What Is Particle Board

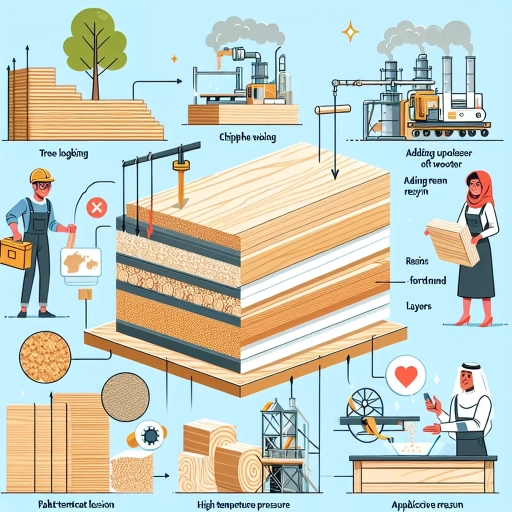
What is Particle Board?
Particle board, a versatile and widely used engineered wood product, has become a staple in modern construction and furniture making. To fully understand its significance, it is essential to delve into its definition and composition, manufacturing process, and historical background. **Definition and Composition** provide the foundational knowledge of what particle board is made of and how its unique properties are achieved. This section will explore the mixture of wood particles, adhesives, and other additives that form this material, highlighting its durability and cost-effectiveness. The **Manufacturing Process** reveals the intricate steps involved in transforming raw materials into a finished product. From the collection of wood waste to the final pressing and shaping, this process showcases the technological advancements that have made particle board a reliable choice for various applications. Lastly, the **Historical Background** offers a glimpse into the origins of particle board, tracing its development from post-war Europe to its global use today. This historical context underscores the material's evolution and its adaptation to changing environmental and economic conditions. By examining these three aspects, readers will gain a comprehensive understanding of particle board's role in contemporary building practices and its enduring relevance in the industry. Let us begin by exploring the **Definition and Composition** of this versatile material.
Definition and Composition
Particle board, a versatile and widely used engineered wood product, is defined by its unique composition and manufacturing process. At its core, particle board is made from small wood particles, such as wood chips, shavings, and sawdust, which are bonded together using a synthetic resin or adhesive. This composition distinguishes it from other types of engineered wood like plywood or medium-density fiberboard (MDF). The process of creating particle board begins with the collection and processing of wood particles. These particles are typically derived from wood waste materials that would otherwise be discarded. The wood particles are then dried to a specific moisture content to ensure optimal bonding. Next, they are mixed with a synthetic resin, usually a type of formaldehyde-based adhesive, which acts as the binding agent. Other additives such as wax and preservatives may also be included to enhance the board's durability and resistance to moisture. Once the mixture is prepared, it is formed into a mat using heat and pressure. The mat is then pressed under high pressure in a hydraulic press to compact the particles and cure the adhesive. This pressing process can vary in duration and pressure depending on the desired density and quality of the final product. The resulting board is dense, flat, and uniform in thickness, making it ideal for a variety of applications including furniture manufacturing, construction, and interior design. The composition of particle board also includes various grades based on density and intended use. For instance, low-density particle board is often used for non-load bearing applications such as wall linings or ceiling tiles, while high-density particle board is more suitable for load-bearing applications like shelving and flooring. Additionally, some particle boards are treated with fire retardants or moisture-resistant coatings to meet specific performance requirements. In terms of environmental impact, particle board offers several advantages. It utilizes wood waste that would otherwise contribute to landfill waste or be burned, thereby reducing the demand on virgin timber resources. However, it is important to note that some particle boards contain formaldehyde-based adhesives which can emit volatile organic compounds (VOCs), posing potential health risks. In response to these concerns, many manufacturers are now producing formaldehyde-free particle boards using alternative adhesives. Overall, the definition and composition of particle board highlight its innovative use of wood waste materials and its versatility in various industrial and domestic applications. Its ability to be engineered to meet specific performance criteria makes it a valuable resource in modern construction and manufacturing practices. As technology continues to evolve, particle board remains a significant component in sustainable building solutions while addressing environmental and health considerations.
