What Is A Grommet

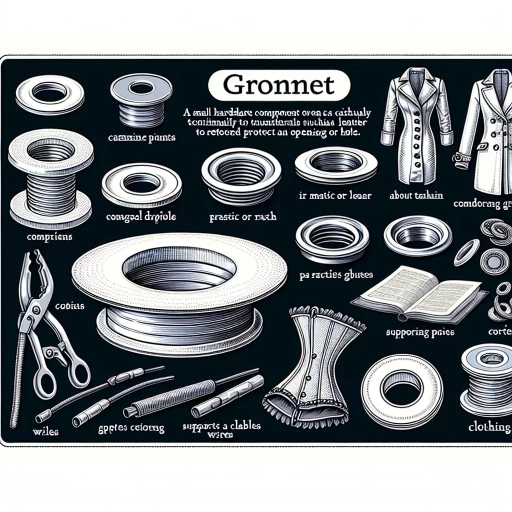
A grommet is a versatile and essential component in various industries, including construction, electronics, and textiles. This small but crucial piece of hardware serves multiple purposes, making it a fundamental element in many applications. To understand the significance of grommets, it is important to delve into their definition and purpose, which will be explored in the following section. Additionally, grommets come in different types and are used in diverse applications, each tailored to specific needs. The installation, maintenance, and safety considerations of grommets are also critical aspects that ensure their effective and safe use. This article will provide a comprehensive overview of grommets, starting with their definition and purpose, followed by an examination of their types and applications, and concluding with practical insights into their installation, maintenance, and safety considerations. By understanding these key aspects, readers will gain a thorough appreciation for the role grommets play in various contexts. Let us begin by defining what a grommet is and its purpose.
Definition and Purpose of a Grommet
A grommet is a small ring or tube, typically made of metal, plastic, or rubber, used to protect and reinforce holes in various materials such as fabric, leather, or metal. The definition and purpose of a grommet are multifaceted and have evolved significantly over time. Historically, grommets have been integral in maritime and textile industries, serving as a crucial component in sailmaking and rope reinforcement. This historical context sets the stage for understanding their evolution and widespread adoption across different sectors. In modern times, grommets play primary functions in various industries, including construction, automotive, and electronics, where they ensure durability and prevent wear and tear around holes. Key characteristics and features of grommets, such as their material composition and design variations, further underscore their versatility and importance. By examining the historical context and evolution of grommets, we can better appreciate their significance and how they have adapted to meet the needs of diverse industries. Let us delve into the historical context and evolution of grommets to understand their origins and development.
Historical Context and Evolution
The historical context and evolution of grommets are deeply intertwined with the development of various industries, particularly textiles, maritime, and construction. The term "grommet" itself has its roots in the 15th century, derived from the Old French word "grommet," meaning "a ring or eyelet." Initially, grommets were used in sailing to reinforce holes in sails and prevent them from tearing. These early grommets were typically made of metal or leather and served as a crucial component in the durability and functionality of maritime equipment. As industrialization progressed, the use of grommets expanded beyond the maritime sector. In the textile industry, grommets became essential for creating reinforced holes in fabrics, which was particularly important for tents, awnings, and other canvas products. The introduction of new materials such as rubber and plastic during the 19th and 20th centuries further diversified the applications of grommets. They began to be used in electrical wiring to protect cables from abrasion and damage, enhancing safety and reliability in electrical installations. In modern times, grommets have evolved to cater to a wide range of industries including construction, automotive, and electronics. Advanced materials like nylon, polyethylene, and stainless steel have been incorporated into grommet design, offering improved durability and resistance to environmental factors. The development of specialized grommets for specific applications—such as cable management grommets in IT infrastructure or architectural grommets in building design—has further underscored their versatility. The evolution of manufacturing processes has also played a significant role in the widespread adoption of grommets. Modern manufacturing techniques allow for mass production with high precision, making grommets more accessible and affordable. Additionally, advancements in design have led to the creation of self-tapping grommets that can be easily installed without the need for pre-drilled holes, simplifying the installation process across various applications. In summary, the historical context and evolution of grommets reflect a journey from simple maritime reinforcements to sophisticated components integral to multiple industries. Their adaptability, coupled with advancements in materials and manufacturing, has solidified their importance in ensuring the integrity and functionality of various products and systems. This rich history underscores the definition and purpose of a grommet as a versatile tool designed to enhance durability, safety, and efficiency across diverse applications.
