What Are Hockey Sticks Made Of

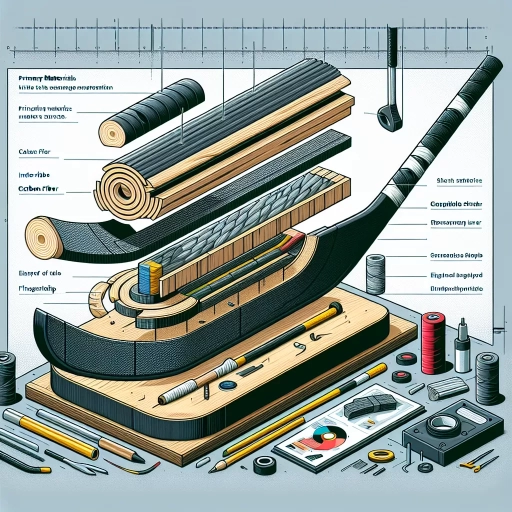
Hockey sticks, a crucial piece of equipment in the fast-paced and physically demanding sport of ice hockey, have undergone significant transformations over the years. From their humble beginnings to the high-tech marvels of today, the materials used in hockey sticks have evolved to enhance performance, durability, and player safety. This article delves into the fascinating journey of hockey stick materials, starting with the historical evolution that saw sticks transition from wooden branches to more sophisticated materials. We will explore how current materials such as carbon fiber, Kevlar, and advanced composites have revolutionized the game. Additionally, we will examine the intricate manufacturing process and rigorous quality control measures that ensure these sticks meet the highest standards of excellence. By understanding these aspects, we gain a deeper appreciation for the science and craftsmanship behind every hockey stick, setting the stage for a comprehensive look at their historical evolution. --- **Historical Evolution of Hockey Stick Materials**
Historical Evolution of Hockey Stick Materials
The evolution of hockey stick materials has been a transformative journey, reflecting advancements in technology and the relentless pursuit of performance. From the early days when wooden sticks were the norm, to the introduction of composite materials that revolutionized the game, and finally to the modern innovations that continue to push the boundaries of what is possible, each era has contributed significantly to the sport. In the early use of wood, hockey players relied on sturdy, handcrafted sticks that demanded skill and strength. The introduction of composite materials marked a significant shift, offering lighter, more durable, and versatile sticks that enhanced player performance. Today, modern innovations in materials have led to sticks that are not only stronger and lighter but also tailored to individual player preferences and styles. This article delves into the historical evolution of hockey stick materials, exploring these pivotal stages and how they have shaped the game into what it is today. By examining the transition from wood to composite materials and the latest advancements, we gain a deeper understanding of the historical evolution of hockey stick materials.
Early Use of Wood
The early use of wood in hockey sticks marks a significant chapter in the historical evolution of hockey stick materials. Wood, particularly ash, hickory, and birch, was the primary material for hockey sticks from the sport's inception in the mid-19th century until well into the 20th century. The choice of wood was driven by its availability, durability, and flexibility. Early hockey sticks were often crafted by hand, with skilled craftsmen carefully selecting and shaping the wood to create a stick that balanced strength and lightness. The wooden sticks were typically heavier and less consistent than modern materials but offered a unique feel and playability that many players cherished. Wood's natural properties made it an ideal choice for early hockey. Ash, with its high tensile strength and shock resistance, was a favorite among stick makers. Hickory, known for its hardness and toughness, provided additional durability against impacts on the ice. Birch, lighter and more flexible than ash or hickory, allowed for quicker stickhandling and better puck control. The craftsmanship involved in creating these sticks was meticulous; each piece of wood was carefully inspected for knots and other imperfections that could affect performance. The manufacturing process was labor-intensive and time-consuming. Sticks were often made from a single piece of wood, with the blade and shaft being part of a continuous piece rather than separate components. This construction method required precise cutting and shaping to ensure that the stick had the desired curve and balance. Despite these challenges, wooden sticks became synonymous with hockey, and their use spanned generations of players. However, as the game evolved and player skills improved, the limitations of wood became apparent. Wooden sticks were prone to cracking and breaking under stress, which could lead to injuries or interruptions during games. Additionally, the weight and inconsistency of wooden sticks made them less appealing as technology advanced. The transition from wood to other materials began in the mid-20th century with the introduction of fiberglass and aluminum sticks. These new materials offered greater durability and consistency but lacked the traditional feel of wood. Despite this shift, wooden sticks remain a nostalgic part of hockey's history and are still used today by some players who prefer their unique characteristics. In summary, the early use of wood in hockey sticks reflects a period where craftsmanship and natural materials defined the sport. While wood has largely been replaced by more modern materials, its legacy continues to influence the design and feel of contemporary hockey sticks, ensuring that the historical significance of wooden sticks remains an integral part of hockey's narrative.
