What Is A Cricket Ball Made Of

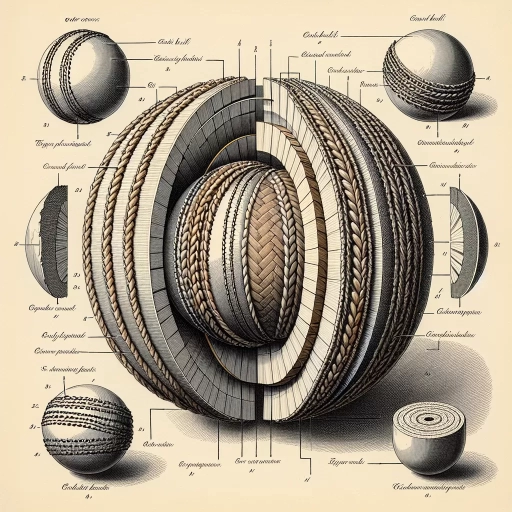
Materials Used in Cricket Ball Construction
The construction of a cricket ball is a meticulous process that involves several key materials, each contributing to its performance, durability, and overall quality. At the heart of this process are three primary components: the leather or synthetic cover, the cork core, and the yarn and thread wrapping. The choice between a leather or synthetic cover significantly impacts the ball's behavior on the field, with leather balls offering a more traditional feel and performance. The cork core provides the necessary hardness and resilience, ensuring consistent bounce and longevity. Meanwhile, the yarn and thread wrapping around the core adds additional strength and helps maintain the ball's shape. Understanding these components is crucial for appreciating the craftsmanship and science behind cricket ball construction. Let's delve into the first of these critical elements: the leather or synthetic cover, which sets the stage for the ball's overall characteristics and performance.
Leather or Synthetic Cover
When it comes to the construction of a cricket ball, one of the most critical components is the cover, which can be made from either leather or synthetic materials. The choice between these two materials significantly impacts the ball's performance, durability, and overall playability. Leather covers, traditionally used in high-quality cricket balls, are renowned for their superior grip and feel. High-grade leather, often sourced from cows or buffaloes, is meticulously selected and processed to ensure it meets the stringent standards set by governing bodies such as the International Cricket Council (ICC). The natural texture of leather allows for better seam movement and swing, making it a favorite among professional cricketers. However, leather covers are more expensive and require regular maintenance to maintain their integrity. On the other hand, synthetic covers offer a more affordable and durable alternative. These covers are typically made from polyurethane or polyvinyl chloride (PVC) and are designed to mimic the look and feel of leather while offering enhanced resistance to wear and tear. Synthetic covers are ideal for lower-level cricket matches, training sessions, and younger players due to their cost-effectiveness and longevity. They also perform well in various weather conditions, making them a practical choice for outdoor games. Despite these advantages, synthetic covers often lack the precise seam movement and swing characteristics that leather covers provide, which can affect the ball's aerodynamics and overall performance. In recent years, advancements in technology have led to the development of high-quality synthetic covers that closely replicate the performance of leather. These advanced synthetic materials are engineered to provide a similar grip and seam movement, making them a viable option for competitive matches. However, the ICC and other governing bodies still prefer leather covers for international and first-class cricket due to their proven performance and historical significance. In summary, the choice between leather and synthetic covers in cricket ball construction is influenced by factors such as budget, level of play, and desired performance characteristics. While leather covers remain the gold standard for professional cricket due to their exceptional grip and aerodynamic properties, synthetic covers offer a reliable, cost-effective alternative that is gaining popularity across various levels of the sport. As technology continues to evolve, it is likely that synthetic covers will become even more competitive with their leather counterparts, providing cricketers with a wider range of options tailored to their specific needs.
