What Is The Key Difference Between Inkjet And Other Print Processes

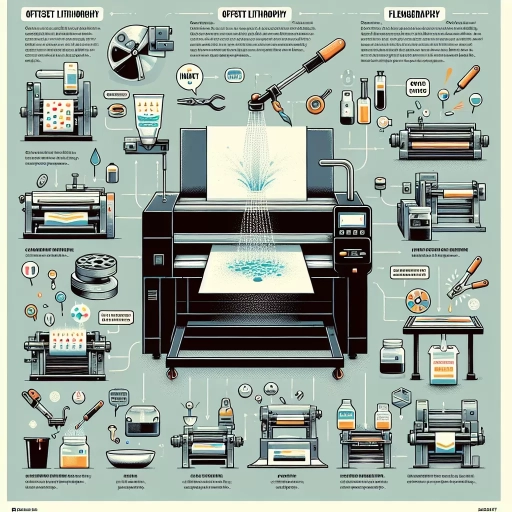
1. Printing Technology and Mechanism
Printing technology has evolved significantly over the years, transforming the way we produce high-quality documents and images. At the heart of this advancement lies a complex mechanism that involves several critical components. This article delves into the intricacies of printing technology, focusing on three key aspects: the design of inkjet print heads, the process of droplet formation and placement, and the interaction between paper and ink. Understanding these elements is crucial for appreciating the precision and efficiency of modern printing systems. Firstly, the design of inkjet print heads is a cornerstone of printing technology. These heads are responsible for delivering tiny droplets of ink onto the paper with remarkable accuracy. The intricate architecture of these heads, including the nozzles and piezoelectric elements, ensures that each droplet is precisely controlled, leading to high-resolution prints. This precision is what sets modern inkjet printers apart from their predecessors. Transitioning to the specifics of inkjet print head design, it becomes clear that this component is the linchpin of the entire printing process. The design of these heads dictates the quality and speed of printing, making it a focal point for innovation in the field. By exploring the intricacies of inkjet print head design, we can gain a deeper understanding of how printing technology continues to evolve and improve. --- **1.1. Inkjet Print Head Design** The design of inkjet print heads is a marvel of engineering, combining microelectronics and fluid dynamics to achieve unparalleled print quality. These heads consist of a series of tiny nozzles, each capable of ejecting droplets of ink as small as a few picoliters. The nozzles are typically arranged in a linear array, allowing for precise control over the placement of each droplet. The mechanism behind this precision involves piezoelectric elements that deform when an electric charge is applied, forcing ink through the nozzles. This technology enables high-resolution printing with minimal waste and maximum efficiency. Understanding the design of inkjet print heads provides insight into the foundational principles that drive modern printing technology.
1.1. Inkjet Print Head Design
Inkjet print head design is a critical component of inkjet printing technology, distinguishing it from other print processes such as laser, offset, and screen printing. At the heart of an inkjet printer lies the print head, which is responsible for ejecting tiny droplets of ink onto the printing medium. The design of the print head is what sets inkjet apart in terms of precision, flexibility, and cost-effectiveness. The print head in an inkjet printer consists of a series of tiny nozzles, each capable of producing droplets as small as a few picoliters. These nozzles are arranged in a linear array or matrix, depending on the type of printer. There are two primary types of inkjet print heads: piezoelectric and thermal. Piezoelectric print heads use piezoelectric materials that change shape when an electric charge is applied, creating pressure waves that expel ink droplets. Thermal print heads, on the other hand, use heat to create vapor bubbles in the ink, which then force the ink out through the nozzles. The precision and control over droplet size and placement are key advantages of inkjet technology. This allows for high-resolution printing with intricate details and vibrant colors. Unlike laser printing, which uses a toner-based system to create images by attracting toner particles to a drum, inkjet printing directly deposits ink onto the paper. This direct deposition method eliminates the need for intermediate steps like toner transfer and fusing, making it more straightforward and less energy-intensive. Moreover, inkjet print heads can be designed to accommodate various types of ink formulations, including dye-based, pigment-based, and even specialized inks like metallic or UV-curable inks. This versatility makes inkjet printing suitable for a wide range of applications, from standard office documents to high-end photographic prints and industrial labeling. In contrast to offset printing, which involves transferring ink from metal plates to rubber blankets before finally reaching the paper, inkjet printing does not require any physical contact between the print head and the printing surface. This non-contact method reduces wear and tear on the print head and eliminates the need for frequent plate replacements, making it more cost-effective for short-run or variable data printing jobs. Additionally, modern advancements in inkjet print head design have led to the development of high-speed and high-resolution printers capable of producing professional-grade output at lower costs than traditional methods. For instance, printheads with integrated circuits can control each nozzle independently, allowing for precise control over droplet size and placement at speeds that rival those of commercial printing presses. In summary, the innovative design of inkjet print heads underpins the unique advantages of inkjet printing technology. By enabling precise droplet ejection without physical contact with the printing surface, inkjet print heads offer unparalleled flexibility, resolution, and cost-effectiveness compared to other print processes. This makes inkjet printing an indispensable tool across various industries, from consumer electronics to industrial manufacturing and graphic arts.
