What Is A Grinder

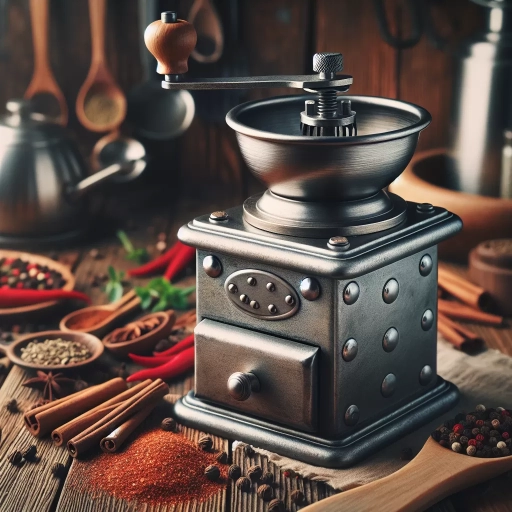
A grinder is a versatile and essential tool in various industries, including construction, manufacturing, and culinary arts. This multifaceted device is designed to perform a range of tasks, from shaping and smoothing materials to grinding and polishing surfaces. To fully understand the significance and functionality of grinders, it is crucial to delve into their definition and types, components and mechanisms, and applications and uses. Starting with the **Definition and Types of Grinders**, we will explore the different categories of grinders, such as angle grinders, bench grinders, and die grinders, each tailored for specific tasks. This foundational knowledge sets the stage for understanding how these tools operate and their diverse applications. By examining the **Components and Mechanisms of Grinders**, we can appreciate the intricate design and engineering that goes into these machines, enabling them to efficiently handle various materials. Finally, **Applications and Uses of Grinders** will highlight how these tools are integral in different sectors, from heavy-duty industrial processes to precise craftsmanship. Understanding these aspects will provide a comprehensive view of what a grinder is and why it remains an indispensable tool across multiple disciplines. Let's begin by defining and categorizing the different types of grinders.
Definition and Types of Grinders
Grinders are versatile tools that play a crucial role in various industries, from construction and manufacturing to culinary arts. Understanding the definition and types of grinders is essential for selecting the right tool for specific tasks. This article delves into the comprehensive world of grinders, starting with an **Overview of Grinder Terminology**, which clarifies the key terms and concepts associated with these tools. It then proceeds to **Classification of Grinders by Function**, where we explore how different grinders are categorized based on their primary uses. Finally, we examine **Specialized Grinder Types**, highlighting unique and niche grinders designed for specific applications. By grasping these foundational aspects, readers will gain a deeper appreciation for the diversity and utility of grinders. Let's begin by exploring the fundamental language and concepts that underpin our understanding of grinders in the **Overview of Grinder Terminology**.
Overview of Grinder Terminology
In the realm of grinding machinery, understanding the terminology is crucial for effective communication and operation. Here’s an overview of key grinder terminology that complements the definition and types of grinders: **Grinder Types**: Grinders are categorized based on their function and design. **Surface Grinders** are used to grind flat surfaces, while **Cylindrical Grinders** handle cylindrical parts. **Centerless Grinders** grind cylindrical parts without using centers, and **Internal Grinders** are designed for grinding internal surfaces of workpieces. **Bench Grinders** are versatile tools mounted on a bench for various grinding tasks, and **Angle Grinders** are handheld devices used for grinding, cutting, and polishing. **Grinding Wheels**: These are the abrasive components that perform the actual grinding. **Coarse Grit** wheels are used for heavy stock removal, while **Fine Grit** wheels are for finishing and polishing. The **Bond Type** (vitrified, resinoid, or rubber) and **Abrasive Material** (aluminum oxide, silicon carbide) determine the wheel's durability and effectiveness. **Grinding Operations**: Key operations include **Rough Grinding**, which involves removing large amounts of material, and **Finish Grinding**, aimed at achieving precise dimensions and surface finish. **Through-Feed Grinding** involves continuous feeding of the workpiece through the grinder, whereas **In-Feed Grinding** involves intermittent feeding. **Machine Components**: Understanding the components is essential. The **Spindle** holds the grinding wheel, and the **Chuck** or **Mandrel** secures the workpiece. The **Table** or **Bed** supports the workpiece during grinding, and **Coolant Systems** help in maintaining optimal temperatures. **Safety and Maintenance**: Proper **Guarding** of the grinding wheel is critical for safety. Regular **Wheel Dressing** ensures the grinding wheel remains sharp and effective. **Balancing** the wheel prevents vibration, which can lead to poor surface finish or machine damage. **Precision and Tolerances**: Grinders are often used to achieve high precision. Terms like **Tolerance** (the acceptable deviation from a specified dimension) and **Surface Finish** (the texture of the ground surface) are crucial in determining the quality of the grind. By grasping these terms, users can better select, operate, and maintain grinders to achieve desired outcomes efficiently and safely. This foundational knowledge is essential for anyone working with grinding machinery, whether in manufacturing, maintenance, or other industrial settings.
