What Are Grommets

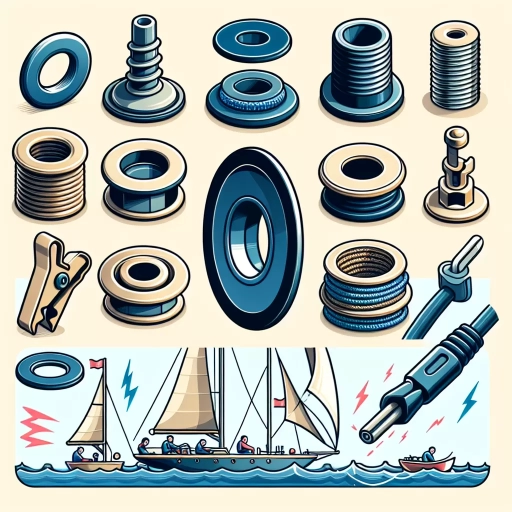
Grommets are versatile components that play a crucial role in various industries, from electronics and automotive to textiles and construction. These small, ring-shaped devices serve multiple purposes, making them an essential part of many modern products. To understand their significance, it is important to delve into what grommets are, how they function, and their numerous benefits and applications. This article will explore these aspects in detail, starting with the fundamental question: **What Are Grommets?** By examining their definition, we will set the stage for a deeper understanding of their mechanisms and the wide range of advantages they offer across different sectors.
What Are Grommets?
Grommets are versatile components that play a crucial role in various industries, from manufacturing and construction to electronics and textiles. Understanding what grommets are and their significance involves delving into their definition and purpose, the different types available, and their common uses. At their core, grommets serve as protective or reinforcing elements, often used to prevent damage to materials or to facilitate the passage of cables, wires, or other objects. The article will explore these aspects in detail, starting with the fundamental definition and purpose of grommets, which sets the stage for understanding their diverse applications and types. By examining the different types of grommets, readers will gain insight into how these components are tailored for specific needs. Finally, an overview of their common uses will highlight the widespread importance of grommets across various sectors. This comprehensive approach ensures a thorough understanding of what grommets are and why they are indispensable in modern technology and everyday life. Let's begin by defining what grommets are and their purpose.
Definition and Purpose
Grommets are small, typically ring-shaped components used to reinforce and protect holes in various materials such as fabric, leather, plastic, or metal. The primary **definition** of a grommet is a device that prevents the material around a hole from fraying or tearing, thereby extending the lifespan of the material and enhancing its durability. The **purpose** of grommets is multifaceted. Firstly, they provide structural integrity by distributing stress evenly around the hole, preventing it from expanding or deforming under tension. This is particularly crucial in applications where the material is subject to constant use or environmental stressors. For instance, in sailmaking, grommets are used to reinforce holes through which ropes or cables pass, ensuring that the fabric does not tear or weaken over time. Secondly, grommets serve as protective barriers against abrasion and wear. By encasing the edge of a hole with a smooth, often metal or plastic ring, grommets prevent the material from chafing against other objects that pass through it. This is especially important in industrial settings where machinery and equipment are frequently moved or manipulated. Thirdly, grommets can enhance the aesthetic appeal of a product by providing a clean and finished look to what would otherwise be a raw or rough edge. In consumer goods like clothing, bags, and upholstery, grommets can add a touch of professionalism and quality. Lastly, grommets facilitate easier installation and maintenance by providing a secure anchor point for fasteners or cables. This simplifies tasks such as threading wires through panels in electronics or securing ropes in outdoor gear. In summary, grommets are essential components that combine functional benefits like durability and protection with practical advantages such as ease of use and improved appearance. Their versatility makes them indispensable across various industries and applications.