Introduction of Composite Materials
The introduction of composite materials has revolutionized the manufacturing of hockey sticks, marking a significant milestone in the historical evolution of these essential sports equipment. Composite materials, which are engineered from two or more constituent materials with significantly different physical or chemical properties, offer a unique combination of strength, durability, and lightweight characteristics. This innovation began to gain traction in the late 20th century as advancements in materials science allowed for the development of high-performance composites. In hockey, the transition from traditional wood sticks to composite ones was driven by the need for enhanced performance and reduced weight. Early composite sticks were made from carbon fiber reinforced polymers (CFRP), which provided exceptional stiffness and strength-to-weight ratio compared to their wooden counterparts. These initial composites were often combined with other materials like Kevlar and fiberglass to improve impact resistance and durability. The integration of composite materials into hockey stick manufacturing has led to several key benefits. Firstly, composite sticks are significantly lighter, allowing players to generate more speed and power in their shots and passes. Secondly, these sticks exhibit superior durability; they are less prone to cracking and breaking under impact, extending their lifespan and reducing maintenance costs. Additionally, composite materials enable precise control over the stick's flex profile, allowing manufacturers to tailor the stick's stiffness and flexibility to meet specific player preferences. From a manufacturing perspective, the use of composites has also streamlined production processes. Modern composite sticks are often produced using advanced techniques such as pultrusion and resin transfer molding (RTM), which ensure consistent quality and reduce production time. These methods allow for intricate designs and complex geometries that would be difficult or impossible to achieve with traditional materials. The adoption of composite materials has not only transformed the performance characteristics of hockey sticks but has also influenced player technique and game strategy. Players can now execute shots with greater precision and power, contributing to a faster-paced and more dynamic game. Furthermore, the customization options available with composite sticks have enabled players to fine-tune their equipment to better suit their playing styles, enhancing overall performance. In conclusion, the introduction of composite materials has been a pivotal development in the history of hockey stick manufacturing. By offering unparalleled strength, durability, and customization options, these materials have elevated the sport by enhancing player performance and contributing to a more exciting and competitive game environment. As technology continues to evolve, it is likely that future innovations in composite materials will further redefine what is possible in hockey stick design and functionality.
