What Does A Welder Do

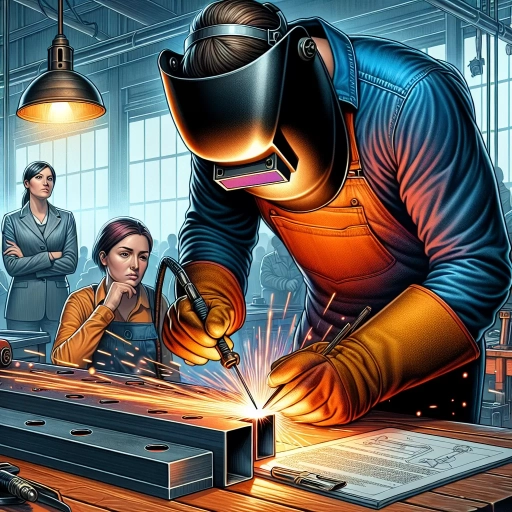
Welding is a crucial skill that underpins various industries, from construction and manufacturing to automotive and aerospace. A welder's role is multifaceted, requiring a blend of technical expertise, physical stamina, and attention to detail. To fully appreciate the significance of welding, it is essential to delve into the intricacies of the profession. This article will explore what a welder does, starting with an in-depth look at **Understanding the Role of a Welder**. We will then examine the **Skills and Qualifications Required for Welding**, highlighting the educational background, training, and personal attributes necessary for success in this field. Finally, we will discuss **Career Path and Opportunities in Welding**, outlining the diverse career trajectories and growth prospects available to those who pursue this rewarding profession. By understanding these aspects, readers will gain a comprehensive insight into the world of welding and the vital contributions welders make to modern society. Let us begin by **Understanding the Role of a Welder**.
Understanding the Role of a Welder
Understanding the role of a welder is crucial for appreciating the intricate skills and responsibilities involved in this vital profession. Welders play a pivotal role in various industries, including construction, manufacturing, and automotive, by ensuring the integrity and durability of metal structures. To fully grasp the significance of their work, it is essential to delve into three key aspects: **Primary Responsibilities and Tasks**, **Types of Welding Processes**, and **Work Environment and Safety Considerations**. Welders are not just skilled craftsmen but also problem solvers who must adapt to different materials and environments. Their primary responsibilities include reading blueprints, preparing metal surfaces, and executing precise welding techniques to meet specific standards. The variety of welding processes they employ, such as shielded metal arc welding (SMAW), gas metal arc welding (GMAW), and gas tungsten arc welding (GTAW), each requires a deep understanding of the unique challenges and benefits associated with each method. Additionally, welders must navigate complex work environments that demand strict adherence to safety protocols to prevent injuries and ensure quality outcomes. By examining these facets, we can gain a comprehensive understanding of the multifaceted role that welders fulfill. Let us begin by exploring their **Primary Responsibilities and Tasks**, which form the foundation of their daily work and highlight the precision and skill required in this demanding yet rewarding profession.
Primary Responsibilities and Tasks
**Primary Responsibilities and Tasks** As a crucial component of various industries, including construction, manufacturing, and automotive, the role of a welder is multifaceted and demanding. At the heart of their job are several primary responsibilities and tasks that ensure the integrity and safety of structures and products. First and foremost, welders are responsible for reading and interpreting blueprints, diagrams, and specifications to understand the requirements of each project. This involves identifying the types of materials to be used, the welding techniques required, and any specific safety protocols that must be followed. Once the project parameters are clear, welders prepare the work area by cleaning and degreasing surfaces to ensure optimal welding conditions. They then select and set up the appropriate welding equipment, such as arc welders, MIG welders, or TIG welders, depending on the task at hand. This includes calibrating machines, checking for any defects or malfunctions, and ensuring all safety gear is in place. The core task of a welder is to join metal parts together using heat and pressure. This involves applying various welding techniques such as shielded metal arc welding (SMAW), gas metal arc welding (GMAW), or gas tungsten arc welding (GTAW). Each technique requires precision and skill to achieve strong, durable bonds without compromising the structural integrity of the materials. In addition to welding, these professionals are also responsible for inspecting their work to ensure it meets quality standards. This includes visually examining welds for defects like cracks or porosity and conducting tests such as radiography or ultrasonic testing to verify the strength and integrity of the welds. Safety is paramount in this role; welders must adhere to strict safety guidelines to protect themselves and others from hazards such as sparks, fumes, and electrical shock. This includes wearing personal protective equipment (PPE) like helmets, gloves, and respirators, as well as maintaining a clean and organized workspace. Furthermore, welders often collaborate with other professionals such as engineers, fabricators, and quality control specialists to ensure that projects are completed efficiently and effectively. They may also be required to troubleshoot issues that arise during the welding process and develop solutions to overcome them. In summary, the primary responsibilities and tasks of a welder encompass a broad range of activities from preparation and execution to inspection and safety adherence. These duties require a combination of technical skills, attention to detail, physical stamina, and the ability to work collaboratively within a team environment. Understanding these responsibilities is essential for appreciating the critical role that welders play in various industries and the importance of their work in ensuring the safety and durability of structures and products.