Cork Core
In the intricate construction of a cricket ball, one of the most critical components is the cork core. This central element provides the foundational structure and resilience that are essential for the ball's performance and durability. The cork core is typically made from high-quality, dense cork material that is carefully selected for its ability to absorb impact without deforming excessively. This property is crucial because it allows the ball to maintain its shape and bounce consistently, even after being hit by a bat or bouncing on the ground. The process of creating the cork core involves several precise steps. First, raw cork is harvested from the bark of cork oak trees, primarily in regions like Portugal and Spain. This natural material is then cleaned, sorted, and processed to ensure uniformity and quality. The selected cork pieces are then compressed and shaped into spherical forms using specialized machinery. This compression enhances the cork's density, making it more robust and better suited for withstanding the high-impact forces involved in cricket. Once the cork core is formed, it is encased in layers of rubber and then wrapped with yarn or thread to provide additional strength and stability. This layering process helps distribute the force of impact evenly across the ball, ensuring that it behaves predictably during play. The combination of the cork core with these outer layers also contributes to the ball's weight and balance, which are critical factors in determining its aerodynamics and overall performance. The choice of cork for the core is not arbitrary; it offers several advantages that make it ideal for this application. Cork is lightweight yet resilient, allowing the ball to maintain its speed and trajectory without becoming too heavy or unwieldy. Additionally, cork has natural shock-absorbing properties that help reduce the risk of injury to players, particularly bowlers and batsmen who are frequently exposed to high-speed impacts. Moreover, the use of cork in cricket balls has a long history and tradition. The material has been favored for centuries due to its unique combination of strength, elasticity, and lightness. Modern manufacturing techniques have refined this process, but the fundamental principle remains the same: to create a core that is both durable and responsive. In summary, the cork core is a vital component in the construction of a cricket ball, providing the necessary structure and resilience for optimal performance. Its unique properties, combined with precise manufacturing processes, ensure that the ball behaves consistently and predictably under various conditions, making it an indispensable part of the game. As cricket continues to evolve, the role of the cork core remains steadfast, a testament to its enduring importance in this beloved sport.
Yarn and Thread Wrapping
In the intricate process of constructing a cricket ball, one of the most critical components is the yarn and thread wrapping that encases the core. This layer is pivotal in providing the ball with its necessary durability, texture, and aerodynamic properties. The yarn used for wrapping is typically made from high-quality wool or synthetic fibers, chosen for their strength and elasticity. The choice between wool and synthetic fibers depends on the desired performance characteristics of the ball; wool is often preferred for its natural grip and feel, while synthetic fibers offer greater consistency and resistance to wear. The wrapping process involves meticulously layering the yarn around the cork core, which is initially covered with a thin layer of rubber. This core provides the foundation for the ball's bounce and hardness. The yarn is wound tightly and evenly to ensure uniformity in weight distribution and surface texture. Each layer of yarn is carefully aligned to prevent any irregularities that could affect the ball's aerodynamics or balance. The thread wrapping stage follows the yarn layering, where a finer thread is used to bind the yarn in place securely. This thread is usually made from cotton or a blend of natural and synthetic fibers, selected for their tensile strength and flexibility. The thread is wrapped in a specific pattern to enhance the ball's seam, which plays a crucial role in its movement through the air. The seam's height and texture are critical factors that influence how the ball swings or spins when bowled. The combination of yarn and thread wrapping not only adds to the ball's overall weight but also contributes significantly to its performance characteristics. For instance, the tightness and pattern of the thread can affect how much the ball swings when bowled at high speeds. Similarly, the type of yarn used can influence how well the ball grips the surface when bowled on different types of pitches. In professional cricket, adherence to strict manufacturing standards ensures that each ball meets precise specifications regarding size, weight, and surface texture. The International Cricket Council (ICC) sets these standards to maintain fairness and consistency across all levels of play. Manufacturers must carefully control every aspect of the yarn and thread wrapping process to ensure compliance with these regulations. In summary, the yarn and thread wrapping in cricket ball construction are essential elements that contribute to the ball's performance, durability, and overall quality. These materials must be selected and applied with great care to meet the stringent requirements set by governing bodies like the ICC. The meticulous attention to detail in this process underscores the complexity and craftsmanship involved in creating a cricket ball that meets the demands of this highly competitive sport.
Manufacturing Process of Cricket Balls
The manufacturing process of cricket balls is a meticulous and multi-step procedure that requires precision, quality materials, and stringent quality control. This intricate process can be broken down into three key stages: the selection and preparation of raw materials, the assembly and shaping of the ball, and the finishing touches with quality control. Each stage is crucial in ensuring that the final product meets the high standards required for professional cricket. The journey begins with the careful selection and preparation of raw materials, where the quality of leather, cork, and rubber directly impacts the ball's performance. This initial step sets the foundation for the entire manufacturing process. Next, the assembly and shaping stage involves combining these materials into a cohesive unit, requiring skilled craftsmanship to achieve the perfect spherical shape and weight distribution. Finally, the finishing touches and quality control ensure that every ball adheres to strict specifications, guaranteeing consistency and reliability on the field. By understanding these stages, one can appreciate the craftsmanship and attention to detail that goes into creating a high-quality cricket ball. Let's delve deeper into the first critical stage: the selection and preparation of raw materials.
