What Does Whims Stand For

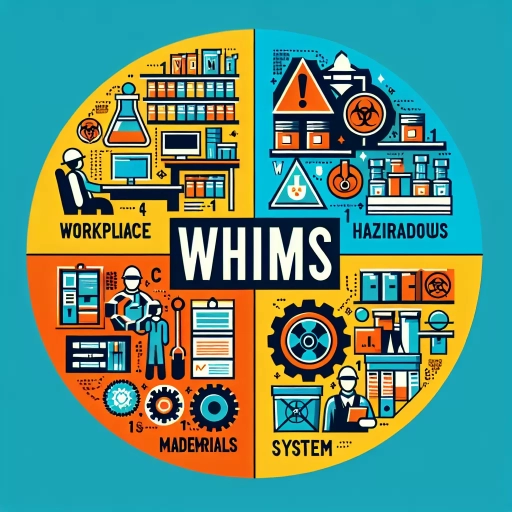
In today's fast-paced and dynamic work environments, effective management and safety protocols are crucial for maintaining productivity and ensuring the well-being of employees. One such protocol that has gained significant attention is WHIMS, an acronym that stands for Workplace Hazardous Materials Information System. This system is designed to provide comprehensive information about hazardous materials in the workplace, helping to mitigate risks and enhance safety standards. To fully grasp the importance and implementation of WHIMS, it is essential to delve into its core components. This article will explore three key aspects: **Understanding the Acronym WHIMS**, which will provide a foundational knowledge of what WHIMS entails; **Breaking Down Each Letter of WHIMS**, which will dissect the acronym to understand its individual elements; and **Implementing WHIMS in Modern Workplaces**, which will discuss practical applications and benefits in contemporary settings. By starting with **Understanding the Acronym WHIMS**, we will lay the groundwork for a deeper exploration of this vital safety system.
Understanding the Acronym WHIMS
Understanding the Acronym WHIMS is a multifaceted exploration that delves into the historical, practical, and global dimensions of this significant term. At its core, WHIMS stands for Workplace Hazardous Materials Information System, a critical framework designed to ensure the safe handling and management of hazardous materials in various work environments. To fully grasp the implications of WHIMS, it is essential to consider its historical context, tracing back to the legislative and regulatory milestones that have shaped its development. Additionally, examining the common uses and applications of WHIMS reveals its practical importance in safeguarding workers and workplaces. Finally, understanding the global recognition and standards surrounding WHIMS highlights its international relevance and the harmonization efforts across different countries. By navigating through these three key aspects, this article aims to provide a comprehensive understanding of the acronym WHIMS, shedding light on its evolution, utility, and global significance. Transitioning seamlessly into the heart of the matter, we will delve into the Historical Context of WHIMS, followed by its Common Uses and Applications, and conclude with an overview of its Global Recognition and Standards. Understanding the Acronym WHIMS is crucial for anyone involved in workplace safety and compliance.
Historical Context of WHIMS
The acronym WHIMS, standing for Workplace Hazardous Materials Information System, is deeply rooted in a historical context that highlights the evolving need for workplace safety and regulatory compliance. In the late 20th century, the industrial landscape was marked by significant health and safety concerns. Workers were frequently exposed to hazardous materials without adequate information or protective measures, leading to numerous occupational illnesses and injuries. This dire situation prompted governments and regulatory bodies to intervene. In Canada, the federal government responded by enacting the Hazardous Products Act in 1987, which mandated the creation of a system to provide workers with critical information about the hazardous materials they handled. This legislation laid the groundwork for WHIMS, which was officially implemented in 1988. WHIMS was designed to ensure that employers provided their employees with comprehensive information about the safe handling, use, storage, and disposal of hazardous materials through three key components: labels, material safety data sheets (MSDS), and worker education and training programs. The introduction of WHIMS marked a significant shift towards a more proactive approach to workplace safety. It aligned with broader international efforts to standardize chemical safety, such as those led by the United Nations and the International Labour Organization. Over time, WHIMS has undergone several updates and revisions to keep pace with scientific advancements and changing workplace environments. For instance, the transition from MSDS to Safety Data Sheets (SDS) in 2015 reflected global harmonization efforts under the Globally Harmonized System of Classification and Labelling of Chemicals (GHS). Today, WHIMS remains a cornerstone of occupational health and safety in Canada, ensuring that workers are equipped with the knowledge they need to safely manage hazardous materials. Its historical context underscores the importance of continuous improvement in workplace safety regulations and the collaborative efforts between governments, industries, and workers to protect human health and well-being. As industries continue to evolve, the principles established by WHIMS serve as a model for other countries and jurisdictions seeking to enhance their own occupational safety standards.
