What Is Cross Docking

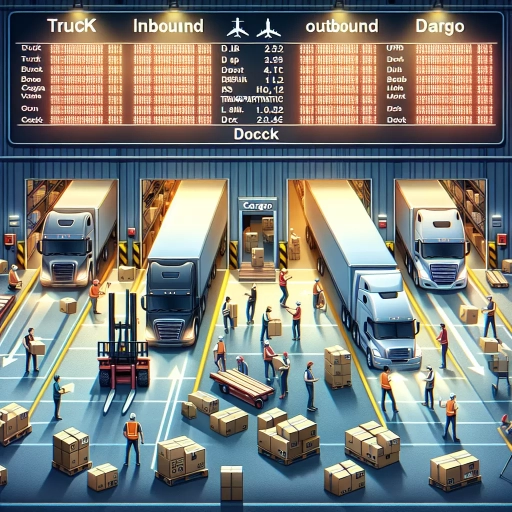
What is Cross Docking?
Cross docking is a logistics strategy that has revolutionized the way goods are handled and distributed, offering significant improvements in efficiency, cost savings, and customer satisfaction. At its core, cross docking involves the direct transfer of goods from incoming to outgoing vehicles without storing them in a warehouse, thereby minimizing handling and storage costs. To fully understand this concept, it is essential to delve into its definition and basic principles, which form the foundation of this logistics technique. Additionally, exploring the historical context and evolution of cross docking provides valuable insights into how this method has adapted to changing market demands and technological advancements. Finally, examining the key benefits and advantages of cross docking highlights why it has become a preferred strategy for many businesses seeking to streamline their supply chains. By understanding these aspects, one can appreciate the comprehensive value that cross docking brings to modern logistics operations. Let us begin by defining and exploring the basic principles of cross docking.
Definition and Basic Principles
**Definition and Basic Principles** Cross docking is a logistics strategy that streamlines the distribution process by minimizing or eliminating the need for inventory storage. At its core, cross docking involves the direct transfer of goods from incoming shipments to outgoing shipments without intermediate storage. This approach leverages a facility, often referred to as a cross dock, where products are received, sorted, and then immediately shipped out to their final destinations. The basic principles of cross docking are rooted in efficiency and speed. 1. **Efficient Receipt and Sorting**: Goods are received at the cross dock facility in a manner that allows for quick identification and sorting. This is typically achieved through advanced tracking systems and clear labeling. 2. **Minimal Handling**: To reduce costs and prevent damage, products are handled as little as possible. This means that goods are moved directly from the receiving dock to the shipping dock with minimal intervention. 3. **Real-Time Coordination**: Effective cross docking relies on real-time coordination between suppliers, carriers, and customers. This ensures that incoming shipments are matched with outgoing shipments seamlessly. 4. **Just-in-Time Delivery**: Cross docking aligns perfectly with just-in-time delivery principles, where products are delivered exactly when they are needed, reducing the need for inventory holding. 5. **Technology Integration**: Modern cross docking operations heavily rely on technology such as barcode scanning, RFID tags, and sophisticated software systems to manage the flow of goods efficiently. By adhering to these principles, businesses can significantly reduce their operational costs associated with storage, handling, and inventory management. Cross docking also enhances supply chain visibility, allowing for better tracking and monitoring of goods throughout the distribution process. This approach is particularly beneficial for perishable items or products with high demand variability, as it ensures that goods reach their destinations quickly and in optimal condition. In summary, the definition of cross docking revolves around the swift transfer of goods without intermediate storage, while its basic principles focus on efficiency, minimal handling, real-time coordination, just-in-time delivery, and technology integration. By implementing these principles effectively, businesses can achieve a more agile and responsive supply chain that meets the dynamic needs of today's market.