Classification of Grinders by Function
Grinders, essential tools in various industries and households, are classified based on their specific functions to cater to diverse needs. **Surface Grinders** are designed to grind flat surfaces, ensuring precision and smoothness. They are commonly used in metalworking and manufacturing to achieve accurate dimensions and finishes. **Cylindrical Grinders** specialize in grinding cylindrical objects, such as rods and tubes, making them crucial for producing precision parts like engine components and gears. **Centerless Grinders** operate without the use of centers or spindles, allowing for continuous grinding of cylindrical parts without interruption, which is particularly beneficial for high-volume production. **Internal Grinders**, also known as ID grinders, focus on grinding the internal surfaces of holes and bores. These grinders are vital in industries where precise internal dimensions are required, such as in the production of engine blocks and hydraulic cylinders. **Universal Grinders** offer versatility by combining the capabilities of surface, cylindrical, and internal grinders, making them a valuable asset for workshops that need to handle a variety of grinding tasks. **Bench Grinders** are compact and mounted on a bench or pedestal, ideal for small-scale grinding operations and sharpening tools. They are widely used in workshops and garages for general-purpose grinding. **Angle Grinders**, also known as side grinders or disc grinders, are handheld tools that use a rotating disc to grind, cut, or polish materials. They are versatile and commonly used in construction, metal fabrication, and automotive repair. **Die Grinders**, another type of handheld grinder, are smaller and more precise than angle grinders, often used for detailed work such as grinding small parts or removing material from tight spaces. **Creep Feed Grinders** are specialized for heavy-duty grinding operations where large amounts of material need to be removed quickly and efficiently. These grinders are typically used in aerospace and automotive manufacturing for grinding complex shapes. Each type of grinder is engineered to perform specific tasks with precision and efficiency, making them indispensable in various sectors. Understanding the classification of grinders by function helps users select the right tool for their needs, ensuring optimal performance and safety. Whether it's for industrial production or DIY projects, selecting the appropriate grinder based on its intended function is crucial for achieving desired results.
Specialized Grinder Types
Specialized grinder types are designed to cater to specific needs and applications, offering enhanced performance and precision in various industries. **Surface Grinders**, for instance, are used to grind flat surfaces and achieve a high degree of accuracy. These grinders typically feature a rotating wheel that moves back and forth across the workpiece, ensuring uniformity and smoothness. **Cylindrical Grinders** specialize in grinding cylindrical parts such as rods, tubes, and other round components. They can be further divided into plain, universal, and centerless grinders, each serving distinct purposes like precision grinding of external surfaces or through-feed operations. **Tool and Cutter Grinders** are essential in the manufacturing sector for sharpening and reconditioning cutting tools. These grinders are highly versatile and can handle a wide range of tools, from drill bits to milling cutters, ensuring optimal cutting performance. **Bench Grinders**, often found in workshops and garages, are compact and versatile tools used for sharpening, polishing, and buffing small parts. They usually come with two wheels of different grits for various tasks. **Die Grinders**, also known as rotary tools or Dremel tools, are handheld devices that offer high-speed grinding capabilities for detailed work. They are commonly used in metalworking, woodworking, and other precision tasks where small areas need to be ground or polished. **Angle Grinders**, also known as side grinders or disc grinders, are powerful handheld tools that use a rotating disc to grind, cut, or polish metal and other materials. They are widely used in construction, automotive repair, and metal fabrication. **Creep Feed Grinders** are specialized for heavy-duty applications where large amounts of material need to be removed quickly. These grinders use a slow feed rate but apply significant pressure to achieve deep cuts efficiently. **Gear Grinders** are designed specifically for grinding gears and other complex toothed components. They ensure precise tooth geometry and surface finish, which is critical in applications requiring high torque and low noise levels. **Internal Grinders**, also known as ID grinders, focus on grinding internal surfaces such as bores and holes. These grinders are crucial in industries like aerospace and automotive where precise internal dimensions are necessary. **Jig Grinders** combine the capabilities of surface grinders with the precision of jig boring machines, allowing for intricate grinding operations on complex shapes and profiles. Each specialized grinder type is engineered to address specific challenges and requirements across various industries, ensuring that the grinding process is efficient, accurate, and tailored to the task at hand. By understanding the unique features and applications of these specialized grinders, users can select the right tool for their needs, thereby enhancing productivity and quality in their work.
