What Is The Correct Order Of Elements In The Whmis Classification System

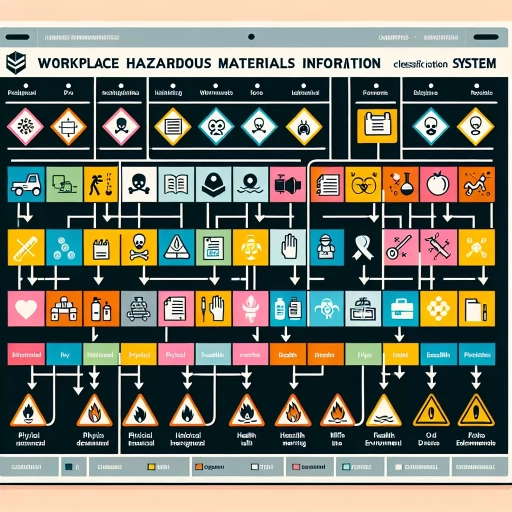
The Workplace Hazardous Materials Information System (WHMIS) is a crucial framework for managing and communicating the hazards associated with chemical substances in Canadian workplaces. Understanding the correct order of elements within the WHMIS classification system is essential for ensuring safety, compliance, and effective risk management. This article delves into the intricacies of WHMIS, starting with a comprehensive overview of the WHMIS classification system, which sets the foundation for understanding its components and their significance. We will then explore the correct order of elements in WHMIS classification, highlighting the specific criteria and categories that define hazardous substances. Finally, we will discuss the practical application and compliance aspects of WHMIS, emphasizing how these principles are applied in real-world scenarios to safeguard workers and maintain regulatory adherence. By grasping these key concepts, individuals can better navigate the complexities of WHMIS and contribute to a safer work environment. Let's begin by understanding the WHMIS classification system.
Understanding the WHMIS Classification System
In the realm of workplace safety, few systems are as crucial as the Workplace Hazardous Materials Information System (WHMIS). This comprehensive framework is designed to protect workers from the dangers associated with hazardous materials. To fully grasp the significance of WHMIS, it is essential to delve into its core components and historical development. This article will provide an **Overview of WHMIS and Its Importance**, highlighting how this system has become a cornerstone of occupational health and safety in Canada. We will also explore the **Key Components of the WHMIS Classification**, detailing how substances are categorized and communicated to ensure safe handling. Additionally, we will examine the **Historical Context and Evolution of WHMIS**, tracing its development from inception to its current form. By understanding these facets, readers will gain a deeper appreciation for the intricacies of the WHMIS classification system, ultimately enhancing their ability to navigate and apply it effectively in their workplaces. This knowledge is pivotal for ensuring a safe and compliant work environment, making it imperative to **Understand the WHMIS Classification System**.
Overview of WHMIS and Its Importance
**Overview of WHMIS and Its Importance** The Workplace Hazardous Materials Information System (WHMIS) is a critical component of workplace safety in Canada, designed to protect workers from the hazards associated with chemical products. Implemented in 1988, WHMIS is a collaborative effort between the federal, provincial, and territorial governments to ensure that workers are informed about the dangers of hazardous materials they handle. The system is based on a comprehensive framework that includes classification, labeling, safety data sheets (SDSs), and worker training. At its core, WHMIS classifies hazardous products into categories based on their physical and health hazards. This classification system is pivotal as it helps in identifying the potential risks associated with each product, enabling employers to implement appropriate safety measures and provide necessary training to their employees. The labels and SDSs that accompany these products serve as essential tools for communicating hazard information. Labels provide immediate visual warnings and critical safety information, while SDSs offer detailed data on the safe handling, use, storage, and emergency procedures for each product. The importance of WHMIS cannot be overstated. By ensuring that workers are well-informed about the hazards they face, WHMIS significantly reduces the risk of workplace injuries and illnesses. It also fosters a culture of safety within organizations, encouraging responsible handling and use of hazardous materials. Compliance with WHMIS regulations is mandatory for employers, making it a legal requirement to protect both employees and the environment. Furthermore, WHMIS aligns with international standards such as the Globally Harmonized System of Classification and Labelling of Chemicals (GHS), enhancing its global relevance and effectiveness. In summary, WHMIS is a vital system that underpins workplace safety by providing a structured approach to managing hazardous materials. Its classification system, labeling requirements, and training components work together to safeguard workers and promote a safer working environment. Understanding the WHMIS classification system is essential for anyone handling hazardous materials, as it forms the foundation of effective risk management and compliance with regulatory standards. By adhering to WHMIS guidelines, employers can ensure a safer workplace, reduce the incidence of accidents, and protect their employees from the potential dangers of hazardous substances. **Correct Order of Elements in the WHMIS Classification System:** 1. **Classification:** Identify the physical and health hazards of the product. 2. **Labeling:** Apply labels that include hazard symbols, risk phrases, and precautionary statements. 3. **Safety Data Sheets (SDSs):** Prepare detailed sheets providing comprehensive safety information. 4. **Training:** Educate workers on the safe handling, use, and emergency procedures for hazardous products. Understanding this sequence is crucial for effective implementation of WHMIS in any workplace setting.