Historical Context and Evolution
Cross docking, a logistics strategy that involves the direct transfer of goods from incoming to outgoing vehicles without intermediate storage, has a rich historical context and evolutionary journey. The concept of cross docking dates back to the early 20th century when railroads began using this method to expedite the movement of goods. However, it wasn't until the post-World War II era that cross docking started to gain significant traction. During this period, the rise of suburbanization and the expansion of the interstate highway system in the United States created a demand for more efficient distribution networks. In the 1960s and 1970s, as global trade increased and supply chains became more complex, companies began to adopt cross docking as a way to reduce inventory costs and improve delivery times. The advent of barcode scanning and other automated technologies in the 1980s further enhanced the efficiency of cross docking operations by allowing for real-time tracking and quicker processing of goods. The 1990s saw a significant leap forward with the integration of advanced information technologies such as Electronic Data Interchange (EDI) and Enterprise Resource Planning (ERP) systems. These technologies enabled better coordination between suppliers, manufacturers, and retailers, making it possible to streamline cross docking processes even further. In recent years, the evolution of cross docking has been influenced by e-commerce growth and consumer expectations for fast and reliable delivery. The rise of omnichannel retailing has necessitated more agile supply chains, with cross docking playing a crucial role in meeting these demands. Modern cross docking facilities are equipped with sophisticated automation tools like robotics and artificial intelligence, which help in optimizing operations and reducing errors. Moreover, sustainability concerns have led companies to adopt greener practices within their cross docking operations. This includes using energy-efficient equipment, reducing waste through better packaging strategies, and implementing green logistics initiatives. Today, cross docking is not just a tactical tool but a strategic component of supply chain management. It allows businesses to respond quickly to market changes while maintaining high levels of customer satisfaction. As technology continues to advance and consumer behaviors evolve, the role of cross docking will likely become even more pivotal in ensuring the efficiency and resilience of global supply chains. This historical context underscores how cross docking has transformed from a simple logistics technique into a sophisticated strategy that underpins modern supply chain operations. Its evolution reflects broader trends in technology, consumer behavior, and economic conditions, making it an indispensable part of contemporary business practices.
Key Benefits and Advantages
Cross docking offers a multitude of key benefits and advantages that make it an indispensable logistics strategy for many businesses. At its core, cross docking streamlines the supply chain by minimizing storage time and maximizing the speed of goods movement. One of the primary advantages is **reduced inventory costs**; since products are not stored for extended periods, businesses can avoid the expenses associated with warehousing and inventory management. This approach also **enhances operational efficiency** by eliminating the need for extensive handling and storage processes, thereby reducing labor costs and improving overall productivity. Another significant benefit of cross docking is **improved delivery times**. By directly transferring goods from incoming to outgoing vehicles, cross docking accelerates the shipment process, ensuring that products reach their destinations more quickly. This rapid transit not only satisfies customer expectations but also helps businesses to stay competitive in fast-paced markets. Additionally, cross docking **reduces damage and loss** of goods, as the minimal handling involved in the process minimizes the risk of product damage or theft. From a strategic perspective, cross docking **optimizes supply chain visibility**. With real-time tracking and monitoring capabilities, businesses can better manage their inventory flow, identify bottlenecks, and make informed decisions to improve their logistics operations. This heightened visibility also enables more effective **demand forecasting**, allowing companies to adjust their supply chains according to market demands and avoid stockouts or overstocking. Moreover, cross docking is particularly beneficial for **perishable goods**. By ensuring that these items are moved swiftly through the supply chain, businesses can maintain product quality and extend shelf life. This is crucial for industries such as food and pharmaceuticals where timely delivery is paramount. In terms of environmental impact, cross docking can contribute to **sustainability** by reducing the number of trips required to transport goods. Fewer trips mean lower fuel consumption and reduced carbon emissions, aligning with many companies' sustainability goals. Furthermore, the efficiency of cross docking can lead to **cost savings** on fuel and transportation costs, which can be reinvested into other areas of the business. Overall, the integration of cross docking into a company's logistics strategy can lead to significant improvements in operational efficiency, cost savings, and customer satisfaction. By leveraging these advantages, businesses can enhance their competitive edge and achieve greater success in today's dynamic market environment.
