What Is Acwb

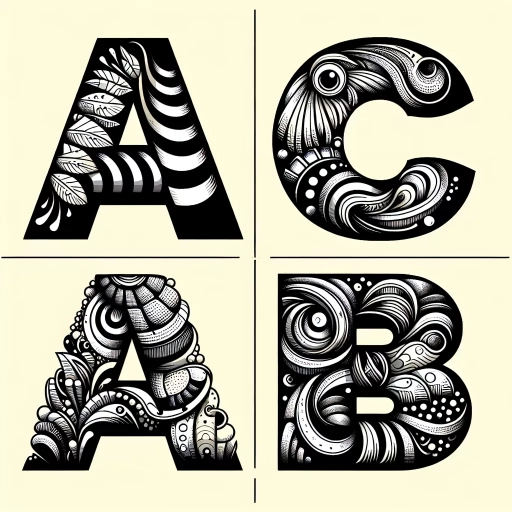
In the realm of advanced materials and engineering, the term "ACWB" (Advanced Composite Wing Box) has emerged as a significant innovation, revolutionizing the way we design and construct aircraft structures. This cutting-edge technology combines lightweight yet incredibly strong materials to enhance aircraft performance, efficiency, and safety. To fully appreciate the impact of ACWB, it is essential to delve into its fundamental principles, explore its diverse applications, and consider its future potential. Understanding the basics of ACWB will provide a solid foundation for grasping how this technology integrates various composite materials to achieve superior structural integrity. Beyond its technical aspects, ACWB has numerous applications across aerospace and other industries, offering unique benefits such as reduced weight and increased durability. As we look to the future, the benefits of ACWB are poised to expand, driving advancements in both current and emerging fields. In this article, we will begin by **Understanding the Basics of ACWB**, laying the groundwork for a comprehensive exploration of this transformative technology.
Understanding the Basics of ACWB
Understanding the Basics of ACWB (Advanced Composite Wing Box) is a crucial step for anyone interested in aerospace engineering and modern aircraft design. This article delves into the fundamental aspects of ACWB, providing a comprehensive overview that is both informative and engaging. To fully grasp the concept, it is essential to explore three key areas: **Definition and Origin**, which outlines what ACWB is and how it came into existence; **Key Components and Features**, which details the structural elements and technological advancements that make ACWB unique; and **Historical Context and Development**, which traces the evolution of ACWB from its inception to its current state. By examining these aspects, readers will gain a thorough understanding of how ACWB has revolutionized aircraft construction, enhancing performance, efficiency, and safety. This article aims to demystify the complexities of ACWB, making it accessible to a broad audience while maintaining the technical rigor required for a deep understanding. Ultimately, this exploration will lead to a clearer comprehension of the basics of ACWB.
Definition and Origin
**Understanding the Basics of ACWB: Definition and Origin** The term "ACWB" stands for "Advanced Composite Wing Box," a cutting-edge aerospace engineering concept that has revolutionized aircraft design and manufacturing. To grasp the essence of ACWB, it is crucial to delve into its definition and origin. An ACWB is a structural component of an aircraft wing, fabricated using advanced composite materials such as carbon fiber reinforced polymers (CFRP) and other high-performance composites. These materials offer significant advantages over traditional metals, including reduced weight, enhanced strength-to-weight ratio, improved durability, and resistance to fatigue and corrosion. The origin of ACWB can be traced back to the late 20th century when the aerospace industry began to explore the potential of composite materials. The advent of advanced manufacturing techniques, such as automated fiber placement (AFP) and resin transfer molding (RTM), enabled the production of complex composite structures with unprecedented precision and efficiency. Pioneering efforts by companies like Boeing, Airbus, and Lockheed Martin led to the development of the first composite wing boxes, which were initially used in military aircraft due to their superior performance characteristics. One of the key milestones in the evolution of ACWB was the introduction of the Boeing 787 Dreamliner, which featured extensive use of composite materials in its airframe, including the wing box. This marked a significant shift towards composite-intensive aircraft design, driven by the need for fuel efficiency, reduced maintenance costs, and enhanced passenger comfort. The success of the 787 has since inspired other manufacturers to adopt similar technologies, leading to widespread adoption across both commercial and military aviation sectors. The integration of ACWB into modern aircraft has not only improved structural integrity but also enabled innovative designs that were previously unfeasible with traditional materials. For instance, the use of composites allows for smoother aerodynamic profiles and more efficient wing geometries, contributing to better fuel economy and reduced emissions. Additionally, the reduced weight of composite structures translates into lower operational costs and increased payload capacity. In summary, the Advanced Composite Wing Box represents a paradigm shift in aerospace engineering, leveraging advanced materials and manufacturing techniques to create lighter, stronger, and more efficient aircraft structures. Its definition is rooted in the innovative use of composites, while its origin is tied to decades of research and development by industry leaders. Understanding ACWB is essential for appreciating the technological advancements that are transforming the aviation industry today.