1.2. Droplet Formation and Placement
In the realm of printing technology, droplet formation and placement are critical components that distinguish inkjet printing from other print processes. Unlike traditional methods such as offset printing or screen printing, which rely on physical contact between the printing plate and the substrate, inkjet printing employs a non-contact approach. This is achieved through the precise formation and placement of tiny droplets of ink onto the printing surface. The process begins with the creation of these droplets within the printhead, a sophisticated component of inkjet printers. There are two primary methods used for droplet formation: thermal and piezoelectric. In thermal inkjet technology, heating elements within the printhead vaporize a small portion of the ink, creating a bubble that forces a droplet out of the nozzle. Conversely, piezoelectric inkjet technology utilizes electrically charged crystals that change shape when an electric field is applied, generating pressure to expel the ink droplets. Once formed, these droplets must be accurately placed on the substrate to ensure high-quality prints. This is where the precision of inkjet technology shines. Modern inkjet printers can produce droplets as small as a few picoliters, allowing for incredibly fine detail and resolution. The placement of these droplets is controlled by advanced algorithms and precise mechanical systems, ensuring that each droplet lands exactly where intended. This level of control over droplet formation and placement is what sets inkjet printing apart from other processes. For instance, in offset printing, ink is transferred from a metal plate to a rubber blanket and then to the paper, which can lead to inconsistencies in ink distribution and lower resolution compared to inkjet. Similarly, screen printing involves pushing ink through a mesh screen onto the substrate, which lacks the precision and flexibility offered by inkjet's droplet-by-droplet approach. Moreover, the versatility of inkjet printing extends beyond traditional paper substrates. The ability to form and place droplets with such precision allows for printing on a wide range of materials, including textiles, ceramics, and even three-dimensional objects. This adaptability makes inkjet technology invaluable in various industries such as textiles, electronics, and biomedical engineering. In summary, the key difference between inkjet and other print processes lies in its unique method of droplet formation and placement. By leveraging thermal or piezoelectric mechanisms to create tiny ink droplets and advanced systems to place them with precision, inkjet printing offers unparalleled resolution, flexibility, and versatility. This makes it an indispensable tool in modern printing applications where high quality and customization are paramount.