How Does Cross Docking Work?
Cross docking is a logistics strategy that streamlines the supply chain by minimizing storage and maximizing efficiency. This innovative approach involves the direct transfer of goods from incoming to outgoing vehicles, bypassing traditional warehousing processes. To understand how cross docking works, it is essential to delve into its step-by-step process, explore the various types of cross docking operations, and examine the technology and infrastructure requirements that support this method. The **Step-by-Step Process Overview** will provide a detailed look at how goods are received, sorted, and dispatched in a seamless manner. This section will outline the critical stages involved in ensuring that products move swiftly through the cross dock facility without unnecessary delays. Additionally, **Types of Cross Docking Operations** will discuss the different models that can be implemented, such as continuous cross docking, consolidation cross docking, and deconsolidation cross docking. Each type caters to specific business needs and can be tailored to optimize logistics for various industries. Finally, **Technology and Infrastructure Requirements** will highlight the importance of advanced systems and physical infrastructure in facilitating smooth cross docking operations. From automated sorting systems to robust data analytics, these elements are crucial for maintaining the efficiency and accuracy that define successful cross docking. By understanding these components, businesses can better leverage cross docking to enhance their supply chain operations. Let's begin with a closer look at the **Step-by-Step Process Overview** to see how this efficient logistics strategy unfolds in practice.
Step-by-Step Process Overview
Cross docking is a logistics strategy that streamlines the distribution process by minimizing storage and maximizing efficiency. Here is a step-by-step overview of how cross docking works: 1. **Receipt of Goods**: The process begins with the arrival of goods at the cross dock facility. These goods can come from various suppliers and are typically transported via trucks or other vehicles. 2. **Inspection and Sorting**: Upon arrival, the goods are inspected for quality and accuracy. They are then sorted based on their destination, often using advanced technology such as barcode scanners and automated sorting systems. 3. **Labeling and Tagging**: Once sorted, the goods are labeled and tagged with the appropriate shipping information. This includes details like the final destination, handling instructions, and any special requirements. 4. **Loading onto Outbound Vehicles**: The sorted and labeled goods are then loaded directly onto outbound vehicles. This step is crucial as it ensures that the goods are ready for immediate shipment without the need for storage. 5. **Consolidation**: In some cases, goods from multiple suppliers may be consolidated into a single shipment to optimize transportation costs and efficiency. This involves combining different products into a single load. 6. **Immediate Shipment**: The loaded vehicles are then dispatched immediately to their respective destinations. This rapid turnaround time is a hallmark of cross docking, significantly reducing the time goods spend in transit. 7. **Real-Time Tracking**: Throughout the process, real-time tracking systems are often used to monitor the movement of goods. This ensures transparency and allows for quick adjustments if any issues arise during transit. 8. **Continuous Improvement**: After each shipment, data is collected and analyzed to identify areas for improvement. This feedback loop helps in optimizing the cross docking process over time. By following these steps, cross docking eliminates the need for extensive warehousing and reduces handling costs, making it an efficient and cost-effective logistics solution for many businesses. This streamlined approach not only speeds up the delivery process but also enhances customer satisfaction by ensuring timely and accurate receipt of goods.
