What Does Whmis Stands For

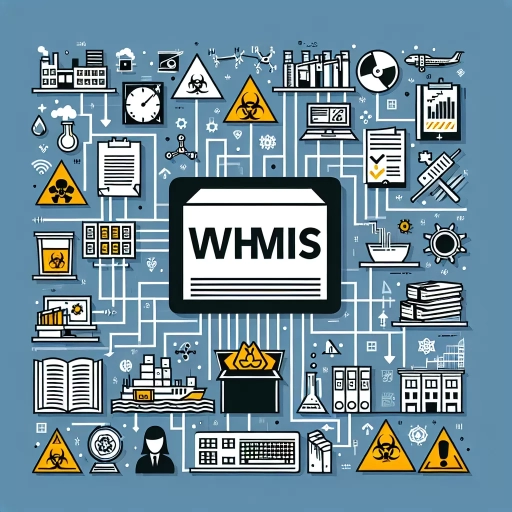
WHMIS, or the Workplace Hazardous Materials Information System, is a critical component of workplace safety in Canada. This comprehensive system ensures that workers are informed about the hazards associated with the chemicals they use, handle, and store. The acronym WHMIS encapsulates a multifaceted approach to chemical safety, which includes understanding the meaning behind the acronym, identifying its key components, and ensuring proper implementation and compliance. In this article, we will delve into these essential aspects of WHMIS. First, we will explore the meaning and significance of the WHMIS acronym, providing a foundational understanding of its role in workplace safety. Next, we will examine the key components of WHMIS, including labels, safety data sheets (SDS), and training requirements. Finally, we will discuss the implementation and compliance measures necessary to ensure that workplaces adhere to WHMIS standards. By understanding these elements, employers and employees can better navigate the complexities of chemical safety in the workplace. Let's begin by **Understanding the Acronym WHMIS**.
Understanding the Acronym WHMIS
Understanding the acronym WHMIS (Workplace Hazardous Materials Information System) is crucial for ensuring safety and compliance in workplaces that handle hazardous materials. This comprehensive system provides a framework for identifying, labeling, and communicating the hazards associated with chemical products. To grasp the significance of WHMIS, it is essential to delve into its definition and full form, which sets the foundation for understanding its role in workplace safety. Additionally, exploring the historical context and development of WHMIS reveals how it has evolved over time to address emerging safety concerns. Comparing WHMIS with international standards also highlights its unique features and global relevance. By examining these aspects, we can appreciate the importance of WHMIS in safeguarding workers and the environment. Let us begin by defining WHMIS and understanding its full form, which is the cornerstone of this critical safety system.
Definition and Full Form
**Understanding the Acronym WHMIS** WHMIS, or the Workplace Hazardous Materials Information System, is a crucial component of workplace safety in Canada. The full form of WHMIS encapsulates its primary function: to provide workers with essential information about hazardous materials they may encounter on the job. This system ensures that employees are well-informed and equipped to handle, use, and dispose of hazardous substances safely. WHMIS includes several key elements such as labels on containers, safety data sheets (SDS), and worker training programs. These components work together to minimize risks associated with hazardous materials, thereby protecting the health and safety of workers. By understanding WHMIS, employers and employees alike can adhere to regulatory standards and maintain a safer work environment. This comprehensive approach to hazard management is mandated by Canadian law, emphasizing the importance of clear communication and education regarding chemical hazards in the workplace. As such, WHMIS stands as a cornerstone of occupational health and safety in Canada, ensuring that all stakeholders are aware of and prepared to manage potential hazards effectively.