1.3. Paper Interaction and Absorption
In the realm of printing technology, the interaction between paper and ink is a critical factor that distinguishes inkjet printing from other print processes. Unlike offset printing, which relies on transferring ink from a metal plate to a rubber blanket before reaching the paper, or laser printing, which uses electrostatic charges to attract toner particles onto the paper, inkjet printing involves the direct deposition of ink droplets onto the paper surface. This direct interaction necessitates a deep understanding of paper absorption characteristics. Paper's ability to absorb ink is governed by its porosity, surface energy, and fiber structure. In inkjet printing, the paper must balance between absorbing enough ink to prevent smudging and bleeding while maintaining sufficient surface tension to hold the ink droplets in place. This delicate balance is achieved through the use of specialized coatings or treatments that enhance the paper's hydrophilic properties. For instance, some papers are treated with silica or calcium carbonate to increase their surface area and improve ink absorption rates. The absorption mechanism in inkjet printing can be divided into two primary phases: capillary action and diffusion. Initially, capillary action draws the ink into the paper's pores, where it spreads out and is absorbed by the fibers. Subsequently, diffusion occurs as the ink molecules penetrate deeper into the paper, distributing evenly throughout the fiber matrix. This process ensures that the ink is retained within the paper without excessive spreading or feathering, which can compromise print quality. In contrast to other print processes, the direct ink-paper interaction in inkjet printing allows for greater flexibility in terms of paper types and finishes. While offset and laser printing often require specific paper stocks optimized for their respective technologies, inkjet printers can accommodate a wide range of papers, from glossy photo papers to matte finishes and even textiles. This versatility makes inkjet printing particularly appealing for applications requiring diverse media types, such as fine art reproduction, textile printing, and specialty packaging. Moreover, advancements in paper technology have further enhanced the performance of inkjet printing. Modern papers designed for inkjet use often feature advanced coatings that not only improve ink absorption but also enhance color gamut and durability. These coatings can include nanoparticles or polymers that help to stabilize the ink droplets upon impact, reducing dot gain and improving overall print resolution. In summary, the unique interaction between paper and ink in inkjet printing underscores its distinct advantages over other print processes. By leveraging specialized paper treatments and coatings, inkjet technology can achieve high-quality prints across a broad spectrum of media types, making it an indispensable tool in various industries ranging from graphic design to industrial manufacturing. The intricate dance between ink droplets and paper fibers highlights the sophisticated engineering that underpins modern printing technologies, ensuring that each printed page meets the highest standards of clarity, vibrancy, and durability.
2. Print Quality and Resolution
When evaluating the print quality and resolution of any printing technology, several key factors come into play. These elements collectively determine the overall visual appeal and accuracy of the printed output. First, the variability in dot size and density significantly impacts the final image quality, as it affects the level of detail and texture that can be achieved. Second, the color gamut and accuracy are crucial for ensuring that the printed colors match the intended hues, which is particularly important for applications requiring precise color representation. Lastly, comparing the clarity of text and images helps in understanding how well the printer handles different types of content. By examining these aspects, one can gain a comprehensive understanding of a printer's capabilities. To delve deeper into these considerations, let's start by exploring the first critical factor: dot size and density variability. This aspect is fundamental in determining the printer's ability to produce high-resolution prints with nuanced detail. --- **2.1. Dot Size and Density Variability**
2.1. Dot Size and Density Variability
In the realm of print quality and resolution, one critical factor that distinguishes inkjet printing from other print processes is the variability in dot size and density. Inkjet printers achieve their high-resolution outputs by precisely controlling the size and spacing of tiny ink droplets, or dots, deposited onto the printing surface. This control allows for a wide range of tonal values and detailed images. However, the variability in dot size and density can significantly impact the final print quality. ### Dot Size Variability Dot size variability refers to the differences in the diameter of the ink droplets ejected by the print head. Modern inkjet printers use advanced technologies such as piezoelectric or thermal printheads to generate these droplets. The precision with which these droplets are produced can vary, leading to differences in dot size. Smaller dots generally contribute to higher resolution and finer details, while larger dots may result in coarser images but can also enhance color saturation and vibrancy. Inkjet printers often employ multiple drop sizes to achieve a broader dynamic range, allowing for both detailed text and rich, vibrant colors. ### Density Variability Density variability pertains to how closely these ink droplets are spaced on the printing surface. The density of dots directly influences the perceived brightness and color intensity of the printed image. Higher dot densities typically result in darker, more saturated colors and finer details, whereas lower densities may lead to lighter, less saturated areas. Advanced inkjet systems often use variable dot spacing to optimize print quality, ensuring that areas requiring high detail have densely packed dots while areas needing less detail can have more spaced-out dots. ### Impact on Print Quality The interplay between dot size and density variability is crucial for achieving optimal print quality. For instance, in photographic prints, maintaining consistent dot sizes and densities is essential for preserving the nuances of color and detail. In contrast, for large-format prints like posters or banners, slightly larger and more variably spaced dots might be acceptable as they enhance visibility from a distance without compromising overall image quality. ### Comparison with Other Print Processes Unlike other print processes such as laser printing or offset printing, inkjet's reliance on variable dot sizes and densities offers unique advantages. Laser printers use toner particles that are fused onto the paper, resulting in a more uniform but less flexible output compared to inkjet's dynamic dot placement. Offset printing, which involves transferring ink onto a metal plate and then onto paper, lacks the precision control over individual dots that inkjet provides. This flexibility in dot size and density makes inkjet particularly adept at producing high-resolution images with rich color gamuts and detailed textures. In summary, the ability of inkjet printers to manipulate dot size and density variability is a key differentiator in achieving superior print quality and resolution compared to other print processes. This capability allows for a wide range of applications, from fine art reproductions to commercial signage, making inkjet a versatile and preferred choice for many printing needs.
