What Is Prime Cost

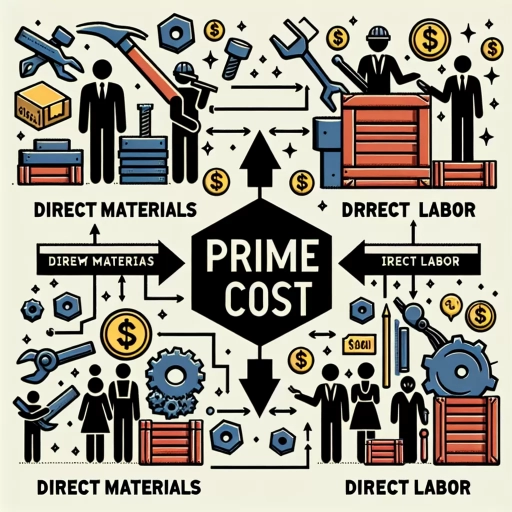
In the realm of business and accounting, understanding the concept of prime cost is crucial for making informed decisions and optimizing operational efficiency. Prime cost, a fundamental component of a company's total cost structure, encompasses the direct costs associated with producing goods or services. This article delves into the intricacies of prime cost, providing a comprehensive overview that will guide readers through its definition and basics, the steps and formulas involved in calculating it, and its significant applications and implications in business operations. First, we will explore the definition and basics of prime cost, clarifying what it includes and how it differs from other cost categories. Next, we will outline the steps and formulas necessary for accurately calculating prime cost, ensuring that readers can apply this knowledge in practical scenarios. Finally, we will examine the applications and implications of prime cost in business, highlighting its role in budgeting, pricing strategies, and overall financial management. By grasping these key aspects, businesses can better manage their resources, enhance profitability, and maintain a competitive edge. Let us begin by understanding the core concept: **Understanding Prime Cost: Definition and Basics**.
Understanding Prime Cost: Definition and Basics
Understanding prime cost is a fundamental concept in cost accounting, crucial for businesses to accurately assess and manage their expenses. Prime cost, at its core, encompasses the direct costs associated with producing goods or services. To delve into this concept effectively, it is essential to break it down into its key components. First, we need to define what prime cost is and how it differs from other types of costs. This definition sets the groundwork for understanding the specific elements that constitute prime cost. Next, we must identify the components of prime cost, which typically include direct materials and direct labor costs. Finally, recognizing the importance of prime cost in cost accounting helps businesses make informed decisions about pricing, budgeting, and resource allocation. By grasping these aspects, businesses can better navigate their financial landscape and optimize their operations. Let's begin by defining what prime cost is and exploring its significance in the broader context of cost accounting.
1. Definition of Prime Cost
**Definition of Prime Cost** Prime cost, a fundamental concept in accounting and cost management, refers to the total direct costs associated with producing a product or delivering a service. It encompasses two primary components: direct materials and direct labor. Direct materials are the raw materials or components that are directly used in the production process and can be easily traced to the final product. For example, in a manufacturing plant, this would include the raw materials such as steel, wood, or fabric. Direct labor, on the other hand, includes the wages and benefits paid to employees who are directly involved in the production process. This typically includes factory workers, assembly line workers, and other personnel whose efforts are directly tied to the creation of the product. Understanding prime cost is crucial for businesses as it helps in determining the minimum amount that must be recovered through sales to avoid losses. It serves as a baseline for pricing strategies and profitability analysis. By accurately calculating prime cost, companies can better manage their production costs, optimize resource allocation, and make informed decisions about pricing and inventory management. Additionally, prime cost is a key metric in budgeting and forecasting, allowing businesses to predict future expenses and plan accordingly. In practical terms, calculating prime cost involves summing up the direct material costs and direct labor costs for a given period. For instance, if a company uses $100,000 worth of raw materials and pays $150,000 in direct labor wages during a month, its prime cost for that month would be $250,000. This figure does not include indirect costs such as overheads, marketing expenses, or administrative salaries, which are accounted for separately under total cost or full cost. The distinction between prime cost and other types of costs is essential for financial reporting and decision-making. Unlike total cost, which includes both direct and indirect costs, prime cost provides a clear picture of the direct expenses incurred in producing goods or services. This clarity is vital for cost control measures and efficiency improvements within the production process. In summary, prime cost is a critical metric that reflects the direct expenses involved in producing goods or services. It is composed of direct materials and direct labor costs and serves as a foundational element in cost accounting and financial analysis. By understanding and accurately calculating prime cost, businesses can enhance their operational efficiency, improve profitability, and make more informed strategic decisions.
