What Is Mild Steel

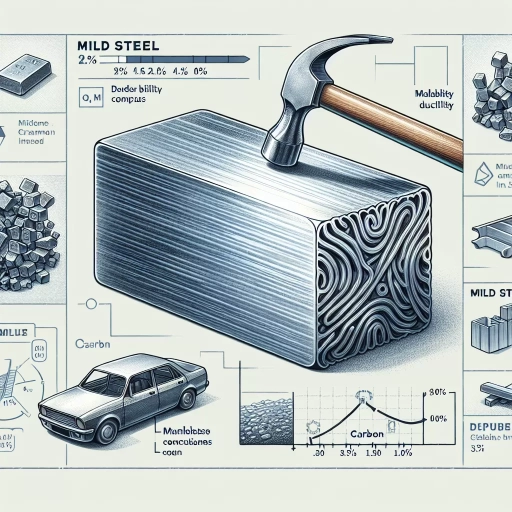
Mild steel, a versatile and widely used material, is a cornerstone in various industries due to its unique properties and applications. This article delves into the essence of mild steel, exploring its definition and composition, its diverse applications and uses, and the manufacturing process involved in its production. Understanding the fundamental characteristics of mild steel is crucial for appreciating its role in construction, automotive, and consumer goods sectors. The definition and composition of mild steel set the stage for its broad utility, as it is known for its high ductility and relatively low carbon content. By examining the applications and uses of mild steel, we can see how it contributes to everyday life, from building frames to car bodies. Additionally, the manufacturing process and production methods reveal the intricacies behind transforming raw materials into this indispensable metal. To begin, let's first define and explore the composition of mild steel, which forms the basis of its widespread adoption and versatility.
Definition and Composition of Mild Steel
Mild steel, a widely used material in construction and manufacturing, is characterized by its unique definition and composition. Understanding these aspects is crucial for appreciating its versatility and applications. This article delves into the core attributes of mild steel, focusing on three key areas: its chemical composition, physical properties, and how it compares to other types of steel. The chemical composition of mild steel, which includes a specific percentage of carbon and other elements, sets it apart from other steel types. This composition directly influences its physical properties, such as strength, ductility, and weldability. Additionally, comparing mild steel with other steel types highlights its distinct advantages and limitations. By examining these facets, we gain a comprehensive understanding of why mild steel remains a preferred choice in various industries. Let's begin by exploring the chemical composition of mild steel, which forms the foundation of its inherent qualities.
Chemical Composition
Mild steel, a widely used material in construction and manufacturing, is characterized by its specific chemical composition. The primary components of mild steel include iron, carbon, and small amounts of other elements. Iron constitutes the majority of the alloy, typically making up about 98-99% of its composition. Carbon is the second most significant element, usually present in amounts ranging from 0.05% to 0.25%. This low carbon content is what distinguishes mild steel from other types of steel and contributes to its ductility and weldability. Other elements such as manganese, silicon, and phosphorus are also present in smaller quantities, typically less than 1%. Manganese helps in deoxidizing the steel during the smelting process and improves its strength and hardness. Silicon also acts as a deoxidizer and enhances the steel's magnetic properties. Phosphorus, while present in trace amounts, can affect the steel's brittleness and is often kept to a minimum. The precise balance of these elements ensures that mild steel maintains its desirable properties, including high tensile strength, good formability, and resistance to corrosion when properly coated or treated. This balanced chemical composition makes mild steel an ideal choice for a wide range of applications, from structural beams and pipes to automotive parts and consumer goods. Understanding the chemical makeup of mild steel is crucial for engineers and manufacturers who need to select materials that meet specific performance requirements while being cost-effective and easy to work with.
