What Is A Digital Print

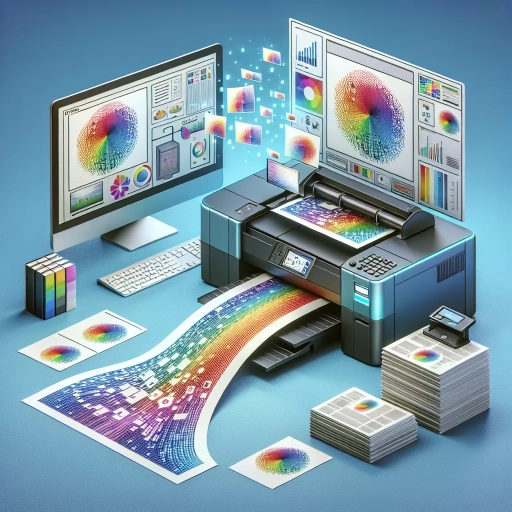
In the modern era of technology, digital printing has revolutionized the way we produce and distribute visual content. This innovative method offers unparalleled precision, speed, and versatility, making it a cornerstone in various industries such as advertising, publishing, and art. To fully appreciate the impact of digital printing, it is essential to delve into its fundamental principles, the intricate processes involved, and its diverse applications. This article will explore the basics of digital printing, detailing how it works and what sets it apart from traditional methods. We will also examine the sophisticated techniques that enable high-quality outputs and discuss the wide range of applications where digital printing excels. Finally, we will highlight the numerous benefits that make digital printing a preferred choice for many professionals. By understanding these aspects, readers will gain a comprehensive insight into the world of digital printing. Let us begin by understanding the basics of digital printing.
Understanding the Basics of Digital Printing
Understanding the basics of digital printing is crucial in today's fast-paced, technologically driven world. Digital printing has revolutionized the way we produce and distribute printed materials, offering unparalleled speed, flexibility, and quality. To grasp the full scope of digital printing, it is essential to delve into its definition and history, explore the key technologies involved, and compare it with traditional printing methods. Starting with the **Definition and History of Digital Printing**, we uncover how this technology emerged and evolved over time. This foundational knowledge sets the stage for understanding the advancements that have led to its current state. Next, examining the **Key Technologies Involved in Digital Printing** reveals the intricate mechanisms and innovations that make digital printing possible. Finally, a **Comparison with Traditional Printing Methods** highlights the advantages and unique benefits that digital printing offers over its predecessors. By exploring these three aspects, readers can gain a comprehensive understanding of digital printing's significance and its role in modern communication and production. Let us begin by tracing the roots of digital printing through its definition and history.
Definition and History of Digital Printing
**Definition and History of Digital Printing** Digital printing is a modern printing technique that involves the direct transfer of digital data from a computer to a printing device, bypassing the need for intermediate steps such as film negatives or plates. This method allows for high-quality, precise, and customizable prints with minimal setup time and cost. The history of digital printing dates back to the 1960s when the first digital printers were developed, primarily for use in research and development environments. However, it wasn't until the 1990s that digital printing began to gain widespread acceptance in commercial and consumer markets. The early stages of digital printing saw the introduction of inkjet and laser printers, which were initially used for small-scale printing needs such as documents and photographs. The inkjet printer, invented by Canon in the late 1970s, used a series of tiny nozzles to spray ink onto paper, while laser printers, developed by Xerox in the 1960s and commercially available from the 1980s, used a laser beam to create an electrostatic image on a drum which attracted toner particles. In the 1990s, advancements in technology led to the development of more sophisticated digital printing methods. The introduction of the Indigo press by Hewlett-Packard in 1993 revolutionized commercial printing by offering high-quality, variable data printing capabilities. This allowed for personalized prints with different text and images on each sheet without the need for multiple setups. The 21st century has seen further innovations with the rise of large-format digital printing, 3D printing, and digital textile printing. Large-format printers enable the production of banners, posters, and other oversized materials with high resolution and vibrant colors. 3D printing technology has expanded beyond prototyping to include production of functional parts and consumer products. Digital textile printing has transformed the fashion industry by allowing for rapid production of custom designs on fabrics. Today, digital printing is integral to various industries including publishing, advertising, packaging, and art. Its ability to produce short runs economically and its flexibility in terms of design changes make it an indispensable tool for businesses and individuals alike. The continuous evolution of digital printing technology ensures that it remains at the forefront of innovative printing solutions, offering unparalleled quality, speed, and customization options. Understanding these basics is crucial for anyone looking to leverage the full potential of digital printing in their creative or professional endeavors.