Types of Grommets
Grommets are versatile components used in various industries to protect wires, cables, and other materials from abrasion and damage. There are several types of grommets, each designed to serve specific purposes and meet different requirements. 1. **Rubber Grommets**: These are the most common type and are made from rubber or elastomers. They are flexible, durable, and provide excellent insulation and sealing properties. Rubber grommets are widely used in electrical applications to protect cables and wires from moisture and abrasion. 2. **Plastic Grommets**: Made from materials like nylon, polyethylene, or polypropylene, plastic grommets offer a more rigid alternative to rubber grommets. They are often used in applications where high strength and resistance to chemicals are necessary. Plastic grommets are commonly found in automotive, aerospace, and industrial settings. 3. **Metal Grommets**: These grommets are made from metals such as brass, aluminum, or stainless steel. Metal grommets provide superior strength and durability, making them ideal for heavy-duty applications where high load-bearing capacity is required. They are often used in construction, marine, and industrial environments. 4. **Fabric Grommets**: Also known as eyelets, fabric grommets are used to reinforce holes in fabrics like canvas, leather, or nylon. They are typically made from metal or plastic and are used in applications such as sailmaking, awning manufacturing, and bag production. 5. **Split Grommets**: These grommets have a split or slit along one side, allowing them to be easily installed over existing cables or wires without the need for disassembly. Split grommets are particularly useful in retrofitting situations where access is limited. 6. **Threaded Grommets**: These grommets have internal threads that allow them to be screwed into place, providing a secure and stable installation. Threaded grommets are often used in applications where the grommet needs to be firmly anchored to a surface. 7. **Self-Tapping Grommets**: Similar to threaded grommets but with self-tapping screws, these grommets can be directly screwed into materials like plastic or metal without pre-drilling a hole. Self-tapping grommets save time and effort during installation. 8. **Cable Management Grommets**: Designed specifically for cable management, these grommets help organize and protect multiple cables and wires. They often feature multiple channels or compartments to keep cables separated and tidy. 9. **Custom Grommets**: For unique applications, custom grommets can be designed and manufactured to meet specific requirements. These can vary in material, size, shape, and functionality based on the needs of the user. Each type of grommet is engineered to address different challenges and ensure the longevity and integrity of the materials they protect. By selecting the appropriate type of grommet for a particular application, users can enhance performance, safety, and overall system reliability.
Common Uses
Grommets are versatile components with a wide range of applications across various industries. In the context of textiles, grommets are commonly used to reinforce holes in fabric, preventing them from fraying or tearing. This is particularly useful in outdoor gear such as tents, tarps, and awnings, where durability is crucial. In the marine industry, grommets are employed to secure ropes and cables on boats and ships, ensuring a secure and watertight seal. They are also integral in the manufacturing of curtains and drapes, allowing for smooth operation of drawstrings and cords. In electrical and electronic applications, grommets serve as protective sleeves for cables and wires, shielding them from abrasion and environmental damage. This is essential in automotive, aerospace, and industrial settings where cables are exposed to harsh conditions. Additionally, grommets are used in construction to protect pipes and conduits as they pass through walls or floors, preventing damage from friction and moisture. In medical devices, grommets play a critical role in ensuring the integrity of tubing and catheters. They provide a secure seal around these components, preventing leakage and contamination. Furthermore, grommets are utilized in the production of musical instruments, particularly drums, where they help to secure drumheads and maintain tuning stability. In the realm of DIY projects and home improvement, grommets are often used to organize cables and wires behind furniture or in home theaters, keeping spaces tidy and organized. They also find use in crafting and sewing projects, such as making bags or pouches with reinforced holes for straps or zippers. Overall, the common uses of grommets highlight their adaptability and importance across diverse sectors, from enhancing durability in textiles to ensuring safety and efficiency in electrical systems. Their ability to provide a secure, protective seal makes them an indispensable component in many applications.
How Do Grommets Work?