Modern Innovations in Materials
Modern innovations in materials have revolutionized the construction of hockey sticks, significantly enhancing performance, durability, and player safety. The historical evolution from traditional wood to contemporary composites has been marked by several key advancements. One of the most significant innovations is the widespread adoption of carbon fiber, which offers exceptional strength-to-weight ratio and flexibility. Carbon fiber sticks are lighter, allowing for quicker stickhandling and more powerful shots, while their high tensile strength reduces the likelihood of breakage during intense gameplay. Additionally, advancements in resin technology have improved the bonding between carbon fibers, enhancing overall stick durability and resistance to impact. Another critical innovation is the integration of advanced polymers and hybrid materials. Manufacturers now blend different types of fibers such as Kevlar, basalt, and fiberglass with carbon fiber to create sticks that are not only strong but also resistant to wear and tear. These hybrid materials provide better vibration dampening, reducing the shock felt by players upon impact, thereby enhancing comfort and reducing fatigue. Furthermore, advancements in manufacturing processes like 3D printing and automated layup techniques have enabled precise control over material placement, allowing for customized stick designs tailored to individual player preferences and playing styles. Sustainability has also become a focus in modern material innovations. Eco-friendly materials such as bamboo and recycled carbon fibers are being explored as alternatives to traditional resources. These sustainable options not only reduce environmental impact but also offer unique performance characteristics that can appeal to players looking for a greener option without compromising on quality. Moreover, technological advancements in stick design have led to the development of smart sticks equipped with sensors that track performance metrics such as shot speed, accuracy, and stickhandling efficiency. These smart sticks provide real-time feedback to players and coaches, enabling data-driven training and performance optimization. In conclusion, modern innovations in materials have transformed hockey sticks into high-performance tools that combine strength, durability, and sustainability with advanced technology. These advancements continue to shape the sport by enhancing player performance while ensuring safety and environmental responsibility. As technology continues to evolve, it is likely that future hockey sticks will incorporate even more sophisticated materials and technologies, further revolutionizing the game of hockey.
Current Materials Used in Hockey Sticks
The evolution of hockey sticks has been a dynamic journey, driven by advancements in materials science and technology. Today, hockey sticks are crafted from a variety of high-performance materials, each contributing unique benefits to the game. At the forefront of this innovation is carbon fiber, renowned for its exceptional strength-to-weight ratio and durability, which significantly enhances player performance. Additionally, fiberglass and Kevlar play crucial roles in stick construction, offering flexibility and impact resistance that are vital for withstanding the rigors of the game. The integration of these materials has led to the development of blends and hybrid materials, further optimizing stick performance by combining the best attributes of each component. This article delves into the current materials used in hockey sticks, exploring the benefits of carbon fiber, the role of fiberglass and Kevlar, and the advantages of blended and hybrid materials. Understanding these modern materials provides a rich context for appreciating the historical evolution of hockey stick materials, which will be examined in greater detail later in this discussion.
Carbon Fiber and Its Benefits
Carbon fiber is a pivotal material in the construction of modern hockey sticks, offering a myriad of benefits that enhance performance, durability, and overall player experience. This lightweight yet incredibly strong material is composed of long chains of carbon atoms bonded together in a crystalline structure. The unique properties of carbon fiber make it an ideal choice for hockey sticks: it boasts an exceptionally high strength-to-weight ratio, meaning it provides robust support and stability without adding unnecessary bulk. This allows players to wield their sticks with greater agility and precision, enabling faster and more accurate shots. One of the most significant advantages of carbon fiber in hockey sticks is its resistance to fatigue and impact. Unlike traditional materials like wood or aluminum, carbon fiber maintains its structural integrity even after repeated use and collisions with the puck or other sticks. This durability ensures that the stick remains consistent in its performance over time, reducing the likelihood of breakage during critical moments in the game. Additionally, carbon fiber's low weight helps reduce player fatigue, allowing for longer periods of play without compromising on power or control. The flexibility of carbon fiber also plays a crucial role in hockey stick design. By carefully engineering the weave and orientation of the carbon fibers, manufacturers can create sticks with tailored flex profiles. This customization allows players to choose sticks that match their playing style—whether they prefer a stiffer stick for powerful slapshots or a more flexible one for better puck control. The precise control over flex also enhances the stick's ability to absorb shock from impacts, further protecting the player's hands and wrists. Moreover, carbon fiber's ability to be combined with other materials like Kevlar or fiberglass allows for the creation of hybrid sticks that leverage the strengths of multiple materials. These composite sticks can offer enhanced toughness and resistance to wear and tear while maintaining the lightweight and responsive characteristics of pure carbon fiber. This versatility in material composition enables manufacturers to cater to a wide range of player preferences and skill levels. In summary, carbon fiber's integration into hockey sticks has revolutionized the sport by providing players with tools that are stronger, lighter, and more durable. Its unique combination of strength, flexibility, and resistance to fatigue makes it an indispensable component in modern hockey equipment, allowing players to perform at their best while minimizing the risk of injury. As technology continues to evolve, it is likely that carbon fiber will remain a cornerstone material in the development of high-performance hockey sticks.