Primary Functions in Various Industries
In various industries, primary functions play a crucial role in defining the operational efficiency and effectiveness of each sector. For instance, in the **manufacturing industry**, primary functions include production, quality control, and supply chain management. These functions ensure that products are made to specifications, meet quality standards, and are delivered to customers on time. In **healthcare**, primary functions revolve around patient care, medical research, and administrative support. Healthcare providers focus on diagnosing and treating patients while also conducting research to improve medical practices and managing administrative tasks to ensure smooth operations. In the **financial sector**, primary functions include investment management, risk assessment, and regulatory compliance. Financial institutions manage client investments, assess market risks, and adhere to regulatory requirements to maintain stability and trust. **Agriculture** relies on primary functions such as crop cultivation, livestock management, and market distribution. Farmers and agricultural companies focus on growing crops and raising livestock efficiently while ensuring that products reach consumers through effective distribution channels. **Technology** industries prioritize software development, data analytics, and cybersecurity as their primary functions. Tech companies develop software solutions, analyze data to drive decision-making, and protect against cyber threats to safeguard user information. In **construction**, primary functions include project planning, site management, and materials procurement. Construction companies plan projects meticulously, manage construction sites efficiently, and procure necessary materials to complete projects on schedule. **Retail** businesses focus on inventory management, customer service, and sales strategies as their primary functions. Retailers manage inventory levels to meet demand, provide excellent customer service to build loyalty, and implement sales strategies to drive revenue. **Transportation** industries emphasize route optimization, fleet management, and safety protocols as their primary functions. Transportation companies optimize routes for efficiency, manage fleets to ensure reliability, and implement safety protocols to protect drivers and cargo. Understanding these primary functions across different industries highlights the importance of specialized roles and processes in achieving industry-specific goals. For example, in the context of grommets—small rings or tubes used to protect or insulate wires and cables—primary functions in industries like manufacturing and technology are crucial. Grommets are essential for ensuring the integrity of electrical systems by preventing damage from friction or environmental factors. Their use underscores the critical role of component quality in maintaining operational efficiency across various sectors. By recognizing these primary functions, businesses can better integrate grommets and other components into their operations to enhance overall performance and reliability.
Key Characteristics and Features
A grommet, a small ring or tube typically made of metal, plastic, or rubber, is characterized by several key features that define its purpose and functionality. **Material and Construction**: Grommets are often fabricated from durable materials such as brass, stainless steel, or high-quality plastics to ensure longevity and resistance to wear and tear. Rubber grommets are also common, providing flexibility and insulation. **Shape and Design**: The most common shapes are cylindrical and tubular, designed to fit snugly around wires or cables while protecting them from abrasion and environmental factors. Some grommets have flared ends to secure them in place more effectively. **Size and Fit**: Grommets come in various sizes to accommodate different diameters of wires and cables, ensuring a precise fit that prevents damage or exposure. **Installation Method**: They can be installed using simple insertion methods or may require specialized tools for more secure fastening. **Sealing Properties**: Many grommets are designed with sealing capabilities, such as O-rings or gaskets, to prevent water, dust, or other contaminants from entering the protected area. **Electrical Insulation**: Some grommets are specifically designed to provide electrical insulation, safeguarding against short circuits and ensuring safe passage of electrical wires through panels or enclosures. **Aesthetic Appeal**: While functional, grommets can also contribute to the overall appearance of a product by offering color options and sleek designs that blend with the surrounding material. **Versatility**: Grommets are used across various industries including electronics, automotive, aerospace, and construction due to their adaptability in different applications. Overall, these characteristics make grommets indispensable components in maintaining the integrity and functionality of systems by protecting wires and cables from potential hazards while ensuring a secure and reliable connection.
