What Is A Micrometer

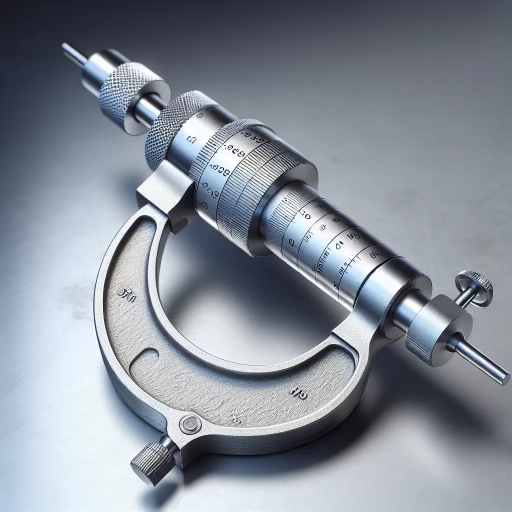
A micrometer is a precision measuring instrument that plays a crucial role in various fields, including engineering, manufacturing, and scientific research. This tool is designed to measure small distances or thicknesses with high accuracy, making it indispensable for tasks that require precise measurements. To fully appreciate the utility of a micrometer, it is essential to understand its fundamental principles, learn how to use it effectively, and recognize its diverse applications. In this article, we will delve into the basics of a micrometer, explaining its components and how it operates. We will also provide guidance on how to use a micrometer effectively, ensuring accurate and reliable measurements. Finally, we will explore the applications and importance of micrometers across different industries. By understanding these aspects, you will gain a comprehensive insight into the world of micrometers. Let us begin by understanding the basics of a micrometer.
Understanding the Basics of a Micrometer
Understanding the basics of a micrometer is crucial for anyone involved in precision measurement, whether in engineering, manufacturing, or scientific research. A micrometer is a highly accurate measuring instrument that allows users to measure small distances with great precision. To fully grasp the utility of a micrometer, it is essential to delve into three key aspects: its definition and purpose, the various types available, and its key components. Firstly, understanding the definition and purpose of a micrometer sets the foundation for its use. This involves recognizing how it differs from other measuring tools and why it is indispensable in certain fields. Secondly, knowing the different types of micrometers—such as digital, mechanical, and vernier micrometers—helps in selecting the right tool for specific tasks. Lastly, familiarizing oneself with the key components of a micrometer, such as the anvil, spindle, and thimble, ensures proper handling and accurate measurements. By exploring these facets, users can unlock the full potential of this precise instrument. Let's begin by examining the definition and purpose of a micrometer, which will provide a clear understanding of its role in precision measurement.
Definition and Purpose
A micrometer is a precision measuring instrument designed to accurately measure small distances, typically in the range of millimeters or inches. The definition of a micrometer revolves around its ability to provide precise measurements with high resolution, often down to 0.01 millimeters or 0.001 inches. The primary purpose of a micrometer is to facilitate the measurement of dimensions such as the thickness of objects, the diameter of cylindrical objects, and other linear dimensions where high accuracy is crucial. In various fields like engineering, manufacturing, and quality control, micrometers serve as essential tools for ensuring that components meet specific dimensional tolerances. For instance, in the production of mechanical parts, micrometers help verify that the dimensions of parts are within acceptable limits, thereby ensuring proper fit and function. In scientific research, micrometers are used to measure the dimensions of small specimens or components with precision, which is vital for accurate data collection and analysis. The use of micrometers also extends to educational settings where students learn about measurement techniques and the importance of precision in scientific and engineering applications. Understanding how to use a micrometer correctly involves knowing its components, such as the anvil, spindle, and thimble, and how to read the measurements accurately from the scale. Overall, the purpose of a micrometer is multifaceted: it provides reliable and precise measurements, enhances quality control processes, supports scientific research, and educates users on the principles of accurate measurement. By understanding the basics of a micrometer, individuals can effectively utilize this tool to achieve high levels of precision in their work, whether in industry, research, or education.
