What Are The Two Groups Of Hazards Used In Whmis Classification?

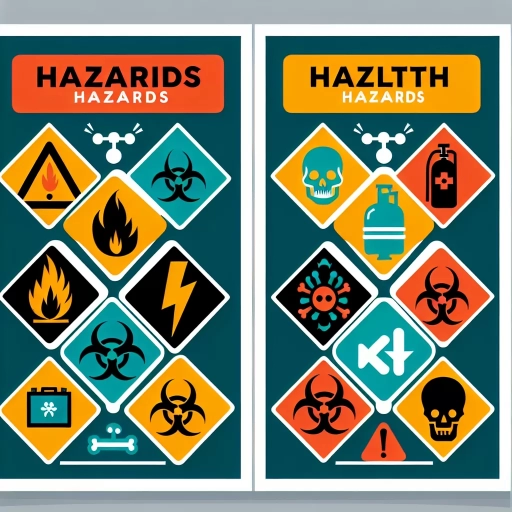
The Workplace Hazardous Materials Information System (WHMIS) is a critical framework designed to protect workers from the dangers associated with hazardous materials in the workplace. At its core, WHMIS categorizes hazards into two distinct groups: physical hazards and health hazards. Understanding these classifications is essential for ensuring workplace safety and compliance with regulatory standards. This article delves into the intricacies of WHMIS classification, starting with the foundational principles outlined in "Understanding WHMIS Classification Basics." It then explores the specific characteristics and implications of "Physical Hazards in WHMIS Classification," which include flammable liquids, gases, and reactive substances. Finally, it examines "Health Hazards in WHMIS Classification," which encompass toxic substances, carcinogens, and other health-threatening materials. By grasping these fundamental concepts, employers and employees can better navigate the complexities of hazardous material management, ultimately fostering a safer work environment. To begin, let's lay the groundwork by understanding the basics of WHMIS classification.
Understanding WHMIS Classification Basics
In the realm of workplace safety, understanding the Workplace Hazardous Materials Information System (WHMIS) is paramount. This comprehensive system is designed to protect workers from the dangers associated with hazardous materials. To delve into the intricacies of WHMIS, it is essential to grasp its fundamental components. First, we must define and understand the purpose of WHMIS, which revolves around providing critical information about hazardous substances to ensure safe handling and use. Next, exploring the historical context and evolution of WHMIS sheds light on how this system has adapted to meet changing safety standards and regulatory requirements. Finally, familiarizing oneself with the key principles and guidelines that underpin WHMIS is crucial for effective implementation. By examining these aspects, we can transition seamlessly into understanding the core of WHMIS: its classification basics. This foundational knowledge is vital for ensuring that workers are adequately informed and protected from the risks posed by hazardous materials, making it imperative to understand WHMIS classification basics thoroughly.
Definition and Purpose of WHMIS
**Understanding WHMIS Classification Basics: Definition and Purpose of WHMIS** The Workplace Hazardous Materials Information System (WHMIS) is a comprehensive safety standard designed to protect workers from the hazards associated with handling, storing, and using hazardous materials in the workplace. Established under Canadian law, WHMIS aims to ensure that workers are informed about the potential dangers of the chemicals they work with and how to handle them safely. The system is built around three key components: labels, safety data sheets (SDSs), and worker training. Labels provide immediate visual warnings and essential information about the hazards of a product, while SDSs offer detailed information on safe handling, use, storage, and emergency procedures. Worker training is crucial as it equips employees with the knowledge to recognize and manage hazards effectively. WHMIS categorizes hazardous materials into two primary groups: physical hazards and health hazards. Physical hazards include substances that can cause immediate harm through explosion, fire, or other physical means. Examples include flammable gases, oxidizing solids, and corrosive liquids. Health hazards, on the other hand, involve substances that can cause harm through prolonged exposure or contact, such as toxic substances, biohazardous materials, and carcinogens. This dual classification system helps workers understand the specific risks associated with each type of hazard and take appropriate precautions to mitigate those risks. The purpose of WHMIS extends beyond mere compliance; it is a proactive approach to workplace safety. By providing clear and consistent information about hazardous materials, WHMIS empowers workers to make informed decisions about their safety and the safety of their colleagues. It also fosters a culture of safety within organizations by ensuring that all stakeholders—from manufacturers to end-users—are aware of their responsibilities in handling hazardous materials safely. Furthermore, WHMIS aligns with international standards such as the Globally Harmonized System of Classification and Labelling of Chemicals (GHS), enhancing its relevance and effectiveness in a globalized workplace. In summary, WHMIS is an essential tool for workplace safety in Canada, providing a structured framework for identifying, communicating, and managing hazards associated with hazardous materials. Its dual classification system of physical and health hazards ensures that workers are well-equipped to handle these substances safely, thereby reducing the risk of accidents and promoting a healthier work environment. As part of understanding WHMIS classification basics, recognizing these two groups of hazards is fundamental to implementing effective safety protocols and ensuring compliance with regulatory requirements.