Key Components of the WHMIS Classification
The WHMIS (Workplace Hazardous Materials Information System) classification system is a comprehensive framework designed to ensure the safe handling and use of hazardous materials in Canadian workplaces. At its core, the WHMIS classification system is structured around several key components that work together to provide a clear and consistent method for identifying and communicating the hazards associated with chemical substances. First, **hazard classification** is the foundational element, where substances are categorized based on their physical, health, and environmental hazards. This involves evaluating the substance's properties and potential risks to determine its classification into one or more hazard classes such as flammable gases, toxic substances, or corrosive materials. Next, **hazard categories** further refine these classifications by specifying the severity of the hazard within each class. For example, a substance classified as a flammable liquid might be categorized as highly flammable (Category 1) or moderately flammable (Category 3). This tiered approach allows for a more nuanced understanding of the risks involved. Following classification and categorization, **Safety Data Sheets (SDSs)** play a crucial role in providing detailed information about the substance's hazards, safe handling practices, emergency procedures, and first aid measures. These documents are essential for employers and workers to understand how to safely manage hazardous materials. Another critical component is **labels**, which serve as immediate visual indicators of the hazards present. Labels must include specific information such as the product identifier, hazard statements, precautionary statements, and pictograms that graphically represent the type of hazard (e.g., explosion, toxicity). Finally, **worker training** is an integral part of the WHMIS system. Employers are required to educate workers on how to read and understand SDSs and labels, as well as how to handle substances safely according to their classifications. This ensures that all personnel are equipped with the knowledge necessary to mitigate risks and respond effectively in case of emergencies. In summary, the correct order of elements in the WHMIS classification system begins with hazard classification into specific classes based on physical, health, and environmental risks. These classifications are then further detailed through hazard categories that specify the severity of each hazard. Safety Data Sheets provide comprehensive information for safe handling practices, while labels serve as quick reference points for identifying hazards. Ultimately, worker training ensures that all personnel are knowledgeable about these components and can apply this understanding in their daily work environments to maintain a safe workplace.
