What Is An Anchor Point

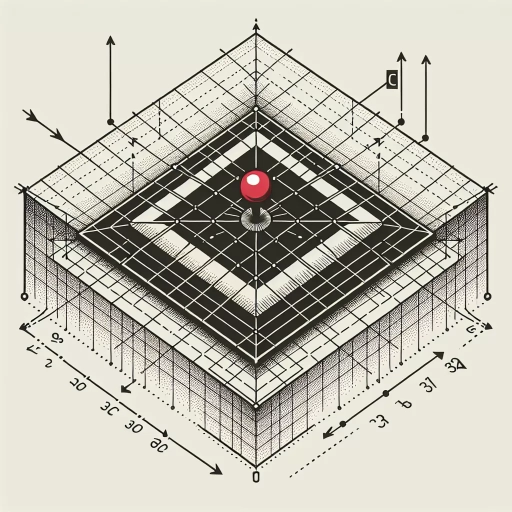
An anchor point is a crucial component in various industries, including construction, climbing, and maritime, serving as a secure attachment for ropes, harnesses, and other safety equipment. Understanding the concept of an anchor point is essential for ensuring safety and efficiency in these fields. This article delves into the multifaceted nature of anchor points, beginning with their definition and purpose. We will explore how anchor points are designed to provide a reliable anchor for loads, highlighting their critical role in preventing accidents and ensuring compliance with safety standards. Additionally, we will examine the diverse types and variations of anchor points, each tailored to specific applications and environments. Finally, we will discuss the importance of proper installation, maintenance, and safety considerations to ensure these points remain effective over time. By grasping these key aspects, individuals can better appreciate the significance of anchor points and their integral role in safeguarding lives and operations. Let's start by defining and understanding the purpose of an anchor point.
Definition and Purpose of an Anchor Point
An anchor point is a critical component in various industries, serving as a secure attachment for ropes, harnesses, and other safety equipment. The definition and purpose of an anchor point are rooted in its ability to provide a reliable and stable connection, ensuring the safety of individuals and equipment. This concept is explored through three key aspects: Historical Context and Evolution, Technical Specifications and Standards, and Practical Applications Across Industries. Historically, anchor points have evolved significantly from simple hooks and eyebolts to sophisticated engineered systems. Understanding this evolution is crucial for appreciating the advancements in safety protocols. Technically, anchor points must adhere to strict standards to ensure they can withstand various loads and conditions. These specifications are vital for maintaining safety and compliance. Practically, anchor points are applied across diverse industries such as construction, climbing, and maritime, each with unique requirements and challenges. By examining these facets, we gain a comprehensive understanding of the definition and purpose of an anchor point. Let's begin by delving into the Historical Context and Evolution of anchor points, tracing their development from early rudimentary designs to the sophisticated systems of today.
Historical Context and Evolution
The concept of an anchor point has its roots in various historical contexts, evolving over time to serve diverse purposes across different fields. In navigation, the term "anchor point" dates back to ancient maritime practices where ships would drop anchors to secure their position in the water. This physical anchor served as a stable reference point, allowing sailors to gauge their surroundings and navigate safely. As navigation techniques advanced with the advent of cartography and later GPS technology, the concept of an anchor point transitioned from a physical object to a metaphorical reference point on maps and charts, helping navigators orient themselves and chart courses. In psychology, particularly within the realm of cognitive science, anchor points refer to initial pieces of information that influence subsequent judgments or decisions. This concept emerged from the work of psychologists Amos Tversky and Daniel Kahneman in the 1970s, who demonstrated how people rely on mental anchors when making estimates or decisions under uncertainty. For instance, if someone is asked whether the population of a city is greater or less than a given number (the anchor), their subsequent estimate will often be biased towards that initial number. In engineering and construction, anchor points are critical for ensuring safety and structural integrity. Here, they refer to secure locations where safety equipment such as harnesses can be attached to prevent falls or other accidents. The evolution of safety regulations and standards has led to the development of more robust and reliable anchor points, which are now a cornerstone of workplace safety protocols. In digital design and user experience (UX), anchor points play a crucial role in creating intuitive interfaces. In graphic design software like Adobe Illustrator or Photoshop, anchor points are used to define the shape and position of objects on a canvas. These points allow designers to manipulate shapes with precision, enabling the creation of complex designs with ease. The evolution of anchor points across these fields highlights their versatility and importance. From physical anchors in navigation to cognitive anchors in psychology, and from structural anchors in engineering to digital anchors in design, each context underscores the need for a stable reference or starting point. This common thread underscores the definition and purpose of an anchor point: to provide stability, orientation, and precision in various domains. In summary, the historical context and evolution of anchor points reveal a multifaceted concept that has adapted to meet the needs of different disciplines. Whether it's ensuring safe navigation, influencing cognitive judgments, securing physical structures, or facilitating precise design work, the anchor point remains an essential element that provides a foundation for accuracy and reliability. This understanding is crucial for appreciating the broader significance of anchor points in their respective fields and their enduring relevance in modern applications.