Manufacturing Process
The manufacturing process of particle board is a complex yet highly efficient operation that transforms raw materials into a versatile and widely used engineered wood product. It begins with the collection and processing of wood particles, typically from sawdust, wood shavings, and other wood residues. These particles are first dried to a moisture content of around 5-10% to ensure optimal bonding during the manufacturing process. The dried particles are then mixed with a resin, usually a urea-formaldehyde or melamine-formaldehyde adhesive, along with other additives such as wax and preservatives to enhance the board's durability and resistance to moisture. Next, the particle-resin mixture is spread evenly onto a conveyor belt or forming table, where it is distributed in a uniform layer. The thickness of this layer determines the final thickness of the particle board. Once the mixture is evenly spread, it is pressed using a hydraulic press or a continuous press. The pressing process involves applying high pressure and heat to consolidate the particles and activate the resin, binding them together into a solid panel. After pressing, the panels are removed from the press and allowed to cool. They are then cut to the desired size using saws or cutting machines. The edges may be trimmed to ensure smoothness and uniformity. Some particle boards undergo additional processing steps such as sanding to improve surface quality or applying a decorative veneer for aesthetic purposes. Quality control measures are integral throughout the manufacturing process. Samples are regularly tested for density, moisture content, and mechanical properties to ensure that the final product meets industry standards. This rigorous quality control ensures that particle board is consistent in its performance and suitable for various applications, ranging from furniture making to construction. In summary, the manufacturing process of particle board involves careful preparation of raw materials, precise mixing with adhesives and additives, controlled pressing under heat and pressure, and meticulous quality control. This process transforms waste wood particles into a valuable resource that is both cost-effective and environmentally friendly, making particle board an essential material in modern construction and furniture industries.
Historical Background
The historical background of particle board is deeply intertwined with the evolution of engineered wood products, reflecting a broader narrative of innovation and resource optimization in the construction industry. The concept of particle board emerged in the early 20th century, driven by the need for cost-effective and efficient use of wood resources. In the 1920s, German engineer Max Himmelheber is credited with developing the first particle board, which he called "Düspohlplatte." This pioneering work involved pressing wood chips and shavings together with a binding agent, typically a synthetic resin, to form a solid panel. The post-World War II era saw significant advancements in particle board technology. As traditional lumber became scarce and expensive, manufacturers turned to alternative materials. The introduction of new adhesives and manufacturing processes improved the strength, durability, and affordability of particle board. By the 1950s and 1960s, particle board had become a staple in furniture manufacturing and construction, particularly in Europe and North America. Its versatility allowed it to be used in a wide range of applications, from cabinetry and shelving to flooring and wall panels. The environmental concerns of the 1970s further propelled the development of particle board as a sustainable alternative to solid wood. Manufacturers began to incorporate recycled wood fibers into their products, reducing waste and conserving natural resources. This shift aligned with broader societal trends towards environmental stewardship and sustainable practices. Today, particle board continues to evolve with advancements in technology, including improved adhesives that reduce formaldehyde emissions and enhance product safety. Throughout its history, particle board has been shaped by economic, environmental, and technological factors. It represents a successful example of how innovation can transform waste materials into valuable products, contributing to more efficient use of resources and reducing the environmental footprint of the construction industry. As demand for sustainable building materials continues to grow, the legacy of particle board serves as a testament to human ingenuity in finding practical solutions to complex challenges. This historical context underscores the significance of particle board not just as a product but as part of a larger narrative of innovation and sustainability in the built environment.
Properties and Characteristics of Particle Board
Particle board, a widely used engineered wood product, is characterized by its unique properties and characteristics that make it a versatile material in various applications. This article delves into the multifaceted nature of particle board, exploring its physical properties, chemical properties, and environmental impact. Understanding these aspects is crucial for evaluating the suitability of particle board for different uses. Firstly, the physical properties of particle board, such as density, strength, and moisture resistance, are pivotal in determining its performance in construction and furniture manufacturing. These properties influence how well the material can withstand mechanical stress and environmental conditions. Secondly, the chemical properties of particle board, including its composition and bonding agents, play a significant role in its durability and stability. The type of adhesives used can affect the board's resistance to chemicals and its overall lifespan. Lastly, the environmental impact of particle board is an increasingly important consideration. Factors such as the source of raw materials, production processes, and end-of-life disposal contribute to its ecological footprint. By examining these three critical areas—physical properties, chemical properties, and environmental impact—we can gain a comprehensive understanding of particle board's capabilities and limitations. Let us begin by exploring the physical properties that underpin its structural integrity and functional versatility.