Role of Fiberglass and Kevlar
In the realm of modern hockey sticks, two materials stand out for their exceptional durability, strength, and lightweight properties: fiberglass and Kevlar. These advanced materials have revolutionized the construction of hockey sticks, offering players enhanced performance and safety. Fiberglass, known for its high tensile strength and resistance to impact, is often used in the shaft and blade of hockey sticks. Its flexibility allows for better stick handling and puck control, while its durability ensures that the stick can withstand the rigors of high-speed impacts and physical play. Additionally, fiberglass is relatively lightweight, enabling players to maintain speed and agility on the ice. Kevlar, a synthetic polymer renowned for its exceptional strength-to-weight ratio, is frequently integrated into the stick's construction to enhance its resilience. Kevlar's unique molecular structure provides superior resistance to cuts and abrasions, making it an ideal component for areas of the stick that are prone to wear and tear. When combined with fiberglass, Kevlar adds an extra layer of protection against cracks and breaks, extending the lifespan of the hockey stick. This composite material also helps in absorbing shock from puck impacts, reducing the risk of injury to the player's hands and wrists. The synergy between fiberglass and Kevlar in hockey sticks is a testament to innovative material science. By leveraging the strengths of both materials, manufacturers can create sticks that are not only robust but also tailored to specific playing styles. For instance, sticks with higher fiberglass content may offer more flexibility for players who prefer a softer feel, while those with more Kevlar may provide added durability for players who engage in more physical play. This versatility allows hockey players to choose sticks that align with their performance needs, whether they are professional athletes or recreational enthusiasts. Moreover, the use of fiberglass and Kevlar in hockey sticks has contributed significantly to player safety. The enhanced durability of these materials reduces the likelihood of stick breakage during games, minimizing the risk of injury from sharp edges or flying debris. This safety aspect is particularly crucial in a high-speed sport like hockey, where player safety is paramount. In summary, the role of fiberglass and Kevlar in modern hockey sticks is pivotal. These materials combine to offer a perfect blend of strength, flexibility, and durability, making them indispensable components in the construction of high-performance hockey sticks. As technology continues to evolve, it is likely that these materials will remain at the forefront of hockey stick innovation, ensuring that players have access to equipment that enhances their performance while prioritizing their safety.
Blends and Hybrid Materials
In the realm of hockey stick manufacturing, blends and hybrid materials have revolutionized the game by offering a perfect balance of strength, durability, and performance. These advanced composites are engineered to combine the best attributes of different materials, resulting in sticks that are lighter, more resilient, and capable of delivering superior power and control. At the heart of these innovations are carbon fiber, Kevlar, and various types of polymers. Carbon fiber, known for its exceptional strength-to-weight ratio, provides the necessary rigidity and stiffness required for powerful shots and precise stickhandling. Kevlar, renowned for its impact resistance and toughness, enhances the stick's durability by absorbing shocks and reducing the risk of breakage. By blending these materials with advanced polymers such as polyurethane or polyethylene, manufacturers can tailor the stick's flex profile, ensuring optimal feel and responsiveness. The integration of hybrid materials also allows for the creation of unique layups that can be customized to meet specific player preferences. For instance, a stick might feature a carbon fiber shaft for maximum stiffness while incorporating Kevlar in the blade to enhance puck control and resistance to wear. This versatility enables manufacturers to produce sticks that cater to various playing styles, from the aggressive forward who needs a stick that can withstand heavy impacts to the finesse player who requires precision and agility. Additionally, advancements in manufacturing techniques such as resin transfer molding (RTM) and vacuum bagging have improved the consistency and quality of these blends, ensuring that each stick meets high standards of performance and reliability. Moreover, the use of blends and hybrid materials has significantly reduced the weight of hockey sticks without compromising their strength. This reduction in weight allows players to generate more speed and agility on the ice, contributing to faster breakaways and quicker passes. The enhanced durability also means that sticks last longer, reducing maintenance costs and minimizing downtime due to equipment failure. Overall, the incorporation of blends and hybrid materials into hockey stick design represents a significant leap forward in technology, offering players a competitive edge through improved performance, durability, and customization options. As the sport continues to evolve, it is likely that these advanced composites will play an increasingly crucial role in shaping the future of hockey equipment.