Historical Context and Evolution
The evolution of WHMIS (Workplace Hazardous Materials Information System) classification is deeply rooted in historical context, reflecting a gradual shift towards enhanced safety and regulatory compliance. Initially introduced in Canada in 1988, WHMIS was a response to the growing concern over workplace safety and the need for standardized communication about hazardous materials. This system was designed to ensure that workers, employers, and emergency responders had access to critical information about the hazards associated with chemicals in the workplace. Over the years, WHMIS has undergone significant transformations, particularly with the alignment of Canadian regulations with the Globally Harmonized System of Classification and Labelling of Chemicals (GHS) in 2015. This alignment introduced new classification criteria and labelling requirements, enhancing the clarity and consistency of hazard communication. The GHS integration expanded the scope of WHMIS to include more detailed categorization of physical, health, and environmental hazards. Under the current WHMIS 2015 framework, hazardous products are classified into two primary groups: physical hazards and health hazards. Physical hazards include substances that can cause immediate harm through physical means, such as flammable liquids, gases, and solids, as well as reactive substances that can explode or release harmful gases. Health hazards, on the other hand, encompass substances that can cause adverse health effects through exposure, including toxic substances, carcinogens, and mutagens. This dual classification system ensures that workers are informed about both immediate and long-term risks associated with handling various chemicals. The evolution of WHMIS has also seen advancements in labelling and safety data sheets (SDS). Labels now feature standardized pictograms and hazard statements that provide clear, concise information about the hazards of a product. SDSs offer more detailed information on safe handling practices, emergency procedures, and first aid measures. These enhancements have significantly improved workplace safety by ensuring that all stakeholders have access to accurate and consistent information about chemical hazards. In summary, the historical context and evolution of WHMIS reflect a continuous effort to enhance workplace safety through better hazard communication. The classification into physical and health hazards under WHMIS 2015 ensures comprehensive coverage of potential risks, aligning with international standards and fostering a safer work environment for all individuals handling hazardous materials. Understanding these classifications is crucial for effective implementation of WHMIS guidelines and for maintaining a safe and compliant workplace.