Physical Properties
Physical properties of particle board are crucial in determining its suitability for various applications, particularly in construction and furniture manufacturing. **Density** is one of the key physical properties, which can vary significantly depending on the manufacturing process and raw materials used. Generally, particle board densities range from 600 to 800 kg/m³, with higher densities indicating greater strength and durability. **Moisture resistance** is another critical property, as particle board is often prone to swelling and disintegration when exposed to moisture. Manufacturers may treat the board with moisture-resistant adhesives or coatings to enhance its performance in humid environments. **Thermal conductivity** is also an important consideration, especially in building insulation applications. Particle board has a relatively low thermal conductivity compared to solid wood, making it a decent insulator. However, its thermal performance can be improved by incorporating insulating materials during the manufacturing process. **Mechanical properties**, such as tensile strength, compressive strength, and bending strength, are vital for structural integrity. These properties are influenced by factors like particle size distribution, adhesive type, and pressing conditions. High-quality particle boards exhibit better mechanical properties, making them suitable for load-bearing applications. **Dimensional stability** refers to the board's ability to maintain its shape and size under varying environmental conditions. Particle board generally has good dimensional stability due to its uniform composition and manufacturing process. However, it may still undergo some degree of shrinkage or expansion with changes in humidity and temperature. **Surface quality** is another significant physical property, affecting the board's appearance and usability. A smooth surface finish is essential for painting or laminating, while a textured surface may be preferred for certain decorative purposes. In addition to these properties, **fire resistance** has become a critical factor in recent years due to safety regulations. Particle boards can be treated with fire retardants to improve their performance in case of a fire. This treatment involves incorporating chemicals that slow down the spread of flames, thereby enhancing safety standards. **Acoustic properties** are also relevant, particularly in applications where sound insulation is necessary. The porous nature of particle board can make it an effective sound absorber, although its performance may vary based on density and composition. Overall, understanding the physical properties of particle board is essential for selecting the right product for specific uses. By considering factors such as density, moisture resistance, thermal conductivity, mechanical strength, dimensional stability, surface quality, fire resistance, and acoustic performance, users can ensure that their particle board meets the required standards and performs optimally over its lifespan. This comprehensive approach not only enhances the functionality of particle board but also contributes to sustainable and efficient use of this versatile material.
Chemical Properties
Chemical properties play a crucial role in understanding the behavior and durability of particle board, a composite material made from wood particles bonded together with adhesives. These properties are essential for determining the material's performance under various environmental conditions and its suitability for different applications. One key chemical property is the moisture resistance of particle board, which is influenced by the type of adhesive used. For instance, boards made with phenol-formaldehyde (PF) adhesives generally exhibit higher moisture resistance compared to those made with urea-formaldehyde (UF) adhesives. This difference is critical because it affects the board's dimensional stability and resistance to swelling when exposed to water or high humidity. Another important chemical property is the pH level of the particle board. The pH can impact the material's compatibility with other substances and its potential for degradation over time. Particle boards with a neutral pH are less likely to react with acidic or alkaline substances, thereby maintaining their integrity longer. Additionally, the presence of volatile organic compounds (VOCs) in some adhesives can affect indoor air quality, making it a significant consideration for health-conscious consumers and builders. The chemical composition of particle board also influences its fire resistance. Some manufacturers incorporate fire-retardant chemicals into the adhesive or wood particles to enhance the material's performance in fire scenarios. These additives can significantly reduce the spread of flames and smoke, making particle board safer for use in residential and commercial settings. Furthermore, the chemical properties of particle board impact its susceptibility to biological degradation. The use of preservatives and fungicides in some formulations helps protect the material from mold, mildew, and insect damage. This is particularly important for applications where the board may be exposed to damp conditions or outdoor environments. In terms of chemical reactivity, particle board's interaction with various substances must be considered. For example, certain chemicals in cleaning products or paints can degrade the adhesive bonds within the board, leading to structural weakening. Understanding these interactions is vital for ensuring the longevity and performance of particle board in different contexts. Overall, the chemical properties of particle board are multifaceted and significantly influence its overall quality, durability, and suitability for various uses. By selecting appropriate adhesives, controlling pH levels, minimizing VOCs, enhancing fire resistance, protecting against biological degradation, and understanding reactivity with other substances, manufacturers can produce high-quality particle boards that meet specific needs while ensuring safety and performance standards are met. This comprehensive approach to chemical properties underscores the importance of careful material selection and formulation in the production of particle board.
