If A Boat Is Made Of Mostly Non-metallic Materials What Is Needed

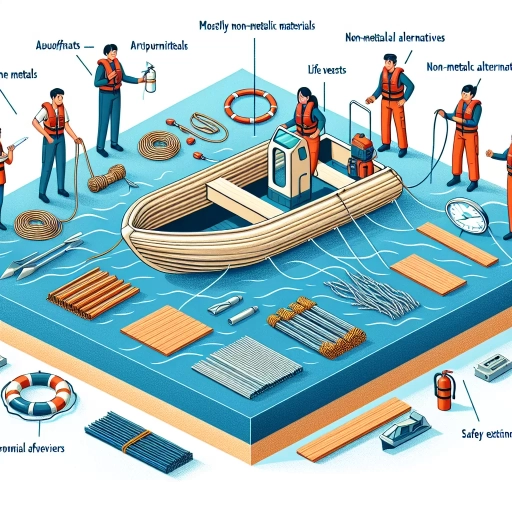
In the modern era of boat construction, the shift towards non-metallic materials has revolutionized the industry, offering numerous advantages over traditional metallic counterparts. When a boat is primarily made of non-metallic materials, several critical factors come into play to ensure its durability, performance, and longevity. This article delves into the essential considerations for such vessels, exploring three key aspects: Design and Material Selection, Manufacturing and Construction, and Performance and Maintenance. Design and Material Selection are crucial in determining the overall structure and functionality of the boat. The choice of materials such as fiberglass, carbon fiber, or advanced polymers must be carefully considered to meet specific requirements like weight, strength, and resistance to environmental factors. Manufacturing and Construction processes also play a pivotal role in ensuring that the boat is built to withstand various conditions. Techniques such as infusion molding or hand layup must be meticulously executed to achieve optimal results. Finally, Performance and Maintenance are vital for the long-term health of the boat. Understanding how non-metallic materials perform under different conditions and implementing effective maintenance strategies can significantly extend the lifespan of the vessel. By examining these three critical areas, we can gain a comprehensive understanding of what is needed when constructing a boat primarily from non-metallic materials. Let's begin by exploring the intricacies of Design and Material Selection.
Design and Material Selection
In the realm of engineering and design, the selection of materials is a critical decision that can significantly impact the performance, longevity, and overall success of a project. When it comes to choosing the right materials, several key factors must be carefully considered. First, understanding non-metallic materials is essential, as these alternatives offer unique properties that can be advantageous in various applications. For instance, polymers and composites can provide lightweight solutions with high strength-to-weight ratios, making them ideal for industries such as aerospace and automotive. Second, ensuring structural integrity and durability is paramount; materials must withstand the stresses and strains they will encounter in their intended environment. This involves evaluating factors like tensile strength, corrosion resistance, and fatigue life. Third, weight and buoyancy considerations are crucial, particularly in marine and aerospace engineering where these factors directly influence operational efficiency and safety. By meticulously evaluating these aspects—understanding non-metallic materials, ensuring structural integrity and durability, and considering weight and buoyancy—designers can make informed decisions that optimize their projects. This article delves into these critical considerations, providing a comprehensive guide to design and material selection.