Types and Applications of Grommets
Grommets are versatile components that play a crucial role in various industries and consumer applications, offering protection, reinforcement, and insulation where cables, wires, or other materials pass through holes in materials. The diversity of grommets is underscored by the different materials used in their construction, each tailored to meet specific requirements. For instance, rubber grommets are ideal for applications requiring flexibility and insulation, while metal grommets provide durability and strength. The distinction between industrial and consumer applications further highlights the adaptability of grommets; industrial settings often demand high-performance grommets that can withstand harsh conditions, whereas consumer products may use more standard types. Additionally, specialized grommets are designed for specific uses, such as waterproof grommets for marine applications or high-temperature grommets for aerospace. Understanding these variations is essential for selecting the right grommet for any given task. To delve deeper into this topic, let's first explore the different materials used in grommet construction, which form the foundation of their diverse applications and functionalities.
Different Materials Used in Grommet Construction
In the construction of grommets, various materials are employed to cater to different applications and ensure optimal performance. **Rubber** is a common material due to its flexibility, durability, and resistance to abrasion. Rubber grommets are often used in electrical and automotive industries where they protect wires from damage and provide a seal against moisture and dust. **Plastic** grommets, typically made from polyethylene or nylon, offer a cost-effective alternative with good chemical resistance and are frequently used in consumer electronics and industrial settings. **Metal** grommets, usually made from brass or stainless steel, are chosen for their strength and resistance to high temperatures, making them suitable for heavy-duty applications such as in machinery and marine equipment. **Silicone** grommets are preferred in environments requiring high temperature resistance and flexibility, such as in aerospace and medical devices. **Teflon (PTFE)** grommets are valued for their non-stick properties and chemical inertness, making them ideal for use in chemical processing and food industries. Additionally, **fabric** grommets, often used in textile applications like curtains and tarps, provide a softer, more pliable option that can be easily integrated into fabric-based products. Each material selection is driven by the specific requirements of the application, including factors such as environmental conditions, mechanical stress, and compatibility with other materials involved. By choosing the appropriate material, grommets can effectively serve their purpose of protecting cables, providing seals, and enhancing the overall functionality of various systems.
Industrial vs. Consumer Applications
When it comes to the types and applications of grommets, a significant distinction lies between industrial and consumer uses. **Industrial applications** of grommets are characterized by their robustness and durability, designed to withstand harsh environments and heavy-duty operations. In manufacturing settings, grommets are used to protect cables and wires from abrasion and damage, ensuring the integrity of electrical connections in machinery and equipment. For instance, in automotive manufacturing, grommets are crucial for routing wires through metal panels without causing damage or compromising the electrical system. Similarly, in aerospace and defense industries, grommets play a critical role in maintaining the structural integrity of aircraft and military vehicles by protecting sensitive wiring from environmental factors. These industrial-grade grommets are often made from high-strength materials such as nylon, polyethylene, or even metal, ensuring they can endure extreme temperatures, vibrations, and other rigorous conditions. On the other hand, **consumer applications** of grommets are more focused on convenience, aesthetics, and user safety. In consumer electronics, grommets are used to manage cables and wires in a neat and organized manner, enhancing the overall user experience. For example, in home entertainment systems, grommets help route HDMI cables through walls or furniture without causing damage to the cables or the surrounding material. In furniture design, grommets are used to create clean lines and modern aesthetics by allowing cables to pass through tables or desks discreetly. Additionally, in outdoor gear such as tents and camping equipment, grommets serve as reinforced holes for ropes and lines, providing durability and ease of use. Consumer-grade grommets are typically made from flexible materials like rubber or plastic, which offer sufficient protection without compromising on flexibility or ease of installation. Overall, while industrial grommets prioritize durability and performance under extreme conditions, consumer grommets emphasize functionality, design, and user convenience.