Historical Context and Evolution of WHMIS
The Historical Context and Evolution of WHMIS (Workplace Hazardous Materials Information System) is a narrative that underscores the progressive efforts to enhance workplace safety in Canada. WHMIS was first introduced in 1988 as a response to the growing concern over the handling and use of hazardous materials in workplaces. This system was designed to provide workers with critical information about the hazards associated with the chemicals they use, thereby reducing the risk of injuries and illnesses. Initially, WHMIS was based on the U.S. Hazard Communication Standard (HCS), but it quickly evolved to include unique Canadian standards and regulations. In its early stages, WHMIS focused on ensuring that workers had access to Material Safety Data Sheets (MSDSs) and labels that provided essential information about chemical hazards. However, as global standards for chemical safety continued to evolve, so did WHMIS. The most significant transformation came with the alignment of WHMIS with the Globally Harmonized System of Classification and Labelling of Chemicals (GHS) in 2015. This alignment, known as WHMIS 2015, introduced new classification criteria, standardized label elements, and Safety Data Sheets (SDSs) to replace MSDSs. The evolution of WHMIS has been marked by several key milestones. The initial phase saw the establishment of a national standard for hazard communication, which mandated that all hazardous materials be classified, labeled, and accompanied by an MSDS. As scientific understanding of chemical hazards improved, so did the classification criteria. The transition to WHMIS 2015 brought about a more comprehensive and harmonized approach, aligning Canada's system with international best practices. This change included the adoption of standardized pictograms, hazard statements, and precautionary statements on labels and SDSs. Throughout its evolution, WHMIS has remained committed to its core principle: ensuring that workers are adequately informed about the hazards they encounter in their workplaces. The system's continuous improvement reflects a collaborative effort between government agencies, industry stakeholders, and labor organizations to create a safer work environment. Understanding the WHMIS classification system is crucial for anyone working with hazardous materials, as it provides a structured framework for identifying and mitigating risks. By grasping the historical context and evolution of WHMIS, individuals can better appreciate the importance of this system in safeguarding health and safety in Canadian workplaces. In summary, the correct order of elements in the WHMIS classification system involves several key steps: **identification of the substance**, **classification based on hazard criteria**, **labeling with standardized elements**, and **provision of a Safety Data Sheet**. This structured approach ensures that workers are well-informed and equipped to handle hazardous materials safely, reflecting the ongoing commitment to workplace safety that has defined the evolution of WHMIS.
The Correct Order of Elements in WHMIS Classification
The Workplace Hazardous Materials Information System (WHMIS) is a critical framework for ensuring the safe handling and use of hazardous materials in Canadian workplaces. At the heart of WHMIS is the classification system, which categorizes substances based on their potential hazards. Understanding the correct order of elements in WHMIS classification is essential for effective risk management and compliance. This article delves into the intricacies of WHMIS classification, focusing on three key areas: **Classification Criteria for Physical Hazards**, **Classification Criteria for Health Hazards**, and **Classification Criteria for Environmental Hazards**. By examining these criteria, we will gain a comprehensive understanding of how substances are categorized and why this classification is vital. This knowledge is crucial for employers, workers, and anyone involved in the handling of hazardous materials, as it directly impacts safety protocols and regulatory adherence. In this article, we will explore each of these classification criteria in detail, ultimately leading to a deeper understanding of the WHMIS classification system.
Classification Criteria for Physical Hazards
When navigating the complexities of the Workplace Hazardous Materials Information System (WHMIS), understanding the classification criteria for physical hazards is crucial. Physical hazards in WHMIS are categorized based on their potential to cause harm through physical means, distinct from health hazards which focus on toxicological effects. The primary categories under physical hazards include flammable gases, flammable aerosols, oxidizing gases, gases under pressure, flammable liquids, flammable solids, self-reactive substances, pyrophoric liquids and solids, self-heating substances, substances which, in contact with water, emit flammable gases, oxidizing liquids and solids, corrosive to metals, and explosive substances. Each of these categories has specific criteria that must be met for a substance to be classified within it. For instance, flammable gases are those that can ignite in air at temperatures below 60°C and have a flammable range with air of at least 12% by volume. Flammable liquids are classified based on their flash point and boiling point; they must have a flash point below 93°C to be considered highly flammable. Oxidizing substances are those that can cause or enhance the combustion of other materials, while gases under pressure are classified based on their physical state and the pressure they are stored under. The classification process involves a series of tests and evaluations to determine the hazard potential of a substance. For example, self-reactive substances are tested for their thermal stability and propensity to undergo a strongly exothermic decomposition. Pyrophoric substances are those that ignite spontaneously in air at temperatures below 54°C. Substances that emit flammable gases upon contact with water are evaluated for their reactivity with water. Understanding these classification criteria is essential for the correct order of elements in WHMIS classification. The order typically follows a logical sequence starting with the most severe hazards: explosive substances, followed by flammable gases and aerosols, then oxidizing gases and substances, and so on. This hierarchical approach ensures that the most critical hazards are addressed first, thereby enhancing workplace safety and compliance with regulatory standards. In summary, the classification criteria for physical hazards in WHMIS are meticulously defined to ensure accurate identification and communication of potential dangers. By adhering to these criteria and following the correct order of elements, employers can effectively manage risks, provide appropriate training, and ensure a safer working environment for all employees. This systematic approach is fundamental to the overall effectiveness of the WHMIS classification system.