Key Technologies Involved in Digital Printing
Digital printing leverages several key technologies to produce high-quality, precise, and versatile prints. At the core of digital printing is **Inkjet Technology**, which involves the ejection of tiny droplets of ink onto a substrate to form images. This method is widely used in both consumer and commercial printers due to its flexibility and cost-effectiveness. **Laser Printing** is another critical technology, particularly in high-volume applications, where it offers superior speed and resolution. Laser printers use a laser beam to create an electrostatic image on a drum, which attracts toner particles that are then transferred to the paper. **Electrophotography** is the underlying process in laser printing, enabling the creation of detailed and crisp images by charging a drum with an electrostatic charge that attracts toner. **Thermal Transfer Printing** is another significant technology, often used in label printing and other specialized applications. This method involves transferring ink from a ribbon onto the substrate using heat. **UV Printing** has gained prominence for its ability to print on non-traditional materials such as plastics, metals, and even fabrics. This technology uses ultraviolet light to cure the ink immediately after application, ensuring durability and resistance to fading. **Dye Sublimation Printing** is another advanced technique that converts solid dye into gas, which then bonds with the substrate at a molecular level, resulting in vibrant and long-lasting prints. **Variable Data Printing (VDP)** allows for the customization of each print with unique data, making it ideal for personalized marketing materials and variable information printing. This technology integrates seamlessly with digital workflows to automate the printing process efficiently. **Digital Front Ends (DFEs)** play a crucial role in managing the entire printing process by handling file processing, color management, and job scheduling. These systems ensure that prints are produced consistently and accurately by optimizing the use of resources and minimizing waste. In addition to these core technologies, advancements in **Color Management Systems** have significantly improved the accuracy and consistency of color reproduction across different devices and substrates. These systems ensure that colors appear as intended from design to final print. Lastly, **Automation and Workflow Solutions** are essential for streamlining the digital printing process. These solutions integrate various stages of production, from pre-press to post-press, enhancing productivity and reducing manual intervention. Together, these technologies enable digital printing to offer unparalleled flexibility, speed, and quality, making it a cornerstone of modern printing solutions.
Comparison with Traditional Printing Methods
When comparing digital printing to traditional printing methods, several key differences emerge that highlight the unique advantages and limitations of each approach. Traditional printing, such as offset printing, involves transferring ink onto a metal plate, which is then used to print large quantities of identical images. This method excels in high-volume production due to its cost-effectiveness and consistency once the initial setup costs are covered. However, it requires significant upfront investment in plates and setup time, making it less feasible for small or variable print runs. In contrast, digital printing uses toner or inkjet technology to directly print images onto various substrates without the need for plates. This allows for greater flexibility and speed in producing small to medium-sized print runs, as well as variable data printing where each piece can be customized. Digital printing also offers faster turnaround times since there is no need for lengthy setup processes. Additionally, digital printers can handle a wider range of paper types and finishes, providing more creative options for designers. Another significant advantage of digital printing is its environmental impact. Unlike traditional methods that often generate substantial waste from plate production and ink disposal, digital printing tends to be more eco-friendly with lower waste generation and energy consumption. However, the cost per unit for digital prints can be higher compared to large-scale offset printing, making it less economical for very high-volume jobs. In terms of image quality, both methods have their strengths. Traditional offset printing can achieve high-resolution images with precise color control, especially beneficial for large-scale commercial prints like magazines and billboards. Digital printing has also made significant strides in image quality but may not match the exacting standards of offset printing in certain applications. For businesses and individuals requiring quick turnaround times, customization, and flexibility in their printing needs, digital printing is often the preferred choice. It enables rapid prototyping, proofing, and production without the hefty upfront costs associated with traditional methods. On the other hand, for large-scale commercial projects where cost per unit is a critical factor and high-quality consistency is paramount, traditional offset printing remains the gold standard. In summary, while traditional printing excels in high-volume production with superior image quality at lower costs per unit once setup is complete, digital printing offers unparalleled flexibility, speed, and customization capabilities that make it ideal for smaller or variable print runs. Understanding these differences is crucial for making informed decisions about which printing method best suits specific needs and objectives.