Key Principles and Guidelines
Understanding the key principles and guidelines of WHMIS (Workplace Hazardous Materials Information System) classification is crucial for ensuring a safe and compliant work environment. WHMIS categorizes hazardous materials into two primary groups: physical hazards and health hazards. **Physical hazards** include substances that can cause immediate harm due to their physical properties, such as flammability, explosiveness, or reactivity. For instance, flammable liquids and gases pose a significant risk of fire or explosion, while reactive materials can undergo dangerous chemical reactions under certain conditions. These hazards are often associated with immediate and severe consequences, making their identification and handling critical. On the other hand, **health hazards** involve substances that can cause adverse health effects through exposure, either acute or chronic. This category includes toxic substances, carcinogens, and mutagens, which can lead to serious health issues such as organ damage, cancer, or genetic mutations. Health hazards may not always be immediately apparent but can have long-term detrimental effects on workers' health. The classification of health hazards is based on the severity of the potential health effects and the likelihood of exposure. To ensure compliance with WHMIS regulations, employers must adhere to several key principles and guidelines. First, all hazardous materials must be properly labeled with Safety Data Sheets (SDSs) that provide detailed information about the substance's hazards, safe handling practices, and emergency procedures. Second, workers must receive comprehensive training on WHMIS classification, hazard recognition, and safe use of hazardous materials. This training should include understanding the Globally Harmonized System of Classification and Labelling of Chemicals (GHS) symbols and pictograms used on labels and SDSs. Additionally, workplaces must implement control measures to minimize exposure to hazardous substances. This includes using personal protective equipment (PPE), engineering controls such as ventilation systems, and administrative controls like work procedures and safety protocols. Employers are also required to maintain accurate records of hazardous materials used in the workplace and ensure that these records are accessible to all workers. By following these principles and guidelines, workplaces can significantly reduce the risks associated with hazardous materials. Effective WHMIS classification and training programs not only protect workers from immediate physical hazards but also safeguard their long-term health by mitigating exposure to harmful substances. This integrated approach ensures a safer working environment where workers are well-informed and equipped to handle hazardous materials responsibly.
Physical Hazards in WHMIS Classification
In the realm of workplace safety, understanding the classification of physical hazards is paramount. The Workplace Hazardous Materials Information System (WHMIS) plays a crucial role in this context by providing a standardized framework for identifying and managing hazardous materials. Physical hazards, a key component of WHMIS classification, encompass a variety of dangers that can pose significant risks to workers and the environment. This article delves into the critical aspects of physical hazards under WHMIS, starting with an exploration of the **Types of Physical Hazards**, such as flammable and explosive substances, which are inherently dangerous and require specific handling protocols. It also examines **Examples and Case Studies** to illustrate the practical implications and real-world consequences of these hazards. Additionally, the article outlines **Regulatory Requirements and Standards** that govern the handling and management of these substances, ensuring compliance and safety. By understanding these elements, readers will gain a comprehensive insight into the complexities of physical hazards within the WHMIS classification system, ultimately enhancing their grasp of **Understanding WHMIS Classification Basics**.
Types of Physical Hazards (e.g., Flammable, Explosive)
In the context of WHMIS (Workplace Hazardous Materials Information System) classification, physical hazards are a critical category that highlights the potential dangers associated with the physical properties of substances. These hazards can lead to severe injuries or fatalities if not properly managed. There are several key types of physical hazards that fall under this classification. **Flammable and Combustible Substances**: These substances can ignite and burn, posing significant fire risks. Flammable liquids, gases, and solids are highly susceptible to ignition, often requiring minimal energy to start a fire. Combustible materials, while less volatile, can still ignite under certain conditions, such as when heated or exposed to an ignition source. Proper storage, handling, and ventilation are essential to mitigate these risks. **Explosive Substances**: Explosives are highly reactive and can release a large amount of energy rapidly, causing devastating explosions. These substances are extremely hazardous and require stringent safety measures, including specialized storage facilities and strict handling protocols. Even minor mishandling can result in catastrophic consequences. **Oxidizing Substances**: These substances can cause or enhance the combustion of other materials, often leading to fires or explosions. Oxidizers can react violently with combustible materials, making them particularly dangerous in environments where flammable substances are present. Proper segregation and handling are crucial to prevent such reactions. **Corrosive to Metals**: While not typically considered a traditional physical hazard, corrosive substances that attack metals can lead to structural failures and equipment malfunctions, which in turn can create physical hazards. For instance, a corroded pipe might rupture, releasing hazardous materials or causing mechanical failures that could result in physical harm. **Pyrophoric Substances**: These substances ignite spontaneously in air at temperatures below 54°C (129°F), making them extremely hazardous. Handling pyrophoric materials requires specialized equipment and procedures to prevent accidental ignition. **Water-Reactive Substances**: When these substances come into contact with water, they can release flammable gases or generate heat, leading to fires or explosions. Handling these materials demands careful planning and execution to avoid any contact with moisture. Understanding and identifying these types of physical hazards is paramount for ensuring workplace safety. Employers must provide comprehensive training and implement robust safety protocols to manage these risks effectively. By doing so, they can significantly reduce the likelihood of accidents and protect their employees from the dangers associated with physical hazards. This knowledge is integral to the WHMIS classification system, which aims to categorize and communicate the hazards of workplace chemicals effectively.