2.2. Color Gamut and Accuracy
When discussing print quality and resolution, one crucial aspect to consider is the color gamut and accuracy of different printing processes. The color gamut refers to the range of colors that a printer can produce, while color accuracy pertains to how closely these colors match their intended hues. In the context of inkjet printing, these factors are particularly significant. Inkjet printers, known for their versatility and wide range of applications, often boast a broad color gamut. This is due in part to the use of multiple ink cartridges, which can include not only the standard CMYK (cyan, magenta, yellow, and black) but also additional colors such as light cyan, light magenta, and even specialized inks like red or green. These extra inks help expand the printer's color gamut, allowing it to produce more vibrant and nuanced colors. For instance, photo inkjet printers designed for professional photographers may include up to 10 or more different ink colors to achieve highly accurate and detailed color reproduction. In contrast, other print processes like laser printing typically have a more limited color gamut. Laser printers usually rely on a four-color CMYK model without the additional specialized inks found in many inkjet systems. While this can still produce high-quality prints, it may not match the depth and range of colors achievable with inkjet technology. Furthermore, laser printers often use toner rather than liquid ink, which can affect the final color appearance and accuracy. Color accuracy is another critical dimension where inkjet printers often excel. Advanced inkjet models employ sophisticated algorithms and calibration processes to ensure that the printed colors closely align with the original digital image. This is particularly important in fields such as graphic design, fine art printing, and commercial signage where precise color matching is essential. Some high-end inkjet printers even support ICC (International Color Consortium) profiles, which help standardize color reproduction across different devices and media types. Moreover, the physical properties of inkjet printing contribute to its superior color accuracy. The droplet size and placement precision of modern inkjet heads allow for fine-grained control over color deposition, resulting in smoother gradients and more detailed color transitions. This level of precision is harder to achieve with other print technologies like laser or solid ink printing, where the nature of the toner or solid ink particles can introduce variability in color output. In summary, when it comes to color gamut and accuracy, inkjet printing stands out as a leader among various print processes. Its ability to utilize multiple ink cartridges and advanced calibration techniques makes it an ideal choice for applications requiring high-quality, precise color reproduction. Whether you are a professional photographer seeking to print gallery-quality images or a graphic designer needing accurate color matching for branding materials, inkjet printing offers a level of color fidelity that is hard to match with other technologies. This makes it a preferred option for anyone looking to achieve the best possible print quality and resolution in their work.