Technical Specifications and Standards
Technical specifications and standards play a crucial role in ensuring the safety, reliability, and performance of anchor points, which are critical components in various industries such as construction, manufacturing, and rescue operations. These specifications outline the precise requirements for the design, materials, installation, and testing of anchor points to guarantee they can withstand the intended loads and stresses. For instance, standards like those set by the Occupational Safety and Health Administration (OSHA) in the United States or the European Union's EN 795 specify minimum strength requirements, material properties, and inspection protocols. Compliance with these standards ensures that anchor points are capable of supporting the weight and forces they are subjected to, thereby preventing accidents and injuries. Additionally, technical specifications often include details on corrosion resistance, durability, and compatibility with other equipment, which are essential for maintaining the integrity of the anchor point over time. By adhering to these technical specifications and standards, users can trust that their anchor points will function as intended, providing a secure attachment point for fall protection systems, lifting equipment, or other applications. This adherence not only enhances safety but also ensures compliance with regulatory requirements, reducing legal and financial risks associated with non-compliance. In summary, technical specifications and standards are indispensable for defining the quality and functionality of anchor points, making them a cornerstone of safe and reliable operations across diverse industries.
Practical Applications Across Industries
Anchor points, defined as secure and stable attachment points for various types of equipment or systems, have numerous practical applications across diverse industries. In **construction**, anchor points are crucial for ensuring the safety of workers. They are used to secure safety harnesses, preventing falls from heights and reducing the risk of injury or death. For instance, roof anchors and beam clamps provide stable attachment points for personal fall arrest systems. In **manufacturing**, anchor points are essential for the safe operation of machinery and equipment. They help in securing tools, machinery, and even workers during maintenance tasks, thereby enhancing workplace safety and efficiency. For example, anchor points on cranes and hoists ensure that loads are properly secured during lifting operations. The **oil and gas industry** also relies heavily on anchor points for offshore and onshore operations. Here, they are used to secure drilling equipment, pipelines, and other critical infrastructure against environmental forces like wind and waves. This ensures the integrity of operations and prevents potential disasters. In **aviation**, anchor points are vital for aircraft maintenance and repair. They are used to secure aircraft during ground operations, preventing unintended movement that could cause damage or injury. Additionally, anchor points are used in aircraft rescue and firefighting (ARFF) operations to stabilize aircraft in emergency situations. The **healthcare industry** benefits from anchor points in patient care settings. For example, anchor points are used in patient lifting systems to safely transfer patients between beds, wheelchairs, or other medical equipment, reducing the risk of injury to both patients and healthcare workers. In **recreational activities** such as rock climbing and adventure sports, anchor points are indispensable for ensuring participant safety. Climbing anchors like bolts, cams, and nuts provide secure attachment points for ropes and harnesses, allowing climbers to ascend safely. Furthermore, in **transportation**, anchor points are used in securing cargo on trucks, ships, and trains. Properly secured cargo prevents shifting during transit, which can lead to accidents or damage to goods. In **emergency services**, such as firefighting and search and rescue operations, anchor points play a critical role. They enable rescue teams to safely access and retrieve individuals from challenging environments like high-rise buildings or disaster zones. Overall, the practical applications of anchor points span a wide range of industries, each leveraging these secure attachment points to enhance safety, efficiency, and operational integrity. Whether it's protecting workers in construction or securing cargo in transportation, anchor points are fundamental components that underpin many critical operations.
