What Is Dcs/dec

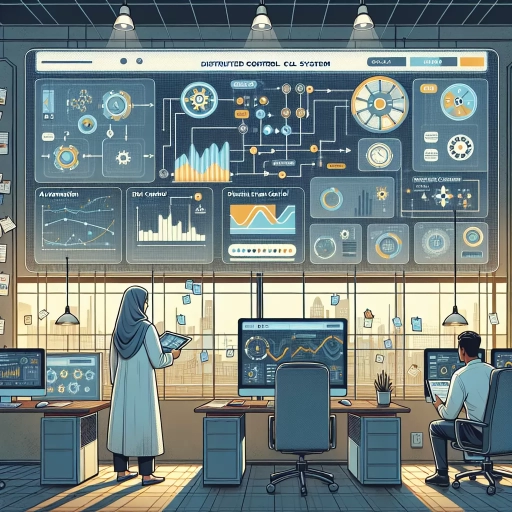
In the realm of industrial automation, Distributed Control Systems (DCS) and Digital Electronic Control (DEC) play pivotal roles in enhancing efficiency, reliability, and precision. These advanced technologies have revolutionized the way industries operate by integrating various control functions into a unified system. To fully appreciate the impact of DCS/DEC, it is essential to delve into their fundamental principles, explore their diverse applications, and examine both the benefits and challenges associated with their implementation. Understanding the basics of DCS/DEC is crucial as it lays the groundwork for comprehending how these systems are applied in various sectors, from manufacturing to energy production. By grasping the applications and uses of DCS/DEC, one can see how they streamline processes and improve performance. Additionally, recognizing the benefits and challenges of implementing these systems helps in making informed decisions about their adoption. In this article, we will start by understanding the basics of DCS/DEC, setting the stage for a deeper exploration of their applications and the advantages and challenges they present.
Understanding the Basics of DCS/DEC
In the realm of industrial automation, Distributed Control Systems (DCS) and Digital Electronic Control (DEC) play pivotal roles in ensuring the efficient and reliable operation of complex processes. To fully grasp the significance and functionality of these systems, it is essential to delve into their fundamental aspects. This article aims to provide a comprehensive understanding of DCS/DEC by exploring three critical dimensions: **Definition and Acronym Explanation**, which clarifies the terminology and acronyms associated with these systems; **Historical Context and Development**, which traces the evolution and milestones in the development of DCS/DEC; and **Key Components and Architecture**, which details the structural elements and operational framework of these control systems. By examining these facets, readers will gain a solid foundation in understanding the basics of DCS/DEC, enabling them to appreciate their importance in modern industrial settings. This knowledge is crucial for anyone seeking to navigate the intricacies of industrial automation effectively. Understanding the Basics of DCS/DEC is therefore a vital step in mastering the tools that drive contemporary manufacturing and process control.
Definition and Acronym Explanation
**Understanding the Basics of DCS/DEC: Definition and Acronym Explanation** To delve into the intricacies of Distributed Control Systems (DCS) and Digital Electronic Control (DEC), it is essential to start with a clear understanding of what these terms mean. **DCS**, or Distributed Control Systems, refers to a type of control system that uses a network of controllers and sensors to monitor and control industrial processes. Unlike centralized control systems, DCS distributes control functions across various nodes or stations, enhancing flexibility, reliability, and scalability. Each node in the DCS can operate independently but also communicates with other nodes to ensure cohesive system operation. On the other hand, **DEC**, or Digital Electronic Control, pertains to the use of digital technology for controlling electronic devices and systems. This involves the application of microprocessors, programmable logic controllers (PLCs), and other digital components to manage and regulate various processes. DEC is integral in modern automation because it allows for precise control, real-time monitoring, and efficient data processing. The distinction between DCS and DEC lies in their scope and application. While DCS is a broader system architecture designed for complex industrial processes, DEC focuses on the specific digital technologies used within these systems. In practice, DCS often incorporates DEC elements to achieve advanced automation capabilities. For instance, in a manufacturing plant, a DCS might oversee overall production processes, while DEC components such as PLCs and microcontrollers handle specific tasks like temperature control or motor speed regulation. Understanding these definitions is crucial for grasping how these systems work together to optimize industrial operations. By recognizing the roles of both DCS and DEC, engineers and operators can better design, implement, and maintain sophisticated control systems that enhance productivity, safety, and efficiency. This foundational knowledge also sets the stage for exploring more advanced topics in automation technology, such as system integration, data analytics, and cybersecurity measures. As industries continue to evolve with technological advancements, a solid comprehension of DCS and DEC remains vital for staying at the forefront of industrial automation.