1. Understanding Non-Metallic Materials
When designing a boat primarily made of non-metallic materials, it is crucial to understand the unique properties and requirements of these materials to ensure durability, safety, and performance. Non-metallic materials, such as fiberglass, carbon fiber, and various polymers, offer several advantages over traditional metals. They are generally lighter, which can enhance the boat's speed and fuel efficiency. Additionally, non-metallic materials are often resistant to corrosion, reducing maintenance costs and extending the lifespan of the vessel. However, these materials also present specific challenges. For instance, fiberglass and other composite materials can be prone to damage from impact or fatigue, necessitating careful selection of reinforcement types and layup techniques. Carbon fiber, while incredibly strong and lightweight, is expensive and requires precise manufacturing processes to achieve optimal performance. Polymers and resins used in these composites must be chosen for their compatibility with marine environments, including resistance to UV degradation and chemical exposure. To successfully design a boat with non-metallic materials, engineers must consider several key factors. First, the structural integrity of the hull and superstructure must be ensured through detailed finite element analysis and testing. This involves understanding the material's mechanical properties under various loads and environmental conditions. Second, the manufacturing process must be meticulously controlled to avoid defects such as voids or delamination, which can compromise the material's strength. Furthermore, the selection of appropriate fastening systems and adhesives is critical. Unlike metal boats where welding is common, non-metallic boats rely on mechanical fasteners or advanced adhesives that must withstand the stresses of wave impact and other dynamic loads. The choice of coatings and finishes is also important for protecting the material from UV radiation and marine organisms that could cause degradation. In addition to these technical considerations, regulatory compliance is essential. Boat builders must adhere to standards set by organizations such as the American Boat and Yacht Council (ABYC) or the International Organization for Standardization (ISO), which provide guidelines for safety, performance, and environmental impact. In summary, designing a boat made mostly of non-metallic materials requires a deep understanding of their properties, careful material selection, precise manufacturing techniques, and adherence to regulatory standards. By addressing these factors comprehensively, boat designers can create vessels that are not only aesthetically pleasing but also safe, efficient, and durable in marine environments. This holistic approach ensures that the benefits of non-metallic materials are fully realized while mitigating potential drawbacks, resulting in a superior boating experience.
2. Structural Integrity and Durability
When designing a boat primarily constructed from non-metallic materials, ensuring structural integrity and durability is paramount. Non-metallic materials, such as fiberglass, carbon fiber, and advanced polymers, offer significant advantages in terms of weight reduction, corrosion resistance, and ease of maintenance. However, they also present unique challenges that must be addressed to guarantee the boat's performance and longevity. First and foremost, the selection of appropriate non-metallic materials is crucial. For instance, fiberglass reinforced plastic (FRP) is a popular choice due to its strength-to-weight ratio and resistance to environmental degradation. However, it requires careful consideration of the resin type, fiber orientation, and laminate thickness to achieve optimal structural integrity. Similarly, carbon fiber composites offer exceptional stiffness and strength but demand precise engineering to avoid delamination and other forms of failure. Beyond material selection, the design process must incorporate robust structural analysis. Finite element analysis (FEA) and computational fluid dynamics (CFD) are essential tools for simulating various loading conditions, including wave impacts, wind forces, and operational stresses. These analyses help in identifying potential weak points and optimizing the structural layout to distribute loads efficiently. Additionally, the manufacturing process plays a critical role in maintaining structural integrity. Techniques such as vacuum bagging, resin infusion, and 3D printing can ensure consistent quality and minimize defects. Quality control measures, including non-destructive testing methods like ultrasonic inspection and radiography, are vital for detecting any anomalies before the boat is put into service. Durability is also a key consideration, particularly in marine environments where exposure to saltwater, UV radiation, and extreme temperatures can accelerate degradation. Coatings and surface treatments can enhance the material's resistance to these factors. For example, applying a gelcoat or paint specifically formulated for marine use can protect the underlying material from UV damage and chemical corrosion. Finally, regular maintenance and inspection are indispensable for extending the lifespan of a non-metallic boat. Scheduled checks should include visual inspections for signs of damage or wear, as well as more detailed assessments using advanced diagnostic tools. This proactive approach helps in identifying and addressing potential issues before they become major problems. In summary, achieving structural integrity and durability in a boat made from non-metallic materials requires meticulous attention to material selection, design optimization, precise manufacturing techniques, and ongoing maintenance. By leveraging advanced engineering tools and best practices in construction and upkeep, boat builders can create vessels that are not only lightweight and efficient but also robust and long-lasting. This holistic approach ensures that the boat performs reliably over its lifespan, providing a safe and enjoyable experience for its users.