2. Components of Prime Cost
Understanding the components of prime cost is crucial for any business aiming to accurately calculate and manage its production expenses. Prime cost, also known as direct cost, is the total cost of producing a product or service and consists of two primary components: **Direct Materials** and **Direct Labor**. **Direct Materials** are the raw materials or components that are directly used in the production process. These materials can range from raw ingredients in food manufacturing to fabric in textile production. The cost of direct materials includes the purchase price of these items, as well as any additional costs such as transportation, storage, and handling. For instance, in a bakery, flour, sugar, and yeast would be considered direct materials because they are essential ingredients in baking bread. Accurate tracking of direct material costs is vital to ensure that the business can maintain profitability and make informed decisions about pricing and inventory management. **Direct Labor**, on the other hand, refers to the wages and benefits paid to employees who are directly involved in the production process. This includes workers on the assembly line, craftsmen, and any other personnel whose efforts directly contribute to the creation of the product. Direct labor costs not only encompass hourly wages but also include benefits, overtime pay, and other compensation that is directly attributable to production activities. For example, in a manufacturing plant, the workers assembling parts would be considered direct labor because their work is directly tied to the production of the final product. Both direct materials and direct labor are essential for calculating prime cost because they represent the core expenses associated with producing goods or services. By accurately identifying and tracking these costs, businesses can better understand their cost structure, optimize production processes, and make strategic decisions about pricing, inventory levels, and resource allocation. Additionally, understanding these components helps in identifying areas where cost savings can be achieved without compromising product quality or production efficiency. In summary, the components of prime cost—direct materials and direct labor—are fundamental elements that businesses must meticulously track to ensure accurate cost accounting and effective financial management. By grasping these concepts, businesses can enhance their operational efficiency, improve profitability, and maintain a competitive edge in their respective markets. This foundational understanding of prime cost components is indispensable for any organization seeking to optimize its production processes and achieve long-term financial health.
3. Importance in Cost Accounting
The importance of cost accounting cannot be overstated, particularly when it comes to understanding and managing prime costs. Cost accounting serves as a critical tool for businesses to make informed decisions, optimize operations, and maintain financial health. Here are three key reasons why cost accounting is essential: 1. **Accurate Cost Determination**: Cost accounting helps in the precise calculation of prime costs, which include direct materials and direct labor. By accurately determining these costs, businesses can set realistic prices for their products or services, ensuring they cover all expenses and maintain profitability. This accuracy also aids in budgeting and forecasting, allowing companies to anticipate future expenses and plan accordingly. 2. **Operational Efficiency**: Cost accounting provides detailed insights into the cost structure of a business, enabling managers to identify areas of inefficiency and opportunities for cost reduction. For instance, analyzing direct labor costs can reveal whether certain processes are overly labor-intensive or if there is room for automation. Similarly, examining direct material costs can help in negotiating better deals with suppliers or finding more cost-effective alternatives. This analytical approach fosters operational efficiency, leading to improved productivity and reduced waste. 3. **Strategic Decision-Making**: The data generated through cost accounting is invaluable for strategic decision-making. By understanding the prime cost components, businesses can make informed decisions about product mix, pricing strategies, and investment opportunities. For example, if a company finds that the prime cost of a particular product is higher than anticipated, it may decide to discontinue that product line or adjust its pricing strategy to ensure profitability. Additionally, cost accounting data can be used to evaluate the feasibility of new projects or investments by assessing their potential impact on prime costs. In summary, cost accounting is crucial for businesses as it ensures accurate cost determination, enhances operational efficiency, and supports strategic decision-making. These benefits are particularly relevant when understanding and managing prime costs, as they form the foundation of a company's overall cost structure and profitability. By leveraging cost accounting effectively, businesses can navigate complex financial landscapes with greater precision and confidence.