Types of Welding Processes
Welding processes are the backbone of a welder's craft, each offering unique advantages and applications that cater to various industries and materials. There are several key types of welding processes that welders must master to excel in their role. 1. **Shielded Metal Arc Welding (SMAW) or "Stick" Welding**: This traditional method uses a consumable electrode covered in a flux to protect the arc and molten metal from atmospheric gases. It is versatile, portable, and widely used for repair and maintenance work due to its simplicity and effectiveness on a variety of metals. 2. **Gas Metal Arc Welding (GMAW) or "MIG" Welding**: Employing a continuous wire electrode and an inert gas shield, GMAW is known for its high speed and clean welds. It is commonly used in automotive, construction, and manufacturing industries where efficiency and precision are paramount. 3. **Gas Tungsten Arc Welding (GTAW) or "TIG" Welding**: This process utilizes a non-consumable tungsten electrode and an inert gas shield. GTAW is renowned for producing high-quality, precise welds and is often used in aerospace, automotive, and artistic applications where cleanliness and control are critical. 4. **Flux Cored Arc Welding (FCAW)**: Similar to SMAW but using a special electrode that produces a flux to shield the arc, FCAW offers a balance between the ease of use of SMAW and the efficiency of GMAW. It is particularly useful for welding thick materials and in outdoor environments. 5. **Submerged Arc Welding (SAW)**: In this process, the arc is shielded by a layer of flux that covers the work area. SAW is highly efficient and used extensively in shipbuilding, pipeline construction, and other heavy industries where large quantities of material need to be welded quickly. 6. **Electroslag Welding (ESW) and Electrogas Welding (EGW)**: These processes involve melting the filler metal and base metal with an electric arc, then shielding the molten metal with a flux or gas. They are typically used for welding thick sections of steel in a single pass, making them ideal for structural steel fabrication. 7. **Laser Beam Welding (LBW)**: Utilizing a high-energy laser beam to melt and join metals, LBW offers exceptional precision and speed. It is commonly employed in high-tech industries such as aerospace and automotive manufacturing where intricate designs require precise welding. 8. **Resistance Welding**: This method involves generating heat through electrical resistance at the interface between two metal pieces. It is widely used in mass production environments like automotive assembly lines for tasks such as spot welding and seam welding. Understanding these various welding processes is essential for a welder to select the appropriate technique for each job, ensuring quality, efficiency, and safety. Each process has its own set of skills and equipment requirements, making the role of a welder both challenging and rewarding as they adapt to different projects and materials. By mastering these techniques, welders can deliver high-quality results across diverse industries, from construction to aerospace, highlighting their critical role in modern manufacturing and infrastructure development.