3. Weight and Buoyancy Considerations
When designing a boat primarily made of non-metallic materials, weight and buoyancy considerations are paramount to ensure stability, performance, and safety. Non-metallic materials such as fiberglass, carbon fiber, and advanced polymers offer significant advantages in terms of corrosion resistance and reduced maintenance, but they also present unique challenges. Firstly, the weight of the boat must be carefully managed. Non-metallic materials can be lighter than their metallic counterparts, which is beneficial for achieving higher speeds and better fuel efficiency. However, this lightness can also lead to reduced stability in rough waters if not balanced properly. Designers must meticulously calculate the distribution of weight across the hull to maintain optimal buoyancy and prevent capsizing. This involves strategic placement of heavier components like engines and batteries to lower the center of gravity. Secondly, buoyancy is a critical factor that directly impacts the boat's ability to stay afloat. Non-metallic materials inherently provide some level of buoyancy due to their lower density compared to metals. However, additional buoyancy measures may still be necessary to ensure the boat remains afloat even when damaged or flooded. This can be achieved through the incorporation of foam cores within the hull structure or by designing compartments that can trap air in case of water ingress. Thirdly, material selection plays a crucial role in balancing weight and buoyancy. For instance, using sandwich construction techniques where a lightweight core is sandwiched between two layers of a stronger material can enhance structural integrity without adding excessive weight. Additionally, selecting materials with high strength-to-weight ratios such as carbon fiber can help in achieving the desired performance without compromising on safety. In summary, designing a boat made mostly of non-metallic materials requires a holistic approach to weight and buoyancy considerations. By carefully managing weight distribution, ensuring adequate buoyancy through design and material choices, and leveraging advanced materials for optimal strength-to-weight ratios, boat designers can create vessels that are not only efficient and durable but also safe and stable on the water. This balanced approach is essential for maximizing the benefits of non-metallic materials while mitigating their potential drawbacks.
Manufacturing and Construction
In the dynamic and interconnected fields of manufacturing and construction, innovation and precision are paramount. The evolution of these industries has been driven by advancements in various key areas, each contributing to the creation of more efficient, durable, and sustainable structures. This article delves into three critical components that underpin modern manufacturing and construction practices: Advanced Manufacturing Techniques, Adhesives and Bonding Methods, and Quality Control and Testing. Advanced manufacturing techniques, such as 3D printing and robotic assembly, have revolutionized the production process by enhancing speed and accuracy. Adhesives and bonding methods have transformed the way materials are joined, offering superior strength and versatility. Meanwhile, rigorous quality control and testing protocols ensure that final products meet stringent standards. These innovations not only improve the overall quality of manufactured and constructed products but also pave the way for more informed Design and Material Selection, enabling professionals to make better choices that align with project requirements and environmental considerations. By exploring these facets, we can gain a deeper understanding of how cutting-edge technologies and methodologies are reshaping the future of manufacturing and construction.
1. Advanced Manufacturing Techniques
In the realm of manufacturing and construction, particularly when it comes to crafting boats from mostly non-metallic materials, advanced manufacturing techniques play a pivotal role in ensuring the production of high-quality, durable, and performance-driven vessels. One of the key techniques is **Composite Manufacturing**, which involves combining different materials such as carbon fiber, fiberglass, and advanced polymers to create lightweight yet incredibly strong structures. This method allows for the creation of complex geometries and shapes that would be challenging or impossible with traditional metalworking processes. Another critical technique is **3D Printing**, also known as Additive Manufacturing. This technology enables the precise layer-by-layer construction of components using materials like carbon fiber-reinforced polymers (CFRP) and other advanced composites. 3D printing offers unparalleled flexibility in design, allowing for the creation of intricate structures with minimal material waste and reduced production time. For boat construction, this means that complex components such as hulls, propellers, and even entire sections of the boat can be manufactured with high accuracy and speed. **Resin Transfer Molding (RTM)** is another advanced technique that has gained prominence in non-metallic boat manufacturing. RTM involves injecting resin into a mold under pressure to ensure uniform distribution and minimal voids, resulting in parts with superior mechanical properties. This method is particularly useful for producing large, complex components like boat hulls and decks with consistent quality. Additionally, **Automated Fiber Placement (AFP)** has revolutionized the production of composite parts by enabling the precise placement of fibers in specific orientations to maximize strength and minimize weight. AFP systems use robotic arms to lay down fibers in a predetermined pattern, significantly reducing labor costs and improving consistency compared to manual processes. The integration of these advanced manufacturing techniques not only enhances the structural integrity and performance of non-metallic boats but also reduces production time and costs. Furthermore, these methods allow for greater design flexibility, enabling boat manufacturers to create vessels that are not only aesthetically pleasing but also highly functional and environmentally friendly. By leveraging these cutting-edge technologies, the maritime industry can produce boats that are lighter, stronger, and more efficient than ever before, setting new standards in both manufacturing excellence and environmental sustainability.