Common Uses and Applications
Understanding the acronym WHIMS (Waste Handling and Incineration Management System) is crucial for grasping its multifaceted applications across various industries. WHIMS is not just a term; it represents a comprehensive approach to managing waste, particularly hazardous materials, ensuring compliance with environmental regulations and safety standards. One of the most common uses of WHIMS is in the healthcare sector, where it plays a pivotal role in the disposal of medical waste. Hospitals and clinics utilize WHIMS to categorize, store, transport, and incinerate biohazardous materials safely, preventing the spread of infectious diseases and protecting both patients and staff. In industrial settings, WHIMS is essential for managing chemical and toxic waste generated during manufacturing processes. Companies in the chemical, pharmaceutical, and oil and gas industries rely on WHIMS to handle hazardous substances from production to disposal, minimizing environmental impact and adhering to stringent regulatory requirements. The system ensures that all waste is tracked from generation to final disposal, providing a transparent and auditable trail that helps in compliance reporting. WHIMS also finds significant application in research institutions and laboratories where hazardous chemicals are frequently used. These environments require stringent waste management protocols to prevent accidents and ensure the safety of researchers. By implementing WHIMS, these facilities can systematically manage their chemical waste, reducing the risk of contamination and ensuring that all materials are disposed of in an environmentally responsible manner. Furthermore, WHIMS is integral to municipal waste management systems. Local governments use WHIMS to oversee the collection, transportation, and disposal of household hazardous waste such as batteries, electronics, and pesticides. This helps in maintaining public health standards by preventing the improper disposal of these items into regular trash streams. In addition to these sectors, WHIMS has applications in military operations where the handling of explosive and toxic materials is critical. Military bases use WHIMS to manage their hazardous waste efficiently, ensuring that all materials are handled according to strict safety protocols and environmental guidelines. Overall, WHIMS is a versatile system that enhances safety, compliance, and environmental stewardship across diverse industries. Its ability to streamline waste management processes makes it an indispensable tool for any organization dealing with hazardous materials. By understanding what WHIMS stands for and its applications, individuals can appreciate the importance of effective waste management in protecting public health and the environment.
Global Recognition and Standards
Global recognition and standards play a pivotal role in ensuring the safety, efficiency, and consistency of various industries, particularly in the realm of workplace health and safety. The acronym WHIMS, which stands for Workplace Hazardous Materials Information System, is a prime example of how global standards are adapted and implemented at a national level. WHIMS is based on the United Nations' Globally Harmonized System of Classification and Labelling of Chemicals (GHS), which aims to standardize the classification, labelling, and safety data sheets for hazardous chemicals worldwide. This harmonization ensures that chemical hazards are communicated consistently across different countries, facilitating safer handling, storage, and use of these substances. The adoption of GHS by countries like Canada through WHIMS underscores the importance of global recognition in regulatory frameworks. By aligning with international standards, countries can leverage the collective expertise and research from around the world to enhance their own safety protocols. This not only improves workplace safety but also simplifies international trade by reducing confusion over different labelling systems. For instance, under WHIMS, chemical manufacturers and suppliers must provide Safety Data Sheets (SDS) that follow a standardized format, making it easier for workers to understand the risks associated with the chemicals they handle. Moreover, global recognition fosters a culture of continuous improvement. As new research emerges or best practices evolve, these updates can be quickly integrated into existing standards, ensuring that workplaces remain up-to-date with the latest safety measures. This collaborative approach also encourages innovation, as industries strive to meet or exceed these standards, driving technological advancements and better safety outcomes. In addition to workplace safety, global recognition extends to various other sectors such as environmental protection, food safety, and healthcare. International standards like ISO 9001 for quality management or ISO 14001 for environmental management are widely adopted across industries, demonstrating the value placed on consistency and excellence. These standards not only enhance operational efficiency but also build trust among consumers and stakeholders by ensuring that products and services meet rigorous criteria. In conclusion, global recognition and standards are essential for creating a safer, more efficient, and interconnected world. The implementation of WHIMS in Canada exemplifies how aligning with international frameworks like GHS can significantly enhance workplace safety while promoting broader economic and environmental benefits. By embracing these standards, industries can ensure compliance, drive innovation, and contribute to a safer global community.