Calculating Prime Cost: Steps and Formulas
Calculating prime cost is a crucial step in understanding the financial health and operational efficiency of any business. This process involves several key steps and formulas that help in accurately determining the direct costs associated with producing goods or services. To begin, it is essential to identify the direct materials and labor costs, as these are the primary components of prime cost. Once these costs are accurately determined, applying the appropriate formulas for prime cost calculation becomes straightforward. Finally, using example calculations can provide clarity and ensure that the process is well understood. By following these steps, businesses can gain a clear picture of their prime costs, which is vital for making informed decisions regarding pricing, budgeting, and resource allocation. Let's start by delving into the first critical step: identifying direct materials and labor costs.
1. Identifying Direct Materials and Labor Costs
Identifying direct materials and labor costs is a crucial step in calculating prime cost, as these components directly contribute to the production of a product. **Direct Materials Costs** refer to the expenses incurred for raw materials, components, or parts that are directly used in the manufacturing process. These costs can be easily traced to specific products and are typically the largest component of prime cost. For instance, in a furniture manufacturing company, direct materials would include wood, fabric, and hardware such as screws and nails. To accurately identify these costs, companies must maintain detailed records of material purchases and usage rates. This involves tracking inventory levels, purchase orders, and consumption rates to ensure that all material expenditures are accounted for. **Direct Labor Costs**, on the other hand, pertain to the wages and benefits paid to employees who are directly involved in the production process. These workers are typically those on the assembly line or in roles where their efforts can be directly linked to the creation of a product. For example, in an automotive factory, direct labor would include assembly line workers and quality control inspectors who ensure that each vehicle meets standards before it leaves the factory. Identifying direct labor costs involves analyzing payroll records to isolate wages and benefits paid to these specific employees. It is essential to distinguish between direct labor and indirect labor (such as administrative staff) to avoid misallocating costs. To ensure accuracy in identifying both direct materials and labor costs, companies often implement robust accounting systems that categorize expenses based on their nature. This may involve using job costing or process costing methods depending on the type of production process. Job costing is suitable for custom or batch production where each job has unique requirements, while process costing is more appropriate for continuous production processes where products are homogeneous. In addition to maintaining accurate records, companies should regularly review their cost structures to identify any inefficiencies or areas for improvement. This could involve analyzing material usage rates to minimize waste or optimizing labor schedules to reduce overtime costs. By precisely identifying and managing direct materials and labor costs, businesses can better control their prime cost, which in turn helps in setting competitive prices, improving profitability, and making informed strategic decisions. Moreover, understanding these costs allows companies to make better decisions regarding inventory management and supply chain optimization. For instance, knowing the exact cost of raw materials can help in negotiating better prices with suppliers or identifying alternative sources that offer cost savings without compromising quality. In summary, identifying direct materials and labor costs is fundamental to calculating prime cost accurately. By meticulously tracking these expenses through robust accounting systems and regular reviews, businesses can gain a clearer understanding of their production costs. This clarity enables them to optimize operations, enhance efficiency, and ultimately drive profitability in a competitive market environment.