Types of Micrometers
Micrometers are precision measuring instruments used to measure small distances, thicknesses, and diameters with high accuracy. There are several types of micrometers, each designed for specific applications and offering unique advantages. 1. **Outside Micrometer**: This is the most common type and is used to measure the outside dimensions of objects such as the diameter of a rod or the width of a piece of material. It consists of a U-shaped frame with a movable jaw that can be adjusted to fit around the object being measured. 2. **Inside Micrometer**: Designed to measure the inside dimensions of objects, such as the diameter of a hole or the width of an opening. It typically has a set of interchangeable rods and spindles that allow for different ranges of measurement. 3. **Depth Micrometer**: Used to measure the depth of holes, steps, or recesses in objects. It features a vertical spindle that moves up and down within a fixed sleeve, allowing precise depth measurements. 4. **Digital Micrometer**: Offers electronic measurement and display, often with additional features like data storage and statistical analysis. These micrometers provide quick readings and are particularly useful in high-volume production environments where speed and accuracy are crucial. 5. **Bore Micrometer**: Specialized for measuring the internal diameters of bores or holes. It usually includes a set of interchangeable anvil sets that can be adjusted to fit different bore sizes. 6. **Thread Micrometer**: Designed specifically for measuring the pitch diameter of threads on screws, bolts, and other threaded components. It ensures that the threads are within specified tolerances. 7. **Vernier Micrometer**: Uses a vernier scale for precise measurements, often used in applications where high accuracy is required but digital technology is not necessary. It combines the simplicity of mechanical measurement with the precision of vernier scales. 8. **Caliper Micrometer**: Combines the functionality of calipers with the precision of a micrometer, allowing for both inside and outside measurements without needing to switch between different tools. Each type of micrometer is engineered to meet specific measurement needs, ensuring that users can achieve accurate and reliable results across various industrial, scientific, and engineering applications. Understanding these different types is essential for selecting the right tool for the job and ensuring that measurements are taken accurately and efficiently.
Key Components
When understanding the basics of a micrometer, it is crucial to familiarize yourself with its key components. A micrometer, whether it is a digital or mechanical type, consists of several essential parts that work together to provide precise measurements. 1. **Frame**: The frame is the main body of the micrometer and houses all other components. It provides structural support and ensures stability during measurements. 2. **Anvil**: The anvil is one of the two flat surfaces that come into contact with the object being measured. It is typically fixed and serves as a reference point. 3. **Spindle**: The spindle is the movable part that extends from the frame and has a flat surface at its end, which comes into contact with the object being measured. It moves in and out when the thimble is turned. 4. **Thimble**: The thimble is a rotating ring that surrounds the barrel. Turning the thimble causes the spindle to move in or out, allowing for precise adjustments. 5. **Barrel**: The barrel is the cylindrical part that contains the graduated scale. It moves along with the spindle as the thimble is turned. 6. **Graduated Scale**: This scale is marked on the barrel and indicates the measurement in units such as millimeters or inches. It is divided into main scale divisions and vernier scale divisions for finer measurements. 7. **Vernier Scale**: The vernier scale is a secondary scale that slides along the main scale. It allows for more precise readings by aligning with the main scale to indicate fractional parts of a division. 8. **Ratchet Stop**: Some micrometers come with a ratchet stop, which helps to apply consistent pressure when taking measurements, ensuring accuracy and reducing user error. 9. **Lock Nut**: The lock nut is used to secure the spindle in place once a measurement has been taken, allowing for easy reading and recording of the measurement. Understanding these components and how they interact is fundamental to using a micrometer effectively. Each part plays a critical role in ensuring accurate and reliable measurements, making it essential to handle and maintain them properly. By knowing how to operate these components correctly, users can achieve high precision in their measurements, which is vital in various fields such as engineering, manufacturing, and quality control.