Manufacturing Process and Quality Control
In the realm of modern manufacturing, the integration of advanced processes and stringent quality control measures is paramount for producing high-quality products. This article delves into the critical phases that define the manufacturing process, ensuring that final products meet or exceed industry standards. We begin by examining the **Design and Prototyping Phase**, where innovative ideas are translated into tangible prototypes, laying the groundwork for successful production. Next, we explore **Production Techniques and Technologies**, highlighting the cutting-edge methods and tools that enable efficient and precise manufacturing. Finally, we discuss **Testing and Quality Assurance**, emphasizing the rigorous checks and balances that guarantee product reliability and performance. By understanding these interconnected stages, manufacturers can optimize their workflows, enhance product quality, and maintain a competitive edge. This comprehensive approach to manufacturing is akin to the historical evolution of hockey stick materials, where advancements in design, production, and testing have transformed the sport, illustrating the universal importance of quality and innovation in any field.
Design and Prototyping Phase
In the context of manufacturing hockey sticks, the Design and Prototyping Phase is a critical juncture that sets the stage for both the production process and the eventual quality control measures. This phase involves a meticulous blend of creativity, technical expertise, and iterative refinement. It begins with conceptual design, where designers use computer-aided design (CAD) software to create detailed models of the hockey stick. These designs are informed by market research, player feedback, and advancements in materials science. Once the initial design is complete, prototyping takes center stage. Prototypes are created using various materials such as carbon fiber, Kevlar, and wood to test their durability, weight distribution, and overall performance. This stage is crucial as it allows manufacturers to identify potential flaws and make necessary adjustments before moving into mass production. For instance, impact testing and flexural strength tests are conducted to ensure that the stick can withstand the rigors of the game without compromising on performance. The iterative process of prototyping involves continuous feedback loops between designers, engineers, and professional players. This collaboration ensures that the final product meets both technical specifications and user expectations. Advanced technologies like 3D printing may also be employed during this phase to quickly produce and test multiple iterations of the design. Effective design and prototyping not only enhance the quality of the final product but also streamline the manufacturing process. By identifying and resolving issues early on, manufacturers can avoid costly reworks during production, thereby improving efficiency and reducing waste. Additionally, a well-designed prototype serves as a blueprint for quality control checks later in the process, ensuring that every stick produced adheres to stringent standards. In summary, the Design and Prototyping Phase is pivotal in the manufacturing of hockey sticks. It combines innovative design with rigorous testing to produce a high-quality product that meets both performance and safety standards. This meticulous approach lays the groundwork for a seamless transition into the manufacturing process while ensuring that quality control measures are robust and effective. By investing time and resources into this phase, manufacturers can deliver hockey sticks that are not only durable but also optimized for player performance.