Classification Criteria for Health Hazards
The Classification Criteria for Health Hazards play a crucial role in the Workplace Hazardous Materials Information System (WHMIS) classification process, ensuring that workers are adequately informed about the potential risks associated with the chemicals they handle. These criteria are meticulously designed to categorize substances based on their potential to cause harm to human health. The health hazard classification under WHMIS is divided into several key categories, each with specific criteria that must be met for a substance to be classified within that category. Firstly, **Toxicity** is a primary classification criterion, where substances are evaluated based on their ability to cause harm through ingestion, inhalation, or skin contact. This includes acute toxicity, which refers to the adverse effects resulting from a single exposure, as well as chronic toxicity, which involves long-term exposure leading to health issues such as cancer or reproductive problems. Substances are classified into different toxicity categories based on their LD50 (the dose required to kill 50% of test subjects) or LC50 (the concentration required to kill 50% of test subjects). Another critical criterion is **Mutagenicity**, which involves the ability of a substance to cause genetic mutations. Substances that are mutagenic can lead to heritable genetic damage and are classified accordingly. **Carcinogenicity** is also a significant classification criterion, focusing on substances that have the potential to cause cancer. These substances are categorized based on evidence from human studies and animal experiments. **Reproductive Toxicity** is another key area, where substances are evaluated for their potential to affect fertility or cause developmental toxicity. This includes effects on both male and female reproductive systems as well as the development of the fetus during pregnancy. **Respiratory Sensitization** and **Skin Sensitization** are additional criteria, where substances are classified based on their ability to induce allergic reactions in the respiratory system or skin. These sensitizers can cause severe reactions upon subsequent exposure. **Target Organ Toxicity** involves substances that can cause damage to specific organs or organ systems, such as the liver, kidneys, or nervous system. This classification helps in identifying substances that may pose long-term health risks even at low exposure levels. Lastly, **Aspiration Hazard** is considered for substances that can cause lung damage if inhaled into the lungs, often due to their physical properties like viscosity and surface tension. Understanding these classification criteria is essential for the correct order of elements in WHMIS classification. By systematically evaluating each criterion, employers and workers can ensure that hazardous materials are properly labeled and handled, reducing the risk of adverse health effects. This structured approach not only enhances workplace safety but also aligns with international standards for chemical hazard communication, making it a cornerstone of effective occupational health and safety practices.
Classification Criteria for Environmental Hazards
When navigating the complexities of the Workplace Hazardous Materials Information System (WHMIS) classification, understanding the classification criteria for environmental hazards is crucial. Environmental hazards, as defined by WHMIS, pertain to substances that can harm aquatic life, persist in the environment, or bioaccumulate. The correct classification of these hazards ensures that workers and the environment are adequately protected. The classification criteria for environmental hazards are based on several key factors. First, **aquatic toxicity** is assessed to determine if a substance can cause harm to aquatic organisms. This involves evaluating the substance's potential to be toxic to fish, invertebrates, and algae. Substances that exhibit high toxicity to these organisms are classified accordingly. Second, **persistence** in the environment is evaluated. Persistent substances do not readily break down and can remain in the environment for extended periods, posing long-term risks. This criterion helps identify substances that may accumulate over time and cause ongoing harm. Third, **bioaccumulation** potential is considered. Bioaccumulative substances tend to accumulate in living organisms and can be passed up the food chain, leading to significant environmental and health impacts. The bioaccumulation factor (BAF) or bioconcentration factor (BCF) is often used to quantify this potential. Lastly, **mobility** and **degradability** are also important considerations. Substances that are highly mobile in the environment or resistant to degradation pose greater risks due to their ability to spread and persist. By carefully evaluating these criteria, substances can be accurately classified under WHMIS as either "Toxic to Aquatic Life," "Persistent," "Bioaccumulative," or a combination thereof. This classification informs the development of safety data sheets (SDSs), labels, and other safety measures that protect workers from exposure and mitigate environmental impacts. Ensuring the correct order of elements in WHMIS classification—starting with physical hazards, followed by health hazards, and then environmental hazards—ensures a comprehensive approach to managing workplace and environmental risks. This systematic approach ensures that all relevant hazards are identified and addressed, providing a robust framework for safe handling and use of hazardous materials.