Types of Cross Docking Operations
Cross docking operations are a critical component of modern logistics and supply chain management, offering several types tailored to different business needs and operational environments. **Pre-Distribution Cross Docking** is one of the most common types, where products are received from suppliers, sorted, and then immediately shipped to customers without being stored in a warehouse. This method is particularly effective for perishable goods or high-demand items that need rapid distribution. **Post-Distribution Cross Docking**, on the other hand, involves consolidating shipments from multiple suppliers at a central location before redistributing them to various retail stores or customers. This type is beneficial for companies that need to manage a diverse range of products and ensure timely delivery to multiple destinations. **Hub and Spoke Cross Docking** operates through a central hub where goods are collected, sorted, and then dispatched to various spokes or satellite locations. This model is ideal for companies with extensive distribution networks, as it streamlines the process and reduces transit times. **Manufacturing Cross Docking** integrates cross docking directly into the manufacturing process. Here, raw materials or components are received at a manufacturing facility, processed, and then shipped out as finished products without intermediate storage. This approach is particularly useful for just-in-time production systems. **Retail Cross Docking** focuses on the final leg of the supply chain, where products are received at a retail distribution center, sorted according to store requirements, and then shipped directly to retail outlets. This method helps retailers maintain inventory levels and ensure that products reach shelves quickly. Each type of cross docking operation leverages the core principles of efficiency, speed, and reduced inventory holding costs. By selecting the appropriate type based on their specific needs, businesses can optimize their supply chain operations, enhance customer satisfaction, and gain a competitive edge in the market. Understanding these different types is essential for implementing effective cross docking strategies that align with overall business objectives.
Technology and Infrastructure Requirements
To fully understand how cross docking works, it is crucial to delve into the technology and infrastructure requirements that underpin this efficient logistics strategy. Cross docking, a process where goods are received from inbound shipments and then immediately transferred to outbound shipments without being stored in a warehouse, relies heavily on advanced technology and robust infrastructure. At the heart of cross docking operations is a sophisticated warehouse management system (WMS) that orchestrates the entire process. This WMS integrates with various technologies such as barcode scanning, RFID tags, and automated sorting systems to ensure seamless tracking and movement of goods. Advanced data analytics and real-time monitoring tools are also essential, enabling logistics managers to optimize workflows, predict demand, and manage inventory levels effectively. Additionally, robust transportation management systems (TMS) are necessary to coordinate inbound and outbound shipments efficiently, ensuring that goods are moved swiftly from one location to another. The physical infrastructure of the cross docking facility itself is equally important; it must be designed with high ceilings, ample docking bays, and efficient material handling equipment such as conveyor belts and forklifts. This setup allows for rapid loading and unloading of goods, minimizing dwell times and maximizing throughput. Furthermore, modern cross docking facilities often incorporate automation technologies like automated storage and retrieval systems (AS/RS) and robotic picking systems to enhance speed and accuracy. These technologies not only streamline operations but also reduce labor costs and minimize the risk of human error. Moreover, the integration of IoT devices and sensors helps in monitoring environmental conditions such as temperature and humidity, which is particularly important for handling perishable goods. In terms of communication infrastructure, reliable and high-speed networks are vital for real-time data exchange between different stakeholders including suppliers, carriers, and customers. This ensures that all parties are informed about the status of shipments at every stage of the cross docking process. Finally, cybersecurity measures must be robust to protect sensitive data from potential breaches, given the critical nature of logistics operations. In summary, the successful implementation of cross docking hinges on a combination of cutting-edge technology and well-designed infrastructure. By leveraging these tools and systems, businesses can achieve significant reductions in costs, improvements in efficiency, and enhanced customer satisfaction through faster delivery times. As logistics continue to evolve with technological advancements, the role of these elements will only become more pivotal in driving the effectiveness of cross docking operations.
Applications and Best Practices in Cross Docking
Cross docking is a logistics strategy that has revolutionized the way goods are handled and distributed, offering significant benefits in terms of efficiency, cost reduction, and enhanced customer satisfaction. This article delves into the applications and best practices of cross docking, providing a comprehensive overview that is both informative and engaging. We will explore industry-specific use cases, highlighting how different sectors such as retail, manufacturing, and pharmaceuticals leverage cross docking to streamline their supply chains. Additionally, we will discuss optimization strategies for efficiency, including the use of advanced technology and data analytics to maximize throughput and minimize errors. Finally, we will address common challenges and solutions, offering practical advice on how to overcome obstacles that may arise during the implementation of cross docking operations. By understanding these key aspects, businesses can better position themselves to reap the full benefits of cross docking. Let's begin by examining industry-specific use cases, where we will see firsthand how various industries are successfully integrating cross docking into their operations.