Specialized Grommets for Specific Uses
Specialized grommets are designed to cater to specific needs across various industries, ensuring optimal performance and durability. In the realm of electrical engineering, for instance, **electrical grommets** are used to protect wires and cables from abrasion and damage when passing through holes in panels or enclosures. These grommets are typically made from materials like rubber or plastic and are often reinforced with metal or fiber to enhance their protective capabilities. In marine applications, **marine grommets** are crucial for sealing and protecting cables and hoses from seawater and other corrosive elements. These grommets are usually made from materials such as silicone or polyurethane, which offer superior resistance to saltwater and UV exposure. They play a vital role in maintaining the integrity of marine equipment and preventing water ingress. For medical devices, **medical grommets** are designed with stringent quality standards to ensure sterility and biocompatibility. These grommets are often made from materials like silicone or Teflon, which are non-reactive and can withstand the rigors of sterilization processes. They are used in medical tubing, catheters, and other devices where cleanliness and safety are paramount. In the automotive sector, **automotive grommets** are used to seal and protect wiring harnesses, fuel lines, and other critical components from environmental factors such as moisture, dust, and extreme temperatures. These grommets are typically made from durable materials like EPDM rubber or thermoplastic elastomers, ensuring long-term reliability. Aerospace applications also rely on specialized grommets that meet stringent specifications for weight, durability, and resistance to extreme conditions. **Aerospace grommets** are often made from advanced materials like fluoropolymers or high-temperature-resistant plastics, which can withstand the harsh environments encountered in flight. Additionally, **architectural grommets** are used in building construction to seal gaps around pipes, ducts, and other penetrations through walls and floors. These grommets help prevent air leaks, reduce noise transmission, and improve overall building efficiency. They are commonly made from flexible materials like foam or rubber. Each type of specialized grommet is engineered to address specific challenges and requirements, ensuring that they provide the necessary protection, sealing, or support in their respective applications. By selecting the right type of grommet for a particular use case, users can enhance the performance, safety, and longevity of their systems and equipment.
Installation, Maintenance, and Safety Considerations
When it comes to the effective use of grommets in various applications, understanding the intricacies of installation, maintenance, and safety is paramount. A well-executed installation is the foundation upon which the longevity and performance of grommets depend. This article will delve into a **Step-by-Step Installation Guide** to ensure that each grommet is correctly placed and secured. Additionally, we will explore **Maintenance Tips for Longevity**, providing insights on how to keep grommets in optimal condition over time. Equally important are **Safety Precautions When Handling Grommets**, as improper handling can lead to injuries and damage. By following these guidelines, users can ensure that their grommets function as intended while minimizing risks. To begin, let's start with the critical first step: a detailed **Step-by-Step Installation Guide**.
Step-by-Step Installation Guide
When it comes to installing grommets, a step-by-step guide is essential to ensure the process is both efficient and safe. Here’s a detailed breakdown of the installation steps: 1. **Prepare the Workspace**: Clear your workspace of any debris or obstructions. Ensure you have all necessary tools and materials within reach, including the grommet, grommet punch or die set, hammer, and any additional fasteners. 2. **Measure and Mark**: Measure the diameter of the grommet and mark the center point on the material where you want to install it. Use a ruler or caliper for accuracy. 3. **Cut Out the Hole**: Using a sharp utility knife or a hole punch, carefully cut out a hole slightly smaller than the grommet's inner diameter. If using a hole punch, align it with your mark and strike it gently but firmly with a hammer. 4. **Position the Grommet**: Place the grommet over the hole, ensuring it is centered and even. For metal grommets, you may need to use a grommet setting tool to secure it in place. 5. **Set the Grommet**: If using a metal grommet with a flange, place the setting tool over the grommet and strike it with a hammer to crimp the flange into place. For rubber or plastic grommets, simply press them into position until they are snug. 6. **Test the Installation**: Once installed, test the grommet by gently tugging on it to ensure it is securely fastened and won’t come loose under normal use. 7. **Maintenance Check**: Regularly inspect grommets for signs of wear or damage. Replace any grommets that show signs of deterioration to prevent further damage to surrounding materials. 8. **Safety Considerations**: Always wear protective gear such as safety glasses and gloves when working with sharp tools like hole punches and utility knives. Ensure that your workspace is well-lit to avoid accidents. By following these steps meticulously, you can ensure that your grommet installation is both durable and safe, providing long-lasting protection against abrasion and wear on cables or wires passing through the material. This attention to detail not only enhances functionality but also contributes to overall safety in various applications ranging from electrical wiring to marine hardware.
