What Is The Six

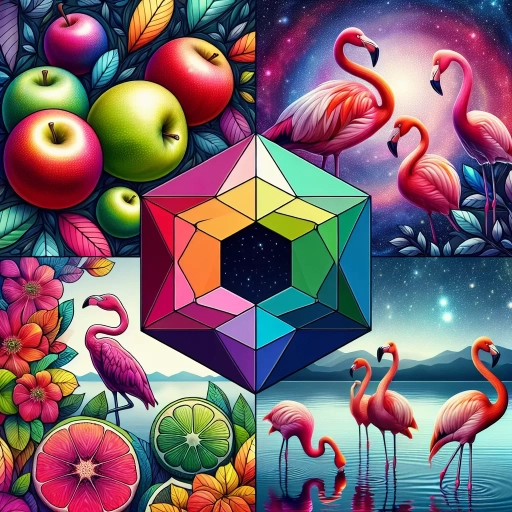
In today's competitive business landscape, organizations are continually seeking ways to enhance efficiency, reduce defects, and improve overall quality. One methodology that has gained widespread recognition for achieving these goals is Six Sigma. This data-driven approach focuses on eliminating defects and variations in processes, leading to significant improvements in productivity and customer satisfaction. To fully grasp the impact of Six Sigma, it is essential to delve into its core principles. This article will explore the concept of Six Sigma, detailing its underlying philosophy and how it differs from other quality management strategies. We will then examine the Six Sigma process, from the initial Define phase through to the final Control phase, highlighting key steps and tools involved. Additionally, we will discuss how Six Sigma is implemented across various industries, showcasing its versatility and effectiveness. By understanding these aspects, readers will gain a comprehensive view of what Six Sigma entails and how it can be applied to drive excellence in their own organizations. Let us begin by understanding the concept of Six Sigma.
Understanding the Concept of Six Sigma
Understanding the concept of Six Sigma is crucial for any organization aiming to achieve operational excellence and customer satisfaction. This methodology, rooted in statistical analysis and process improvement, has been widely adopted across various industries. To grasp the essence of Six Sigma, it is essential to delve into its definition and origins, key principles and methodologies, and the benefits and applications it offers. Starting with the **Definition and Origins**, we explore how Six Sigma emerged as a quality management strategy in the 1980s, primarily driven by Motorola's efforts to reduce defects in manufacturing processes. This foundational understanding sets the stage for comprehending the rigorous standards and metrics that define Six Sigma. The **Key Principles and Methodologies** section will outline the DMAIC (Define, Measure, Analyze, Improve, Control) framework, which is the backbone of Six Sigma projects. Here, we will discuss how each phase contributes to identifying and solving problems systematically. Finally, the **Benefits and Applications** section will highlight how implementing Six Sigma can lead to significant cost savings, enhanced product quality, and improved customer satisfaction. By applying these principles in diverse sectors, organizations can achieve substantial improvements in efficiency and effectiveness. By examining these three critical aspects, readers will gain a comprehensive understanding of what Six Sigma entails and how it can be leveraged to drive organizational success. Let's begin by exploring the **Definition and Origins** of this powerful quality management tool.
Definition and Origins
**Definition and Origins** Six Sigma is a data-driven approach to quality management that aims to reduce defects and variations in business processes. The term "Six Sigma" refers to a statistical measure of quality that strives for near perfection, with the goal of achieving no more than 3.4 defects per million opportunities. This methodology was first introduced by Bill Smith, an engineer at Motorola, in the 1980s. Smith's work built upon earlier quality control initiatives and incorporated elements from Total Quality Management (TQM) and statistical process control. The origins of Six Sigma can be traced back to Motorola's quest for improved quality in the face of intense competition. In 1987, Motorola won the Malcolm Baldrige National Quality Award, which further validated the effectiveness of the Six Sigma approach. The methodology gained widespread recognition and adoption after General Electric (GE) implemented it under the leadership of Jack Welch in the 1990s. GE's success with Six Sigma led to its widespread adoption across various industries, including manufacturing, healthcare, and finance. At its core, Six Sigma is based on the DMAIC (Define, Measure, Analyze, Improve, Control) framework. This structured approach ensures that projects are systematically managed from inception to completion. The Define phase involves identifying the problem or opportunity for improvement; Measure entails collecting data to understand the current process; Analyze involves analyzing data to identify root causes of defects; Improve focuses on implementing solutions; and Control ensures that the new process is sustained over time. Six Sigma also employs a belt-based certification system, similar to martial arts, to denote levels of expertise. The most common belts are White Belt (basic knowledge), Yellow Belt (participation in improvement projects), Green Belt (lead small-scale projects), Black Belt (lead complex projects), and Master Black Belt (expert-level practitioners who mentor and guide others). The rigorous application of statistical tools and methodologies in Six Sigma has made it a powerful tool for driving continuous improvement and achieving operational excellence. By focusing on data-driven decision-making and process optimization, organizations can significantly reduce variability, enhance customer satisfaction, and improve bottom-line performance. As a result, Six Sigma has become an integral part of many organizations' quality management strategies worldwide.