How to Use a Micrometer Effectively
To use a micrometer effectively, it is crucial to understand and master several key aspects. First, proper calibration and zeroing are essential to ensure accurate measurements. This involves setting the micrometer to a known standard and adjusting it so that the zero mark aligns correctly. Second, employing the right measurement techniques is vital; this includes handling the micrometer correctly, applying consistent pressure, and reading the measurements accurately. Finally, being aware of common mistakes to avoid can significantly improve the reliability of your measurements. By focusing on these three areas—calibration and zeroing, measurement techniques, and common mistakes to avoid—you can ensure that your use of a micrometer is both precise and reliable. Let's start by delving into the importance of calibration and zeroing, as this foundational step sets the stage for all subsequent measurements.
Calibration and Zeroing
Calibration and zeroing are crucial steps in ensuring the accuracy and reliability of a micrometer, a precision measuring instrument used to measure small distances or dimensions. **Calibration** involves comparing the measurements obtained from the micrometer against a known standard to verify its accuracy. This process is essential because micrometers, like any other measuring tool, can drift over time due to wear and tear, environmental changes, or improper handling. Calibration typically involves using certified calibration standards or reference gauges that have been precisely calibrated to known dimensions. By comparing the micrometer's readings against these standards, any deviations can be identified and corrected, ensuring that the micrometer provides accurate measurements. **Zeroing**, on the other hand, is the process of setting the micrometer to a zero reference point before taking measurements. This step is vital because it ensures that the initial position of the micrometer is correctly aligned with the object being measured. To zero a micrometer, the anvil and spindle are brought into contact, and the thimble is adjusted until the zero mark on the thimble aligns with the zero mark on the barrel. This ensures that any subsequent measurements are relative to this zero point, eliminating any potential offset errors. Proper zeroing also helps in maintaining consistency across multiple measurements, which is critical in precision engineering and quality control applications. In practice, calibration and zeroing should be performed regularly as part of routine maintenance to ensure the micrometer remains accurate. For instance, before starting a series of measurements, it is good practice to quickly zero the micrometer to account for any minor adjustments that may have occurred since the last use. Additionally, periodic calibration checks should be scheduled based on usage and environmental conditions to maintain the highest level of precision. By adhering to these procedures, users can trust their micrometer to deliver precise measurements consistently, which is paramount in various fields such as engineering, manufacturing, and scientific research where small variations can have significant implications. Effective use of a micrometer thus hinges on these foundational steps of calibration and zeroing, ensuring that measurements are reliable and accurate.
Measurement Techniques
Measurement techniques are fundamental in various fields, including engineering, science, and quality control, where precision and accuracy are paramount. One of the most precise measurement tools is the micrometer, which allows for the measurement of small distances and dimensions with high accuracy. To use a micrometer effectively, it is crucial to understand the different types available, such as digital micrometers, dial micrometers, and vernier micrometers. Each type has its own set of advantages and specific applications. For instance, digital micrometers offer quick and easy readings with high precision, while vernier micrometers provide a more traditional approach that requires careful alignment of the vernier scale. When using a micrometer, proper handling and setup are essential. Start by ensuring the micrometer is calibrated and free from any debris or wear. The object to be measured should be placed between the anvil and the spindle, ensuring it is centered and securely held in place. The thimble should be turned clockwise until it makes light contact with the object; over-tightening can lead to inaccurate readings due to deformation of the object being measured. It is also important to take multiple readings from different angles to account for any irregularities in the object's surface. In addition to proper use of the micrometer itself, understanding the environment in which measurements are taken is critical. Temperature variations can affect the accuracy of measurements due to thermal expansion or contraction of materials. Therefore, it is advisable to conduct measurements in a controlled environment where temperature fluctuations are minimal. Furthermore, maintaining good practice in recording and interpreting measurements is vital. Readings should be recorded carefully, and any uncertainties or limitations of the measurement technique should be noted. For example, if using a vernier micrometer, ensure that the zero error is accounted for before taking final readings. Incorporating other measurement techniques alongside micrometer use can enhance overall accuracy and reliability. For example, using a combination of calipers and micrometers can provide a more comprehensive understanding of an object's dimensions. Additionally, leveraging advanced technologies such as laser interferometry or coordinate measuring machines (CMMs) can offer even higher precision in certain applications. In conclusion, effective use of a micrometer involves not only mastering the tool itself but also understanding the broader context of measurement techniques and best practices. By ensuring proper calibration, handling, and environmental control, along with integrating other measurement methods where necessary, users can achieve highly accurate and reliable results that are essential in various professional and scientific endeavors.