Production Techniques and Technologies
In the realm of hockey stick manufacturing, production techniques and technologies play a pivotal role in ensuring both performance and durability. Modern hockey sticks are crafted using advanced materials and sophisticated processes that combine traditional craftsmanship with cutting-edge technology. One of the key techniques is the use of composite materials, primarily carbon fiber, Kevlar, and fiberglass. These materials are woven together in specific patterns to achieve optimal strength, flexibility, and weight distribution. The manufacturing process often begins with the creation of a pre-preg, where fibers are impregnated with resin, which is then molded into the desired shape using high-pressure and high-temperature (HPHT) processes. This method ensures uniform consistency and enhances the stick's overall performance. Another critical aspect is the integration of advanced technologies such as 3D printing and computer-aided design (CAD). These tools allow manufacturers to design intricate geometries and customize sticks to meet individual player preferences. For instance, 3D printing can be used to create complex internal structures that improve the stick's balance and feel. Additionally, CAD software enables precise control over the manufacturing process, allowing for minute adjustments in dimensions and material distribution to optimize performance characteristics like flex, torque, and impact resistance. Quality control is also a stringent part of the production process. Manufacturers employ various testing protocols to ensure that each stick meets rigorous standards. This includes impact testing, where sticks are subjected to repeated blows to assess durability; flex testing, which measures the stick's ability to absorb and release energy; and weight testing, ensuring that the stick meets specific weight requirements. Furthermore, visual inspections are conducted to check for any defects or irregularities in the material or construction. The use of automation and robotics has also revolutionized the manufacturing process. Automated systems can handle tasks such as cutting, shaping, and assembling components with high precision and speed, reducing human error and increasing efficiency. This not only improves the consistency of the final product but also allows for faster production times, enabling manufacturers to meet high demand without compromising on quality. In summary, the production techniques and technologies used in hockey stick manufacturing are highly sophisticated and multifaceted. By leveraging advanced materials, cutting-edge technologies, and rigorous quality control measures, manufacturers can produce hockey sticks that are both high-performance and durable. These advancements have significantly enhanced the game of hockey by providing players with tools that are tailored to their needs and capable of withstanding the intense demands of the sport.
Testing and Quality Assurance
In the manufacturing process of hockey sticks, Testing and Quality Assurance play pivotal roles in ensuring the final product meets stringent performance and safety standards. This critical phase involves a series of rigorous tests designed to evaluate the stick's durability, flexibility, and overall functionality. Manufacturers employ various methods to assess the stick's structural integrity, including impact testing where the stick is subjected to repeated blows to simulate game conditions. Additionally, flex testing is conducted to measure how much the stick bends under load, ensuring it maintains its shape without compromising its strength. The blade of the stick is also scrutinized for its ability to withstand puck impacts without cracking or deforming excessively. Quality Assurance extends beyond physical tests; it encompasses meticulous inspections at every stage of production. From raw material selection to the final assembly, each component is scrutinized for defects or inconsistencies. For instance, the carbon fiber used in high-end sticks is inspected for any imperfections that could affect its tensile strength. Similarly, the bonding process between different materials is closely monitored to ensure a seamless integration that enhances the stick's performance and longevity. Moreover, manufacturers often conduct environmental testing to simulate real-world conditions such as extreme temperatures and humidity levels. This helps in identifying any potential weaknesses that might arise during actual use on the ice. User feedback is also integral to the Quality Assurance process; manufacturers gather data from professional players and amateur enthusiasts alike to identify areas for improvement and make necessary adjustments. The integration of advanced technologies like computer-aided design (CAD) and 3D printing further enhances the testing and quality assurance processes. These tools allow for precise prototyping and rapid iteration, enabling manufacturers to refine their designs more efficiently. Furthermore, automated testing systems can perform repetitive tests with high accuracy, reducing human error and increasing the reliability of the results. Ultimately, the rigorous testing and quality assurance protocols ensure that hockey sticks not only meet but exceed industry standards. This commitment to excellence translates into sticks that are both durable and high-performing, providing players with the confidence they need to perform at their best on the ice. By combining cutting-edge technology with meticulous attention to detail, manufacturers can produce hockey sticks that are as reliable as they are effective, making them an indispensable part of any hockey player's arsenal.