What Is A Subfloor

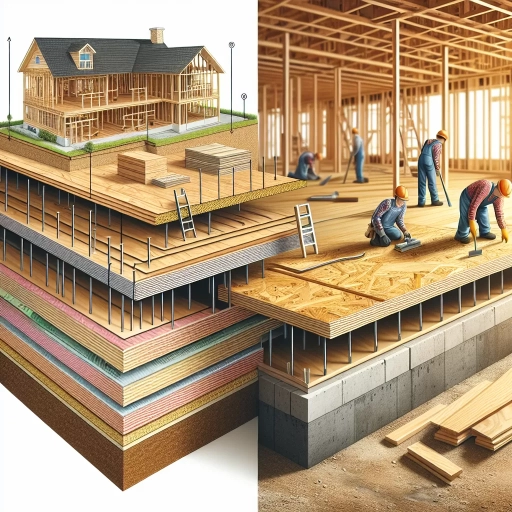
A subfloor is a crucial component of any building, serving as the foundation for the entire flooring system. It plays a pivotal role in ensuring the structural integrity, stability, and durability of the floors above. Understanding what a subfloor is and its significance is essential for homeowners, builders, and architects alike. This article delves into the comprehensive aspects of a subfloor, starting with **Understanding the Basics of a Subfloor**, where we explore its fundamental purpose and how it integrates with the overall construction process. We will also examine **Components and Materials of a Subfloor**, highlighting the various materials used and their characteristics. Finally, we will discuss **Installation and Maintenance of a Subfloor**, providing insights into the best practices for installing and maintaining this critical layer. By grasping these key elements, readers will gain a thorough understanding of how a subfloor functions and why it is indispensable in modern construction. Let's begin by **Understanding the Basics of a Subfloor**.
Understanding the Basics of a Subfloor
Understanding the basics of a subfloor is crucial for any construction or renovation project, as it forms the foundation upon which the entire floor system is built. A subfloor serves multiple critical functions, and grasping its definition and purpose is essential for ensuring structural integrity and longevity. In this article, we will delve into three key aspects: the definition and purpose of a subfloor, the various types of subfloors available, and the importance of subfloors in construction. First, we will explore the **Definition and Purpose** of a subfloor, clarifying its role in supporting the finished floor and the overall structure of a building. This foundational knowledge is vital for architects, builders, and homeowners alike. Next, we will examine the **Types of Subfloors**, including plywood, oriented strand board (OSB), concrete, and others, highlighting their unique characteristics and applications. Finally, we will discuss the **Importance in Construction**, emphasizing how a well-designed and properly installed subfloor can prevent issues such as uneven flooring, moisture damage, and structural instability. By understanding these fundamental concepts, individuals can make informed decisions that ensure their projects are both durable and aesthetically pleasing. Let's begin by defining what a subfloor is and why it is so pivotal in building design.
Definition and Purpose
Understanding the basics of a subfloor begins with a clear definition and purpose. A subfloor is the structural layer of a floor that lies directly beneath the finish flooring, such as hardwood, carpet, or tile. It serves as the foundation for the entire flooring system, providing a stable and level surface for the installation of various types of flooring materials. The primary purpose of a subfloor is to distribute the weight of the flooring and any loads placed upon it evenly, ensuring that the floor remains stable and free from damage. This critical layer also acts as a barrier against moisture and other environmental factors that could compromise the integrity of the flooring. In terms of construction, subfloors are typically made from materials like plywood, oriented strand board (OSB), or concrete. Each material has its own set of advantages and is chosen based on factors such as budget, desired durability, and specific installation requirements. For instance, plywood and OSB are commonly used in residential construction due to their cost-effectiveness and ease of installation, while concrete subfloors are more prevalent in commercial settings where higher load-bearing capacities are necessary. The design and installation of a subfloor must adhere to strict standards to ensure it meets its intended purpose. This includes ensuring that the subfloor is level, securely fastened to the joists or beams beneath it, and free from any defects or irregularities. Properly installed subfloors also play a crucial role in soundproofing and thermal insulation, contributing to a more comfortable living or working environment. Moreover, understanding the definition and purpose of a subfloor is essential for homeowners and builders alike because it directly impacts the longevity and performance of the flooring. A well-constructed subfloor can extend the lifespan of the finish flooring by preventing issues such as warping, buckling, or uneven wear. Conversely, a poorly installed subfloor can lead to costly repairs down the line. In summary, the definition and purpose of a subfloor are fundamental to understanding its role within the broader context of flooring systems. By recognizing its importance as a structural foundation and barrier against environmental factors, individuals can better appreciate the necessity of proper installation techniques and material selection. This knowledge not only enhances the aesthetic appeal of a room but also ensures that the flooring remains functional and durable over time.