Common Mistakes to Avoid
When using a micrometer effectively, it is crucial to avoid several common mistakes that can compromise the accuracy and reliability of your measurements. One of the most significant errors is improper calibration. Always ensure that your micrometer is calibrated correctly before use, as any deviation can lead to inaccurate readings. Another critical mistake is failing to clean the micrometer and the object being measured. Dirt, oil, or other contaminants can interfere with the precision of the measurement, so it is essential to keep both the micrometer and the object free from debris. Incorrect handling is another common issue. Always hold the micrometer firmly but gently, avoiding excessive pressure which can distort the measurement. Additionally, ensure that the micrometer is perpendicular to the object being measured; any angle can introduce errors. Misreading the scale is also a frequent mistake. Pay close attention to the zero point and the direction of measurement to avoid misinterpretation. It is also important to use the correct type of micrometer for your specific application; for example, using a digital micrometer when precision is paramount or an analog micrometer for more general measurements. Furthermore, neglecting to check for wear and tear on the micrometer itself can lead to inaccurate readings over time. Regularly inspect the anvil and spindle for signs of wear and replace them if necessary. Consistency in measurement technique is also vital; always use the same method and apply consistent pressure to ensure reproducibility of results. Lastly, not following proper measurement procedures can lead to significant errors. Always take multiple readings and average them to account for any minor variations. It is also advisable to measure in different locations on the object to ensure uniformity. By avoiding these common mistakes, you can ensure that your measurements are accurate, reliable, and consistent, thereby enhancing the effectiveness of your micrometer usage.
Applications and Importance of Micrometers
Micrometers are precision instruments that have revolutionized various fields by enabling accurate measurements at the microscopic level. Their applications span across multiple domains, each highlighting their importance in different contexts. In industrial settings, micrometers play a crucial role in ensuring the precise dimensions of components, which is vital for maintaining quality and efficiency. They are also indispensable in scientific research, where accurate measurements are essential for conducting experiments and gathering data. Additionally, micrometers are pivotal in quality control and precision engineering, where they help in verifying the specifications of products and components. By understanding these diverse applications, we can appreciate the significance of micrometers in modern industries. Let's delve into the industrial uses of micrometers first, where their impact is particularly evident.
Industrial Uses
Industrial uses of micrometers are diverse and critical, reflecting their precision and reliability in various sectors. In manufacturing, micrometers are essential for quality control, ensuring that components meet exact specifications. For instance, in the automotive industry, micrometers measure the thickness of engine components, brake pads, and other parts to guarantee safety and performance. Similarly, in aerospace engineering, micrometers verify the dimensions of aircraft parts to maintain stringent safety standards. In the field of metalworking, micrometers are used to measure the thickness of metal sheets, rods, and other materials before and after processing. This ensures that the final products adhere to required tolerances. In electronics manufacturing, micrometers measure the dimensions of tiny components such as circuit boards, wires, and semiconductor devices. This precision is crucial for ensuring proper assembly and functionality. The construction industry also relies heavily on micrometers for measuring materials like wood, concrete, and steel. Accurate measurements are vital for structural integrity and compliance with building codes. Additionally, in the medical device industry, micrometers are used to measure the dimensions of implants, surgical instruments, and other medical equipment where precision is paramount for patient safety. Furthermore, micrometers play a significant role in research and development across various industries. Scientists use them to measure samples in laboratories, ensuring accurate data collection and analysis. In the textile industry, micrometers measure fabric thickness and density, which affects the quality and performance of fabrics. Overall, the applications of micrometers in industrial settings underscore their importance in maintaining quality, safety, and efficiency. By providing precise measurements, micrometers help industries produce reliable products that meet or exceed standards, thereby enhancing consumer trust and satisfaction. Their versatility and accuracy make them indispensable tools in modern industrial practices.