Work Environment and Safety Considerations
When understanding the role of a welder, it is crucial to delve into the work environment and safety considerations that are integral to this profession. Welders operate in a variety of settings, including manufacturing plants, construction sites, and repair shops, each presenting unique challenges and hazards. The work environment for welders is often physically demanding, requiring them to stand for long periods, lift heavy equipment, and work in confined spaces. Additionally, welders are frequently exposed to extreme temperatures, noise, and vibrations, which can lead to fatigue and other health issues if proper precautions are not taken. Safety considerations are paramount in welding due to the inherent risks associated with the job. One of the most significant hazards is the exposure to harmful fumes and gases emitted during the welding process. These fumes can contain toxic substances such as particulate matter, ozone, and volatile organic compounds, which can cause respiratory problems and other health issues. To mitigate this risk, welders must use appropriate ventilation systems and personal protective equipment (PPE) like respirators and masks. Another critical safety concern is the risk of burns and fires. Welding involves working with high temperatures and open flames, making it essential for welders to wear protective gear such as heat-resistant gloves, safety glasses with shaded lenses, and fire-resistant clothing. The workspace must also be free from flammable materials and have fire extinguishers readily available. Electrical safety is another key consideration. Welders often work with electrical equipment that can pose risks of electrical shock or arc flash if not handled properly. Ensuring that all electrical equipment is well-maintained and following strict safety protocols can help prevent these accidents. Furthermore, ergonomics play a significant role in maintaining a safe work environment for welders. Proper ergonomic practices help reduce the risk of musculoskeletal disorders by ensuring that the workspace is set up to minimize strain on the body. This includes using ergonomic chairs, positioning welding equipment at comfortable heights, and taking regular breaks to avoid prolonged static postures. In addition to these physical safety measures, psychological well-being is also important. The high-stress nature of welding jobs can lead to mental health issues if not managed properly. Employers should provide resources for stress management and ensure a supportive work culture that encourages open communication about mental health concerns. Finally, ongoing training and education are vital components of maintaining a safe work environment for welders. Regular training sessions on new technologies, safety procedures, and best practices help welders stay updated with industry standards and reduce the risk of accidents. By combining these elements—physical safety measures, ergonomic practices, mental health support, and continuous education—welders can perform their roles effectively while minimizing risks to their health and well-being. This holistic approach not only ensures compliance with safety regulations but also fosters a culture of safety that benefits both the individual welder and the broader workplace community.
Skills and Qualifications Required for Welding
Welding is a highly specialized profession that demands a unique blend of technical skills, physical endurance, and mental acuity. To excel in this field, welders must possess a comprehensive set of qualifications that span multiple dimensions. First, they need to have robust technical skills and knowledge, including proficiency in various welding techniques, understanding of metallurgy, and the ability to interpret blueprints and specifications. Additionally, welding is a physically demanding job that requires stamina, dexterity, and the capacity to work in challenging environments, which highlights the importance of physical and mental demands. Lastly, formal education and training are crucial for acquiring the necessary competencies and staying updated with industry standards. By delving into these three critical areas—technical skills and knowledge, physical and mental demands, and education and training requirements—we can gain a deeper understanding of what it takes to be a skilled welder. Let's start by examining the technical skills and knowledge that form the foundation of this profession.