Examples and Case Studies
In the context of WHMIS (Workplace Hazardous Materials Information System) classification, Physical Hazards represent a critical category that encompasses substances and materials that can cause harm through physical means, rather than chemical or biological interactions. To illustrate the significance and practical implications of these hazards, several examples and case studies are particularly instructive. One notable example involves **Flammable Liquids**. These substances are classified under Physical Hazards due to their ability to ignite and sustain combustion. A case study from a manufacturing plant highlights the importance of proper handling and storage. In this instance, a worker failed to follow safety protocols when transferring a flammable liquid, resulting in a spill that ignited due to an open flame nearby. The ensuing fire caused significant damage and injuries, underscoring the need for stringent adherence to WHMIS guidelines for flammable liquids. Another example is **Compressed Gases**, which are also categorized under Physical Hazards due to their potential for explosion or release of high-pressure gas. A case study from a construction site demonstrates the risks associated with these gases. Here, a compressed gas cylinder was improperly secured, leading to a sudden release of gas that propelled the cylinder like a missile, causing severe injury to nearby workers. This incident emphasizes the critical importance of proper handling, storage, and use of compressed gases as outlined in WHMIS standards. **Oxidizing Substances** are another group within Physical Hazards that merit attention. These substances can cause or enhance the combustion of other materials. A case study from a chemical plant illustrates the dangers: an oxidizing substance was stored in close proximity to combustible materials, leading to an uncontrolled fire when a spark ignited the mixture. The resulting blaze necessitated an emergency response and highlighted the necessity of segregating oxidizing substances from other hazardous materials as per WHMIS guidelines. Lastly, **Explosive Materials** are perhaps the most dramatic example of Physical Hazards in WHMIS classification. These materials can detonate or deflagrate under specific conditions, posing extreme risks to life and property. A case study from a mining operation underscores this point: improper handling of explosive materials led to an unintended detonation during transportation, resulting in fatalities and extensive damage. This tragic event reinforces the stringent safety measures and training required for handling explosive materials as mandated by WHMIS regulations. These examples and case studies collectively underscore the importance of understanding and adhering to WHMIS classifications for Physical Hazards. By recognizing the potential dangers associated with flammable liquids, compressed gases, oxidizing substances, and explosive materials, workplaces can implement effective safety protocols to mitigate risks and ensure a safer working environment for all employees.
Regulatory Requirements and Standards
Regulatory requirements and standards play a crucial role in the classification and management of physical hazards under the Workplace Hazardous Materials Information System (WHMIS). WHMIS, a Canadian standard, is designed to ensure that workers are informed about the hazards associated with the chemicals they use. When it comes to physical hazards, WHMIS categorizes them into two primary groups: compressed gases and oxidizing substances, and flammable and combustible substances. **Compressed Gases and Oxidizing Substances:** For compressed gases, regulatory requirements focus on the safe handling, storage, and transportation of these materials. Standards such as those set by the Canadian Standards Association (CSA) and Transport Canada dictate specific labeling, packaging, and safety protocols to mitigate risks like explosion or asphyxiation. Oxidizing substances, which can cause or intensify fires, are subject to stringent controls to prevent accidental ignition. Manufacturers must adhere to strict guidelines for the classification, labeling, and safety data sheets (SDS) of these substances, ensuring that workers are aware of the potential hazards and necessary precautions. **Flammable and Combustible Substances:** Flammable and combustible substances pose significant fire risks and are regulated under WHMIS to ensure their safe use. The National Fire Protection Association (NFPA) and CSA standards provide detailed guidelines for the classification of these substances based on their flash points and other properties. Regulatory bodies mandate that these substances be labeled with appropriate hazard symbols and warnings, and that SDSs include critical information on fire-fighting measures, storage conditions, and emergency procedures. Employers are also required to implement workplace controls such as ventilation systems, fire suppression equipment, and training programs to minimize the risk of fires. **Enforcement and Compliance:** The enforcement of these regulatory requirements is overseen by various federal and provincial agencies in Canada. Health Canada, for instance, is responsible for ensuring compliance with WHMIS regulations through inspections and audits. Non-compliance can result in significant fines and penalties, emphasizing the importance of adhering to these standards. Additionally, ongoing education and training programs are essential for maintaining a safe work environment, as they equip workers with the knowledge needed to handle hazardous materials safely. In summary, the regulatory requirements and standards for physical hazards under WHMIS are comprehensive and multifaceted. By adhering to these guidelines, employers can significantly reduce the risks associated with compressed gases, oxidizing substances, flammable liquids, and combustible materials. This not only protects workers but also ensures compliance with legal mandates, contributing to a safer and more responsible workplace environment.
