when the set torque is achieved. This type is often preferred in situations where noise needs to be minimized or where the user requires a more subtle indication of reaching the desired torque. **3. Digital Torque Wrenches:** Incorporating modern technology, digital torque wrenches offer enhanced precision and convenience. These tools display the applied torque on an LCD screen and often include features such as memory storage for previous readings, multiple unit measurements (e.g., Nm, ft-lbs), and even Bluetooth connectivity for data transfer. Digital torque wrenches are ideal for applications requiring high accuracy and detailed record-keeping. **4. Pneumatic Torque Wrenches:** These wrenches utilize compressed air to generate torque, making them particularly useful in heavy-duty industrial environments where high levels of torque are required. Pneumatic torque wrenches are often used in oil and gas, mining, and construction industries due to their ability to apply consistent and powerful rotational force. **5. Hydraulic Torque Wrenches:** Similar to pneumatic wrenches but using hydraulic fluid instead of compressed air, these tools are designed for extreme torque applications. Hydraulic torque wrenches are typically used in heavy industries such as power generation and petrochemicals where bolts and fasteners need to be tightened with immense force. **6. Adjustable vs. Fixed Torque Wrenches:** Torque wrenches can also be categorized based on their adjustability. Adjustable torque wrenches allow users to set different torque values depending on the task at hand, offering flexibility across various projects. Fixed torque wrenches, on the other hand, are set to a specific torque value during manufacturing and are often used in quality control or production environments where consistency is paramount. Understanding these different types of torque wrenches is essential for selecting the right tool for your specific needs. Whether you are working in a professional setting or tackling DIY projects, choosing the appropriate torque wrench ensures that bolts and fasteners are tightened correctly, preventing damage or failure due to over- or under-tightening. By recognizing the unique features and applications of each type, you can enhance your efficiency and accuracy in any task that requires precise rotational force.
How to Use a Torque Wrench Effectively
Using a torque wrench effectively is crucial for ensuring the integrity and safety of various mechanical assemblies. This tool, when employed correctly, can prevent over-tightening or under-tightening, which can lead to component failure or damage. To master the use of a torque wrench, it is essential to follow a step-by-step application guide that outlines the proper procedures for each task. Additionally, understanding the importance of calibration and maintenance is vital to ensure the wrench remains accurate and reliable over time. However, even with the best practices in place, common mistakes can still occur, and being aware of these pitfalls is key to avoiding them. By adhering to these guidelines, you can guarantee that your work is precise and durable. In this article, we will delve into these critical aspects, starting with a detailed step-by-step application guide to help you get started on using your torque wrench effectively.
Step-by-Step Application Guide
To use a torque wrench effectively, it is crucial to follow a step-by-step application guide that ensures precision and safety. Here’s a detailed guide to help you master the process: 1. **Choose the Right Torque Wrench**: Select a torque wrench that matches the specifications of your project. Ensure it has the correct range and unit of measurement (e.g., ft-lbs, Nm) for your bolts or nuts. 2. **Read the Manual**: Before starting, read the manual provided with your torque wrench to understand its specific features and any unique instructions. 3. **Set the Torque Value**: Use the adjustment mechanism to set the desired torque value. This is usually done by rotating a dial or adjusting a lever until the desired number is aligned with an indicator mark. 4. **Position the Wrench**: Place the torque wrench on the bolt or nut, ensuring it is securely seated and aligned with the axis of the bolt. Make sure there are no obstructions that could interfere with the wrench’s operation. 5. **Apply Even Pressure**: Hold the wrench firmly but avoid applying excessive force, which could damage either the wrench or the bolt. Apply even pressure in a smooth, continuous motion until you hear a click or feel a slight release of tension, indicating that the set torque has been reached. 6. **Check and Verify**: After applying torque, double-check that the bolt or nut is tightened to the specified value by re-measuring with your torque wrench if necessary. 7. **Store Properly**: After use, store your torque wrench in a dry place away from direct sunlight and extreme temperatures to maintain its accuracy and longevity. 8. **Calibrate Regularly**: Regular calibration is essential to ensure accuracy over time. Follow manufacturer guidelines for calibration intervals and procedures. 9. **Maintain Cleanliness**: Keep your torque wrench clean and free from debris. Regularly inspect for signs of wear or damage and replace parts as needed according to manufacturer instructions. 10. **Practice Safety**: Always wear protective gear such as gloves and safety glasses when working with tools to prevent injury from flying debris or tool slippage. By following these steps meticulously, you can ensure that your torque wrench is used effectively and safely, thereby preventing over-tightening or under-tightening of bolts and nuts which can lead to serious mechanical failures or safety hazards. This methodical approach not only enhances precision but also prolongs the lifespan of both your tools and the components you are working on.