Types and Variations of Anchor Points
When discussing the types and variations of anchor points, it is crucial to consider several key factors that influence their effectiveness and suitability for different applications. First, understanding the distinction between permanent and temporary anchor points is essential, as each type serves unique purposes and offers different levels of stability and convenience. Additionally, material differences play a significant role in determining the durability and reliability of anchor points, with various materials offering distinct advantages depending on the environment and task at hand. Finally, specialized anchor points designed for specific tasks can significantly enhance safety and efficiency by providing tailored solutions for particular needs. By examining these aspects, users can make informed decisions about which anchor points to use in various scenarios. Let's start by delving into the critical differences between permanent and temporary anchor points, which form the foundation of understanding the broader spectrum of anchor point types.
Permanent vs. Temporary Anchor Points
When discussing anchor points, it is crucial to differentiate between permanent and temporary anchor points, as each type serves distinct purposes and offers unique advantages. **Permanent Anchor Points** are designed to be long-lasting and are typically integrated into the structure of a building or facility. These anchor points are usually made from durable materials such as steel or concrete and are installed during the construction phase. They are often used in industries where frequent access is required, such as in construction, maintenance, and rescue operations. Permanent anchor points provide a high level of reliability and safety due to their robust design and secure installation. For example, roof anchors on commercial buildings allow maintenance personnel to safely perform tasks without the need for temporary setups. However, their installation can be more expensive upfront, and they may require periodic inspections to ensure they remain in good condition. **Temporary Anchor Points**, on the other hand, are used for short-term applications or in situations where permanent installation is not feasible. These can include portable anchors, hooks, or other devices that can be easily set up and removed. Temporary anchor points are versatile and cost-effective, making them ideal for projects with limited duration or in environments where permanent fixtures are not allowed. For instance, temporary anchors might be used during a one-time event or in a historic building where altering the structure is prohibited. While they offer flexibility, temporary anchor points may require more frequent checks to ensure they are properly secured and functioning correctly. In summary, the choice between permanent and temporary anchor points depends on the specific needs of the task at hand. Permanent anchor points offer long-term reliability and are best suited for frequent use in stable environments, while temporary anchor points provide flexibility and are ideal for short-term or variable situations. Understanding the differences between these two types is essential for ensuring safety and efficiency in various industries and applications.
Material Differences and Durability
When discussing anchor points, the material differences and durability play a crucial role in determining their effectiveness and longevity. Anchor points, which are critical components in various applications such as climbing, construction, and industrial settings, must withstand significant stress and environmental conditions. Here are the key material differences and their implications on durability: 1. **Steel vs. Aluminum**: Steel anchor points are generally more durable and stronger than aluminum ones. Steel offers higher tensile strength, making it ideal for heavy-duty applications where high loads are anticipated. However, steel is heavier and more prone to corrosion if not properly coated. Aluminum, on the other hand, is lighter and corrosion-resistant but has lower tensile strength, making it suitable for lighter loads and applications where weight is a concern. 2. **Stainless Steel**: This material combines the strength of steel with excellent corrosion resistance, making it a preferred choice for marine and outdoor environments. Stainless steel anchor points are more expensive but offer superior durability in harsh conditions. 3. **Carbon Fiber**: Although less common for anchor points due to cost and manufacturing complexities, carbon fiber offers exceptional strength-to-weight ratio. It is highly resistant to corrosion and fatigue but requires careful handling to avoid damage. 4. **Plastics and Polymers**: These materials are often used in lighter-duty applications or as components within more complex anchor systems. They are generally cheaper and lighter but lack the strength and durability of metal materials, making them less suitable for high-load scenarios. 5. **Coatings and Treatments**: The durability of an anchor point can also be significantly enhanced by coatings or treatments such as galvanizing, powder coating, or anodizing. These treatments protect the material from corrosion and wear, extending the lifespan of the anchor point. In terms of durability, the choice of material directly influences how well an anchor point will perform over time. For instance: - **Fatigue Resistance**: Materials like stainless steel and high-strength alloys exhibit better fatigue resistance, meaning they can withstand repeated loading cycles without failing. - **Corrosion Resistance**: Materials exposed to harsh environments benefit from corrosion-resistant properties found in stainless steel or aluminum. - **Impact Resistance**: Steel and certain alloys have higher impact resistance compared to lighter materials like aluminum or plastics. Ultimately, selecting the right material for an anchor point involves balancing factors such as load capacity, environmental conditions, weight considerations, and budget constraints. Understanding these material differences is crucial for ensuring that anchor points meet safety standards and perform reliably over their intended lifespan. By choosing the appropriate material based on specific needs, users can maximize the durability and effectiveness of their anchor points.