Types of Subfloors
When delving into the world of subfloors, it's crucial to understand the various types that exist, each with its own set of characteristics, advantages, and applications. A subfloor serves as the foundation for your finished flooring, whether it's hardwood, tile, carpet, or laminate. There are primarily three main types of subfloors: concrete, plywood, and oriented strand board (OSB). **Concrete Subfloors** are the most common in new construction and are often found in basements and ground-level floors. They consist of a poured concrete slab that can be finished with various toppings such as self-leveling compounds or epoxy coatings to create a smooth surface. Concrete subfloors are durable and can withstand heavy loads but may require additional preparation before installing certain types of finished flooring. For instance, concrete must be dry and free of cracks to ensure a successful installation. **Plywood Subfloors** are made from layers of wood veneer pressed together with adhesives. They are widely used in residential construction due to their strength and stability. Plywood subfloors come in different thicknesses, typically ranging from 3/4 inch to 1 inch, and are often installed over joists spaced 16 inches apart. The key advantage of plywood is its ability to provide a smooth, even surface that is ideal for installing various types of finished flooring without significant preparation. **Oriented Strand Board (OSB) Subfloors** are another popular option, known for their cost-effectiveness and environmental sustainability. OSB is made from strands of wood pressed together with wax and resin adhesives. While it shares many similarities with plywood, OSB tends to be less expensive but can be more prone to moisture damage. Therefore, it's essential to ensure that OSB subfloors are properly sealed and maintained to prevent water damage. In addition to these primary types, there are also **Composite Subfloors**, which combine different materials like concrete and wood. These hybrid subfloors offer the benefits of both worlds—durability from concrete and the ease of installation associated with wood products. Understanding the differences between these types of subfloors is vital for homeowners and builders alike. Each type has specific requirements for installation, maintenance, and compatibility with various finished flooring options. For example, certain types of flooring may require additional underlayment materials when installed over specific subfloor types. By selecting the right subfloor for your project, you can ensure a stable foundation that supports your finished flooring and enhances the overall integrity of your structure. In summary, the choice of subfloor type depends on factors such as budget, intended use, and environmental conditions. Whether you opt for the robustness of concrete, the versatility of plywood, or the affordability of OSB, each type offers unique benefits that can significantly impact the success and longevity of your flooring installation. By grasping these fundamentals, you'll be better equipped to make informed decisions that align with your project's needs and ensure a solid foundation for years to come.