Physical Properties
Mild steel, known for its versatility and widespread use in various industries, exhibits a range of physical properties that make it an ideal material for numerous applications. **Density** is one of the key physical properties, with mild steel typically having a density of approximately 7.9 grams per cubic centimeter. This density is relatively consistent across different grades of mild steel, making it predictable and reliable for engineering calculations. **Melting Point** is another crucial property; mild steel generally melts between 1400°C to 1450°C, which is lower than many other types of steel due to its lower carbon content. This lower melting point makes mild steel easier to weld and shape compared to higher-carbon steels. The **Thermal Conductivity** of mild steel is moderate, around 50 W/m-K, which means it can conduct heat reasonably well but not as efficiently as some metals like copper or aluminum. This property is important in applications where heat transfer is a consideration, such as in construction and automotive industries. **Magnetic Properties** are also significant; mild steel is ferromagnetic, meaning it is capable of being magnetized and is attracted to magnets. This property is utilized in various applications including electrical motors and generators. **Tensile Strength** and **Yield Strength** are critical mechanical properties that define the material's ability to withstand stress. Mild steel typically has a tensile strength ranging from 400 to 550 MPa and a yield strength between 200 to 300 MPa, depending on the specific grade and treatment. These values indicate that mild steel can support substantial loads before deforming or breaking, making it suitable for structural components in buildings, bridges, and machinery. The **Ductility** of mild steel is another important aspect; it can be significantly deformed without breaking, which allows for easy shaping and forming into various shapes and structures. This ductility also contributes to its ability to absorb impact without fracturing, enhancing its safety in dynamic environments. **Corrosion Resistance** is relatively low compared to stainless steel or other alloyed steels due to its low chromium content. However, mild steel can be protected against corrosion through various coatings or treatments such as galvanizing or painting. In terms of **Elasticity**, mild steel has a Young's Modulus of approximately 200 GPa, indicating its stiffness and resistance to deformation under elastic conditions. This property is essential for designing structures that need to maintain their shape under load. Overall, the combination of these physical properties—density, melting point, thermal conductivity, magnetic properties, tensile and yield strength, ductility, corrosion resistance, and elasticity—makes mild steel a highly versatile material suitable for a wide range of applications from construction and automotive manufacturing to consumer goods and machinery components. Understanding these properties is crucial for engineers and designers who need to select materials that meet specific performance criteria while balancing cost and practicality.
Comparison with Other Steel Types
Mild steel, known for its versatility and widespread use, stands out from other types of steel due to its unique composition and properties. When compared to other steel types, mild steel's defining characteristics become more apparent. For instance, **high-carbon steel** contains a higher percentage of carbon (typically between 0.6% and 1.4%), which makes it stronger and more durable but less ductile and more difficult to weld compared to mild steel. **Stainless steel**, on the other hand, is alloyed with chromium and sometimes nickel, providing excellent corrosion resistance but at a higher cost and with different mechanical properties. **Alloy steel**, which includes a variety of elements like manganese, silicon, and vanadium in addition to carbon, offers enhanced strength and toughness but often requires specialized processing techniques. In contrast, **mild steel** has a relatively low carbon content (usually around 0.1% to 0.3%), making it highly ductile and easy to form, weld, and machine. This lower carbon content also contributes to its lower strength compared to high-carbon or alloy steels but makes it an ideal choice for applications where formability is crucial, such as in construction materials like beams, pipes, and sheets. Additionally, mild steel is generally more affordable than other types of steel due to its simpler composition and manufacturing process. Another key distinction lies in the application areas: while **high-strength low-alloy (HSLA) steel** is used in demanding environments requiring high strength-to-weight ratios (e.g., automotive parts), **mild steel** is more commonly found in everyday structures like buildings, bridges, and consumer goods where cost-effectiveness and ease of fabrication are paramount. Furthermore, the magnetic properties of mild steel make it suitable for use in electrical applications such as motors and transformers. Overall, the balance of cost, ease of use, and adequate strength makes mild steel a preferred choice across various industries despite its limitations compared to other specialized steels. Its widespread availability and adaptability ensure that it remains a cornerstone material in modern engineering and construction projects.