Key Principles and Methodologies
**Key Principles and Methodologies** At the heart of Six Sigma lies a robust set of principles and methodologies designed to drive continuous improvement and achieve near-perfect quality. The core principle is the DMAIC (Define, Measure, Analyze, Improve, Control) framework, which serves as a structured approach to problem-solving. **Define** involves identifying the problem or opportunity for improvement and defining the project goals. **Measure** entails collecting data to understand the current process and its performance. **Analyze** involves examining the data to identify the root causes of problems. **Improve** focuses on developing and implementing solutions to address these issues. Finally, **Control** ensures that the improvements are sustained over time through monitoring and adjustments. Another critical methodology is the use of statistical tools and techniques, such as regression analysis, hypothesis testing, and control charts. These tools help in quantifying the impact of changes and ensuring that improvements are statistically significant. The concept of "Voice of the Customer" (VOC) is also integral, emphasizing the importance of understanding customer needs and expectations to align process improvements accordingly. Six Sigma projects are typically led by certified professionals known as Belts—White Belts, Yellow Belts, Green Belts, Black Belts, and Master Black Belts—each with varying levels of expertise and responsibility. These roles ensure that projects are managed effectively and that the necessary skills and knowledge are applied throughout the DMAIC process. Additionally, Six Sigma incorporates the concept of "Critical to Quality" (CTQ) characteristics, which are key performance indicators that directly impact customer satisfaction. By focusing on these CTQs, organizations can prioritize their efforts on what truly matters to their customers. The methodology also emphasizes the importance of a data-driven decision-making culture. This involves leveraging tools like Pareto charts, fishbone diagrams, and failure mode and effects analysis (FMEA) to identify and mitigate risks. The goal is to create a culture where decisions are based on empirical evidence rather than intuition or guesswork. Overall, the key principles and methodologies of Six Sigma provide a comprehensive framework for achieving operational excellence by systematically reducing variability and defects in processes. By adhering to these principles, organizations can enhance their efficiency, reduce costs, and significantly improve customer satisfaction.
Benefits and Applications
The benefits and applications of Six Sigma are multifaceted and far-reaching, making it a highly valuable methodology for organizations across various industries. **Cost Reduction**: One of the primary benefits is significant cost reduction. By minimizing defects and variability in processes, companies can save on rework, scrap, and other inefficiencies, leading to substantial financial savings. **Enhanced Customer Satisfaction**: Six Sigma focuses on understanding customer needs and delivering products or services that meet or exceed those expectations, thereby enhancing customer satisfaction and loyalty. **Improved Efficiency**: This methodology streamlines processes, eliminating unnecessary steps and reducing cycle times, which results in increased productivity and efficiency. **Data-Driven Decision Making**: Six Sigma relies heavily on data analysis, ensuring that decisions are based on facts rather than intuition, which leads to more accurate and reliable outcomes. **Employee Engagement**: By involving employees in improvement projects, Six Sigma fosters a culture of continuous improvement and employee engagement, which can lead to higher morale and retention rates. In terms of applications, Six Sigma is versatile and can be applied in various sectors. **Manufacturing**: It is widely used in manufacturing to improve product quality and reduce defects. **Healthcare**: In healthcare, Six Sigma helps in reducing medical errors, improving patient care, and optimizing hospital operations. **Finance**: Financial institutions use Six Sigma to enhance transaction processing efficiency, reduce errors in financial reporting, and improve customer service. **Service Industries**: Service-oriented businesses leverage Six Sigma to improve service delivery times, reduce complaints, and enhance overall customer experience. **Government**: Government agencies apply Six Sigma to streamline administrative processes, reduce waste, and improve public services. Moreover, the tools and techniques of Six Sigma are applicable at different levels within an organization. **DMAIC (Define, Measure, Analyze, Improve, Control)**: This framework is used for process improvement projects. **DMADV (Define, Measure, Analyze, Design, Verify)**: This framework is used for new product or service development. **Belt Certifications**: From White Belts to Black Belts, these certifications ensure that employees have the necessary skills and knowledge to lead or participate in improvement projects effectively. Overall, the benefits of Six Sigma include cost savings, enhanced customer satisfaction, improved efficiency, data-driven decision making, and increased employee engagement. Its applications span across manufacturing, healthcare, finance, service industries, and government sectors, making it a powerful tool for any organization seeking to achieve excellence in their operations.