Selection and Preparation of Raw Materials
The selection and preparation of raw materials are crucial steps in the manufacturing process of cricket balls, as they directly influence the final product's quality, performance, and durability. The primary components of a cricket ball include high-quality leather, cork, rubber, and thread. **Leather Selection:** The outer cover of a cricket ball is made from premium leather, typically sourced from cows or buffaloes. The leather must be strong, yet supple, to withstand the rigors of the game. Manufacturers often choose full-grain leather for its superior strength and resistance to wear. The leather is carefully inspected for any imperfections or blemishes that could affect the ball's aerodynamics or overall performance. **Cork and Rubber:** At the heart of every cricket ball lies a core composed of cork and rubber. Cork provides the necessary resilience and elasticity, while rubber adds additional bounce and hardness. The cork is usually harvested from the bark of cork oak trees, known for its light weight and compressibility. The rubber used is of high quality to ensure consistent rebound properties. **Thread and Stitching:** The thread used for stitching the leather cover together is also a critical component. Traditionally, cotton or nylon threads are employed due to their strength and durability. The stitching pattern, typically 80-90 stitches per ball, is meticulously designed to ensure even distribution of pressure and maintain the ball's shape under various conditions. **Preparation Process:** Once the raw materials are selected, they undergo a rigorous preparation process. The leather is cut into precise shapes using specialized machinery to ensure uniformity. The cork core is shaped and compressed to achieve the desired hardness and size. Rubber layers are then applied around the cork core to enhance its properties. **Assembly and Quality Control:** The leather pieces are then hand-stitched over the core using the carefully chosen thread. Each ball is inspected multiple times during this process to ensure that it meets the stringent standards set by governing bodies such as the International Cricket Council (ICC). The finished balls are tested for weight, size, seam height, and rebound resilience before being certified for use in professional matches. In summary, the meticulous selection and preparation of raw materials such as high-quality leather, cork, rubber, and thread are essential for producing cricket balls that meet the demanding requirements of the sport. Each component plays a vital role in ensuring that the ball performs consistently and safely, making these steps integral to the overall manufacturing process.
Assembly and Shaping the Ball
In the intricate process of manufacturing cricket balls, the assembly and shaping phase is a critical step that transforms raw materials into a precise, high-performance product. This stage follows the initial selection and preparation of leather, cork, and rubber components. The core of the ball, typically made from a dense cork and rubber composite, is carefully crafted to ensure uniform density and resilience. This core is then wrapped in layers of tightly wound yarn to achieve the desired weight and hardness. Next, the leather cover is meticulously cut into two identical halves, known as the "quarters," which are then stitched together using a strong thread. The stitching pattern, often 65-70 hand-stitches, is crucial for maintaining the ball's aerodynamics and performance. The quarters are positioned in such a way that the seam runs along the middle of the ball, creating an even surface. The assembly process involves placing the cork-rubber core within the leather cover, ensuring it is centered and evenly distributed. The leather is then tightly wrapped around the core, and the seam is hand-stitched with precision. Each stitch must be perfectly aligned to avoid any irregularities that could affect the ball's flight. Shaping the ball to its precise spherical form is an art that requires great skill. Manufacturers use specialized tools to ensure that the ball meets the International Cricket Council (ICC) standards, which dictate that a cricket ball must weigh between 155.9 and 163 grams and have a circumference of 22.4 cm for men's cricket and 21.1 cm for women's cricket. Throughout this process, quality control is paramount. Each ball is inspected for any imperfections in the leather, stitching, or core. The ball must also pass rigorous tests for weight, size, and bounce to ensure it meets the stringent standards required for professional play. The final touches involve applying a layer of polish to enhance the ball's appearance and performance. This polish helps in maintaining the ball's condition during play and ensures that it retains its shine and grip. In summary, the assembly and shaping of a cricket ball is a meticulous process that demands precision, skill, and attention to detail. From the careful selection of materials to the final polishing stage, each step is crucial in creating a ball that not only meets but exceeds the expectations of cricketers around the world. This phase underscores the craftsmanship and dedication involved in transforming raw materials into a high-quality cricket ball that can withstand the rigors of the game while delivering consistent performance.