Practical Application and Compliance with WHMIS
In the realm of workplace safety, the Workplace Hazardous Materials Information System (WHMIS) stands as a cornerstone for ensuring the safe handling and use of hazardous materials. This comprehensive system is designed to protect workers from the dangers associated with chemical substances, making it imperative for employers and employees alike to understand its practical applications and compliance requirements. At the heart of WHMIS compliance are three critical components: **Labeling and Signage Requirements**, which ensure that hazardous materials are clearly identified; **Safety Data Sheets (SDS) and Their Role**, which provide detailed information on the safe use, handling, and emergency procedures for these substances; and **Training and Education for Workplace Compliance**, which equip workers with the knowledge needed to handle hazardous materials safely. By delving into these aspects, organizations can ensure a safer work environment and adhere to regulatory standards. Understanding these elements is crucial for transitioning smoothly into the more nuanced **Understanding the WHMIS Classification System**, which forms the foundation of effective hazard management and compliance. This article will explore each of these key areas in depth, providing a comprehensive guide to practical application and compliance with WHMIS.
Labeling and Signage Requirements
Labeling and signage are crucial components of the Workplace Hazardous Materials Information System (WHMIS), ensuring that workers are adequately informed about the hazards associated with the chemicals they handle. The correct order of elements in the WHMIS classification system is pivotal for effective labeling and signage. Here, we delve into the practical application and compliance aspects of these requirements. First, it is essential to understand that WHMIS categorizes hazardous products based on their physical and health hazards. The classification system involves identifying the hazard class and category, which then dictates the specific labeling and signage needs. For instance, physical hazards include flammable gases, liquids, and solids, while health hazards encompass toxic substances and biohazardous materials. Each hazard class has multiple categories that reflect the severity of the hazard. Once a product is classified, the next step is to ensure proper labeling. WHMIS labels must include specific information: the product identifier, hazard statements, precautionary statements, and pictograms. The product identifier is the name or identifier of the hazardous product as it appears on the Safety Data Sheet (SDS). Hazard statements describe the nature of the hazard, while precautionary statements provide advice on how to minimize or prevent adverse effects. Pictograms are standardized symbols that visually communicate the type of hazard. Signage also plays a critical role in WHMIS compliance. Hazardous materials storage areas, for example, must be clearly marked with signs indicating the types of hazards present. These signs should include the same pictograms found on the labels to maintain consistency and ensure immediate recognition by workers. Additionally, signs should be placed in areas where workers are likely to see them, such as near storage rooms or at entrances to hazardous areas. Compliance with WHMIS labeling and signage requirements is not just a regulatory necessity but also a key factor in workplace safety. Employers must ensure that all hazardous products are properly labeled and that signage is maintained in good condition. Regular training programs for employees on how to read and understand WHMIS labels and signs are also mandatory. This training helps workers recognize potential hazards quickly and take appropriate actions to protect themselves and others. In summary, the correct order of elements in the WHMIS classification system—hazard class, category, labeling, and signage—forms the backbone of practical application and compliance. By adhering to these guidelines, workplaces can significantly reduce the risk of accidents and ensure a safer environment for all employees. Effective labeling and signage are not just legal requirements; they are essential tools in preventing injuries and illnesses related to hazardous materials.