The Six Sigma Process: From Define to Control
The Six Sigma process is a robust methodology designed to improve the quality of processes and products by identifying and eliminating defects. This structured approach is divided into five phases: Define, Measure, Analyze, Improve, and Control. Each phase plays a crucial role in achieving the ultimate goal of near-perfect quality. The journey begins with the **Define Phase: Identifying the Problem**, where the scope of the project is clearly outlined and the problem to be addressed is defined. Following this, the **Measure Phase: Data Collection and Analysis** ensures that accurate data is collected and analyzed to understand the current process performance. Finally, the **Control Phase: Sustaining Improvements** focuses on implementing controls to ensure that the improvements made are sustained over time. By understanding these key phases, organizations can systematically drive quality improvements and achieve significant reductions in variability and defects. Let's delve deeper into the first critical step: **Define Phase: Identifying the Problem**.
Define Phase: Identifying the Problem
In the Define Phase of the Six Sigma process, the primary focus is on identifying and clearly articulating the problem or opportunity for improvement. This initial stage sets the foundation for the entire project by ensuring that all stakeholders are aligned and working towards a common goal. Here, project leaders gather data to understand the current state of the process, define the problem statement, and establish clear objectives. Key activities include conducting stakeholder analysis to identify those affected by the process, gathering voice of the customer (VOC) data to understand customer needs and expectations, and defining the project scope and boundaries. The problem statement is then formulated using tools like the SMART criteria (Specific, Measurable, Achievable, Relevant, Time-bound) to ensure clarity and focus. Additionally, a high-level process map or SIPOC (Suppliers, Inputs, Processes, Outputs, Customers) diagram is created to visualize the process flow and identify potential areas for improvement. By the end of this phase, a clear project charter is developed, outlining the problem statement, goals, and objectives, which serves as a guiding document for the subsequent phases of the Six Sigma methodology. This meticulous approach in defining the problem ensures that efforts are directed towards meaningful and impactful improvements, ultimately leading to enhanced process efficiency and customer satisfaction.
Measure Phase: Data Collection and Analysis
In the Measure Phase of the Six Sigma process, data collection and analysis are crucial steps that lay the foundation for subsequent phases. This phase is designed to gather accurate and reliable data about the current process, which helps in understanding the baseline performance and identifying opportunities for improvement. Here, teams use various tools such as process maps, fishbone diagrams, and Pareto charts to visualize the process flow and pinpoint potential problem areas. Data collection involves several key activities. First, it is essential to define clear metrics and Key Performance Indicators (KPIs) that align with the project's objectives. These metrics could include cycle time, throughput, defect rates, or customer satisfaction scores. Next, data collection plans are developed to ensure that the right data is collected from the right sources at the right time. This may involve setting up data collection tools like surveys, checklists, or automated sensors. Once data is collected, it undergoes rigorous analysis to extract meaningful insights. Statistical Process Control (SPC) techniques are often employed to monitor and control processes in real-time. Tools like histograms, scatter plots, and control charts help in understanding the distribution of data and identifying any trends or anomalies. Additionally, techniques such as regression analysis and hypothesis testing are used to establish cause-and-effect relationships between variables. The output of this phase is a detailed report that summarizes the findings from the data analysis. This report typically includes baseline performance metrics, process capability analysis, and identification of critical X's (input variables) that impact the Y's (output variables). These insights are then used in the Analyze Phase to develop hypotheses about the root causes of problems and to design experiments to test these hypotheses. Effective data collection and analysis during the Measure Phase are critical because they provide a factual basis for decision-making in later phases. By ensuring that data is accurate, complete, and relevant, teams can avoid making assumptions or relying on anecdotal evidence, thereby increasing the likelihood of successful process improvements. Overall, the Measure Phase sets the stage for a data-driven approach to problem-solving, which is a hallmark of the Six Sigma methodology.