Applications and Uses of Mild Steel
Mild steel, known for its versatility and affordability, is a cornerstone material in various industries. Its applications span across multiple sectors, each leveraging its unique properties to achieve specific goals. In the realm of construction and building, mild steel is used extensively due to its strength, durability, and ease of fabrication. It forms the backbone of structural frameworks, from beams and columns to reinforcement in concrete. The automotive industry also relies heavily on mild steel for manufacturing vehicle bodies and chassis, benefiting from its high tensile strength and cost-effectiveness. Additionally, consumer goods and appliances often incorporate mild steel components, such as in kitchen utensils, tools, and machinery, where its malleability and resistance to corrosion are invaluable. As we delve into the diverse uses of mild steel, we begin by examining its critical role in construction and building, where it has revolutionized the way structures are designed and built.
Construction and Building
In the realm of construction and building, mild steel plays a pivotal role due to its versatility, strength, and cost-effectiveness. This type of steel, characterized by its low carbon content (typically less than 0.3%), is widely used in various structural components such as beams, columns, and girders. Its high tensile strength and ductility make it an ideal material for constructing buildings, bridges, and other infrastructure projects. Mild steel is also preferred for its ease of welding and forming, which simplifies the fabrication process and reduces construction time. Additionally, its resistance to corrosion can be enhanced with appropriate coatings or treatments, making it suitable for both indoor and outdoor applications. In residential construction, mild steel is often used in framing, roofing, and flooring due to its ability to support heavy loads while maintaining structural integrity. Commercial buildings also benefit from mild steel's durability and flexibility, allowing for the creation of complex designs without compromising on safety or functionality. Furthermore, mild steel's recyclability aligns with modern sustainability goals, making it a preferred choice for environmentally conscious builders. Overall, the applications of mild steel in construction are diverse and extensive, contributing significantly to the efficiency, safety, and aesthetic appeal of modern buildings.
Automotive Industry
The automotive industry is a significant sector that heavily relies on mild steel for various applications due to its unique properties. Mild steel, known for its high strength-to-weight ratio, ductility, and affordability, is a preferred material in the production of vehicles. Here are some key ways mild steel is utilized in the automotive industry: 1. **Body and Chassis**: The structural integrity of a vehicle is largely dependent on mild steel. It is used extensively in the body and chassis of cars, trucks, and other vehicles. The body panels such as doors, hoods, and trunk lids are made from mild steel sheets that provide the necessary strength while keeping the weight manageable. 2. **Engine Components**: Mild steel is also used in engine components like engine blocks, cylinder heads, and crankshafts. Its ability to withstand high temperatures and stresses makes it an ideal choice for these critical parts. 3. **Suspension and Steering**: The suspension and steering systems of vehicles often incorporate mild steel parts such as axles, steering columns, and control arms. These components require the durability and flexibility that mild steel offers. 4. **Fasteners and Hardware**: From bolts and nuts to screws and rivets, mild steel is used in various fasteners that hold the vehicle together. Its tensile strength ensures that these fasteners can withstand the stresses of daily use. 5. **Safety Features**: In terms of safety, mild steel plays a crucial role in the construction of crash structures and safety cages within vehicles. Its ability to absorb impact energy helps protect occupants during collisions. 6. **Cost Efficiency**: One of the primary reasons for the widespread use of mild steel in the automotive industry is its cost-effectiveness. Compared to other metals like aluminum or high-strength steels, mild steel is relatively inexpensive while still offering excellent performance characteristics. 7. **Manufacturing Ease**: Mild steel is easy to form, weld, and machine, making it a convenient choice for mass production. This ease of manufacturing helps in reducing production time and costs, which are critical factors in the competitive automotive market. 8. **Recyclability**: Another significant advantage of using mild steel in vehicles is its recyclability. At the end of a vehicle's life cycle, the mild steel components can be easily recycled, reducing waste and conserving resources. In summary, mild steel's versatility, strength, and cost-effectiveness make it an indispensable material in the automotive industry. Its widespread use ensures that vehicles are both safe and economical, contributing significantly to the industry's efficiency and sustainability.