Finishing Touches and Quality Control
In the meticulous world of cricket ball manufacturing, the finishing touches and quality control processes are as crucial as the initial stages of production. After the core, cork, and rubber layers have been carefully assembled and the leather cover has been stitched on, the ball undergoes a series of rigorous checks to ensure it meets the stringent standards set by governing bodies such as the International Cricket Council (ICC). First, each ball is inspected for any visible defects or irregularities in the stitching, cover, and overall shape. Skilled craftsmen meticulously examine every seam, ensuring that it is perfectly aligned and securely stitched to prevent any weaknesses that could affect performance during play. The weight and size of the ball are also verified to ensure compliance with ICC regulations, which specify that a cricket ball must weigh between 155.9 and 163 grams and have a circumference of between 22.4 and 22.9 centimeters. Next, the ball's surface is treated with a combination of natural and synthetic waxes to enhance its durability and performance. This process involves applying a layer of linseed oil or similar substances to condition the leather, making it more resistant to wear and tear while maintaining its grip on the bowler's fingers. The ball is then polished to a high sheen, which not only improves its appearance but also helps in achieving consistent aerodynamics during flight. Quality control extends beyond physical inspection; performance tests are conducted to gauge the ball's aerodynamic properties, bounce, and swing characteristics. These tests simulate real-game conditions, ensuring that the ball behaves predictably and consistently across different environmental conditions. For instance, the ball's ability to swing in the air—a critical aspect of cricket—is evaluated by observing how it moves when bowled at various speeds and angles. Finally, every batch of cricket balls undergoes random sampling for further detailed analysis. This includes checking for uniformity in weight distribution, rebound resilience when dropped from a standard height, and resistance to water absorption—a factor that could alter its weight and performance over time. Only after passing these rigorous tests can a cricket ball be certified as ready for use in professional matches. The attention to detail in these finishing touches and quality control measures underscores the importance of precision in cricket ball manufacturing. It is this unwavering commitment to excellence that ensures players can rely on consistent performance from their equipment, thereby enhancing the integrity and enjoyment of the game. By combining traditional craftsmanship with modern testing techniques, manufacturers can produce high-quality cricket balls that meet the exacting standards required at all levels of play.
Standards and Regulations for Cricket Balls
Standards and regulations for cricket balls are crucial to ensure fairness, safety, and consistency in the game. These guidelines are meticulously crafted to cover various aspects of the ball's construction and performance. The first key area is **Size and Weight Specifications**, which dictates the precise dimensions and mass of the ball to maintain uniformity across different manufacturers. This ensures that players can rely on consistent behavior from the ball, regardless of its origin. Another critical aspect is **Material Compliance and Testing**, where the materials used in the ball's core, cover, and stitching are scrutinized to meet specific standards. This involves rigorous testing to guarantee that the ball performs as expected under different conditions. Finally, **Certification and Approval Processes** play a vital role in verifying that each ball meets all the required standards before it is deemed fit for play. By adhering to these regulations, cricket balls can be trusted to deliver a high-quality gaming experience. Understanding these standards begins with a closer look at the **Size and Weight Specifications**, which form the foundation of a ball's integrity.
Size and Weight Specifications
When it comes to the standards and regulations governing cricket balls, size and weight specifications are paramount to ensure fair play and consistency across all levels of the game. According to the International Cricket Council (ICC), the governing body responsible for setting these standards, a cricket ball must adhere to very specific dimensions and weights. For men's cricket, the ball must weigh between 155.9 grams and 163 grams, while its circumference should be between 22.4 centimeters and 22.9 centimeters. The diameter of the ball should fall within the range of 7.1 centimeters to 7.3 centimeters. These precise measurements are crucial as they affect the ball's aerodynamics, bounce, and overall performance during a match. For women's cricket, the specifications are slightly different but equally stringent. Women's cricket balls must weigh between 140 grams and 150 grams, with a circumference ranging from 21.1 centimeters to 21.5 centimeters. The diameter for women's balls should be between 6.9 centimeters and 7.1 centimeters. These variations are designed to accommodate the physical differences between male and female players while maintaining the integrity of the game. The importance of adhering to these size and weight specifications cannot be overstated. Deviations from these standards could significantly impact the game's dynamics, potentially leading to unfair advantages or disadvantages for teams. For instance, a ball that is too heavy or too light could alter its trajectory and speed unpredictably, affecting bowlers' accuracy and batsmen's ability to score runs. Similarly, variations in circumference and diameter can influence how the ball grips the surface, which is critical for spin bowling techniques. Manufacturers of cricket balls must undergo rigorous testing to ensure their products meet these exacting standards. The ICC has established a series of tests that include weight checks, circumference measurements, and rebound tests to verify that each ball performs consistently within the specified parameters. Additionally, balls are inspected for their seam height and texture to ensure uniformity. In practice, these specifications translate into a more predictable and enjoyable game for players and spectators alike. They help maintain the balance between batting and bowling, ensuring that no team has an undue advantage due to irregularities in the ball. This consistency also allows players to develop their skills based on known variables, enhancing their performance over time. In conclusion, the size and weight specifications for cricket balls are fundamental components of the game's regulations. These precise measurements ensure fairness, consistency, and predictability in every match, whether at the amateur or professional level. By adhering strictly to these standards, cricket maintains its integrity as a sport that values skill, strategy, and fair play above all else.