Control Phase: Sustaining Improvements
In the Control Phase of the Six Sigma process, the primary focus is on sustaining the improvements achieved during the previous phases. This phase ensures that the new processes and solutions implemented are stable, reliable, and consistent over time. Here, the emphasis is on monitoring and controlling the performance of the process to prevent any drift or degradation. Key activities include establishing control plans, which outline the steps necessary to maintain the new process parameters and ensure that any deviations are promptly addressed. Statistical Process Control (SPC) tools are often employed to monitor key performance indicators (KPIs) and detect any anomalies or trends that may indicate a need for corrective action. Additionally, training programs are implemented to ensure that all team members understand their roles and responsibilities in maintaining the improved processes. Regular audits and reviews are conducted to verify compliance with the control plans and identify areas for further improvement. By embedding these controls into the organizational culture, the Control Phase ensures that the gains from the Six Sigma project are sustained long-term, leading to continuous improvement and enhanced operational efficiency. This phase also involves documenting lessons learned and best practices, which can be applied to future projects, thereby fostering a culture of continuous improvement within the organization. Overall, the Control Phase is crucial for ensuring that the benefits of Six Sigma initiatives are not only realized but also sustained over time.
Implementing Six Sigma in Various Industries
Implementing Six Sigma across various industries has proven to be a transformative strategy, enhancing efficiency, reducing defects, and improving overall quality. This methodology, rooted in data-driven decision-making, has been successfully applied in multiple sectors. In the manufacturing sector, Six Sigma has led to significant improvements through case studies and documented successes, showcasing its ability to streamline processes and increase productivity. The service sector, particularly in healthcare and finance, has also seen substantial benefits from Six Sigma implementation, enhancing patient care and financial services. However, the journey to Six Sigma certification is not without its challenges, necessitating careful adherence to best practices for successful implementation. By examining these aspects, we can gain a comprehensive understanding of how Six Sigma can be effectively integrated into different industries. Let us begin by exploring the manufacturing sector, where numerous case studies and successes have set the stage for widespread adoption of this powerful methodology.
Manufacturing Sector: Case Studies and Successes
The manufacturing sector has seen significant transformations and successes through the implementation of Six Sigma methodologies. One notable case study is that of General Electric (GE), which adopted Six Sigma in the late 1990s. Under the leadership of Jack Welch, GE integrated Six Sigma into its operations, resulting in substantial cost savings and quality improvements. By 2000, GE reported savings of over $2 billion, primarily due to reduced defects and improved efficiency. This success was achieved through rigorous training programs that certified thousands of employees as Black Belts and Green Belts, ensuring a widespread understanding and application of Six Sigma principles. Another exemplary case is Motorola, which pioneered the use of Six Sigma in the 1980s. Motorola's commitment to Six Sigma led to a dramatic reduction in defect rates, from 4,000 parts per million (ppm) to just 3.4 ppm. This improvement not only enhanced product quality but also contributed to Motorola's competitive edge in the market. The company's focus on continuous improvement and customer satisfaction further solidified its position as a leader in the telecommunications industry. In the automotive sector, companies like Ford and Toyota have also leveraged Six Sigma to drive excellence. Ford's implementation of Six Sigma led to significant reductions in warranty claims and production costs. For instance, Ford's Powertrain Division reported a 70% reduction in warranty claims over a five-year period following the adoption of Six Sigma. Similarly, Toyota's integration of Six Sigma with its existing lean manufacturing practices has enabled the company to maintain its reputation for high-quality vehicles while continuously improving operational efficiency. The aerospace industry has also benefited from Six Sigma. Companies like Boeing have used Six Sigma to streamline processes and enhance product reliability. Boeing's use of Six Sigma in its manufacturing operations has resulted in improved delivery times and reduced defect rates, contributing to the company's ability to meet stringent customer requirements. These case studies highlight the versatility and effectiveness of Six Sigma across various manufacturing sectors. By focusing on data-driven decision-making, process optimization, and continuous improvement, companies can achieve substantial gains in quality, efficiency, and customer satisfaction. The widespread adoption of Six Sigma underscores its value as a powerful tool for driving excellence in manufacturing operations.