Key Components and Features
Understanding the basics of Air-Cooled Water Chillers (ACWB) involves delving into their key components and features, which are crucial for their efficient operation and effectiveness. At the heart of an ACWB lies the **compressor**, responsible for compressing the refrigerant and driving the cooling cycle. This component is typically a screw or scroll compressor, chosen for its reliability and performance. The **condenser coils** are another vital part, where the hot refrigerant gas is cooled by ambient air, allowing it to condense into a liquid. These coils are usually arranged in a V-shape or a horizontal configuration to maximize heat transfer. The **evaporator** is where the liquid refrigerant absorbs heat from the water being chilled, causing it to evaporate into a gas. This process occurs within tubes or plates that are designed to optimize heat exchange. The **expansion valve** plays a critical role in reducing the pressure of the refrigerant before it enters the evaporator, ensuring that it can absorb heat efficiently. Additionally, **fans** are integral to ACWBs, providing airflow over the condenser coils to enhance cooling efficiency. **Control systems** are sophisticated features that monitor and regulate various parameters such as temperature, pressure, and flow rates. These systems often include sensors, programmable logic controllers (PLCs), and human-machine interfaces (HMIs) that allow for precise control and real-time monitoring. **Pumps** are also essential components, circulating chilled water through the system to distribute cooling where needed. Furthermore, modern ACWBs often incorporate **energy-saving technologies** like variable frequency drives (VFDs) for compressors and fans, which adjust speed according to load demands to minimize energy consumption. **Corrosion-resistant materials** are used in construction to ensure durability and longevity, especially in harsh environments. The **cabinet design** is also noteworthy; it must be robust yet accessible for maintenance, with features such as easy-open panels and tool-free access points. In terms of **safety features**, ACWBs typically include high and low pressure switches, overheat protection for compressors, and leak detection systems to prevent accidents and ensure safe operation. Some models may also offer **remote monitoring capabilities**, allowing operators to check system performance and receive alerts via mobile devices or web interfaces. Understanding these key components and features not only helps in selecting the right ACWB for specific applications but also in maintaining and optimizing its performance over time. By grasping how each part contributes to the overall functioning of the system, users can better appreciate the complexity and efficiency of air-cooled water chillers in various industrial and commercial settings.