Components and Mechanisms of Grinders
Grinders are versatile tools that play a crucial role in various industries, from construction and manufacturing to culinary arts. Understanding the components and mechanisms of grinders is essential for optimal performance, safety, and maintenance. This article delves into the key aspects of grinders, starting with an in-depth look at the **Key Parts and Their Functions**. Here, we will explore the critical components such as motors, blades, and gearboxes, and how they work together to achieve the desired grinding action. Additionally, we will compare **Mechanical vs. Electric Grinders**, highlighting their differences in terms of efficiency, cost, and application suitability. Finally, we will discuss **Safety Features and Precautions**, emphasizing the importance of proper usage and protective measures to prevent accidents. By understanding these fundamental aspects, users can maximize the effectiveness of their grinders while ensuring a safe working environment. Let's begin by examining the key parts and their functions, which form the backbone of any grinder's operation.
Key Parts and Their Functions
In the context of grinders, understanding the key parts and their functions is crucial for optimal performance and maintenance. A grinder, whether it be an angle grinder, bench grinder, or surface grinder, consists of several critical components that work in harmony to achieve the desired outcome. 1. **Motor**: The motor is the heart of any grinder, providing the power necessary to drive the grinding wheel or disc. It can be electric, pneumatic, or gasoline-powered, depending on the type of grinder. The motor's horsepower and RPM (revolutions per minute) determine the grinder's efficiency and capability. 2. **Grinding Wheel/Disc**: This is the most visible part of a grinder and comes in various types such as abrasive wheels, diamond blades, or sanding discs. Each type is designed for specific tasks like cutting, grinding, or polishing different materials. 3. **Spindle**: The spindle is a rotating shaft that holds the grinding wheel or disc in place. It must be durable and precisely aligned to ensure smooth operation and prevent vibration. 4. **Bearing**: Bearings support the spindle and allow it to rotate smoothly. High-quality bearings are essential for reducing friction and extending the lifespan of the grinder. 5. **Gearbox**: In some grinders, a gearbox is used to adjust the speed of the spindle. This allows for more versatility in handling different materials and tasks. 6. **Guard**: Safety guards protect users from flying debris and accidental contact with the grinding wheel. They are adjustable and can be removed for certain tasks but should always be used when possible. 7. **Handle**: The handle provides control and comfort during operation. Ergonomic design is important to reduce fatigue and improve precision. 8. **Switch/Trigger**: The switch or trigger mechanism controls the power supply to the motor. It must be reliable and easy to operate, often featuring safety features like lock-off switches to prevent accidental start-ups. 9. **Mounting System**: For bench grinders, a mounting system secures the grinder to a workbench or stand, ensuring stability during use. For handheld grinders, this might include clamps or brackets for attaching accessories. 10. **Cooling System**: Some grinders, especially those used for heavy-duty applications, may have a cooling system to prevent overheating. This could be as simple as air vents or as complex as liquid cooling systems. Understanding these key parts and their functions not only helps in selecting the right grinder for a specific task but also in maintaining and troubleshooting the equipment effectively. Proper care and maintenance of these components can significantly extend the lifespan of a grinder and ensure consistent performance over time.
Mechanical vs. Electric Grinders
When it comes to grinders, the choice between mechanical and electric models is crucial, as each type offers distinct advantages and disadvantages. **Mechanical Grinders**, often referred to as manual grinders, rely on human power to operate. These grinders use a handle or lever that the user must turn or press to grind materials. They are typically more affordable and require no electricity, making them ideal for remote or off-grid applications. Mechanical grinders are also quieter and produce less vibration compared to their electric counterparts, which can be beneficial in noise-sensitive environments. However, they demand more physical effort and time, limiting their efficiency for large-scale grinding tasks. On the other hand, **Electric Grinders** are powered by motors that significantly reduce the manual labor required. These grinders come in various forms, including bench grinders, angle grinders, and die grinders, each designed for specific tasks such as sharpening tools, cutting through metal, or polishing surfaces. Electric grinders offer higher speed and efficiency, allowing users to complete tasks much faster than with mechanical grinders. They are also more versatile, with adjustable speed settings and interchangeable attachments that enhance their functionality. However, electric grinders are generally more expensive to purchase and maintain, require a power source, and can be noisy and produce significant vibration. In terms of safety, both types have their considerations. Mechanical grinders are generally safer because they lack the risk of electrical shock and are less likely to cause accidents due to their slower operation speed. Electric grinders, while safer in terms of physical effort required, pose risks such as electrical shock if not used properly and can cause severe injuries if the user loses control or if the tool malfunctions. For **Components and Mechanisms**, mechanical grinders typically consist of a grinding wheel or stone attached to a shaft that is turned by a handle. The simplicity of these components makes them easier to maintain and repair. In contrast, electric grinders have more complex mechanisms involving motors, gearboxes, and control circuits. These components require regular maintenance to ensure optimal performance and longevity. In summary, the choice between mechanical and electric grinders depends on the specific needs of the user. For small-scale, low-frequency grinding tasks where manual effort is acceptable, mechanical grinders are a cost-effective and reliable option. For larger-scale projects or tasks requiring high speed and efficiency, electric grinders are the better choice despite their higher cost and maintenance requirements. Understanding the differences in these grinders helps users select the right tool for their needs, ensuring safety and efficiency in their work.
