What Is A Self Tapping Screw

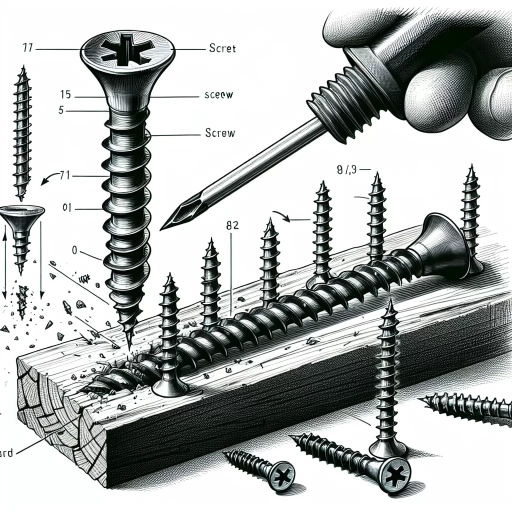
In the realm of fastening technology, self-tapping screws stand out as a versatile and efficient solution for various applications. These screws are designed to create their own threads in materials such as metal, plastic, and wood, eliminating the need for pre-drilled holes. The article delves into the intricacies of self-tapping screws, starting with their definition and purpose. Here, we explore how these screws are engineered to simplify the fastening process and enhance structural integrity. We then examine the diverse types and variations of self-tapping screws, each tailored to specific materials and uses. Finally, we discuss critical installation and usage considerations to ensure optimal performance and longevity. By understanding these aspects, users can leverage the full potential of self-tapping screws in their projects. Let's begin by defining and understanding the purpose of self-tapping screws.
Definition and Purpose of Self-Tapping Screws
Self-tapping screws are a versatile and essential component in various industries, including construction, automotive, and electronics. These screws are designed to create their own threads in materials such as metal, plastic, or wood, eliminating the need for pre-drilled holes. Understanding the definition and purpose of self-tapping screws is crucial for appreciating their utility. This article delves into the core aspects of self-tapping screws, starting with **What is a Self-Tapping Screw?**, where we explore the fundamental characteristics and types of these screws. We then examine **Primary Uses of Self-Tapping Screws**, highlighting their applications across different sectors. Finally, we discuss **Advantages Over Traditional Screws**, outlining the benefits that make self-tapping screws a preferred choice in many scenarios. By grasping these key points, readers will gain a comprehensive understanding of why self-tapping screws are indispensable in modern engineering and manufacturing. Let's begin by defining what a self-tapping screw is.
What is a Self-Tapping Screw?
A self-tapping screw is a type of screw that can create its own thread in the material it is being screwed into, eliminating the need for pre-drilling a hole or using a separate tapping tool. This innovative design makes self-tapping screws highly versatile and efficient for various applications. The primary purpose of self-tapping screws is to simplify the fastening process, especially in materials like plastic, metal, and wood, where traditional screws might not be effective. Self-tapping screws are engineered with a unique tip that acts as a drill bit, allowing them to penetrate the material and form threads as they are driven in. This feature is particularly beneficial in scenarios where precision and speed are crucial, such as in mass production environments or when working with materials that are difficult to pre-drill. For instance, in the construction industry, self-tapping screws are often used for assembling metal studs and drywall because they can quickly and securely fasten these materials without the need for additional tools. The design of self-tapping screws includes several key components that contribute to their functionality. The tip of the screw is typically tapered and has cutting edges that help to remove material as it penetrates. The threads on the screw are also specially designed to engage with the newly formed threads in the material, ensuring a secure hold. Additionally, some self-tapping screws come with a coarse thread pattern which enhances grip in softer materials. The use of self-tapping screws extends across various industries due to their convenience and reliability. In automotive manufacturing, they are used for assembling parts made from lightweight metals and plastics. In electronics, they are often employed for securing components within enclosures. Even in DIY projects, self-tapping screws are preferred because they save time and effort by eliminating the need for pre-drilling. In summary, self-tapping screws are designed to streamline the fastening process by creating their own threads in the material they are screwed into. Their unique design makes them indispensable in a wide range of applications, from industrial manufacturing to everyday DIY projects. By combining the functions of a drill bit and a screw, self-tapping screws offer a convenient, efficient, and reliable solution for securing materials quickly and securely.