Historical Context and Development
Understanding the basics of ACWB (Advanced Composite Wing Box) necessitates a deep dive into its historical context and development. The evolution of composite materials in aerospace engineering has been a gradual yet transformative process. In the 1950s and 1960s, the first composite materials were introduced, primarily consisting of glass fibers embedded in a polymer matrix. These early composites were used in non-structural components due to their limited strength and durability. However, as technology advanced, so did the sophistication of these materials. The 1970s and 1980s saw significant breakthroughs with the introduction of carbon fiber reinforced polymers (CFRP). CFRP offered superior strength-to-weight ratios compared to traditional metals, making it an ideal candidate for aerospace applications. The first major milestone was the use of CFRP in secondary structures such as fairings and control surfaces. This initial integration paved the way for more critical components. The 1990s marked a pivotal era for composite materials in aviation. Boeing's 787 Dreamliner and Airbus's A350 XWB became flagship projects that heavily relied on advanced composites for primary structures, including wing boxes. These aircraft demonstrated that composites could not only reduce weight but also enhance structural integrity and resistance to fatigue. The development of ACWB was a direct result of these advancements, as engineers sought to optimize wing design for better performance, fuel efficiency, and reduced maintenance costs. The ACWB's design leverages cutting-edge manufacturing techniques such as automated fiber placement (AFP) and resin transfer molding (RTM). These methods ensure precise control over fiber orientation and resin distribution, leading to consistent quality and reduced defects. Additionally, advancements in computational tools have enabled detailed simulations and testing, allowing for the optimization of wing box structures without extensive physical prototyping. Today, ACWBs are at the forefront of aerospace innovation, offering unparalleled benefits in terms of weight reduction, increased payload capacity, and improved aerodynamic efficiency. The historical context underscores a journey from humble beginnings with early composite materials to the sophisticated, high-performance structures seen in modern aircraft. This progression highlights the relentless pursuit of innovation within the aerospace industry and sets the stage for continued advancements in composite technology. By understanding this historical development, one can appreciate the complexity and ingenuity behind ACWBs and their role in shaping the future of aviation.
Applications and Uses of ACWB
The Applications and Uses of Advanced Composite Welded Beams (ACWB) are multifaceted and transformative, impacting various industries and applications. ACWB technology has revolutionized industrial and manufacturing processes by offering enhanced strength, durability, and versatility. In the industrial sector, ACWBs are used to create robust structures that withstand extreme conditions, optimizing production efficiency and reducing maintenance costs. In construction and building applications, ACWBs provide innovative solutions for structural integrity, enabling the creation of complex architectural designs while ensuring safety and sustainability. Additionally, environmental and safety considerations are paramount when utilizing ACWBs, as they offer eco-friendly alternatives to traditional materials and adhere to stringent safety standards. Understanding these diverse applications is crucial for appreciating the full potential of ACWBs. To delve deeper into these aspects, it is essential to begin by understanding the basics of ACWBs, which will provide a solid foundation for exploring their industrial, construction, and environmental implications. Understanding the Basics of ACWB will be discussed in the following sections.
Industrial and Manufacturing Uses
Industrial and manufacturing sectors heavily rely on Advanced Composite Welded Beams (ACWB) due to their exceptional strength-to-weight ratio, durability, and versatility. In these environments, ACWBs are often used as structural components in machinery, equipment, and infrastructure. For instance, in the automotive industry, ACWBs are integrated into vehicle chassis and body frames to enhance structural integrity while reducing overall weight, thereby improving fuel efficiency and performance. Similarly, in aerospace manufacturing, these beams are crucial for building lightweight yet robust aircraft components such as fuselage sections and wing spars. In the construction industry, ACWBs serve as ideal materials for building frames, bridges, and other civil engineering projects. Their resistance to corrosion and fatigue makes them particularly suitable for harsh environments where traditional materials might fail. Additionally, ACWBs are used in the production of wind turbines, where their high strength and low weight are essential for maximizing energy output while minimizing material costs. The manufacturing process itself also benefits from ACWBs. They are used in the fabrication of production lines, conveyor systems, and other machinery due to their ability to withstand heavy loads and repetitive stress without compromising performance. This results in increased operational efficiency and reduced downtime for maintenance. Furthermore, ACWBs play a significant role in the energy sector. They are utilized in the construction of offshore platforms and pipelines due to their resistance to corrosive marine environments. In the nuclear industry, ACWBs are used for containment structures and other critical components that require high strength and durability under extreme conditions. The use of ACWBs also extends to the field of robotics and automation. Here, they are employed in the construction of robotic arms and other moving parts that require precision, strength, and minimal weight. This ensures smooth operation and high accuracy in tasks such as assembly and material handling. Overall, the industrial and manufacturing applications of ACWBs are diverse and widespread, leveraging their unique properties to enhance performance, reduce costs, and improve safety across various sectors. Their integration into modern manufacturing processes continues to drive innovation and efficiency, making them an indispensable component in today's industrial landscape.