Health Hazards in WHMIS Classification
In the realm of workplace safety, the Workplace Hazardous Materials Information System (WHMIS) plays a crucial role in protecting workers from the dangers posed by hazardous materials. One of the most critical aspects of WHMIS is the classification of health hazards, which helps in identifying and managing risks associated with toxic and irritant substances. This article delves into the key components of health hazards under WHMIS, starting with an exploration of the **Types of Health Hazards**, such as toxic and irritant substances, to understand their specific risks. It then transitions to **Risk Assessment and Mitigation Strategies**, outlining how to evaluate and reduce the dangers these hazards present. Finally, it discusses **Labeling and Safety Data Sheets (SDS) Requirements**, highlighting the importance of proper labeling and documentation in ensuring worker safety. By understanding these elements, readers will gain a comprehensive insight into the health hazards classified under WHMIS, ultimately leading to a deeper appreciation of **Understanding WHMIS Classification Basics**.
Types of Health Hazards (e.g., Toxic, Irritant)
In the context of WHMIS (Workplace Hazardous Materials Information System) classification, health hazards are categorized into two primary groups: toxic and irritant. Understanding these categories is crucial for ensuring workplace safety and proper handling of hazardous materials. **Toxic Health Hazards** involve substances that can cause harm or death if inhaled, ingested, or absorbed through the skin. These substances can affect various bodily systems, including the nervous, reproductive, and immune systems. Toxic health hazards are further divided into acute and chronic effects. Acute toxicity refers to immediate harm caused by a single exposure, such as poisoning from ingesting a toxic substance. Chronic toxicity, on the other hand, results from prolonged or repeated exposure over time, leading to conditions like cancer or organ damage. Examples of toxic substances include pesticides, heavy metals like lead and mercury, and certain industrial chemicals. **Irritant Health Hazards** are substances that cause inflammation or irritation upon contact with the skin, eyes, or respiratory tract. Unlike toxic substances, irritants do not necessarily cause systemic harm but can still lead to significant discomfort and injury. Irritants can be further classified as skin irritants, eye irritants, or respiratory tract irritants. For instance, strong acids and bases are common skin and eye irritants that can cause burns upon contact. Respiratory tract irritants, such as ammonia gas or chlorine gas, can lead to coughing, wheezing, and shortness of breath. Proper protective equipment and ventilation are essential when handling these substances to prevent irritation and potential long-term health issues. Both types of health hazards necessitate specific safety protocols and personal protective equipment (PPE) to mitigate risks. Employers must ensure that workers are trained on the safe handling, storage, and disposal of these substances. Labels and safety data sheets (SDS) provided under WHMIS guidelines help identify the specific hazards associated with each substance, enabling workers to take appropriate precautions. By recognizing and understanding the differences between toxic and irritant health hazards, workplaces can implement targeted strategies to protect employee health and prevent accidents. This dual categorization in WHMIS classification underscores the importance of a comprehensive approach to managing workplace hazards effectively.