Importance in Construction
The importance of construction in the context of a subfloor cannot be overstated. A subfloor serves as the foundational layer upon which the entire floor system is built, making it crucial for the structural integrity, durability, and overall performance of the flooring. Here, precision and quality in construction are paramount. Firstly, a well-constructed subfloor ensures that the finished floor remains level and even, which is essential for aesthetic appeal as well as functionality. Any irregularities or defects in the subfloor can lead to uneven surfaces, which may cause issues with flooring materials such as hardwood, tile, or carpet. For instance, an uneven subfloor can result in creaking floors, cracked tiles, or buckled hardwood planks. This not only compromises the appearance but also reduces the lifespan of the flooring. Secondly, a properly constructed subfloor plays a critical role in load distribution. It must be able to support the weight of the finished floor along with any furniture, appliances, and foot traffic. A subfloor that is inadequately built can lead to sagging or collapse under heavy loads, posing significant safety risks. Moreover, it can also affect the stability of walls and ceilings if the structural integrity is compromised. Thirdly, construction quality impacts moisture management. A subfloor that is not correctly sealed or insulated can allow moisture to seep through, leading to mold growth, rotting wood, and other forms of damage. This is particularly important in areas prone to high humidity or water exposure like bathrooms and kitchens. Proper construction techniques ensure that the subfloor is adequately protected against moisture ingress. Additionally, energy efficiency is another key aspect where construction quality matters. A well-insulated subfloor can significantly reduce heat loss during winter and heat gain during summer, thereby lowering energy costs and enhancing comfort levels within the building. This is especially relevant in regions with extreme climates where energy consumption can be high. From a maintenance perspective, a high-quality subfloor construction minimizes future repair needs. When done correctly, it reduces the likelihood of costly repairs down the line due to issues like unevenness or water damage. This not only saves money but also reduces downtime and inconvenience associated with repairs. Lastly, compliance with building codes and standards is essential for ensuring safety and legal compliance. A subfloor constructed according to these guidelines guarantees that it meets minimum requirements for strength, durability, and safety. This is critical for both residential and commercial properties as it impacts insurance coverage, property value, and regulatory approvals. In summary, the importance of construction in creating a robust and reliable subfloor cannot be overemphasized. It underpins every aspect of flooring performance—from aesthetics and functionality to safety and energy efficiency. By focusing on high-quality construction practices from the outset, builders can ensure that their projects stand the test of time while providing optimal comfort and value to occupants. Understanding these basics is fundamental for anyone involved in building or renovating properties where a solid foundation is essential for long-term success.
Components and Materials of a Subfloor
When constructing or renovating a building, the subfloor is a critical component that often goes unnoticed but plays a pivotal role in the overall integrity and functionality of the structure. A well-designed subfloor must balance several key factors to ensure it supports the weight of the building, maintains structural stability, and provides a comfortable living or working environment. This article delves into the essential components and materials of a subfloor, exploring three crucial aspects: **Common Subfloor Materials**, **Structural Elements**, and **Moisture and Insulation Considerations**. Understanding these elements is vital for architects, builders, and homeowners alike, as they directly impact the durability, safety, and comfort of the space above. By examining the various materials used in subfloor construction, we can better appreciate how different choices affect the final outcome. Let's begin by looking at **Common Subfloor Materials**, which form the foundation of any successful subfloor design.
Common Subfloor Materials
When it comes to constructing a subfloor, the choice of material is crucial for ensuring durability, stability, and overall performance. Several common subfloor materials are widely used due to their unique properties and advantages. **Plywood** is one of the most popular choices, known for its strength, stability, and resistance to moisture. It is made from layers of wood veneer pressed together with adhesive, offering a smooth surface ideal for various flooring types. Another option is **Oriented Strand Board (OSB)**, which is more cost-effective than plywood but still provides good structural integrity. OSB is composed of strands of wood pressed together with wax and resin, making it suitable for most residential and commercial applications. **Concrete** subfloors are also common, especially in basements and garages. Concrete offers excellent durability and can withstand heavy loads, making it a preferred choice for high-traffic areas. However, it requires careful preparation to ensure it is level and free of cracks before installing any finish flooring. **Cement-based underlayment** materials are often used over concrete subfloors to create a smooth, even surface. These underlayment materials help in correcting minor imperfections and provide a better bond between the subfloor and the finish flooring. For historical or traditional construction, **solid hardwood** subfloors may be used. These subfloors are made from individual planks of hardwood and offer a unique aesthetic appeal. However, they can be more expensive and require more maintenance compared to other materials. **Engineered wood** subfloors are another alternative, combining the benefits of solid hardwood with the stability of engineered products. They consist of multiple layers of wood, with the top layer being the desired hardwood species, making them less prone to warping and shrinking. In addition to these materials, **cement-based self-leveling compounds** are increasingly popular for creating a perfectly level subfloor. These compounds are poured onto the existing subfloor and spread evenly to fill any gaps or uneven areas, providing a smooth surface ready for finish flooring installation. For areas requiring extra insulation or soundproofing, **foam underlayment** materials can be used. These materials are typically made from polyethylene or polypropylene foam and are designed to reduce noise and provide thermal insulation. Each of these subfloor materials has its own set of advantages and considerations, making the selection process dependent on factors such as budget, intended use, and environmental conditions. Understanding the characteristics of each material helps in making an informed decision that ensures the longevity and performance of the entire flooring system. By choosing the right subfloor material, homeowners and builders can create a solid foundation that supports the entire structure and enhances the overall quality of the finished floor.