Construction and Building Applications
Construction and building applications are at the forefront of innovation, leveraging advanced materials and technologies to enhance efficiency, sustainability, and safety. One such critical component is the Alternating Current Welding (ACWB) process, which plays a pivotal role in various construction projects. ACWB is particularly advantageous in welding aluminum and other non-ferrous metals, which are increasingly used in modern architecture due to their lightweight yet robust properties. In high-rise buildings, for instance, aluminum alloys are often employed for structural components like beams and columns because they offer excellent strength-to-weight ratios, reducing the overall load on the foundation while maintaining structural integrity. In addition to structural elements, ACWB is also essential for fabricating architectural features such as facades, roofing systems, and cladding. These components not only provide aesthetic appeal but also serve as critical barriers against weather elements like rain and wind. The precision and reliability of ACWB ensure that these exterior layers are seamlessly integrated into the building envelope, enhancing both the durability and energy efficiency of the structure. Furthermore, in civil engineering projects like bridges and highways, ACWB is utilized for welding aluminum railings, guardrails, and other safety features that require high corrosion resistance and minimal maintenance. The versatility of ACWB extends beyond traditional construction materials; it is also integral in the fabrication of specialized equipment and tools used on construction sites. For example, aluminum is often used in the manufacture of scaffolding, ladders, and other temporary structures due to its lightweight nature and ease of transportation. The use of ACWB in these applications ensures that these essential tools are robust enough to withstand rigorous use while minimizing the risk of accidents. Moreover, the environmental benefits of ACWB should not be overlooked. Aluminum is highly recyclable, making it an attractive choice for sustainable building practices. By employing ACWB in construction projects, builders can significantly reduce waste and lower the carbon footprint associated with material extraction and processing. This aligns with the growing trend towards green building standards, where materials selection plays a crucial role in achieving LEED certifications and other sustainability benchmarks. In summary, ACWB is a cornerstone technology in modern construction and building applications. Its ability to weld non-ferrous metals with precision and reliability makes it indispensable for a wide range of structural, architectural, and specialized components. As the construction industry continues to evolve towards more sustainable and efficient practices, the role of ACWB will only become more pronounced, driving innovation and excellence in building design and execution.
Environmental and Safety Considerations
When considering the applications and uses of Advanced Composite Wing Boxes (ACWB), it is crucial to delve into the environmental and safety considerations that underpin their development and deployment. ACWBs, known for their lightweight yet robust structure, are increasingly used in aerospace and other high-performance industries. However, their production, use, and eventual disposal must be scrutinized through the lens of sustainability and safety. From an environmental perspective, the manufacturing process of ACWBs involves the use of advanced materials such as carbon fiber reinforced polymers (CFRP). While these materials offer significant weight reduction and strength improvements, their production is energy-intensive and generates substantial greenhouse gas emissions. Additionally, the end-of-life disposal of CFRP components poses challenges due to their non-biodegradable nature and the difficulty in recycling them. To mitigate these impacts, manufacturers are exploring sustainable production methods, including the use of renewable energy sources and developing closed-loop recycling systems. Safety considerations are equally paramount. The lightweight and high-strength characteristics of ACWBs make them ideal for reducing fuel consumption and enhancing structural integrity in aircraft. However, these benefits must be balanced against potential risks associated with material failure under extreme conditions. Comprehensive testing and validation protocols are essential to ensure that ACWBs meet stringent safety standards. This includes rigorous fatigue testing, impact resistance assessments, and environmental conditioning to simulate real-world operational scenarios. Moreover, the handling and maintenance of ACWBs require specialized training to avoid damage and ensure safe operation. Workers involved in the production and maintenance of these components must adhere to strict safety guidelines to prevent injuries from sharp edges or exposure to hazardous materials during manufacturing processes. In terms of regulatory compliance, manufacturers must align their practices with international standards and regulations such as those set by the Federal Aviation Administration (FAA) or the European Aviation Safety Agency (EASA). These regulatory bodies mandate specific safety and environmental protocols that must be followed throughout the lifecycle of ACWBs. In conclusion, while ACWBs offer numerous advantages in terms of performance and efficiency, their adoption must be accompanied by a thorough examination of environmental and safety implications. By integrating sustainable practices into their production cycle, ensuring rigorous safety testing, and adhering to regulatory standards, the aerospace industry can harness the full potential of ACWBs while minimizing their ecological footprint and ensuring operational safety. This holistic approach not only enhances the reliability and sustainability of ACWBs but also contributes to a more responsible and forward-thinking industrial ecosystem.