Historical Context and Development
The acronym WHMIS, standing for Workplace Hazardous Materials Information System, has its roots deeply embedded in historical context and development. The need for a standardized system to manage hazardous materials in the workplace became increasingly evident in the late 20th century. Prior to WHMIS, Canada lacked a unified approach to handling and communicating the risks associated with hazardous substances, leading to inconsistencies and gaps in worker safety. In the 1980s, the Canadian government recognized the urgency of addressing these issues. This led to the establishment of WHMIS through a collaborative effort between federal, provincial, and territorial governments. The system was officially implemented in 1988 with the passage of the Hazardous Products Act and the Controlled Products Regulations. WHMIS was designed to ensure that workers were adequately informed about the hazards of materials they worked with, thereby reducing the risk of injuries and illnesses. A key component of WHMIS is the classification of hazardous products based on their physical and health hazards. This classification system is aligned with international standards, such as those set by the United Nations' Globally Harmonized System of Classification and Labelling of Chemicals (GHS). The implementation of GHS principles in WHMIS has further enhanced its effectiveness by providing a globally recognized framework for hazard communication. The development of WHMIS also involved the creation of standardized labels and safety data sheets (SDSs) for hazardous products. These labels and SDSs are crucial tools that provide workers with essential information about the safe handling, use, storage, and disposal of hazardous materials. Training programs were also mandated as part of WHMIS to ensure that workers understood how to interpret this information and take necessary precautions. Over the years, WHMIS has undergone several updates and revisions to align with evolving international standards and best practices. For instance, in 2015, WHMIS 2015 was introduced, which incorporated GHS principles more fully into the Canadian system. This update aimed to improve the clarity and consistency of hazard communication, making it easier for workers to understand and respond to potential hazards. In summary, WHMIS is a comprehensive system that has evolved significantly since its inception in the late 1980s. Its development reflects a commitment to enhancing worker safety through standardized hazard communication and training. By understanding the historical context and ongoing development of WHMIS, individuals can better appreciate its importance in protecting workers from the risks associated with hazardous materials in the workplace.
International Comparisons
When delving into the realm of workplace safety and chemical management, understanding international comparisons is crucial for a comprehensive grasp of the acronym WHMIS (Workplace Hazardous Materials Information System). WHMIS, a Canadian standard, is part of a broader global landscape where various countries have their own regulations and standards for handling hazardous materials. For instance, the United States has OSHA's Hazard Communication Standard (HCS), while the European Union operates under the REACH (Registration, Evaluation, Authorisation and Restriction of Chemicals) and CLP (Classification, Labelling and Packaging) regulations. These systems share common goals—ensuring workers are informed about the hazards of chemicals they handle—but differ in specifics. In Canada, WHMIS mandates that employers provide workers with information about hazardous materials through labels, safety data sheets (SDS), and training. This aligns with the Globally Harmonized System of Classification and Labelling of Chemicals (GHS), an international standard adopted by many countries to ensure consistency in chemical hazard communication. The GHS framework provides a uniform approach to classifying chemicals and communicating their hazards, facilitating international trade and safety compliance. Comparing WHMIS to other international standards highlights both similarities and differences. For example, while both WHMIS and OSHA's HCS require SDSs and labels, the specific requirements for these documents can vary. In contrast, the EU's CLP regulation focuses more on the classification and labelling aspects, with REACH addressing the registration and authorization of chemicals. Understanding these differences is essential for companies operating globally, as they must comply with multiple regulatory frameworks. Moreover, international comparisons underscore the importance of harmonization efforts. The adoption of GHS by various countries has streamlined the process of managing hazardous materials across borders, reducing confusion and enhancing safety. This harmonization also facilitates trade by ensuring that chemical products meet consistent safety standards worldwide. In summary, understanding WHMIS within the context of international comparisons provides a deeper appreciation for the global efforts to manage hazardous materials safely. By recognizing the similarities and differences between various national standards, employers can better navigate the complexities of chemical safety regulations, ultimately enhancing workplace safety and compliance on a global scale. This knowledge is pivotal for any organization aiming to operate safely and efficiently in today's interconnected world.
Key Components of WHMIS
The Workplace Hazardous Materials Information System (WHMIS) is a critical framework designed to ensure the safe handling, use, and disposal of hazardous materials in Canadian workplaces. At its core, WHMIS comprises three key components that work together to protect workers and the environment. First, the **Classification of Hazardous Materials** categorizes substances based on their potential health and physical hazards, providing a standardized way to identify risks. Second, **Labeling and Signage Requirements** mandate clear and consistent labeling of hazardous materials, ensuring that workers are aware of the dangers they may face. Third, **Safety Data Sheets (SDS)** provide detailed information on the safe handling, storage, and emergency procedures for each hazardous material. Understanding these components is essential for maintaining a safe work environment. By classifying hazardous materials accurately, employers can take the first crucial step in safeguarding their workforce, which is why the classification process is a foundational element of WHMIS. Transitioning to the classification process, it is imperative to delve into how hazardous materials are categorized to ensure compliance and safety.