Grommets are versatile components used in various industries, including electronics, automotive, and construction, to protect cables and wires from abrasion and damage. Understanding how grommets work involves delving into three key aspects: their material composition, the installation process, and their functional mechanism. Firstly, the material composition of grommets is crucial as it determines their durability and performance. Grommets can be made from a variety of materials such as rubber, plastic, or metal, each offering different properties like flexibility, resistance to chemicals, or strength. Secondly, the installation process of grommets is straightforward yet critical for their effectiveness. Proper installation ensures that the grommet fits snugly around the cable or wire, preventing any damage or exposure to harsh environments. Lastly, the functional mechanism of grommets revolves around their ability to provide a protective barrier while allowing for smooth passage of cables and wires. This mechanism is essential for maintaining the integrity of electrical systems and preventing potential hazards. To begin with, let's explore the **Material Composition** of grommets, which forms the foundation of their functionality and reliability.
Material Composition
Material composition plays a crucial role in the functionality and durability of grommets. Grommets are typically made from materials such as rubber, plastic, metal, or a combination of these. Rubber grommets are often used in applications requiring flexibility and resistance to abrasion, making them ideal for protecting cables and wires from damage. They are commonly composed of synthetic rubber compounds like neoprene or EPDM (ethylene propylene diene monomer), which offer excellent resistance to chemicals, ozone, and extreme temperatures. Plastic grommets, on the other hand, are more rigid and may be made from materials like nylon, polypropylene, or PVC. These are often used in applications where a higher level of structural integrity is necessary and can be formulated to meet specific requirements such as UV resistance or high impact strength. Metal grommets are less common but provide superior strength and are typically used in heavy-duty applications. They can be made from materials like stainless steel, aluminum, or brass, offering excellent corrosion resistance and mechanical strength. In some cases, grommets may also be reinforced with additional materials to enhance their performance. For instance, a rubber grommet might have a metal insert for added stability or a plastic grommet might be reinforced with fiberglass for increased tensile strength. The choice of material depends on the specific use case and environmental conditions in which the grommet will operate. For example, in marine environments where exposure to saltwater is a concern, stainless steel grommets would be preferred due to their high corrosion resistance. In contrast, indoor electrical applications might use rubber or plastic grommets due to their insulating properties and ease of installation. Understanding the material composition of grommets is essential for ensuring they perform their intended function effectively. Whether it's protecting cables from abrasion, providing structural support, or withstanding harsh environmental conditions, the right material choice can significantly impact the overall performance and lifespan of the grommet. This attention to detail in material selection underscores the importance of considering all aspects when determining how grommets work and how they can best serve their purpose in various applications.
Installation Process
The installation process of grommets is a straightforward yet crucial step to ensure their effective functionality. Here’s a step-by-step guide to installing grommets: 1. **Preparation**: Begin by selecting the appropriate grommet size and type for your specific application. Ensure you have the necessary tools, such as a grommet punch or a sharp utility knife, and a hammer or press. 2. **Marking**: Identify the location where you want to install the grommet. Mark this spot carefully to ensure it is centered and aligned with any other components or holes. 3. **Cutting**: Use your chosen tool to cut a hole in the material at the marked location. If using a grommet punch, place it over the mark and strike it with a hammer to create a clean, precise hole. If using a utility knife, carefully cut out a circle slightly smaller than the grommet's inner diameter. 4. **Insertion**: Place the grommet over the hole, ensuring it is centered. For metal grommets, you may need to use a grommet setting tool or press to secure it in place. For rubber or plastic grommets, they can often be pressed in by hand or with light tapping from a hammer. 5. **Securing**: If using metal grommets with flanges on both sides, use your setting tool or press to crimp the flanges over the material, securing the grommet firmly in place. This ensures that the grommet does not move or fall out under stress. 6. **Inspection**: Once installed, inspect the grommet to ensure it is properly seated and there are no signs of damage or misalignment. 7. **Testing**: Finally, test the installation by passing a wire or cable through the grommet to verify that it fits smoothly and does not cause any abrasion or damage to the cable. By following these steps meticulously, you can ensure that your grommets are installed correctly, providing long-lasting protection and support for cables and wires while preventing wear and tear on surrounding materials. Proper installation is key to maximizing the benefits of using grommets in various applications.