Structural Elements
When discussing the components and materials of a subfloor, it is crucial to delve into the structural elements that form its foundation. These elements are the backbone of any subfloor, ensuring stability, durability, and the overall integrity of the floor system. At the core of these structural components are joists, which are typically spaced at regular intervals (usually 16 or 24 inches on center) and span the width of the room. Joists can be made from various materials such as solid wood, engineered wood, or even steel, each offering different strengths and advantages. For instance, solid wood joists provide a traditional and often preferred option due to their ease of installation and natural aesthetic appeal, while engineered wood joists offer enhanced stability and resistance to warping. Another critical structural element is the subfloor sheathing, which is laid over the joists to create a solid surface. This sheathing can be composed of plywood, oriented strand board (OSB), or even concrete in some cases. Plywood and OSB are popular choices due to their cost-effectiveness and ease of installation; however, plywood is generally preferred for its superior strength and moisture resistance. The sheathing material must be carefully selected to ensure it can withstand the loads imposed by the finished flooring and any additional elements such as furniture or appliances. In addition to joists and sheathing, beams and posts play a significant role in supporting the subfloor structure. Beams are larger, heavier timbers that span longer distances than joists and often serve as primary support members for the entire floor system. Posts, on the other hand, are vertical elements that transfer loads from beams down to the foundation or footings below ground level. These components work in tandem to distribute weight evenly across the subfloor, preventing sagging or collapse. The connection between these structural elements is also vital for the overall stability of the subfloor. This is where fasteners such as nails, screws, and bolts come into play. Proper fastening techniques ensure that joists are securely attached to beams and that sheathing is tightly fixed to the joists. In modern construction, advanced fastening systems like ring-shank nails or structural screws are often used for their enhanced holding power. Finally, it's important to consider the role of adhesives in reinforcing these structural connections. Adhesives like construction glue can be applied between layers of sheathing or between sheathing and joists to add an extra layer of strength and rigidity to the subfloor system. In summary, the structural elements of a subfloor—joists, sheathing, beams, posts, fasteners, and adhesives—work together harmoniously to provide a robust foundation for any flooring installation. Understanding these components and their interdependencies is essential for ensuring a safe, durable, and aesthetically pleasing final product. By selecting appropriate materials and adhering to best practices in construction techniques, builders can create subfloors that meet both functional needs and architectural standards.
Moisture and Insulation Considerations
When it comes to the components and materials of a subfloor, moisture and insulation considerations are paramount for ensuring the longevity and performance of the entire flooring system. Moisture can be a significant enemy of subfloors, as it can lead to structural damage, mold growth, and compromised integrity. To mitigate these risks, it is crucial to select materials that are resistant to moisture. For instance, using waterproof membranes or vapor barriers between the subfloor and the finished floor can prevent moisture from seeping into the subfloor, thereby reducing the risk of rot, warping, or delamination. Additionally, materials like concrete or cement-based underlayment are often preferred due to their inherent resistance to moisture. Insulation is another critical factor that should not be overlooked. Proper insulation not only enhances thermal comfort by reducing heat loss in colder climates and heat gain in warmer climates but also helps in controlling humidity levels within the building. This is particularly important for subfloors as it prevents condensation from forming, which could otherwise lead to moisture-related issues. Insulation materials such as foam board, fiberglass batts, or reflective insulation can be effectively used in subfloor construction to achieve these benefits. Furthermore, ensuring adequate ventilation in crawl spaces or basements is essential for maintaining a dry environment and preventing moisture buildup. The choice of insulation material also depends on the specific requirements of the building and its geographical location. For example, in regions with high humidity or extreme temperatures, more robust insulation solutions may be necessary. It is also important to consider the R-value (thermal resistance) of the insulation material to ensure it meets local building codes and standards. In addition to material selection, proper installation techniques play a vital role in maintaining a moisture-free and well-insulated subfloor. Ensuring that all joints and seams are sealed correctly and that there are no gaps or voids where moisture could penetrate is essential. Regular maintenance checks should also be conducted to identify any potential issues early on. In summary, addressing moisture and insulation considerations is fundamental when designing and constructing a subfloor. By choosing appropriate materials, ensuring proper installation practices, and maintaining good ventilation, homeowners and builders can create a durable and efficient flooring system that withstands various environmental conditions while providing long-term comfort and structural integrity. These considerations are integral components of a well-designed subfloor that supports the overall health and functionality of the building.