Service Sector: Application in Healthcare and Finance
The service sector, a significant component of modern economies, plays a crucial role in industries such as healthcare and finance. In these sectors, the application of Six Sigma methodologies can significantly enhance operational efficiency, customer satisfaction, and overall quality. In healthcare, Six Sigma is applied to streamline clinical processes, reduce medical errors, and improve patient outcomes. For instance, hospitals use Six Sigma to optimize patient flow, reducing wait times and improving the timeliness of care. By analyzing data on patient throughput, hospitals can identify bottlenecks and implement changes that ensure smoother transitions between departments. Additionally, Six Sigma helps in reducing medication errors by standardizing prescribing practices and improving communication among healthcare providers. This not only enhances patient safety but also reduces costs associated with adverse events. In the finance sector, Six Sigma is utilized to enhance transactional processes, reduce errors in financial reporting, and improve customer service. Financial institutions apply Six Sigma to optimize their back-office operations, such as account opening and loan processing. By mapping out these processes and identifying inefficiencies, banks can reduce cycle times and minimize errors, leading to higher customer satisfaction and lower operational costs. Furthermore, Six Sigma helps in risk management by identifying potential failures in financial systems and implementing controls to mitigate these risks. This ensures compliance with regulatory requirements and maintains the integrity of financial transactions. Both healthcare and finance benefit from the data-driven approach of Six Sigma, which relies on statistical analysis to identify areas for improvement. The DMAIC (Define, Measure, Analyze, Improve, Control) framework of Six Sigma provides a structured methodology for problem-solving, ensuring that improvements are sustainable and measurable. By adopting Six Sigma principles, these industries can achieve higher levels of quality, reduce variability in processes, and ultimately deliver better services to their customers. In summary, the application of Six Sigma in the service sector, particularly in healthcare and finance, is instrumental in driving quality improvements and operational efficiencies. By leveraging data analytics and process optimization techniques, these industries can enhance their service delivery, reduce errors, and improve customer satisfaction, ultimately contributing to better outcomes and higher value for stakeholders.
Challenges and Best Practices for Implementation
Implementing Six Sigma across various industries presents several challenges that must be addressed to ensure successful integration and sustained improvement. One of the primary challenges is **cultural resistance**, as employees may be hesitant to adopt new methodologies and processes. To overcome this, it is crucial to engage in thorough **change management** strategies, including clear communication, training, and involving key stakeholders in the decision-making process. Another significant challenge is **data quality and availability**, as Six Sigma relies heavily on accurate and comprehensive data to drive decision-making. Best practices include establishing robust data collection systems and ensuring that data is reliable, accessible, and consistently updated. **Resource allocation** is another critical challenge, as implementing Six Sigma requires significant investment in training, tools, and personnel. Effective resource management involves allocating sufficient time and budget for training Black Belts and Green Belts, as well as providing necessary software and infrastructure. **Sustainability** is also a key concern; to maintain long-term benefits, organizations should integrate Six Sigma into their core business processes and continuously monitor and evaluate project outcomes. Best practices for implementation include **aligning Six Sigma projects with strategic goals**, ensuring that initiatives are focused on high-impact areas that drive business value. **Strong leadership support** is essential, as it sets the tone for organizational commitment and provides the necessary resources and encouragement. Additionally, **cross-functional collaboration** is vital; involving teams from different departments fosters a holistic approach to problem-solving and ensures that solutions are practical and feasible. **Continuous improvement** should be embedded in the organizational culture, encouraging ongoing learning and adaptation. This can be achieved through regular **feedback loops** and **performance metrics** that measure the effectiveness of Six Sigma projects. Furthermore, **celebrating successes** and recognizing the contributions of team members can help maintain morale and motivation. In summary, while implementing Six Sigma poses several challenges, adhering to best practices such as effective change management, robust data systems, strategic alignment, strong leadership support, cross-functional collaboration, continuous improvement, and recognizing team achievements can significantly enhance the likelihood of successful implementation and sustained benefits across various industries.