2. Applying Formulas for Prime Cost Calculation
When it comes to calculating prime cost, applying the right formulas is crucial for accuracy and efficiency. Prime cost, which represents the total direct costs associated with producing a product or service, is a fundamental metric in cost accounting. To apply these formulas effectively, one must first understand the components that make up prime cost: direct materials and direct labor. **Direct Materials:** The cost of direct materials can be calculated using the formula: \[ \text{Direct Materials Cost} = \text{Quantity of Materials Used} \times \text{Unit Price of Materials} \] For example, if a company uses 100 units of raw material at $5 per unit, the direct materials cost would be \(100 \times 5 = \$500\). **Direct Labor:** Similarly, direct labor costs can be determined using: \[ \text{Direct Labor Cost} = \text{Total Hours Worked} \times \text{Hourly Wage Rate} \] If an employee works 40 hours at $20 per hour, the direct labor cost would be \(40 \times 20 = \$800\). **Combining Direct Costs:** To find the total prime cost, you simply add the direct materials cost and the direct labor cost together: \[ \text{Prime Cost} = \text{Direct Materials Cost} + \text{Direct Labor Cost} \] Using our previous examples, if direct materials cost is $500 and direct labor cost is $800, then: \[ \text{Prime Cost} = \$500 + \$800 = \$1,300 \] **Additional Considerations:** While these formulas provide a clear method for calculating prime cost, it's important to consider other factors that might affect your calculations. For instance, any changes in material prices or labor rates should be reflected in your calculations to ensure accuracy. Additionally, if there are any inefficiencies or waste in the production process, these should be accounted for as well. **Practical Application:** In practical terms, understanding and applying these formulas helps businesses make informed decisions about pricing strategies, budgeting, and resource allocation. For instance, knowing the prime cost allows a company to set a minimum selling price that ensures profitability. It also helps in identifying areas where costs can be optimized without compromising on quality. In summary, applying formulas for prime cost calculation involves straightforward yet precise steps. By accurately determining direct materials and direct labor costs and combining them, businesses can gain a clear picture of their prime costs. This not only aids in financial planning but also enhances operational efficiency by highlighting potential cost-saving opportunities. By mastering these formulas, companies can better navigate the complexities of cost management and drive towards sustainable growth.
3. Example Calculations for Clarity
To illustrate the concept of prime cost and its calculation, let's delve into three example calculations that provide clarity on how this crucial metric is determined. **Example 1: Simple Manufacturing Scenario** Consider a small manufacturing firm that produces wooden chairs. The firm uses 10 units of wood, each costing $5, and 5 units of labor, each costing $20 per hour. The total direct material cost would be \(10 \text{ units} \times \$5/\text{unit} = \$50\), while the total direct labor cost would be \(5 \text{ units} \times \$20/\text{unit} = \$100\). Therefore, the prime cost for producing these chairs is \(\$50 + \$100 = \$150\). **Example 2: Complex Production with Multiple Materials** In a more complex scenario, a textile company produces 100 units of a specific fabric. The production requires 200 kg of cotton at $3 per kg, 50 kg of polyester at $4 per kg, and 300 hours of labor at $15 per hour. The direct material costs are calculated as follows: \(200 \text{ kg} \times \$3/\text{kg} = \$600\) for cotton and \(50 \text{ kg} \times \$4/\text{kg} = \$200\) for polyester. The total direct material cost is \(\$600 + \$200 = \$800\). For labor, it is \(300 \text{ hours} \times \$15/\text{hour} = \$4500\). Thus, the prime cost for this fabric production is \(\$800 + \$4500 = \$5300\). **Example 3: Incorporating Overheads** In some cases, companies may choose to include certain overheads in their prime cost calculations to get a more comprehensive view of their production costs. For instance, a bakery producing 500 loaves of bread might include the cost of electricity and maintenance as part of its direct costs. If the direct material cost for ingredients is $1000, direct labor cost is $2000, and overheads such as electricity and maintenance amount to $500, then the prime cost would be \(\$1000 + \$2000 + \$500 = \$3500\). These examples highlight how prime cost can be calculated in various scenarios, from simple to complex, and how different components such as materials, labor, and sometimes overheads are considered to arrive at this critical figure. By understanding these calculations, businesses can better manage their production costs and make informed decisions about pricing and resource allocation.