Installation and Maintenance of a Subfloor
When it comes to ensuring the integrity and longevity of any flooring system, the installation and maintenance of a subfloor are paramount. A well-installed subfloor serves as the foundation for your entire flooring structure, impacting both its aesthetic appeal and functional durability. This article delves into the critical aspects of subfloor management, covering three essential areas: **Preparation and Installation Steps**, **Common Issues and Solutions**, and **Long-Term Maintenance Tips**. Understanding these elements is crucial for homeowners, contractors, and DIY enthusiasts alike. By following the right preparation and installation steps, you can avoid common pitfalls that might arise during the process. Identifying and addressing common issues promptly can save time and resources in the long run. Finally, adhering to long-term maintenance tips ensures that your subfloor remains in optimal condition over years of use. In this comprehensive guide, we will start by exploring the meticulous **Preparation and Installation Steps** necessary to lay a solid foundation for your flooring system.
Preparation and Installation Steps
When it comes to the installation and maintenance of a subfloor, the preparation and installation steps are crucial for ensuring a stable, durable, and long-lasting foundation. The process begins with thorough preparation, which involves inspecting the site for any obstructions or unevenness. This includes clearing the area of debris, old flooring materials, and any other obstacles that could interfere with the installation. Next, the subgrade—the ground beneath the subfloor—must be leveled and compacted to create a solid base. This step is essential for preventing future settling or shifting issues. Once the site is prepared, the next step is to lay down a vapor barrier or underlayment material. This layer helps protect the subfloor from moisture rising from the ground, which can cause damage over time. The type of underlayment used depends on the specific requirements of the project, such as climate conditions and the type of flooring that will be installed on top. Following the underlayment, the actual subfloor material is installed. For wooden subfloors, this typically involves laying down joists spaced at regular intervals, followed by the installation of plywood or oriented strand board (OSB) sheets. These sheets should be securely fastened to the joists using screws or nails to ensure a tight bond. For concrete subfloors, the process involves pouring and finishing the concrete to achieve a smooth surface. During installation, it is vital to check for any gaps or uneven areas and address them promptly. This may involve applying self-leveling compounds or patching materials to create a uniform surface. After the subfloor is installed, it should be inspected for any defects or imperfections before proceeding with the final flooring installation. Proper installation also includes ensuring that all joints and seams are sealed appropriately to prevent moisture intrusion and structural issues. Additionally, the subfloor should be allowed sufficient time to dry and cure before any further work is done on top of it. In summary, meticulous preparation and adherence to precise installation steps are key to creating a reliable and durable subfloor. By following these guidelines, homeowners and builders can ensure that their flooring system remains stable and functional over its lifespan, minimizing the need for costly repairs and maintenance down the line. This attention to detail not only enhances the overall quality of the flooring but also contributes to a safer and more comfortable living environment.