Historical Context and Development
The historical context and development of Distributed Control Systems (DCS) and Digital Electronic Control (DEC) are deeply intertwined with the evolution of industrial automation. In the early 20th century, industrial processes were primarily controlled by manual operators or simple mechanical systems. However, as industries grew in complexity and scale, the need for more sophisticated control mechanisms became evident. The advent of electronic control systems in the mid-20th century marked a significant turning point. The 1960s saw the introduction of the first digital computers, which laid the groundwork for modern control systems. These early digital systems were cumbersome and expensive but paved the way for future innovations. The 1970s witnessed the emergence of DCS, which integrated various control functions into a single, cohesive system. Companies like Honeywell and Yokogawa were among the pioneers in this field, developing systems that could monitor and control multiple processes simultaneously. The 1980s brought significant advancements with the introduction of microprocessors and personal computers, which further democratized access to digital control technologies. This period also saw the development of DEC systems, which focused on precision and reliability in electronic control. DEC systems were particularly influential in high-precision applications such as aerospace and automotive manufacturing. Throughout the 1990s and 2000s, advancements in networking technologies and software development led to more integrated and networked control systems. The widespread adoption of Ethernet and other communication protocols enabled real-time data exchange between different parts of a plant, enhancing overall efficiency and reliability. Modern DCS/DEC systems now incorporate advanced technologies such as artificial intelligence, machine learning, and the Internet of Things (IoT), allowing for predictive maintenance, optimized performance, and enhanced safety. Understanding this historical context is crucial for appreciating the current state of DCS/DEC technology. It highlights how these systems have evolved from simple mechanical controls to sophisticated digital networks capable of managing complex industrial processes with precision and reliability. This evolution underscores the continuous innovation driven by technological advancements and industrial needs, ultimately leading to more efficient, safe, and productive operations across various sectors. By grasping this developmental journey, users can better leverage the capabilities of modern DCS/DEC systems to optimize their operations and stay competitive in an increasingly automated world.
Key Components and Architecture
Understanding the basics of Distributed Control Systems (DCS) and Distributed Engineering Controllers (DEC) hinges on grasping their key components and architecture. At the heart of a DCS/DEC system lies a robust network infrastructure that facilitates real-time communication between various control elements. This network is typically built around a combination of hardware and software components, each playing a critical role in the overall functionality. **Key Components:** 1. **Control Processors:** These are the brain of the DCS/DEC, responsible for executing control algorithms and managing data exchange. They are usually high-performance computers or specialized control units. 2. **Input/Output (I/O) Modules:** These modules interface with field devices such as sensors, actuators, and valves, converting raw data into a format understandable by the control processors. 3. **Human-Machine Interface (HMI):** HMIs provide operators with a user-friendly interface to monitor and control the process. They can include graphical displays, alarms, and trending capabilities. 4. **Communication Networks:** These networks, often based on industrial protocols like Ethernet or fieldbus standards, ensure seamless data exchange between different parts of the system. 5. **Field Devices:** Sensors, actuators, and other field devices are integral for collecting data and executing control actions in real-time. **Architecture:** The architecture of a DCS/DEC system is designed for redundancy, reliability, and scalability. It typically follows a hierarchical structure: 1. **Field Level:** This level involves field devices that interact directly with the process. 2. **Control Level:** Here, control processors and I/O modules work together to execute control strategies based on data from field devices. 3. **Supervisory Level:** HMIs and supervisory control software reside at this level, enabling operators to monitor and adjust the process as needed. 4. **Enterprise Level:** This level integrates with higher-level systems such as enterprise resource planning (ERP) and manufacturing execution systems (MES) for broader business management. In addition to this hierarchical structure, modern DCS/DEC systems often incorporate advanced features such as redundancy in critical components, secure communication protocols, and integration with other automation technologies like Programmable Logic Controllers (PLCs) and Supervisory Control and Data Acquisition (SCADA) systems. The modular design allows for easy expansion or modification as process requirements evolve, making DCS/DEC systems highly adaptable and efficient solutions for complex industrial processes. By understanding these key components and architectural elements, users can better appreciate how DCS/DEC systems optimize process control, enhance operational efficiency, and ensure reliability in demanding industrial environments.