2.3. Text and Image Clarity Comparison
When evaluating the key differences between inkjet and other print processes, one crucial aspect to consider is the clarity of text and images. This comparison falls under the broader category of print quality and resolution, which significantly impacts the overall output of printed materials. Inkjet printing, known for its versatility and wide range of applications, often stands out due to its ability to produce high-quality text and images with remarkable clarity. Inkjet printers achieve this clarity through a precise droplet placement mechanism. Unlike laser printers, which use a toner-based system to create images, inkjet printers deposit tiny droplets of ink onto the paper. This method allows for finer details and smoother gradients, particularly beneficial for photographic prints and detailed graphics. For instance, in high-resolution images, inkjet printers can capture subtle color transitions and minute details that might be lost in other printing methods. This is especially evident in the reproduction of fine lines and small text, where inkjet's precision ensures that characters remain sharp and legible even at smaller font sizes. In contrast, other print processes such as laser printing and offset printing have their own strengths but may fall short in certain areas of text and image clarity. Laser printers, while excellent for high-volume text-based documents due to their speed and cost-efficiency, can sometimes lack the finesse required for intricate graphics or photographs. The toner-based system can result in slightly less vibrant colors and less detailed gradients compared to inkjet. Offset printing, on the other hand, excels in mass production scenarios but often requires significant setup costs and may not offer the same level of detail as inkjet for smaller print runs or highly detailed work. Moreover, advancements in inkjet technology have further enhanced text and image clarity. Modern inkjet printers often incorporate multiple ink cartridges with a wide gamut of colors, allowing for more accurate color reproduction. Additionally, features like variable droplet size and advanced paper handling capabilities contribute to improved print quality. These innovations make inkjet printing a preferred choice for applications where visual fidelity is paramount, such as in professional photography, fine art reproduction, and high-end marketing materials. In summary, when comparing text and image clarity across different print processes, inkjet printing emerges as a leader due to its precise droplet placement and ability to capture fine details. While other methods have their advantages in terms of speed or cost-effectiveness, inkjet's superior clarity makes it an indispensable tool for any application requiring high-quality visual output. This distinction underscores why inkjet printing remains a cornerstone in various industries where print quality is not just desirable but essential.
3. Cost, Speed, and Practical Applications
When evaluating the effectiveness of any technology, particularly in the context of industrial processes, three key factors come to the forefront: cost, speed, and practical applications. These elements are interwoven and crucial for determining the overall viability and efficiency of a system. The initial investment and operating costs are fundamental considerations, as they directly impact the financial sustainability of an operation. Additionally, the printing speed and throughput efficiency play a significant role in meeting production demands and maintaining competitiveness. Lastly, understanding industry-specific use cases and preferences is essential for tailoring solutions to meet unique needs and optimize performance. By examining these aspects, businesses can make informed decisions that align with their strategic goals. Let's begin by delving into the initial investment and operating costs, which set the stage for understanding the broader financial implications of adopting new technologies. --- **3.1. Initial Investment and Operating Costs**
3.1. Initial Investment and Operating Costs
When considering the key differences between inkjet printing and other print processes, one crucial aspect to examine is the initial investment and operating costs. Inkjet technology, particularly in its industrial and commercial applications, often requires a significant upfront investment. This includes the cost of high-quality inkjet printers, which can range from tens of thousands to hundreds of thousands of dollars depending on the scale and complexity of the printing operation. Additionally, there are costs associated with ink and maintenance, as well as any necessary pre-treatment or post-treatment processes that may be required for certain substrates. In contrast, other print processes such as screen printing or offset printing may also have substantial initial costs but offer different economies of scale. For instance, while the initial setup for screen printing can be expensive due to the need for screens and a press, it becomes more cost-effective for large print runs because the cost per unit decreases significantly as the volume increases. Offset printing, similarly, has high initial costs due to plate production and press setup but is highly efficient for large-scale commercial printing due to its ability to produce thousands of copies quickly. However, inkjet printing excels in its flexibility and adaptability, making it a more practical choice for variable data printing and short to medium-sized print runs. The absence of plates or screens in inkjet technology reduces setup times and costs, allowing for quicker turnaround times and lower overheads for smaller batches. This flexibility is particularly beneficial in industries where customization is key, such as in packaging, textiles, and direct mail marketing. Moreover, the operating costs of inkjet printing can be more manageable over time. While ink costs can be higher compared to some other processes, advancements in inkjet technology have led to more efficient ink usage and longer printhead lifetimes. This reduces the need for frequent replacements and minimizes downtime, thereby lowering overall operational expenses. In summary, the initial investment and operating costs of inkjet printing are significant but offer unique advantages that make it a compelling choice for certain applications. Its ability to handle variable data, short print runs, and diverse substrates without the need for extensive setup makes it an attractive option despite higher upfront costs. As technology continues to evolve, the cost-effectiveness of inkjet printing is likely to improve further, solidifying its position as a versatile and efficient print process in various industries.