Common Issues and Solutions
When it comes to the installation and maintenance of a subfloor, several common issues can arise that may compromise the integrity and performance of the entire flooring system. One of the most prevalent problems is unevenness or sagging, which can occur due to improper installation, settling of the building, or water damage. To address this issue, it is crucial to ensure that the subfloor is levelled correctly during installation. This involves using self-levelling compounds or patching materials to fill in any gaps or depressions. Regular inspections are also essential to catch any signs of sagging early, allowing for prompt repairs before the problem escalates. Another significant concern is moisture-related issues. Excessive moisture can lead to warping, rotting, or mold growth on the subfloor, particularly in areas prone to high humidity like bathrooms and kitchens. To mitigate this risk, it is vital to ensure proper ventilation and drainage. Installing a vapour barrier between the subfloor and the finished flooring can help prevent moisture from seeping into the subfloor. Additionally, using materials resistant to moisture such as cement-based underlayment or waterproof membranes can provide an extra layer of protection. Cracks in the subfloor are another common issue that can affect the stability of the flooring. These cracks often result from shrinkage or settlement over time. To solve this problem, it is advisable to fill the cracks with a suitable patching compound and then seal them to prevent further damage. For more extensive cracking, it may be necessary to resurface the entire subfloor. Furthermore, inadequate fastening can lead to creaking and movement of the subfloor, which can be both annoying and structurally problematic. Ensuring that all joists and plywood sheets are securely fastened during installation is critical. Regular checks on fasteners and tightening them as needed can prevent this issue from arising. Lastly, pest infestations such as termites or carpenter ants can weaken the structural integrity of the subfloor. Regular inspections for signs of pest activity are essential. If an infestation is detected, prompt treatment by a pest control professional is necessary to prevent further damage. In summary, addressing common issues such as unevenness, moisture problems, cracks, inadequate fastening, and pest infestations through proper installation techniques and regular maintenance is key to ensuring a durable and stable subfloor. By taking proactive steps to identify and resolve these issues promptly, homeowners can safeguard their flooring investment and maintain a safe and comfortable living environment.
Long-Term Maintenance Tips
**Long-Term Maintenance Tips** Ensuring the longevity and integrity of your subfloor requires consistent and meticulous maintenance. This involves a combination of regular inspections, proactive repairs, and preventive measures. Start by conducting periodic checks for signs of wear, such as cracks, unevenness, or water damage. Addressing these issues promptly can prevent minor problems from escalating into major structural concerns. For instance, if you notice any cracks or gaps, seal them immediately with appropriate sealants to prevent moisture intrusion and pest infestation. Regular cleaning is also crucial. Sweep or vacuum the subfloor regularly to remove debris and dust that can accumulate and cause damage over time. In areas prone to moisture, such as bathrooms or kitchens, ensure that the subfloor is properly sealed and consider using waterproofing materials to protect against water seepage. Additionally, maintain a stable humidity level in your home to prevent warping or buckling of the subfloor material. Another key aspect is ensuring proper ventilation. Adequate airflow helps in drying out any moisture that might seep into the subfloor, reducing the risk of mold and rot. This is particularly important in crawl spaces or basements where moisture tends to accumulate. Installing vents or dehumidifiers can help maintain a dry environment. Furthermore, it's essential to monitor the weight distribution on your subfloor. Avoid placing heavy furniture or appliances in a way that could put uneven stress on the subfloor, which might lead to sagging or structural damage. If you're planning to install new flooring, ensure it is compatible with your existing subfloor material and follows the manufacturer's guidelines for installation. In addition to these measures, consider implementing a routine maintenance schedule. For example, every six months, inspect the subfloor for any signs of damage or wear. Use this opportunity to tighten any loose fasteners and apply additional coats of sealant if necessary. By being proactive and diligent in your maintenance efforts, you can significantly extend the lifespan of your subfloor and maintain the overall integrity of your home's structure. Moreover, staying informed about the specific needs of your subfloor material is vital. Different materials—such as plywood, oriented strand board (OSB), or concrete—have unique maintenance requirements. For instance, wood-based subfloors may require periodic treatment against pests and rot, while concrete subfloors might need periodic sealing to protect against moisture. Finally, consider the importance of professional inspections. While regular self-inspections are valuable, hiring a professional to inspect your subfloor every few years can help identify potential issues before they become major problems. These professionals can provide expert advice tailored to your specific situation and help you implement a comprehensive maintenance plan. By following these long-term maintenance tips, you can ensure that your subfloor remains in excellent condition, providing a solid foundation for your home's flooring and overall structural integrity. This proactive approach not only saves you from costly repairs down the line but also enhances the safety and comfort of your living space.