Applications and Uses of DCS/DEC
In the realm of modern industrial operations, Distributed Control Systems (DCS) and Digital Electronic Controllers (DEC) play a pivotal role in enhancing efficiency, reliability, and precision. These advanced technologies have revolutionized various sectors by offering robust solutions for industrial automation and control systems, enabling seamless real-time data processing and monitoring, and facilitating integration with other cutting-edge technologies. The applications of DCS/DEC are multifaceted, ranging from optimizing production processes in manufacturing plants to ensuring the smooth operation of critical infrastructure such as power plants and water treatment facilities. By delving into the industrial automation and control systems facilitated by DCS/DEC, we can understand how these systems automate complex processes, reducing human error and increasing productivity. Additionally, the real-time data processing and monitoring capabilities of DCS/DEC allow for immediate response to changes in operational conditions, ensuring optimal performance and safety. Furthermore, the integration of DCS/DEC with other technologies like IoT and AI enhances their functionality, making them indispensable in today's interconnected world. To fully appreciate these advancements, it is essential to start by understanding the basics of DCS/DEC.
Industrial Automation and Control Systems
Industrial automation and control systems are the backbone of modern manufacturing, significantly enhancing efficiency, productivity, and safety across various industries. At the heart of these systems lies the Distributed Control System (DCS) and the Digital Electronic Control (DEC) system, which play pivotal roles in managing complex processes. DCS/DEC systems are designed to monitor and control multiple aspects of industrial operations, from temperature and pressure to flow rates and quality parameters. These advanced control systems integrate sensors, actuators, and control algorithms to ensure real-time data acquisition, precise control actions, and continuous process optimization. In applications such as chemical processing, oil refining, and power generation, DCS/DEC systems are indispensable for maintaining operational stability and achieving high-quality output. For instance, in a chemical plant, a DCS can manage the entire production line by regulating chemical reactions, monitoring safety parameters, and adjusting process variables to meet product specifications. Similarly, in oil refineries, these systems help in optimizing crude oil processing by controlling temperature, pressure, and flow rates to maximize yield and minimize waste. The versatility of DCS/DEC extends beyond traditional manufacturing sectors. In water treatment plants, these systems ensure that water quality meets stringent standards by controlling pH levels, disinfection processes, and filtration rates. In the automotive industry, they are used in assembly lines to synchronize robotic movements, manage inventory, and maintain quality control. Additionally, in renewable energy sectors like wind farms and solar power plants, DCS/DEC systems optimize energy production by adjusting turbine angles or panel orientations based on real-time weather data. One of the key advantages of DCS/DEC is their ability to provide centralized control while allowing for decentralized execution. This architecture enables faster response times to process changes and enhances system reliability by minimizing single points of failure. Moreover, these systems support advanced analytics and machine learning algorithms, enabling predictive maintenance, energy efficiency improvements, and overall operational excellence. The integration of DCS/DEC with other technologies such as the Internet of Things (IoT), cloud computing, and artificial intelligence (AI) further amplifies their capabilities. This convergence allows for remote monitoring, real-time data analytics, and automated decision-making processes that drive continuous improvement in industrial operations. As industries continue to evolve towards Industry 4.0 standards, the role of DCS/DEC will become even more critical in enabling smart factories, optimizing resource usage, and ensuring sustainable growth. In summary, industrial automation and control systems powered by DCS/DEC are essential for modern industrial operations. Their widespread applications across diverse sectors underscore their importance in driving efficiency, safety, and quality. As technology continues to advance, the integration of these systems with emerging technologies will further enhance their capabilities, making them a cornerstone of future industrial development.