Importance of Calibration and Maintenance
Calibration and maintenance are crucial components in the effective use of a torque wrench, ensuring accuracy, reliability, and safety in various applications. Proper calibration guarantees that the torque wrench delivers precise torque values, which is essential for preventing damage to components, avoiding over-tightening or under-tightening, and maintaining the integrity of assemblies. Without regular calibration, a torque wrench can drift out of specification, leading to potential failures or malfunctions in critical systems such as automotive engines, aerospace components, or medical devices. Maintenance involves regular inspections to check for wear and tear on parts like the ratchet mechanism, handle, and drive shaft. Lubrication of moving parts and cleaning the tool can also extend its lifespan and maintain its performance. Additionally, storing the torque wrench in a dry environment away from direct sunlight and extreme temperatures helps preserve its accuracy. By adhering to a scheduled calibration and maintenance routine, users can ensure their torque wrench remains a trusted tool that consistently provides accurate readings, thereby enhancing overall efficiency and reducing the risk of errors. This meticulous approach not only safeguards the tool itself but also contributes to the quality and reliability of the work being performed, making it an indispensable practice for professionals across various industries. In essence, calibration and maintenance are not just supplementary tasks; they are integral to the effective use of a torque wrench and the success of any project that relies on precise torque application.
Common Mistakes to Avoid
When using a torque wrench effectively, it is crucial to avoid common mistakes that can lead to inaccurate readings, damage to the tool or the workpiece, and even safety hazards. One of the most frequent errors is failing to calibrate the torque wrench regularly. Calibration ensures that the wrench provides accurate torque measurements, which is vital for maintaining the integrity of bolts and fasteners. Neglecting this step can result in over- or under-tightening, potentially causing structural failures or other mechanical issues. Another critical mistake is not following the manufacturer's instructions for the specific torque wrench model. Each torque wrench has unique features and settings that must be understood and adhered to. Misunderstanding these guidelines can lead to improper use, such as applying too much force or using the wrong socket size, which can damage both the wrench and the fastener. Using a torque wrench at an angle is another common error. Torque wrenches are designed to be used in a straight line with the axis of the bolt or fastener. Applying torque at an angle can cause uneven stress distribution, leading to inaccurate readings and potential damage to the tool or workpiece. Additionally, many users overlook the importance of maintaining their torque wrenches. Regular cleaning and storage in a dry environment are essential to prevent rust and corrosion. Failing to do so can compromise the accuracy and longevity of the tool. Furthermore, not using the correct socket or adapter can significantly affect the performance of a torque wrench. Using a socket that does not fit snugly onto the bolt head can cause slippage, resulting in stripped threads or rounded bolt heads. Always ensure that the socket is securely seated before applying torque. It is also important to avoid using a torque wrench as a breaker bar or ratchet. These tools are designed for different purposes and using them interchangeably can lead to misuse and potential damage. A breaker bar is meant for loosening stuck fasteners, while a ratchet is used for applying continuous force; neither should be used as a substitute for a precision torque wrench. Lastly, ignoring the audible or visual signals provided by some torque wrenches is a significant oversight. These signals indicate when the set torque value has been reached, ensuring that bolts are tightened to the correct specification without over-tightening. Disregarding these signals can lead to over-torquing, which may cause damage to threads or other components. By being aware of these common mistakes and taking steps to avoid them, users can ensure that their torque wrenches function accurately and reliably, thereby enhancing the quality and safety of their work. Proper use not only extends the life of the tool but also guarantees that bolts and fasteners are tightened correctly, preventing potential failures and ensuring optimal performance of machinery and structures.