Safety Features and Precautions
When discussing the components and mechanisms of grinders, it is crucial to emphasize the importance of safety features and precautions. Grinders, whether they are handheld power tools or industrial machinery, pose significant risks if not used properly. Here are some key safety features and precautions that must be considered: 1. **Guarding**: One of the most critical safety features is the presence of guards. These guards protect users from flying debris and accidental contact with the grinding wheel or blade. Ensure that all guards are in place and securely fastened before operating the grinder. 2. **Personal Protective Equipment (PPE)**: Always wear appropriate PPE, including safety glasses or goggles, a dust mask, gloves, and a face shield. This protective gear helps prevent injuries from flying particles and reduces exposure to dust and noise. 3. **Proper Training**: Users should undergo thorough training on the safe operation of grinders. This includes understanding the correct handling techniques, how to change blades or wheels safely, and how to maintain the tool. 4. **Regular Maintenance**: Regular maintenance is essential to ensure the grinder remains in good working condition. Check for any damage or wear on the tool and its components before each use. Lubricate moving parts as recommended by the manufacturer. 5. **Work Area Safety**: Ensure the work area is clear of clutter and flammable materials. Keep a fire extinguisher nearby and avoid overreaching or working in awkward positions that could lead to loss of control. 6. **Electrical Safety**: For electric grinders, ensure that cords are not damaged and are kept away from water and heat sources. Use Ground Fault Circuit Interrupters (GFCIs) in wet or damp environments to prevent electrical shock. 7. **Ventilation**: Proper ventilation is vital when grinding materials that produce dust or fumes. Use a vacuum system or ensure good airflow in the work area to minimize inhalation risks. 8. **Emergency Procedures**: Establish clear emergency procedures, such as knowing how to stop the grinder quickly and having a first aid kit nearby. Familiarize yourself with the location of emergency exits and fire extinguishers. 9. **Compliance with Standards**: Ensure that all grinders and their components comply with relevant safety standards and regulations. This includes adherence to industry-specific guidelines and local laws. 10. **User Manuals**: Always refer to the user manual provided by the manufacturer for specific safety instructions tailored to the particular model of grinder being used. By adhering to these safety features and precautions, users can significantly reduce the risk of accidents and injuries associated with grinder operation, ensuring a safer working environment for everyone involved.
Applications and Uses of Grinders
Grinders are versatile tools that have become indispensable in various sectors due to their efficiency and precision. These machines are not limited to a single type of application; instead, they serve multiple purposes across different fields. In the industrial and commercial realm, grinders are crucial for heavy-duty tasks such as metal fabrication, construction, and manufacturing. They enable the smooth operation of production lines by ensuring materials are cut, polished, and shaped to exact specifications. Beyond industrial settings, grinders also play a significant role in home and DIY projects, allowing individuals to tackle tasks like tile cutting, woodwork, and other household repairs with ease. Additionally, specialized applications in various fields such as aerospace, automotive, and medical industries rely on grinders for precise and intricate work. This article will delve into these diverse applications, starting with the industrial and commercial uses of grinders, where their impact is most pronounced.