Specialized Anchor Points for Specific Tasks
Specialized anchor points are designed to cater to specific tasks, ensuring safety and efficiency in various applications. For instance, in rock climbing, anchor points such as cams, nuts, and bolts are tailored for different types of rock formations. Cams are ideal for cracks where they can expand to fit snugly, while nuts are better suited for smaller crevices. Bolts, on the other hand, provide a more permanent solution but require drilling into the rock face. In maritime contexts, mooring anchors like the Danforth or plow anchor are engineered to hold fast in different seabed conditions—Danforth anchors excel in mud and sand, while plow anchors perform well in rocky or hard bottoms. In construction, anchor points like eye bolts and J-hooks are used for lifting heavy loads; these are often rated for specific weight capacities to prevent accidents. In rescue operations, specialized anchor points such as rappel rings and quick links allow for swift and secure attachment of ropes, crucial for timely rescue efforts. Additionally, in industrial settings like warehouses or factories, overhead anchor points such as beam clamps and trolley systems facilitate safe lifting and moving of heavy equipment. Each type of anchor point is meticulously designed to meet the unique demands of its intended task, ensuring reliability and safety under various conditions. This specialization underscores the importance of selecting the right anchor point for the job at hand to avoid potential hazards and optimize performance.
Installation, Maintenance, and Safety Considerations
When it comes to ensuring the longevity and efficiency of any system or equipment, three critical aspects must be meticulously addressed: proper installation techniques and tools, regular maintenance and inspection protocols, and safety guidelines along with emergency procedures. Proper installation sets the foundation for optimal performance and minimizes the risk of future malfunctions. Regular maintenance is essential for identifying and addressing potential issues before they escalate, thereby extending the lifespan of the equipment. Safety guidelines and emergency procedures are vital for protecting both the operators and the surrounding environment from potential hazards. By focusing on these three areas, individuals can guarantee that their systems operate at peak levels while maintaining a safe working environment. To begin, it is crucial to understand the importance of proper installation techniques and tools, as this initial step significantly influences the overall success of the system. Transitioning to the first supporting idea, proper installation techniques and tools are fundamental in ensuring that the system is set up correctly from the outset.
Proper Installation Techniques and Tools
Proper installation techniques and tools are crucial for ensuring the safety and effectiveness of anchor points. When installing anchor points, it is essential to follow specific guidelines to avoid potential hazards. First, select the appropriate anchor point type based on the intended use and environmental conditions. For instance, roof anchors should be designed to withstand wind loads and weather conditions, while wall anchors must be compatible with the wall material. ### Tools and Equipment 1. **Drill Bits and Drivers**: Use high-quality drill bits that are compatible with the anchor material to prevent damage or stripping of threads. 2. **Leveling Tools**: Ensure the anchor is installed level to maintain even distribution of forces. 3. **Torque Wrenches**: Apply the correct torque to secure the anchor firmly without over-tightening, which can lead to material failure. 4. **Safety Harnesses**: Always wear personal protective equipment (PPE) such as safety harnesses during installation to prevent falls. ### Installation Steps 1. **Pre-Installation Inspection**: Inspect the area for any obstructions or weaknesses in the structure before starting the installation. 2. **Marking and Drilling**: Mark the exact location where the anchor will be installed and drill pilot holes carefully to avoid damaging surrounding materials. 3. **Anchor Placement**: Insert the anchor into the pilot hole, ensuring it is seated properly according to manufacturer instructions. 4. **Securing the Anchor**: Tighten the anchor using a torque wrench to the specified torque value to ensure it is securely fastened. ### Safety Considerations 1. **Load Testing**: Perform load tests on newly installed anchors to verify their strength and stability. 2. **Regular Inspections**: Conduct regular inspections of anchor points for signs of wear, corrosion, or damage. 3. **Training and Certification**: Ensure that all personnel involved in the installation process are trained and certified in proper techniques and safety protocols. By adhering to these installation techniques and using the right tools, you can significantly reduce the risk of accidents and ensure that your anchor points are reliable and durable. This meticulous approach not only enhances safety but also extends the lifespan of your equipment, making it a critical component of overall installation, maintenance, and safety considerations.