Applications and Benefits of Using a Torque Wrench
The use of a torque wrench is a cornerstone in various industries, offering a multitude of benefits that enhance both the efficiency and safety of operations. This versatile tool is indispensable in industrial and automotive settings, where precise torque application is crucial for ensuring the integrity of assemblies and preventing potential failures. Beyond its practical applications, a torque wrench also plays a significant role in ensuring safety and precision, as it helps avoid over-tightening or under-tightening, which can lead to catastrophic consequences. Additionally, the cost-effective and time-saving nature of torque wrenches makes them an essential asset for any workshop or manufacturing facility. By leveraging these advantages, professionals can streamline their processes, reduce errors, and maintain high standards of quality. In this article, we will delve into the industrial and automotive uses of torque wrenches, exploring how they contribute to the overall performance and reliability of machinery and vehicles. --- **Industrial and Automotive Uses**
Industrial and Automotive Uses
In the realms of industrial and automotive applications, the torque wrench is an indispensable tool that ensures precision, safety, and efficiency. Within industrial settings, torque wrenches are crucial for assembling and maintaining complex machinery. For instance, in manufacturing plants, these tools are used to tighten bolts and screws to exact specifications, preventing over-tightening which can lead to material damage or under-tightening which can result in loose connections that compromise the integrity of the equipment. This precision is particularly vital in industries such as aerospace and energy production where even slight deviations from specified torque values can have catastrophic consequences. In the automotive sector, torque wrenches play a pivotal role in both routine maintenance and critical repairs. Mechanics rely on these tools to ensure that engine components, suspension parts, and other critical systems are secured with the correct amount of force. For example, when replacing a cylinder head or tightening wheel lug nuts, using a torque wrench guarantees that the bolts are tightened to the manufacturer's specifications. This not only prevents damage to the vehicle but also ensures safety on the road by minimizing the risk of parts coming loose during operation. Moreover, torque wrenches contribute significantly to quality control and compliance with regulatory standards. In industries governed by strict safety protocols like automotive and aerospace, documentation of torque values applied during assembly or maintenance is often required. Torque wrenches equipped with digital readouts or memory functions facilitate this process by providing accurate records of applied torque, thereby enhancing traceability and accountability. Additionally, the use of torque wrenches in industrial and automotive contexts extends beyond mere functionality; it also enhances operational efficiency. By ensuring that all bolts and screws are tightened uniformly and correctly, technicians can reduce the time spent on rework and minimize downtime due to faulty assemblies. This streamlined workflow translates into cost savings and improved productivity. From a safety perspective, torque wrenches are essential for preventing accidents caused by improperly secured components. In high-stress environments such as construction sites or race tracks, the failure of a single bolt can lead to severe consequences including equipment failure or even loss of life. By adhering strictly to recommended torque specifications using a reliable torque wrench, professionals can significantly mitigate these risks. In summary, the industrial and automotive uses of torque wrenches underscore their importance as precision instruments that safeguard against potential hazards while optimizing operational efficiency. Whether in manufacturing plants or automotive repair shops, these tools are indispensable for ensuring that assemblies meet stringent quality standards and remain safe under various operating conditions. Their role in maintaining compliance with regulatory requirements further solidifies their position as essential tools in these critical industries.