Primary Uses of Self-Tapping Screws
Self-tapping screws are versatile fasteners designed to create their own threads in materials such as metal, plastic, and wood, eliminating the need for pre-drilling pilot holes. The primary uses of self-tapping screws include: 1. **Construction and Building**: Self-tapping screws are widely used in construction for assembling metal studs, roofing, and drywall. They provide a quick and efficient way to secure materials without the hassle of pre-drilling. 2. **Automotive Industry**: In the automotive sector, self-tapping screws are used for various applications including body panels, trim components, and engine parts. Their ability to form threads in thin metals makes them ideal for these purposes. 3. **Electronics and Appliances**: Self-tapping screws are commonly used in the assembly of electronic devices and household appliances. They offer a reliable method for securing components such as circuit boards, casings, and other internal parts. 4. **Furniture Assembly**: Many furniture pieces rely on self-tapping screws for assembly. They simplify the process by allowing users to attach parts directly without needing to drill pilot holes. 5. **Aerospace and Defense**: In aerospace and defense industries, self-tapping screws are used where high strength and reliability are critical. They are often employed in lightweight yet robust applications such as aircraft components and military equipment. 6. **Plastic and Composite Materials**: Self-tapping screws are particularly useful when working with plastics and composite materials because they can create threads without splitting the material, ensuring a secure hold. 7. **Temporary or Prototype Assemblies**: For temporary or prototype assemblies, self-tapping screws offer a convenient solution as they can be easily removed and reused without damaging the material. 8. **DIY Projects**: Homeowners and DIY enthusiasts frequently use self-tapping screws for various projects such as hanging shelves, assembling cabinets, and repairing furniture due to their ease of use and versatility. In summary, self-tapping screws are indispensable in a wide range of industries and applications due to their ability to form threads in various materials efficiently and reliably, making them a go-to choice for both professionals and hobbyists alike.
Advantages Over Traditional Screws
Self-tapping screws offer several significant advantages over traditional screws, making them a preferred choice in various applications. One of the primary benefits is their ability to create their own threads in the material they are being screwed into, eliminating the need for pre-drilled holes or tapping operations. This not only saves time but also reduces the risk of material damage and increases efficiency, particularly in high-volume production environments. Additionally, self-tapping screws provide better holding power compared to traditional screws because they create a more secure and tighter fit within the material, which is crucial for ensuring structural integrity and preventing loosening over time. Furthermore, these screws are versatile and can be used with a wide range of materials, including metals, plastics, and wood, making them highly adaptable for different projects. The reduced need for additional tools and steps in the assembly process also lowers overall costs and simplifies the manufacturing process. Moreover, self-tapping screws often require less torque to drive them into place, which can be beneficial when working with delicate or brittle materials that might be damaged by excessive force. Overall, the convenience, efficiency, and reliability of self-tapping screws make them an indispensable tool in many industries, from construction and automotive to electronics and consumer goods manufacturing.
Types and Variations of Self-Tapping Screws
Self-tapping screws are a versatile and essential component in various industries, including construction, automotive, and electronics. These screws offer the convenience of creating their own threads in materials, eliminating the need for pre-drilled holes. To fully understand the utility and diversity of self-tapping screws, it is crucial to explore their different types, the materials used in their construction, and their specialized applications. Different types of self-tapping screws cater to various needs, such as fine thread, coarse thread, and thread-forming screws, each designed for specific tasks and materials. The materials used in self-tapping screws also vary widely, including steel, stainless steel, and brass, which provide different levels of strength, corrosion resistance, and cost-effectiveness. Additionally, specialized self-tapping screws are designed for specific applications, such as drywall screws, deck screws, and roofing screws, which are tailored to meet the unique demands of their respective environments. Understanding these aspects is key to selecting the right self-tapping screw for any project. Let's begin by examining the different types of self-tapping screws, which form the foundation of their versatility and widespread use.