Scientific Research Applications
Scientific research applications of micrometers are diverse and pivotal, underscoring their importance in various fields. In materials science, micrometers are used to measure the thickness and dimensions of materials with high precision, which is crucial for understanding material properties and optimizing manufacturing processes. For instance, in the development of nanomaterials, accurate measurements at the micrometer scale are essential for characterizing particle sizes and distributions, influencing their performance in applications such as electronics and biomedical devices. In biology and life sciences, micrometers are indispensable tools for cell biology and histology. They enable researchers to measure cell sizes, tissue thickness, and other microscopic dimensions accurately, which is vital for diagnosing diseases and understanding cellular behavior. For example, in cancer research, precise measurements of tumor cells can help in assessing the progression of the disease and evaluating treatment efficacy. In engineering and manufacturing, micrometers play a critical role in quality control and precision engineering. They are used to measure the dimensions of parts and components with high accuracy, ensuring that products meet stringent specifications. This is particularly important in industries such as aerospace and automotive, where even slight deviations can have significant safety implications. In environmental science, micrometers are used to analyze particulate matter in air and water samples. By measuring the size and distribution of particles, researchers can assess air and water quality, which is crucial for public health and environmental policy-making. Additionally, in geology, micrometers help in analyzing rock samples and sediment cores, providing insights into geological processes and historical environmental conditions. The importance of micrometers extends to educational settings as well. They serve as teaching tools in science and engineering curricula, helping students understand measurement principles and develop practical skills in scientific inquiry. Furthermore, advancements in digital micrometers have enhanced their usability and accuracy, making them more accessible to a broader range of users. Overall, the applications of micrometers in scientific research highlight their versatility and necessity across multiple disciplines. Their ability to provide precise measurements at the micrometer scale is fundamental to advancing our understanding of materials, biological systems, engineering processes, environmental conditions, and educational practices. As technology continues to evolve, the role of micrometers will remain central to ensuring accuracy and precision in various scientific endeavors.
Quality Control and Precision Engineering
Quality Control and Precision Engineering are pivotal in ensuring the accuracy and reliability of manufactured products. In these fields, micrometers play a crucial role as they provide precise measurements down to the smallest details. Quality control involves rigorous inspection and testing to guarantee that products meet specified standards, and micrometers are essential tools for this process. They allow engineers to measure dimensions with high accuracy, which is critical in industries such as aerospace, automotive, and medical devices where even slight deviations can have significant consequences. Precision engineering, on the other hand, focuses on the design and manufacture of components that require exacting tolerances. Here, micrometers are indispensable for verifying that parts are made to precise specifications. For instance, in the production of precision machinery or electronic components, micrometers help ensure that each part fits perfectly into its intended assembly without any discrepancies. This level of precision not only enhances the performance and longevity of the final product but also reduces the risk of defects and failures. The importance of micrometers in these contexts cannot be overstated. They enable engineers to detect even minor variations that could compromise the integrity of a product. In quality control, micrometers facilitate the identification of defects early in the manufacturing process, allowing for immediate corrective actions and thus saving time and resources. In precision engineering, they ensure that components are fabricated with the required level of accuracy, which is vital for maintaining the overall quality and functionality of complex systems. Moreover, advancements in technology have led to the development of digital micrometers that offer even greater precision and ease of use compared to their analog counterparts. These digital tools often come with additional features such as data storage and statistical analysis capabilities, further enhancing their utility in quality control and precision engineering applications. In summary, micrometers are fundamental instruments in quality control and precision engineering due to their ability to provide highly accurate measurements. Their role in ensuring product reliability, detecting defects, and maintaining stringent manufacturing standards makes them an indispensable asset across various industries. As technology continues to evolve, the importance of micrometers will only grow, underscoring their critical position in maintaining the highest levels of quality and precision in modern manufacturing processes.