Consumer Goods and Appliances
Consumer goods and appliances are integral components of modern life, and mild steel plays a crucial role in their manufacturing. Mild steel, known for its strength, durability, and affordability, is widely used in the production of various household items. For instance, kitchen appliances such as refrigerators, ovens, and dishwashers often have mild steel components due to its excellent structural integrity and resistance to corrosion. The frames and outer casings of these appliances are frequently made from mild steel, providing a robust yet lightweight structure that can withstand daily use. Additionally, mild steel is used in the manufacture of furniture like beds, tables, and chairs due to its malleability and ease of fabrication. This versatility allows for the creation of intricate designs while maintaining the necessary strength and stability. In the realm of consumer electronics, mild steel is sometimes used in the construction of computer cases and other electronic enclosures where a balance between weight and strength is essential. Furthermore, tools and hardware such as wrenches, pliers, and screwdrivers often have mild steel components due to its high tensile strength and resistance to wear. The widespread use of mild steel in these applications underscores its importance as a material that combines performance with cost-effectiveness, making it an indispensable resource in the consumer goods and appliances industry. By leveraging the properties of mild steel, manufacturers can produce high-quality products that meet consumer demands for reliability and durability.
Manufacturing Process and Production
The manufacturing process and production are intricate and multifaceted, involving several critical stages that ensure the final product meets high standards of quality and functionality. At the heart of this process are the raw materials, which must be carefully extracted and prepared to serve as the foundation for subsequent steps. This article delves into three key aspects of manufacturing: Raw Materials and Extraction, Steel Production Techniques, and Quality Control and Testing. Understanding the sourcing and extraction of raw materials is essential, as it sets the stage for the entire production cycle. The techniques used in steel production are equally important, as they determine the strength, durability, and versatility of the final product. Finally, rigorous quality control and testing ensure that the manufactured goods adhere to industry standards and customer expectations. By examining these components, we can gain a comprehensive understanding of how manufacturing processes are optimized to produce high-quality products. Let's begin by exploring the first crucial step: Raw Materials and Extraction.
Raw Materials and Extraction
Raw materials and extraction are crucial components of the manufacturing process for mild steel, a widely used ferrous metal alloy. The primary raw materials required for mild steel production include iron ore, coal, and limestone. Iron ore, typically hematite (Fe2O3) or magnetite (Fe3O4), is extracted through open-pit or underground mining operations. Coal, which serves as a reducing agent and energy source, is obtained from coal mines. Limestone, used to remove impurities from the iron ore, is quarried from limestone deposits. The extraction process begins with the mining of these raw materials. Iron ore is extracted using heavy machinery and transported to processing facilities where it is crushed and ground into a fine powder. Coal is mined using both surface and underground methods, depending on the depth and quality of the coal seam. Limestone is quarried using drilling and blasting techniques followed by crushing and grinding. Once the raw materials are prepared, they are transported to steel production facilities. Here, they undergo various stages of processing. In the blast furnace, iron ore, coal, and limestone are combined and heated to extremely high temperatures to produce pig iron. This pig iron is then further refined in a basic oxygen furnace (BOF) or electric arc furnace (EAF) to produce steel. During this refining process, impurities are removed, and the carbon content is adjusted to achieve the desired properties of mild steel. The quality and purity of the raw materials significantly impact the final product's characteristics. For instance, high-grade iron ore with minimal impurities ensures better mechanical properties in the finished mild steel. Similarly, the quality of coal affects the efficiency of the reduction process and the overall energy consumption during production. In addition to these primary raw materials, other elements such as manganese, silicon, and phosphorus may be added in small quantities to enhance specific properties of mild steel. These additives can improve strength, ductility, and resistance to corrosion. The extraction and processing of raw materials for mild steel production also involve environmental considerations. Modern mining and extraction techniques aim to minimize environmental impact through practices such as reclamation of mined land and efficient use of resources. However, the extraction process still poses challenges related to pollution, land degradation, and resource depletion. In summary, the extraction of high-quality raw materials is essential for producing mild steel with desired mechanical properties. The careful selection and processing of iron ore, coal, limestone, and other additives ensure that the final product meets industry standards for strength, durability, and versatility. This meticulous approach underscores the importance of raw materials in the manufacturing process of mild steel.