Risk Assessment and Mitigation Strategies
Risk assessment and mitigation strategies are crucial components in managing health hazards within the Workplace Hazardous Materials Information System (WHMIS) classification. When dealing with hazardous materials, it is essential to identify potential risks and implement effective measures to mitigate them. The process begins with a thorough risk assessment, which involves evaluating the likelihood and potential impact of exposure to hazardous substances. This includes considering factors such as the chemical properties of the substance, its handling and storage procedures, and the protective measures in place. Once risks are identified, mitigation strategies can be developed to minimize or eliminate these hazards. One key strategy is the use of personal protective equipment (PPE), such as gloves, masks, and eye protection, which can significantly reduce exposure to harmful substances. Another critical approach is proper ventilation and engineering controls, such as fume hoods and exhaust systems, which help to remove hazardous vapors from the work environment. Training and education also play a vital role in risk mitigation. Ensuring that workers are well-informed about the hazards associated with specific chemicals and know how to handle them safely can prevent accidents. Regular safety drills and emergency response plans further enhance preparedness and response capabilities. Additionally, administrative controls such as safe work procedures, labeling requirements, and material safety data sheets (MSDS) provide essential information for safe handling practices. These documents outline the necessary precautions and emergency procedures for each hazardous material. In the context of WHMIS classification, understanding these risk assessment and mitigation strategies is particularly important because they directly impact how health hazards are categorized and communicated. The two main groups of hazards in WHMIS classification—physical hazards and health hazards—require distinct risk assessments and mitigation approaches. For health hazards specifically, understanding the toxicological properties of substances allows for targeted mitigation strategies that protect workers from long-term health effects. By integrating these risk assessment and mitigation strategies into daily operations, workplaces can significantly reduce the risks associated with hazardous materials, ensuring a safer environment for all employees. This holistic approach not only complies with regulatory requirements but also fosters a culture of safety and responsibility within the organization. Ultimately, effective risk management is pivotal in preventing injuries and illnesses related to chemical exposure, thereby safeguarding worker health and well-being.
Labeling and Safety Data Sheets (SDS) Requirements
In the context of WHMIS (Workplace Hazardous Materials Information System) classification, labeling and Safety Data Sheets (SDS) are crucial components that ensure the safe handling and use of hazardous materials. Under WHMIS, substances are categorized into two primary groups: physical hazards and health hazards. For health hazards, which include substances that can cause adverse health effects through inhalation, ingestion, or skin contact, accurate labeling and SDS are essential. Labeling requirements for health hazards involve the use of specific symbols, known as hazard pictograms, which visually communicate the nature of the hazard. For example, the "Health Hazard" pictogram features a red circle with a white interior and a black silhouette of a person with an "X" marked through it, indicating potential harm to human health. Additionally, labels must include hazard statements that describe the nature of the hazard and precautionary statements that provide advice on how to minimize or prevent adverse effects. Safety Data Sheets (SDS) provide more detailed information about the substance, including its composition, first aid measures, fire-fighting measures, accidental release measures, handling and storage instructions, exposure controls/personal protection, physical and chemical properties, stability and reactivity information, toxicological information, ecological information, disposal considerations, transport information, regulatory information, and any other relevant data. Each SDS must follow a standardized format to ensure consistency and ease of use. The SDS for substances classified as health hazards will typically include sections such as "Hazards Identification" and "Toxicological Information," which outline the specific health risks associated with the substance. For instance, if a chemical is known to cause respiratory problems or skin irritation, this information will be clearly stated in these sections. The "First Aid Measures" section will provide instructions on how to treat exposure to the substance, while the "Exposure Controls/Personal Protection" section will advise on appropriate protective equipment and workplace controls to prevent exposure. Compliance with labeling and SDS requirements is not only legally mandated but also critical for ensuring workplace safety. Employers must ensure that all workers who handle hazardous substances have access to and understand the information provided on labels and SDS. Training programs should be implemented to educate employees on how to read and interpret this information effectively. By adhering to these guidelines, workplaces can significantly reduce the risk of adverse health effects associated with hazardous materials, thereby fostering a safer working environment for all employees.