Regular Maintenance and Inspection Protocols
Regular maintenance and inspection protocols are crucial components of ensuring the longevity, safety, and efficiency of anchor points and their associated systems. These protocols involve systematic checks and upkeep activities designed to identify potential issues before they become critical. Here are the key elements: 1. **Scheduled Inspections**: Regularly scheduled inspections should be conducted by trained professionals to assess the condition of anchor points, including visual examinations for signs of wear, corrosion, or damage. These inspections should be documented to track any changes over time. 2. **Component Checks**: Each component of the anchor point system, such as bolts, nuts, and hangers, must be inspected for integrity. This includes checking for proper torque values, signs of rust or corrosion, and ensuring that all parts are securely fastened. 3. **Load Testing**: Periodic load testing is essential to verify that the anchor points can withstand the intended loads. This involves applying a controlled load to the anchor point and monitoring its performance under stress. 4. **Cleaning and Lubrication**: Regular cleaning of anchor points helps remove dirt, grime, and other substances that could compromise their functionality. Lubrication of moving parts ensures smooth operation and reduces wear. 5. **Documentation and Records**: Maintaining detailed records of inspections, maintenance activities, and any repairs is vital for compliance with safety regulations and for tracking the history of each anchor point. 6. **Training and Competency**: Personnel responsible for conducting inspections and maintenance must be adequately trained and certified to perform these tasks effectively. This includes understanding the specific requirements for different types of anchor points. 7. **Compliance with Standards**: All maintenance and inspection activities should adhere to relevant industry standards and regulations, such as those set by OSHA or other governing bodies, to ensure compliance and safety. 8. **Repair and Replacement**: Any issues identified during inspections should be addressed promptly. This may involve repairing or replacing damaged components to prevent failures that could lead to accidents. By implementing these regular maintenance and inspection protocols, organizations can significantly reduce the risk of equipment failure, ensure compliance with safety standards, and extend the lifespan of their anchor points. This proactive approach not only enhances safety but also optimizes operational efficiency and reduces downtime due to unexpected failures.
Safety Guidelines and Emergency Procedures
When it comes to installation, maintenance, and safety considerations for anchor points, adhering to strict safety guidelines and emergency procedures is paramount. Here are the key points to ensure a safe and secure environment: 1. **Pre-Installation Checks**: Before installing an anchor point, conduct a thorough risk assessment of the site. Ensure that the structure can support the intended load and that all necessary permits and approvals are in place. 2. **Proper Installation**: Follow the manufacturer's instructions for installation. Ensure that anchor points are securely fastened to a solid structure, such as a roof or wall, using appropriate hardware. Regularly inspect the anchor points for any signs of wear or damage. 3. **Regular Maintenance**: Schedule regular maintenance checks to inspect anchor points for corrosion, damage, or wear. Replace any compromised components immediately to prevent accidents. 4. **Training and Certification**: Ensure that all personnel involved in the installation, maintenance, and use of anchor points are properly trained and certified. This includes understanding how to use personal protective equipment (PPE) correctly. 5. **Emergency Procedures**: - **Fall Arrest Plans**: Develop and implement a fall arrest plan that includes procedures for rescuing individuals who may fall while using anchor points. - **First Aid Kits**: Keep first aid kits readily available and ensure that personnel know how to administer basic first aid. - **Emergency Contact Information**: Display emergency contact information prominently at the site. - **Regular Drills**: Conduct regular emergency drills to ensure that all personnel are familiar with the procedures. 6. **Personal Protective Equipment (PPE)**: Mandate the use of PPE such as harnesses, lanyards, and helmets when working with anchor points. Ensure that PPE is inspected regularly and replaced as needed. 7. **Compliance with Standards**: Adhere to relevant industry standards and regulations, such as those set by OSHA (Occupational Safety and Health Administration) or local authorities. 8. **Documentation**: Maintain detailed records of all installations, maintenance activities, and training sessions. This documentation can be crucial in the event of an audit or investigation. By following these safety guidelines and emergency procedures, you can significantly reduce the risk of accidents and ensure a safe working environment for everyone involved in the installation and maintenance of anchor points.