2. Adhesives and Bonding Methods
When manufacturing a boat primarily from non-metallic materials, the selection and application of adhesives and bonding methods become crucial for ensuring structural integrity, durability, and performance. Non-metallic materials such as fiberglass, carbon fiber, and various polymers are commonly used in boat construction due to their lightweight yet robust properties. However, these materials require specialized adhesives that can effectively bond them together without compromising their inherent strengths. Adhesives play a pivotal role in this context as they must provide strong mechanical bonds while also being resistant to environmental factors such as moisture, UV exposure, and extreme temperatures. Epoxy resins are among the most popular choices for bonding non-metallic materials in boat construction. These resins offer excellent mechanical strength, chemical resistance, and flexibility, making them ideal for applications where high performance is required. Additionally, polyurethane adhesives are also widely used due to their versatility and ability to bond a variety of substrates. The bonding methods employed are equally important. Mechanical fastening techniques can be used in conjunction with adhesives to enhance the overall strength of the bond. However, for many non-metallic materials, mechanical fasteners can introduce stress concentrations that may lead to material failure over time. Therefore, advanced bonding techniques such as vacuum bagging or resin infusion are often preferred. These methods ensure uniform distribution of the adhesive and minimize air pockets or voids that could weaken the bond. Innovative technologies like structural adhesives and advanced composites have further enhanced the capabilities of non-metallic boat construction. These materials allow for the creation of complex geometries and optimized structural designs that would be difficult or impossible to achieve with traditional metallic materials. Moreover, the use of advanced adhesives has enabled the integration of multiple components into a single monolithic structure, reducing weight while maintaining or even increasing overall strength. In summary, when constructing a boat from mostly non-metallic materials, the careful selection and application of appropriate adhesives and bonding methods are essential. By leveraging high-performance adhesives such as epoxy resins and polyurethane adhesives, combined with advanced bonding techniques like vacuum bagging or resin infusion, manufacturers can create robust and durable structures that meet the demanding requirements of marine environments. This approach not only ensures the longevity of the boat but also contributes to its overall performance and efficiency.
3. Quality Control and Testing
In the realm of manufacturing and construction, particularly when a boat is made of mostly non-metallic materials, quality control and testing are paramount to ensure the vessel's durability, safety, and performance. Non-metallic materials such as fiberglass, carbon fiber, and advanced polymers offer unique advantages like reduced weight and enhanced corrosion resistance but also present distinct challenges. Quality control begins at the material selection stage, where suppliers must be vetted for consistency and quality. This involves rigorous testing of raw materials to verify their mechanical properties, such as tensile strength, flexural strength, and impact resistance. Once materials are approved, the manufacturing process itself must adhere to strict standards. For instance, in the case of fiberglass boats, the layup process—where layers of fiberglass and resin are applied—must be meticulously controlled to avoid defects like voids or delamination. Testing is a critical phase that follows quality control. Non-destructive testing (NDT) methods such as ultrasonic inspection and radiography are employed to detect any internal flaws without damaging the structure. Additionally, destructive testing may be conducted on sample pieces to evaluate the material's ultimate strength and failure modes. Environmental testing is also essential; boats made from non-metallic materials must withstand various conditions including exposure to sunlight, saltwater, and extreme temperatures. Functional testing is another crucial aspect where the boat's systems are evaluated under operational conditions. This includes testing of propulsion systems, steering mechanisms, and electrical systems to ensure they function seamlessly with the non-metallic hull. Furthermore, performance trials are conducted to assess the boat's speed, maneuverability, and stability in different water conditions. Compliance with industry standards and regulations is also a key component of quality control and testing. Organizations such as the American Boat and Yacht Council (ABYC) and the International Organization for Standardization (ISO) provide guidelines that manufacturers must follow to guarantee safety and reliability. By integrating these rigorous quality control measures and comprehensive testing protocols into the manufacturing process, boat builders can deliver high-quality vessels that meet or exceed customer expectations while ensuring safety at sea. In summary, when constructing a boat primarily from non-metallic materials, a robust quality control and testing regimen is indispensable. This involves meticulous material selection, adherence to manufacturing standards, thorough non-destructive and destructive testing, environmental and functional evaluations, and compliance with industry regulations. Such a multifaceted approach ensures that the final product is not only aesthetically pleasing but also robust, reliable, and safe for its intended use.