Material Compliance and Testing
Material compliance and testing are crucial components in the manufacturing of cricket balls, ensuring that these critical pieces of equipment adhere to stringent standards and regulations. The International Cricket Council (ICC) and various national governing bodies have established rigorous guidelines to guarantee that cricket balls meet specific criteria for performance, safety, and fairness. These standards dictate the materials used, such as high-quality leather for the cover and cork or synthetic cores, which must be tested for durability, weight, size, and rebound resilience. The testing process involves several stages. Initially, the raw materials are inspected to ensure they meet the required specifications. For instance, the leather used must be of a certain thickness and have specific tensile strength properties to withstand the impacts during a game. The cork core, which provides the ball's bounce and hardness, is also subject to precise measurements and tests to ensure it complies with weight and size regulations. Once the raw materials pass these initial checks, the assembled ball undergoes a series of physical tests. These include drop tests to assess the ball's rebound height and consistency, compression tests to evaluate its hardness, and seam tests to ensure the stitching is even and secure. Additionally, the ball's circumference and weight are meticulously measured to ensure they fall within the prescribed limits. Moreover, cricket balls are subjected to environmental testing to simulate various playing conditions. This includes exposing the balls to different temperatures and humidity levels to check for any adverse effects on their performance. Such comprehensive testing ensures that the balls behave consistently across different climates and conditions, maintaining the integrity of the game. Compliance with these standards is not just about ensuring fair play but also about player safety. A ball that does not meet these criteria could potentially cause injuries due to irregular behavior or excessive hardness. Therefore, manufacturers must adhere strictly to these regulations, and any non-compliance can result in the ball being deemed unfit for play. In summary, material compliance and testing are essential for producing cricket balls that meet the high standards set by governing bodies. Through rigorous inspection and testing of raw materials and finished products, manufacturers can ensure that every ball delivered to the field is safe, consistent, and fair for all players involved. This meticulous process underscores the importance of quality control in maintaining the integrity and enjoyment of the game of cricket.
Certification and Approval Processes
Certification and approval processes are crucial components in ensuring that cricket balls meet the stringent standards and regulations set by governing bodies such as the International Cricket Council (ICC). These processes involve a series of rigorous tests and evaluations to guarantee that the balls adhere to specific criteria regarding size, weight, shape, and performance. The ICC, in collaboration with national cricket boards and manufacturers, establishes these standards to maintain consistency and fairness across all levels of the game. The certification process typically begins with the selection of raw materials, where manufacturers must source high-quality leather or synthetic materials that comply with ICC specifications. Once the raw materials are approved, the balls undergo various stages of production, including cutting, stitching, and shaping. Each stage is meticulously monitored to ensure that the final product meets the required dimensions and weight limits. After production, the balls are subjected to a battery of tests designed to evaluate their performance characteristics. These tests include assessments of rebound resilience, seam height, and surface texture. For instance, the ICC mandates that a cricket ball must rebound between 0.525 and 0.575 meters when dropped from a height of 2 meters onto a hard surface. Similarly, the seam height must be within specified limits to ensure consistent aerodynamic behavior. Manufacturers also conduct internal quality control checks to verify that their products conform to these standards. This may involve using advanced technology such as 3D scanning and computer-aided design (CAD) software to measure precise dimensions and simulate performance under different conditions. Once a batch of cricket balls passes these internal checks, they are submitted to independent testing laboratories accredited by the ICC for final certification. These laboratories conduct comprehensive tests that replicate real-game scenarios, including impact resistance and durability assessments. Only after successfully passing these external evaluations are the cricket balls awarded certification and approved for use in official matches. The approval process extends beyond the physical attributes of the ball; it also encompasses ethical considerations such as fair labor practices and environmental sustainability. Manufacturers must provide documentation showing compliance with international labor standards and environmental regulations, ensuring that the production process does not harm workers or the environment. In summary, the certification and approval processes for cricket balls are multifaceted and rigorous, involving meticulous material selection, precise manufacturing, thorough testing, and ethical compliance. These processes are essential in maintaining the integrity of the game by ensuring that all cricket balls used in official matches meet uniform standards of quality and performance. This consistency is vital for fair play and player safety, making these processes an integral part of the broader framework of standards and regulations governing cricket equipment.