Technical Skills and Knowledge
To excel as a welder, one must possess a robust set of technical skills and knowledge that span both theoretical understanding and practical application. At the core of these skills is a deep comprehension of various welding processes, including Shielded Metal Arc Welding (SMAW), Gas Metal Arc Welding (GMAW), Gas Tungsten Arc Welding (GTAW), and Flux Cored Arc Welding (FCAW). Each process has its unique characteristics, advantages, and challenges, requiring the welder to be adept at selecting the appropriate method based on the material being welded and the desired outcome. In addition to process-specific skills, welders must have a solid grasp of metallurgy. This includes understanding the properties of different metals and alloys, their thermal expansion rates, and how they react under various welding conditions. Knowledge of metal fabrication techniques is also crucial, as it involves cutting, bending, and shaping metals to prepare them for welding. Safety protocols are another critical aspect of a welder's technical skills. This includes familiarity with personal protective equipment (PPE) such as helmets, gloves, and respirators, as well as adherence to safety standards and regulations to prevent injuries from electrical shock, arc flash, and toxic fumes. Understanding how to properly set up and maintain welding equipment is essential for both safety and efficiency. Furthermore, modern welding often involves the use of advanced technologies such as robotic welding systems and computer-aided design (CAD) software. Proficiency in these tools allows welders to work more accurately and efficiently, especially in high-volume production environments. Additionally, knowledge of quality control measures is vital for ensuring that welds meet industry standards and specifications. The ability to read blueprints and technical drawings is another key skill for welders. This involves interpreting dimensions, tolerances, and other specifications to ensure that the final product meets design requirements. Problem-solving skills are also essential, as welders frequently encounter issues such as porosity, lack of fusion, or distortion that require immediate resolution. Finally, staying updated with industry developments through continuous education and training is imperative. This includes attending workshops, seminars, and certification programs offered by organizations like the American Welding Society (AWS) to enhance skills and stay compliant with evolving industry standards. In summary, the technical skills and knowledge required for welding are multifaceted and demanding. They encompass a broad range of competencies from process-specific techniques to safety protocols, metallurgy, metal fabrication, advanced technologies, quality control, blueprint reading, problem-solving, and ongoing education. Mastery of these skills is essential for any welder aiming to deliver high-quality work while ensuring safety and efficiency in the workplace.
Physical and Mental Demands
Welding is a physically and mentally demanding profession that requires a unique blend of skills, qualifications, and personal attributes. Physically, welders must endure long hours of standing, bending, and lifting heavy equipment, often in confined or elevated spaces. The job involves working with intense heat, sparks, and potentially hazardous materials, necessitating the use of protective gear such as helmets, gloves, and safety glasses. This protective gear, while essential, can add to the physical strain due to its weight and the need for constant vigilance to ensure proper use. Additionally, welders frequently work in environments with varying temperatures and humidity levels, which can exacerbate physical discomfort. Mentally, the demands are equally significant. Welding requires high levels of concentration and attention to detail to ensure precision and safety. The process involves interpreting blueprints, following strict safety protocols, and making precise adjustments to equipment settings. This level of focus can be mentally taxing, especially when working on complex projects or under tight deadlines. Furthermore, welders must be able to troubleshoot issues as they arise, which demands problem-solving skills and the ability to remain calm under pressure. The mental strain is compounded by the responsibility of producing high-quality work that meets stringent standards, as faulty welds can have serious consequences in terms of safety and structural integrity. To excel in this field, welders need to possess a combination of technical skills, physical stamina, and mental resilience. They must be adept at operating various welding machines and tools, understanding different welding techniques such as MIG (GMAW), TIG (GTAW), and ARC (SMAW) welding. Proficiency in reading blueprints and understanding metallurgy is also crucial for selecting the appropriate materials and techniques for each project. Moreover, effective communication skills are essential for collaborating with other team members and ensuring that all safety protocols are followed. In addition to these technical competencies, welders benefit from having strong problem-solving abilities, adaptability, and a keen eye for detail. These qualities enable them to navigate the complexities of different projects while maintaining high standards of quality and safety. The ability to work independently as well as part of a team is also vital, as many welding tasks require coordination with other professionals such as engineers, fabricators, and inspectors. Ultimately, the physical and mental demands of welding underscore the importance of comprehensive training programs that equip individuals with both the technical knowledge and the personal attributes necessary for success in this field. By combining rigorous education with hands-on experience and continuous professional development, aspiring welders can build the skills and qualifications required to thrive in this challenging yet rewarding profession.