The Process and Techniques of Digital Printing
The process of digital printing is a multifaceted and highly specialized field that involves several critical stages to produce high-quality prints. At its core, digital printing relies on meticulous pre-press preparation and file setup to ensure that the final product meets the desired standards. This initial phase is crucial as it sets the foundation for the entire printing process. Following pre-press, various printing technologies such as inkjet, laser, and others come into play, each offering unique advantages and applications. Finally, post-printing finishing techniques are applied to enhance the appearance and durability of the printed material. Understanding these three key components—pre-press preparation and file setup, printing technologies, and post-printing finishing techniques—is essential for mastering the art of digital printing. By delving into these aspects, one can appreciate the complexity and precision required to achieve outstanding results. Let's begin by examining the first and most foundational step: pre-press preparation and file setup.
Pre-Press Preparation and File Setup
Pre-Press Preparation and File Setup are crucial steps in the digital printing process, ensuring that the final output meets the desired quality and specifications. This phase involves several key activities that prepare the digital files for printing. First, **file creation and editing** are essential, where designers use software like Adobe Creative Suite to create or modify the artwork. It is vital to ensure that all elements, including text, images, and graphics, are correctly aligned and formatted according to the print specifications. **Color management** is another critical aspect of pre-press preparation. This involves setting up color profiles to match the printing device's capabilities, ensuring that the colors in the digital file accurately translate to the printed output. Designers must also consider **resolution and image quality**, ensuring that images are high-resolution (typically 300 DPI) to avoid pixelation or blurriness in the final print. **File formatting** is also a key consideration. Files should be saved in compatible formats such as PDF, which encapsulates all necessary information including fonts, images, and layout. The use of **bleed areas** is important for ensuring that there are no white edges around the edges of the print when it is trimmed. A bleed area extends the design slightly beyond the trim line to account for any minor misalignments during cutting. Additionally, **proofing** plays a significant role in pre-press preparation. Soft proofs (on-screen previews) and hard proofs (physical samples) help identify any errors or discrepancies before proceeding with large-scale printing. This step allows for corrections to be made before incurring significant costs. **Font embedding** and **image linking** are also critical steps. Embedding fonts ensures that they are included within the file itself, preventing any issues with font substitution during printing. Similarly, linking images correctly ensures they are properly referenced and included in the final print file. Finally, **preflight checks** are conducted to verify that all elements of the file are correctly set up for printing. This includes checking for missing fonts, low-resolution images, incorrect color modes, and other potential issues that could affect print quality. By meticulously attending to these aspects of pre-press preparation and file setup, printers can ensure that digital files are accurately translated into high-quality prints, meeting client expectations and maintaining professional standards in digital printing.
Printing Technologies: Inkjet, Laser, and More
In the realm of digital printing, various technologies have emerged to cater to different needs and applications. Among these, inkjet and laser printing are two of the most prevalent methods. **Inkjet Printing**: This technology involves the ejection of tiny droplets of ink onto a substrate, such as paper or fabric, to create the desired image. Inkjet printers use a print head that moves back and forth across the paper, depositing ink droplets in a precise pattern. There are two main types: drop-on-demand (DOD) and continuous inkjet (CIJ). DOD printers are more common and suitable for home and office use, while CIJ printers are typically used in industrial settings for high-speed applications. Inkjet printing is versatile, allowing for the use of various ink types, including dye-based, pigment-based, and even UV-curable inks. This versatility makes it ideal for printing on a wide range of materials, from standard paper to textiles and ceramics. **Laser Printing**: Laser printing relies on electrostatic charges to attract toner particles onto the paper. The process begins with a laser beam drawing an electrostatic image on a drum, which then attracts toner particles. These particles are transferred to the paper and fused using heat and pressure. Laser printers are known for their high speed and precision, making them a staple in office environments. They produce crisp, high-quality text and images, especially in black and white. However, color laser printing can be more expensive due to the need for multiple toner cartridges. Despite this, laser printers offer excellent durability and long-term cost-effectiveness. **Other Printing Technologies**: Beyond inkjet and laser, several other digital printing technologies are gaining prominence. **Solid Ink Printing**, for instance, uses solid ink sticks that are melted and applied to the paper. This method is known for its vibrant colors and is often used in graphic design and professional printing environments. **Dye-Sublimation Printing** involves transferring dye onto materials like fabric, metal, or plastic using heat. This technique is popular for creating custom apparel, mugs, and other promotional items. **UV Printing** uses ultraviolet light to cure ink, allowing for printing on non-porous surfaces such as plastics, metals, and glass. It is particularly useful in industrial and commercial applications where durability is crucial. Each of these technologies has its own set of advantages and limitations, making them suitable for different types of digital printing needs. Understanding the unique characteristics of each can help in selecting the most appropriate method for specific projects, ensuring optimal results in terms of quality, cost, and efficiency. Whether it's the versatility of inkjet, the precision of laser, or the specialized capabilities of other technologies, digital printing offers a wide array of solutions to meet diverse printing requirements.