3.2. Printing Speed and Throughput Efficiency
When evaluating the key differences between inkjet and other print processes, one critical factor to consider is printing speed and throughput efficiency. Inkjet printing, particularly in its industrial and commercial forms, has made significant strides in recent years to match or even surpass the speeds of other technologies like offset and flexography. For instance, high-speed inkjet presses can achieve speeds of up to 1,000 feet per minute, making them highly competitive for large-scale production runs. This is particularly beneficial for applications such as newspaper printing, direct mail campaigns, and packaging where volume and speed are paramount. In contrast, offset printing, while traditionally faster for very large runs due to its ability to produce thousands of impressions per hour once the press is set up, often requires longer setup times and higher initial costs. Flexography, commonly used in packaging and label printing, also offers high speeds but may not match the versatility and cost-effectiveness of inkjet for variable data printing and short to medium run lengths. The throughput efficiency of inkjet is further enhanced by its ability to handle variable data with ease, allowing for personalized prints without significant speed penalties. This capability is especially valuable in sectors like direct marketing and personalized packaging where customization is key. Moreover, advancements in inkjet technology have led to the development of single-pass printing systems that significantly boost throughput efficiency. These systems print the entire image in a single pass across the substrate, eliminating the need for multiple passes and thereby increasing overall production speed. Additionally, inkjet's digital nature means that it can switch between different print jobs quickly without the need for extensive setup changes, reducing downtime and increasing overall productivity. In practical applications, this means that businesses can leverage inkjet printing for a wide range of tasks from high-volume commercial printing to specialized applications like textile and 3D printing. The combination of high speed, flexibility, and cost-effectiveness makes inkjet an attractive option for many industries seeking to balance production efficiency with customization and quality. As technology continues to evolve, it is likely that inkjet will further close any remaining gaps in terms of speed and throughput efficiency compared to other print processes, solidifying its position as a leading choice for diverse printing needs.
3.3. Industry-Specific Use Cases and Preferences
In the realm of printing, industry-specific use cases and preferences play a crucial role in determining the suitability of inkjet technology over other print processes. For instance, in the **textile industry**, inkjet printing has revolutionized fabric design by offering unparalleled flexibility and speed. Unlike traditional screen printing, which requires significant setup time and is less adaptable to small batches or custom designs, inkjet allows for rapid prototyping and production of intricate patterns on various fabric types. This makes it an ideal choice for fashion designers who need to quickly produce samples or limited-edition collections. In **packaging**, inkjet printing is preferred for its ability to handle variable data and high-speed production. Companies can print unique codes, serial numbers, and even personalized messages directly onto packaging materials without the need for pre-printed labels. This not only enhances product traceability but also adds a personal touch to consumer goods. Additionally, inkjet's non-contact nature reduces wear and tear on packaging materials, making it particularly beneficial for delicate or irregularly shaped items. The **pharmaceutical industry** also benefits from inkjet's precision and flexibility. For example, inkjet can be used to print expiration dates, batch numbers, and other critical information directly onto pills or capsules. This method ensures accuracy and compliance with regulatory requirements while minimizing the risk of human error. Moreover, inkjet's ability to handle small droplets allows for precise dosing in pharmaceutical applications, such as printing active ingredients onto tablets. In **industrial manufacturing**, inkjet is utilized for marking and coding parts during production. Its high speed and reliability make it an essential tool for just-in-time manufacturing processes. Unlike laser marking, which can be expensive and limited in terms of material compatibility, inkjet offers a cost-effective solution that works well with a wide range of materials including metals, plastics, and ceramics. Lastly, in **art and design**, inkjet printing has become a staple for artists and designers due to its ability to produce high-resolution images with vibrant colors. Fine art printers use archival-quality inks that ensure longevity and durability of the artwork. This makes inkjet an attractive option for creating limited-edition prints or reproducing original works with fidelity. In summary, the versatility of inkjet technology across various industries stems from its unique combination of speed, precision, and adaptability. Whether it's textile design, packaging customization, pharmaceutical labeling, industrial marking, or fine art reproduction, inkjet printing offers distinct advantages that set it apart from other print processes. Its ability to handle variable data, produce high-resolution images, and work with diverse materials makes it an indispensable tool in modern manufacturing and creative fields.