Education and Training Requirements
To excel as a welder, one must undergo rigorous education and training that combines theoretical knowledge with hands-on practice. Typically, aspiring welders start by earning a high school diploma or equivalent, which provides a foundational understanding of mathematics, science, and technical skills. Post-secondary education is highly recommended and often required for advanced positions. Many welders pursue vocational training or an associate's degree in welding technology from a community college or technical school. These programs usually span one to two years and cover essential topics such as welding processes, safety protocols, blueprint reading, and metallurgy. In addition to formal education, extensive hands-on training is crucial. Many aspiring welders enroll in apprenticeship programs that last three to four years. These apprenticeships offer the opportunity to work under experienced welders while gaining practical experience in various welding techniques and technologies. Some welders also choose to obtain specialized certifications from organizations like the American Welding Society (AWS) or the American Society of Mechanical Engineers (ASME). These certifications, such as the AWS Certified Welder (CW) or the ASME Welding Qualification, demonstrate a welder's proficiency in specific welding processes and can significantly enhance job prospects. Continuous learning is another vital aspect of a welder's career. The field of welding is constantly evolving with new technologies and techniques being introduced regularly. Therefore, welders must commit to ongoing education and training to stay updated with industry standards and advancements. This may involve attending workshops, seminars, and online courses that focus on emerging trends in welding technology. Moreover, safety training is an integral part of any welding education program. Welders must be well-versed in safety procedures to protect themselves and others from potential hazards such as burns, electrical shock, and toxic fumes. This includes understanding how to properly use personal protective equipment (PPE) like helmets, gloves, and respirators. In summary, becoming a skilled welder requires a blend of formal education, hands-on training, and continuous learning. By combining these elements with specialized certifications and a strong emphasis on safety protocols, welders can ensure they possess the necessary skills and qualifications to excel in this demanding yet rewarding profession. This comprehensive approach not only enhances job readiness but also contributes to the overall quality and safety of welding work in various industries.
Career Path and Opportunities in Welding
Welding is a dynamic and versatile career path that offers a wide range of opportunities for individuals seeking a challenging and rewarding profession. This field is not only essential in various industries but also provides ample room for career advancement and professional development. For those interested in welding, it is crucial to understand the diverse job specializations available, the industries that rely heavily on welding expertise, and the potential for career growth. Additionally, knowing the salary and benefits associated with welding careers can help aspiring welders make informed decisions about their future. In this article, we will delve into the various job specializations and industries where welders are in high demand, explore the avenues for career advancement and professional development, and provide an overview of the salary and benefits that come with a career in welding. Let's begin by examining the diverse job specializations and industries that form the backbone of this vital profession.
Job Specializations and Industries
In the dynamic and multifaceted world of welding, job specializations and industries play a crucial role in defining career paths and opportunities. Welding is not a one-size-fits-all profession; instead, it encompasses a variety of specialized roles that cater to different sectors. For instance, **Structural Welders** are essential in the construction industry, where they work on building frameworks, bridges, and other large-scale infrastructure projects. These welders must possess strong knowledge of blueprints and the ability to work at heights. **Pipe Welders**, on the other hand, are in high demand within the oil and gas industry, as well as in water treatment facilities. Their expertise lies in welding pipes that transport fluids and gases, requiring precision and adherence to strict safety standards. **Automotive Welders** specialize in the automotive sector, focusing on vehicle manufacturing and repair. They work with various metals to ensure the structural integrity of vehicles. The **Aerospace Industry** also relies heavily on skilled welders who can handle advanced materials like titanium and aluminum alloys. These welders must meet stringent quality control standards due to the critical nature of their work. Similarly, **Shipbuilding Welders** contribute to the maritime industry by constructing and repairing ships, submarines, and other marine vessels. In addition to these specialized roles, welding professionals can find opportunities in **Manufacturing**, where they produce consumer goods such as appliances, machinery, and equipment. **Maintenance Welders** are vital across various industries for their ability to repair and maintain existing equipment, reducing downtime and increasing operational efficiency. The **Energy Sector**, including nuclear power plants and wind farms, also employs welders who are trained to handle unique materials and environments. Furthermore, advancements in technology have led to the emergence of **Robotic Welding**, where welders program and operate robotic systems to perform repetitive tasks with high precision. Each specialization requires specific training and certifications but offers a rewarding career path with opportunities for advancement. For example, experienced welders can move into supervisory roles or become welding inspectors who ensure that all welding work meets industry standards. The diversity of job specializations within welding not only underscores the versatility of this trade but also highlights the numerous career opportunities available to those who pursue it. Ultimately, understanding these various specializations and industries is key for anyone considering a career in welding. It allows individuals to tailor their training and experience to align with their interests and career goals, ensuring a fulfilling and successful professional journey. Whether it's working on towering skyscrapers or intricate aerospace components, the field of welding offers a rich tapestry of opportunities that cater to different skills, interests, and ambitions.