Industry-Specific Use Cases
Cross docking, a logistics strategy that involves the direct transfer of goods from one vehicle to another without intermediate storage, has diverse and impactful applications across various industries. In the **retail sector**, cross docking is crucial for maintaining inventory levels and ensuring timely product availability. Retailers can consolidate shipments from multiple suppliers into a single truck, reducing transportation costs and enhancing supply chain efficiency. For instance, big-box retailers like Walmart and Target use cross docking to manage high volumes of inventory, ensuring that products reach stores quickly and efficiently. In the **pharmaceutical industry**, cross docking plays a vital role in maintaining the integrity and safety of products. Given the stringent regulations and temperature control requirements for pharmaceuticals, cross docking facilities are designed to handle these sensitive items swiftly and securely. This approach minimizes the risk of product degradation and ensures compliance with regulatory standards. The **food and beverage industry** also benefits significantly from cross docking. Perishable goods such as meat, dairy products, and fresh produce require rapid handling to preserve their quality. Cross docking allows these items to be transferred directly from suppliers to distribution centers or retail outlets, reducing transit times and maintaining product freshness. In **e-commerce**, cross docking is essential for meeting the high demand for fast and reliable shipping. Online retailers can use cross docking to consolidate orders from various suppliers, streamline packaging processes, and expedite delivery times. This strategy helps in managing the complexities of last-mile delivery, ensuring customer satisfaction through timely and accurate order fulfillment. The **automotive industry** leverages cross docking for just-in-time (JIT) manufacturing. Automotive parts and components are transferred directly from suppliers to manufacturing facilities, enabling car manufacturers to maintain production schedules without holding large inventories. This approach enhances operational efficiency and reduces costs associated with inventory storage. In **healthcare**, cross docking is used to manage medical supplies and equipment efficiently. Hospitals and healthcare providers rely on timely deliveries of critical supplies, such as surgical instruments, medications, and personal protective equipment (PPE). Cross docking ensures that these essential items are delivered promptly, supporting continuous patient care without disruptions. For **construction projects**, cross docking facilitates the coordination of materials and equipment. Building materials such as lumber, steel, and concrete can be transferred directly from suppliers to construction sites, ensuring that projects stay on schedule. This method helps in managing the logistics of large-scale construction projects efficiently. In summary, industry-specific use cases for cross docking highlight its versatility and value across diverse sectors. By streamlining logistics operations, reducing costs, and enhancing supply chain efficiency, cross docking remains a critical strategy for businesses seeking to optimize their operations and improve customer satisfaction. Whether it's retail, pharmaceuticals, food and beverage, e-commerce, automotive, healthcare, or construction, the benefits of cross docking are clear: faster delivery times, lower costs, and improved operational efficiency.