Functional Mechanism
**Functional Mechanism of Grommets** Grommets are small, ring-shaped components designed to protect and reinforce holes in various materials such as fabric, leather, plastic, or metal. The functional mechanism of grommets revolves around their ability to distribute stress evenly and prevent damage to the surrounding material. Here’s how they work: 1. **Installation**: Grommets are typically installed by pressing them into pre-drilled holes. They consist of two parts: an outer ring and an inner ring. The outer ring is usually larger and has a flange that sits on the surface of the material, while the inner ring has a smaller diameter and fits snugly inside the hole. 2. **Stress Distribution**: When a grommet is in place, it distributes the stress caused by pulling or pushing through the hole more evenly. This is crucial because without a grommet, the material around the hole can tear or fray under tension, leading to premature wear and potential failure. 3. **Protection**: The inner ring of the grommet acts as a barrier between the material and any objects passing through it, such as wires, ropes, or tubes. This prevents abrasion and friction that could otherwise damage the material over time. 4. **Reinforcement**: By providing a rigid structure around the hole, grommets reinforce the material against tearing or stretching. This is particularly important in applications where the material is subject to repeated stress or heavy use. 5. **Sealing**: In some cases, grommets can also serve as seals to prevent water, dust, or other contaminants from entering through the hole. This is achieved through the tight fit of the grommet within the hole and sometimes with additional sealing materials like rubber or silicone. 6. **Versatility**: Grommets come in various sizes and materials to suit different applications. For example, metal grommets are often used in industrial settings for durability, while plastic grommets might be preferred in lighter applications such as clothing or bags. In summary, the functional mechanism of grommets involves distributing stress, protecting materials from abrasion, reinforcing holes against damage, and sometimes sealing against contaminants. These small components play a significant role in ensuring the longevity and integrity of various products across different industries.
Benefits and Applications of Grommets
Grommets are versatile components that offer a multitude of benefits and applications across various industries. At their core, grommets provide essential protection and reinforcement, ensuring the integrity and longevity of materials and systems. They also exhibit remarkable versatility, adapting seamlessly to different industrial needs, from electrical and automotive to medical and textile sectors. Additionally, grommets offer cost-effective solutions, reducing maintenance costs and enhancing overall efficiency. By understanding these key aspects, it becomes clear why grommets are an indispensable tool in modern manufacturing and engineering. This article will delve into these benefits, starting with the critical role of protection and reinforcement that grommets play in safeguarding against wear and tear, thereby extending the lifespan of critical components.
Protection and Reinforcement
Protection and reinforcement are pivotal aspects of the benefits and applications of grommets. Grommets serve as protective barriers that shield cables, wires, and other materials from abrasion, wear, and tear. By encasing these elements within a durable, often rubber or plastic, sleeve, grommets prevent damage caused by friction against sharp edges or rough surfaces. This protection is particularly crucial in industrial settings where machinery and equipment are subject to constant use and potential hazards. For instance, in automotive manufacturing, grommets protect electrical wiring from the harsh conditions inside vehicle compartments, ensuring reliable performance and safety. In addition to protection, grommets also provide reinforcement by adding structural integrity to the points where they are installed. They distribute stress evenly around the hole through which cables or wires pass, thereby preventing the material from tearing or deforming under load. This reinforcement is essential in applications such as aerospace engineering where lightweight yet robust components are necessary. Here, grommets not only protect sensitive wiring but also contribute to the overall durability of the aircraft's systems. Moreover, grommets offer a versatile solution for various industries due to their adaptability. They come in different sizes, shapes, and materials to suit specific needs. For example, in marine environments where corrosion is a significant concern, grommets made from marine-grade materials can be used to protect electrical connections from seawater and salt spray. Similarly, in medical devices where sterility is paramount, grommets can be designed with antimicrobial properties to prevent the spread of infections. The use of grommets also enhances the aesthetic appeal of products by providing a neat and organized appearance. In consumer electronics like smartphones and laptops, grommets help manage cables efficiently within the device casing, contributing to a sleek design that appeals to users. Furthermore, they facilitate easier assembly and maintenance by allowing for quick access to internal components without compromising the integrity of the device. In summary, the protection and reinforcement offered by grommets are fundamental to their widespread adoption across diverse industries. By safeguarding against mechanical stress and environmental factors while adding structural strength, grommets ensure the reliability and longevity of various systems. Their versatility in terms of material selection and design makes them an indispensable component in modern engineering and manufacturing processes.