Real-Time Data Processing and Monitoring
Real-time data processing and monitoring are pivotal components of Distributed Control Systems (DCS) and Digital Electronic Control (DEC) systems, enabling immediate response to changing conditions in industrial environments. This capability is crucial for maintaining optimal performance, ensuring safety, and reducing downtime. In real-time data processing, DCS/DEC systems continuously collect data from various sensors and field devices, process it instantly, and provide actionable insights. This allows operators to make informed decisions promptly, whether it's adjusting process parameters, detecting anomalies, or initiating corrective actions. The applications of real-time data processing and monitoring are diverse and impactful. For instance, in manufacturing plants, real-time monitoring helps in quality control by continuously tracking production parameters such as temperature, pressure, and flow rates. Any deviation from set points can trigger alerts, enabling swift intervention to prevent defects or equipment failure. In power generation and distribution, real-time data processing ensures grid stability by monitoring voltage levels, frequency, and load demand in real-time, facilitating quick adjustments to maintain supply reliability. In the oil and gas sector, real-time monitoring is essential for managing drilling operations, pipeline integrity, and refining processes. It helps in detecting potential leaks or equipment malfunctions early on, thereby preventing environmental disasters and ensuring compliance with safety regulations. Similarly, in healthcare facilities, real-time monitoring of critical systems like HVAC, power backup, and medical equipment ensures patient safety and comfort. The use of advanced analytics within DCS/DEC systems further enhances real-time data processing by predicting potential issues before they occur. Predictive maintenance, for example, uses historical data and machine learning algorithms to forecast when equipment might fail, allowing for scheduled maintenance rather than unplanned shutdowns. This proactive approach not only reduces maintenance costs but also improves overall plant reliability and efficiency. Moreover, the integration of IoT technologies with DCS/DEC systems expands the scope of real-time monitoring by connecting a vast array of devices across the enterprise. This interconnectedness facilitates holistic monitoring and control, enabling organizations to optimize their operations at a granular level. For instance, smart sensors can provide detailed insights into energy consumption patterns, helping companies implement energy-saving measures that contribute to sustainability goals. In summary, real-time data processing and monitoring are fundamental to the effective operation of DCS/DEC systems. By providing immediate access to critical information, these systems empower operators to respond swiftly to changing conditions, enhance operational efficiency, ensure safety, and drive innovation across various industries. As technology continues to evolve, the role of real-time data processing will only become more central to achieving excellence in industrial control and automation.
Integration with Other Technologies
Integration with other technologies is a crucial aspect of Distributed Control Systems (DCS) and Digital Electronic Controllers (DEC), as it enhances their functionality, efficiency, and adaptability in various industrial settings. Modern DCS/DEC systems are designed to seamlessly integrate with a wide range of technologies to create a cohesive and highly automated control environment. For instance, integration with Supervisory Control and Data Acquisition (SCADA) systems allows for real-time monitoring and control of processes over large geographical areas, enabling operators to make informed decisions quickly. Additionally, the integration of DCS/DEC with Enterprise Resource Planning (ERP) systems facilitates the exchange of data between production and business operations, streamlining inventory management, scheduling, and financial reporting. The incorporation of Internet of Things (IoT) devices into DCS/DEC networks expands the scope of data collection and analysis, enabling predictive maintenance and optimizing process performance. Advanced analytics and machine learning algorithms can be integrated to analyze the vast amounts of data generated by these systems, providing insights that can lead to significant improvements in operational efficiency and product quality. Furthermore, the integration with Human-Machine Interface (HMI) technologies ensures that operators have intuitive and user-friendly interfaces to interact with the control system, reducing errors and enhancing operational safety. In the realm of cybersecurity, integrating DCS/DEC with robust security protocols and intrusion detection systems is essential to protect against potential threats. This includes implementing secure communication protocols such as OPC-UA and ensuring compliance with industry standards like IEC 62443. The integration of DCS/DEC with other automation technologies such as Programmable Logic Controllers (PLCs) and Remote Terminal Units (RTUs) ensures a comprehensive control strategy that can be tailored to specific industrial needs. Moreover, the integration of DCS/DEC with emerging technologies like artificial intelligence (AI) and blockchain can revolutionize industrial processes by introducing autonomous decision-making capabilities and transparent data management. AI can optimize control strategies in real-time based on historical data and current conditions, while blockchain can ensure the integrity and traceability of data across the entire supply chain. In summary, the ability of DCS/DEC systems to integrate with various technologies is a key factor in their widespread adoption across industries. This integration not only enhances operational efficiency but also provides a robust framework for future technological advancements, making these systems indispensable for modern industrial automation. By leveraging these integrations, industries can achieve higher levels of automation, improved safety, and enhanced productivity, ultimately driving innovation and competitiveness in the global market.