Industrial and Commercial Uses
Industrial and commercial uses of grinders are diverse and critical, reflecting their versatility and efficiency in various sectors. In manufacturing, grinders are essential for precision machining, enabling the production of high-quality components with tight tolerances. Surface grinders, for instance, are used to achieve flat surfaces on metal parts, while cylindrical grinders ensure precise dimensions on cylindrical objects. These machines are integral in the automotive industry for grinding engine components, gears, and other critical parts that require precise dimensions. In the aerospace sector, grinders play a crucial role in producing lightweight yet durable components. Here, they are often used in conjunction with advanced materials like titanium and composites. The precision grinding capabilities are crucial for ensuring the safety and performance of aircraft parts. In construction and civil engineering, grinders are used for preparing surfaces for painting or coating, removing old adhesives or coatings, and smoothing out concrete floors. Angle grinders and floor grinders are particularly useful in these applications due to their ability to handle heavy-duty tasks efficiently. The food processing industry also relies on grinders for various tasks such as grinding spices, nuts, and grains. Meat grinders are used extensively in butcher shops and meat processing plants to prepare ground meat products like sausages and burgers. Additionally, grinders find significant use in the pharmaceutical industry where they are employed to grind active ingredients into fine powders that can be easily mixed into formulations. This ensures uniformity and consistency in drug production. In the realm of maintenance and repair, grinders are indispensable tools for technicians. They are used for sharpening tools, cutting through metal pipes or bars, and polishing surfaces to remove rust or corrosion. This versatility makes them a staple in workshops across different industries. Overall, the industrial and commercial applications of grinders underscore their importance as precision tools that enhance productivity, quality, and safety across a wide range of sectors. Their ability to perform a variety of tasks with high accuracy makes them an essential component of modern manufacturing processes.
Home and DIY Projects
In the realm of home and DIY projects, grinders are indispensable tools that offer versatility and efficiency. Whether you're a seasoned DIY enthusiast or a beginner, grinders can help you tackle a wide range of tasks with precision and ease. For instance, angle grinders are perfect for cutting through metal pipes, concrete, or stone, making them essential for plumbing, masonry, and landscaping projects. Bench grinders, on the other hand, are ideal for sharpening tools and grinding down rough edges on metalwork, ensuring your tools remain in top condition. When it comes to woodworking, belt grinders can be used to smooth out wood surfaces, remove old finishes, and shape intricate designs. Grinders also play a crucial role in home renovation projects. For example, they can be used to remove old tile adhesive or grout from floors and walls, preparing the surface for new installations. In addition, grinders equipped with sanding attachments can help in smoothing out rough surfaces before painting or applying finishes. This not only saves time but also ensures a professional-grade finish. Moreover, grinders are invaluable for various automotive and motorcycle maintenance tasks. They can be used to clean rust off metal parts, grind down rough edges on engine components, and even polish chrome surfaces to a high shine. For those who enjoy crafting and making jewelry, rotary grinders with diamond bits can be used to shape and polish stones and metals with great accuracy. In terms of safety and convenience, modern grinders often come with advanced features such as variable speed controls, ergonomic designs, and dust collection systems. These features make it easier to handle different materials and reduce the risk of injury by providing better control over the grinding process. Overall, incorporating a grinder into your DIY toolkit can significantly enhance your ability to complete a variety of home and DIY projects efficiently and effectively. Whether you're working on a small craft project or a major home renovation, the right grinder can make all the difference in achieving professional-quality results.
Specialized Applications in Various Fields
In various fields, grinders have specialized applications that leverage their versatility and precision. **In Manufacturing and Metalworking**, grinders are crucial for surface finishing, deburring, and sharpening tools. For instance, cylindrical grinders are used to achieve precise dimensions on cylindrical parts, while surface grinders ensure flatness and smoothness on metal surfaces. **In Construction**, grinders are essential for preparing surfaces for painting or coating by removing old paint, rust, or concrete. Angle grinders, in particular, are handy for cutting through concrete, brick, or stone when renovating or demolishing structures. **In the Automotive Industry**, grinders play a key role in maintaining and repairing vehicles. They are used to smooth out rough edges on metal parts, polish chrome surfaces, and grind down rust spots before applying new coatings. **In the Medical Field**, specialized grinders are used in dental labs to shape and polish dental implants and prosthetics with high precision. Additionally, grinders are employed in surgical instrument manufacturing to ensure sharpness and cleanliness. **In the Food Industry**, grinders are vital for processing ingredients efficiently. Meat grinders, for example, are used to grind meat into various textures for sausages, burgers, and other products. Spice grinders help in pulverizing spices to the desired consistency without losing flavor. **In Aerospace**, precision grinders are used to manufacture critical components such as engine parts and turbine blades, where accuracy is paramount. **In the Arts and Crafts Sector**, grinders serve as versatile tools for sculptors and artisans. They are used to shape and smooth out materials like wood, stone, and metal for intricate designs and sculptures. **In Landscaping and Gardening**, grinders help in pruning trees and shrubs by grinding through thick branches efficiently. Overall, the specialized applications of grinders across these diverse fields underscore their importance as multifunctional tools that enhance productivity, precision, and quality in various industries. Whether it's refining metal surfaces or preparing food ingredients, grinders are indispensable assets that contribute significantly to the efficiency and effectiveness of numerous processes.