Steel Production Techniques
Steel production techniques are pivotal in the manufacturing process, ensuring the quality and consistency of mild steel. The primary methods include the Basic Oxygen Furnace (BOF) and Electric Arc Furnace (EAF) processes. In the BOF method, molten iron from a blast furnace is mixed with scrap steel and oxygen in a large vessel, reducing impurities and achieving the desired chemical composition. This process is highly efficient and widely used for producing large quantities of steel. On the other hand, the EAF process involves melting scrap steel using an electric arc, which is particularly advantageous for producing specialty steels and recycling materials. Both methods can be followed by secondary refining processes such as ladle metallurgy, where additional elements are added to fine-tune the steel's properties. Continuous casting is another crucial step in steel production, where molten steel is solidified into a semi-finished product like a slab, bloom, or billet. This technique eliminates the need for ingot casting and rolling, significantly reducing production time and energy consumption. The semi-finished products are then further processed through rolling mills to achieve the desired shape and size. Rolling can be done at various temperatures; hot rolling is used for large-scale production of plates, sheets, and bars, while cold rolling is employed for producing thinner, more precise products with enhanced surface finish. Quality control is integral throughout these processes. Techniques such as spectroscopy and ultrasonic testing ensure that the chemical composition and physical properties of the steel meet industry standards. Additionally, advanced technologies like computer-controlled systems and automation enhance efficiency and accuracy in modern steel production facilities. Innovations in steel production also include the use of alternative raw materials and energy sources. For instance, direct reduced iron (DRI) can be used instead of molten iron from blast furnaces, offering environmental benefits by reducing greenhouse gas emissions. Furthermore, the integration of renewable energy sources into steel production facilities is becoming more prevalent, contributing to a more sustainable manufacturing process. Overall, the combination of these advanced techniques and technologies ensures that mild steel produced today is of high quality, versatile, and environmentally friendly, making it a cornerstone material in various industries ranging from construction to automotive manufacturing.
Quality Control and Testing
Quality control and testing are integral components of the manufacturing process and production, particularly in the context of mild steel production. These processes ensure that the final product meets the required standards, specifications, and safety regulations. Here’s how quality control and testing are crucial: **Raw Material Inspection**: The journey begins with the inspection of raw materials such as iron ore, coal, and limestone. Quality control teams verify the chemical composition and physical properties to ensure they align with the production requirements. **Process Monitoring**: During the manufacturing process, continuous monitoring is conducted at various stages. This includes checking the temperature, pressure, and chemical reactions in the blast furnace and basic oxygen furnace. Real-time data helps in making adjustments to maintain optimal conditions. **Sampling and Testing**: Regular sampling of the steel at different stages allows for comprehensive testing. Tests include tensile strength, yield strength, hardness, and chemical analysis to ensure the steel meets the specified grade and standards. **Non-Destructive Testing (NDT)**: Techniques like ultrasonic testing, radiography, and magnetic particle testing are used to detect internal defects without damaging the material. This ensures that any flaws are identified early, preventing potential failures in the final product. **Certification and Compliance**: The finished mild steel products undergo rigorous testing to comply with industry standards such as those set by ASTM (American Society for Testing and Materials) or ISO (International Organization for Standardization). Certification from recognized bodies adds credibility and assures customers of the product's quality. **Final Inspection**: Before dispatch, a thorough final inspection is conducted to check for any visible defects or irregularities. This includes visual examination as well as dimensional checks to ensure the product meets the customer's specifications. By integrating these quality control measures into the manufacturing process, producers can guarantee that their mild steel products are reliable, durable, and suitable for various applications such as construction, automotive, and consumer goods. This not only enhances customer satisfaction but also reduces the risk of product failures and associated costs. Effective quality control and testing are therefore essential for maintaining a high standard of production in the mild steel industry.