Benefits and Challenges of Implementing DCS/DEC
In the modern industrial landscape, Distributed Control Systems (DCS) and Digital Electric Control (DEC) have emerged as pivotal technologies, transforming the way operations are managed and optimized. These advanced systems offer a myriad of benefits, including enhanced efficiency and productivity, which can significantly streamline processes and improve overall performance. However, their implementation is not without challenges. Cost considerations and Return on Investment (ROI) analysis are critical factors that must be carefully evaluated to ensure that the financial outlay is justified by the anticipated gains. Additionally, security concerns and maintenance requirements pose significant hurdles that need to be addressed to safeguard against potential risks and ensure continuous operation. As industries navigate these complexities, understanding the intricacies of DCS/DEC becomes essential. This article delves into the benefits and challenges associated with implementing these systems, providing a comprehensive overview that transitions seamlessly into understanding the basics of DCS/DEC. By exploring these key aspects, readers will gain a deeper insight into how to leverage these technologies effectively while mitigating potential drawbacks.
Enhanced Efficiency and Productivity
Enhanced efficiency and productivity are pivotal benefits of implementing Distributed Control Systems (DCS) and Digital Electronic Control (DEC) in various industrial settings. These advanced control systems revolutionize operational processes by integrating multiple control functions into a unified platform, thereby streamlining operations and reducing complexity. With DCS/DEC, real-time data monitoring and control become seamless, allowing for immediate adjustments to optimize performance. This real-time capability enhances predictive maintenance, enabling proactive measures to prevent downtime and reduce the likelihood of equipment failures. Additionally, automated workflows and optimized process control algorithms inherent in DCS/DEC systems lead to significant improvements in production quality and throughput. The centralized control architecture facilitates better decision-making by providing comprehensive insights into system performance, which in turn boosts overall operational efficiency. Moreover, the scalability of DCS/DEC systems allows for easy integration with existing infrastructure, making them adaptable to evolving industrial needs. This adaptability ensures that as production demands increase or new technologies emerge, the control system can be upgraded or expanded without major disruptions. The user-friendly interfaces and intuitive design of modern DCS/DEC systems also contribute to enhanced productivity by reducing the learning curve for operators, thereby minimizing errors and maximizing operational uptime. Furthermore, these systems often include advanced analytics and reporting tools that help in identifying bottlenecks and areas for improvement, facilitating continuous optimization. However, while these benefits are substantial, there are also challenges associated with the implementation of DCS/DEC. One of the primary challenges is the initial investment required for hardware, software, and training. The complexity of these systems can also necessitate specialized technical expertise for installation, configuration, and maintenance. Additionally, cybersecurity concerns arise with the increased connectivity and data exchange inherent in these systems, requiring robust security measures to protect against potential threats. Despite these challenges, the long-term gains in efficiency and productivity make DCS/DEC a valuable asset for industries seeking to modernize their operations and stay competitive in a rapidly evolving market landscape. By leveraging these advanced control systems effectively, businesses can achieve higher levels of operational excellence and sustainability.