Breaking Down Each Letter of WHIMS
In the realm of workplace safety, acronyms often hold significant importance, and one such term is WHIMS. Standing for Workplace Hazardous Materials Information System, Health and Safety Regulations, Information, Management, and Safety Protocols, WHIMS encapsulates a comprehensive framework designed to protect workers from hazardous materials. This article delves into the intricacies of each letter, beginning with the "W" which underscores the critical role of the Workplace Hazardous Materials Information System in ensuring that employees are well-informed about the dangers they may face. The "H" highlights the stringent Health and Safety Regulations that govern the handling and use of hazardous substances. Finally, the "I," "M," and "S" collectively emphasize the importance of Information, Management, and Safety Protocols in maintaining a safe working environment. By breaking down each letter of WHIMS, this article aims to provide a detailed understanding of how these components work together to safeguard workers and promote a culture of safety in the workplace. Understanding the Acronym WHIMS is crucial for any organization committed to protecting its employees and ensuring compliance with regulatory standards.
W - Workplace Hazardous Materials Information System
**W - Workplace Hazardous Materials Information System** The Workplace Hazardous Materials Information System (WHMIS) is a critical component of workplace safety in Canada, designed to protect workers from the dangers associated with hazardous materials. WHMIS is a comprehensive system that ensures employers and workers are informed about the safe handling, use, storage, and disposal of hazardous products. At its core, WHMIS mandates that all hazardous products be labeled with standardized symbols and information, known as Safety Data Sheets (SDSs), which provide detailed instructions and warnings. This system is governed by federal, provincial, and territorial regulations, ensuring a uniform approach across Canada. WHMIS requires that all workers receive training on how to read and understand the labels and SDSs associated with the hazardous materials they handle. This training includes recognizing the pictograms and hazard statements on labels, understanding the classification of hazards, and knowing how to respond in case of emergencies. Employers are responsible for ensuring that their workplaces are compliant with WHMIS regulations, which includes maintaining up-to-date SDSs for all hazardous products, ensuring proper labeling, and providing ongoing training to employees. The implementation of WHMIS has significantly improved workplace safety by reducing the risk of accidents and exposures to hazardous substances. It fosters a culture of safety awareness among workers, enabling them to make informed decisions about their health and safety. Additionally, WHMIS aligns with international standards, such as the Globally Harmonized System of Classification and Labelling of Chemicals (GHS), ensuring that Canadian workplaces adhere to global best practices in chemical safety. In summary, WHMIS is an essential framework that safeguards workers from the risks posed by hazardous materials. By mandating clear labeling, providing comprehensive safety data sheets, and requiring thorough training, WHMIS ensures that workplaces in Canada are safer and more compliant with regulatory standards. This systematic approach to managing hazardous materials underscores the importance of proactive safety measures in protecting worker health and preventing workplace accidents. As part of the broader acronym WHMIS, the "W" stands for a robust and integrated system that is fundamental to maintaining a safe working environment.
H - Health and Safety Regulations
Health and Safety Regulations are a cornerstone of the WHIMS (Workplace Hazardous Materials Information System) framework, ensuring that workplaces handle hazardous materials with utmost care and vigilance. These regulations are designed to protect workers from the potential dangers associated with chemical substances, emphasizing both preventive measures and emergency response protocols. At the heart of these regulations is the requirement for comprehensive hazard communication, which includes labeling, material safety data sheets (MSDS), and employee training. Employers must ensure that all hazardous materials are properly labeled with clear warnings and safety information, while MSDS provide detailed data on the chemical composition, health hazards, and safe handling practices of each substance. Employee training programs are also mandatory, equipping workers with the knowledge to identify risks, use personal protective equipment (PPE) correctly, and respond effectively in case of accidents or spills. Additionally, health and safety regulations mandate regular inspections and audits to identify potential hazards before they become incidents. This proactive approach helps in maintaining a safe working environment by addressing issues such as ventilation, storage, and disposal of hazardous materials. Compliance with these regulations not only safeguards the well-being of employees but also contributes to a more efficient and productive workplace by minimizing downtime due to accidents or health-related issues. Furthermore, adherence to health and safety standards can reduce legal liabilities and enhance the overall reputation of an organization. In summary, health and safety regulations under WHIMS are crucial for creating a safe, compliant, and responsible workplace culture that prioritizes the well-being of all employees while ensuring operational excellence.