Different Types of Self-Tapping Screws
Self-tapping screws are versatile fasteners that eliminate the need for pre-drilling holes, making them a convenient choice for various applications. There are several types and variations of self-tapping screws, each designed to meet specific needs. **1. Thread-Forming Screws:** These screws create threads in the material they are driven into, typically used in plastics, wood, and thin metals. They have a coarse thread and a blunt point, which helps to displace material rather than cutting it. **2. Thread-Cutting Screws:** Unlike thread-forming screws, thread-cutting screws have a sharp cutting edge that removes material to create the thread. They are often used in thicker metals and harder materials where thread formation is not feasible. **3. Self-Drilling Screws:** These screws combine the functions of a drill bit and a self-tapping screw. They have a drill point at the tip, allowing them to penetrate and create holes in materials like metal, wood, or plastic before tapping threads. **4. Self-Piercing Screws:** Designed for use in thin materials such as sheet metal, self-piercing screws have a sharp point that pierces the material without creating a hole. They are commonly used in automotive and construction industries. **5. Tri-Wing and Spanner Screws:** These screws feature unique drive types (tri-wing or spanner) that provide added security against tampering or unauthorized removal. They are often used in applications requiring high security, such as electronics or machinery. **6. Fine and Coarse Thread Screws:** Depending on the application, self-tapping screws can have fine or coarse threads. Fine threads offer better resistance to pull-out forces but may require more torque to drive, while coarse threads are easier to drive but may not provide as much holding power. **7. Pan Head and Flat Head Screws:** The head type of self-tapping screws can vary; pan head screws have a rounded top with a flat underside, while flat head screws have a flat top and countersink into the material. The choice between these depends on the desired finish and application requirements. Each type of self-tapping screw is engineered to optimize performance in different materials and scenarios, ensuring that users can select the most appropriate fastener for their specific needs. Understanding these variations is crucial for achieving reliable and efficient fastening solutions across various industries.
Materials Used in Self-Tapping Screws
Self-tapping screws are engineered to create their own threads in pre-drilled holes, making them a versatile and efficient fastening solution. The materials used in the construction of self-tapping screws are crucial for their performance, durability, and compatibility with various applications. **Steel** is one of the most common materials due to its strength, cost-effectiveness, and availability. Within steel, there are several grades such as **carbon steel**, **alloy steel**, and **stainless steel**. Carbon steel is widely used for general-purpose applications due to its balance of strength and affordability. Alloy steel, which includes elements like chromium, molybdenum, or vanadium, offers enhanced strength and resistance to wear. Stainless steel, known for its corrosion resistance, is ideal for use in harsh environments where exposure to moisture or chemicals is a concern. **Brass** and **bronze** are also used for self-tapping screws, particularly in applications requiring good electrical conductivity and resistance to corrosion. These materials are often chosen for use in electrical components, marine hardware, and other scenarios where non-magnetic properties are beneficial. **Aluminum** self-tapping screws are lightweight and corrosion-resistant, making them suitable for aerospace, automotive, and other industries where weight reduction is critical. However, aluminum screws generally have lower tensile strength compared to steel or brass counterparts. **Plastics** like nylon or polypropylene are used in specialized applications where metal screws might be too heavy or could cause damage to the material being fastened. Plastic self-tapping screws are often used in consumer electronics, furniture, and other lightweight assemblies. The choice of material also influences the screw's finish and coating. For instance, **zinc plating** or **galvanizing** can be applied to steel screws to enhance corrosion resistance. **Chromium plating** or **nickel plating** can provide a durable, wear-resistant surface. In some cases, screws may be coated with **Teflon** or other non-stick materials to reduce friction during installation. In summary, the selection of material for self-tapping screws depends on the specific requirements of the application, including factors such as strength, corrosion resistance, electrical conductivity, weight, and cost. Each material offers unique advantages that make it suitable for a wide range of industries and uses. Understanding these differences is essential for choosing the right self-tapping screw for any given project.