Performance and Maintenance
In the realm of engineering and technology, the performance and maintenance of systems and structures are paramount for ensuring efficiency, reliability, and longevity. These critical aspects are multifaceted, involving several key components that collectively contribute to optimal functioning. First, hydrodynamic efficiency plays a crucial role in systems that interact with fluids, such as pipelines, turbines, and marine vessels, where minimizing drag and maximizing flow can significantly impact overall performance. Second, resistance to environmental factors is essential for withstanding the harsh conditions that many systems face, including extreme temperatures, corrosive substances, and physical stress. Third, effective maintenance and repair strategies are vital for sustaining performance over time, preventing failures, and extending the lifespan of equipment. Understanding these elements is not only crucial for operational success but also informs design and material selection decisions, as the choice of materials and design principles can significantly influence a system's hydrodynamic efficiency, environmental resilience, and maintenance requirements. By delving into these areas, we can better appreciate the intricate balance between performance and maintenance, ultimately guiding more informed design and material selection processes.
1. Hydrodynamic Efficiency
When a boat is constructed primarily from non-metallic materials, such as fiberglass, carbon fiber, or advanced polymers, hydrodynamic efficiency becomes a critical factor in its performance and maintenance. Hydrodynamic efficiency refers to the ability of the boat's hull to move through water with minimal resistance, thereby optimizing speed and fuel efficiency. For non-metallic boats, several key considerations are essential to achieve and maintain high hydrodynamic efficiency. Firstly, the design of the hull must be meticulously engineered to reduce drag. This involves creating a smooth, aerodynamic shape that allows water to flow effortlessly around the hull. Non-metallic materials offer the advantage of being lightweight and flexible, which can be leveraged to create complex geometries that enhance hydrodynamic performance. Additionally, these materials can be molded into precise shapes that minimize turbulence and maximize laminar flow. Secondly, surface finish plays a crucial role. A smooth, glossy finish on the hull surface reduces frictional drag, allowing the boat to cut through the water more efficiently. Regular maintenance is necessary to ensure that the hull remains free from fouling organisms and debris, which can significantly impede performance. Non-metallic materials are often more resistant to fouling than metallic ones, but they still require periodic cleaning and application of anti-fouling coatings to maintain optimal hydrodynamic efficiency. Furthermore, weight distribution is vital for hydrodynamic efficiency. Non-metallic boats tend to be lighter than their metallic counterparts, which can improve overall performance by reducing the energy required to propel the boat through the water. However, it is crucial to ensure that the weight distribution is balanced to maintain stability and prevent excessive pitching or yawing, which can disrupt the flow around the hull. In terms of maintenance, regular inspections are necessary to identify any damage or wear on the hull that could compromise hydrodynamic efficiency. Non-metallic materials are generally more resistant to corrosion but can be prone to scratches or cracks that need prompt attention. Repairing these issues promptly not only maintains performance but also prevents more severe damage from occurring over time. In conclusion, achieving high hydrodynamic efficiency in a boat made primarily of non-metallic materials requires careful design, meticulous maintenance, and attention to detail. By leveraging the advantages of these materials—such as their lightweight nature and resistance to fouling—and ensuring a smooth hull surface, balanced weight distribution, and regular upkeep, boat owners can optimize their vessel's performance and enjoy enhanced speed and fuel efficiency on the water. This focus on hydrodynamic efficiency is integral to the broader theme of performance and maintenance, underscoring the importance of these factors in maximizing the overall capabilities of a non-metallic boat.