Safety Data Sheets (SDS) and Their Role
Safety Data Sheets (SDS) are pivotal documents in the realm of workplace safety, particularly under the Workplace Hazardous Materials Information System (WHMIS). These sheets provide comprehensive information about the safe handling, use, storage, and disposal of hazardous products. The correct order of elements in the WHMIS classification system is crucial for understanding and utilizing SDS effectively. 1. **Classification**: The first step involves classifying the hazardous product based on its physical and health hazards. This includes categorizing substances into classes such as flammable gases, toxic substances, or corrosive materials. 2. **Labeling**: Once classified, products must be labeled with specific information that includes the product identifier, hazard statements, precautionary statements, and pictograms. 3. **Safety Data Sheets (SDS)**: For each classified product, an SDS must be prepared. The SDS is a detailed document that outlines the product's hazards, safe handling practices, emergency procedures, and regulatory information. The SDS plays a critical role in compliance with WHMIS by ensuring that workers have access to essential safety information. Here’s how it supports practical application and compliance: - **Section 1: Identification** - Provides the product identifier, manufacturer's name, and contact information. - **Section 2: Hazard Identification** - Lists the classification of the substance, hazard statements, and pictograms. - **Section 3: Composition/Information on Ingredients** - Details the chemical composition of the product. - **Section 4: First Aid Measures** - Outlines procedures for treating exposure to the substance. - **Section 5: Fire-Fighting Measures** - Describes how to extinguish fires involving the product. - **Section 6: Accidental Release Measures** - Offers guidance on spill response and cleanup. - **Section 7: Handling and Storage** - Recommends safe handling practices and storage conditions. - **Section 8: Exposure Controls/Personal Protection** - Specifies exposure limits and personal protective equipment (PPE) requirements. - **Section 9: Physical and Chemical Properties** - Lists physical and chemical properties of the substance. - **Section 10: Stability and Reactivity** - Discusses stability and potential reactivity hazards. - **Section 11: Toxicological Information** - Provides data on the substance's toxicological effects. - **Section 12: Ecological Information** - Addresses environmental impacts. - **Section 13: Disposal Considerations** - Offers guidelines for safe disposal. - **Section 14: Transport Information** - Includes information relevant to transportation regulations. - **Section 15: Regulatory Information** - Summarizes relevant regulatory requirements. - **Section 16: Other Information** - Contains any additional relevant information. By adhering to this structured format, SDS ensures that all necessary safety information is readily available to workers, thereby enhancing workplace safety and compliance with WHMIS regulations. Employers must ensure that SDS are accessible to all employees who handle hazardous materials, fostering a culture of safety and adherence to regulatory standards. This systematic approach not only protects workers but also helps organizations avoid legal and financial repercussions associated with non-compliance.
Training and Education for Workplace Compliance
Training and education are pivotal components in ensuring workplace compliance, particularly when it comes to Practical Application and Compliance with WHMIS (Workplace Hazardous Materials Information System). The correct order of elements in the WHMIS classification system is crucial for effective training. Here’s how it aligns: 1. **Classification**: The first step involves classifying hazardous products based on their physical and health hazards. This includes categorizing substances into various hazard classes such as flammable gases, toxic substances, or corrosive materials. 2. **Labels**: Once a product is classified, it must be labeled accordingly. Labels provide critical information about the hazards associated with the product and include pictograms, hazard statements, precautionary statements, and supplier identifiers. 3. **Safety Data Sheets (SDSs)**: These detailed documents provide comprehensive information about the safe handling, use, storage, and disposal of hazardous products. They are essential for workers who need to understand the specific risks and necessary precautions. 4. **Training**: Effective training is the backbone of WHMIS compliance. Employees must be trained to recognize and understand the information provided on labels and SDSs. This includes knowing how to handle emergencies, use personal protective equipment (PPE), and follow safe work practices. 5. **Program Implementation**: The final element involves implementing a WHMIS program within the workplace. This includes ensuring that all hazardous materials are properly labeled and that SDSs are readily available. Regular training sessions and updates are also necessary to maintain compliance. By following this order, workplaces can ensure that employees are well-equipped to handle hazardous materials safely. Training programs should be engaging, informative, and tailored to the specific needs of the workforce. They should include practical demonstrations, quizzes, and hands-on exercises to reinforce learning. Additionally, ongoing education and refresher courses are essential to keep employees up-to-date with any changes in regulations or new hazards introduced into the workplace. In summary, a robust training and education program is indispensable for maintaining compliance with WHMIS. By adhering to the correct order of classification, labeling, SDSs, training, and program implementation, workplaces can significantly reduce the risk of accidents and ensure a safer environment for all employees. This structured approach not only meets regulatory requirements but also fosters a culture of safety and responsibility within the organization.