Specialized Self-Tapping Screws for Specific Applications
Specialized self-tapping screws are designed to cater to specific applications where standard self-tapping screws may not suffice. These screws are engineered with unique features that enhance their performance in particular environments or materials. For instance, **plastic self-tapping screws** are optimized for use in plastic materials, often featuring coarse threads and a sharp point to ensure easy penetration and secure fastening without splitting the material. **Metal self-tapping screws**, on the other hand, are made from hardened steel or other alloys to provide superior strength and durability when fastening metal components. They may include features like a drill point or a pilot point to facilitate drilling and tapping in one step. In **woodworking applications**, specialized self-tapping screws often have a coarse thread pattern and a countersinking head to blend seamlessly with the wood surface. These screws may also be coated with a lubricant to reduce friction during insertion. **Drywall self-tapping screws** are another example, designed with bugle heads that countersink into drywall without creating a bulge on the surface. These screws typically have coarse threads to provide strong hold in the drywall material. For **electrical and electronic applications**, specialized self-tapping screws may be made from non-conductive materials or coated to prevent electrical conductivity. **Stainless steel self-tapping screws** are used in marine and chemical environments where corrosion resistance is crucial. These screws are resistant to rust and can withstand harsh conditions. In **automotive and aerospace industries**, high-strength self-tapping screws are used to ensure reliability and safety. These screws are often made from advanced materials like titanium or high-strength alloys and are designed to meet stringent specifications for load-bearing capacity and resistance to fatigue. Additionally, **security self-tapping screws** are designed with tamper-resistant features such as pin-in or spanner drive heads to prevent unauthorized removal. These are commonly used in public facilities or high-security installations where tampering could pose a risk. Overall, specialized self-tapping screws offer tailored solutions for various industries and applications, ensuring that the fastening needs are met with precision and reliability. By selecting the right type of self-tapping screw for a specific job, users can achieve stronger, more durable fastenings that meet the demands of their particular environment.
Installation and Usage Considerations
When considering the installation and usage of any system or product, several key factors must be taken into account to ensure a smooth and efficient process. First, a thorough understanding of the step-by-step installation guide is crucial to avoid any potential pitfalls and ensure that the system is set up correctly from the outset. This guide will walk you through each necessary step, providing clear instructions to help you navigate the installation process with ease. Additionally, being aware of common mistakes to avoid during installation can save time and resources by preventing unnecessary setbacks. Finally, knowing maintenance and replacement tips can extend the lifespan of your system and optimize its performance over time. By following these guidelines, you can ensure a successful installation and ongoing operation. To begin, let's delve into the step-by-step installation guide, which will provide you with the detailed instructions needed to get started.
Step-by-Step Installation Guide
### Step-by-Step Installation Guide When it comes to installing self-tapping screws, precision and the right technique are crucial to ensure a secure and durable fastening. Here is a step-by-step guide to help you through the process: 1. **Prepare the Material**: Ensure the material you are working with is clean and free from debris. For metals, this may involve cleaning off any rust or oil residue. For plastics or wood, make sure the surface is dry and free of dust. 2. **Choose the Right Screw**: Select a self-tapping screw that matches the thickness and type of material you are working with. Different materials require different screw types; for example, coarse threads are better for softer materials like wood, while fine threads are more suitable for harder materials like metal. 3. **Mark the Drilling Spot**: Use a marker or a small punch to mark where you want to drill the hole. This helps in maintaining accuracy and prevents the screw from slipping during installation. 4. **Drill a Pilot Hole (Optional)**: While self-tapping screws can create their own threads, drilling a pilot hole can sometimes be beneficial, especially in harder materials or when precision is key. The pilot hole should be slightly smaller than the screw's diameter. 5. **Align the Screw**: Place the self-tapping screw at the marked spot, ensuring it is aligned perpendicular to the surface. 6. **Start Drilling**: Begin drilling slowly and steadily. Apply gentle to moderate pressure depending on the material's hardness. For softer materials like wood, you may not need to apply much pressure, while harder materials like metal may require more force. 7. **Monitor Progress**: As you drill, monitor the screw's progress to ensure it is threading correctly and not slipping out of alignment. 8. **Tighten Securely**: Once the screw has started to thread into the material, continue tightening until it reaches the desired depth. Be careful not to overtighten, as this can damage the surrounding material or strip the threads. 9. **Check the Fit**: After installation, check that the screw is securely in place and that there are no signs of damage around the screw head or threads. 10. **Final Inspection**: Perform a final inspection to ensure all screws are properly seated and that there are no gaps or misalignments. By following these steps meticulously, you can ensure that your self-tapping screws are installed correctly, providing a strong and reliable fastening solution for your project. This method applies across various materials and applications, making self-tapping screws a versatile tool in many industries.