2. Resistance to Environmental Factors
When a boat is constructed primarily from non-metallic materials, such as fiberglass, carbon fiber, or advanced polymers, resistance to environmental factors becomes a critical aspect of its performance and maintenance. Non-metallic materials offer several advantages over traditional metallic ones, including reduced weight, improved corrosion resistance, and enhanced durability. However, they also present unique challenges that must be addressed to ensure the boat's longevity and optimal performance. First and foremost, non-metallic boats are more susceptible to damage from UV radiation. Prolonged exposure to sunlight can cause the material to degrade, leading to discoloration, brittleness, and eventual cracking. To mitigate this, manufacturers often apply specialized coatings or gelcoats that provide UV protection. Regular maintenance involves inspecting these coatings for any signs of wear and applying additional protective layers as needed. Another environmental factor that non-metallic boats must contend with is water absorption. While these materials are generally more resistant to water than metals, they can still absorb moisture over time, particularly if there are any cracks or breaches in the surface. This can lead to weight gain, reduced buoyancy, and structural weakening. To prevent this, it is essential to maintain a watertight seal and address any damage promptly. Regular inspections for signs of water intrusion and ensuring that all fittings and fasteners are securely sealed are crucial. In addition to UV and water resistance, non-metallic boats also need protection against mechanical stress and impact. These materials can be prone to scratches and dings, which can compromise their integrity. Applying protective films or paints can help safeguard against minor impacts, while more significant damage should be repaired immediately to prevent further deterioration. Finally, non-metallic boats require careful handling during storage and transportation to avoid damage from extreme temperatures and physical stress. Storing the boat in a shaded area or using covers can protect it from direct sunlight, while ensuring that it is properly supported during transportation can prevent flexing or bending that could cause structural damage. In summary, while non-metallic materials offer numerous benefits for boat construction, they demand specific care and maintenance to resist environmental factors effectively. By understanding and addressing these needs—such as protecting against UV radiation, preventing water absorption, safeguarding against mechanical stress, and ensuring proper storage and transportation—boat owners can ensure their vessel remains in optimal condition for years to come. This proactive approach not only enhances the boat's performance but also extends its lifespan, making it a worthwhile investment for any maritime enthusiast.
3. Maintenance and Repair Strategies
When a boat is primarily constructed from non-metallic materials such as fiberglass, carbon fiber, or advanced polymers, the maintenance and repair strategies differ significantly from those for metal-hulled vessels. Here, the focus shifts to preserving the integrity of these materials and addressing unique challenges they present. **Inspection and Cleaning**: Regular inspections are crucial to identify any signs of damage or wear early on. Non-metallic surfaces are more prone to scratches and cracks, which can compromise their structural integrity. Cleaning these surfaces requires gentle methods to avoid damaging the material. Soft cloths, mild detergents, and freshwater should be used to remove dirt and grime without scratching the surface. **Protection from UV Damage**: Non-metallic materials are highly susceptible to ultraviolet (UV) degradation, which can cause them to become brittle and crack over time. Applying a high-quality marine wax or protective coating can help shield these surfaces from UV rays. Additionally, using canvas covers or sunshades when the boat is not in use can provide extra protection. **Repair Techniques**: When repairs are necessary, specialized techniques and materials must be employed. For example, fiberglass repairs often involve using epoxy resins and fiberglass mats to patch damaged areas. Carbon fiber repairs may require more advanced methods such as vacuum bagging or autoclaving to ensure proper bonding and strength restoration. It is essential to follow manufacturer guidelines and consult with experienced professionals if you are not familiar with these repair processes. **Moisture Management**: Non-metallic materials can absorb moisture, leading to issues like blistering in fiberglass hulls or delamination in composite structures. Ensuring that all through-hull fittings are properly sealed and that any water intrusion is promptly addressed is vital. Regularly inspecting for signs of moisture ingress and maintaining a dry bilge area are key preventive measures. **Specialized Tools and Materials**: Unlike metal repairs, which often involve welding or metalworking tools, non-metallic repairs require specialized tools such as gelcoat sanders, fiberglass choppers, and vacuum pumps. The right materials like marine-grade epoxies, polyurethane paints, and compatible fillers must also be used to ensure durable and long-lasting repairs. By adopting these tailored maintenance and repair strategies, boat owners can extend the lifespan of their non-metallic vessels while maintaining their performance and aesthetic appeal. Regular upkeep not only prevents costly repairs but also enhances safety by ensuring that the boat remains seaworthy and reliable. Whether you're dealing with routine cleaning or more complex repairs, understanding the unique needs of non-metallic materials is essential for optimal boat care.