Cost Considerations and ROI Analysis
When evaluating the implementation of Distributed Control Systems (DCS) or Distributed Energy Controllers (DEC), cost considerations and Return on Investment (ROI) analysis are crucial components that must be meticulously assessed. The initial investment in DCS/DEC can be substantial, encompassing hardware costs, software licenses, installation fees, and training expenses for personnel. However, these systems offer significant long-term benefits that can justify the upfront expenditure. One key cost consideration is the potential for energy efficiency improvements. DCS/DEC systems can optimize energy consumption by dynamically adjusting parameters based on real-time data, leading to reduced operational costs over time. For instance, in industrial settings, a DCS can fine-tune production processes to minimize energy usage without compromising output quality. Similarly, in buildings, a DEC can optimize HVAC and lighting systems to achieve optimal energy efficiency. Another critical aspect is the enhancement of system reliability and uptime. By providing real-time monitoring and predictive maintenance capabilities, DCS/DEC systems can help prevent costly downtime and extend the lifespan of equipment. This not only reduces maintenance costs but also ensures continuous operation, thereby safeguarding revenue streams. In addition to these operational savings, DCS/DEC implementations often lead to improved safety and compliance. Automated control systems can enforce safety protocols more consistently than manual operations, reducing the risk of accidents and associated legal liabilities. Compliance with regulatory standards is also easier to maintain, as these systems can provide detailed records and reports required by regulatory bodies. To conduct a comprehensive ROI analysis, organizations should consider both direct and indirect benefits. Direct benefits include reduced energy costs, lower maintenance expenses, and increased productivity. Indirect benefits may include enhanced brand reputation due to improved safety and environmental performance, as well as potential incentives from utilities or government agencies for adopting energy-efficient technologies. Moreover, the scalability of DCS/DEC systems is another factor that influences ROI. These systems can be expanded or modified as organizational needs evolve, making them a flexible investment that adapts to future growth. This adaptability ensures that the initial investment remains relevant and valuable over an extended period. In conclusion, while the initial costs of implementing DCS/DEC may seem daunting, a thorough ROI analysis reveals that these systems offer substantial long-term financial and operational advantages. By optimizing energy use, enhancing system reliability, improving safety and compliance, and providing scalable solutions, DCS/DEC can significantly enhance an organization's bottom line and overall efficiency. Therefore, when considering the benefits and challenges of implementing these technologies, it is essential to weigh these cost considerations carefully to make an informed decision that aligns with strategic business objectives.
Security Concerns and Maintenance Requirements
When implementing Distributed Control Systems (DCS) or Distributed Energy Controllers (DEC), security concerns and maintenance requirements are paramount considerations that cannot be overlooked. These systems, which are integral to modern industrial and energy management, present a complex landscape of vulnerabilities and upkeep needs. From a security perspective, DCS/DEC systems are susceptible to cyber threats due to their interconnected nature and reliance on networked communication protocols. Cyberattacks can compromise system integrity, leading to operational disruptions, data breaches, and even physical harm. Therefore, robust cybersecurity measures such as encryption, firewalls, and regular software updates are essential. Additionally, implementing secure by design principles and conducting regular vulnerability assessments can help mitigate these risks. Maintenance is another critical aspect that ensures the optimal functioning of DCS/DEC systems. Regular maintenance involves routine checks on hardware and software components to prevent failures and downtime. This includes monitoring system performance metrics, updating firmware, and performing preventive maintenance tasks like cleaning and inspecting equipment. Training personnel on system operation and troubleshooting is also crucial to ensure that any issues are quickly identified and resolved. Furthermore, having a comprehensive maintenance schedule can help in predicting and preventing potential failures, thereby reducing the likelihood of unplanned outages and associated costs. In addition to these technical considerations, compliance with industry standards and regulations is vital. Adhering to guidelines such as those set by the International Society of Automation (ISA) or the National Institute of Standards and Technology (NIST) helps in ensuring that the system meets stringent security and reliability benchmarks. This not only enhances the overall security posture but also builds trust among stakeholders. Moreover, the integration of advanced technologies like artificial intelligence (AI) and machine learning (ML) into DCS/DEC systems can enhance both security and maintenance. AI-driven monitoring tools can detect anomalies in real-time, alerting operators to potential security breaches or system malfunctions before they escalate. Similarly, predictive maintenance algorithms can forecast equipment failures based on historical data, allowing for proactive maintenance actions. In conclusion, while DCS/DEC systems offer numerous benefits in terms of efficiency and control, they also introduce significant security concerns and maintenance requirements. Addressing these challenges through robust cybersecurity measures, regular maintenance practices, compliance with industry standards, and leveraging advanced technologies is essential for ensuring the reliability and integrity of these critical systems. By doing so, organizations can maximize the benefits of DCS/DEC while minimizing the associated risks.