Environmental Impact
When considering the properties and characteristics of particle board, it is crucial to delve into its environmental impact, as this aspect significantly influences its sustainability and overall appeal. Particle board, a composite material made from wood particles bonded together with adhesives, has both positive and negative environmental implications. On the positive side, particle board is often produced from wood waste and residues that would otherwise be discarded, thereby reducing the amount of waste sent to landfills and conserving natural resources. This recycling of wood materials aligns with sustainable forestry practices and helps in managing wood waste efficiently. Additionally, particle board can be engineered to have specific properties that make it a viable alternative to solid wood, potentially reducing the demand on virgin timber and thus helping to preserve forests. However, the environmental impact of particle board is not entirely benign. The production process involves the use of adhesives, many of which contain formaldehyde, a volatile organic compound (VOC) that can contribute to indoor air pollution and pose health risks. Furthermore, the manufacturing process itself can generate significant amounts of energy consumption and greenhouse gas emissions. The sourcing of raw materials also raises concerns; while some particle board is made from recycled wood, other products may be derived from non-sustainably managed forests, contributing to deforestation and habitat destruction. To mitigate these negative impacts, many manufacturers are adopting more sustainable practices. For instance, some producers are transitioning to formaldehyde-free adhesives or using alternative binders that are less harmful to human health and the environment. There is also a growing trend towards using certified sustainable wood sources, such as those accredited by organizations like the Forest Stewardship Council (FSC), ensuring that the wood used in particle board production comes from responsibly managed forests. In conclusion, while particle board offers several environmental benefits due to its efficient use of wood waste and potential to reduce demand on virgin timber, it also presents challenges related to adhesive emissions and energy consumption. As consumers become more environmentally conscious, the industry is responding with innovations aimed at minimizing these adverse effects. By choosing particle board products made with sustainable materials and safer adhesives, consumers can support more environmentally friendly practices within the industry. This balance between resource efficiency and reduced environmental harm underscores the importance of considering the broader ecological footprint when evaluating the properties and characteristics of particle board.
Uses and Applications of Particle Board
Particle board, a versatile and cost-effective engineered wood product, has found widespread use across various industries due to its unique properties and advantages. This article delves into the diverse applications of particle board, highlighting its significance in three key areas: Furniture and Cabinetry, Construction and Building, and Other Industrial Uses. In the realm of Furniture and Cabinetry, particle board is a preferred material for manufacturers due to its affordability, ease of production, and consistent quality. It is often used in the construction of shelving units, cabinets, and other furniture pieces where structural integrity and aesthetic appeal are crucial. The ability to produce large, flat panels with minimal waste makes particle board an ideal choice for mass production. In Construction and Building, particle board serves as a valuable component in wall linings, flooring, and roofing. Its lightweight yet durable nature makes it an excellent option for reducing overall building weight while maintaining structural strength. Additionally, its thermal insulation properties contribute to energy-efficient buildings. Beyond these primary uses, particle board also finds Other Industrial Uses such as in the production of soundproofing materials, decorative panels, and even as a substrate for various types of laminates. Its adaptability and eco-friendly nature make it a go-to material for innovative applications. Transitioning to the first supporting section, we explore how particle board revolutionizes the world of Furniture and Cabinetry by offering a balance between functionality and affordability.
Furniture and Cabinetry
Furniture and cabinetry are among the most prevalent applications of particle board, leveraging its unique blend of affordability, durability, and versatility. Particle board, a composite material made from wood particles bonded together with adhesives, offers several advantages that make it an ideal choice for these industries. In furniture manufacturing, particle board is often used for the construction of frames, shelves, and other structural components due to its stability and resistance to warping. This is particularly beneficial in mass production settings where consistency and cost-efficiency are paramount. For instance, particle board can be easily machined and shaped to precise specifications, allowing for the creation of intricate designs without the high costs associated with solid wood. In cabinetry, particle board's density and smooth surface make it an excellent substrate for veneers and laminates. This combination enhances the aesthetic appeal while maintaining structural integrity. Kitchen and bathroom cabinets, where moisture resistance is crucial, often incorporate particle board cores coated with water-resistant materials to ensure longevity. Additionally, the uniform texture of particle board facilitates the application of various finishes, enabling manufacturers to achieve a wide range of styles and designs that cater to diverse consumer preferences. The environmental benefits of using particle board in furniture and cabinetry are also noteworthy. By utilizing wood waste and residues that would otherwise be discarded, particle board production helps reduce the demand on virgin timber resources. This sustainable approach aligns with contemporary consumer values emphasizing eco-friendliness and responsible resource management. Furthermore, the manufacturing process for particle board typically involves lower energy consumption compared to solid wood processing, contributing to a reduced carbon footprint. From a practical standpoint, particle board's weight and ease of handling make it a favorite among DIY enthusiasts and professional builders alike. It can be easily transported and installed, reducing labor costs and project timelines. Moreover, the material's affordability allows for budget-friendly solutions without compromising on quality, making it accessible to a broader market segment. Innovations in particle board technology have further expanded its applications in furniture and cabinetry. Advanced formulations now include additives that enhance moisture resistance, fire retardancy, and even acoustic insulation properties. These advancements have opened up new possibilities for using particle board in high-performance applications such as soundproofing panels or fire-resistant partitions. In conclusion, the versatility and practicality of particle board make it a cornerstone material in the production of furniture and cabinetry. Its combination of cost-effectiveness, sustainability, and performance characteristics ensures that it remains a preferred choice for both manufacturers and consumers seeking reliable and stylish solutions for their home and office spaces. As technology continues to evolve, the potential uses of particle board are likely to expand even further, solidifying its position as a key component in modern furniture and cabinetry design.