I, M, S - Information, Management, and Safety Protocols
In the context of WHIMS (Workplace Hazardous Materials Information System), the components of Information, Management, and Safety Protocols are crucial for ensuring a safe and compliant work environment. **Information** is the foundation of WHIMS, as it involves the accurate labeling, classification, and documentation of hazardous materials. This includes Safety Data Sheets (SDSs) that provide detailed information about the chemical composition, hazards, handling procedures, and emergency response measures for each substance. Employees must have easy access to this information to understand the risks associated with the materials they work with and how to handle them safely. **Management** plays a pivotal role in implementing WHIMS effectively. It encompasses the policies, procedures, and training programs that ensure all employees are aware of and adhere to safety protocols. This includes regular training sessions on how to read SDSs, use personal protective equipment (PPE), and follow safe handling practices. Effective management also involves conducting regular audits to ensure compliance with regulations and updating protocols as necessary to reflect changes in workplace conditions or new information about hazardous materials. **Safety Protocols** are the actionable steps taken to mitigate risks associated with hazardous materials. These protocols include emergency response plans, spill procedures, and first aid guidelines. They also involve the use of PPE such as gloves, goggles, and respirators to protect workers from exposure. Additionally, safety protocols may include measures like ventilation systems to reduce airborne contaminants and proper storage facilities to prevent accidents. By integrating these safety protocols into daily operations, workplaces can significantly reduce the risk of injuries and illnesses related to hazardous materials. Together, Information, Management, and Safety Protocols form a robust system that protects workers from the dangers of hazardous materials. By ensuring that all employees have access to accurate information, are well-trained in safe practices, and follow stringent safety protocols, organizations can create a safer work environment that complies with regulatory standards. This holistic approach not only safeguards health but also enhances operational efficiency and reduces the likelihood of costly accidents or legal repercussions. In essence, the I, M, S components of WHIMS are interdependent elements that collectively contribute to a safer and more responsible workplace culture.
Implementing WHIMS in Modern Workplaces
In today's modern workplaces, ensuring the safety and health of employees is paramount. One crucial aspect of achieving this goal is the implementation of Workplace Hazardous Materials Information System (WHIMS). WHIMS is a comprehensive framework designed to manage and communicate the risks associated with hazardous materials in the workplace. Effective implementation of WHIMS involves several key components. First, robust **Training and Education Programs** are essential to equip employees with the knowledge and skills necessary to handle hazardous materials safely. Second, **Labeling and Signage Requirements** must be strictly adhered to, ensuring that all hazardous substances are clearly identified and understood by workers. Finally, **Compliance and Enforcement Mechanisms** are vital for ensuring that all regulations and standards are met, thereby preventing accidents and ensuring a safe working environment. By understanding these critical elements, organizations can successfully integrate WHIMS into their operations, ultimately enhancing workplace safety and compliance. Understanding the Acronym WHIMS is the first step towards a safer, more informed workplace.
Training and Education Programs
**Implementing WHIMS in Modern Workplaces: The Crucial Role of Training and Education Programs** Training and education programs are indispensable components in the successful implementation of Workplace Hazardous Materials Information System (WHIMS) in modern workplaces. WHIMS, which stands for Workplace Hazardous Materials Information System, is a comprehensive system designed to provide workers with the information they need to safely handle hazardous materials. Effective training ensures that employees understand the risks associated with these materials and know how to mitigate them. A well-structured training program begins with an introduction to WHIMS, explaining its purpose, components, and legal requirements. This foundational knowledge is crucial as it sets the stage for more detailed training on safety data sheets (SDSs), labels, and the classification of hazardous products. Employees must be able to interpret SDSs accurately, recognizing the hazards, safe handling practices, and emergency procedures outlined in these documents. Hands-on training sessions are equally important, allowing workers to practice using personal protective equipment (PPE) and participating in simulated emergency scenarios. This experiential learning reinforces theoretical knowledge and builds confidence in handling hazardous materials safely. Regular refresher courses and updates on new regulations or changes in workplace procedures are also essential to maintain a culture of safety. Moreover, education programs should be tailored to meet the specific needs of different job roles within the workplace. For instance, supervisors and managers need training on how to conduct hazard assessments, develop safe work procedures, and ensure compliance with WHIMS regulations. Meanwhile, frontline workers require practical training on safe handling techniques and emergency response protocols. Technology can also play a significant role in enhancing WHIMS training. Online modules, interactive simulations, and mobile apps can provide accessible and engaging learning experiences. These tools allow employees to learn at their own pace and can be particularly useful for remote or shift workers who may not be able to attend traditional classroom sessions. Ultimately, the effectiveness of WHIMS depends on a workforce that is well-trained and educated. By investing in robust training and education programs, organizations can reduce the risk of accidents, improve compliance with regulations, and foster a safer work environment. This not only protects employees but also enhances operational efficiency and reduces potential liabilities. In summary, comprehensive training and education are the bedrock upon which successful WHIMS implementation is built, ensuring that modern workplaces remain safe and compliant.