Classification of Hazardous Materials
The classification of hazardous materials is a critical component of the Workplace Hazardous Materials Information System (WHMIS), ensuring that workers are aware of the potential dangers associated with the substances they handle. Under WHMIS, hazardous materials are categorized based on their physical and health hazards. **Physical hazards** include flammable liquids, gases, and solids, as well as oxidizing substances and corrosive materials. These classifications help in understanding how a substance can cause harm through explosion, fire, or chemical reaction. For instance, flammable liquids are those that can ignite easily and burn rapidly, posing significant fire risks. **Health hazards** are another key classification, encompassing substances that can cause adverse health effects through inhalation, ingestion, or skin contact. This category includes toxic substances, biohazardous materials, and substances that can cause skin or eye irritation. For example, toxic substances may be carcinogenic (cancer-causing), teratogenic (causing birth defects), or mutagenic (causing genetic mutations). Biohazardous materials, on the other hand, include pathogens and other biological agents that can cause disease. The classification process involves evaluating the intrinsic properties of a substance and its potential to cause harm. This evaluation is typically conducted by the manufacturer or supplier of the hazardous material and is based on scientific data and testing. The results of this evaluation are then communicated through Safety Data Sheets (SDSs) and labels, which provide essential information about the hazards associated with each substance. WHMIS also mandates specific criteria for classifying hazardous materials into different categories and subcategories. For example, substances are classified as "toxic" if they meet certain concentration limits that indicate potential harm. Similarly, corrosive substances are classified based on their ability to cause severe skin or eye damage. The accurate classification of hazardous materials is crucial for ensuring workplace safety. It enables employers to implement appropriate control measures, such as personal protective equipment (PPE), ventilation systems, and safe handling procedures. Workers can also make informed decisions about how to handle substances safely and respond effectively in case of emergencies. Overall, the classification of hazardous materials under WHMIS serves as a foundational element in protecting worker health and safety by providing clear and consistent information about the risks associated with various substances.
Labeling and Signage Requirements
Labeling and signage are crucial components of the Workplace Hazardous Materials Information System (WHMIS), ensuring that workers are adequately informed about the hazards associated with the chemicals they handle. Under WHMIS, labeling requirements are stringent to ensure clear communication of hazard information. Suppliers must label all hazardous products with a Safety Data Sheet (SDS) and a label that includes specific elements such as the product identifier, hazard statements, precautionary statements, and pictograms. These pictograms are standardized symbols that visually convey the nature of the hazard, making it easier for workers to quickly identify potential dangers. Signage is another vital aspect, particularly in workplaces where hazardous materials are stored or used. Employers are required to post signs in areas where hazardous materials are present, indicating the location of these substances and any necessary safety precautions. These signs must be legible, visible, and durable enough to withstand the work environment. The use of standardized signage ensures consistency across different workplaces, reducing confusion and enhancing safety. Compliance with labeling and signage requirements is not only a legal obligation but also a critical step in preventing workplace accidents and ensuring a safe working environment. Proper labeling helps workers understand how to handle chemicals safely, while signage alerts them to potential hazards in their immediate surroundings. This dual approach of clear labeling and effective signage reinforces the overall goal of WHMIS: to protect workers from the risks associated with hazardous materials through accurate and accessible information. In addition, employers must ensure that all labels and signs are regularly updated and maintained. This includes replacing damaged or worn-out labels and signs promptly to maintain their effectiveness. Training programs should also be implemented to educate workers on how to interpret labels and signs correctly, further enhancing workplace safety. Overall, the labeling and signage requirements under WHMIS are designed to provide a comprehensive system for communicating hazard information effectively. By adhering to these requirements, workplaces can significantly reduce the risk of accidents and ensure a safer environment for all employees. This aligns with the broader objectives of WHMIS, which aims to protect workers' health and safety through informed handling of hazardous materials.