Post-Printing Finishing Techniques
Post-printing finishing techniques are crucial steps in the digital printing process that enhance the final product's appearance, durability, and functionality. These techniques transform raw printed materials into polished, professional outputs. Here are some key post-printing finishing methods: 1. **Cutting and Trimming**: Precision cutting and trimming ensure that the printed material is accurately sized and shaped. This can be done using guillotine cutters, laser cutters, or die-cutting machines for intricate designs. 2. **Folding and Creasing**: Folding and creasing are essential for creating brochures, leaflets, and other folded materials. Techniques include accordion folding, saddle-stitching, and perfect binding. 3. **Binding**: Various binding methods such as perfect binding, saddle-stitching, spiral binding, and hardcover binding are used to assemble multiple pages into a cohesive unit. 4. **Laminating**: Laminating involves encasing the printed material in a protective layer of plastic or vinyl to enhance durability and resistance to wear and tear. 5. **Embossing and Debossing**: These techniques add texture and depth to the print by raising (embossing) or lowering (debossing) specific areas of the material. 6. **Foiling**: Foiling involves applying metallic foil to selected areas of the print using heat and pressure, adding a luxurious finish. 7. **Spot Varnishing**: This technique applies a glossy or matte varnish to specific areas of the print to highlight key elements or add visual interest. 8. **Die-Cutting**: Die-cutting uses custom-made dies to cut out unique shapes from the printed material, ideal for creating custom designs and shapes. 9. **Perforation**: Perforation involves creating a series of small holes along a line where the material can be easily torn apart, commonly used for tear-off coupons or tickets. 10. **Finishing Coatings**: Applying coatings such as UV coating, aqueous coating, or varnish enhances the print's appearance and protects it from environmental factors. Each of these post-printing finishing techniques plays a vital role in transforming raw prints into finished products that meet specific needs and aesthetic standards, ensuring that the final output is both visually appealing and functionally robust. By integrating these techniques into the digital printing process, businesses can produce high-quality materials that stand out in their respective markets.
Applications and Benefits of Digital Printing
Digital printing has revolutionized various sectors by offering unparalleled flexibility, precision, and efficiency. This technology has far-reaching applications that extend beyond traditional printing methods, making it a cornerstone in both commercial and industrial settings, as well as artistic and creative fields. In the commercial and industrial realm, digital printing enables rapid production of customized materials such as labels, packaging, and signage, which are crucial for branding and marketing strategies. On the artistic front, digital printing opens up new avenues for creatives to produce high-quality prints of their work with intricate details and vibrant colors. Additionally, the economic and environmental benefits of digital printing cannot be overstated; it reduces waste, conserves resources, and offers cost-effective solutions compared to traditional printing methods. As we delve into the specifics of these applications, it becomes clear that digital printing is a multifaceted tool with significant implications. Let us first explore the commercial and industrial uses of digital printing, where its impact is most pronounced in terms of operational efficiency and market reach.