Construction and Building
In the realm of construction and building, particle board plays a pivotal role due to its versatility, cost-effectiveness, and environmental benefits. This engineered wood product, made from wood chips and shavings bonded together with a synthetic resin, is widely used in various applications across the construction industry. One of the primary uses of particle board is in furniture manufacturing, where it serves as a durable and affordable alternative to solid wood. However, its applications extend far beyond this realm. In residential construction, particle board is often utilized for interior components such as wall panels, flooring underlayment, and roof decking. Its uniform density and smooth surface make it an ideal material for these purposes, providing a stable base for finishes like laminate or carpet. Additionally, particle board's ability to be easily machined and shaped allows for precise fitting and minimal waste during the construction process. Commercial buildings also benefit from the use of particle board. It is commonly employed in the creation of office partitions, shelving units, and other interior fixtures due to its lightweight yet robust nature. This makes it easier to transport and install, reducing labor costs and project timelines. Furthermore, particle board can be treated with fire retardants and other chemicals to enhance its performance in terms of fire resistance and moisture tolerance, making it a safe choice for high-traffic areas. Sustainability is another key factor driving the adoption of particle board in modern construction practices. Unlike solid wood products that require large trees to be harvested, particle board can be made from wood waste materials that would otherwise be discarded. This reduces the demand on natural resources and helps in minimizing the environmental footprint of construction projects. Moreover, many manufacturers now produce particle board using eco-friendly resins and adhesives that are free from harmful chemicals like formaldehyde. From a design perspective, particle board offers considerable flexibility. It can be laminated with various finishes such as melamine or veneer to achieve different aesthetic looks without compromising on durability. This versatility makes it a favorite among architects and designers who seek to balance functionality with visual appeal. In summary, particle board's unique combination of affordability, sustainability, and performance characteristics makes it an indispensable material in contemporary construction and building practices. Whether it's used in residential homes, commercial spaces, or industrial settings, particle board continues to prove itself as a reliable choice for builders and designers alike. Its widespread adoption underscores its value as a versatile tool in the pursuit of efficient and sustainable building solutions.
Other Industrial Uses
Beyond its widespread use in furniture and construction, particle board has a diverse array of other industrial applications that leverage its unique properties and cost-effectiveness. In the automotive industry, particle board is often used in the production of car parts such as dashboards, door panels, and trunk linings due to its lightweight yet durable nature. This material helps in reducing the overall weight of vehicles, which can improve fuel efficiency and performance. In the aerospace sector, particle board's ability to be engineered with specific densities and strengths makes it a valuable component for certain aircraft parts. It is used in cabin interiors, seat components, and other non-structural elements where weight reduction is crucial without compromising on safety standards. The electronics industry also benefits from particle board's versatility. It is used as a substrate for printed circuit boards (PCBs) due to its stable dimensional properties and low moisture absorption, which are critical for maintaining the integrity of electronic components. Additionally, particle board is employed in the manufacture of various electronic enclosures and casings because it can be easily machined and finished to precise specifications. In the field of acoustics, particle board is utilized in soundproofing materials and acoustic panels. Its porous structure and density can be tailored to absorb sound waves effectively, making it an ideal material for recording studios, home theaters, and other sound-sensitive environments. Furthermore, particle board plays a significant role in the packaging industry. Its strength-to-weight ratio and affordability make it an excellent choice for producing pallets, crates, and other packaging materials that need to be durable yet lightweight. This reduces shipping costs and minimizes the environmental impact associated with heavier packaging materials. In addition to these applications, particle board is also used in various other industrial sectors such as marine construction, where it is used for boat interiors and other non-structural components due to its resistance to moisture and rot. In the agricultural sector, it is used for animal enclosures and farm equipment due to its ease of cleaning and durability. Overall, the adaptability and economic benefits of particle board make it a highly sought-after material across multiple industries. Its ability to be engineered for specific needs, combined with its environmental sustainability compared to solid wood products, positions particle board as a key component in modern industrial manufacturing processes. As technology continues to evolve, the potential uses of particle board are likely to expand further, solidifying its place as a versatile and indispensable material in various industrial applications.