Career Advancement and Professional Development
Career advancement and professional development are crucial components for welders seeking to elevate their careers and capitalize on the diverse opportunities available in the welding industry. As a welder progresses through their career, it is essential to continually enhance skills, stay updated with industry advancements, and pursue certifications that validate expertise. Starting with foundational skills in various welding processes such as Shielded Metal Arc Welding (SMAW), Gas Metal Arc Welding (GMAW), and Gas Tungsten Arc Welding (GTAW), welders can expand their repertoire by learning specialized techniques like robotic welding, underwater welding, or precision welding. Professional development can be achieved through formal education programs, workshops, and training sessions offered by institutions like the American Welding Society (AWS) or the American Society of Mechanical Engineers (ASME). These programs not only provide hands-on experience but also offer certifications such as the Certified Welder (CW) or the Senior Certified Welder (SCW), which significantly enhance job prospects and career advancement opportunities. Additionally, staying abreast of industry trends and technological innovations, such as the integration of AI and automation in welding processes, can position welders as leaders in their field. Networking within professional organizations is another key aspect of career advancement. Joining industry-specific groups allows welders to connect with peers, share best practices, and gain insights into emerging opportunities. For instance, attending conferences or participating in online forums can provide valuable information about new job openings, contract opportunities, or entrepreneurial ventures. Moreover, transitioning into supervisory or management roles requires developing soft skills such as communication, leadership, and project management. Pursuing higher education in fields like engineering or business administration can equip welders with the necessary knowledge to oversee projects, manage teams, and make strategic decisions. This holistic approach to professional development not only ensures career longevity but also opens doors to diverse career paths within the welding industry. In summary, career advancement for welders is multifaceted and involves continuous skill enhancement, certification, staying updated with industry developments, networking, and developing leadership skills. By adopting these strategies, welders can navigate a wide range of opportunities from specialized technical roles to managerial positions, ensuring a fulfilling and progressive career trajectory.
Salary and Benefits Overview
**Salary and Benefits Overview** For those considering a career in welding, understanding the compensation and benefits landscape is crucial. Welders are generally well-compensated professionals, reflecting the high demand for their skills across various industries such as construction, manufacturing, and energy. The salary range for welders can vary significantly based on factors like location, industry, level of experience, and specific job duties. On average, entry-level welders can expect to earn around $35,000 to $45,000 per year. However, experienced welders can command salaries ranging from $50,000 to over $70,000 annually. Specialized roles such as pipeline welders or those working in high-risk environments like offshore oil rigs may earn even higher wages, sometimes exceeding $100,000 per year. In addition to competitive salaries, welders often enjoy a robust benefits package. Many employers offer comprehensive health insurance, retirement plans such as 401(k) or pension plans, and paid time off. Some companies also provide additional perks like tool allowances, safety equipment stipends, and opportunities for overtime pay which can significantly boost earnings. Moreover, the nature of welding work allows for flexibility in career paths. Welders can choose between full-time employment with a single company or opt for contract work that offers greater autonomy and potentially higher earnings through freelance or consulting roles. This flexibility is particularly appealing to those who value independence or wish to balance work with other life commitments. The benefits extend beyond financial compensation; welders also have access to continuous training and certification programs. These programs not only enhance their skills but also open up opportunities for career advancement. For instance, obtaining specialized certifications like AWS (American Welding Society) or ASME (American Society of Mechanical Engineers) can lead to higher-paying jobs and greater job security. Furthermore, the demand for skilled welders is expected to remain strong due to ongoing infrastructure projects and the need for maintenance and repair in various sectors. This stability in job prospects adds another layer of security and peace of mind for those entering this profession. In summary, a career in welding offers not only a competitive salary but also a comprehensive benefits package, flexibility in career paths, opportunities for continuous skill enhancement, and a stable job market. These factors make welding an attractive and rewarding profession for those who enjoy hands-on work and are committed to mastering their craft.