Benefits and Future of ACWB
The advent of Advanced Composite Wind Blades (ACWB) marks a significant milestone in the evolution of renewable energy, particularly in the wind power sector. These innovative blades are poised to revolutionize the industry by offering a multitude of benefits that extend beyond traditional wind turbine designs. Economically, ACWBs promise enhanced efficiency and reduced operational costs, making wind energy more competitive with fossil fuels. Technologically, they leverage cutting-edge materials and manufacturing techniques, enabling longer blade lengths and improved performance. Additionally, ACWBs contribute to a more sustainable future by minimizing environmental impact through reduced material usage and extended lifespan. As we delve into the specifics of these advantages, it becomes clear that understanding the basics of ACWB is crucial for grasping their full potential. In this article, we will explore the economic and efficiency benefits, technological advancements and innovations, and sustainability and environmental impact of ACWBs, providing a comprehensive overview that transitions seamlessly into understanding the basics of this transformative technology.
Economic and Efficiency Benefits
The adoption of Advanced Composite Wing Boxes (ACWB) in aerospace engineering is poised to revolutionize the industry by offering significant economic and efficiency benefits. One of the primary advantages of ACWB is the substantial reduction in weight compared to traditional metal structures. Composite materials, such as carbon fiber reinforced polymers (CFRP), are lighter yet stronger, leading to improved fuel efficiency and lower operational costs for aircraft. This weight reduction translates into reduced fuel consumption, which not only decreases operating expenses but also minimizes environmental impact by lowering greenhouse gas emissions. Additionally, the use of composites allows for more complex geometries and integrated designs, reducing the number of parts and joints required, thereby simplifying manufacturing processes and reducing production costs. From an economic standpoint, ACWBs also offer extended lifespan and reduced maintenance needs. Composite materials are less prone to fatigue and corrosion compared to metals, which means fewer repairs and replacements over the life of the aircraft. This extended durability can significantly lower maintenance costs and downtime, ensuring that aircraft remain operational for longer periods. Furthermore, the integration of advanced materials and manufacturing techniques in ACWBs enables the production of larger, more complex components in a single piece, reducing assembly time and increasing overall efficiency. In terms of future benefits, the development and widespread adoption of ACWBs are expected to drive innovation in aerospace manufacturing. The integration of advanced technologies such as 3D printing and automated fiber placement (AFP) will further enhance production efficiency and reduce material waste. These advancements will also pave the way for more sustainable aviation practices by enabling the creation of lighter, more fuel-efficient aircraft that can meet stringent environmental regulations while maintaining or improving performance standards. Moreover, the economic benefits of ACWBs extend beyond the aerospace industry itself. By enabling the development of more efficient aircraft, ACWBs can contribute to broader economic growth by reducing transportation costs and increasing the speed of global commerce. This can have a ripple effect across various sectors, from logistics and trade to tourism and business travel, ultimately contributing to economic stability and growth. In conclusion, the economic and efficiency benefits of Advanced Composite Wing Boxes are multifaceted and far-reaching. From reduced weight and improved fuel efficiency to extended lifespan and lower maintenance costs, ACWBs represent a significant step forward in aerospace engineering. As technology continues to evolve, these benefits are likely to expand, driving innovation, sustainability, and economic growth both within the aerospace industry and beyond.