Safety Data Sheets (SDS)
Safety Data Sheets (SDS) are a crucial component of the Workplace Hazardous Materials Information System (WHMIS), providing essential information to ensure the safe handling, use, storage, and disposal of hazardous materials in the workplace. An SDS is a detailed document that outlines the properties, hazards, and safety precautions associated with a particular chemical product. It is typically divided into 16 sections, each addressing a specific aspect of the substance: identification, hazard identification, composition/information on ingredients, first aid measures, fire-fighting measures, accidental release measures, handling and storage, exposure controls/personal protection, physical and chemical properties, stability and reactivity, toxicological information, ecological information, disposal considerations, transport information, regulatory information, and other information. The SDS serves as a critical resource for workers, employers, and emergency responders by providing clear instructions on how to manage potential risks. For instance, Section 4 of an SDS outlines first aid measures in case of exposure, while Section 5 details fire-fighting measures to mitigate risks during a fire. Section 8 focuses on exposure controls and personal protective equipment (PPE) necessary to prevent harm. Employers are required to ensure that SDSs are readily accessible to all employees who work with or around hazardous materials, fostering a culture of safety and compliance within the workplace. Moreover, SDSs play a pivotal role in training programs under WHMIS. They help in educating workers about the hazards of specific chemicals and the appropriate safety protocols to follow. This includes understanding the Globally Harmonized System of Classification and Labelling of Chemicals (GHS) symbols and statements found on the SDS, which provide immediate visual cues about the nature of the hazard. In summary, Safety Data Sheets are indispensable tools within WHMIS, offering comprehensive guidance on managing hazardous substances safely. By adhering to the information provided in an SDS, workplaces can significantly reduce the risk of accidents and ensure a safer environment for all employees.
Implementation and Compliance with WHMIS
Implementing and complying with the Workplace Hazardous Materials Information System (WHMIS) is crucial for ensuring a safe and healthy work environment. This comprehensive system involves several key components that work together to protect workers from hazardous materials. First, **Training and Education for Workers** is essential as it equips employees with the knowledge and skills necessary to handle hazardous substances safely. Second, a robust **Regulatory Framework and Enforcement** ensures that all stakeholders adhere to the standards and guidelines set forth by WHMIS, providing a structured approach to compliance. Finally, **Best Practices for Workplace Safety** help organizations go beyond mere compliance by implementing proactive measures to mitigate risks associated with hazardous materials. By focusing on these three areas, organizations can create a culture of safety and compliance. Effective training programs, stringent regulatory adherence, and best practices all contribute to a workplace where workers are well-informed and equipped to manage hazards effectively. This article will delve into each of these critical aspects, starting with the foundational element of **Training and Education for Workers**, which is vital for ensuring that every employee understands their role in maintaining a safe and compliant work environment.
Training and Education for Workers
Training and education for workers are crucial components in the implementation and compliance with the Workplace Hazardous Materials Information System (WHMIS). WHMIS is a national standard for the safe handling, use, storage, and disposal of hazardous products in Canadian workplaces. Effective training ensures that workers understand the risks associated with hazardous materials and know how to protect themselves and others. Workers must be trained on the WHMIS system, including the classification of hazardous products, the interpretation of safety data sheets (SDSs), and the understanding of labels on hazardous products. This training should cover the Globally Harmonized System of Classification and Labelling of Chemicals (GHS) standards, which WHMIS has adopted. Workers need to know how to identify hazards, understand the necessary precautions, and respond to emergencies involving hazardous materials. Comprehensive training programs should include both theoretical knowledge and practical skills. For instance, workers should learn how to read and interpret SDSs, which provide detailed information about the safe handling, use, storage, and emergency procedures for each hazardous product. They must also understand the significance of labels and how they convey critical safety information. Hands-on training is equally important. Workers should be familiarized with personal protective equipment (PPE) and learn how to use it correctly. They should also participate in simulated emergency scenarios to practice their response skills in a controlled environment. Regular refresher courses are essential to ensure that workers remain up-to-date with any changes in WHMIS regulations or new hazardous products introduced into the workplace. Employers have a legal responsibility to provide this training and ensure that all workers are competent in WHMIS procedures. This includes documenting training sessions, conducting regular audits to ensure compliance, and making sure that all new employees receive the necessary training before starting work with hazardous materials. In summary, thorough training and education are vital for ensuring that workers can safely handle hazardous materials in compliance with WHMIS regulations. By providing comprehensive training programs that include both theoretical knowledge and practical skills, employers can protect their workers from potential hazards and maintain a safe working environment.