Commercial and Industrial Uses of Digital Printing
Digital printing has revolutionized the commercial and industrial sectors by offering unparalleled flexibility, speed, and quality. In commercial settings, digital printing is widely used for producing marketing materials such as brochures, flyers, business cards, and posters. This technology allows for on-demand printing, enabling businesses to print small quantities without incurring significant setup costs. This is particularly beneficial for startups and small businesses that need to test market responses or frequently update their promotional materials. Additionally, digital printing supports variable data printing (VDP), which enables personalized messages and images to be printed on each item, enhancing customer engagement and response rates. In industrial applications, digital printing plays a crucial role in manufacturing processes. It is used for printing labels and packaging materials with high precision and speed. For instance, in the pharmaceutical industry, digital printing ensures that labels comply with stringent regulatory requirements by accurately printing complex information such as barcodes, serial numbers, and expiration dates. Similarly, in the food and beverage sector, digital printing helps in producing custom labels that meet specific branding and safety standards. Another significant industrial use of digital printing is in the production of textiles and fabrics. Digital textile printing offers vibrant colors and intricate designs without the need for screens or plates, making it ideal for fashion brands looking to create unique and limited-edition designs quickly. This technology also reduces waste and environmental impact compared to traditional methods. Furthermore, digital printing is integral to the automotive industry where it is used for printing vehicle wraps, interior components, and safety labels. The precision and durability of digital prints ensure that these elements withstand harsh environmental conditions while maintaining their aesthetic appeal. The benefits of digital printing in these sectors include reduced turnaround times, lower costs for small to medium-sized print runs, and the ability to make last-minute changes without significant additional costs. Moreover, the high-quality output of digital printers ensures that the final products are visually appealing and durable, which is critical for maintaining brand integrity and customer satisfaction. Overall, the versatility and efficiency of digital printing make it an indispensable tool across various commercial and industrial applications, driving innovation and competitiveness in these sectors.
Artistic and Creative Applications
Digital printing has revolutionized the realm of artistic and creative applications, offering unparalleled flexibility, precision, and speed. Artists and designers can now explore a wide range of mediums and techniques that were previously inaccessible or impractical. For instance, digital printing allows for the creation of intricate patterns and designs on various materials such as fabrics, ceramics, and even 3D objects. This versatility enables artists to experiment with new textures, colors, and dimensions, pushing the boundaries of traditional art forms. In the field of fine art, digital printing has made it possible for artists to produce high-quality reproductions of their work with remarkable fidelity. Giclée printing, a form of inkjet printing, is particularly popular among artists for its ability to capture the subtleties of color and detail found in original artworks. This technology not only helps artists reach a broader audience but also preserves the integrity of their work by ensuring that each print is a faithful representation of the original piece. Fashion designers have also embraced digital printing as a means to create unique and complex designs on fabrics without the need for extensive screen printing setups. This allows for rapid prototyping and production, enabling designers to quickly respond to trends and consumer demands. Additionally, digital textile printing reduces waste and environmental impact by eliminating the need for large quantities of ink and water required in traditional dyeing processes. Graphic designers benefit from digital printing's ability to produce small batches of custom prints quickly and cost-effectively. This is particularly advantageous for limited-edition prints, promotional materials, and personalized products such as business cards, posters, and packaging. The precision of digital printing ensures that every detail is accurately rendered, making it ideal for branding and marketing materials where consistency is crucial. Moreover, digital printing has opened up new avenues in interior design and architecture. Custom wall coverings, floor tiles, and even furniture can be printed with intricate designs that would be impossible to achieve through traditional manufacturing methods. This allows designers to create cohesive and visually stunning environments tailored to specific themes or client preferences. In educational settings, digital printing facilitates hands-on learning experiences in art classes. Students can experiment with various techniques and materials without the constraints of traditional printing methods. This interactive approach fosters creativity and innovation while providing immediate feedback on their work. Overall, the artistic and creative applications of digital printing are vast and diverse. By offering precision, flexibility, and speed, digital printing empowers artists, designers, and educators to explore new frontiers in their respective fields while maintaining high standards of quality and sustainability.
Economic and Environmental Benefits
The integration of digital printing technology offers significant economic and environmental benefits, making it a highly desirable choice in various industries. Economically, digital printing reduces costs associated with traditional printing methods. It eliminates the need for large print runs, thereby minimizing waste and saving resources. This flexibility allows businesses to print on demand, reducing inventory costs and the financial risk of unsold products. Additionally, digital printing enables rapid turnaround times, which can lead to faster time-to-market for new products and marketing materials, giving companies a competitive edge. From an environmental perspective, digital printing is more sustainable compared to conventional methods. It uses less ink and paper, resulting in lower material consumption and reduced waste generation. The absence of chemical-based inks and solvents in many digital printing processes also minimizes the release of harmful pollutants into the environment. Furthermore, digital printing often employs eco-friendly materials such as recycled paper and biodegradable inks, contributing to a greener supply chain. The reduced need for transportation due to on-demand printing also lowers carbon emissions from logistics. Overall, the economic efficiency and environmental sustainability of digital printing make it an attractive option for businesses seeking to balance profitability with environmental responsibility.