Versatility in Industries
Versatility in industries is a cornerstone of innovation and efficiency, and grommets exemplify this principle perfectly. Across various sectors, grommets demonstrate their adaptability and multifunctionality, making them an indispensable component in diverse applications. In the automotive industry, grommets protect wires and cables from abrasion and moisture, ensuring the reliability of electrical systems. In construction, they serve as seals around pipes and cables, preventing water and air leaks while maintaining structural integrity. The aerospace sector leverages grommets to shield sensitive wiring from extreme temperatures and vibrations, enhancing the safety and performance of aircraft. In electronics manufacturing, grommets are used to manage cable management systems, reducing clutter and improving airflow within enclosures. Even in medical devices, grommets play a crucial role by providing sterile seals for tubing and wires, ensuring the hygiene and functionality of life-saving equipment. This widespread adoption underscores the versatility of grommets, highlighting their ability to adapt to different environments and requirements while consistently delivering high performance. By offering protection, sealing, and organizational benefits across multiple industries, grommets illustrate the power of versatile design in enhancing operational efficiency and product reliability.
Cost-Effective Solutions
Cost-effective solutions are a crucial aspect of any business or project, and grommets offer several advantages in this regard. By integrating grommets into various applications, users can significantly reduce costs without compromising on quality or performance. Here are some key ways grommets provide cost-effective solutions: 1. **Durability**: Grommets are designed to withstand wear and tear, extending the lifespan of cables, wires, and other materials they protect. This durability reduces the need for frequent replacements, thereby saving money on maintenance and replacement costs. 2. **Efficient Installation**: Grommets are relatively easy to install compared to other protective solutions. Their simplicity in design means less labor is required, which translates to lower installation costs. Additionally, they can be easily integrated into existing systems without major modifications. 3. **Versatility**: Grommets come in various sizes and materials, making them adaptable to a wide range of applications. This versatility allows businesses to use the same type of grommet across different projects, reducing inventory costs and simplifying supply chain management. 4. **Protection Against Damage**: By providing a protective barrier around cables and wires, grommets prevent damage from abrasion, moisture, and other environmental factors. This protection reduces the likelihood of equipment failure, which can lead to costly repairs or replacements. 5. **Enhanced Safety**: In industries where safety is paramount, such as electrical or aerospace engineering, grommets play a critical role in preventing electrical shorts or other hazards. Ensuring safety through the use of grommets avoids potential legal liabilities and downtime due to accidents. 6. **Reduced Material Waste**: Because grommets are precision-made to fit specific needs, they minimize material waste during installation. This precision also ensures that the correct amount of material is used each time, further reducing overall costs. 7. **Long-Term Cost Savings**: While the initial cost of purchasing grommets may seem insignificant compared to other components, their long-term benefits add up substantially. Over time, the cumulative savings from reduced maintenance, fewer replacements, and enhanced safety contribute significantly to a company's bottom line. In summary, grommets offer a multifaceted approach to cost-effectiveness by enhancing durability, simplifying installation, providing versatility, protecting against damage, ensuring safety, reducing material waste, and delivering long-term cost savings. These benefits make grommets an indispensable component in various industries seeking efficient and economical solutions.