Regulatory Framework and Enforcement
The regulatory framework and enforcement of the Workplace Hazardous Materials Information System (WHMIS) are crucial components in ensuring the safe handling, use, and disposal of hazardous materials in Canadian workplaces. WHMIS is governed by federal, provincial, and territorial legislation, which mandates that employers provide workers with essential information about the hazards of chemicals they use. The framework is based on the Hazardous Products Act and the Controlled Products Regulations, which outline the requirements for labeling, material safety data sheets (MSDS), and worker training. At the federal level, Health Canada is responsible for establishing and enforcing the standards for WHMIS. This includes setting criteria for hazard classification, labeling requirements, and the content of safety data sheets (SDS). Provincial and territorial authorities, such as occupational health and safety (OHS) agencies, enforce these standards within their jurisdictions. These agencies conduct inspections, investigate incidents, and impose penalties for non-compliance. Enforcement mechanisms include regular workplace inspections to ensure that employers are adhering to WHMIS regulations. Inspectors verify that hazardous products are properly labeled, that SDSs are readily available to workers, and that employees have received adequate training on the safe handling of these substances. Non-compliance can result in fines, penalties, and even prosecution under relevant OHS legislation. Employers must also maintain records of worker training and ensure that all hazardous materials are classified according to the Globally Harmonized System of Classification and Labelling of Chemicals (GHS). This harmonization helps in standardizing hazard communication across different regions and countries, enhancing safety and reducing confusion among workers. In addition to regulatory enforcement, there are also mechanisms for public reporting and whistleblower protection. Workers who identify hazards or non-compliance can report these issues to their employers or directly to regulatory authorities without fear of reprisal. This encourages a culture of safety and accountability within workplaces. Overall, the robust regulatory framework and stringent enforcement mechanisms of WHMIS play a pivotal role in safeguarding worker health and safety by ensuring that hazardous materials are handled responsibly. By adhering to these regulations, employers not only comply with legal requirements but also contribute to a safer work environment for all employees.
Best Practices for Workplace Safety
**Best Practices for Workplace Safety** Implementing and complying with the Workplace Hazardous Materials Information System (WHMIS) is crucial for maintaining a safe and healthy work environment. Here are some best practices to ensure effective workplace safety: 1. **Training and Education**: Provide comprehensive training to all employees on WHMIS, including the Globally Harmonized System of Classification and Labelling of Chemicals (GHS). Ensure that workers understand the hazards associated with the materials they handle and how to read Safety Data Sheets (SDS) and labels. 2. **Labeling and Signage**: Ensure that all hazardous materials are properly labeled with GHS-compliant labels. Use clear and consistent signage to identify hazardous areas and materials, making it easy for employees to recognize potential dangers. 3. **SDS Management**: Maintain an up-to-date inventory of SDSs for all hazardous materials in the workplace. Make these documents easily accessible to employees and ensure they are reviewed regularly. 4. **Personal Protective Equipment (PPE)**: Provide and enforce the use of appropriate PPE for tasks involving hazardous materials. Conduct regular inspections to ensure PPE is in good condition and properly used. 5. **Emergency Preparedness**: Develop and regularly practice emergency response plans, including procedures for spills, fires, and exposure to hazardous substances. Ensure that first aid kits are readily available and that employees know how to use them. 6. **Regular Inspections**: Conduct regular workplace inspections to identify potential hazards and implement corrective actions promptly. Involve employees in the inspection process to gather their insights and concerns. 7. **Employee Participation**: Encourage employee participation in safety initiatives through open communication channels. Foster a culture where employees feel comfortable reporting safety concerns without fear of reprisal. 8. **Record Keeping**: Maintain accurate records of training sessions, inspections, incidents, and compliance activities. This helps in tracking progress, identifying trends, and making necessary improvements. 9. **Continuous Improvement**: Regularly review and update safety policies and procedures to reflect changes in regulations, new technologies, or lessons learned from incidents. 10. **Compliance Audits**: Perform periodic compliance audits to ensure that all aspects of WHMIS are being followed correctly. Address any gaps or deficiencies identified during these audits promptly. By adhering to these best practices, organizations can create a robust safety culture that not only complies with WHMIS regulations but also protects the health and well-being of their employees. This proactive approach to workplace safety is essential for preventing accidents, reducing injuries, and maintaining a productive work environment.