Technological Advancements and Innovations
Technological advancements and innovations are pivotal in shaping the future of various industries, including the realm of Advanced Composite Wing Boxes (ACWB). The integration of cutting-edge technologies such as 3D printing, artificial intelligence, and advanced materials science has significantly enhanced the design, manufacturing, and performance of ACWBs. For instance, 3D printing allows for the creation of complex geometries that cannot be achieved through traditional manufacturing methods, enabling lighter yet stronger wing structures. Artificial intelligence and machine learning algorithms can optimize wing design for better aerodynamics and structural integrity, while advanced materials like carbon fiber reinforced polymers (CFRP) offer superior strength-to-weight ratios. These innovations not only improve the efficiency and durability of ACWBs but also contribute to reduced production costs and environmental impact. The use of sustainable materials and energy-efficient manufacturing processes aligns with the industry's growing focus on sustainability. Furthermore, real-time monitoring and predictive maintenance enabled by IoT sensors and AI analytics ensure that ACWBs operate at peak performance, minimizing downtime and enhancing overall safety. Looking ahead, the future of ACWBs is promising with ongoing research into new materials and technologies. The development of smart materials that can adapt to changing environmental conditions is on the horizon, potentially leading to self-healing structures and dynamic shape control. Additionally, advancements in digital twin technology will allow for virtual testing and simulation, reducing the need for physical prototypes and accelerating the development cycle. In summary, technological advancements are transforming the landscape of ACWBs by enhancing their design, manufacturing, and operational capabilities. These innovations not only drive efficiency and sustainability but also pave the way for future breakthroughs that will continue to elevate the performance and reliability of ACWBs. As these technologies mature, they will play a crucial role in shaping the future of aerospace engineering, ensuring that ACWBs remain at the forefront of innovation and excellence.
Sustainability and Environmental Impact
Sustainability and environmental impact are pivotal considerations in the context of Advanced Cooling Water (ACWB) systems. As the world grapples with the challenges of climate change, water scarcity, and energy efficiency, ACWB emerges as a beacon of innovation. By leveraging cutting-edge technology, ACWB systems significantly reduce water consumption and energy usage, thereby minimizing their ecological footprint. This is achieved through advanced cooling mechanisms that optimize heat transfer efficiency, allowing for lower water flow rates without compromising performance. Additionally, ACWB systems often incorporate recycled or reclaimed water, further reducing the demand on potable water resources and aligning with global sustainability goals. The environmental benefits of ACWB extend beyond water conservation. These systems are designed to operate at higher temperatures than traditional cooling systems, which reduces the amount of chemicals required for water treatment. This decrease in chemical usage not only lowers operational costs but also minimizes the release of harmful substances into the environment. Moreover, the enhanced efficiency of ACWB systems results in lower greenhouse gas emissions, contributing to a cleaner and healthier atmosphere. In the future, the adoption of ACWB is expected to play a crucial role in shaping sustainable industrial practices. As industries continue to evolve and expand, the demand for efficient and environmentally friendly cooling solutions will only grow. ACWB stands poised to meet this demand by offering a scalable and adaptable solution that can be integrated into various industrial settings. Furthermore, ongoing research and development in this field promise even more significant advancements, such as the integration of renewable energy sources and advanced materials that enhance performance while reducing environmental impact. The long-term benefits of ACWB are multifaceted. By adopting these systems, industries can not only comply with increasingly stringent environmental regulations but also enhance their brand reputation and appeal to environmentally conscious consumers. The economic advantages are equally compelling; reduced water and energy consumption translate into lower operational costs, making ACWB a sound investment for businesses looking to balance profitability with sustainability. As the world moves towards a more sustainable future, ACWB stands as a testament to the power of innovation in addressing some of our most pressing environmental challenges.