Optimization Strategies for Efficiency
Optimization strategies for efficiency are crucial in the context of cross docking, a logistics technique that streamlines the movement of goods from incoming to outgoing transportation without intermediate storage. To maximize efficiency, several key strategies can be employed. First, **advanced planning and scheduling** play a pivotal role. Utilizing sophisticated software and data analytics, companies can predict demand, optimize shipment routes, and schedule dock operations to minimize congestion and delays. This proactive approach ensures that all stakeholders are aligned and prepared, reducing the likelihood of bottlenecks. **Process standardization** is another critical aspect. By establishing clear, consistent procedures for receiving, sorting, and shipping goods, cross docking facilities can maintain high levels of productivity. Standardized processes also facilitate training and onboarding new staff, ensuring that everyone understands their roles and responsibilities. Additionally, **technology integration** is essential for optimizing cross docking operations. Implementing automated systems such as barcode scanning, RFID tracking, and conveyor belts can significantly enhance the speed and accuracy of goods handling. **Inventory management** is also vital for efficient cross docking. Real-time inventory tracking allows for better decision-making regarding stock allocation and shipment prioritization. This ensures that high-priority items are moved quickly through the system while minimizing the risk of stockouts or overstocking. Furthermore, **collaboration with suppliers** can lead to substantial improvements in efficiency. Working closely with suppliers to synchronize delivery schedules and ensure compliance with labeling and packaging standards can reduce errors and streamline the entire process. **Continuous improvement** through regular audits and performance metrics is another key strategy. Regularly assessing operational efficiency and identifying areas for improvement helps in implementing corrective measures promptly. This could involve reconfiguring dock layouts, adjusting staffing levels during peak periods, or implementing new technologies to address specific challenges. Lastly, **employee training and engagement** are often overlooked but are crucial components of an optimized cross docking operation. Well-trained employees who understand the importance of their roles in maintaining efficiency can significantly impact overall performance. Engaged employees are more likely to identify inefficiencies and suggest improvements, fostering a culture of continuous improvement within the organization. By combining these optimization strategies—advanced planning, process standardization, technology integration, effective inventory management, supplier collaboration, continuous improvement, and employee training—companies can achieve significant gains in efficiency within their cross docking operations. These best practices not only reduce costs and enhance productivity but also improve customer satisfaction by ensuring timely and accurate delivery of goods.
Common Challenges and Solutions
Cross docking, a logistics strategy that involves the direct transfer of goods from inbound to outbound vehicles without intermediate storage, is not without its challenges. One common issue is the need for precise timing and coordination to ensure that shipments arrive and depart in a synchronized manner. This requires robust communication systems and real-time tracking to manage the flow of goods efficiently. Another challenge is maintaining inventory accuracy, as the rapid movement of goods can lead to discrepancies if not properly monitored. Implementing advanced inventory management software can help mitigate this by providing real-time updates and alerts. Space constraints are also a significant challenge in cross docking facilities. Efficient use of space is crucial to handle high volumes of goods quickly. Solutions include optimizing warehouse layout, using vertical storage solutions, and implementing a first-in-first-out (FIFO) inventory system to ensure that older stock is moved out promptly. Additionally, cross docking operations often face issues related to labor management, particularly during peak periods when demand surges. To address this, companies can invest in training programs for their workforce and consider flexible staffing arrangements such as temporary or seasonal workers. Quality control is another critical aspect that can be challenging in cross docking environments due to the fast-paced nature of operations. Ensuring that products are inspected thoroughly before being shipped out requires streamlined quality control processes. This can be achieved through automated inspection systems and clear quality control protocols that are strictly adhered to by all staff members. Furthermore, cross docking operations are vulnerable to disruptions such as weather conditions, traffic congestion, or supplier delays. Developing contingency plans and having backup suppliers or alternative routes can help mitigate these risks. Leveraging data analytics and predictive modeling can also provide insights into potential disruptions, allowing for proactive measures to be taken. In terms of solutions, technology plays a pivotal role in overcoming these challenges. For instance, using RFID tags or barcode scanning can enhance inventory tracking and reduce errors. Automated sorting systems can streamline the process of directing goods to their correct outbound vehicles quickly and accurately. Moreover, integrating cross docking operations with broader supply chain management systems ensures seamless communication between different stakeholders involved in the logistics process. Best practices in cross docking include adopting a lean approach to minimize waste and maximize efficiency. This involves eliminating unnecessary steps in the process and continuously evaluating operations for areas of improvement. Regular audits and performance metrics help in identifying bottlenecks and implementing corrective actions promptly. In conclusion, while cross docking presents several challenges due to its fast-paced and complex nature, these can be effectively managed through a combination of technological solutions, efficient processes, and well-trained personnel. By focusing on precise timing, inventory accuracy, space optimization, labor management, quality control, and contingency planning, businesses can leverage cross docking to enhance their supply chain efficiency and customer satisfaction significantly.