Applications and Implications of Prime Cost in Business
In the realm of business, understanding and effectively utilizing prime cost is crucial for maintaining competitiveness and ensuring financial health. Prime cost, which encompasses the direct costs associated with producing goods or services, plays a pivotal role in various aspects of business operations. This article delves into the applications and implications of prime cost, exploring its significance in three key areas: its role in pricing strategies, its impact on profitability and break-even analysis, and its use in budgeting and financial reporting. By grasping how prime cost influences pricing decisions, businesses can set prices that balance profitability with market demand. Additionally, analyzing prime cost helps in determining the break-even point, thereby guiding strategic decisions to enhance profitability. Furthermore, integrating prime cost into budgeting and financial reporting processes ensures accurate financial forecasting and transparency. This comprehensive approach underscores the multifaceted importance of prime cost in driving business success. Let us begin by examining the critical role of prime cost in pricing strategies, a foundational element in any business's competitive strategy.
1. Role in Pricing Strategies
In the realm of business operations, prime cost plays a pivotal role in pricing strategies, serving as a foundational element that influences how companies set their product prices. Prime cost, which encompasses the direct costs associated with producing a product—such as raw materials, labor, and direct overheads—provides a baseline from which businesses can determine their pricing structures. By accurately calculating prime cost, companies can ensure that their pricing strategies are both competitive and profitable. One of the primary applications of prime cost in pricing is in the cost-plus pricing method. Here, businesses add a markup to the prime cost to arrive at the selling price. This approach ensures that all direct costs are covered while allowing for a desired level of profit. For instance, if a company's prime cost for a product is $100 and they wish to achieve a 20% profit margin, they would set the selling price at $120. This method is particularly useful for new products or in markets where competition is not intense, as it guarantees a minimum return on investment. Another significant role of prime cost is in break-even analysis. By knowing the prime cost per unit, businesses can calculate how many units need to be sold to cover all costs and break even. This analysis is crucial for determining production levels and pricing thresholds. For example, if a company has fixed costs of $10,000 and a prime cost per unit of $50, they can calculate that they need to sell at least 200 units (assuming no other variable costs) to break even if they set their selling price at $75 per unit. Moreover, prime cost is essential for competitive pricing strategies. Companies often use prime cost as a benchmark to compare their costs with those of competitors. If a business finds that its prime cost is higher than that of its competitors, it may need to adjust its pricing strategy or look for ways to reduce costs without compromising quality. Conversely, if a company has lower prime costs due to efficient operations or economies of scale, it can leverage this advantage to offer competitive pricing while maintaining profitability. Additionally, prime cost influences value-based pricing strategies where the perceived value of the product to the customer is considered. While value-based pricing focuses more on what customers are willing to pay rather than just the cost of production, understanding prime cost helps businesses ensure that their prices are grounded in reality. It prevents them from setting prices so high that they become uncompetitive or so low that they fail to cover essential costs. In summary, prime cost is a critical component in various pricing strategies due to its ability to provide a clear picture of direct production costs. It aids in setting realistic and competitive prices, ensures profitability through cost-plus pricing, informs break-even analysis, and supports competitive and value-based pricing approaches. By meticulously calculating and utilizing prime cost data, businesses can make informed decisions that balance profitability with market competitiveness. This strategic use of prime cost not only enhances pricing accuracy but also contributes significantly to overall business success.