Ensuring Safety and Precision
Ensuring safety and precision is paramount when utilizing a torque wrench, as it directly impacts the reliability and longevity of the assembled components. A torque wrench is designed to apply a specific amount of rotational force to a bolt or nut, preventing over-tightening or under-tightening, which can lead to catastrophic failures. In critical applications such as aerospace, automotive, and industrial manufacturing, the accuracy of torque application is not just a matter of quality control but also a safety imperative. For instance, in the automotive sector, improper torque can result in loose bolts that may cause wheel detachment or engine failure while driving, posing significant risks to both the vehicle occupants and other road users. Similarly, in aerospace engineering, precise torque specifications are crucial to ensure that aircraft components are securely fastened to withstand the stresses of flight. The precision offered by a torque wrench also extends to the realm of maintenance and repair. Technicians rely on these tools to ensure that parts are reassembled correctly after servicing, thereby preventing premature wear and tear. This not only enhances the overall performance of machinery but also reduces downtime and maintenance costs in the long run. Additionally, using a torque wrench helps in maintaining consistent quality standards across different assembly lines and workshops, which is essential for compliance with industry regulations and standards. Moreover, modern torque wrenches often come equipped with advanced features such as digital displays, audible signals, and slip-resistant handles that further enhance safety and precision. These features allow users to monitor the applied torque in real-time, ensuring that they do not exceed or fall short of the recommended specifications. The ergonomic design of these tools also reduces user fatigue and improves grip stability, minimizing the risk of accidents caused by slippage or loss of control. In summary, ensuring safety and precision with a torque wrench is fundamental across various industries where mechanical integrity is critical. By adhering to specified torque values and leveraging the advanced features of modern torque wrenches, professionals can significantly reduce the risk of mechanical failures, enhance product reliability, and maintain high standards of quality and safety. This underscores the importance of integrating torque wrenches into standard operating procedures for any application requiring precise bolt tightening or loosening.
Cost-Effective and Time-Saving
In the realm of precision and efficiency, the use of a torque wrench stands out as a cost-effective and time-saving tool in various applications. When it comes to ensuring that bolts and nuts are tightened to the exact specifications required, a torque wrench is indispensable. This precision instrument eliminates the guesswork associated with manual tightening, thereby reducing the risk of over-tightening or under-tightening, which can lead to costly repairs or even safety hazards. By providing a precise measurement of torque, it helps in maintaining the integrity of the assembly, extending the lifespan of components, and preventing premature wear and tear. From automotive maintenance to aerospace engineering, the benefits of using a torque wrench are multifaceted. In automotive repair shops, for instance, technicians can quickly and accurately tighten bolts on engines, transmissions, and other critical components without risking damage. This not only saves time but also ensures that vehicles are safe to operate, reducing the likelihood of mechanical failures that could result in costly repairs or accidents. In industrial settings, such as manufacturing plants and construction sites, torque wrenches are essential for ensuring that machinery and equipment are assembled correctly, thereby enhancing operational efficiency and reducing downtime. Moreover, the use of a torque wrench promotes consistency across different tasks and projects. For example, in the aerospace industry where precision is paramount, torque wrenches guarantee that every bolt and nut is tightened to the exact specification required by regulatory standards. This consistency is crucial for maintaining the safety and reliability of aircraft components. Additionally, in DIY projects around the home or workshop, a torque wrench can be a valuable asset for hobbyists and enthusiasts who need to ensure that their projects are built to last. The cost-effectiveness of a torque wrench lies in its ability to prevent errors that could lead to significant financial losses. Over-tightening can damage threads or strip bolts, while under-tightening can result in loose connections that may fail under stress. By avoiding these common pitfalls, users can save money on replacement parts and labor costs associated with rework. Furthermore, the durability of a well-maintained torque wrench means it can be used for years with minimal maintenance, making it a worthwhile investment for both professionals and amateurs alike. In summary, incorporating a torque wrench into your toolkit offers a dual advantage of being both cost-effective and time-saving. It ensures precision in tightening bolts and nuts, thereby enhancing the reliability and longevity of assemblies. Whether in professional settings or personal projects, this versatile tool is an essential asset that promotes efficiency, safety, and cost savings. By leveraging the precise control offered by a torque wrench, users can streamline their work processes, reduce errors, and achieve superior results consistently.