Maintenance Tips for Longevity
To ensure the longevity of grommets, regular maintenance is crucial. Here are some key tips to keep in mind: 1. **Inspection**: Regularly inspect grommets for signs of wear, such as cracks, fraying, or discoloration. Early detection can prevent minor issues from becoming major problems. 2. **Cleaning**: Clean grommets periodically to remove dirt and debris that can cause friction and wear. Use a soft brush or a damp cloth, avoiding harsh chemicals that might damage the material. 3. **Lubrication**: Apply a suitable lubricant to moving parts associated with grommets, such as cables or wires passing through them. This reduces friction and prevents wear on both the grommet and the cable. 4. **Protection from Environmental Factors**: Shield grommets from extreme temperatures, moisture, and UV exposure, which can degrade materials over time. Use protective coatings or covers if necessary. 5. **Proper Installation**: Ensure that grommets are installed correctly according to manufacturer guidelines. Incorrect installation can lead to premature wear and failure. 6. **Avoid Overloading**: Do not overload grommets with excessive weight or tension, as this can cause them to stretch or break. Distribute loads evenly and follow recommended capacity limits. 7. **Material Selection**: Choose grommets made from high-quality materials suitable for the specific application. For example, rubber grommets are ideal for electrical applications due to their insulating properties. 8. **Replacement**: Replace grommets at the first sign of significant wear or damage. Delaying replacement can lead to more severe issues down the line, including equipment failure or safety hazards. By following these maintenance tips, you can significantly extend the lifespan of your grommets, ensuring they continue to perform their intended function effectively and safely. Regular upkeep not only saves time and money in the long run but also enhances overall system reliability and efficiency.
Safety Precautions When Handling Grommets
When handling grommets, it is crucial to adhere to strict safety precautions to prevent injuries and ensure the longevity of both the grommet and the surrounding material. First, always wear protective gear such as gloves and safety glasses to shield against sharp edges or flying debris. Ensure that your workspace is well-lit and free from clutter to avoid accidents. Before starting any installation or maintenance task, inspect the grommet for any signs of damage or wear; damaged grommets can fail unexpectedly, leading to potential hazards. During installation, use the appropriate tools to avoid applying excessive force, which can cause the grommet to split or the surrounding material to tear. For instance, when using a grommet punch, make sure it is aligned correctly and apply steady, controlled pressure. If you are working with electrical cables or wires through grommets, ensure they are properly insulated to prevent electrical shock. In maintenance tasks, regularly inspect grommets for signs of wear such as cracks, splits, or corrosion. Replace any damaged grommets promptly to maintain the integrity of the system. When cleaning around grommets, avoid using harsh chemicals that could degrade the material; instead, opt for mild detergents and soft brushes. It is also important to follow specific guidelines based on the type of grommet you are handling. For example, rubber grommets may require different care compared to metal or plastic ones. Always refer to the manufacturer's instructions for specific safety recommendations tailored to the particular type of grommet you are working with. Additionally, consider the environmental conditions in which the grommets will be used. Extreme temperatures, exposure to chemicals, or high humidity can affect the durability and performance of grommets. Ensure that the chosen grommet is suitable for its intended application and follow any special handling instructions provided by the manufacturer. By adhering to these safety precautions and guidelines, you can significantly reduce the risk of accidents and ensure that your grommets function optimally over their lifespan. Proper handling not only protects you but also extends the life of your equipment and maintains operational efficiency. Always prioritize safety when working with grommets to create a secure and reliable working environment.