Common Mistakes to Avoid During Installation
When installing self-tapping screws, it is crucial to avoid common mistakes that can compromise the integrity of the assembly and lead to potential failures. One of the most significant errors is **insufficient material thickness**; ensuring that the material is thick enough to accommodate the screw's length without piercing through is essential. **Incorrect screw selection** is another critical mistake, as choosing a screw with the wrong thread type or size can result in poor engagement and reduced holding power. **Over-tightening** should be avoided, as it can strip the threads or damage the surrounding material, while **under-tightening** may not provide sufficient security. **Misalignment** of the screw with the intended hole can lead to uneven stress distribution and weaken the joint. It is also important to **avoid cross-threading**, which can occur if the screw is not aligned properly with the hole before starting to turn it. **Using the wrong drill bit size** can result in a hole that is either too small or too large for the screw, affecting its ability to self-tap effectively. Additionally, **not pre-drilling a pilot hole** in harder materials can cause the screw to slip or break. **Ignoring surface preparation** is another common mistake; ensuring that the surface is clean and free from debris or oils can significantly improve the screw's holding power. **Applying excessive force** during installation can damage both the screw and the material it is being inserted into. Furthermore, **not following manufacturer guidelines** for specific types of self-tapping screws can lead to suboptimal performance and potential failure. By being mindful of these common mistakes and taking steps to avoid them, users can ensure a secure and reliable installation of self-tapping screws. Proper installation practices not only enhance the structural integrity of the assembly but also extend its lifespan and performance. Always refer to the manufacturer's instructions and consider the specific requirements of your project to achieve optimal results.
Maintenance and Replacement Tips
When it comes to the long-term performance and durability of self-tapping screws, maintenance and replacement are crucial considerations. Regular inspection is key; check for signs of wear, corrosion, or damage. For screws exposed to harsh environments, such as moisture or extreme temperatures, apply a rust-inhibiting coating to prevent corrosion. Ensure that the surrounding material remains intact and free from cracks or splits that could compromise the screw's hold. Proper tightening techniques are essential to avoid stripping the screw head or damaging the surrounding material. Use the correct screwdriver or drill bit size to prevent slippage and maintain even torque distribution. If a screw becomes loose over time, re-tighten it carefully without over-tightening, which can lead to stripping. For replacement, select screws that match the original specifications in terms of material, thread type, and size to ensure compatibility and optimal performance. When replacing a self-tapping screw, remove the old one carefully to avoid damaging the surrounding material. If the hole has become enlarged due to wear, consider using a screw anchor or filler material before installing the new screw. In applications where screws are subject to heavy loads or vibrations, consider using screws with locking mechanisms such as nylon inserts or lock washers to prevent loosening over time. Additionally, maintaining accurate records of screw installations can help in identifying which screws may need more frequent inspections or replacements. Finally, always follow manufacturer guidelines for maintenance and replacement procedures specific to the type of self-tapping screw being used. This ensures that any warranties remain valid and that the screws continue to perform as intended throughout their lifespan. By adhering to these maintenance and replacement tips, you can extend the life of your self-tapping screws and ensure reliable performance in various applications.