2. Impact on Profitability and Break-Even Analysis
The impact of prime cost on profitability and break-even analysis is a critical aspect of business operations, as it directly influences a company's financial health and sustainability. Prime cost, which includes the direct costs of materials and labor, forms the foundation of a product's total cost. Understanding and managing prime cost is essential because it affects the pricing strategy, profit margins, and overall profitability of a business. When analyzing profitability, prime cost serves as a baseline to determine the minimum price at which a product must be sold to avoid losses. By subtracting prime cost from the selling price, businesses can calculate the contribution margin, which is crucial for assessing the profitability of individual products or product lines. A lower prime cost can lead to higher profit margins if selling prices remain constant, thereby enhancing overall profitability. Conversely, an increase in prime cost can erode profit margins unless offset by higher selling prices or improved operational efficiencies. Break-even analysis, another vital tool in business decision-making, relies heavily on prime cost. The break-even point is the point at which total revenue equals total fixed and variable costs. Prime cost is a key component of variable costs, and changes in prime cost directly affect the break-even point. For instance, if prime costs rise due to increased material prices or labor rates, the break-even point will shift upward, meaning the business must sell more units to cover its costs and achieve profitability. Conversely, reducing prime costs through efficient sourcing or process improvements can lower the break-even point, allowing businesses to reach profitability with fewer sales. Moreover, understanding prime cost helps businesses make informed decisions about production levels and pricing strategies. By analyzing how changes in prime cost impact the break-even point, companies can better navigate market fluctuations and competitive pressures. For example, during periods of high demand but rising material costs, a business might choose to absorb some of the increased prime costs to maintain market share rather than passing them on to consumers through higher prices. In addition to its direct impact on financial metrics, managing prime cost also has broader implications for business strategy. Companies that successfully control their prime costs are better positioned to invest in research and development, expand their product offerings, or enter new markets. This competitive advantage can lead to sustained growth and higher long-term profitability. In conclusion, the impact of prime cost on profitability and break-even analysis underscores its importance in business operations. By closely monitoring and managing prime costs, businesses can optimize their pricing strategies, enhance profit margins, and achieve financial stability. This meticulous approach to cost management not only ensures short-term viability but also fosters long-term success by enabling strategic investments and market expansion. As such, prime cost remains a fundamental element in the financial toolkit of any business seeking to maximize its potential for growth and profitability.
3. Use in Budgeting and Financial Reporting
In the realm of business finance, prime cost plays a pivotal role in budgeting and financial reporting, serving as a cornerstone for strategic decision-making. Prime cost, which encompasses the direct costs associated with producing goods or services—such as raw materials, labor, and overheads—provides a clear snapshot of the minimum expenses required to maintain production levels. This metric is essential in budgeting as it helps businesses allocate resources efficiently. By accurately calculating prime costs, companies can set realistic production targets and price their products competitively without compromising profitability. For instance, if a manufacturing firm identifies that its prime cost for producing a unit of product is $50, it can then determine the minimum selling price needed to break even and make informed decisions about pricing strategies. In financial reporting, prime cost is equally crucial as it enhances transparency and accountability. Including prime costs in financial statements allows stakeholders to understand the true cost structure of the business. This transparency is particularly important for investors who need to assess the company's operational efficiency and potential for future growth. Moreover, by separating prime costs from other expenses like marketing and administrative costs, businesses can better analyze their cost structure and identify areas for improvement. For example, if a company notices that its prime costs are increasing disproportionately compared to other expenses, it may indicate inefficiencies in production processes or supply chain issues that need to be addressed. Furthermore, prime cost analysis aids in variance analysis—a critical tool in financial reporting. By comparing actual prime costs with budgeted or standard costs, businesses can identify variances that may signal underlying issues such as changes in raw material prices or labor productivity. This allows for timely corrective actions to be taken, ensuring that the business remains on track with its financial goals. Additionally, prime cost data can be used to evaluate the performance of different departments or projects within an organization. For instance, comparing the prime costs of different production lines can help management decide which lines are more profitable and where resources should be allocated. In summary, the use of prime cost in budgeting and financial reporting is indispensable for businesses seeking to optimize their operations and make informed strategic decisions. It provides a robust framework for resource allocation, enhances financial transparency, and facilitates detailed cost analysis. By integrating prime cost into their financial planning and reporting processes, businesses can ensure they are operating efficiently, competitively pricing their products, and maintaining strong financial health. This holistic approach to cost management underscores the significance of prime cost as a fundamental metric in business finance.