Labeling and Signage Requirements
Implementing WHIMS (Workplace Hazardous Materials Information System) in modern workplaces is crucial for ensuring the safety and health of employees. A key component of WHIMS is the adherence to strict labeling and signage requirements. These requirements are designed to provide clear, consistent, and easily understandable information about the hazards associated with various chemicals and materials used in the workplace. Proper labeling involves affixing standardized hazard symbols, risk phrases, and safety precautions directly on containers or packaging. This includes the use of Globally Harmonized System (GHS) labels, which feature pictograms that visually communicate hazards such as flammability, toxicity, and environmental risks. Signage extends beyond container labels to include warning signs posted in areas where hazardous materials are stored or used, ensuring that workers are aware of potential dangers even before they encounter specific substances. Compliance with these labeling and signage standards is not only a legal mandate but also a best practice for fostering a safe work environment. Clear and consistent labeling helps prevent accidents by ensuring that workers can quickly identify hazards and take appropriate precautions. For instance, if a chemical is highly flammable, the label will clearly indicate this risk, prompting workers to handle it with care and avoid ignition sources. Similarly, signage in storage areas alerts workers to potential hazards before they enter the space, allowing them to prepare accordingly. Moreover, effective labeling and signage support ongoing training and education initiatives within the workplace. By consistently using standardized symbols and phrases, employers can reinforce safety protocols and ensure that new employees quickly understand the hazards they may encounter. This consistency also aids in compliance with regulatory requirements, reducing the risk of fines and penalties associated with non-compliance. In addition to these practical benefits, adhering to labeling and signage requirements demonstrates a commitment to worker safety and well-being. When employees see that their employer is taking proactive steps to ensure their safety through clear communication of hazards, it enhances trust and morale within the workplace. This, in turn, can lead to improved productivity and reduced turnover rates. In summary, labeling and signage are integral components of implementing WHIMS in modern workplaces. By ensuring that all hazardous materials are properly labeled and that warning signs are prominently displayed, employers can significantly reduce the risk of accidents, enhance compliance with regulations, support ongoing safety training, and foster a safer and more confident workforce. This comprehensive approach to hazard communication is essential for maintaining a safe and healthy work environment.
Compliance and Enforcement Mechanisms
**Compliance and Enforcement Mechanisms** Implementing Workplace Hazardous Materials Information System (WHMIS) in modern workplaces is crucial for ensuring the safety and health of employees. A key component of this implementation is the establishment of robust compliance and enforcement mechanisms. These mechanisms are designed to ensure that all stakeholders adhere to the regulations and standards set forth by WHMIS, thereby minimizing the risks associated with hazardous materials. At the core of these mechanisms is a comprehensive training program that educates employees on the safe handling, use, and disposal of hazardous substances. This training must be mandatory and regularly updated to reflect any changes in regulations or new hazards identified. Employers are also required to maintain accurate and accessible records of employee training, material safety data sheets (MSDS), and labels on containers. Effective enforcement involves regular audits and inspections conducted by both internal safety teams and external regulatory bodies. These audits help identify any gaps in compliance and provide opportunities for corrective actions. Employers must also establish clear policies and procedures for reporting incidents involving hazardous materials, ensuring prompt response and investigation to prevent future occurrences. Moreover, compliance is reinforced through a system of penalties and incentives. Non-compliance can result in fines, legal action, and reputational damage, while adherence to WHMIS standards can lead to reduced insurance premiums, improved employee morale, and enhanced corporate reputation. Additionally, employee participation in safety committees and feedback mechanisms encourages a culture of safety where workers feel empowered to report potential hazards without fear of retribution. Regulatory bodies such as the Occupational Safety and Health Administration (OSHA) in the United States and Health Canada play a critical role in overseeing compliance with WHMIS regulations. These agencies conduct periodic inspections, issue guidelines, and provide resources to support employers in maintaining a safe work environment. They also collaborate with industry stakeholders to update standards based on emerging research and best practices. In summary, the success of WHMIS implementation hinges on stringent compliance and enforcement mechanisms. By combining thorough training programs, rigorous auditing processes, clear reporting protocols, and a balanced system of penalties and incentives, employers can ensure that their workplaces remain safe from the risks posed by hazardous materials. This not only protects employees but also contributes to a more responsible and sustainable business environment.